沸石转轮技术综述知识分享
沸石转轮知识讲解
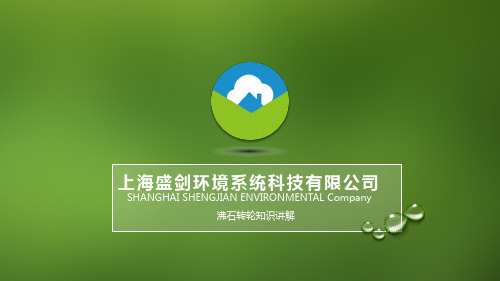
沸石转轮装置概述
沸石转轮的形式
01
02
西部技研、霓佳斯、蒙特、纳博科等
东洋纺
沸石转轮装置概述
盘式转轮结构
沸石转轮可分为吸附区、脱附区、冷却再生区三部分。三
个分区的位置固定不变,转轮以一定的转速(1~6 r/h)进行 转动。
1
2
3
之后转轮转动至冷却再生区,由一股相对低
温的气体对其进行降温冷却,以保证后续重
反应,形成放热导致闷燃情况的发生。
沸石转轮装置概述
防高沸点VOCs残留聚合
1
2
3
4
前端设置高沸点VOCs 去除设备
前置活性炭层、除湿
器或冷凝器等
提高脱附效果 提高脱附温度,温
度控制在180200℃之间; 提高脱附风量
定期进行高温脱附 2~3个月进行一次
高温脱附处理 高温脱附温度一般
取300℃左右
沸石转轮装置概述 沸石转轮的性能参数 2-- 吸附床厚度
在其他因素一定的情况下,某沸 石转轮对特定VOCs的吸附带长度 (h)是一定的,在此条件下,适 当增加床厚(H),有利于提高沸 石的使用效率(η)。
沸石转轮的利用率
床厚H(mm)
400
500
利用率η
以吸附带长度h=120mm为例
70%
76%
600 80%
若脱附热量不足,被吸附的有机
物未被完全脱附,会使得有机物
在近吸附区残留积聚,日久会发
1
生聚合现象,进而阻塞沸石,造
成吸附效能减弱。
当在180-200℃脱附时,若系统异常
停止,无气流流通且无外加氧气供应,
废气中的VOCs成分及在转轮上聚合
2
的高沸点物质,可能会与原残留于转
沸石转轮原理
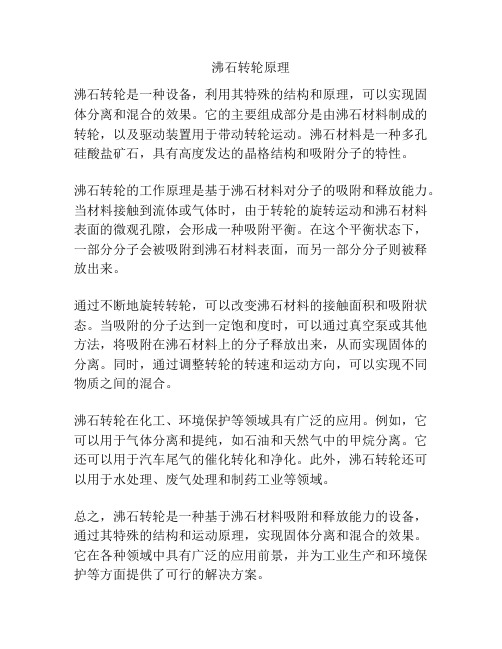
沸石转轮原理
沸石转轮是一种设备,利用其特殊的结构和原理,可以实现固体分离和混合的效果。
它的主要组成部分是由沸石材料制成的转轮,以及驱动装置用于带动转轮运动。
沸石材料是一种多孔硅酸盐矿石,具有高度发达的晶格结构和吸附分子的特性。
沸石转轮的工作原理是基于沸石材料对分子的吸附和释放能力。
当材料接触到流体或气体时,由于转轮的旋转运动和沸石材料表面的微观孔隙,会形成一种吸附平衡。
在这个平衡状态下,一部分分子会被吸附到沸石材料表面,而另一部分分子则被释放出来。
通过不断地旋转转轮,可以改变沸石材料的接触面积和吸附状态。
当吸附的分子达到一定饱和度时,可以通过真空泵或其他方法,将吸附在沸石材料上的分子释放出来,从而实现固体的分离。
同时,通过调整转轮的转速和运动方向,可以实现不同物质之间的混合。
沸石转轮在化工、环境保护等领域具有广泛的应用。
例如,它可以用于气体分离和提纯,如石油和天然气中的甲烷分离。
它还可以用于汽车尾气的催化转化和净化。
此外,沸石转轮还可以用于水处理、废气处理和制药工业等领域。
总之,沸石转轮是一种基于沸石材料吸附和释放能力的设备,通过其特殊的结构和运动原理,实现固体分离和混合的效果。
它在各种领域中具有广泛的应用前景,并为工业生产和环境保护等方面提供了可行的解决方案。
沸石转轮浓缩倍率-概述说明以及解释
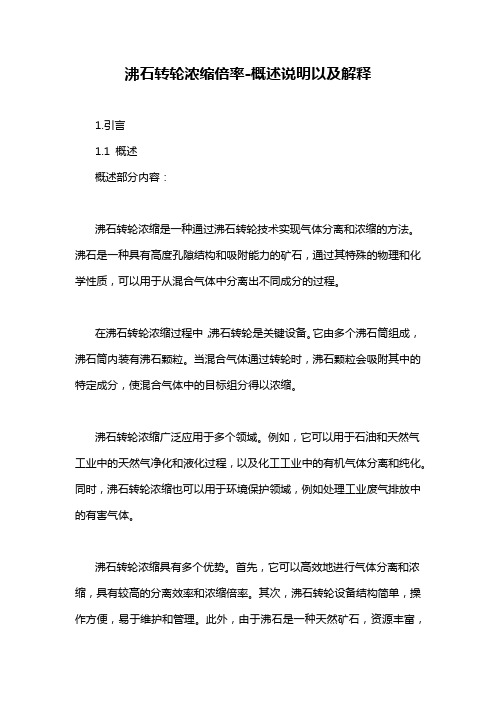
沸石转轮浓缩倍率-概述说明以及解释1.引言1.1 概述概述部分内容:沸石转轮浓缩是一种通过沸石转轮技术实现气体分离和浓缩的方法。
