稼动率与设备总合效率(OEE)分析
OEE设备总和效率.ppt

机台Tact time*Input
Total Time
SUM(A~I)
实际产出就是实际的Input,而理想产出为 Total Time – 停机时间
Performance:在相同時間内,設備實際產出數量與理論 上能夠產出數量的一種比較。
Quality:生産數量與符合客戶規格的產出數量的比較。
衡量一部設備的效率,不光是去看它的生産速度有多快,拼命 運轉,但是做出的都是不良品也都沒用,白白浪費成本。
所以OEE中的最後一個E是Effectiveness,而不是性能稼動率E 中的Efficiency。差別在於:
制程改善
D:品质异常 I:工程借机 G:换料 E:机台点检 F:停机5S
制造改善
J:待料 L:交接班 M:Wip过高 N:待Tray K:休息时间 O:其它问题
P
其它 P:缺料 Q:无排程
AUO OEE Loss Code統計
在做OEE分析之前我們需要定義OEE Loss標準Code。如果能夠 在機臺上直接就統計出這樣的數據是最好的。如不能直接統計,就需要 人員對此時間作記錄。以下為提供的統計格式。
AUO OEE的定义与介绍
解决损失及浪费的课题从哪里面来?我们就从OEE上着手。
OEE设备总合效率=时间稼动率X性能稼动率X良品率 =(负荷时间-停机时间)/负荷时间
X(理论C.TX投入数量)/(负荷时间-停机时间) X(投入数量-不良数量)/投入数量
AUO OEE的定义与介绍
AUO OEE的定义与介绍
Availability——時間稼動率 Performance efficiency——性能稼動率
Quality rate——合格品率
OEE焦點:它衡量的目的在於改善,而不是對人的評價。 OEE重點:掌握造成OEE低下的各類型損失,並加以改善。
OEE(设备综合效率)分析与管理

OEE(设备综合效率)分析与管理嘿,伙计们!今天我们要聊聊一个非常有趣的话题:OEE(设备综合效率)分析与管理。
你知道吗,这个话题可是关乎到咱们工厂的生产效率呢!所以,我们可得认真对待,不能马虎。
让我们来简单了解一下OEE是什么吧。
OEE是设备的运转率、可用率和性能指标的综合体现,它可以帮助我们了解设备的运行状况,从而提高生产效率。
好了,现在我们已经知道了OEE的重要性,那么接下来就要看看如何进行OEE分析和管理了。
我们要做的是收集数据。
这可是个技术活儿,可不是随便拍几张照片就能搞定的。
我们需要定期对设备进行检查,记录下设备的运行时间、故障时间等信息。
这些数据可是OEE分析的基础哦!接下来,我们要对这些数据进行整理。
把相同类型的设备放在一起,把相同的时间段也放在一起。
这样一来,我们就可以更清楚地看到设备的运行状况了。
如果有数据缺失或者不准确的地方,我们要及时进行调整和补充。
整理好数据后,我们就可以开始进行OEE分析了。
这里有几个关键指标:运转率、可用率和性能指标。
运转率是指设备实际运行时间与计划运行时间的比值;可用率是指设备在规定时间内正常运行的时间占总时间的比例;性能指标则是根据设备的性能要求制定的一些标准,比如设备的输出功率、产量等。
通过这三个指标,我们可以得出设备的综合效率。
我们还可以进一步分析设备的瓶颈在哪里,从而找到提高生产效率的方法。
