2.煤气发生炉工作原理
煤气发生炉工作原理与结构

煤气发生炉工作原理与煤气发生炉煤气成分在一般的煤气发生炉中,煤是由上而下、气化剂则是由下而上地进行逆流运动,它们之间发生化学反应和热量交换。
一、煤气发生炉内部在煤气发生炉中形成了几个区域,一般我们称为“层”。
按照煤气发生炉内气化过程进行的程序,可以将发生炉内部分为六层:1、灰渣层;2、氧化层(又称火层);3、还原层;4、干馏层;5、干燥层;6、空层。
其中氧化层和还原层又统称为反应层,干馏层和干燥层又统称为煤料准备层。
(1)灰渣层:煤燃烧后产生灰渣,形成灰渣层,它在发生炉的最下部,覆盖在炉篦子之上。
其主要作用为:A、保护炉篦和风帽,使它们不被氧化层的高温烧坏;B、预热气化剂,气化剂从炉底进入后,首先经过灰渣层进行热交换,使灰渣层温度降低,气化剂温度升高。
一般气化剂能预热达300-450℃左右。
C、灰渣层还起了布风作用,使进入的气化剂在炉膛内尽量均匀分布。
(2)氧化层:也称为燃烧层(火层)。
从灰渣中升上来的气化剂中的氧与碳发生剧烈的燃烧而生成二氧化碳,并放出大量的热量。
它是气化过程中的主要区域之一,其主要反应是:C+O2→CO2+97650大卡。
氧化层的高度一般为所有燃料块度的3-4倍,一般为100-200毫米。
气化层的温度一般要小于煤的灰熔点,控制在1200℃左右。
(3)还原层:在氧化层的上面是还原层。
赤热的碳具有很强的夺取氧化物中的氧而与之化合的本领,所以在还原层中,二氧化碳和水蒸气被碳还原成一氧化碳和氢气。
这一层也因此而得名,称为还原层。
其主要反应为:CO+C→2CO+38790大卡,H2O+C→H2+CO+28380大卡,2H2O+C→CO2+2H2+17970大卡。
由于还原层位于氧化层之上,从上升的气体中得到大量热量,因此还原层有较高的温度约800-1100℃,这就为需要吸收热量的还原反应提供了条件。
而严格地讲,还原层还有第一、第二之分,下部温度较高的地方称第一还原层,温度达950-1100℃,其厚度为300-400毫米左右;第二层为700-950℃之间,其厚度为第一还原层1.5倍,约在450毫米左右。
煤气发生炉的工作原理
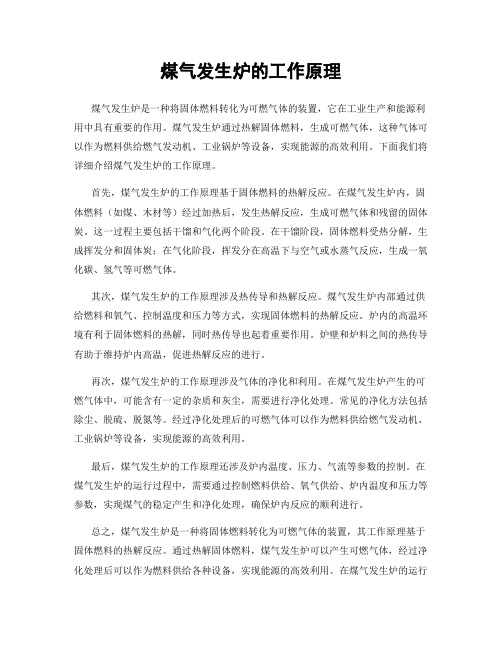
煤气发生炉的工作原理煤气发生炉是一种将固体燃料转化为可燃气体的装置,它在工业生产和能源利用中具有重要的作用。
煤气发生炉通过热解固体燃料,生成可燃气体,这种气体可以作为燃料供给燃气发动机、工业锅炉等设备,实现能源的高效利用。
下面我们将详细介绍煤气发生炉的工作原理。
首先,煤气发生炉的工作原理基于固体燃料的热解反应。
在煤气发生炉内,固体燃料(如煤、木材等)经过加热后,发生热解反应,生成可燃气体和残留的固体炭。
这一过程主要包括干馏和气化两个阶段。
在干馏阶段,固体燃料受热分解,生成挥发分和固体炭;在气化阶段,挥发分在高温下与空气或水蒸气反应,生成一氧化碳、氢气等可燃气体。
其次,煤气发生炉的工作原理涉及热传导和热解反应。
煤气发生炉内部通过供给燃料和氧气、控制温度和压力等方式,实现固体燃料的热解反应。
炉内的高温环境有利于固体燃料的热解,同时热传导也起着重要作用。
炉壁和炉料之间的热传导有助于维持炉内高温,促进热解反应的进行。
再次,煤气发生炉的工作原理涉及气体的净化和利用。
