稼动率与设备总合效率(OEE)分析
生产稼动率与OEE
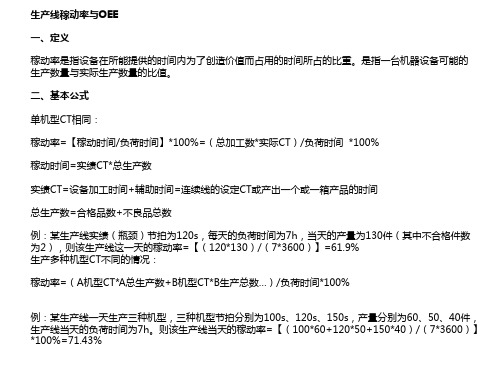
例:某生产线一天生产三种机型,三种机型节拍分别为100s、120s、150s,产量分别为60、50、40件, 生产线当天的负荷时间为7h。则该生产线当天的稼动率=【(100*60+120*50+150*40)/(7*3600)】 *100%=71.43%
三、OEE与稼动率的区别
OEE定义:OEE是Overall Equipment Effectiveness(全局设备效率)的缩写。一般,每一个生产设备都有 自己的理论产能,要实现这一理论产能必须保证没有任何干扰和质量损耗。OEE就是用来表现实际的生产能 力相对于理论产能的比率,它是一个独立的测量工具。
OEE计算实例:
设某设备某天工作时间为8H,班前计划停机10min,故障停机30 min,设备调整35 min,产品的理论加工 周期为1min/件,一天共加工产品400件,有20件废品,求这台设备的OEE。
根据上面可知: 计划运行时间=8*60-10=470(min) 实际运行时间=470-30-35=405(min) 时间利用率=405/470=0.86(86%) 性能利用率=400/405=0.98(98%) 良品率=(400-20)/400=0.95(95%)OEE=有效率*表现性*质量指数=80%
生产线稼动率与OEE
一、定义
稼动率是指设备在所能提供的时间内为了创造价值而占用的时间所占的比重。是指一台机器设备可能的 生产数量与实际生产数量的比值。
二、基本公式
单机型CT相同:
稼动率=【稼动时间/负荷时间】*100%=(总加工数*实际CT)/负荷时间 *100%
稼动时间=实绩CT*总生产数
实绩CT=设备加工时间+辅助时间=连续线的设定CT或产出一个或一箱产品的时间
OEE

C/T 总生产数
换线换模 机械故障 搬运
需求加工时间
良品率%
总不良数
量检刀具异常 材料异常
总和设备效率 %
质量异常处理
产品名称 :
项目 设备稼动率 %
总劳动时间 休息 教育训练
计画停止 计画停止 时间 净 劳动时间
换线换模 机械故障 搬运 量检刀具异常 材料异常 质量异常处理
数据定义– 瓶颈作业CT
可辨识的中小止 设备故障 设定及调整损失 模工具损失 起始暖车损失
速度减缓损失 惰速及中小止损失
制程不良损失
总和设备效率(OEE)损失
开会、打扫、休
应劳动 息、未计划生产
工时(出 勤班次/
日)
净劳动 工时
换线及故 障损失
可稼动 工时
作业性能 损失
品质
损失
OEE 损失
OEE 损失
有效 工时
OEE计算
OEE计算 案例
例3 :组立线采总作业时间(T/CT)方式生产,相关之生产数据如 下,请回答本组立线之 OEE% = ?
