稼动率分析与改善
设备稼动率提升方案

设备稼动率提升方案设备稼动率提升方案一、原因分析设备稼动率指设备在一定时间内处于运行状态的时间与总时间的比值,是衡量设备利用率高低的重要指标。
提升设备稼动率可以有效提高生产效率和降低生产成本。
分析设备稼动率低的原因主要包括以下几个方面:1.1 设备故障率高:设备故障率高会导致设备频繁停机,影响设备连续运转的时间。
1.2 停工时间长:可能是由于维修、保养等原因,导致设备长时间停工,无法正常运行。
1.3 换线时间长:生产线上产品切换时,如果换线时间长,会严重影响设备稼动率。
1.4 人为操作不当:操作人员技术水平低或操作不规范可能导致设备异常停机。
二、提升设备稼动率的方案2.1 加强设备维护保养:定期进行设备的维护和保养工作,对设备进行检查、清洁和润滑,及时更换老化部件,以减少设备故障率和延长设备的使用寿命。
2.2 改进维修方案:建立完善的维修方案和紧急维修预案,提前准备好备品备件,及时响应设备故障,缩短停机时间。
2.3 引入设备远程监控系统:通过设备远程监控系统,可以实时监测设备的运行情况,及时发现异常,减少停机时间。
2.4 提升操作人员技术水平:加强操作人员的培训和技术交流,提高操作人员的技术水平和操作规范性,减少人为因素对设备稼动率的影响。
2.5 优化换线方案:通过优化产品换线方案,减少换线时间,提高生产线的运转效率。
2.6 加强设备整体规划:合理安排设备的布局和运作方式,减少设备之间的干扰,提高设备的整体稼动率。
2.7 进行设备升级改造:对老旧设备进行技术改造和升级,提高设备的稳定性和生产能力。
2.8 建立绩效评估体系:建立设备稼动率的考核指标和绩效评估体系,通过考核结果对设备稼动率低的原因进行深入分析,找出问题的根源并加以解决。
三、实施方案3.1 制定详细的实施计划:明确实施方案的目标、内容、计划和责任人,确保方案的顺利执行。
3.2 逐步推进:根据实际情况,分阶段逐步推进设备稼动率提升方案的实施,避免一次性过大改变导致生产中断。
自动化设备的稼动率与可动率

自动化设备的稼动率与可动率引言概述:自动化设备在现代工业生产中扮演着重要的角色,其稼动率和可动率是衡量设备运行效率和可靠性的重要指标。
稼动率指设备实际运行时间与总运行时间的比值,可动率则是指设备在规定时间内能够正常运行的概率。
本文将深入探讨自动化设备的稼动率与可动率,分析影响因素并提出提高稼动率和可动率的方法。
一、稼动率的影响因素1.1 设备故障率:设备故障率高会导致设备停机时间增加,从而降低稼动率。
1.2 维护保养:定期维护保养能够减少设备故障率,提高稼动率。
1.3 操作人员技能:操作人员技能和操作规范对设备稼动率有着直接影响。
二、可动率的计算方法2.1 可动率=设备正常运行时间/总运行时间,通常以百分比表示。
2.2 可动率的计算需要考虑设备的故障时间、维护时间和停机时间等因素。
2.3 可动率可以通过实际运行数据进行统计分析,以评估设备的运行状况。
三、提高稼动率的方法3.1 引入预防性维护:通过定期检查和保养,提前发现设备问题并进行修复,减少设备故障率。
3.2 持续改进:定期对设备运行数据进行分析,发现问题并及时改进,提高设备稼动率。
3.3 培训操作人员:提高操作人员的技能水平,让其能够熟练操作设备,减少操作失误导致的停机时间。
四、提高可动率的方法4.1 设备升级改造:对老化设备进行升级改造,提高设备的稳定性和可靠性。
4.2 定期维护保养:定期进行设备维护保养,减少设备故障率,提高可动率。
4.3 实施预防性维护计划:通过预防性维护计划,提前发现设备问题并进行修复,减少设备故障时间。
五、结论通过对自动化设备的稼动率与可动率进行深入分析,我们可以发现影响因素和改进方法,提高设备运行效率和可靠性。
在实际生产中,企业可以根据具体情况采取相应措施,不断优化设备管理,提高生产效率和竞争力。
