湿法炼锌中沸腾焙烧过程的研究现状与进展
浅谈硫化锌精矿制粒沸腾焙烧工艺的生产实践

硫化锌精矿制粒沸腾焙烧工艺硫化锌精矿炼锌在现行的湿法和火法工艺过程中,都必须先进行焙烧脱硫,同时,为了提高成品锌的质量,还必须尽可能脱铅和锐镉。
然而现行的高温氧化沸腾焙烧粉状锌精矿工艺,由于烟尘率高达20%以上,不但铅、镉得不到很好的富集,而且烟尘残硫高,必须进行二次焙烧脱硫。
我公司在进行冶炼技改时,采用了硫化锌精矿制粒沸腾焙烧并回收烟气制酸工艺。
一、工艺概况1、物料特点用于焙烧的硫化锌精矿,是由我公司自行生产的,其主要特点是:①、化学成分(表1)②、物理性能烧结点:1170℃~1180℃粒度:-200目占80%以上二、工艺特点①、制料工段制粒沸腾焙烧工艺要在锌精矿焙烧前进行制粒,并保证其强度在整个焙烧过程中不粉化,因此要添加粘结剂,设计时采用烟尘和锌精矿与粘结剂及适当的水份混合制粒,并干燥到水份入炉不汽化爆裂,一般含水2%以下,粘结剂为ZnSO4溶液和膨润土。
ZnSO4可用返回烟尘(ZnO)混上硫酸溶液(浓度30~40%)形成,增加少量膨润土(~1.5%)成粒强度更大,因此配料、混合、干燥以及筛分是不可少的过程。
②、焙烧工段由于入炉粒矿粒径较大,使粒矿表面因燃烧反应生成的氧化铁薄膜层较厚,阻碍氧分子向矿粒中心扩散。
生成的二氧化硫也不能很快地离开,即减慢了传递速度,使在一定的停留时间内,硫化锌精矿中的硫来不及燃烧完全,因而排出的焙砂残硫较高,为解决这一矛盾,采取了增加粒矿在沸腾炉内停留时间的办法,即在沸腾炉内的加料端和排粒端之间增加一道隔墙,从而在相同温度条件下,降低了焙砂的残硫。
③、主要设备本工艺主要设备见表2:三、生产情况试生产情况表明,制粒沸腾焙烧工艺的设计、施工及选用的设备是较为成功的。
主要技术经济指标如表3所表。
表3、主要技术经济指标表4、焙砂质量情况(平均值)四、几点体会①、在制粒过程中同时加入ZnSO4和膨润土作粘结剂,使粒矿强度很大,在焙烧过程中粉化较少,烟尘率在9%~13%左右,焙砂产出率已较高,但排硫效果不好,当沸腾层温度在1100℃~1150℃时,焙砂含硫在 1.8%左右,后取消膨润土,只用ZnSO4作为粘结剂,粒矿强度有所减少,烟尘率达13%~18%左右,但排硫效果有所提高,在相同温度条件下,焙砂含硫在1.2%左右。
湿法炼锌实验报告

一、实验目的1. 了解湿法炼锌的基本原理和工艺流程。
2. 掌握湿法炼锌的主要操作步骤和注意事项。
3. 培养实验操作能力和数据处理能力。
二、实验原理湿法炼锌是将锌精矿中的锌通过浸出、净化、电解等工艺步骤提取出来的过程。
实验主要采用硫酸浸出锌精矿,通过控制反应条件,使锌离子溶解于溶液中,然后进行电解得到纯锌。
三、实验材料与仪器1. 实验材料:锌精矿、硫酸、氢氧化钠、锌粉、氧化锌等。
2. 实验仪器:烧杯、漏斗、玻璃棒、锥形瓶、滴定管、pH计、电解槽、电极等。
四、实验步骤1. 锌精矿的浸出(1)将锌精矿加入烧杯中,加入适量的硫酸,搅拌溶解。
(2)调节pH值,使锌离子充分溶解。
(3)过滤得到浸出液。
2. 净化(1)将浸出液加入锥形瓶中,加入适量的氢氧化钠,调节pH值,使锌离子沉淀。
(2)过滤得到沉淀物,洗涤。
(3)将沉淀物加入烧杯中,加入适量的硫酸,溶解。
(4)过滤得到净化液。
3. 电解(1)将净化液加入电解槽中,加入适量的锌粉,作为阳极。
(2)将氧化锌作为阴极。
(3)通入直流电,进行电解。
(4)观察电解过程,记录电流、电压、时间等参数。
五、实验结果与分析1. 浸出实验结果(1)锌精矿浸出率:80%(2)浸出液pH值:2.02. 净化实验结果(1)锌离子沉淀率:95%(2)净化液pH值:6.03. 电解实验结果(1)电流:2A(2)电压:4V(3)电解时间:2小时(4)电解得到的锌纯度:99.5%六、实验结论1. 通过本次实验,成功掌握了湿法炼锌的基本原理和工艺流程。