比如,如果发现设备的某个部件经常故障,那我们就需要及时更换或者维修这个部件,以保证设备的正常运行。
在进行OEE分析的过程中,我们还要注意数据的准确性和可靠性。
毕竟,这些数据关系到我们的生产效率,可不能马虎大意。
所以,我们在收集数据、整理数据的过程中,一定要细心、耐心地去做。
我们要把OEE分析的结果运用到实际生产中去。
比如,我们可以根据OEE分析的结果,调整生产线的布局,优化设备的使用方式等。
这样一来,我们的生产效率就会得到显著提高啦!OEE分析和管理是一个系统性的工作,需要我们从多个方面入手。
IE改善与提高OEE、稼动率:提升生产效率和竞争力
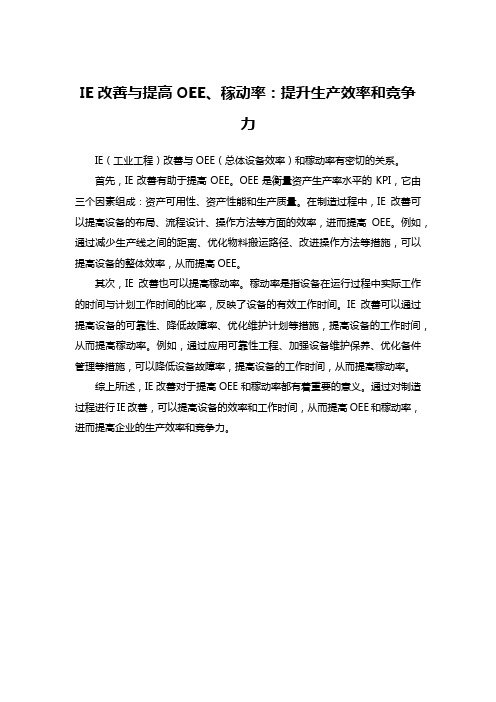
IE改善与提高OEE、稼动率:提升生产效率和竞争
力
IE(工业工程)改善与OEE(总体设备效率)和稼动率有密切的关系。
首先,IE改善有助于提高OEE。
OEE是衡量资产生产率水平的KPI,它由三个因素组成:资产可用性、资产性能和生产质量。
在制造过程中,IE改善可以提高设备的布局、流程设计、操作方法等方面的效率,进而提高OEE。
例如,通过减少生产线之间的距离、优化物料搬运路径、改进操作方法等措施,可以提高设备的整体效率,从而提高OEE。
其次,IE改善也可以提高稼动率。
稼动率是指设备在运行过程中实际工作的时间与计划工作时间的比率,反映了设备的有效工作时间。
IE改善可以通过提高设备的可靠性、降低故障率、优化维护计划等措施,提高设备的工作时间,从而提高稼动率。
例如,通过应用可靠性工程、加强设备维护保养、优化备件管理等措施,可以降低设备故障率,提高设备的工作时间,从而提高稼动率。
综上所述,IE改善对于提高OEE和稼动率都有着重要的意义。
通过对制造过程进行IE改善,可以提高设备的效率和工作时间,从而提高OEE和稼动率,进而提高企业的生产效率和竞争力。
WS-06 设备综合效率OEE

(#其他停机时间)
0
Hr
0.5
停机损失总时间
0.5
E.
开动时间(可用时间-停 机时间)
F.
时间稼动率(开动时间/ 可用时间)*100%(E/C)
7.25
Hr
94%
性能稼动率(速 度)
G.
生产数量(包含好件和坏 件)
425
H.
理论加工时间(完成加工 一件产品的时间)
1
J.
性能稼动率(生产数量* 理论加工时间/开动时间
98%
良品率(品质)
G.
生产数量(包含好件和坏 件)
425
H.
良品数量品率(良品数量/生产 数量*100%)
94%
设备综合效率OEE
K.
设备综合效率OEE(时间 稼动率*性能稼动率*良品
时间利用率
设备利用率
产品合格率
1#设备综合效 率
94%
98%
94%
86%
工厂/车间的设备综合效率 =(1#设备综合效率*产量+2#设备综合效率*产量+…+N#设备综合效率*产量)/总产量
“100%(完美)”、“85%(世界一流)”、“60%(一般)”和“40%(低水平)”这四个OEE分数档次已经成为行业基准。
设备综合效率OEE Overall Equipment Effectiveness
时间稼动率(开
动时间/可用时
A.
负荷时间(正常计划工作 时间,除过吃饭和休息)
8
Hr
B.
计划停机时间(无订单)
0.25
Hr
C.
可用时间
7.75
Hr
D.