在煤气发生炉产生的可燃气体中,可能含有一定的杂质和灰尘,需要进行净化处理。
常见的净化方法包括除尘、脱硫、脱氮等。
经过净化处理后的可燃气体可以作为燃料供给燃气发动机、工业锅炉等设备,实现能源的高效利用。
最后,煤气发生炉的工作原理还涉及炉内温度、压力、气流等参数的控制。
在煤气发生炉的运行过程中,需要通过控制燃料供给、氧气供给、炉内温度和压力等参数,实现煤气的稳定产生和净化处理,确保炉内反应的顺利进行。
总之,煤气发生炉是一种将固体燃料转化为可燃气体的装置,其工作原理基于固体燃料的热解反应。
通过热解固体燃料,煤气发生炉可以产生可燃气体,经过净化处理后可以作为燃料供给各种设备,实现能源的高效利用。
在煤气发生炉的运行过程中,需要控制炉内温度、压力、气流等参数,确保煤气的稳定产生和净化处理。
这就是煤气发生炉的工作原理。
两段式煤气发生炉工作原理
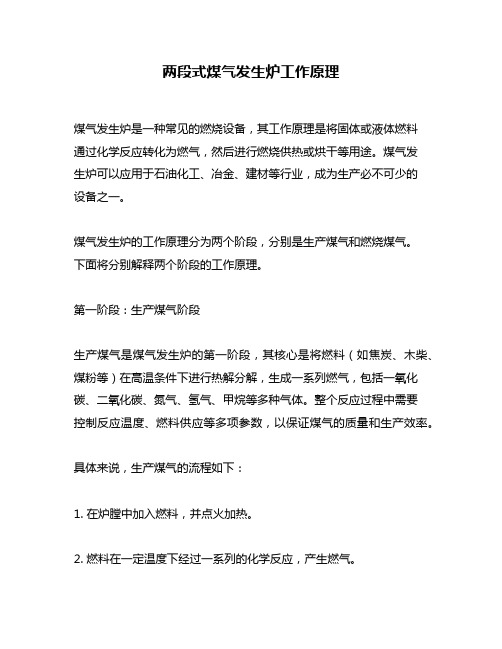
两段式煤气发生炉工作原理煤气发生炉是一种常见的燃烧设备,其工作原理是将固体或液体燃料通过化学反应转化为燃气,然后进行燃烧供热或烘干等用途。
煤气发生炉可以应用于石油化工、冶金、建材等行业,成为生产必不可少的设备之一。
煤气发生炉的工作原理分为两个阶段,分别是生产煤气和燃烧煤气。
下面将分别解释两个阶段的工作原理。
第一阶段:生产煤气阶段生产煤气是煤气发生炉的第一阶段,其核心是将燃料(如焦炭、木柴、煤粉等)在高温条件下进行热解分解,生成一系列燃气,包括一氧化碳、二氧化碳、氮气、氢气、甲烷等多种气体。
整个反应过程中需要控制反应温度、燃料供应等多项参数,以保证煤气的质量和生产效率。
具体来说,生产煤气的流程如下:1. 在炉膛中加入燃料,并点火加热。
2. 燃料在一定温度下经过一系列的化学反应,产生燃气。
3. 燃气经过水冷却,去除其中大部分的固态颗粒和小部分液态物质,得到煤气。
第二阶段:燃烧煤气阶段燃烧煤气是煤气发生炉的第二阶段,其核心是将生产的煤气送入燃烧室进行燃烧。
燃烧时需要保证煤气与空气的比例严格控制,以确保完全燃烧,并通过调节燃烧室的温度和风量来达到所需的供热或烘干效果。
具体来说,燃烧煤气的流程如下:1. 将生产的煤气送入燃烧室。
2. 在燃烧室中分别控制煤气和空气的供应量,保证其比例合适,实现完全燃烧。
3. 焚烧产生的高温烟气经过换热器进行热回收,以提高能源利用效率。
综上所述,煤气发生炉的工作原理分为生产煤气和燃烧煤气两个阶段。
其生产过程中需要控制多项参数,以保证煤气质量和生产效率。
燃烧过程中需要严格控制煤气和空气的供应量,保证完全燃烧,并通过热回收提高能源利用效率。
煤气发生炉基础知识

煤气发生炉基础知识煤气发生炉是一种用于生产合成气的设备,其主要原理是将燃料(通常是煤、木材或其他有机物)在缺氧或部分缺氧的条件下进行热解,产生一种含有可燃气体和一些有害气体的混合气体。
这种气体可以被进一步处理成合成气,用于各种工业生产和能源供应。
在使用煤气发生炉进行合成气生产之前,我们必须了解一些基础知识。
在本篇文档中,我们将介绍煤气发生炉的工作原理、炉体结构、操作要点以及安全措施等方面的知识。
1. 工作原理煤气发生炉的主要工作原理是在缺氧或部分缺氧的条件下,将燃料在高温下分解成气体。
具体来说,当燃料进入炉膛时,先经过预热的反应器内,接着燃料在干燥炉中进行脱水处理,随后由焙烧段进入热解器进行高温分解,产生一种含有可燃气体和一些有害气体的混合气体。
