煤气发生炉工作原理与结构
煤气发生炉的工作原理
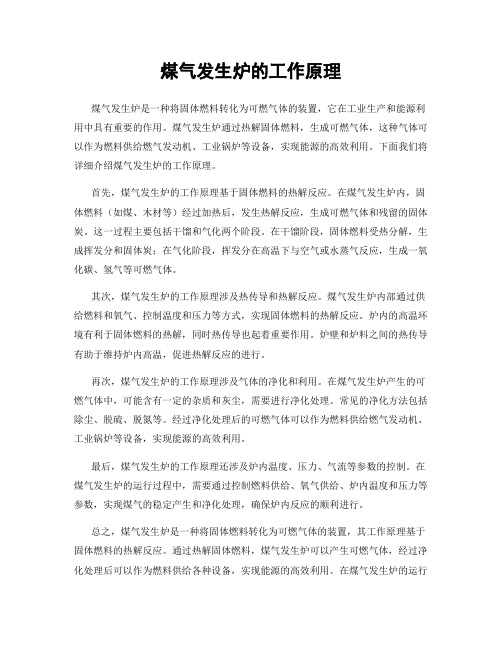
煤气发生炉的工作原理煤气发生炉是一种将固体燃料转化为可燃气体的装置,它在工业生产和能源利用中具有重要的作用。
煤气发生炉通过热解固体燃料,生成可燃气体,这种气体可以作为燃料供给燃气发动机、工业锅炉等设备,实现能源的高效利用。
下面我们将详细介绍煤气发生炉的工作原理。
首先,煤气发生炉的工作原理基于固体燃料的热解反应。
在煤气发生炉内,固体燃料(如煤、木材等)经过加热后,发生热解反应,生成可燃气体和残留的固体炭。
这一过程主要包括干馏和气化两个阶段。
在干馏阶段,固体燃料受热分解,生成挥发分和固体炭;在气化阶段,挥发分在高温下与空气或水蒸气反应,生成一氧化碳、氢气等可燃气体。
其次,煤气发生炉的工作原理涉及热传导和热解反应。
煤气发生炉内部通过供给燃料和氧气、控制温度和压力等方式,实现固体燃料的热解反应。
炉内的高温环境有利于固体燃料的热解,同时热传导也起着重要作用。
炉壁和炉料之间的热传导有助于维持炉内高温,促进热解反应的进行。
再次,煤气发生炉的工作原理涉及气体的净化和利用。
在煤气发生炉产生的可燃气体中,可能含有一定的杂质和灰尘,需要进行净化处理。
常见的净化方法包括除尘、脱硫、脱氮等。
经过净化处理后的可燃气体可以作为燃料供给燃气发动机、工业锅炉等设备,实现能源的高效利用。
最后,煤气发生炉的工作原理还涉及炉内温度、压力、气流等参数的控制。
在煤气发生炉的运行过程中,需要通过控制燃料供给、氧气供给、炉内温度和压力等参数,实现煤气的稳定产生和净化处理,确保炉内反应的顺利进行。
总之,煤气发生炉是一种将固体燃料转化为可燃气体的装置,其工作原理基于固体燃料的热解反应。
通过热解固体燃料,煤气发生炉可以产生可燃气体,经过净化处理后可以作为燃料供给各种设备,实现能源的高效利用。
在煤气发生炉的运行过程中,需要控制炉内温度、压力、气流等参数,确保煤气的稳定产生和净化处理。
这就是煤气发生炉的工作原理。
两段式煤气发生炉内部构造
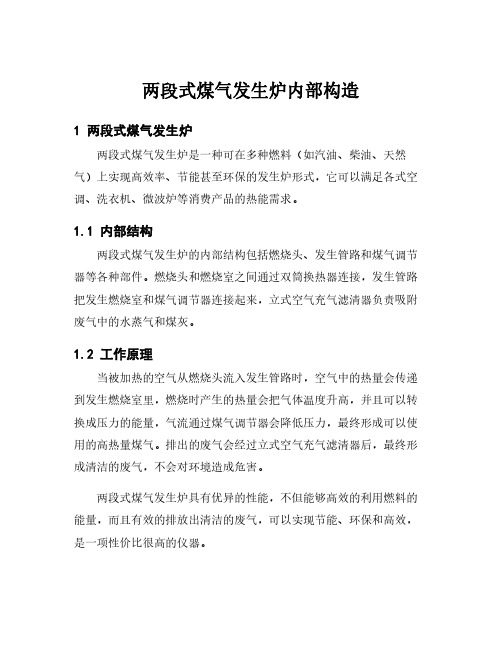
两段式煤气发生炉内部构造
1两段式煤气发生炉
两段式煤气发生炉是一种可在多种燃料(如汽油、柴油、天然气)上实现高效率、节能甚至环保的发生炉形式,它可以满足各式空调、洗衣机、微波炉等消费产品的热能需求。
1.1内部结构
两段式煤气发生炉的内部结构包括燃烧头、发生管路和煤气调节器等各种部件。
燃烧头和燃烧室之间通过双筒换热器连接,发生管路把发生燃烧室和煤气调节器连接起来,立式空气充气滤清器负责吸附废气中的水蒸气和煤灰。
1.2工作原理
