复合材料热压罐成型技
第4章热压罐成型工艺(PDF)

胶膜压延法
树脂含量可由胶膜 厚度,辊压力与间 距、纤维张力、加 热温度等控制
线速度大,效率高 树脂含量容易控制 挥发分含量低,污染小 制膜和浸渍过程分步进
行,减少对纤维损伤
预浸料制备
大纱束或织物难于浸透 高粘度树脂难于浸渍 设备投资高,纤维用量大
2 辅助材料 Auxiliary material
碳纤维 其热膨胀系数与所成型复合材料构件一致,质量轻,材料模量高,模具
复合材料
刚度大;适用于高精度的大型构件的成型,但材料成本高,耐温低,表 面易划伤,有吸湿问题
玻璃纤维 质量轻,材料价格低;但材料模量低,模具刚度差;一般用于简单成型 复合材料 或型面要求不高的结构
3 模具材料-模具的分类
根据模具用材料
可很好的排除挥发物
4 袋压成型——压力袋成型
密封装置
盖板
压缩空气
空气压缩机
压力袋
特点:
模具
复合材料坯料
通过向橡皮囊构成的压力袋(气压室)内注入压缩空气,实现对 复合材料坯料的加压,也叫气压室成型;
真空袋基础上发展而来,气压均匀垂直作用在毛胚的表面,压 力可达0.25-0.5MPa,对模具强度和刚度的要求较高;
真空薄膜
具有较好的强度、延展性、耐温性、耐磨性和韧性。使用时,用腻子 将成型中的构件密封在模具上,形成真空袋
密封胶带
具有常温下的粘性,高温下密封性好,固化后易清理和贮存时间长等 特点
吸胶材料
可定量吸出复合材料毛坯中的多余树脂,并有一定透气性能的材料。 有吸胶毡、玻璃布、吸胶纸等,其单位面积吸树脂量随材料而异
成型工 艺稳定 可靠
热压罐内的压力和温度均匀,可以保证成型构件的质量稳定。一般热压罐成型 工艺制造的构件孔隙率较低、树脂含量均匀,相对其他成型工艺热压罐制备构 件的力学性能稳定可靠,迄今为止,航空航天领域要求高承载的绝大多数复合 材料构件都采用热压罐成型工艺。
热压罐成型复合材料成型工艺的常见缺陷及对策
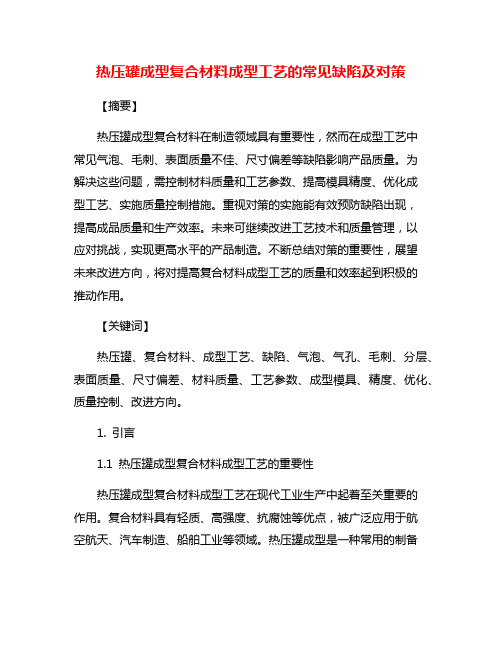
热压罐成型复合材料成型工艺的常见缺陷及对策【摘要】热压罐成型复合材料在制造领域具有重要性,然而在成型工艺中常见气泡、毛刺、表面质量不佳、尺寸偏差等缺陷影响产品质量。
为解决这些问题,需控制材料质量和工艺参数、提高模具精度、优化成型工艺、实施质量控制措施。
重视对策的实施能有效预防缺陷出现,提高成品质量和生产效率。
未来可继续改进工艺技术和质量管理,以应对挑战,实现更高水平的产品制造。
不断总结对策的重要性,展望未来改进方向,将对提高复合材料成型工艺的质量和效率起到积极的推动作用。
【关键词】热压罐、复合材料、成型工艺、缺陷、气泡、气孔、毛刺、分层、表面质量、尺寸偏差、材料质量、工艺参数、成型模具、精度、优化、质量控制、改进方向。
1. 引言1.1 热压罐成型复合材料成型工艺的重要性热压罐成型复合材料成型工艺在现代工业生产中起着至关重要的作用。
复合材料具有轻质、高强度、抗腐蚀等优点,被广泛应用于航空航天、汽车制造、船舶工业等领域。
热压罐成型是一种常用的制备复合材料制品的工艺方法,通过热压的方式将树脂基复合材料与增强材料加热固化,形成具有特定性能和形状的制品。