2. 在浸出、净化、电解等工艺步骤中,控制反应条件对锌的提取率和纯度有重要影响。
3. 实验结果表明,本实验所采用的湿法炼锌工艺可行,具有良好的经济效益。
七、实验注意事项1. 在浸出过程中,注意控制pH值,避免锌离子过度溶解。
2. 在净化过程中,注意沉淀物的洗涤,提高锌离子沉淀率。
3. 在电解过程中,注意电流、电压等参数的控制,保证电解效果。
4. 注意实验过程中的安全操作,避免发生意外事故。
国内外锌冶炼技术现状和发展趋势

小、技术落后、能耗高、劳动生产率低的平罐炼锌
工 艺全 部淘 汰 。
炼锌和 I S P工艺。另外韦氏炉等蒸锌 生产立德粉也 可是为火法炼锌范 畴。 湿法炼锌有两大工艺 , 1 、精矿焙烧——浸出——净液一 一电积
我国是唯一还有 1 0 %左右 的锌 由竖罐生产 的 国家。因为葫芦岛锌厂开发的高温j ! l } 腾焙烧、大型 竖罐、大型精馏塔 、罐渣漩涡挥炉等技术,将竖罐
内需 求 , 依 然 需要 大 量进 口。 据 中国海 关统 计 , 2 0 1 4
转窑等不同工艺生产不同数量 的氧化锌粉 , 一般 占
其锌产量的 5 - 8 %,但 日本达到了 2 0 %。另外 ,意 大 利保留了一 台平罐炼锌炉作为冶金史教学示范
和 供 游客参 观 用 。去年 ,国外 火法 炼锌 ( I S P 加氧
量及储量基 础仅次于澳大利 亚 ,居世界 第二位 。 2 0 1 4 年美国地质调查局数据显示 , 全球锌资源储量 达2 5 0 0 0万 t ,其中澳大利亚 6 4 0 0万 t ,中国 4 3 0 0 万t ,秘鲁 2 4 0 0万 t 。2 0 1 4年世界前十大产锌国 , 中国第一、澳大利亚产锌 1 5 4万 t ,居第二位 ,其 余依次为秘鲁 1 3 2万 t , 美国 8 3 万t , 印度 7 2 万t ,
代化冶炼厂 。在沉铁方法上我国没有开发 “ 针铁矿 法”和 “ 赤铁矿法”, 而是开发 了 “ 低污染铁矾法” 和 “ 喷淋除铁法” 。热酸浸出铁矾渣含锌低,不用 再处理, 可送渣场堆存 , 但渣量大 , 渣库 占用土地 , 并要求严格防渗 ,投资费用较大 ,尚存在环境污染 隐患。低污染铁矾法属于改进 的黄钾铁矾法 ,此法 在沉矾过程中不需要添加焙砂做 中和剂, 避 免了焙 砂 中未反应的锌及其他有色金属进入铁矾渣,渣含 锌低于 3 %,提高了锌、铅、银等有价金属的回收
湿法炼锌系统生产实践浅析
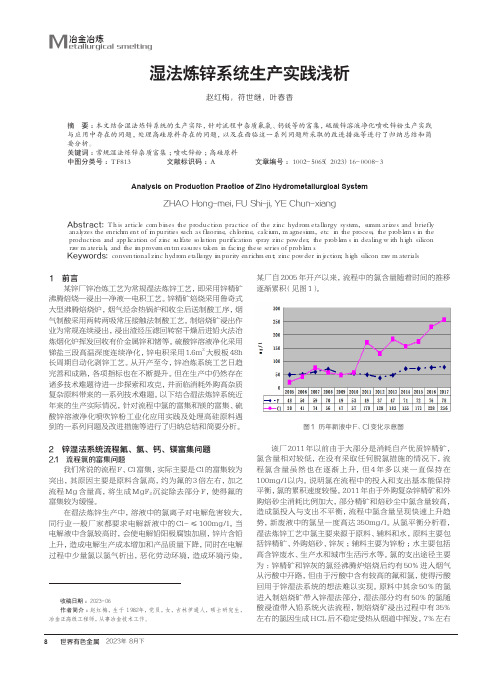
8冶金冶炼M etallurgical smelting湿法炼锌系统生产实践浅析赵红梅,符世继,叶春香(驰宏科技工程股份有限公司,云南 曲靖 655000)摘 要:本文结合湿法炼锌系统的生产实际,针对流程中杂质氟氯、钙镁等的富集,硫酸锌溶液净化喷吹锌粉生产实践与应用中存在的问题,处理高硅原料存在的问题,以及在面临这一系列问题所采取的改进措施等进行了归纳总结和简要分析。
关键词:常规湿法炼锌杂质富集;喷吹锌粉;高硅原料中图分类号:TF813 文献标识码:A 文章编号:1002-5065(2023)16-0008-3Analysis on Production Practice of Zinc Hydrometallurgical SystemZHAO Hong-mei, FU Shi-ji, YE Chun-xiang Chihong Technology Engineering Co., Ltd. Qujin 655000,China ) Abstract: This