沸石是一种具有高度孔隙结构和吸附能力的矿石,通过其特殊的物理和化学性质,可以用于从混合气体中分离出不同成分的过程。
在沸石转轮浓缩过程中,沸石转轮是关键设备。
它由多个沸石筒组成,沸石筒内装有沸石颗粒。
当混合气体通过转轮时,沸石颗粒会吸附其中的特定成分,使混合气体中的目标组分得以浓缩。
沸石转轮浓缩广泛应用于多个领域。
例如,它可以用于石油和天然气工业中的天然气净化和液化过程,以及化工工业中的有机气体分离和纯化。
同时,沸石转轮浓缩也可以用于环境保护领域,例如处理工业废气排放中的有害气体。
沸石转轮浓缩具有多个优势。
首先,它可以高效地进行气体分离和浓缩,具有较高的分离效率和浓缩倍率。
其次,沸石转轮设备结构简单,操作方便,易于维护和管理。
此外,由于沸石是一种天然矿石,资源丰富,使用成本相对较低。
然而,沸石转轮浓缩也存在一些局限性。
首先,转轮内的沸石颗粒容易受到颗粒积灰和结垢的影响,需要定期清洗和维护。
其次,沸石转轮操作过程中需要一定的能源投入,例如电力或压缩空气等,增加了能源消耗。
综上所述,沸石转轮浓缩是一种重要的气体分离和浓缩技术。
它在多个领域都有广泛的应用,并具有较高的分离效率和浓缩倍率。
然而,需要注意的是,在实际应用中需要解决沸石转轮的维护和能源消耗等问题。
1.2 文章结构文章结构部分的内容可以按照以下方式编写:文章结构部分的主要目的是介绍本篇文章的整体结构,以帮助读者更好地理解文章的内容和组织形式。
本文的结构主要分为引言、正文和结论三个部分。
在引言部分,首先进行了概述,简要介绍了沸石转轮浓缩倍率的主题和背景。
接着,详细描述了本文整体的结构布局,包括引言、正文和结论三个部分的内容安排和承担的功能。
正文部分是本文的核心,主要分为2个小节。
首先,在2.1小节中,将详细介绍沸石转轮浓缩的定义和原理,包括沸石转轮浓缩的基本概念和工作原理。
沸石转轮技术综述
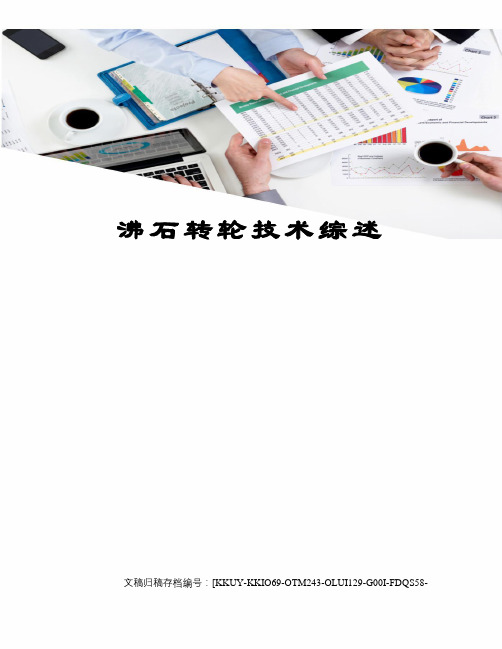
沸石转轮技术综述文稿归稿存档编号:[KKUY-KKIO69-OTM243-OLUI129-G00I-FDQS58-沸石转轮技术综述一、VOCs治理技术现今处理有害空气污染物技术分为五项:焚化、吸收处理、吸附处理、生物处理及冷凝(回收)处理。
焚化是利用燃料产生的热量直接破坏排放的废气,对污染物进行高温迅速的氧化反应,可将VOCs转变为二氧化碳及水等无害物质,吸收是利用吸收液和气体接触时,气流中之污染物扩散至气液接触面,排气中可溶解之污染物会因溶入吸收液而移除,最后再将气液分离即可达到清净空气的目的;吸附是藉由流体和高表面积的多空性固体粒子(吸附剂)之表面接触,产生物理性吸附有机物或其他物质;生物处理是VOCs经微生物吸收氧化后,分解成二氧化碳及水等最终代谢产物;冷凝则是藉由冷水冷凝方式,将VOCs冷凝下来,各种处理技术的优缺点说明如下:VOCs之处理方式可由以下几点考量决定采用何种防治设备,针对浓度高、价值高、风量小之废气可采用冷凝法将VOCs加以冷凝回收,针对浓度低、价值低、风量大之废气可采用活性炭或沸石转轮以吸附方式浓缩再以燃烧或高温氧化方式处理,针对浓度高、价值低、风量小之废气可采用燃烧或高温氧化法处理。