(总作业时间方式生产表示一台机停,不一定所有机器都 停,全员不一定都停,所以算个别的时间的加总(如休息、 停机、换模等))
T/CT = 8.13分;生产数= 95件(含不良品);不良数8件
• 良品率%= (((总生产数– 总不良数) /总生产数 )X 100 ) %
总和设备效率 (OEE)窗体
产品名称 :
项目 设备稼动率 %
总劳动时间
总 和 设 备 效 率 (OEE)
1234 5
项目
人员请假 其他
1234 5
休息 教育训练
中断时间 稼动 时间
计画停止
OEE设备总和效率.ppt

机台Tact time*Input
Total Time
SUM(A~I)
实际产出就是实际的Input,而理想产出为 Total Time – 停机时间
Performance:在相同時間内,設備實際產出數量與理論 上能夠產出數量的一種比較。
Quality:生産數量與符合客戶規格的產出數量的比較。
衡量一部設備的效率,不光是去看它的生産速度有多快,拼命 運轉,但是做出的都是不良品也都沒用,白白浪費成本。
所以OEE中的最後一個E是Effectiveness,而不是性能稼動率E 中的Efficiency。差別在於:
制程改善
D:品质异常 I:工程借机 G:换料 E:机台点检 F:停机5S
制造改善
J:待料 L:交接班 M:Wip过高 N:待Tray K:休息时间 O:其它问题
P
其它 P:缺料 Q:无排程
AUO OEE Loss Code統計
在做OEE分析之前我們需要定義OEE Loss標準Code。如果能夠 在機臺上直接就統計出這樣的數據是最好的。如不能直接統計,就需要 人員對此時間作記錄。以下為提供的統計格式。
AUO OEE的定义与介绍
解决损失及浪费的课题从哪里面来?我们就从OEE上着手。
OEE设备总合效率=时间稼动率X性能稼动率X良品率 =(负荷时间-停机时间)/负荷时间
X(理论C.TX投入数量)/(负荷时间-停机时间) X(投入数量-不良数量)/投入数量
AUO OEE的定义与介绍
AUO OEE的定义与介绍
Availability——時間稼動率 Performance efficiency——性能稼動率
Quality rate——合格品率
OEE焦點:它衡量的目的在於改善,而不是對人的評價。 OEE重點:掌握造成OEE低下的各類型損失,並加以改善。
最新OEE定义和计算方式

N
表示保全性的指标
① MTTR (Mean Time To Repair : 平均修理间距)
停止时间的合计
= 停止回数 (件数) =
ta + t
b +t c
+……………. tx
N × 100(%)
② 故障强动率 =
停止时间
实际时间
提升设备综合效率
设备稼动率
设备短暂停工零化 TPM改善活动 设备开动损失递减 换模调整损失递减 设备故障零化
敬 请 指 教
青蛙的故事
-生活启迪
从前,有一群青蛙组织了一场攀爬比赛 比赛的终点是: 一个非常高的铁塔的塔顶 一大群青蛙围著铁塔看比赛,给它们加油 ,比赛开 始了,老实说:
群蛙中没有谁相信这些小小的青蛙会到达塔顶,
他们都在议论: “这太难了!!它们肯定到不了塔顶!” “他们绝不可能成功的,塔太高了!”
减少等待 物料等待
车体等待
在制品等待 满载停止
提升 OEE
提高品质 提高良品率
返修率的低减 减少短暂停线 三现主义的想法 PM分析
教育训练 个别改善能力提高
保养技能训练 技能员技能的提升 RTC培训(制造、保全)
改善课题
小暂停管控
消除
超出管制
系统水准 TPM改善
工程不均衡 : 前后工程中由于别的因素引起的作业停止或
者担当设备后工程(设备)的生产数量或者目标 量已达成而停止情况的时间 其 它 : 由以上原因以外的原因引发的设备停止时间
案
例
某工厂实施8小时作业体制,其中中午休息1小时,上 班时间包括早会,检查,清扫等20分钟,上、下午期间
稼动率与设备总合效率(OEE)分析