最后,由于燃料与空气的燃烧反应,混合气体中的可燃物质被完全燃烧,产生大量的热能。
2. 炉体结构煤气发生炉的炉体结构可以分为四个部分:预热器、干燥炉、焙烧段和热解器。
在使用许多煤气发生炉时,还会增加煤气净化装置和煤气储存罐等辅助设备。
预热器是炉体结构中的第一个部分,用于预热和热解固体燃料。
在预热器中,燃料被逐渐升温,并在炉体内的高温下分解成气体。
燃料在预热过程中会先与发生炉内的燃烧气体进行热交换,因此能够充分利用燃料中的热能。
干燥炉是炉体结构中的第二个部分,用于将燃料中的水分蒸发。
燃料在干燥炉中暴露于高温、低氧的环境中,使其逐渐脱水并分解成气体。
焙烧段是炉体结构中的第三个部分,其作用是将经过干燥处理的燃料进一步热解,产生含有可燃气体和一些有害气体的混合气体。
在这个过程中,由于在干燥炉中蒸发的水分被逐渐分解,燃料中的碳和其他元素会形成含有炭黑的灰渣,减小了灰份的含量。
热解器是炉体结构中的第四个部分,用于进一步分解焙烧段中产生的混合气体。
在热解器中,混合气体通过难燃性材料的各种感应和热交换表面,让大部分可燃气体完全热分解成燃烧气体。
3. 操作要点在操作煤气发生炉时,我们需要注意以下几点要点:(1)炉体内部的温度和气流状态应该保持充足的供氧,并逐步增加进风速度和更换进风量。
煤气发生炉的工作原理
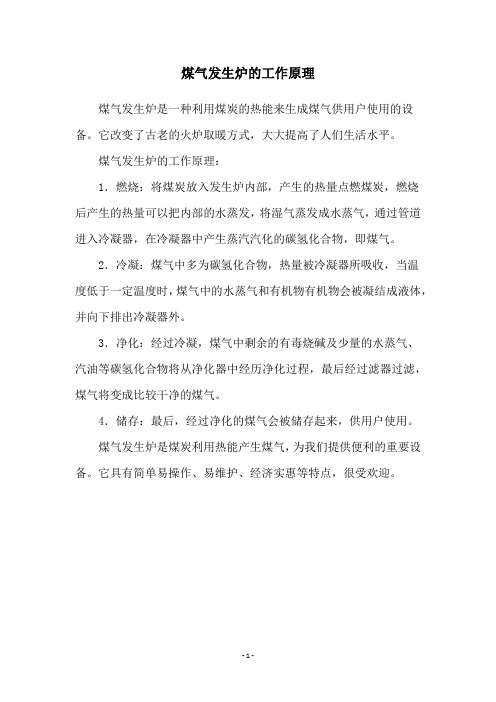
煤气发生炉的工作原理
煤气发生炉是一种利用煤炭的热能来生成煤气供用户使用的设备。
它改变了古老的火炉取暖方式,大大提高了人们生活水平。
煤气发生炉的工作原理:
1.燃烧:将煤炭放入发生炉内部,产生的热量点燃煤炭,燃烧
后产生的热量可以把内部的水蒸发,将湿气蒸发成水蒸气,通过管道进入冷凝器,在冷凝器中产生蒸汽汽化的碳氢化合物,即煤气。
2.冷凝:煤气中多为碳氢化合物,热量被冷凝器所吸收,当温
度低于一定温度时,煤气中的水蒸气和有机物有机物会被凝结成液体,并向下排出冷凝器外。
3.净化:经过冷凝,煤气中剩余的有毒烧碱及少量的水蒸气、
汽油等碳氢化合物将从净化器中经历净化过程,最后经过滤器过滤,煤气将变成比较干净的煤气。
4.储存:最后,经过净化的煤气会被储存起来,供用户使用。
煤气发生炉是煤炭利用热能产生煤气,为我们提供便利的重要设备。
它具有简单易操作、易维护、经济实惠等特点,很受欢迎。
- 1 -。
煤气发生炉工作原理与结构
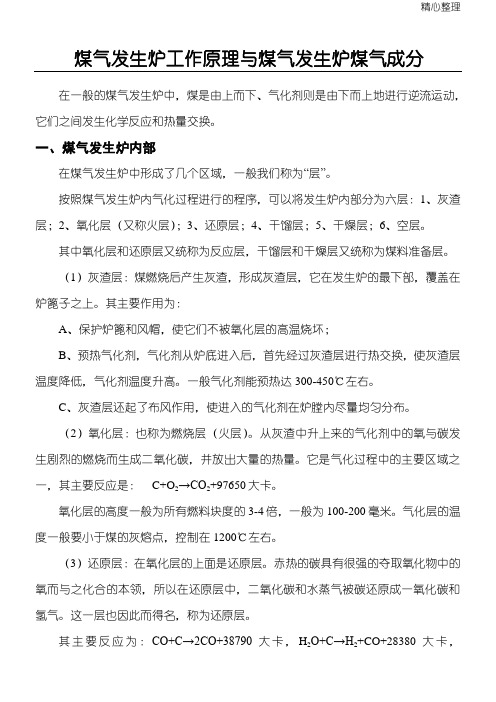
精心整理煤气发生炉工作原理与煤气发生炉煤气成分在一般的煤气发生炉中,煤是由上而下、气化剂则是由下而上地进行逆流运动,它们之间发生化学反应和热量交换。
一、煤气发生炉内部在煤气发生炉中形成了几个区域,一般我们称为“层”。
层;2(A B C (度一般要小于煤的灰熔点,控制在1200℃左右。
(3)还原层:在氧化层的上面是还原层。
赤热的碳具有很强的夺取氧化物中的氧而与之化合的本领,所以在还原层中,二氧化碳和水蒸气被碳还原成一氧化碳和氢气。
这一层也因此而得名,称为还原层。
其主要反应为:CO+C→2CO+38790大卡,H 2O+C→H 2+CO+28380大卡,2H2O+C→CO2+2H2+17970大卡。