热压罐成型复合材料成型工艺的重要性体现在以下几个方面:通过热压罐成型可以实现复合材料高效率、高质量的生产,提高生产效率和制品质量。
热压罐成型工艺可以实现复合材料的复杂成型,满足不同领域对复合材料制品的各种需求。
热压罐成型技术可以有效控制制品的成型过程,减少工艺参数对成品性能的影响,确保制品的稳定性和一致性。
热压罐成型复合材料成型工艺的重要性在于提高生产效率、提高制品质量、满足市场需求,是现代工业制造中不可或缺的一环。
通过对该工艺的研究和不断改进,可以更好地发挥其优势,推动复合材料产业的发展。
1.2 研究目的和意义1.了解热压罐成型复合材料成型工艺的重要性和发展趋势,为提高产品质量和性能提供技术支持。
2.分析常见缺陷对产品品质和成型效率的影响,找出问题根源,提出相应的改进措施。
热压罐成型复合材料成型工艺的常见缺陷及对策

热压罐成型复合材料成型工艺的常见缺陷及对策热压罐成型复合材料成型工艺是一种广泛应用于航空、汽车、船舶等领域的高性能材料成型技术。
由于其具有质量轻、刚性高、耐高温耐腐蚀等优点,因此备受青睐。
在实际生产中,热压罐成型复合材料成型工艺常常会出现各种缺陷,影响产品质量和性能。
本文将重点介绍热压罐成型复合材料成型工艺中常见的缺陷及相应的对策。
一、气泡气泡是热压罐成型复合材料成型工艺中常见的缺陷之一。
气泡的存在会导致制品的密度不均匀,影响其力学性能和耐久性。
气泡的形成原因主要包括树脂充填不足、工装表面粗糙和工艺参数设置不当等。
对策:1. 提高树脂充填效率,保证充填充分;2. 提高工装表面光洁度,减少气泡的产生;3. 调整工艺参数,如温度、压力和时间,使树脂更好地充填并排除气泡。
二、裂纹裂纹是热压罐成型复合材料成型工艺中另一个常见的缺陷。
裂纹的存在会降低制品的强度和韧性,影响其使用寿命。
裂纹的形成主要受到成型温度、成型压力和成型时间的影响,同时也与工装的设计和加工精度有关。
对策:1. 控制成型温度,避免温度过高导致树脂的膨胀收缩,产生裂纹;2. 合理控制成型压力,保证树脂充填充分但不会过大导致裂纹;3. 控制成型时间,避免过长造成树脂过度固化产生裂纹;4. 设计合理的工装结构,减少应力集中和变形,避免裂纹的产生。
三、毛刺对策:1. 优化模具的设计,减少脱模力和剪切力,避免毛刺的产生;2. 提高模具表面的加工精度和光洁度,减少毛刺的生成;3. 采用表面喷涂、电镀等方法,形成一层平滑的保护层,减少毛刺的产生。
四、变形变形是热压罐成型复合材料成型工艺中常见的内部缺陷。
制品的变形会导致尺寸偏差和形状不规则,影响其使用功能和外观美观。
变形的产生主要与工装设计、成型参数和材料性能有关。
对策:1. 优化工装设计,减少应力集中和变形;2. 调整成型参数,如温度、压力和时间,使成型过程更加稳定;3. 选择合适的复合材料,提高材料的强度和韧性,减少变形的产生。
热压罐成型复合材料成型工艺的常见缺陷及对策
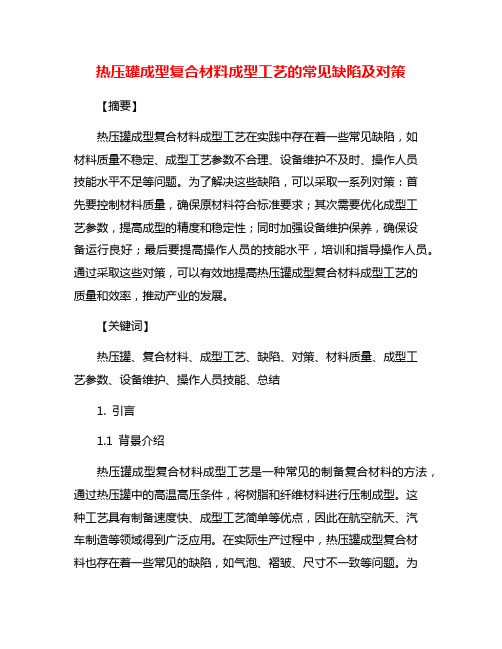