当被加热的空气从燃烧头流入发生管路时,空气中的热量会传递到发生燃烧室里,燃烧时产生的热量会把气体温度升高,并且可以转换成压力的能量,气流通过煤气调节器会降低压力,最终形成可以使用的高热量煤气。
排出的废气会经过立式空气充气滤清器后,最终形成清洁的废气,不会对环境造成危害。
两段式煤气发生炉具有优异的性能,不但能够高效的利用燃料的能量,而且有效的排放出清洁的废气,可以实现节能、环保和高效,是一项性价比很高的仪器。
煤气发生炉的原理

煤气发生炉煤气发生炉是将煤炭转化为可燃性气体——煤气〔主要成分为CO、H2、CH4等〕的生产设备。
工作原理为:将符合气化工艺指标的煤炭筛选后,由加煤机参加到煤气炉,从炉底鼓入自产蒸汽与空气混合气体做为气化剂。
煤炭在炉经物理、化学反响,生成可燃性气体,上段煤气经过旋风除油器、电捕器过滤焦油.下段煤气经过旋风除尘器去除灰尘,经过混合后输送到用户使用。
广泛适用于轧钢炉、退火炉、锻造炉、钢管炉、玻璃炉、熔铝炉、铜材炉、建炉等各种热工炉所需温度围的各种炉形。
中文名:煤气发生炉外文名:Gas furnace用途:熔炼、退火、煤气站等使用原料:煤产出:煤气、焦油、炉渣主体材质:金属构造目录1工作原理.2根本用途.3主要分类.▪单段.▪双段.4配套设备.▪电捕焦油器.▪旋风除尘器.▪窑.5原料.6技术参数.▪环保标准.▪平安措施.▪煤气净化.▪蒸汽调节煤气发生炉工作原理发生炉煤气是通过水蒸气和空气混合形成气化剂后流经炽热的固定燃烧床生成的。
空气中所含的氧气、水蒸气与燃料中的碳反响,生成了共含有CO、CO2、H2、CH4、N2等成分的发生炉煤气。
与空气混合的蒸气提高了热效率,并降低了燃烧床的温度,从而控制了熔块的形成。
蒸气与碳反响是吸热反响:C+H2O=CO+H2-Q〔Q为热量,下同〕当氧气和碳反响时就放出热量:2C+O2=2CO+Q煤气发生炉工作原理燃烧床的温度取决于气化剂的饱和温度,燃料的粒度、类型及发生炉的炉型。
燃烧床的温度是非常重要的,因为对于给定的燃料和炉型,它决定着发生炉煤气的成分:在温度高的情况下,可产生大量的可燃气体。
因此,重要的是既保持燃烧床高温而又不会形成熔块。
形成熔块的温度取决于燃料的渣融特性,在氧气充足的情况下,还会出现两种反响:2CO+O2=2CO2+QC+O2=CO2+Q。
所以说,CO的产生并不一定意味着任何碳燃烧都能使煤气的热值降低。
另外,一些水蒸气还与CO反响,由于每体积CO转化为CO2时,同时生成了一样体积的H2:CO+H2O=CO2+H2。
煤气发生炉基础知识

煤气发生炉基础知识煤气发生炉是一种用于生产合成气的设备,其主要原理是将燃料(通常是煤、木材或其他有机物)在缺氧或部分缺氧的条件下进行热解,产生一种含有可燃气体和一些有害气体的混合气体。