由于还原层位于氧化层之上,从上升的气体中得到大量热量,因此还原层有较高的温度约800-1100℃,这就为需要吸收热量的还原反应提供了条件。
而严格地讲,还原层还有第一、第二之分,下部温度较高的地方称第一还原层,温度达950-1100℃,其厚度为300-400毫米左右;第二层为700-950℃之间,其厚度为第一还原层1.5倍,约在450毫米左右。
((在室温层高。
(CO单叙述,我们可以看出煤气发生炉内进行的气化过程是比较复杂的,既有气化反应,也有干馏和干燥过程。
而且在实际生产的发生炉中,分层也不是很严格的,相邻两层往往是相互交错的,各层的温度也是逐步过渡的,很难具体划分,各层中气体成份的变化就更加复杂了,即使在专门的研究中,看法也是分歧的。
二、煤气炉的结构对于固定床煤气炉有多种结构型式,按不同部位分述如下:1、加煤装置:间歇式加煤罩、双料钟、振动给煤机、拨齿加煤机。
2、炉体结构:带压力全水套、半水套、无水套(耐火材料炉衬)、常压全水套。
3、炉篦:宝塔型、型钢焊接型。
4、灰盘传动结构:拨齿型、蜗轮蜗杆型。
三、煤气发生炉煤气成分所谓煤气发生炉炉出煤气,是指煤在煤气发生炉内气化反应所产生的,自煤气2、煤气中的H2S煤气中的H2S含量多少与气化用煤中的含硫多少有关,一般煤中硫分的80%以H2S状态转入煤气中,20%的硫分残留在灰渣中。
煤气发生炉工作原理与结构
煤气发生炉工作原理与煤气发生炉煤气成分在一般的煤气发生炉中,煤是由上而下、气化剂则是由下而上地进行逆流运动,它们之间发生化学反应和热量交换。
一、煤气发生炉内部在煤气发生炉中形成了几个区域,一般我们称为“层”。
按照煤气发生炉内气化过程进行的程序,可以将发生炉内部分为六层:1、灰渣层;2、氧化层(又称火层);3、还原层;4、干馏层;5、干燥层;6、空层。
其中氧化层和还原层又统称为反应层,干馏层和干燥层又统称为煤料准备层。
(1)灰渣层:煤燃烧后产生灰渣,形成灰渣层,它在发生炉的最下部,覆盖在炉篦子之上。
其主要作用为:A、保护炉篦和风帽,使它们不被氧化层的高温烧坏;B、预热气化剂,气化剂从炉底进入后,首先经过灰渣层进行热交换,使灰渣层温度降低,气化剂温度升高。
一般气化剂能预热达300-450℃左右。
C、灰渣层还起了布风作用,使进入的气化剂在炉膛内尽量均匀分布。
(2)氧化层:也称为燃烧层(火层)。
从灰渣中升上来的气化剂中的氧与碳发生剧烈的燃烧而生成二氧化碳,并放出大量的热量。
它是气化过程中的主要区域之一,其主要反应是:C+O2→CO2+97650大卡。
氧化层的高度一般为所有燃料块度的3-4倍,一般为100-200毫米。
气化层的温度一般要小于煤的灰熔点,控制在1200℃左右。
(3)还原层:在氧化层的上面是还原层。
赤热的碳具有很强的夺取氧化物中的氧而与之化合的本领,所以在还原层中,二氧化碳和水蒸气被碳还原成一氧化碳和氢气。
这一层也因此而得名,称为还原层。
其主要反应为:CO+C→2CO+38790大卡,H2O+C→H2+CO+28380大卡,2H2O+C→CO2+2H2+17970大卡。
由于还原层位于氧化层之上,从上升的气体中得到大量热量,因此还原层有较高的温度约800-1100℃,这就为需要吸收热量的还原反应提供了条件。
而严格地讲,还原层还有第一、第二之分,下部温度较高的地方称第一还原层,温度达950-1100℃,其厚度为300-400毫米左右;第二层为700-950℃之间,其厚度为第一还原层1.5倍,约在450毫米左右。