热压罐成型复合材料成型工艺的常见缺陷及对策【摘要】热压罐成型复合材料成型工艺在实践中存在着一些常见缺陷,如材料质量不稳定、成型工艺参数不合理、设备维护不及时、操作人员技能水平不足等问题。
为了解决这些缺陷,可以采取一系列对策:首先要控制材料质量,确保原材料符合标准要求;其次需要优化成型工艺参数,提高成型的精度和稳定性;同时加强设备维护保养,确保设备运行良好;最后要提高操作人员的技能水平,培训和指导操作人员。
通过采取这些对策,可以有效地提高热压罐成型复合材料成型工艺的质量和效率,推动产业的发展。
【关键词】热压罐、复合材料、成型工艺、缺陷、对策、材料质量、成型工艺参数、设备维护、操作人员技能、总结1. 引言1.1 背景介绍热压罐成型复合材料成型工艺是一种常见的制备复合材料的方法,通过热压罐中的高温高压条件,将树脂和纤维材料进行压制成型。
这种工艺具有制备速度快、成型工艺简单等优点,因此在航空航天、汽车制造等领域得到广泛应用。
在实际生产过程中,热压罐成型复合材料也存在着一些常见的缺陷,如气泡、褶皱、尺寸不一致等问题。
为了提高产品质量和生产效率,需要对这些常见缺陷进行深入分析,并制定相应的对策来解决这些问题。
本文将从控制材料质量、优化成型工艺参数、加强设备维护保养、提高操作人员技能水平等方面进行讨论,为热压罐成型复合材料成型工艺的改进提供参考。
2. 正文2.1 热压罐成型复合材料成型工艺存在的常见缺陷热压罐成型复合材料是一种常用的制备工艺,在许多领域都有广泛的应用。
这种工艺也存在一些常见的缺陷,影响材料的质量和性能。
以下是热压罐成型复合材料成型工艺存在的一些常见缺陷:1. 母材和增强材料不充分混合:在成型过程中,如果母材和增强材料没有充分混合,会导致材料性能不均匀,出现局部强度不足的现象。
2. 难以排气:在热压罐成型过程中,由于材料层间存在气泡,导致成型后出现气孔,影响材料的密实性和强度。
3. 成型温度控制不当:如果成型温度过高或过低,都会影响材料的物理性能,例如过高的温度会导致材料烧损,过低的温度则会影响材料的结晶度。
复合材料热压罐成型模具设计研究方法

复合材料热压罐成型模具设计研究方法复合材料要制造成为热压罐成型模具有哪些设计的技巧和要点呢?下面为你讲解!随着复合材料在飞机结构件上用量的逐步增加,零件越来越大而复杂,并逐步使用到主承力件上,这对复合材料制件的质量提出了更高的要求。
因复合材料制件的固化成型特点,其质量在很大程度上取决于成型模具的质量,而高质量的模具科学、合理的设计,特别是对于大型模具,除模具质量对制件质量的影响外,模具的尺寸、重量对模具成本以及复材制件的总制造成本有很大影响。
通过对复合材料热压罐成型模具的设计、制造、转运及使用验证等工程研究及分析,结合复材模具设计的经验方法,归纳出以下几点模具设计原则。
满足制件结构及工艺要求在设计复合材料成型模具前,要对制件的设计输入进行充分分析,以产生模具结构的初步概念。
(1)分析制件的工程结构。
通常有壁板、梁、肋、长桁、接头、以及整体盒段等结构形式。
根据制件结构形式,可对模具有个大致概念,壁板常为大型框架结构;梁一般较长,常有阴模、阳模形式;长桁一般为细长结构;整体盒段一般需上下合模。