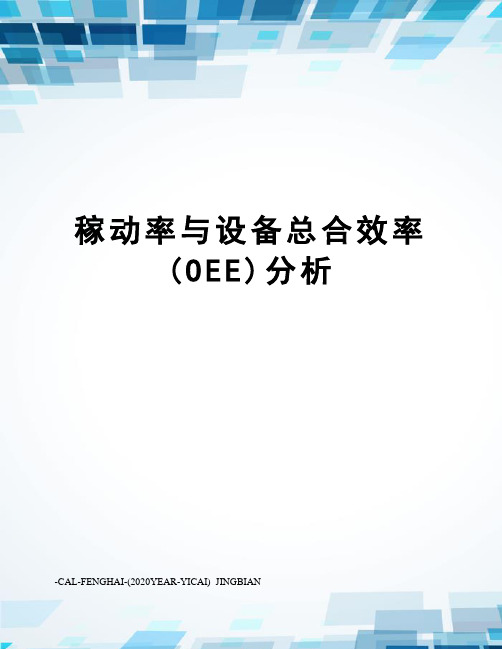
稼动率与设备总合效率(O E E)分析-CAL-FENGHAI-(2020YEAR-YICAI)_JINGBIAN稼动率与设备综合效率分析如果您被问到「我们部门的稼动率为90%,你们厂里是多少」,您可知道其所谓的稼动率定义为何90%这数字代表的是好是坏呢基本上稼动率有数种不同的定义,在此略加解释:1、时间稼动率首先定义最大操作时间,指的是设备可用的最大时间,若设备本身为厂内自购,且可完全由厂内自主使用,则最大操作时间一般为日历时间;而负荷时间则为设备可稼动的时间,乃是最大操作时间扣除停机(Shutdown, SD)损失,停机损失乃是计画上的休止时间,如休假、教育训练、保养等。
而稼动时间则是负荷时间扣除停止时间,而停止时间包括批次转换及制程异常、设备异常停止及修复时间。
最大操作时间:设备可用的最大时间负荷时间:最大操作时间扣除停机(Shutdown, SD)损失;这里的停机损失是计划是可预见的为客观实际的事实:如班前后会,保养、吃饭时间,日历时间或法定假日等。
停机(Shutdown, SD)损失:计画上的休止时间,如休假、教育训练、保养等稼动时间:负荷时间扣除停止时间停止时间:包括批次转换及制程异常、设备异常停止及修复时间。
由以上的定义,即可算出最常用的稼动率定义-设备稼动率(也称为时间稼动率),其公式为时间稼动率=稼动时间 / 负荷时间也可等于(操作时间/计划工作时间)目的:减少停止时间!!!通过资源整合,管理优化,进行资源充分利用,降低成本,提高效率。
2、性能稼动率/实质稼动率/速度稼动率时间稼动率并无法完全表现设备对生产的贡献程度;例如,相同的设备,相等的稼动时间,可能因效率的不同,而有不同的产能,此类效率降低的损失则称为性能损失。
在此定义速度稼动率如下:速度稼动率=基准周期时间/ 实际周期时间其中,基准周期时间:设备原设计产出单位产量所需的时间。
实际周期时间:目前设备实际产出单位产量所需的时间。
设备综合效率计算公式
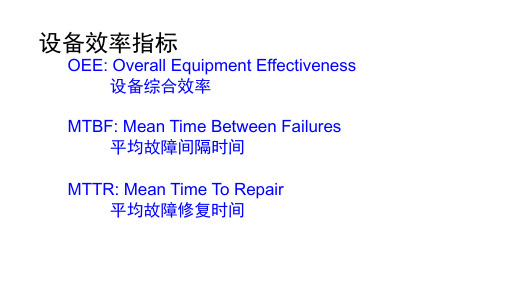
=87.3%×72.7%×95% =60.3%
设备效率指标—MTBF
MTBF(Mean Time Between Failures,平均故障间隔 时间)是பைடு நூலகம்来衡量本次故障发生与上次故障发生的间隔时 间长短指标. MTBF的数值越大,表明相对发生故障的频率就越低,则 被衡量对象的信赖性越高,相对寿命也越长. 整运转时间 MTBF = ×100% 停止次数
OEE答案
负荷时间-停机时间 = 时间稼动率= 负荷时间
460-70
460
×100% = 84.8%
理论周期时间×投入数 0.8×418 ×100% = 85.7% = 性能稼动率= 稼动时间 390
良品率=98%
OEE=时间稼动率×性能稼动率×良品率 =84.8%×85.7%×98% =71.2%
设备效率指标—MTTR
MTTR(Mean Time To Repair,平均故障修复时间)是 指故障后到修复好的平均时间.它是用来衡量一个系统容易 维护保养性的指标. MTTR数值越小,表明修复的时间越短,系统的易维护、 保养性程度越高. 故障修复时间总和 MTTR = ×100% 故障次数
设备效率指标—MTBF & MTTR
良品率是指投入的数量中良品数量所占的比率 良品数 投入数 - 不良数 ×100% ×100% = 良品率= 投入数 投入数
设备效率指标—OEE (1,2,3)
练习题