煤气发生炉的工作原理
煤气发生炉的工作原理
煤气发生炉是一种能够将固体煤炭转化为可燃气体的设备。
它的工作原理基于化学反应,主要包括炉膛预热、干馏和气体化三个阶段。
首先,在炉膛预热阶段,煤气发生炉需要加热炉膛到一定温度。
通常会使用点火器或者预热器等设备来提供必要的热量,使炉膛内的温度达到煤气化反应需要的范围。
接下来,在干馏阶段,煤炭开始分解,并释放出一些揮发分,如挥发性有机物、水蒸气等。
这些挥发分在高温下分解形成气体状的产物,例如一氧化碳(CO)、氢气(H2)以及一些不
稳定的碳氢化合物。
最后,在气化阶段,这些产物由煤气化剂(通常是蒸汽、氧气或二氧化碳)与剩余煤炭反应,生成更多的一氧化碳和氢气。
同时,部分不稳定的碳氢化合物会进一步裂解,产生更多的可燃气体。
这些可燃气体会通过气体出口离开炉膛,成为可用于能源供应、化学产品合成等用途的煤气。
总结起来,煤气发生炉的工作原理就是通过加热和化学反应来使固体煤炭分解并转化为可燃气体。
这个过程需要合适的温度、煤气化剂以及一系列反应来实现。
煤气发生炉工作原理
煤气发生炉工作原理
煤气发生炉是一种用于生产合成气体的设备,它通过煤或其他碳质物质的热解过程,产生一种可燃气体,其中主要成分是一氧化碳和氢气。
煤气发生炉工作原理的核心是煤的热解反应,下面我们来详细了解一下煤气发生炉的工作原理。
首先,煤气发生炉内部的煤气化过程是通过煤与空气或者氧气的反应来实现的。
当煤在高温下遇热分解时,会产生一氧化碳和氢气,这个过程称为煤气化。
煤气发生炉内部的煤气化反应需要在高温下进行,通常在800°C以上才能够有效进行。
因此,煤气发生炉内部需要提供足够的热量来维持煤的热解反应。
其次,煤气发生炉内部的煤气化反应需要控制氧气的供给和煤料的输送速度,以确保煤料在炉内充分接触空气或氧气,从而实现有效的煤气化。
同时,煤气发生炉还需要排出煤气化过程中产生的煤气和煤渣,以保持炉内的稳定工作状态。
最后,煤气发生炉产生的合成气体需要通过净化和冷却处理,以去除其中的杂质和降低温度,从而得到符合要求的合成气体。
这个过程通常包括除尘、脱硫、脱氮等步骤,以确保合成气体的质量
和安全性。
总的来说,煤气发生炉的工作原理是通过煤的热解反应产生合成气体,然后经过净化和处理得到可用的合成气体。
这个过程需要控制炉内的温度、氧气供给和煤料输送速度,同时需要对产生的合成气体进行净化和冷却处理。
煤气发生炉在工业生产中具有重要的应用价值,能够为工业生产提供可靠的燃料和原料来源。
煤气发生炉原理
煤气发生炉原理
煤气发生炉是一种将固体燃料转化为可燃气体的装置,它是工业生产和能源利用中的重要设备。
煤气发生炉的原理是通过热解固体燃料,产生可燃气体,然后将其用作燃料进行燃烧。
下面我们将详细介绍煤气发生炉的原理。
首先,煤气发生炉的主要原理是热解固体燃料。
在煤气发生炉内部,固体燃料(如煤、木材等)在缺氧或氧气不足的环境下受热分解,产生可燃气体。
这个过程主要包括干馏和气化两个阶段。
干馏是指在高温下,固体燃料中的挥发性成分被分解出来,产生液体和气体。
气化是指在高温下,固体燃料中的非挥发性成分被分解成一氧化碳和氢气等可燃气体。
其次,煤气发生炉的原理还涉及气体净化。
由于煤气发生炉产生的气体中含有一定的固体颗粒和有害气体,需要经过净化处理才能作为燃料使用。