设备稼动率提升方案
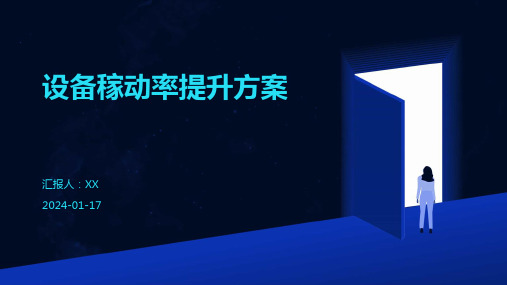
加强员工培训,提高员工对设备的操作和维护技能, 减少人为因素造成的停机时间。
关键成功因素
1 2
完善的设备管理制度
建立完善的设备管理制度,明确设备管理流程和 责任,确保设备的正常运行和维护。
专业的维护团队
组建专业的设备维护团队,具备丰富的设备维护 经验和技能,能够快速响应并解决设备故障。
引入先进技术
引进先进的设备技术和管 理经验,提高设备的自动 化、智能化水平,减少人 工干预,提高生产效率。
设备结构改造
设备结构简化
对设备结构进行简化和优化,降 低设备复杂度和维护难度,提高
设备运行稳定性。
设备模块化设计
采用模块化设计理念,将设备划分 为多个独立的功能模块,方便维修 和更换部件,提高设备可维护性。
02
目标设定
设定明确的提升目标,如提高设备稼动率至95%以上,降低故障率至
1%以下等,确保改进工作有明确的方向和目标。
03
跨部门协作
加强生产、维修、采购等部门之间的沟通与协作,共同推进设备稼动率
的提升工作。
08
总结与展望
项目成果总结回顾
设备稼动率提升
通过实施一系列优化措施,设备稼动率得到了显著提升,生产效率和产能得到了有效改善 。
降低设备故障率
加强设备维护和保养,降低设备故障率,提高设备运行稳定性。
提高生产效率
通过提升设备稼动率,提高生产效率,降低生产成本。
提升计划制定
设备维护计划
制定定期的设备维护计划,包括日常检查、定期保养 和维修等,确保设备处于良好状态。
设备升级计划
根据设备状况和生产需求,制定设备升级计划,包括 硬件更新和软件升级等,提高设备运行效率。
IE改善与提高OEE、稼动率:提升生产效率和竞争力
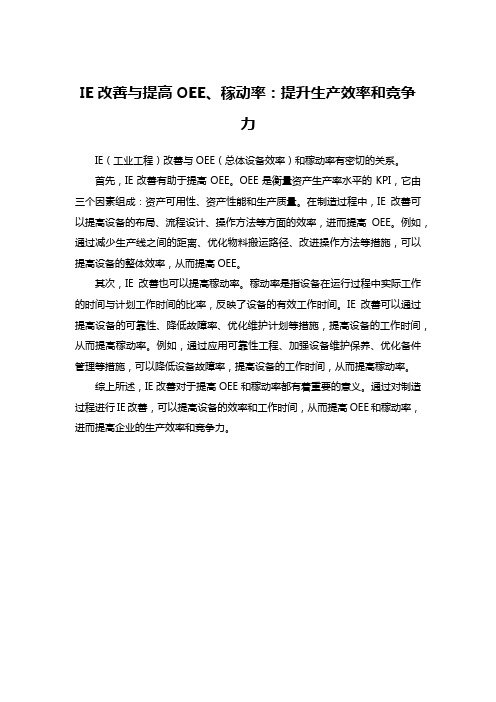
IE改善与提高OEE、稼动率:提升生产效率和竞争
力
IE(工业工程)改善与OEE(总体设备效率)和稼动率有密切的关系。
首先,IE改善有助于提高OEE。
OEE是衡量资产生产率水平的KPI,它由三个因素组成:资产可用性、资产性能和生产质量。
在制造过程中,IE改善可以提高设备的布局、流程设计、操作方法等方面的效率,进而提高OEE。
例如,通过减少生产线之间的距离、优化物料搬运路径、改进操作方法等措施,可以提高设备的整体效率,从而提高OEE。
其次,IE改善也可以提高稼动率。
稼动率是指设备在运行过程中实际工作的时间与计划工作时间的比率,反映了设备的有效工作时间。
IE改善可以通过提高设备的可靠性、降低故障率、优化维护计划等措施,提高设备的工作时间,从而提高稼动率。
例如,通过应用可靠性工程、加强设备维护保养、优化备件管理等措施,可以降低设备故障率,提高设备的工作时间,从而提高稼动率。
综上所述,IE改善对于提高OEE和稼动率都有着重要的意义。
通过对制造过程进行IE改善,可以提高设备的效率和工作时间,从而提高OEE和稼动率,进而提高企业的生产效率和竞争力。
如何提升综合设备稼动率
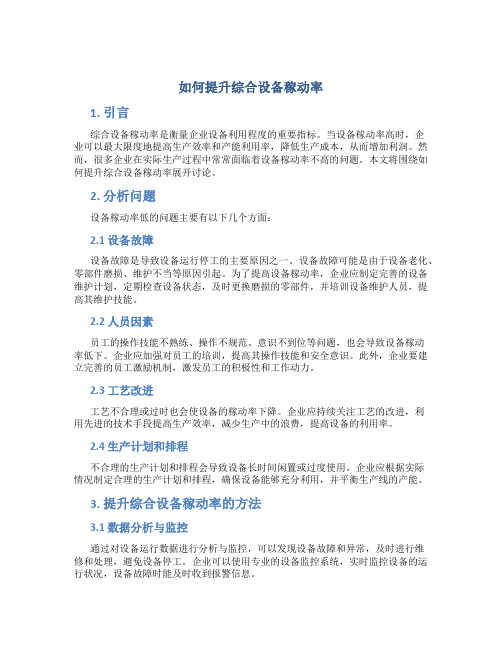
如何提升综合设备稼动率1. 引言综合设备稼动率是衡量企业设备利用程度的重要指标。
当设备稼动率高时,企业可以最大限度地提高生产效率和产能利用率,降低生产成本,从而增加利润。
然而,很多企业在实际生产过程中常常面临着设备稼动率不高的问题。
本文将围绕如何提升综合设备稼动率展开讨论。
2. 分析问题设备稼动率低的问题主要有以下几个方面:2.1 设备故障设备故障是导致设备运行停工的主要原因之一。
设备故障可能是由于设备老化、零部件磨损、维护不当等原因引起。
为了提高设备稼动率,企业应制定完善的设备维护计划,定期检查设备状态,及时更换磨损的零部件,并培训设备维护人员,提高其维护技能。