(2)分析制件的工程界面。
是否有气动面、装配面、胶接面等,一般情况下可确定这些面为贴膜面;但如果这些面结构较复杂时,设计可考虑在工程界面侧添加补偿层,此时贴膜面可设计在工程界面的背面。
(3)分析制件的质量要求。
制件的外形轮廓尺寸精度直接影响到模具的质量要求及成本,可通过设计合理的模具结构、定位方法及加工方法来达到精度要求。
(4)分析制件的成型工艺方法,是共固化、共胶接还是二次交接。
共固化中,所有层为湿铺层一次进罐,需要较多模具组合到一起同时使用,通常整套模具较复杂;共胶接为干湿件进罐固化,需要一部分零件的成型模具,及已固化零件与湿铺层二次进罐固化的模具;二次胶接时所有零件已固化,通过胶膜把他们固化到一起,需要所有零件的成型模以及二次胶接的定位模具。
模具材料的选择用作复合材料成型模具的材料主要有普通钢、INVAR钢、复合材料(双马和环氧树脂)、铝等。
复合材料热压罐技术原理
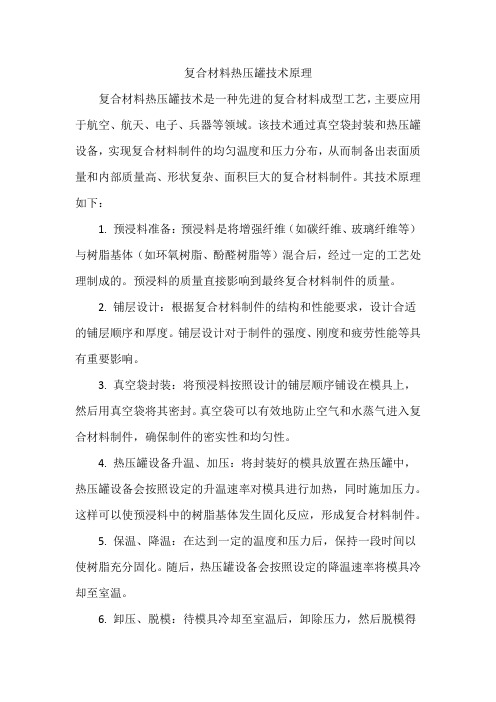
复合材料热压罐技术原理
复合材料热压罐技术是一种先进的复合材料成型工艺,主要应用于航空、航天、电子、兵器等领域。
该技术通过真空袋封装和热压罐设备,实现复合材料制件的均匀温度和压力分布,从而制备出表面质量和内部质量高、形状复杂、面积巨大的复合材料制件。
其技术原理如下:
1. 预浸料准备:预浸料是将增强纤维(如碳纤维、玻璃纤维等)与树脂基体(如环氧树脂、酚醛树脂等)混合后,经过一定的工艺处理制成的。
预浸料的质量直接影响到最终复合材料制件的质量。
2. 铺层设计:根据复合材料制件的结构和性能要求,设计合适的铺层顺序和厚度。
铺层设计对于制件的强度、刚度和疲劳性能等具有重要影响。
3. 真空袋封装:将预浸料按照设计的铺层顺序铺设在模具上,然后用真空袋将其密封。
真空袋可以有效地防止空气和水蒸气进入复合材料制件,确保制件的密实性和均匀性。
4. 热压罐设备升温、加压:将封装好的模具放置在热压罐中,热压罐设备会按照设定的升温速率对模具进行加热,同时施加压力。
这样可以使预浸料中的树脂基体发生固化反应,形成复合材料制件。
5. 保温、降温:在达到一定的温度和压力后,保持一段时间以使树脂充分固化。
随后,热压罐设备会按照设定的降温速率将模具冷却至室温。
6. 卸压、脱模:待模具冷却至室温后,卸除压力,然后脱模得
到复合材料制件。
总之,复合材料热压罐技术原理主要是通过控制温度、压力和时间等参数,实现树脂基体的固化反应,从而制备出具有高性能的复合材料制件。
复合材料热压罐
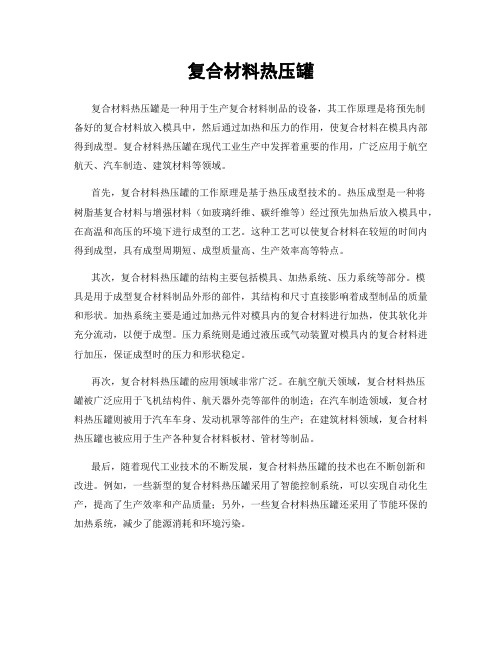
复合材料热压罐复合材料热压罐是一种用于生产复合材料制品的设备,其工作原理是将预先制备好的复合材料放入模具中,然后通过加热和压力的作用,使复合材料在模具内部得到成型。
复合材料热压罐在现代工业生产中发挥着重要的作用,广泛应用于航空航天、汽车制造、建筑材料等领域。
首先,复合材料热压罐的工作原理是基于热压成型技术的。