二、沸石转轮系统简介该系统系结合吸附、脱附及浓缩焚化三项操作单元为一体,是目前提供防治VOCs之较完善设备,但造价及操作维护成本偏高,并不适用于直接处理高沸点挥发性有机物是其限制所在。
较适合每分钟600立方公尺(CMM)高风量以上、VOCs之总碳氢化合物浓度介于500-1000ppm之废气特性厂家应用。
但若废气中含有较多量之高沸点物质,则并不适合单独、直接使用此系统处理之。
高沸点VOCs 虽容易吸附于沸石转轮上,但由于系统设计之安全考量,使得脱附高沸点VOCs温度不足,所以往往造成脱附不易,且高沸点VOCs将蓄积其上、占据吸附位置,影响系统整体效能。
若VOCs废气中含有较多量之高沸点物质,欲应用沸石吸附浓缩系统控制,建议于进入系统前端加装冷凝器、活性碳网栅及除雾器等设备,如此将可有效处理高沸点VOCs。
沸石转轮催化燃烧工作原理

沸石转轮催化燃烧工作原理沸石转轮催化燃烧作为一种新兴的催化燃烧技术,已经在有机废气处理等领域得到了广泛的应用。
那么它的工作原理是什么呢?下面本文将从几个方面进行详细讲解。
一、沸石转轮催化燃烧的基本原理沸石转轮催化燃烧是一种燃烧催化技术,其基本原理是利用铜、铁等过渡金属离子催化剂与空气中的氧气相互作用,使有机废气中的有机物与氧气发生氧化反应,从而使污染物被充分燃烧成为无害化废气。
二、沸石转轮的结构与特点沸石转轮是一种具有特殊结构的催化剂,其结构基本上是由一根中空的陶瓷柱组成,柱子表面布满了一层厚度均匀的沸石,而沸石转轮段与段之间是通过轴连接在一起的。
此外,沸石转轮具有强的热稳定性、耐腐蚀性和较大的比表面积等特点。
三、催化燃烧过程1.吸附阶段:在沸石转轮的表面,存在大量的氧物种,当有机废气进入沸石转轮的时候,其中的有机物质会先被吸附在氧物种上。
2.反应阶段:接下来,当有机物质被吸附至一定量的时候,开始向吸附氧物种上的氧原子进行反应。
这里需要催化剂的引导才能使反应发生,也就是说,催化剂是催化反应的关键。
3.析出阶段:当反应结束后,生成的CO2、H2O等废物会从沸石转轮中析出,同时沸石转轮的表面也会再次生成氧物质,以备下一轮的催化反应。
四、优缺点分析1.优点:能够将有机物质转化为无害废气,对环境没有污染作用;同时由于使用了催化剂,使得反应速度得到了大幅度提高,节约了能源和资源开销。
2.缺点:其寿命较短,需要经常进行维护和更换。
综上所述,沸石转轮催化燃烧作为一种目前应用十分广泛的废气催化燃烧技术,在不断的发展和改进中,必将更好的应对环境保护的需求。
沸石转轮高吸、脱附效率,VOCs去除率高

沸石转轮高吸、脱附效率,VOCS去除率高沸石转轮是将大风量、低浓度的废气浓缩到高浓度、小风量的废气,从而减少设备的投入费用和运行成本,提高VOCS废气的高效率处理。
分子筛浓缩转轮分为吸附区,脱附区,冷却区,转轮在各个区域连续运转。
吸附区:沸石转轮以每小时1-6转的速度持续旋转,与此同时将吸附的挥发性有机物传送到转轮的脱附区。
脱附区:在脱附区中利用小股加热气体(180-220。
C)将挥发性有机物进行脱附。
冷却再生:脱附后的沸石转轮旋转到冷却区,经冷却后旋转至脱附区,持续吸附挥发性有机气体。