article combines the production practice of the zinc hydrometallurgy system, summarizes and briefly analyzes the enrichment of impurities such as fluorine, chlorine, calcium, magnesium, etc. in the process, the problems in the production and application of zinc sulfate solution purification spray zinc powder, the problems in dealing with high silicon raw materials, and the improvement measures taken in facing these series of problems. Keywords: conventional zinc hydrometallurgy impurity enrichment; zinc powder injection; high silicon raw materials收稿日期:2023-06作者简介:赵红梅,生于1982年,党员,女,吉林伊通人,硕士研究生,冶金正高级工程师,从事冶金技术工作。
锌精矿沸腾焙烧设计
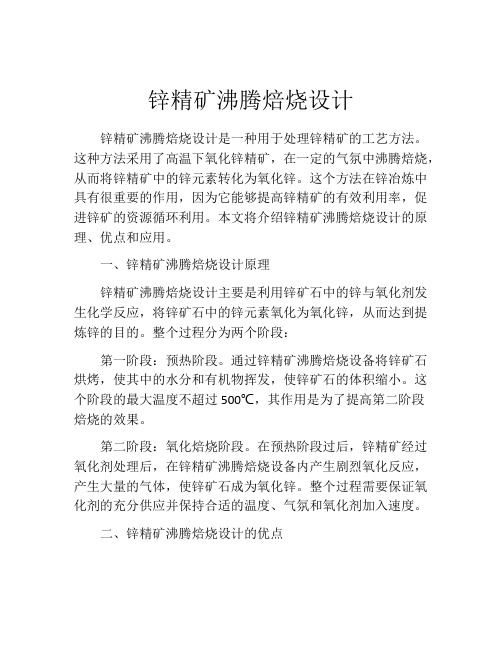
锌精矿沸腾焙烧设计锌精矿沸腾焙烧设计是一种用于处理锌精矿的工艺方法。
这种方法采用了高温下氧化锌精矿,在一定的气氛中沸腾焙烧,从而将锌精矿中的锌元素转化为氧化锌。
这个方法在锌冶炼中具有很重要的作用,因为它能够提高锌精矿的有效利用率,促进锌矿的资源循环利用。
本文将介绍锌精矿沸腾焙烧设计的原理、优点和应用。
一、锌精矿沸腾焙烧设计原理锌精矿沸腾焙烧设计主要是利用锌矿石中的锌与氧化剂发生化学反应,将锌矿石中的锌元素氧化为氧化锌,从而达到提炼锌的目的。
整个过程分为两个阶段:第一阶段:预热阶段。
通过锌精矿沸腾焙烧设备将锌矿石烘烤,使其中的水分和有机物挥发,使锌矿石的体积缩小。
这个阶段的最大温度不超过500℃,其作用是为了提高第二阶段焙烧的效果。
第二阶段:氧化焙烧阶段。
在预热阶段过后,锌精矿经过氧化剂处理后,在锌精矿沸腾焙烧设备内产生剧烈氧化反应,产生大量的气体,使锌矿石成为氧化锌。
整个过程需要保证氧化剂的充分供应并保持合适的温度、气氛和氧化剂加入速度。
二、锌精矿沸腾焙烧设计的优点1、高效:锌精矿沸腾焙烧设计可以快速将锌矿石中的锌元素转化为氧化锌,提高锌资源的利用效率。
2、环保:锌精矿沸腾焙烧设计可以有效地控制污染物排放,减少环境污染。
3、节能:锌精矿沸腾焙烧设计可以大量节约能源,提高工作效率,减少使用成本。
4、灵活性强:锌精矿沸腾焙烧设计可以根据锌矿石的类型、特性和工艺要求进行调节,使其更加适应不同的锌精矿处理工艺。
5、成本低:锌精矿沸腾焙烧设计的设备和工艺比较简单,成本相对较低,可以减少项目的投资。
三、锌精矿沸腾焙烧设计的应用锌精矿沸腾焙烧设计已经成为锌冶炼行业中最常用的处理方法之一。
它广泛用于下列领域:1、锌冶炼:锌精矿沸腾焙烧设计是锌冶炼最重要的处理方法之一,可以提高锌资源利用率,降低生产成本。
2、反渗透:锌精矿沸腾焙烧设计还可以应用于反渗透过程中,用于除去锌元素污染物,提高水质。
3、环保:锌精矿沸腾焙烧设计可以用于处理废水、废气等工业污染物,控制工业污染,保护环境。
湿法炼锌除铁工艺的现状与展望报告
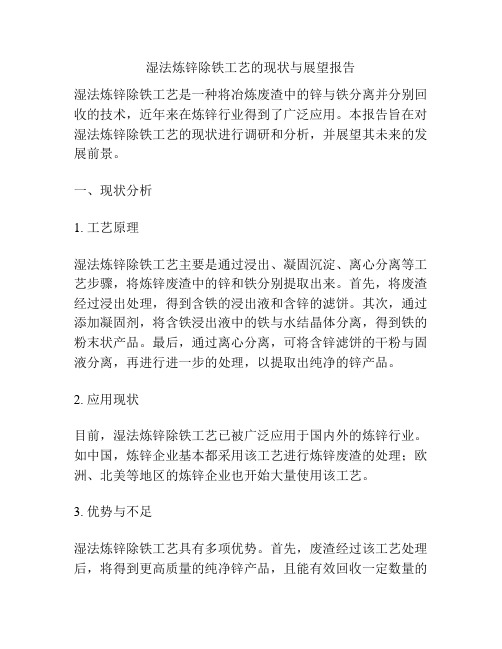