热压成型是一种将树脂基复合材料与增强材料(如玻璃纤维、碳纤维等)经过预先加热后放入模具中,在高温和高压的环境下进行成型的工艺。
这种工艺可以使复合材料在较短的时间内得到成型,具有成型周期短、成型质量高、生产效率高等特点。
其次,复合材料热压罐的结构主要包括模具、加热系统、压力系统等部分。
模具是用于成型复合材料制品外形的部件,其结构和尺寸直接影响着成型制品的质量和形状。
加热系统主要是通过加热元件对模具内的复合材料进行加热,使其软化并充分流动,以便于成型。
压力系统则是通过液压或气动装置对模具内的复合材料进行加压,保证成型时的压力和形状稳定。
再次,复合材料热压罐的应用领域非常广泛。
在航空航天领域,复合材料热压罐被广泛应用于飞机结构件、航天器外壳等部件的制造;在汽车制造领域,复合材料热压罐则被用于汽车车身、发动机罩等部件的生产;在建筑材料领域,复合材料热压罐也被应用于生产各种复合材料板材、管材等制品。
最后,随着现代工业技术的不断发展,复合材料热压罐的技术也在不断创新和改进。
例如,一些新型的复合材料热压罐采用了智能控制系统,可以实现自动化生产,提高了生产效率和产品质量;另外,一些复合材料热压罐还采用了节能环保的加热系统,减少了能源消耗和环境污染。
总之,复合材料热压罐作为一种重要的生产设备,在现代工业生产中发挥着不可替代的作用。
随着技术的不断进步,相信复合材料热压罐的应用领域将会更加广泛,生产效率和产品质量也会得到进一步提高。
复合材料热压罐成型工艺的常见缺陷及对策

复合材料热压罐成型工艺的常见缺陷及对策摘要:热压罐成型是复合材料应用较多、最为常见的一种成型工艺。
热压罐工艺生产的制品占整个复合材料制品产量50%以上。
热压罐成型工艺具有许多其他工艺不具备的优点,可制造形状复杂的制件,成型工艺灵活,适于生产大面积整体成型构件,纤维含量高,孔隙率低。
同时热压罐成型工艺具有设备投资高,成型周期长的特点。
热压罐成型复合材料构件主要缺陷包括外形尺寸超差与内部质量缺陷等,内部质量缺陷包括分层,夹杂等。
造成缺陷的原因种类繁多,包括制造中的人机料法环各环节的相关工序。
本文分析非等厚板材、曲率构件常见缺陷产生原因,分析内容对复合材料零件质量控制具有一定的借鉴作用。
关键词:复合材料;热压罐成型工艺;常见缺陷及对策引言随着复合材料在航空航天领域的用量占比逐渐增加,已成为与钛合金、铝合金、合金钢并驾齐驱的四大航空结构材料之一。
而热压罐成型技术依旧是现阶段制造复合材料构件的主要方法,成型面的温度场分布是影响构件成型质量的重要因素。
研究表明,成型过程中温度场的分布不均匀将会导致复合材料固化后产生残余应力,导致材料力学性能降低,材料受到损坏,最终影响构件成型质量。
成型模具一般为金属模具,具有良好的热传导性,成型模具对复合材料构件温度场的影响远远大于辅助材料对构件温度场的影响。
因此,成型模具在复合材料固化成型中具有重要影响,研究与复合材料构件直接接触的成型模具型板表面温度均匀性对最终成型质量至关重要。
1复合材料热压罐成型工艺特点复合材料热压罐成型工艺主要是将复合材料毛坯或胶接结构用真空袋密封在热压罐中,用罐体内部均匀温度场对成型中的零件施加温度压力,使其成为所需要的形状与质量状态的成型工艺方法。