沸石转轮的技术工艺流程:将饱和的沸石解析出来的有机气体通过脱附引风机作用送入净化装置,(沸石脱附下来的有机溶剂为气体)先通过阻火器系统,然后进入换热器,再送入到加热室,通过加热装置,使气体达到燃烧反应温度,再通过催化床的作用,使有机气体分解成二氧化碳和水,再进入换热器与低温气体进行热交换,使进入的气体温度升高达到反应温度,如达不到反应温度,这样加热系统就可以通过自控系统实现补偿加热,使它燃烧,这样节省了能源,废气有效去除率达标排放,符合国家排放标准。
沸石转轮是将大风量、低浓度的废气浓缩到高浓度、小风量的废气,从而减少设备的投入费用和运行成本,提高VOC废气的效率处理。
在处理大风量、低浓度的废气燃烧和回收的时候,如果没有它,直接进行燃烧的情况下,废气处理设备不仅体积庞大,而且产生的运行费用也会很庞大。
主要是应用在液晶生产、半导体、印刷、涂装等大风量低浓度的废气净化处理上,同时还可以处理一些锂电池、滤纸、制药的低浓度的大风量废气。
沸石转轮的优势:1、高吸、脱附效率,使原本高风量、低浓度的VOCs废气,转换成低风量、高浓度的废气,降低后端终处理设备的成本。
2、吸附VOCS所产生的压降极低,可减少能耗。
3、整体系统采预组及模块化设计,具备了小的空间需求,且提供了持续性及无人化的操控模式。
适应行业:适合于大风量,低浓度场合,包括:印刷、大型喷涂车间、家具、芯片、液晶LED工业等生产场所。
沸石转轮技术综述
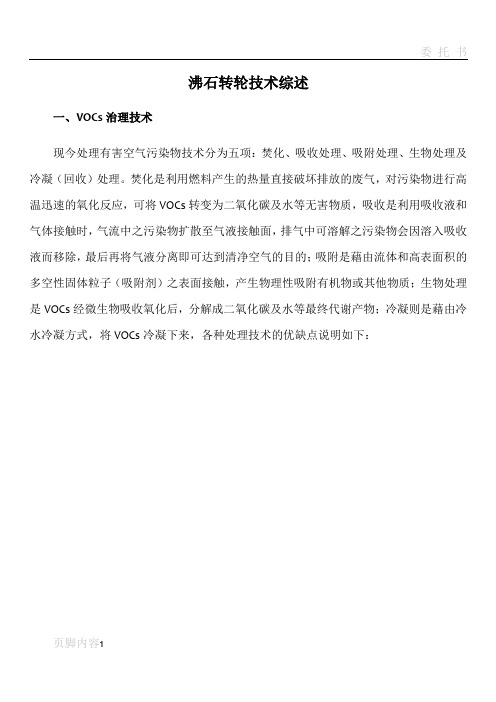
沸石转轮技术综述一、VOCs治理技术现今处理有害空气污染物技术分为五项:焚化、吸收处理、吸附处理、生物处理及冷凝(回收)处理。
焚化是利用燃料产生的热量直接破坏排放的废气,对污染物进行高温迅速的氧化反应,可将VOCs转变为二氧化碳及水等无害物质,吸收是利用吸收液和气体接触时,气流中之污染物扩散至气液接触面,排气中可溶解之污染物会因溶入吸收液而移除,最后再将气液分离即可达到清净空气的目的;吸附是藉由流体和高表面积的多空性固体粒子(吸附剂)之表面接触,产生物理性吸附有机物或其他物质;生物处理是VOCs经微生物吸收氧化后,分解成二氧化碳及水等最终代谢产物;冷凝则是藉由冷水冷凝方式,将VOCs冷凝下来,各种处理技术的优缺点说明如下:VOCs之处理方式可由以下几点考量决定采用何种防治设备,针对浓度高、价值高、风量小之废气可采用冷凝法将VOCs加以冷凝回收,针对浓度低、价值低、风量大之废气可采用活性炭或沸石转轮以吸附方式浓缩再以燃烧或高温氧化方式处理,针对浓度高、价值低、风量小之废气可采用燃烧或高温氧化法处理。
二、沸石转轮系统简介该系统系结合吸附、脱附及浓缩焚化三项操作单元为一体,是目前提供防治VOCs之较完善设备,但造价及操作维护成本偏高,并不适用于直接处理高沸点挥发性有机物是其限制所在。
较适合每分钟600立方公尺(CMM)高风量以上、VOCs之总碳氢化合物浓度介于500-1000ppm之废气特性厂家应用。
但若废气中含有较多量之高沸点物质,则并不适合单独、直接使用此系统处理之。
高沸点VOCs虽容易吸附于沸石转轮上,但由于系统设计之安全考量,使得脱附高沸点VOCs温度不足,所以往往造成脱附不易,且高沸点VOCs将蓄积其上、占据吸附位置,影响系统整体效能。
若VOCs废气中含有较多量之高沸点物质,欲应用沸石吸附浓缩系统控制,建议于进入系统前端加装冷凝器、活性碳网栅及除雾器等设备,如此将可有效处理高沸点VOCs。