2.2 人员因素员工的操作技能不熟练、操作不规范、意识不到位等问题,也会导致设备稼动率低下。
企业应加强对员工的培训,提高其操作技能和安全意识。
此外,企业要建立完善的员工激励机制,激发员工的积极性和工作动力。
2.3 工艺改进工艺不合理或过时也会使设备的稼动率下降。
企业应持续关注工艺的改进,利用先进的技术手段提高生产效率,减少生产中的浪费,提高设备的利用率。
2.4 生产计划和排程不合理的生产计划和排程会导致设备长时间闲置或过度使用。
企业应根据实际情况制定合理的生产计划和排程,确保设备能够充分利用,并平衡生产线的产能。
3. 提升综合设备稼动率的方法3.1 数据分析与监控通过对设备运行数据进行分析与监控,可以发现设备故障和异常,及时进行维修和处理,避免设备停工。
企业可以使用专业的设备监控系统,实时监控设备的运行状况,设备故障时能及时收到报警信息。
3.2 预防性维护预防性维护是提高设备稼动率的有效方法之一。
企业可以制定定期的设备维护计划,通过对设备的定期检查、润滑、更换易损件等维护措施,预防设备故障的发生,确保设备长时间稳定运行。
3.3 培训与提升员工技能加强对员工的培训,提高其操作技能和安全意识,有助于降低设备事故的发生率,并提高设备稼动率。
企业可以定期开展培训课程和技能比赛,激发员工的学习热情和工作积极性。
设备稼动率提升方案连续生产稼动率的提升
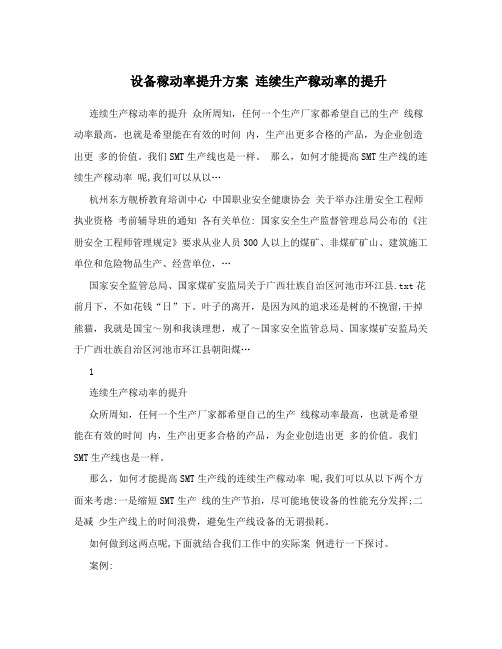
设备稼动率提升方案连续生产稼动率的提升连续生产稼动率的提升众所周知,任何一个生产厂家都希望自己的生产线稼动率最高,也就是希望能在有效的时间内,生产出更多合格的产品,为企业创造出更多的价值。
我们SMT生产线也是一样。
那么,如何才能提高SMT生产线的连续生产稼动率呢,我们可以从以…杭州东方舰桥教育培训中心中国职业安全健康协会关于举办注册安全工程师执业资格考前辅导班的通知各有关单位: 国家安全生产监督管理总局公布的《注册安全工程师管理规定》要求从业人员300人以上的煤矿、非煤矿矿山、建筑施工单位和危险物品生产、经营单位,…国家安全监管总局、国家煤矿安监局关于广西壮族自治区河池市环江县.txt花前月下,不如花钱“日”下。
叶子的离开,是因为风的追求还是树的不挽留,干掉熊猫,我就是国宝~别和我谈理想,戒了~国家安全监管总局、国家煤矿安监局关于广西壮族自治区河池市环江县朝阳煤…1连续生产稼动率的提升众所周知,任何一个生产厂家都希望自己的生产线稼动率最高,也就是希望能在有效的时间内,生产出更多合格的产品,为企业创造出更多的价值。
我们SMT生产线也是一样。
那么,如何才能提高SMT生产线的连续生产稼动率呢,我们可以从以下两个方面来考虑:一是缩短SMT生产线的生产节拍,尽可能地使设备的性能充分发挥;二是减少生产线上的时间浪费,避免生产线设备的无谓损耗。
如何做到这两点呢,下面就结合我们工作中的实际案例进行一下探讨。
案例:松下电器机电(中国)有限公司FA事业所CSE部提供诊断咨询服务的一家客户生产线现状及目标要求:1、生产线配置如图1所示;2、产品信息和料架配置;2生产机种:COGNAC;贴装点数:634点;PCB为两拼板。
两台贴片机料架使用情况如图2所示。
3、各个工位的生产节拍如图3所示;4、每天勤务时间规定如图4所示;5、客户目前的生产节拍和勤务时间:每天最大可能产能是: (60×24-20)×60/43=1981块板(PCS)其中,每天规定的停工时间为20分钟; 每块板的加工时间为43秒。
设备稼动率损失改善研修报告