湿法炼锌除铁工艺的现状与展望报告湿法炼锌除铁工艺是一种将冶炼废渣中的锌与铁分离并分别回收的技术,近年来在炼锌行业得到了广泛应用。
本报告旨在对湿法炼锌除铁工艺的现状进行调研和分析,并展望其未来的发展前景。
一、现状分析1. 工艺原理湿法炼锌除铁工艺主要是通过浸出、凝固沉淀、离心分离等工艺步骤,将炼锌废渣中的锌和铁分别提取出来。
首先,将废渣经过浸出处理,得到含铁的浸出液和含锌的滤饼。
其次,通过添加凝固剂,将含铁浸出液中的铁与水结晶体分离,得到铁的粉末状产品。
最后,通过离心分离,可将含锌滤饼的干粉与固液分离,再进行进一步的处理,以提取出纯净的锌产品。
2. 应用现状目前,湿法炼锌除铁工艺已被广泛应用于国内外的炼锌行业。
如中国,炼锌企业基本都采用该工艺进行炼锌废渣的处理;欧洲、北美等地区的炼锌企业也开始大量使用该工艺。
3. 优势与不足湿法炼锌除铁工艺具有多项优势。
首先,废渣经过该工艺处理后,将得到更高质量的纯净锌产品,且能有效回收一定数量的铁资源;其次,该工艺具有灵活性,不受原料成分等不可控因素的影响,且能够适应不同规模的炼锌企业需求。
然而,湿法炼锌除铁工艺也存在一些不足。
例如,该工艺需要大量的水资源,同时在处理过程中也会产生大量的废水,对环境造成一定的影响;此外,该工艺也需要一定的能源消耗。
二、发展展望1. 在工艺优化方面,可尝试采用新型材料、新型凝固剂等技术,提高工艺的效率和产品质量,并减少对环境的影响。
2. 在应用方面,未来湿法炼锌除铁工艺有望进一步扩大应用范围,涉及更多领域,如冶金、化工等行业。
同时,在国际市场更加竞争激烈的背景下,该工艺也面临更多的挑战,需要加强品牌建设和市场拓展。
3. 在科技创新方面,可适应新型锌矿资源的开发和应用,研发出更适合不同类型锌矿的湿法炼锌除铁工艺。
三、小结湿法炼锌除铁工艺是一种有效地解决炼锌废渣资源化问题的技术,已被广泛应用于炼锌行业。
未来,该工艺有望通过不断的工艺优化、应用扩大和科技创新,为炼锌企业和环保事业带来更大的价值。
湿法炼锌焙烧节能途径探讨
湿法炼锌焙烧节能途径探讨本文围绕如何提高企业能源利用率、降低能耗、提高经济效益进行分析,探讨了余热发电及热电联产的节能技术改造方案,并对其可行性、先进性、经济效益及社会效益进行了分析。
有色冶炼企业是耗能大户,湿法炼锌是排在铝冶炼后的第二耗电大户。
在湿法炼锌工艺生产过程中,浸出、净液工序需要大量的蒸气,电解、熔铸工序需要大量的电力,仅电解电耗就在3200kW·h/t·Zn左右,可见能耗在企业的加工成本占很大的比重。
因此,能耗的高低对企业的经济效益有很大的影响。
在湿法炼锌企业,为提高能源利用率,企业普遍采用余热锅炉回收锌精矿沸腾焙烧产生的大量高温烟气余热,产生的蒸气和燃煤工业锅炉产生的中压蒸气减压至0.48 MPa后供炼锌等用汽单位使用。
某公司炼锌工艺采用国际先进、国内首创、具有自主知识产权的高酸浸出一低污染沉矾湿法炼锌工长期从事冶炼制酸工作艺,焙烧制酸采用锌精矿沸腾焙烧一余热回收一S02 烟气制酸工艺。
现年生产能力达到锌锭11万t,目前,四期扩建工程已开工建设,到2009年,公司年生产能力将达到锌锭21万t。
目前蒸汽由本企业燃煤工业锅炉、5 t/h 余热锅炉和四期新建的30 t/h余热锅炉和50 t/h燃煤工业锅炉提供。
出于锌精矿原料的保障,公司二、三期扩建工程焙烧制酸项目建在了原料产地林东镇郊区,在焙烧制酸生产过程中,余热锅炉回收了大量的高压过热蒸汽,由于没有利用途径,这些蒸汽除部分用于取暖外,其余全部排放,既浪费大量的热能,又造成余热锅炉软化水供应紧张。
随着生产规模不断扩大,能源消耗量也大幅增加,节能工作的重要性也日益突出。