而若是废气中含有高浓度之颗粒,则必须以微粒处理装置设置于沸石转轮之前端,以避免这些颗粒于沸石之蜂巢结构中沉积,其中最简单的微粒过滤装置为单层涂布,但其仅针对较大颗粒之过滤效果较佳,无法有效处理较小粒径之颗粒,因此适用于既设、无空间之工厂,其对沸石转轮之寿命延长仍然有限。
沸石浓缩转轮-催化氧化工艺治理VOCs废气

沸石浓缩转轮-催化氧化工艺治理VOCs废气一、引言挥发性有机化合物(VOCs)是指在大气中易挥发的有机物质,包括多种工业废气、油漆、油墨、粘合剂、溶剂、清洁剂等。
VOCs污染严重影响大气环境质量和人民的健康,因此治理VOCs废气污染已成为环保领域的重要课题。
目前,沸石浓缩转轮-催化氧化工艺作为治理VOCs废气的有效手段已得到广泛应用。
本文将就沸石浓缩转轮-催化氧化工艺的原理、特点及应用进行详细介绍,以期为相关行业提供参考。
二、沸石浓缩转轮-催化氧化工艺原理1. 沸石浓缩转轮工艺沸石浓缩转轮是一种通过物理吸附-脱附原理进行废气治理的技术手段。
其工作原理如下:在固定的时间间隔内,废气在沸石转轮上经过吸附、浓缩,然后将排放出减少了VOCs浓度的废气。
这一过程可连续进行,直至废气中的VOCs被大部分去除。
2. 催化氧化工艺催化氧化是通过引入催化剂,将VOCs废气中的有机物质氧化成二氧化碳和水。
催化氧化的关键在于选择合适的催化剂和控制氧化反应的温度、氧气浓度和气体停留时间。
沸石浓缩转轮-催化氧化工艺就是将沸石浓缩转轮和催化氧化技术结合在一起,通过浓缩+吸附和催化氧化的双重作用,对VOCs废气进行有效治理。
三、沸石浓缩转轮-催化氧化工艺的特点1. 高效性沸石浓缩转轮-催化氧化工艺能够有效去除VOCs废气中的有机物质,使废气排放达标。
相比其他治理技术,其去除效率更高、更稳定。
2. 节能环保与传统的热氧化技术相比,沸石浓缩转轮-催化氧化工艺不需要额外供热设备,节约能源消耗,同时氧化反应产物为水和二氧化碳,无二次污染。
3. 使用寿命长沸石浓缩转轮-催化氧化工艺中的吸附剂和催化剂均可多次循环使用,使用寿命长,降低了治理成本。
4. 适用范围广该工艺可适用于多种VOCs废气治理,包括有机溶剂废气、挥发性有机废气、印染废气等。
四、沸石浓缩转轮-催化氧化工艺的应用1. 印染行业沸石浓缩转轮-催化氧化工艺已成功应用于印染行业的VOCs废气治理。
- 1、下载文档前请自行甄别文档内容的完整性,平台不提供额外的编辑、内容补充、找答案等附加服务。
- 2、"仅部分预览"的文档,不可在线预览部分如存在完整性等问题,可反馈申请退款(可完整预览的文档不适用该条件!)。
- 3、如文档侵犯您的权益,请联系客服反馈,我们会尽快为您处理(人工客服工作时间:9:00-18:30)。
沸石转轮技术综述沸石转轮技术综述一、VOCs治理技术现今处理有害空气污染物技术分为五项:焚化、吸收处理、吸附处理、生物处理及冷凝(回收)处理。