设备稼动率损失改善研修报告设备稼动率损失改善研修报告1. 背景•设备稼动率的损失对企业生产效率产生了巨大影响•为了提高设备稼动率,进行了研修措施的制定和实施2. 目的•提高设备稼动率,减少产品生产损失•优化生产流程,提升生产效率3. 研修内容设备维护•定期维护设备,保持设备的良好状态•加强设备检修,及时发现并解决设备故障操作培训•对操作人员进行培训,提高其操作技能和注意事项的掌握•指导操作人员正确使用设备,避免操作失误信息共享与沟通•加强部门之间的信息共享与沟通,及时传递设备异常情况•设立设备运行情况反馈机制,及时了解并处理设备问题数据分析与优化•对设备运行数据进行实时监测和分析•根据数据结果进行优化,找出设备稼动率损失的主要原因并改进4. 研修效果评估•设备稼动率有明显的改善,产品生产损失大幅减少•生产效率提高,单位时间内的产品产量增加•设备维护成本和人力成本也得到一定的控制5. 结论通过设备稼动率损失的改善研修,能够有效提高企业生产效率和产品质量,减少资源浪费和损失。
研修内容的有效实施和研修效果的评估是持续改进的关键。
6. 推广与应用•根据此次研修的经验和效果,可以将相关的研修方案推广到其他设备和生产线上•通过分享研修成果和经验,促进其他企业也进行设备稼动率损失改善研修7. 持续优化与改进•针对此次研修的效果评估结果,进一步分析和识别可能存在的问题和改进空间•持续跟进设备的运行情况,及时发现并解决新的问题•推动设备管理和维护工作的标准化和规范化8. 参考文献•文献1:设备稼动率的重要性及改善方法,XX杂志,年份,卷号,页码•文献2:生产效率提升的关键因素分析,XX报告,年份,报告编号9. 附录•设备稼动率改善方案•研修培训计划•研修效果评估报告表格以上是对设备稼动率损失改善研修的简要报告,其中包含了背景、目的、研修内容、研修效果评估、结论等主要内容。
通过此次研修的实施,企业能够提高设备稼动率,优化生产流程,提高生产效率,同时也减少了产品生产损失和成本支出。
机器稼动率
陈厂长:「本厂生产的瓶颈在于800吨一号机,以目前M厂的需求,每周须加四天的小夜班外,尚须假日加班,才能按时交货。
K 厂上班时间每天是505分钟,其中包括用餐及休息合计1小时,而在实际勤务的445分钟内,还包括朝会及检查、清扫等20分钟,因此生产线实际稼动的负荷时间为425分。
且800吨一号机的理论周期时间为0.8分钟,因此在正常稼动时间内,每天应该有531个产出,但实际上却只有310个,经实际测得周期时间为1.1分钟,而每天变换工程及故障停机时间平均约70分钟,其它尚有各种极短时间的设备停止稼动,每天约10次以上。
」品管课张课长:「还好800吨一号机的制品品质水准都能维持在不良率2%,否则纵使全力生产,也只是徒费成本而已。
」根据以上资料,请回答下列问题:K厂之800吨一号机其设备总合率为多少?为了提高设备总合效率,应朝那些方面改善较具成效?如果M厂每日需求量为490个,设备总合效率至少应提升至多少,才不必实施加班?设备总合效率之计算(请读者自行计算)假设:A:一班之实勤时间:B:一班之计画休止时间:C:一班之负荷时间=A一B:D:一班之停止损失时间:E:一班之稼动时间=C一DG:一班之生产量:H:良品率:1:理论周期时间:J:实际周期时间:即:F:实际加工时间=J×GEIT:时间稼动率:=-×100%M:速度稼动率=-×l00%:C FJN:纯稼动率=-×l00%EL:性能稼动率=M ×N ×100设备综合效率=T ×L ×H ×100设备总合效率之计算参考解答A:一班之实勤时间= 505B:一班之计画休止时间=80C:一班之负荷时间=A一B =(505一80)=425D:一班之停止损失时间=70E:一班之稼动时间=C一D =355G:一班之生产量=310H:良品率=98%1:理论周期时间=0.8J:实际周期时间=1.1即:F:实加工时间= J ×G =1.1 ×310 = 341E 355T:时间稼动率=-×100%= -×l00%=83.5%C 425I 0.8M:速度稼动率= -×100%=-×100%= 72.7%J 1.1 F341N:纯稼动率= -= 100%= -×100%= 96.05%E355L:性能稼动率=M ×N ×100 =72.7% ×96.05%×100 =69.8%设备总合效率=T ×L ×H ×100 =83.5%×69.8%×98%×100 =57.1%4.运用与分析经计算出设备总合效率后,即可依其计算值加以解析,以寻找出提高设备总合效率最具成效的方法。