其成型工艺特点主要是罐内压力均匀,真空袋内的零件在均匀压力下成型。
适用范围广,成型工艺稳定,热压罐温度条件几乎满足所有聚合物基复合材料的成型工艺要求。
可保证成型零件质量,热压罐成型工艺制造的层压板孔隙率较低,相对其他成型工艺成型层板力学性能稳定。
- 1、下载文档前请自行甄别文档内容的完整性,平台不提供额外的编辑、内容补充、找答案等附加服务。
- 2、"仅部分预览"的文档,不可在线预览部分如存在完整性等问题,可反馈申请退款(可完整预览的文档不适用该条件!)。
- 3、如文档侵犯您的权益,请联系客服反馈,我们会尽快为您处理(人工客服工作时间:9:00-18:30)。
(2)加热与气体循环系统 加热方式: 间接气体点火----常用方式 热油(联苯400oC,硅油425oC)----可燃---潜在危险 蒸汽加热----150oC~180oC-----温度低,使用少 电加热----(适用直径小于2米)-----运营成本高
(6)周边挡条----橡胶
School of Materials Science and Engineering
四、固化成型工艺流程
成型工艺流程
模具准备----裁减与铺叠----组合与装袋----固化与出罐脱模----检测----修整---二次成型----装配
School of Materials Science and Engineering
《复合材料制备新技术》
复合材料热压罐成型技术
主讲:梅启林 单位:材料学院
School of Materials Science and Engineering
一、前言
热压罐:
航空复合材料制品的主要生产设备,具有整体加热系统的大型压力容器。
优点:
(1)大范围内适应各种材料对加工条件的要求 高温环氧175oC,600KPa 聚酰亚胺300~400oC, 1MPa
五、热压罐成型工艺的仿真模拟
热压罐固化成型过程中发生的主要物理化学变化:
(1)促进树脂流动,确保浸渍充分,和预浸料准确到位 (2)纤维网络压实,实现纤维体积含量最大化 (3)合适的压力以抑制基体中空隙的形成 (4)合适的成型温度保证固化充分
成型过程的数值仿真模拟
(1)树脂流动 (2)纤维变形 (3)纤维压实 (4)空隙形成 (5)固化工艺优化热传导
工艺参数:
纤维状态(单丝根数、总纤度、捻度等----影响浸渍程度和含胶量)
胶液浓度(影响含胶量最严重的因素----调节胶液密度、温度来控制)
牵引速度
高----浸渍时间短,浸渍程度低和含胶量低
低----浸渍充分和含胶量高,效率低
纤维张力(高----含胶量低,影响外观)
School of Materials Science and Engineering
三、热压罐系统的结构与成型模具
成型模具
要求: (1)在成型温度和压力下保持适当的性能 (2)成本、寿命、精度、强度、质量、机加工性、热膨胀系数、尺寸稳
定性、表面处理及热导率等 模具材料类别: (1)室温至中温:树脂基复合材料 (2)低温至高温:金属材料 (3)超高温:陶瓷和石墨材料