焚化是利用燃料产生的热量直接破坏排放的废气,对污染物进行高温迅速的氧化反应,可将VOCs转变为二氧化碳及水等无害物质,吸收是利用吸收液和气体接触时,气流中之污染物扩散至气液接触面,排气中可溶解之污染物会因溶入吸收液而移除,最后再将气液分离即可达到清净空气的目的;吸附是藉由流体和高表面积的多空性固体粒子(吸附剂)之表面接触,产生物理性吸附有机物或其他物质;生物处理是VOCs经微生物吸收氧化后,分解成二氧化碳及水等最终代谢产物;冷凝则是藉由冷水冷凝方式,将VOCs冷凝下来,各种处理技术的优缺点说明如下:VOCs之处理方式可由以下几点考量决定采用何种防治设备,针对浓度高、价值高、风量小之废气可采用冷凝法将VOCs加以冷凝回收,针对浓度低、价值低、风量大之废气可采用活性炭或沸石转轮以吸附方式浓缩再以燃烧或高温氧化方式处理,针对浓度高、价值低、风量小之废气可采用燃烧或高温氧化法处理。
二、沸石转轮系统简介该系统系结合吸附、脱附及浓缩焚化三项操作单元为一体,是目前提供防治VOCs之较完善设备,但造价及操作维护成本偏高,并不适用于直接处理高沸点挥发性有机物是其限制所在。
较适合每分钟600立方公尺(CMM)高风量以上、VOCs之总碳氢化合物浓度介于500-1000ppm之废气特性厂家应用。
但若废气中含有较多量之高沸点物质,则并不适合单独、直接使用此系统处理之。
高沸点VOCs虽容易吸附于沸石转轮上,但由于系统设计之安全考量,使得脱附高沸点VOCs温度不足,所以往往造成脱附不易,且高沸点VOCs将蓄积其上、占据吸附位置,影响系统整体效能。
若VOCs废气中含有较多量之高沸点物质,欲应用沸石吸附浓缩系统控制,建议于进入系统前端加装冷凝器、活性碳网栅及除雾器等设备,如此将可有效处理高沸点VOCs。
而若是废气中含有高浓度之颗粒,则必须以微粒处理装置设置于沸石转轮之前端,以避免这些颗粒于沸石之蜂巢结构中沉积,其中最简单的微粒过滤装置为单层涂布,但其仅针对较大颗粒之过滤效果较佳,无法有效处理较小粒径之颗粒,因此适用于既设、无空间之工厂,其对沸石转轮之寿命延长仍然有限。
而拟新设置之工厂,若能预留空间给较有效之微粒处理装置(如袋式集尘装置),方可使沸石转轮之寿命有效延长之。
若无法确认VOCs废气中是否有其他废气混入或含有较多量之高沸点物质,欲应用沸石吸附浓缩系统控制,建议:(1)设置颗粒物过滤设备。
(2)定期以清洁水保养清洗。
能承受水洗程序处理之转轮,可依厂内所处理之废气所含高沸点VOCs物质浓度状况,适时以洁净水清洗沸石吸附转轮。
唯清洗时须特别注意水质状况,若其中含有大量钙、镁等离子,将可能会在沸石内生成碳酸盐或碳酸氢盐,阻塞沸石之蜂巢状孔隙;而水中之氯仿可能占据沸石内吸附位置,阻碍处理废气内所含VOCs之吸附性能,此外水中所含微量之重金属物质亦会毒化沸石,这将随着清洗次数及水质水量状况而有不同之影响;为克服沸石吸附转轮之蜂巢状孔道及其结构使得一般清洗水无法深入转轮内部,有研究采用如下的清洗程序。
利用高压喷嘴将清洗水形成微细雾滴状,并以系统冷却端之干净空气为载流,先将微细雾滴状之清水携入沸石孔道内实施逆洗程序后,再从另一边之吸附端吸入干净空气汇流,除可将附着于沸石内部之水气携出视为第二道清洗外,亦可完成沸石干燥之程序,如此两阶段之清洗转轮,其耗水量经统计可为以往传统方式之20%至30%,能大幅降低废水量,故可在成本考量下顺利、有效进行沸石转轮之清洗。
(3)于操作程序中提高脱附热容量。
除于系统前增设预处理系统、定期实施水洗保养程序外,亦可藉由提升脱附热容量之日常操作参数改善高沸点VOCs对系统所造成之影响,其施行之方法可利用提高再生温度及提高再生风量来达成。