自动化设备的稼动率与可动率
自动化设备的稼动率与可动率稼动率和可动率是评估自动化设备运行效率和可靠性的重要指标。
稼动率指设备在一定时间内实际运行时间与总运行时间的比例,可动率指设备在一定时间内正常运行时间与总运行时间的比例。
本文将详细介绍自动化设备的稼动率和可动率的定义、计算方法以及如何提高这两个指标。
1. 稼动率的定义和计算方法稼动率是指设备在一定时间内实际运行时间与总运行时间的比例,用于衡量设备的运行效率。
稼动率的计算公式如下:稼动率 = (设备实际运行时间 / 总运行时间) × 100%其中,设备实际运行时间是指设备在生产过程中真正工作的时间,不包括停机、故障和维护等非工作时间;总运行时间是指设备在一定时间内应该运行的总时间,一般为24小时。
2. 可动率的定义和计算方法可动率是指设备在一定时间内正常运行时间与总运行时间的比例,用于衡量设备的可靠性。
可动率的计算公式如下:可动率 = (设备正常运行时间 / 总运行时间) × 100%其中,设备正常运行时间是指设备在一定时间内没有发生故障和停机的时间;总运行时间同样是指设备在一定时间内应该运行的总时间。
3. 如何提高稼动率和可动率3.1 定期维护保养定期维护保养是保证设备正常运行和减少故障发生的关键措施。
通过定期检查设备的各个部件,及时发现并修复潜在故障,可以有效提高设备的可动率。
3.2 增加设备的自动化程度增加设备的自动化程度可以减少人为操作的干预,降低人为操作错误的发生概率,提高设备的稼动率和可动率。
例如,引入自动化控制系统、自动化传感器等技术,可以实现设备的自动开关、自动调节等功能。
3.3 增加备件库存合理增加备件库存可以缩短设备故障修复时间,提高设备的可动率。
在设备故障发生时,能够及时更换故障部件,减少停机时间,保证设备的正常运行。
3.4 培训操作人员合格的操作人员能够熟练掌握设备的操作技能,减少操作错误的发生,提高设备的稼动率和可动率。
因此,定期对操作人员进行培训和考核非常重要。
年度稼动率总结(3篇)
第1篇一、引言稼动率,即设备稼动率,是衡量企业生产设备运行效率的重要指标。
它反映了设备在一定时间内的实际运行时间与理论运行时间的比值。
对于企业而言,提高稼动率意味着更高的生产效率、更低的成本和更优的市场竞争力。
本报告将总结过去一年的稼动率情况,分析原因,并提出改进措施。
二、稼动率概述1. 定义稼动率是指在一定时间内,设备实际运行时间与理论运行时间的比值。
计算公式为:稼动率 = 实际运行时间 / 理论运行时间× 100%2. 影响因素影响稼动率的因素有很多,主要包括以下几个方面:(1)设备维护:设备维护不及时、维护质量不高,会导致设备故障率上升,从而降低稼动率。
(2)生产计划:生产计划不合理,会导致设备闲置或过度使用,影响稼动率。
(3)人员操作:操作人员技能水平不高、操作不规范,容易导致设备故障,降低稼动率。
(4)原材料供应:原材料供应不稳定、质量不合格,会影响生产进度,降低稼动率。
(5)市场需求:市场需求波动较大,导致生产计划调整频繁,影响稼动率。
三、年度稼动率分析1. 总体情况在过去的一年里,我国企业稼动率总体呈现以下特点:(1)稼动率水平有所提高:与上一年度相比,企业稼动率平均水平有所上升。
(2)行业间差异明显:不同行业稼动率水平存在较大差异,制造业、电子行业等高技术产业稼动率较高,而传统行业稼动率较低。
(3)区域分布不均衡:东部沿海地区企业稼动率普遍较高,中西部地区企业稼动率相对较低。