为贯彻国家发改委“十一五”十大重点节能工程实施意见精神,降低能耗、提高企业经济效益,公司计划以企业存在的节能潜力为基础,进行节能技术改造。
技术方案围绕如何提高能源利用率。
降低能耗,提高经济效益.认为有以下两方面潜力:(1)林东分厂余热锅炉回收的高温、高压蒸气,应合理、有效地利用。
锌湿法冶炼渣处理工艺研究
锌湿法冶炼渣处理工艺研究摘要:有色金属冶炼的环境保护和资源高效利用已成为制约行业可持续发展的关键因素,湿法炼锌生产的浸出渣开路问题是企业面临的难题之一。
本文针对我国湿法炼锌采用的主流工艺,基于生产过程的产生的各种浸出渣、净化渣、烟尘、污泥等含锌物料的来源、组成和污染物进行分析,较系统地总结了目前各类锌冶炼渣的综合利用及无害化处理技术。
关键词:湿法炼锌;锌冶炼渣;处理工艺1冶炼渣的来源与组成1.1常规浸出冶炼渣常规浸出过程为中性浸出和酸性浸出两段。
中性浸出液的净化采用置换或化学沉淀,一般加入锌粉去除铜镉,然后将溶液升温加锌粉和活化剂锑盐或砷盐去除钴镍,最后加锌粉去除复溶镉,分别得到铜镉渣和镍钴渣,也可采用黄药除钴生成黄酸钴渣。
添加铜渣或石灰乳去除氟、氯,分别得到氯化亚铜和氟化钙沉淀。
通过控制酸性浸出液的pH值,Fe2+被氧化成Fe3+后水解去除,酸性浸出渣含锌约20%,Fe约25%,铅约5%,烟尘中含有少量的氧化锌尘和SO2。
常规浸出冶炼渣为有害渣,含有价金属多,回收利用技术相对成熟。
1.2热酸浸出冶炼渣热酸浸出与常规浸出不同的是中性浸出渣采用二段高温高酸浸出,使渣中难溶于稀硫酸的铁酸锌溶解进入酸性浸出液。
富集于热酸浸出渣中的铅、银等称为铅银渣,其中锌主要以ZnS和ZnFe2O4形式存在,铁主要以Fe2O3和FeO形式存在,铅主要以PbS和PbSO4形式存在,银主要以Ag2S和AgCl形式存在。
热酸浸出液除铁后返回中性浸出流程,除铁工艺主要有:黄钾铁矾法、针铁矿法、赤铁矿法,使浸出液中的Fe以黄钾铁矾、针铁矿、赤铁矿的形式与溶液分离。
1.3高压氧浸浸出渣氧压浸出是在高压釜内直接高温氧压浸出硫化锌精矿,可避免副产硫酸,浸出液的处理过程与常规流程一致。
此工艺反应速度快,提高了原料中镓、锗、铟等稀散金属的回收率和铜、镉的浸出率和回收率,利于铅、银等贵金属的富集。
氧压浸出废渣含20%~25%的水份和12%~15%的元素硫,根据精矿原料的不同及后续渣处理工艺的差异,氧压浸出渣分为高银渣和低银渣,高银渣又分成高铁渣和低铁渣。
锌冶炼可行性研究报告
锌冶炼可行性研究报告一、锌冶炼工艺技术现状分析锌的主要冶炼工艺包括电解法、煤气法、湿法冶炼和熔炼法等。
电解法是目前主要的锌冶炼工艺,它以含锌的硫酸锌溶液为原料,通过电解过程获得纯锌。
煤气法采用氧化锌和煤气作为原料,在高温下还原获得锌金属。
湿法冶炼则是利用含锌的氧化物在酸性介质中进行浸出,然后通过萃取、还原等步骤得到锌。
熔炼法是将锌矿石在高温下熔炼,通过氧化、还原等反应获得锌金属。
这些工艺各有优缺点,需要根据实际情况选择适合的方法。
二、市场需求分析锌是一种重要的有色金属,广泛用于镀锌钢材、合金制品、化工原料等领域。
随着全球经济的发展和工业化进程加快,对锌的需求将不断增加。
尤其是在建筑、汽车、电子等行业,对锌的需求将会持续增长。
三、锌冶炼的可行性评估1.资源条件:锌是一种丰富的金属矿产,其资源分布广泛。
我国拥有丰富的锌矿资源,为锌冶炼提供了良好的资源基础。
2.技术条件:目前的锌冶炼工艺技术已相当成熟,一些先进的技术设备已经能够实现大规模、高效率的生产。
而且,国内外都有多家锌冶炼企业,对于技术设备的供给也是相对充足的。
3.市场条件:随着全球经济的发展,锌的需求将会持续增加,市场前景良好。
4.环保条件:锌冶炼是一种高污染行业,对环境保护要求较高。
但随着环保法律政策的不断完善和企业的自愿改造,锌冶炼产业也在逐渐减少对环境的污染。