系统操作运转时,即给予足够之热容量贯穿整个沸石吸附区,使距再生端较远处依然有充分之热量将吸附其上之高沸点VOCs物质脱附下来,减少其产生蓄积聚合、占据吸附位置影响效能。
三、沸石转轮系统的组成沸石吸附浓缩转轮焚化系统系利用吸附-脱附-浓缩焚化等三项连续程序,其设备特性适合处理高流量、低污染物浓度及含多物种之VOCs 废气,其主要应用于排放较稀薄且接近周界温度之污染物工业,典型应用如影印、涂装制程及半导体工厂等相关产业。
沸石吸附转轮组合(Cassette)为一中心轴承与轴承周围之支撑圆形框架支撑着转体,转体由沸石吸附介质与陶瓷纤维制成。
转轮上包含用以分开处理废气及处理后释出干净气体之密封垫,其材质为需能承受VOCS 腐蚀性及高操作温度之柔软材料制成(一般为硅)。
密封垫将蜂巢状沸石吸附转轮组合隔离成基本之吸附区(Adsorption zone) 及再生脱附区(Regeneration zone;desorption zone),但为提升转轮之吸附处理能力,则常见于前二区间加一隔离冷却区(Cooling zone or Purge zone)。
通常吸附区为较大,而脱附区及冷却区则为两个较小且面积相等之处理侧。
有时为特殊需求亦可分成更多串联区;而吸附转轮由一组电动驱动设备用以旋转转轮,故转轮处理时为可变速、且可控制每小时旋转2 至6 转之能力。
工厂所排放出之VOCS 废气进入系统后,第一阶段系经过疏水性沸石所组成之转轮,VOCS 污染物质首先于转轮上进行吸附;第二阶段之脱附程序是由与后端焚化系统热交换后预热之经冷却区处理后废气(约180 至250 ℃),使其通入转轮内利用高温将有机物脱附下来,此时出流污染物浓度大约可控制为入流废气之5 至20 倍左右,而脱附下来之有机物则可于第三阶段进行温度于700℃以上之焚化或进行冷凝回收再利用等程序,如此可以减少后续之废气处理单元尺寸、操作经费及设备初设费用。
沸石转轮之处理单元如下:(1)沸石转轮的机体是由一些特定的固体基材涂布上一层吸附剂粉末组成,基材是以陶瓷或玻璃或活性碳纤维经烧结所做成,其中陶瓷纤维因具备耐高温、热稳定性高、可水洗、不可燃及耐酸碱的特性而最受广泛使用,吸附剂的种类则视欲处理的气体成分而有所不同,一般可采用活性炭、沸石等。
转轮厚度一般为25cm-45cm。
(2)沸石转轮之基质为陶瓷纤维表面涂布一层吸附剂,一般为活性炭或疏水性沸石,制成蜂巢状圆形转轮,再分为两个区域,分别为吸附处理区及再生脱附区,但为提升转轮之吸附能力,有时会设计于两区之间多一个冷却区,通常吸附区较大,脱附区与冷却区为两个较小且面积相等之处理区域。
使用沸石转轮反应器之规格资料直径(mm)320高(mm)400主体密度(kg/m3)250区域比率(吸附/脱附/冷却)10:1:1孔道形状蜂巢状每平方厘米微孔数42比表面积241吸附剂占基材比重(%)36.66吸附剂类型ZSM-5吸附剂硅铝比166吸附剂孔隙(cm3/g)0.321 (3)热回收设备:将VOCs燃烧或氧化后之干净空气其温度高达500-700℃,将此部分空气经由热交换器将热能加以回收,同时将干净空气温度降低后将其导至转轮脱附区为转轮进行脱附作用;若温度太高则转轮可能发生燃烧,因此进入转轮之温度不可太高,一般会设置两段热回收设备并增设一鼓风机导入新鲜空气与燃烧后之空气混合,以控制脱附温度在180-220℃之范围内。