2. 具体分析(1)设备维护方面在过去的一年里,企业对设备维护的重视程度有所提高,设备故障率有所下降,但仍有部分企业设备维护工作不到位,导致稼动率降低。
(2)生产计划方面部分企业生产计划不合理,导致设备闲置或过度使用,影响稼动率。
此外,市场需求波动较大,导致生产计划调整频繁,对稼动率产生一定影响。
(3)人员操作方面企业对操作人员的培训力度有所加强,操作人员技能水平有所提高,但仍有个别企业操作人员技能水平不高,导致设备故障,影响稼动率。
- 1、下载文档前请自行甄别文档内容的完整性,平台不提供额外的编辑、内容补充、找答案等附加服务。
- 2、"仅部分预览"的文档,不可在线预览部分如存在完整性等问题,可反馈申请退款(可完整预览的文档不适用该条件!)。
- 3、如文档侵犯您的权益,请联系客服反馈,我们会尽快为您处理(人工客服工作时间:9:00-18:30)。
三稼动率分析与改善从综合效率的计算公式(4-8)可以看出,要提升效率,可以从提升作业能率和提升稼动率入手。
首先来分析如何提升稼动率。
从表4-1中可以看出,提升稼动率,就是要减少损失时间,而损失时间又由除外时间与异常时间组成。
基中,除外时间只只能尽量缩短,但往往是必不可少的,因此提升稼动率的主要着眼点即为异常时间的降低。
1异常时间的种类拨所谓的异常时间(或称异常工时),是指造成制造部门停工或生产进度延迟的情形。
由此而产生的时间浪费。
由表面膜势得知,异常时间一般包括:①计划异常因生产计划临时变更或安排失误等导致的异常。
②物料异常因物料供应不及时(断料)、物料品质问题等导致的异常。
(3)设备异常因设备、工装不足或故障等原因而导致的异常。
(4)品质异常因制程中出现了品质问题而导致的异常,也称制程异常。
(5)机种异常因产品设计或其他技术性问题而导致的异常,也称产品异常或技术异常。
(6)水电异常因水、气、电等导致的异常。
2、异常的处理流程(1)异常发生时,发生部门的制造主管应立即与生技单位或相关责任单位联络,共同研拟对策加以处理。
(2)一般应先采取应急对策,并加以执行,以尽快恢复生产,降低异常时间的影响。
(3)在异常处理同时或异常排除之后,由制造部门填具生产异常报告单(如表4-7),并转责任单位。
(4)责任单位填写异常处理之根本对策,以防止异常重复发生。
(5)制造单位、责任单位依据该单作后续追踪工作、确认是否得到改善。
(6)财务部门依该异常单作为制造费用统计之凭证,并作为向厂商索赔之依据。
(7)生管部门依异常状况作为生产进度管制控制点,并作为生产计划调度之参考。
3、异常工时计算规定(1)当所发生的异常,导致生产现场部分或全部人员完全停工等待时,异常工时之影响以100%计算。
(2)当所发生的异常,导致生产现场需增加人力投入,采取临时应急对策处理该异常时,异常工时之影响以实际增加投入的工时为准。
(3)当所发生之异常,导致生产现场作业速度放慢(可能同时也增加人力投入)时,异常工时之影响度以实际影响比例计算。
(4)异常工时损失不足10分钟时,只作口头报告或填入“生产日报表”,可以不另行填具“生产异常报告单”。
(二)稼动率分析1、工时利用率分析投入的人员工时之稼动率,又称为工时利用率,应定期检讨、分析,原则上每周、每月、每季、每年都应分析比较。
分析时可利用层别图、柏拉图等方式。
案例:某企业有250名员工,某周投入总工时16500小时,该周异常工时状况如表4-8。
经过上述的分析以后,可以得出结论:要提高稼动率,应以材料异常与品质异常的预防为重点,要从改善采购部门及品管部门的工作品质、方法和流程着手。
2、设备稼动率分析对设备时间的有效利用率,即设备稼动率的分析,有利于提高稼动率,从而降低制造成本,提升产量与交期。
分析仍可采用层别图与柏拉图。
当然,单纯分析设备的稼动率时,其异常的时间分类与人员工时损失之分类略有不同。