四、发展建议1.技术改造:加强对锌冶炼工艺技术的研究和改进,提高生产效率和产品质量。
2.资源整合:整合国内外锌矿资源,确保原料的充足供应。
3.市场拓展:加大对锌产品的技术开发和市场营销力度,积极拓展国内外市场。
4.环保措施:加强对锌冶炼企业的环保监管,鼓励企业采用清洁生产技术,减少对环境的污染。
总结:锌冶炼具有较好的市场前景和发展潜力,但需要加强技术研究和环境保护措施。
希望本报告的研究和分析,能够为相关企业和政府部门提供有益的决策参考。
国内外锌冶炼技术的现状及发展动向
冶金冶炼M etallurgical smelting 国内外锌冶炼技术的现状及发展动向陈燕彬(湖南有色金属职业技术学院,湖南 长沙 412006)摘 要:锌冶炼技术的整体水平是一个国家金属冶炼能力的重要标志。
文章重点对锌冶炼技术的发展现状与动向进行了分析,以期能够提升我国锌冶炼技术水平,为工业现代化建设做出积极的贡献。
关键词:锌冶炼技术;现状;动向中图分类号:TF813 文献标志码:A 文章编号:1002-5065(2018)15-0005-2Present situation and development trend of zinc smelting technology at home and abroadChen Yan-bin(Hunan nonferrous metals Vocational and Technical College, Changsha 412006,China)Abstract: The overall level of zinc smelting technology is an important symbol of a country's metal smelting capacity. This paper focuses on the development status and trend of zinc smelting technology, in order to improve the level of zinc smelting technology in China and make a positive contribution to industrial modernization.Keywords: zinc smelting technology; status quo; trend目前依然在使用的锌冶炼技术主要包括有火法冶炼与湿法冶炼两种类型,其中火法冶炼中许多常规的冶炼方法已经逐渐被淘汰,而剩余的技术中适应较为广泛的是密封鼓风炉冶炼技术,根据实际生产的需求,其在物料选择方面也存在一定的差异[1,2]。
- 1、下载文档前请自行甄别文档内容的完整性,平台不提供额外的编辑、内容补充、找答案等附加服务。
- 2、"仅部分预览"的文档,不可在线预览部分如存在完整性等问题,可反馈申请退款(可完整预览的文档不适用该条件!)。
- 3、如文档侵犯您的权益,请联系客服反馈,我们会尽快为您处理(人工客服工作时间:9:00-18:30)。
湿法炼锌中沸腾焙烧过程的研究现状与进展
现代炼锌方法分为火法和湿法两大类,世界上大部分的锌都是从硫化锌精矿
中提取出来的。
无论火法还是湿法,一般都需预先焙烧或烧结,脱除大部分硫和其他杂质,以满足下道工序的要求。
目前,在国内应用较成熟的焙烧技术是硫化锌精矿的粉状沸腾焙烧技术。
沸腾焙烧又称流态化焙烧,是众多焙烧方法中的一种。
所谓的沸腾焙烧是指将所要处理的固体破碎,研磨成细粉,增加固体与气体的接触面积,缩短颗粒内部的传递和反应距离。
自下而上流经这些粉料的气体,在达到一定速度时,会将固体颗粒悬浮起来,使之不断运动,犹如沸腾的水,故称沸腾焙烧。