某工厂生产线一天工作时间是8H,加班3H,班前计划停机30min,故障停机 50min,更换产品型号设备调整30min,产品的理论加工周期时间为0.8min/件, 一天共加工产品200件,有10件废品,该生产线设备共有7台,其中最长的周期时 间为2min/件.求该生产线的OEE. 实际作业时间 =60*8min+60*3min=660min OEE= 时间稼动率 ×性能稼动率 ×良品率 时间稼动率 =(550min ÷630min) ×100%=87.3% 计划停机时间=30min 负荷时间=660min-30min=630min 停机损失时间 性能稼动率 =(2min/=50min+30min=80min 件×200件÷550min) ×100%=72.7% 稼动时间=630min-80min=550min 总投入数量=200件 良品率=95% 良品率=[ (200件-10件)/200件] ×100%=95%
设备综合效率(OEE)
<Overall Equipment Effectiveness>
OEE的概念
OEE即设备综合效率, OEE即设备综合效率,其本质就是设 即设备综合效率 备负荷时间内实际产量与理论产量的 比值 OEE=时间稼动率*性能稼动率* OEE=时间稼动率*性能稼动率*良品率 时间稼动率
OEE三个因素表述
时间稼动率反映了设备的时间利用情况 设备的故障, 度量了设备的故障,调整等项停机损失 性能稼动率反映了设备的性能发挥情况, 性能稼动率反映了设备的性能发挥情况, 短暂停机,空转速度降低 度量了设备短暂停机,空转速度降低等 项性能损失 合格品率则反映了设备的有效工作情况, 合格品率则反映了设备的有效工作情况, 度量了设备加工废品损失
谢谢各位 敬请指导!
�
*100%
良品率(Quality Ratc)
良品数 良品率%= * 100% 良品数+不良品数
设备综合效率计算公式
OEE=时间稼动率*性能稼动率*良品率 OEE 直接时间 * 负荷时间 理论周期时间*(良品数+不良品数) * 直接时间 良品数
良品数+不良品数
OEE的实质
如果追究OEE的本质内涵:
直接时间A 直接时间 时间稼动率= *100% 时间稼动率= % 负荷时间B 负荷时间
4.直接时间A=负荷时间B-中断时间(3) 直接时间A 时间稼动率= *100% 负荷时间B
性能稼动率(Performance Efficiency)
性能稼动率=速度稼动率*净动率*100% 理论周期时间*投入数 = 直接时间A 投入数=良品+不良品 理论周期时间=(CYCLE TIME)
OEE设备综合效率
降低设备损失的目的:提高设备的综合使用率,保证设备不产出不良品,同时提高生产效率,要降低 设备的损失首先我们先来认识一下设备的六大损失。
OEE与六大损失
故障停机/损失 故障停机/损失是指故障停机造成时间损失和由于生产缺陷产品导致数量损失。因偶发故障造成的突然的、 显著的设备故障通常是明显的并易于纠正;而频繁的、或慢性的微小故障则经常被忽略或遗漏。由于偶发 性故障在整个损失中占较大比例,所以许多企业都投入了大量时间努力寻找避免这种故障,然而,要消除 这些偶发性故障是很困难的。所以,必须进行提高设备可靠度的研究,要使设备效率最大化,必须使故障 减小到零,因此,首先需要改变传统故障维修中认为故障是不可避免的观点。
质量指数(良品率)
质量指数 = 一次合格产品数 / 总 生产产品数
质量是一个比较明确的结果,合 格或者不合格。但是在计算合格 品数量时不同的公司可能会有不 同的计算方法。比如有的公司可 能用总体合格率,有的公司使用 一次通过率。其中的不同主要是 针对返工后合格的产品是否纳入 计算范围。 不过受到公认的还是 采用一次通过产品数量来计算。
质量指数(良品率)
质量指数 = 一次合格产品数 / 总 生产产品数
质量是一个比较明确的结果,合 格或者不合格。但是在计算合格 品数量时不同的公司可能会有不 同的计算方法。比如有的公司可 能用总体合格率,有的公司使用 一次通过率。其中的不同主要是 针对返工后合格的产品是否纳入 计算范围。 不过受到公认的还是 采用一次通过产品数量来计算。
OEE分析与管理
OEE分析与管理OEE(Overall Equipment Effectiveness)是一种常用的生产效率指标,用于评估生产设备的效率和性能。