一般设备之异常分类有:(1)指令停机因订单不饱满或政策性需要而由上级下达停机之指令的时间。
(2)换模换料因产品型号、规格等变化而更换材料或工模夹具时的停机时间。
(3)设备故障因设备损坏而停机的时间。
(4)设备保养因设备运作需要而安排的必要之保养检修时间。
(5)模具故障因工模夹具的异常而导致设备停机的时间。
(6)品质异常因品质问题未能及时解决,造成设备停机的时间。
(7)其他其他原因导致的停机时间。
设备稼动率的计算一般有两种,分别称为含指令停机的稼动率与不含指令停机的稼动率。
(1)含指令停机的稼动率= 所有停机时间*100%设备理论稼动时间(2)(2)不含指令停机的稼动率=不含指令停机时间*100%设备理论稼动时间-指令停机时间其中设备理论稼动时间= 设备每天理想稼动时间(24小时)*计算周期(天数)*设备数量(三)异常时间的责任归属责任处理规定:(1)公司内部责任单位所致之异常,列入该部门工作考核内容、责任人员并依据公司规定处理。
(2)供应厂商责任除考核内部相关部门(采购、品管)外,列入厂商评鉴。
(3)必要时向厂商责任除考核内部相关部门(如采购、品管)外,列入厂商评鉴。
(4)必要时向厂商索赔,依损失工时计算金额:索赔金额= 公司上年度平均制费率*损失工时四、作业能率提升技巧作业能率体现员工在实际作业时间中的效率,其高低取决于员工的努力程度与作业方法。
而员工的努力与方法均离不开好主管的有力领导,因此现场管理者更应该尽力提升员工的积极性与工作技巧。
这其中的关键,一方面在于管理者的人际技巧,如沟通、激励等技巧,另一方面在于管理者的科学管理理论与方法。
提升作业能率的科学方法主要来自IE的手法。
本节就常用的有效方法进行介绍。
(一)工作抽样1、何谓工作抽样(WORK SAMPLING)所谓工作抽样,就是利用概率的法则,从瞬间观测所需最少限度的样本,分析作业者或机器设备的工作状态,以了解推定其全貌的方法,又称为瞬间观测法。
工作抽样之特色:(1)观测方法简单(2)可以正确地掌握对象之行动(3)可以一人同时观测众多对象(4)不需要观测经费工作抽样的作用:(1)提高作业率(2)求得适当的作业负荷量(3)改善作业人员负责的机器台数(4)调查间接业务,并且使它标准化(5)设备管理的改善(6)设定标准时间的宽放率(7)作为设定标准时间以及成本计算的参考资料表4-13 观测结果之整理由表4-12、表4-13可以看出三辆起重车的作业率仅有53.3%,因此可以减少一辆车,并且可以设法增加部分工作负荷。
2、工作抽样法的步骤步骤一:使分析目的明确化(1)掌握现况的问题点●展开调查,以便掌握作业的实态,并决定改善的重点。
●调查机械的作业率,并尽量地活用它们。
●调查作业人员及机械的作业率,决定一名作业人员应负责的机械数。
●为了提高作业率,应透彻了解非作业的原因,并加以改善。
(2)管理方面的标准化●决定标准时间●收集资料,以决定标准时间●求取宽放率步骤二:决定观测的对象,以及观测的范围步骤三:决定观测的项目最简单的,不外是观测作业与非作业两个项目,不过,仅此两项不能掌握全部的作业状况,可参照表4-14设定观测的项目。
步骤四:决定观测数观测数越多精度越好,而且,更能作出正确的判断。
不过,从另一个角度来看,如果观测数太多,也是既费时又费力的,因此,可参照表4-15或由下列公式计算:N =4(1-P)E其中,P为现象发生机率,E为观测要求精度。
步骤五:求取观测次数观测次数=观测数/观测的对象之数量步骤六:决定观测期间观测期间=观测次数/一天的观测次数步骤七:求取一天的观测次数一天的观测次数=观测次数/观测期间步骤八:决定观测的时刻(1)通常用随机时刻表来决定观测的时刻(2)有时也采用等级时间的间隔法,用乱数表来决定观测的时刻。
步骤九:决定观测路径步骤十:准备观测准备观测用纸、计秒表、笔记用具等。