沸腾焙烧的基础是固体流态化,用沸腾焙烧炉焙烧锌精矿,炉内热容量大且均匀,温差小,料粒与空气接触表面积大,反应速度快,强度高,传热传质效率高,使焙烧过程大大强化,产品质量稳定生产率高。
下面主要叙述在湿法炼锌中沸腾焙烧过程的发展和应用现状。
1 湿法炼锌中沸腾焙烧过程的发展和应用现状
1.1 在制粒焙烧方面的研究情况
李芳、张建彬,张起梅等[1]在锌精矿制粒沸腾焙烧中指出随着原料供应日趋紧张、精矿质量下降,发展沸腾焙烧技术,对提高锌冶炼金属回收率具有重要的意义。
他们进行了锌精矿制粒焙烧的试验研究,重点分析了制粒粘合剂的选择和制粒焙砂质量控制。
在沸腾焙烧试验中,针对焙砂质量及其影响因素诸如焙烧温度、原料粒度、过剩空气系数和物料在炉内的停留时间等进行了研究;另外通过适当减少加料量,使相应提高过剩空气系数,延长停留时间,Pb的脱除有所降低,同时s脱除效果亦有明显提高。
最后他们得出结论:制粒沸腾焙烧提高了炉子的处理能力,床处理能力达到30.4 t/m2·d,炉温控制得当,风量均匀,焙砂质量可以达到Pb<1.0%,Cd<0.05%,S<1%的控制要求。
沸腾炉操作温度可控制在1140~1180℃,比现有粉状物料焙烧操作温度提高60~80℃。
靳澍清、刘丽珍、吉正元等[2]在锌精矿造粒、焙烧试验研究中采用几种粘结剂进行造粒试验,对成粒矿进行静态焙烧试验,提出造粒和焙烧试验工艺条件及参数,粒矿进行静态焙烧试验,为大规模的生产奠定了一定的基础。
张瑜、李志勇、吴志平等[3]在锌精矿制粒沸腾焙烧新工艺的应用与改进中介绍了锌精矿制粒沸腾焙烧新工艺的工业化生产应用与技术改进情况,同时阐述了所取得的成果及存
在的问题。
他们所采用的新工艺为:锌精矿一锤式破碎机一混凝土搅拌机一圆盘制粒机一回转干燥窑一振动筛一沸腾焙烧炉一焙砂。
1.2 在提高沸腾炉产能、提高经济指标方面的研究
涂福炳、周孑民[4]在锌精矿沸腾焙烧炉产能下降原因分析及对策研究中提出了影响焙烧炉产量的主要因素:当沸腾床面积确定后,沸腾炉产量大小主要取决于焙烧强度的高低。
焙烧强度越高,炉子产量越大;焙烧强度越低,炉子产量越小。
而焙烧强度取决于单位时间内从炉内沸腾层移走热量的多少和物料反应速度的快慢。
在原料成分、物理规格、焙烧温度和鼓风压力等生产因素正常的条件下,冷却水套的换热效果越好,吸收的热量越多,焙烧强度就越高。
另外温度一定时,空气富氧浓度增加,反应速度加快,焙烧强度大大提高。
然后指出沸腾炉冷却水套结渣导致换热系数下降,是影响炉子生产能力的重要因素之一。
最后指出了提高炉子产量的途径:加大炉内排热强度,此途径可通过增设炉内喷水装置、适量增大风量、加入适量焙砂、使用活动水套来解决;另外富氧鼓风可大幅提高焙烧强度,是提高锌精矿沸腾焙烧炉生产能力的新的技术思路,具有重要的实践意义和经济价值。
尹亚平[5]在提高50 m2沸腾炉床能力和SO2,烟气浓度初探中根据昆明云冶锌业股份有限公司50m2鲁奇式沸腾炉火法系统建成投产初期系统运行周期短、床能力低、SO2浓度偏低等情况,从工艺技术条件和设备改进等方面对提高床能力和烟气SO2,浓度进行了探讨。
他认为提高炉床能力可以通过提高焙烧温度、增加鼓风量、选择合理的入炉精矿含硫和扩大沸腾层冷却埋管面积来实现。
提高烟气SO2,浓度可以从工艺技术条件和设备漏风点的堵漏两个方面人手。
另外周述勇[6]在109 m2沸腾炉生产实践及提高处理量的途径中指出了提高处理量的三种途径:(1)炉内增加一组埋管;(2)炉内增设喷水装置;(3)富氧鼓风。
1.3 在优化焙烧工艺参数方面的研究
李忠于[7]在锌精矿沸腾焙烧两个关键工艺参数的选取中重点讨论了锌精矿沸腾焙烧最关键的两个工艺参数——焙烧温度与空气过剩系数对锌焙砂质量的影响,以及根据不同的炼锌工艺如何选取焙烧工艺,再根据不同的焙烧工艺如何选择这两个关键工艺参数。