它可用于衡量设备的稼动率、质量合格率和产能损失,以便帮助企业发现和改善生产过程中的问题,提高生产效率和产品质量。
OEE的计算公式为:OEE=设备稼动率×质量合格率×产能利用率设备稼动率指的是设备真正工作时间与计划工作时间的比例,其计算公式为:设备稼动率=设备运行时间/设备计划工作时间质量合格率指的是产品在生产过程中达到质量标准的比例,其计算公式为:质量合格率=合格产品数/(合格产品数+不合格产品数)产能利用率指的是设备在生产过程中实际产能与理论最大产能的比例,其计算公式为:产能利用率=实际产量/理论全能通过OEE分析与管理,企业可以获得以下几个方面的好处:1.发现潜在问题:OEE分析可以帮助企业发现生产过程中的问题和瓶颈,例如设备故障、操作问题、物料供应延迟等。
通过及时发现并解决这些问题,可以避免生产中断和质量问题的发生。
2.提高设备利用率:OEE分析可以帮助企业识别设备非生产时间(例如停机、换模、调机等),并优化生产计划以减少这些时间。
这将提高设备的稼动率,降低生产成本,提高生产效率。
3.提高产品质量:OEE分析可以帮助企业识别生产中的质量问题,并采取相应措施进行改进。
提高质量合格率将减少废品和返工的数量,提高产品的完整性和可靠性。
4.优化生产计划:OEE分析可以帮助企业确定生产的瓶颈和瓶颈,以优化生产计划和资源调度。
通过合理调整生产顺序、提高关键设备的利用率等措施,可以实现更高的产量和更好的资源利用效率。
5.设定目标和监控绩效:OEE分析可以帮助企业设定合理的生产目标,并对实际绩效进行监控和评估。
通过与目标进行比较,可以识别绩效差距并寻找改进之处,确保生产过程保持良好状态。
综上所述,OEE分析与管理是一个重要的管理工具,可以帮助企业提高生产效率和产品质量,降低成本,实现可持续发展。
OEE及嫁动率
OEEOEE是一个独立的测量工具,它用来表现实际的生产能力相对于理论产能的比率。
国际上对OEE的定义为:OEE是Overall Equipment Effectiveness(全局设备效率)的缩写,它由可用率(Availability time),表现性(Performance)以及质量指数(Quality)三个关键要素组成。
目录OEE的定义详细解释OEE计算实例OEE数据采集方法OEE计算实例设备综合效率(OEE)一、OEE的实质一般,每一个生产设备都有自己的最大理论产能,要实现这一产能必须保证没有任何干扰和质量损耗。
当然,实际生产中是不可能达到这一要求,由于许许多多的因素,车间设备存在着大量的失效: 例如除过设备的故障,调整以及设备的完全更换之外,当设备的表现非常低时,可能会影响生产率,产生次品,返工等。
二、详细解释OEE=可用率X 表现性 X质量指数。
其中:可用率(稼动率)=操作时间 / 计划工作时间它是用来考虑停工所带来的损失,包括引起计划生产发生停工的任何事件,例如设备故障,原料短缺以及生产方法的改变等。
表现性=(总产量/操作时间)/理想周期时间=(总产量 / 操作时间)/ 生产速率表现性考虑生产速度上的损失。
包括任何导致生产不能以最大速度运行的因素,例如设备的磨损,材料的不合格以及操作人员的失误等。
质量指数=良品/总产量质量指数考虑质量的损失,它用来反映没有满足质量要求的产品(包括返工的产品)。
利用OEE的一个最重要目的就是减少一般制造业所存在的六大损失:停机损失、换装调试损失、暂停机损失、减速损失、启动过程次品损失和生产正常运行时产生的次品损失。
下面表格是六大损失的说明及其与OEE的关系:三、OEE计算实例我们举一个例子来说明OEE的计算方法:设某设备某天工作时间为8h, 班前计划停机15min, 故障停机30min,设备调整25min, 产品的理论加工周期为0.6 min/件, 一天共加工产品450件, 有20件废品, 求这台设备的OEE。
- 1、下载文档前请自行甄别文档内容的完整性,平台不提供额外的编辑、内容补充、找答案等附加服务。
- 2、"仅部分预览"的文档,不可在线预览部分如存在完整性等问题,可反馈申请退款(可完整预览的文档不适用该条件!)。