这种气体可以被进一步处理成合成气,用于各种工业生产和能源供应。
在使用煤气发生炉进行合成气生产之前,我们必须了解一些基础知识。
在本篇文档中,我们将介绍煤气发生炉的工作原理、炉体结构、操作要点以及安全措施等方面的知识。
1. 工作原理煤气发生炉的主要工作原理是在缺氧或部分缺氧的条件下,将燃料在高温下分解成气体。
具体来说,当燃料进入炉膛时,先经过预热的反应器内,接着燃料在干燥炉中进行脱水处理,随后由焙烧段进入热解器进行高温分解,产生一种含有可燃气体和一些有害气体的混合气体。
最后,由于燃料与空气的燃烧反应,混合气体中的可燃物质被完全燃烧,产生大量的热能。
2. 炉体结构煤气发生炉的炉体结构可以分为四个部分:预热器、干燥炉、焙烧段和热解器。
在使用许多煤气发生炉时,还会增加煤气净化装置和煤气储存罐等辅助设备。
预热器是炉体结构中的第一个部分,用于预热和热解固体燃料。
在预热器中,燃料被逐渐升温,并在炉体内的高温下分解成气体。
燃料在预热过程中会先与发生炉内的燃烧气体进行热交换,因此能够充分利用燃料中的热能。
干燥炉是炉体结构中的第二个部分,用于将燃料中的水分蒸发。
燃料在干燥炉中暴露于高温、低氧的环境中,使其逐渐脱水并分解成气体。
焙烧段是炉体结构中的第三个部分,其作用是将经过干燥处理的燃料进一步热解,产生含有可燃气体和一些有害气体的混合气体。
在这个过程中,由于在干燥炉中蒸发的水分被逐渐分解,燃料中的碳和其他元素会形成含有炭黑的灰渣,减小了灰份的含量。
热解器是炉体结构中的第四个部分,用于进一步分解焙烧段中产生的混合气体。
在热解器中,混合气体通过难燃性材料的各种感应和热交换表面,让大部分可燃气体完全热分解成燃烧气体。
3. 操作要点在操作煤气发生炉时,我们需要注意以下几点要点:(1)炉体内部的温度和气流状态应该保持充足的供氧,并逐步增加进风速度和更换进风量。
煤气发生炉设备介绍及原理

碎渣圈用法兰和水夹套连为一体,其上部伸入炉膛,以保护水夹套下部使其免受灰渣的磨损,下部插入灰盘水中而形成水封。当炉篦转动时,炉篦与碎渣圈的内壁做相对运动,使大块灰渣破碎。碎渣圈下部装有2~5把小灰刀,可以把灰渣从炉内排出到灰盘内箱的组装图见图2-4所示。
灰盘与涡轮固定在一起,下部以其环形导轨座落在环形底座的钢球上,灰盘转动时钢球在上、下凹槽形导轨内滚动,以减少摩擦力。灰盘由钢板制成,内壁表面凸出的斜筋用于帮助大灰刀排灰。灰盘与碎渣圈共同组成灰盘水封。固定不动的大灰刀焊接在炉体及碎渣圈上,其下端插入灰盘水中,其水平夹角为30~400,灰盘转动时,灰盘中的灰渣沿着灰刀的斜面被排出。
40~60
耗煤量(kg/h)
900~1250
1500~2150
1660~2300