School of Materials Science and Engineering
(2)有空或无空隔离薄膜 作用:防止粘模 PTFE、改性氟塑料薄膜
(3)吸胶材料 吸收多余树脂,控制、调节纤维体积含量 玻璃布、滤纸、各种纤维非织布、 200oC以下----多、廉价----涤纶非织造布
(4)透气材料 疏导真空袋内气体。厚涤纶非织造布,高温200oC用玻璃布
(5)脱模布 让多余树和挥发分通过并进入吸胶层;防止粘模 一般采用0.1mmPTFE玻璃布
陶瓷7.2,聚酰胺—4.68)
电成型镍
采用电镀工艺将镍沉积到母模(石膏) 表面光洁、耐磨、易修补、脱模好,但成本高
碳纤维增强环氧复合材料模具
热膨胀与复合材料相似 表面光洁、 轻质、易加工 使用温度不能高于其玻璃化温度,耐压低、耐用性、耐划伤性等不及金属
School of Materials Science and Engineering
主要工艺过程 (1)均匀稳定树脂膜的制备----关键 (2)树脂熔融浸渍纤维 (3)预浸料冷却 (4)预浸料收卷
School of Materials Science and Engineering
预浸料的性能
外观 物理性能
(1)单位面积纤维的质量(GB7192-87) (2)树脂含量(GB7192-87) (3)挥发分含量(GB6056-85) (4)粘性(表征预浸料铺覆性和层间粘合性的指标) (5)流动度(一定条件下,预浸料树脂可流出的数量占预浸料质量的百分比,
三、热压罐系统的结构与成型模具
铝、钢、殷钢模具
良好的表面处理性能、可多次重复使用----应用最广 殷钢硬度与钢相似,热膨胀系数比钢和铝更小-----理想模具材料 铝:软、热膨胀系数大、但密度小,易搬动,机加工性较殷钢好 热膨胀系数(铝—26.2,钢—13.2 (C),17.8(NI),铸铁—11.1,殷钢—0.28,金属-
气体循环系统(保证温度场的均匀性) 最佳气流速度:1~3m/s 太高----撕开真空袋 太低----温度不均匀
School of Materials Science and Engineering
三、热压罐系统的结构与成型模具
(3)气体加压系统 常用压缩气体: 空气:0.7~1.0MPa,温度上限120oC----低成本、但助燃,150oC以上使用危险 氮气(液氮):最常用,1.4~1.55MPa----抑制燃烧、易于分散到空气中 ----成本高 二氧化碳(液态):2.05MPa-----密度大,对人体有害 -----不易分散到空气中
(4)真空系统 最重要的辅助系统 水封型真空泵最可靠,油泵易被固化挥发分副产物腐蚀
(5)控制系统 对固化工艺进行监控----使工艺参数合理化、降低成本 计算机控制系统应同时安装微处理控制器,以防计算机控制系统失灵
(6)其它辅助系统 冷却系统、装卸系统等
School of Materials Science and Engineering
School of Materials Science and Engineering
六、热压罐成型技术的应用
复合材料制件 F-14
F-15