气体净化一般包括除尘、脱硫、脱氮等工艺,通过这些工艺可以将固体颗粒和有害气体去除,从而得到清洁的可燃气体。
最后,煤气发生炉的原理还包括燃烧利用。
经过热解和净化处理后的可燃气体可以用作燃料进行燃烧,产生热能或动力。
燃烧利用是煤气发生炉的最终目的,通过燃烧可燃气体可以产生热能,用于工业生产或供暖,也可以产生动力,用于驱动发电机等设备。
综上所述,煤气发生炉的原理主要包括热解固体燃料、气体净化和燃烧利用三个方面。
通过这些原理,煤气发生炉可以将固体燃料转化为可燃气体,并将其用作燃料进行燃烧,从而产生热能或动力。
煤气发生炉在工业生产和能源利用中具有重要的地位,它的原理和工艺对于提高能源利用效率和减少环境污染具有重要意义。
- 1、下载文档前请自行甄别文档内容的完整性,平台不提供额外的编辑、内容补充、找答案等附加服务。
- 2、"仅部分预览"的文档,不可在线预览部分如存在完整性等问题,可反馈申请退款(可完整预览的文档不适用该条件!)。
- 3、如文档侵犯您的权益,请联系客服反馈,我们会尽快为您处理(人工客服工作时间:9:00-18:30)。
4) 送气时因炉出钟罩阀落下过早导致炉 底爆炸;
5) 联锁失灵,鼓风机或加压机跳闸,导 致炉底爆炸;
2、
防范措施:
1) 使用自动调节时,流量不宜过小,以防煤气 倒流;
2) 确;
在停送气时要统一指挥,密切配合,分工明
3) 定时检查各入孔及水封是否正确;
4) 定期检查各联锁是否正确;
(三)发生炉炉体爆炸事故
煤气站特点 :(一)在整个冷煤气净化工艺中, 底部煤气的处理采用旋风除尘器,强制风冷 器来进行,改变了我国两段炉常用的双竖管、 洗涤塔用水冷却工艺,即节约了生产用水, 又消除了因使用传统工艺带来的酚水量太大 弊端,从而彻底杜绝了国内传统的两段炉对 环境的污染问题。顶部煤气中的大量焦油采 用 37 管电捕器捕集,因其流动性良好,可 直接输送到焦油池储存。
混合煤气采用油洗冷却器冷却,此设备的特 点是,煤气的冷却不与水直接接触,而是管 板式间接冷却,再通过煤气自身冷凝下来的 饱和水(含酚)循环使用洗涤煤气,使煤气 站酚水减至最少量,此少量酚水为正增长, 它的输送储存皆密闭进行。
在整个工艺中,对焦油的捕集采用二级电捕,以 确保在冷煤气净化过程中焦油的含量在 40mg/m3 以下。顶部煤气用 37 管电捕焦,煤 气在其中最大流速为 0.6m /s ,低于《发生炉煤 气站设计规范》(GB50195-94 )中的 61管电 捕青油器,煤气在其中的最大流速为 0.65m /s 低于《发生炉煤气站设计规范》( GB50195-94 ) 中的 0.8m /s 的要求。
1、
事故原因:
Байду номын сангаас
1) 钟罩阀堵塞,用火烧钟罩阀引起炉体 爆炸;
2) 联锁失灵,鼓风机或加压机跳闸导致 炉体爆炸;
3) 运行中检修加煤机引起炉体爆炸;
4) 汽包缺水造成炉体水套爆炸;
5) 汽包超压导致水套爆炸; 6) 水套补水过急,流入空气管导致炉体
爆炸; 7) 停气吹扫因水封回阀门不严导致炉体
(2)氧化层: 也称为燃烧层(火层)。从 灰渣中升上来的气化剂中的氧与碳发生剧烈 的燃烧而生成二氧化碳,并放出大量的热量。 它是气化过程中的主要区域之一,其主要反 应是:C O2→CO2氧化层的高度一般为所 有燃料块度的3-4倍,一般为200毫米。气 化层的温度一般要小于煤的灰熔点.