在酸化焙烧工艺中选取焙烧温度时,应考虑锌精矿原料的成分(特别是杂质含量)和焙烧温度对锌焙砂质量的影响。
一般地,原料矿中铁、二氧化硅含量高时,温度宜取低值,尽量少生成铁酸锌和硅酸锌,以提高锌的可溶率;反之,当原料矿中的铁、二氧化硅含量低时,焙烧生成的铁酸锌、硅酸锌己很少,对锌的可溶率影响很小,可适当提高焙烧温度,并兼顾降低焙砂残硫;原料矿中砷和锑含量高时,温度宜取
低值;反之,当原料矿中的砷和锑含量低时,可适当提高焙烧温度。
选取空气过剩系数时经过综合考虑,一般酸化焙烧的空气过剩系数宜为1.15~1.3,不得超过1.3。
选取氧化焙烧工艺时,焙烧的温度越高,杂质脱除效率明显提高;同时焙烧温度的提高,也有利于矿尘粒度变大,降低烟尘率。
空气过剩系数加大,脱硫率增加,但铅、镉脱除率却降低。
因此在选取氧化焙烧工艺时,也应结合锌精矿的成分和工艺参数对锌焙砂质量的影响来考虑。
刘智能[8]在锌精矿沸腾焙烧产物可溶硫的控制中指出锌精矿沸腾焙烧产物中可溶硫的含量在焙烧过程中并不是简单的单一变量来决定的,而是一个双变量体系,焙烧产物中可溶硫的含量与体系中的热力学、动力学条件有着密切的关系。
在具体的操作中,合理地选择炉型与风帽的配置、控制沸腾炉的料风比、调节沸腾炉的运行风量等方法,可以一定程度地控制产物中的可溶硫的含量。
龚紫涛、李江[9]在微富氧技术在沸腾焙烧的应用中就利用富余的氧气生产能力将沸腾焙烧所需压一缩空气的氧浓度增至23%,对实施富氧焙烧的可行性进行了探索。
指出在富氧条件下,更能发挥沸腾焙烧的优越性。
朱连勇、李科立[10]在锌精矿的粒度对氧化焙烧的影响中分析了粒度小的硫化锌精矿对沸腾焙烧的有利影响,粒度小的硫化锌精矿对氧化焙烧的不利影响,硫化锌精矿粒度的均匀性对沸腾焙烧反应的影响,最后提出了针对不同粒度的硫化锌精矿在配料和沸腾焙烧工序所应采取的措施。
刘风林、金作美、王励生[11]在高硅硫化锌精矿氧化焙烧中硅酸锌生成反应的动力学中研究了温度和粒径对硅酸锌生成速率的影响,固固扩散是硅酸锌形成的限制环节。
因此在焙烧过程中控制粒度不能过细是限制硅酸锌生成速率的有效方法。
温度对硅酸锌的速率常数矗有较大的影响,高硅硫化锌精矿焙烧过程中在不影响正常操作的条件下,为限制硅酸锌的生成速率,应适当降低焙烧温度(至860℃左右)。
黄炜,谢颂明[12]在锌焙砂还原焙烧工艺的试验研究中探讨了焙烧温度、焙烧时间、
煤粉用量对可溶锌的影响,确立最佳焙烧工艺条件为:焙烧温度800℃,焙烧时间30 min,煤粉用量4%,在此条件下锌焙砂中的可溶锌可由92.32%提高至99.09%。
欧阳智武[13]在提高锌焙烧可溶锌率的探讨中详细讨论了焙烧温度、沸腾层直线气流速度、炉内气氛、锌精矿特性对可溶锌率的影响,从理论和实践两方面对提高焙砂可溶锌率作了全面的探讨。
1.4 在除杂方面的研究
吴仲[14]在低温氧化焙烧、高过剩空气系数高温氧化焙烧、低过剩空气系数高温氧化焙烧3种不同的条件下对锌精矿沸腾焙烧过程中砷锑杂质的脱除率进行了比较,发现在较低过剩空气系数高温氧化焙烧的前提下,采用焙烧温度为1170
~1200℃、焙烧强度为7.0 t(干矿)/(m2·d)、炉底鼓风量为7300~7620 m3/h的操作条件对锌精矿进行高低过剩空气系数交替高温氧化焙烧,砷的脱除率达到68.5%以上,锑的脱除率达到69%以上。
2 结语
目前,在我国,湿法炼锌过程中的沸腾焙烧技术已经很成熟,研究它的科技工作者也很多,在今后的研究中,研究方向将朝着改善环境,发展绿色技术,清
洁生产;降低能耗和各种材料消耗,实现设备大型化、机械化和高度自动化,发挥最大的经济效益,发展循环经济的方向发展。