停机时间损失
OEE设备综合效率
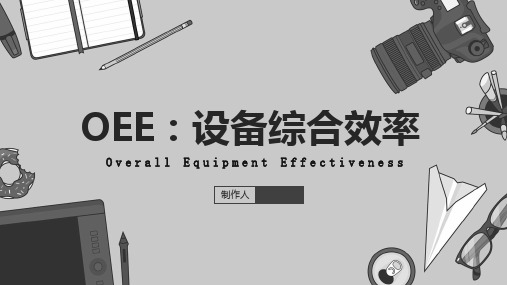
降低设备损失的目的:提高设备的综合使用率,保证设备不产出不良品,同时提高生产效率,要降低 设备的损失首先我们先来认识一下设备的六大损失。
OEE与六大损失
故障停机/损失 故障停机/损失是指故障停机造成时间损失和由于生产缺陷产品导致数量损失。因偶发故障造成的突然的、 显著的设备故障通常是明显的并易于纠正;而频繁的、或慢性的微小故障则经常被忽略或遗漏。由于偶发 性故障在整个损失中占较大比例,所以许多企业都投入了大量时间努力寻找避免这种故障,然而,要消除 这些偶发性故障是很困难的。所以,必须进行提高设备可靠度的研究,要使设备效率最大化,必须使故障 减小到零,因此,首先需要改变传统故障维修中认为故障是不可避免的观点。
质量指数(良品率)
质量指数 = 一次合格产品数 / 总 生产产品数
质量是一个比较明确的结果,合 格或者不合格。但是在计算合格 品数量时不同的公司可能会有不 同的计算方法。比如有的公司可 能用总体合格率,有的公司使用 一次通过率。其中的不同主要是 针对返工后合格的产品是否纳入 计算范围。 不过受到公认的还是 采用一次通过产品数量来计算。
质量指数(良品率)
质量指数 = 一次合格产品数 / 总 生产产品数
质量是一个比较明确的结果,合 格或者不合格。但是在计算合格 品数量时不同的公司可能会有不 同的计算方法。比如有的公司可 能用总体合格率,有的公司使用 一次通过率。其中的不同主要是 针对返工后合格的产品是否纳入 计算范围。 不过受到公认的还是 采用一次通过产品数量来计算。
设备稼动率英文缩写

设备稼动率英文缩写
设备稼动率的英文缩写是OEE,全称为Overall Equipment Effectiveness。
OEE是一个用于衡量设备运行效率的关键性能指标,它综合考虑了设备的开动率、性能率和质量率,能够全面评估设备在生产过程中的运行情况。
在制造业中,OEE被广泛应用于评估设备的生产效率和性能,帮助企业发现并解决生产过程中的瓶颈和问题,从而提高生产效率和降低生产成本。
OEE的计算公式为,OEE = 设备开动率× 设备性能率× 良品率。
通过对OEE的监控和分析,企业可以及时发现设备运行中的问题,采取相应的改进措施,提高设备稼动率,实现生产效率的持续提升。
OEE及嫁动率
OEEOEE是一个独立的测量工具,它用来表现实际的生产能力相对于理论产能的比率。
国际上对OEE的定义为:OEE是Overall Equipment Effectiveness(全局设备效率)的缩写,它由可用率(Availability time),表现性(Performance)以及质量指数(Quality)三个关键要素组成。
目录OEE的定义详细解释OEE计算实例OEE数据采集方法OEE计算实例设备综合效率(OEE)一、OEE的实质一般,每一个生产设备都有自己的最大理论产能,要实现这一产能必须保证没有任何干扰和质量损耗。
当然,实际生产中是不可能达到这一要求,由于许许多多的因素,车间设备存在着大量的失效: 例如除过设备的故障,调整以及设备的完全更换之外,当设备的表现非常低时,可能会影响生产率,产生次品,返工等。
二、详细解释OEE=可用率X 表现性 X质量指数。
其中:可用率(稼动率)=操作时间 / 计划工作时间它是用来考虑停工所带来的损失,包括引起计划生产发生停工的任何事件,例如设备故障,原料短缺以及生产方法的改变等。
表现性=(总产量/操作时间)/理想周期时间=(总产量 / 操作时间)/ 生产速率表现性考虑生产速度上的损失。
包括任何导致生产不能以最大速度运行的因素,例如设备的磨损,材料的不合格以及操作人员的失误等。
质量指数=良品/总产量质量指数考虑质量的损失,它用来反映没有满足质量要求的产品(包括返工的产品)。
利用OEE的一个最重要目的就是减少一般制造业所存在的六大损失:停机损失、换装调试损失、暂停机损失、减速损失、启动过程次品损失和生产正常运行时产生的次品损失。