(3)还原层: 在氧化层的上面是还原层。 赤热的碳具有很强的夺取氧化物中的氧而与 之化合的本领,所以在还原层中,二氧化碳 和水蒸气被碳还原成一氧化碳和氢气。这一 层也因此而得名,称为还原层,其主要反应 为:CO C→2CO<BR>H2O C→H2 CO<BR>2H2O C→CO2 2H2
动火工作票; 2).加压机检修后,经吹扫后,才能试车;
(六)贮煤斗爆炸事故 1、事故原因: 1).检修加煤机动火引起爆炸; 2).加煤机卡,处理不当引起爆炸; 2、防范措施: 1).动火检修时要做好安全防火措施; 2).处理加煤机卡时,上下应密切配合,
煤阀应开启缓慢;
二、着火事故案例分析 (一)贮煤斗着火事故 1、事故原因: 1).检修贮煤仓时火花落入煤斗; 2).其他火源引入(如烟斗及燃着物); 3).检修输煤带时带入火源;
这样在煤气发生炉中形成了几个区域,一般 我们称为“层”。 按照煤气发生炉内气化 过程进行的程序,可以将发生炉内部分为六 层1)灰渣层;2)氧化层(又称火层);
3)还原层;4)干馏层;5)干燥层;
6)空层;其中氧化层和还原层又统称为反 应层,干馏层和干燥层又统称为煤料准备层。
(1)灰渣层: 煤燃烧后产生灰渣,形成灰 渣层,它在发生炉的最下部,覆盖在炉篦子 之上。其主要作用为: a保护炉篦和风帽, 使它们不被氧化层的高温烧坏; b预热气化 剂,气化剂从炉底进入后,首先经过灰渣层 进行热交换,使灰渣层温度降低,气化剂温 度升高。 c灰渣层还起了布风作用,使进入 的气化剂在炉膛内尽量均匀分布。
3) 在全站停电或停气时,要严格按照操作规程 操作;
4) 在处理全站事故情况下要统一指挥,互相配 合,分工明确;
5) 加强劳动纪律,严格工作岗位;
二)发生炉炉底爆炸事故
1、
事故原因:
1) 自控煤气炉翻板关闭引起炉爆炸;
2) 送气时因两炉炉出压力过大引起炉底 爆炸;
3) 炉底入孔未封严引起炉爆炸;
(四)电捕焦操作事故
1、
事故原因:
1) 检修动火引起电捕焦爆炸;
2)
未吹扫或吹扫不彻底,动火检修引起电捕
焦爆炸;
3)
送气时未经吹扫或吹扫不彻底,电捕焦送
电造成爆炸;
4) 送入不合格煤气造成电捕焦爆炸;
5) 炸;
因联锁失灵,鼓风机跳闸,造成电捕焦爆
2、
防范措施、
1) 在煤气管道内动火,要先吹扫,并办理动火 工作票;
3) .全站停电引起空气管道爆炸: a.全站停电处理不当 b.全站停电误操作 c.全站停电未处理; 4) .全站停气时未拉开钟罩阀引起空气总管爆
炸; 5) .鼓风机、加压机停车未停加煤机引起爆炸;
2、
防范措施:
1) 加强技术培训,提高职工的事故判断能力和 事故处理水平;
2) 鼓风机、加压机或“双停车”时,要维持正 压操作;
2、防范措施: 1).检修动火或其他工作时应采取安全措施
杜绝火花落入煤斗; 2).输煤带内禁止吸烟; 3).提高人员素质,增强防火意识;
(二)室外净化区域着火事故
1、事故原因: 1).发生炉出口放散管经雷击着火; 2).旋风除尘器动火引起着火; 3).电捕焦送电未吹扫引起火灾; 4).焦油池着火引起火灾; 5).检修净化设备引起火灾; 6).电缆沟着火引起火灾; 7).其他外来火源引入导致火灾;
(四)厂区管网设备事故
1、 1)
停气; 2) 3) 2、 1) 2)
事故原因: 煤气管道防爆破自然破裂造成全厂
煤气管道下坠引起焊缝开裂; 翻斗车作业撞裂煤气管道;
防范措施: 定期对管道防爆破进行检查; 煤气管道的托架要坚固;
山西省吕梁市“5·17”煤气发生炉爆炸事故