~2200
~2400
空气消耗量(m3/kg煤)
2.0~2.5
2.0~2.5
2.0~2.5
2.0~2.5
2.0~2.5
蒸汽消耗量(t/ h)(kg/kg煤)
0.3~0.5
0.3~0.5
0.3~0.5
0.3~0.5
0.3~0.5
煤气发生炉工艺及主要设备构造
煤气发生炉工作原理与结构
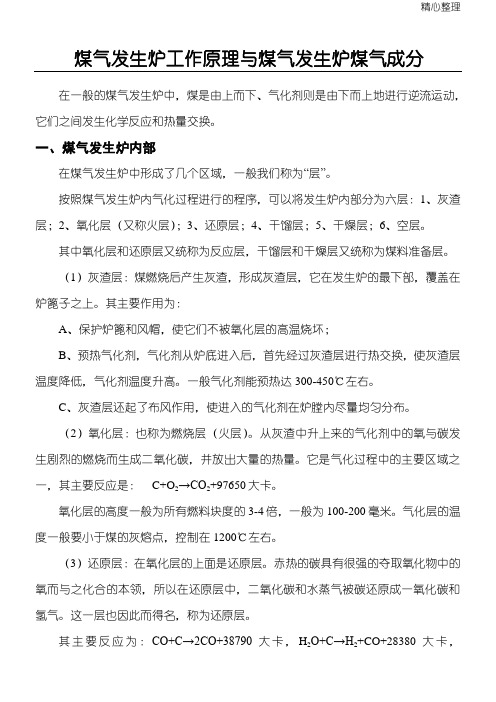
精心整理煤气发生炉工作原理与煤气发生炉煤气成分在一般的煤气发生炉中,煤是由上而下、气化剂则是由下而上地进行逆流运动,它们之间发生化学反应和热量交换。
一、煤气发生炉内部在煤气发生炉中形成了几个区域,一般我们称为“层”。
层;2(A B C (度一般要小于煤的灰熔点,控制在1200℃左右。
(3)还原层:在氧化层的上面是还原层。
赤热的碳具有很强的夺取氧化物中的氧而与之化合的本领,所以在还原层中,二氧化碳和水蒸气被碳还原成一氧化碳和氢气。
这一层也因此而得名,称为还原层。
其主要反应为:CO+C→2CO+38790大卡,H 2O+C→H 2+CO+28380大卡,2H2O+C→CO2+2H2+17970大卡。
由于还原层位于氧化层之上,从上升的气体中得到大量热量,因此还原层有较高的温度约800-1100℃,这就为需要吸收热量的还原反应提供了条件。
而严格地讲,还原层还有第一、第二之分,下部温度较高的地方称第一还原层,温度达950-1100℃,其厚度为300-400毫米左右;第二层为700-950℃之间,其厚度为第一还原层1.5倍,约在450毫米左右。
((在室温层高。
(CO单叙述,我们可以看出煤气发生炉内进行的气化过程是比较复杂的,既有气化反应,也有干馏和干燥过程。
而且在实际生产的发生炉中,分层也不是很严格的,相邻两层往往是相互交错的,各层的温度也是逐步过渡的,很难具体划分,各层中气体成份的变化就更加复杂了,即使在专门的研究中,看法也是分歧的。
二、煤气炉的结构对于固定床煤气炉有多种结构型式,按不同部位分述如下:1、加煤装置:间歇式加煤罩、双料钟、振动给煤机、拨齿加煤机。
2、炉体结构:带压力全水套、半水套、无水套(耐火材料炉衬)、常压全水套。
3、炉篦:宝塔型、型钢焊接型。
4、灰盘传动结构:拨齿型、蜗轮蜗杆型。
三、煤气发生炉煤气成分所谓煤气发生炉炉出煤气,是指煤在煤气发生炉内气化反应所产生的,自煤气2、煤气中的H2S煤气中的H2S含量多少与气化用煤中的含硫多少有关,一般煤中硫分的80%以H2S状态转入煤气中,20%的硫分残留在灰渣中。
煤气发生炉工作原理

煤气发生炉工作原理
煤气发生炉是一种用于生产合成气体的设备,它通过煤或其他碳质物质的热解过程,产生一种可燃气体,其中主要成分是一氧化碳和氢气。