下面表格是六大损失的说明及其与OEE的关系:三、OEE计算实例我们举一个例子来说明OEE的计算方法:设某设备某天工作时间为8h, 班前计划停机15min, 故障停机30min,设备调整25min, 产品的理论加工周期为0.6 min/件, 一天共加工产品450件, 有20件废品, 求这台设备的OEE。
oee设备综合效率目标值
oee设备综合效率目标值一、OEE设备综合效率的定义OEE(Overall Equipment Efficiency),即设备综合效率,是一种用于衡量设备运行效率的指标。
它综合考虑了设备的稼动率、性能效率和质量合格率三个方面,通过计算得出一个综合的效率值。
OEE的计算公式为:OEE = 稼动率× 性能效率× 质量合格率。
通过OEE指标的监控和分析,企业可以评估设备的运行状态和效率水平,为提高生产线的综合效率提供依据。
二、提高设备稼动率设备稼动率是指设备运行时间与总时间之比,反映了设备的利用率。
提高设备稼动率是提高设备综合效率的基础。
要提高设备稼动率,首先需要对设备进行定期维护保养,确保设备处于良好的工作状态。
其次,要合理安排生产计划,避免设备闲置或过度负荷运行。
此外,采用先进的设备监控系统,及时发现并解决设备故障,也是提高稼动率的关键。
三、优化设备性能效率设备性能效率是指设备在单位时间内完成工作量的能力。
提高设备性能效率可以通过多种方式实现。
首先,要对设备进行有效的培训和操作指导,提高操作人员的技能水平。
其次,要进行设备参数的优化调整,确保设备在最佳状态下运行。
另外,采用先进的自动化技术和设备改进措施,也能有效提高设备的性能效率。
四、提高产品质量合格率产品质量合格率是指产品合格数量与总产量之比,反映了产品质量的水平。
提高产品质量合格率可以通过加强质量管理和控制来实现。
首先,要建立完善的质量管理体系,包括从原材料采购到生产过程的全程质量控制。
其次,要加强对生产过程的监控和检测,及时发现并纠正质量问题。
此外,要进行持续的质量改进,通过分析和解决质量问题的根本原因,提高产品质量合格率。
五、综合考虑实现最优化要实现生产线的最优化,除了提高设备综合效率外,还需要综合考虑其他因素。
首先,要合理安排生产计划和调度,确保生产线的平衡运行。
其次,要进行供应链的优化管理,确保原材料和零部件的及时供应。
oee设备综合效率改善案例
oee设备综合效率改善案例
OEE(Overall Equipment Effectiveness),即设备综合效率,是TPM在表示设备该如何有效运作的一种衡量指标,其衡量目的在于设备及制程的改善。
为了提升OEE设备综合效率,可以采用以下改善案例:
某工厂生产车间的设备稼动率偏低,生产计划完成度不高。
经分析,设备故障停机时间较长,且设备调整时间过长,导致稼动率偏低。
对此,工厂采取了以下措施:
1. 加强设备维护:实施定期维护和检查,及时发现和解决设备问题,减少设备故障停机时间。
2. 优化生产流程:合理安排生产计划,减少设备调整时间,提高设备稼动率。
3. 加强员工培训:提高员工的设备操作技能和维护能力,减少因人为因素造成的设备故障。
通过以上措施,该工厂成功地提高了设备稼动率,进而提高了OEE设备综合效率,实现了生产效率的提升。
OEE(设备综合效率)分析及管理
19
5.合格品率
是用设备的生产精度反映设备的运行状况。合格品
率低,或是该设备不适合于该工序的生产,或是设
备经过较长时间的运行,造成设备精度劣化。
合格品率 = (生产产品数 - 不合格品) / 生产产品数 * 100%
20
6.完全有效生产率(TEEP)
1.TEEP=设备利用率*OEE
2.设备利用率=负荷时间/出勤时间 3.负荷时间=出勤时间-计划停机时间-非设备因素停 机时间(指:停水/电/气、等待物料与计划、等待上下工序
4
设备的6大损失
缺陷与返工
启动损失
机器故障
速度下降
停顿
调整与设置
5
6大损失的形象化
100 % 速度损失
生产能力
时间
启动
小停顿 和空转
质量 缺陷
故障
设置和 调整
停机
6
你不可能在设备故障停机时生产出产品
7
设置和调整占用了太多的时间
8
一个微小的问题就会造成设备的停机
9
设备运转过快容易造成故障
10
等所有非本设备因素造成的停机损失)。
21
思考:
设备OEE>100%是否成立?为什么?
22
23
7.OEE衡量的目的?