- 3、如文档侵犯您的权益,请联系客服反馈,我们会尽快为您处理(人工客服工作时间:9:00-18:30)。
稼动率与设备综合效率分析
如果您被问到「我们部门的稼动率为90%,你们厂里是多少?」,您可知道其所谓的稼动率定义为何?90%这数字代表的是好?是坏呢?基本上稼动率有数种不同的定义,在此略加解释:1、时间稼动率首先定义最大操作时间,指的是设备可用的最大时间,若设备本身为厂内自购,且可完全由厂内自主使用,则最大操作时间一般为日历时间;而负荷时间则为设备可稼动的时间,乃是最大操作时间扣除停机(Shutdown, SD)损失,停机损失乃是计画上的休止时间,如休假、教育训练、保养等。
而稼动时间则是负荷时间扣除停止时间,而停止时间包括批次转换及制程异常、设备异常停止及修复时间。
最大操作时间:设备可用的最大时间
负荷时间:最大操作时间扣除停机(Shutdown, SD)损失;这里的停机损失是计划是可预见的为客观实际的事实:如班前后会,保养、吃饭时间,日历时间或法定假日等。
停机(Shutdown, SD)损失:计画上的休止时间,如休假、教育训练、保养等
稼动时间:负荷时间扣除停止时间
停止时间:包括批次转换及制程异常、设备异常停止及修复时间。
由以上的定义,即可算出最常用的稼动率定义-设备稼动率(也称为时间稼动率),其公式为
时间稼动率=稼动时间/ 负荷时间也可等于(操作时间/计划工作时间)
目的:减少停止时间!!!通过资源整合,管理优化,进行资源充分利用,降低成本,提高效率。
2、性能稼动率/实质稼动率/速度稼动率
时间稼动率并无法完全表现设备对生产的贡献程度;例如,相同的设备,相等的稼动时间,可能因效率的不同,而有不同的产能,此类效率降低的损失则称为性能损失。
在此定义速度稼动率如下:
速度稼动率=基准周期时间/ 实际周期时间其中,基准周期时间:设备原设计产出单位产量所需的时间。
实际周期时间:目前设备实际产出单位产量所需的时间。
并定义实质稼动率与性能稼动率如下:
实质稼动率=生产量×实际周期时间/稼动时间
性能稼动率=速度稼动率×实质稼动率
性能稼动时间则定义为:
性能稼动时间(表现指数)=稼动时间×性能稼动率=稼动时间-性能损失时间即表现指数:理想周期时间/(操作时间/总产量)=总产量*生产速率(1MIN/PCS)/操作时间
其中性能损失包括速度低落的损失与短暂停机的损失。
由以上定义可知,若性能稼动率变小,则可判定生产相关设备的效率降低。
3、价值稼动时间与设备综合效率
性能稼动时间表示设备产出产品的时间,但无法表示设备产出良率的好坏,因此定义「价值稼动时间」来表示真正能产出良品的有价值时间,其定义如下:
价值稼动时间=性能稼动时间×良品率而设备的有效使用程度则以「设备总合效率」来判定,其定义如下:
设备综合效率(OEE)=时间稼动率×性能稼动率×良品率(Overall Equipment Effectiveness)也等于理论加工周期*合格产量/符合时间=合格产品的理论加工总时间/负荷时间。
这就是实际产量与负荷时间内理论产量的比值。
例题:
设某设备每天工作8小时,计划班前停机10Min,故障停机30 Min,设备调整35 Min,产品理论加工周期(标准工时)1Nin/件,1天共加工400件,有20件废品求设备综合效率(OEE):时间稼动率(可用率)=8*60-10-30-35/(8*60-10)*100%=405/470=86.17% 性能稼动率(表现指数)=400/405=98.76%
量品率(质量指数)=(400-20)/400*100%=380/400=95%
OEE=86.17%*98.76%*95%=80.85%
按OEE=合格产品的理论加工总时间/负荷时间=(400-20)*1/(8*60-10)*100%=80.85%也可更方便得出OEE的结果,只是不能很清晰地分析出时间稼动率,性能稼动率和良率因素影响,做出最终的改善方案。