为处理VOCs废气,除了沸石吸附浓缩转轮焚化系统外,并可在制程端如光阻涂布机台或去光阻制程废气出口端加装冷凝器,预先分流处理高沸点VOCs (如MEA、BDG、DMSO)。
四、沸石转轮制备工艺4.1 活性炭吸附剂简介一般在选用活性炭时,除须考虑使用类别外,例如:气象或液相之应用,尚须针对处理对象之性质等作特性之考虑。
一般而言,在气象应用中,活性炭洗脱附处理以较适合中等分子量中低沸点且疏水性(低极性)化合物,例如:碳氢化合物、醇类(甲醇例外)、有机氯化物、脂肪酸类、酚类、酮类、脂类等活性炭均有很强的吸附能力;但对于硫化氢、二氧化硫、氯、甲醛、氨基酸类等化合物活性炭之吸附能力很差,除非含浸酸或碱级金属盐加以改质,方可达到较好之效果。
通常活性炭之参考规格有:比表面积、孔洞体积、四氯化碳吸附值、碘值、含水率等(一)粒状活性炭粒状活性炭依形状不同又可分为破碎状、圆柱状及球状等三种,一般来说其吸附能力较粉末活性炭小,但因颗粒尺寸较大较无压力下降之问题,而且具有可以再生的优势,所以一直是使用较为广泛的一种。
(二)纤维活性炭纤维活性炭系利用酚系、丙烯氰系等原料合成,主要目的是揉和粉末活性炭高表面积、高吸附能力及压降小、可再生之优点,而且具有独特的强度,通常其吸附能力也颇好。
一般应用上有固定床式和转轮或转环式,一般来说纤维活性碳的填充重量只有粒状活性碳的1-10%左右,间接减少了碳床累积之着火之危险。
活性碳再生一般以水蒸气脱附再生,若吸附质为含氯VOCs时,采用水蒸气可能会发生水解反应,而使回收之含氯VOCs发生改变,影响脱附产物之纯度及再生活性碳之吸附效能。
4.2 沸石吸附剂的优势相较于传统活性炭吸附剂,疏水性沸石具有以下优点:(1)不具可燃性:沸石为无机化合物二氧化硅等所组成,故不会发生反应性吸附质于吸附过程中着火之事;(2)可处理不同种类的溶剂,包括高沸点物质;(3)有效吸附程度可在较宽长的吸附质进流浓度范围内达成;(4)不会引发溶剂聚合或反应:疏水性沸石含有之金属微量杂质相当少,不会使一些高反应溶剂发生氧化或聚合反应。
传统上沸石为一亲水性(hydrophilic)吸附剂,此主要是Si/Al比值通常为1-5;换言之,沸石的特性与其Si/Al比或SiO2/Al2O3比有重大关联性。
沸石从亲水性转变为疏水性之Si/Al比值至少需8-10以上,所以含高硅含量之沸石疏水性愈高。
4.3 中空状沸石制备方式吸附剂之制备方式分为五大步骤:(1)沸石(zeolite)与粘合剂(binder)均匀混合;(2)胶化(gelling);(3)成型(forming);(4)干燥(drying);(5)煅烧(calcine)。
首先利用二氧化硅为粘合剂,将沸石与二氧化硅均匀混合,再慢慢加入调制好之碱性溶液(NaOH),此时会慢慢形成胶状体,再经由搅拌机搅拌、揉合成面团状,最后放入挤压成型机中制成中空圆柱状之沸石吸附剂。
制作出的吸附剂先放入烘箱中去除水份,再以450℃煅烧4小时,此时沸石吸附剂便制作完成。
4.4 沸石吸附剂的选取沸石是具有分子大小孔洞通道的多空性结晶固体,又称分子筛,其主要结构是以硅八面体(SiO4)所构成之三维空间晶体。
在沸石结构中,有些硅可被三价铝同构置换,于是整个结构由SiO4和AlO4配合碱金属、碱土金属或稀土金属组成之硅铝酸盐之晶体结构。