2012年5月17日6时30分左右,吕梁市恒原耐材有限公司 煤气发生炉发生爆炸,造成3人死亡、1人受伤。
三、中毒事故案例分析 (一)主厂房中毒事故 1、事故原因: 1).煤气管道泄露,未及时发现; 2).误操作导致煤气管道破裂; 3).钟罩阀水封破坏; 4).检修炉未按操作规程进行;
2、防范措施: 1).加强培训,提高职工技术水平,严守岗
位; 2).及时检查各水封正常; 3).佩带好防护用品,并按照规程进行操作;
(4)干馏层: 就是把煤中的挥发份,焦油 等物质经过加热后所产生的CmHm化合物 分离出来,然后再进入还原进行化学反应,其 高度为200厚
(5)干燥层: 干燥层位于干馏层上面,也 即是燃料的面层,主要是把煤中的水发蒸发 即可
(6)空层: 空层即燃料层上部,炉体内的 自由区,其主要作用是汇集煤气。然后出去 2CO→CO2 C以及2H2O CO→CO2 H2
从上面六层简单叙述,我们可以看出煤气发 生炉内进行的气化过程是比较复杂的,既有 气化反应,也有干馏和干燥过程。而且在实 际生产的发生炉中,分层也不是很严格的, 相邻两层往往是相互交错的,各层的温度也 是逐步过渡的,很难具体划分,各层中气体 成份的变化就更加复杂了,即使在专门的研 究中,看法也是分歧的.
2) 要保证灰盘内有充足的密封水;
3) 根据炉内层次适当除灰;
(三)鼓风机、加压机轴承损坏事故
1、
事故原因:
1) 风机大修后中心不对导致轴承损坏;
2) 风机轴承振动导致轴承损坏;
3) 轴承缺油导致轴承损坏;
2、
防范措施:
1) 风机大修后要复查中心正确;
2) 定期给轴承加油;
3) 定时巡检设备,发现问题及时切换
二、事故经过
据初步了解,2012年5月16日,该企业负责人从临县招募 一批农民工开始生产准备,于16日11时左右点火,3号窑 开始生产。5月17日事发时,现场作业人员共11人,其中: 3人在煤气发生炉水套顶板操作台作业,1人在地面加煤 (4人均为16日招募的农民工,企业用工花名册未予登记, 参加过煤气作业培训人员均不在作业现场);其余作业人 员从事现场杂务,距煤气发生炉距离较远。6时30分左右, 该厂煤气发生炉发生爆炸,导致3人死亡(操作台作业人 员)、1人受伤(地面加煤作业)。
(二)输煤通廊和贮煤斗区域中毒 1、事故原因: 1).单人进入贮煤斗工作时发生中毒; 2).不慎掉入贮煤斗中毒; 3).在输煤通道或厂房附近休息发生中毒;
2、防范措施: 1).进入贮煤斗工作时,要有专人监护; 2).进入贮煤斗工作时,要将煤气吹扫彻底; 3).严禁在煤气通道或附近休息;
措施; 3) 所有人员禁止在设备附近休息; 4) 工作时要戴好防护用品,以防中毒; 5) 加强安全教育,提高职工的安全意识;
四设备事故原因
(一)水套烧坏事故
1、
事故原因;
1) 因长期使用自来水,导致水套结垢;
2) 软化水中断,未及时发现;
3) 水位计失灵造成假水位;
2、
防范措施:
1) 若长期使用自来水,要定期排垢;
爆炸; 8) 热备炉检修造成炉体爆炸; 9) 热备炉启动操作失误造成炉挑剔爆炸;
2、
防范措施:
1) 处理钟罩阀堵塞时,要用蒸汽吹或用其他工 具捅、掏、不能用火烧;
2) 运行中对设备进行检修时要做防护措施,动 火要办理动火工作票;
3) 汽包缺水时应先对气包进行“叫水”;
4) 定期检查气包安全阀压力表是否正常;
2) 在送气之前要对电捕焦进行充分吹扫;
3)
送气时要化验煤气合格,氧气含量不超过
0.8%;
4) 要定期检查鼓风机和加压机的联动试验;
(五)加压机爆炸事故 1、事故原因: 1).加压机检修动火,措施不当,引起爆