若观测次数太多的话,最好由两个人分担。
观测用纸可参照表4-13之范例。
步骤十一:实施观测应注意事项:(1)观测必须在看到观测对象的瞬间实施,再确认作业内容,然后,记录在观测用纸上。
(2)作业者不在时,先记录,事后再询问理由。
(3)观测中发现问题,或应予改善之处,应随时记录下来。
(4)除了既定的观测项目外,如果发现了其他的有关作业,也应记录下来。
(5)有关调查的目的,可预先告知被观测部门的主管。
步骤十二:整理观测的结果依观测用纸的栏目作结果的汇总统计。
步骤十三:检讨观测的结果观测结果一旦整理完毕,应立即检讨,检讨项目有:(1)作业状况、非作业状况、作业项目的比例等(2)作业的推移、变动状况(3)人员、设备的作业率的检讨(4)对作业负荷适应化的检讨(5)对间接业务标准化的检讨(6)对其他特定项目的检讨管理者利用工作抽样法,可以获知员工的作业能率为什么低下的原因。
是作业方法不当,或是有大量的中间等待时间,或是员工努力程度不够,虽然每次都在作业,但速度太慢,没有效率。
只有找出真正原因,才能根据本行业的专业特点加以改善,并取得进步。
(二)动作经济原则要想提升作业能率,并不能一味地要求员工加快作业速度,提升作业熟练程度,提高劳动强度,这只能取得短暂的进步或有限的提升。
正确的方式是除了要求员工遵守相关的作业纪律外,尽可能设法改善其劳动强度,经由降低劳动强度和作业难度来提升作业速度。
这就是动作经济原则的出发点。
所谓动作经济原则,即作业人员在操作作业时,能以最少的劳力付出,达到最大的工作效果的法则。
它是由动作的创始Gilbreth 所提倡,尔后再经过专家学者的改进而成的。
其基本原则有三条:●动作能活用原则●动作量节约原则●动作法改善原则1、动作能活用原则人体各部位,凡是具有进行动作能力的,不管何部位,都希望能活用。
(1)脚或左手操作的事,不使用右手。
(2)尽量使双手同时作业,也同时结束动作。
(3)不要使双手同时静止,手空闲时,须动脑想另一工作。
2、动作量节约原则多余的运动量,不仅浪费时间及空间,更会消耗体力,应尽量节约。
(1)尽量使用小运动来操作工作。
(2)材料及器具应放置于伸手能及的范围内,并尽量放在靠手处。
(3)小单元的动作次数应尽量减少。
(4)工具应予以简化、易用。
(5)材料及零件应使用易拿取之容器。
(6)工作物较长、或较重、或体积较大时,应利用保持器具。
3、动作法改善原则使能动的部位全部活动,可以节约的能量、省去的动作也尽量去除,而动作还是有改善的地方。
(1)动作能予规律化(2)双手可反向运动,而不可同向运动。
(3)利用惯性、重力、自然力等,尤其尽量利用动力装置。
(4)为了减少疲劳,作业椅及作业台的高度应适合。
美国学者巴恩斯教授对省工原理继续研究,针对动作经济原则,依人体、工具、场所布置来归纳分类:(1)关于人体动作方面●双手并用原则●对称反向原则●对称反向原则●排除合并原则●降低等级原则●避免限制性原则●避免突变原则●节奏轻松原则●利用惯性原则●手脚并用原则●适当姿势原则(2)关于工具设备●利用工具原则●万能工具原则●易于操作原则●适当位置原则(3)关于场所布置原则●定点放置原则●双手可及原则●按工排序原则●使用容器原则●用坠送法原则●避免担心原则●照明通风原则●服装护具原则善于运用动作经济原则改善作业现状者,既可以提升作业能率,为企业赢得利益,又可以使员工工作更轻松,收益也更高,创造双赢的局面。
(三)生产线平衡分析对于流动作业方式的作业能率改善,利用生产线平衡分析的手法是最有效的手法之一。
所谓生产线的平衡,就是指各装配工程间的作业时间差距很小,作业速度均匀,无明显积压或闲待现象。
各工程的作业时间差距越小,越能够保持生产线的平衡。
1、生产线平衡分析的方法(1)把握各装配工程的作业时间,并调查全部工程的时间平衡。
(2)改善作业时间较长之“瓶颈”工程。