河水与暗礁的比喻
精益生产的目的是要降低库存(河水水位),指出产生生产停顿的潜在原因(暗 礁),清除之使企业能以更强的竞争力即更低水位运作。
通过使企业的库存强制减 少到某个既定目标,企业 可以降低水位,主动使暗 礁浮出水面,从而可以清 除礁石或降低暗礁高度
数量/ 分钟 设备A 设备B 设备C 设备D 设备E
产品数
分钟 投诉 受污染 不合标准 破损
- 1、下载文档前请自行甄别文档内容的完整性,平台不提供额外的编辑、内容补充、找答案等附加服务。
- 2、"仅部分预览"的文档,不可在线预览部分如存在完整性等问题,可反馈申请退款(可完整预览的文档不适用该条件!)。
- 3、如文档侵犯您的权益,请联系客服反馈,我们会尽快为您处理(人工客服工作时间:9:00-18:30)。
稼动率与设备总合效率
(O E E)分析
-CAL-FENGHAI-(2020YEAR-YICAI)_JINGBIAN
稼动率与设备综合效率分析
如果您被问到「我们部门的稼动率为90%,你们厂里是多少」,您可知道其所谓的稼动率定义为何90%这数字代表的是好是坏呢基本上稼动率有数种不同的定义,在此略加解释:
1、时间稼动率首先定义最大操作时间,指的是设备可用的最大时间,若设备本身为厂内自购,且可完全由厂内自主使用,则最大操作时间一般为日历时间;而负荷时间则为设备可稼动的时间,乃是最大操作时间扣除停机(Shutdown, SD)损失,停机损失乃是计画上的休止时间,如休假、教育训练、保养等。
而稼动时间则是负荷时间扣除停止时间,而停止时间包括批次转换及制程异常、设备异常停止及修复时间。
最大操作时间:设备可用的最大时间
负荷时间:最大操作时间扣除停机(Shutdown, SD)损失;这里的停机损失是计划是可预见的为客观实际的事实:如班前后会,保养、吃饭时间,日历时间或法定假日等。
停机(Shutdown, SD)损失:计画上的休止时间,如休假、教育训练、保养等
稼动时间:负荷时间扣除停止时间
停止时间:包括批次转换及制程异常、设备异常停止及修复时间。
由以上的定义,即可算出最常用的稼动率定义-设备稼动率(也称为时间稼动率),其公式为时间稼动率=稼动时间 / 负荷时间也可等于(操作时间/计划工作时间)
目的:减少停止时间!!!通过资源整合,管理优化,进行资源充分利用,降低成本,提高效率。
2、性能稼动率/实质稼动率/速度稼动率
时间稼动率并无法完全表现设备对生产的贡献程度;例如,相同的设备,相等的稼动时间,可能因效率的不同,而有不同的产能,此类效率降低的损失则称为性能损失。
在此定义速度稼动率如下:
速度稼动率=基准周期时间/ 实际周期时间其中,基准周期时间:设备原设计产出单位产量所需的时间。
实际周期时间:目前设备实际产出单位产量所需的时间。
并定义实质稼动率与性能稼动率如下:
实质稼动率=生产量 ×实际周期时间/稼动时间
性能稼动率=速度稼动率 ×实质稼动率
性能稼动时间则定义为:
性能稼动时间(表现指数)=稼动时间 ×性能稼动率=稼动时间-性能损失时间即表现指数:理想周期时间/(操作时间/总产量)=总产量*生产速率(1MIN/PCS)/操作时间
其中性能损失包括速度低落的损失与短暂停机的损失。
由以上定义可知,若性能稼动率变小,则可判定生产相关设备的效率降低。
3、价值稼动时间与设备综合效率
性能稼动时间表示设备产出产品的时间,但无法表示设备产出良率的好坏,因此定义「价值稼动时间」来表示真正能产出良品的有价值时间,其定义如下:
价值稼动时间=性能稼动时间 ×良品率而设备的有效使用程度则以「设备总合效率」来判定,其定义如下:
设备综合效率(OEE)=时间稼动率 ×性能稼动率 ×良品率(Overall Equipment Effectiveness)也等于理论加工周期*合格产量/符合时间=合格产品的理论加工总时间/负荷时间。
这就是实际产量与负荷时间内理论产量的比值。
例题:
设某设备每天工作8小时,计划班前停机10Min,故障停机30 Min,设备调整35 Min,产品理论加工周期(标准工时)1Nin/件,1天共加工400件,有20件废品求设备综合效率(OEE):时间稼动率(可用率)=8*60-10-30-35/(8*60-10)*100%=405/470=%
性能稼动率(表现指数)=400/405=%
量品率(质量指数)=(400-20)/400*100%=380/400=95%
OEE=%*%*95%=%
按OEE=合格产品的理论加工总时间/负荷时间=(400-20)*1/(8*60-10)*100%=%也可更方便得出OEE的结果,只是不能很清晰地分析出时间稼动率,性能稼动率和良率因素影响,做出最终的改善方案。