F-16
F-18
B-1
门
方向舵
升降舵
垂尾
平尾
副翼
扰流板
襟翼
翼盒
机身
AV-8B
DC-10 Demo
School of Materials Science and Engineering
GB5260-85) (6)凝胶时间(GB5259-85)
化学性能
化学成分(红外光谱GB5416-88) 反应热焓(DSC,Q/6S 975-91)
School of Materials Science and Engineering
三、热压罐系统的结构与成型模具
热压罐系统的结构
(中温低压120oCx0.275MPa-----高温高压760oCx69MPa)
陶瓷模具: 适用成型耐高温聚酰亚胺、热塑性树脂基复合材料等
School of Materials Science and Engineering
四、固化成型工艺流程
工艺辅助材料
(1)真空袋材料与密封胶条 100oC以下----PE薄膜 200oC以下----改性尼龙薄膜 耐高温聚酰亚胺、热塑性树脂基复合材料成型----耐高温聚酰亚胺薄膜
(2)加压灵活性强,均匀
缺点:
(1)尺寸、温度、压力要求高,结构复杂,制造成本昂贵 小型:D1m,L2m,10万美元, 大型 :100万美元
(2)升温、加压速度慢,温度控制精度小
School of Materials Science and Engineering
二、预浸料
概念
纤维浸渍树脂后形成的片状材料。
预浸料的制备
(2)连续排铺法 特点: 连续性、效率高、适合大规模生产 基本过程: 若干丝束----整经分丝----浸胶----挤胶----烘干----垫隔离纸----压
实----收卷 工艺参数: 胶液浓度 浸渍时间 -----影响浸渍程度主要因素 牵引速度 挤压辊间隙-----控制含胶量关键部件 烘干温度、时间----(目的----除去挥发分,初步固化(调节粘性))
六、热压罐成型技术的应用
复合材料制件 DC-1011
737
727
757
767
Lear Fan
Demo
Demo
门
方向舵
升降舵
垂尾
平尾
副翼
扰流板
襟翼
翼盒
机身
School of Materials Science and Engineering
六、热压罐成型技术的应用
设计力学、理化性能
School of Materials Science and Engineering
预浸料的制备
溶液浸渍法(辊筒缠绕法、连续排铺法)
(1)辊筒缠绕法
特点:
间歇性、设备简单、生产效率低、批量小
实验室或小批量生产
工作原理:
一系列变速机构----调节辊筒转动、导丝辊丝杠横向移动速度比----纤维间距
School of Materials Science and Engineering
六、热压罐成型技术的应用
School of Materials Science and Engineering
Thanks for your attention!
School of Materials Science and Engineering
三、热压罐系统的结构与成型模具