煤气发生炉工作原理的核心是煤的热解反应,下面我们来详细了解一下煤气发生炉的工作原理。
首先,煤气发生炉内部的煤气化过程是通过煤与空气或者氧气的反应来实现的。
当煤在高温下遇热分解时,会产生一氧化碳和氢气,这个过程称为煤气化。
煤气发生炉内部的煤气化反应需要在高温下进行,通常在800°C以上才能够有效进行。
因此,煤气发生炉内部需要提供足够的热量来维持煤的热解反应。
其次,煤气发生炉内部的煤气化反应需要控制氧气的供给和煤料的输送速度,以确保煤料在炉内充分接触空气或氧气,从而实现有效的煤气化。
同时,煤气发生炉还需要排出煤气化过程中产生的煤气和煤渣,以保持炉内的稳定工作状态。
最后,煤气发生炉产生的合成气体需要通过净化和冷却处理,以去除其中的杂质和降低温度,从而得到符合要求的合成气体。
这个过程通常包括除尘、脱硫、脱氮等步骤,以确保合成气体的质量
和安全性。
总的来说,煤气发生炉的工作原理是通过煤的热解反应产生合成气体,然后经过净化和处理得到可用的合成气体。
这个过程需要控制炉内的温度、氧气供给和煤料输送速度,同时需要对产生的合成气体进行净化和冷却处理。
煤气发生炉在工业生产中具有重要的应用价值,能够为工业生产提供可靠的燃料和原料来源。
煤气发生炉原理

煤气发生炉原理
煤气发生炉是一种将固体燃料转化为可燃气体的装置,它是工业生产和能源利用中的重要设备。
煤气发生炉的原理是通过热解固体燃料,产生可燃气体,然后将其用作燃料进行燃烧。
下面我们将详细介绍煤气发生炉的原理。
首先,煤气发生炉的主要原理是热解固体燃料。
在煤气发生炉内部,固体燃料(如煤、木材等)在缺氧或氧气不足的环境下受热分解,产生可燃气体。
这个过程主要包括干馏和气化两个阶段。
干馏是指在高温下,固体燃料中的挥发性成分被分解出来,产生液体和气体。
气化是指在高温下,固体燃料中的非挥发性成分被分解成一氧化碳和氢气等可燃气体。
其次,煤气发生炉的原理还涉及气体净化。
由于煤气发生炉产生的气体中含有一定的固体颗粒和有害气体,需要经过净化处理才能作为燃料使用。
气体净化一般包括除尘、脱硫、脱氮等工艺,通过这些工艺可以将固体颗粒和有害气体去除,从而得到清洁的可燃气体。
最后,煤气发生炉的原理还包括燃烧利用。
经过热解和净化处理后的可燃气体可以用作燃料进行燃烧,产生热能或动力。
燃烧利用是煤气发生炉的最终目的,通过燃烧可燃气体可以产生热能,用于工业生产或供暖,也可以产生动力,用于驱动发电机等设备。
综上所述,煤气发生炉的原理主要包括热解固体燃料、气体净化和燃烧利用三个方面。
通过这些原理,煤气发生炉可以将固体燃料转化为可燃气体,并将其用作燃料进行燃烧,从而产生热能或动力。
煤气发生炉在工业生产和能源利用中具有重要的地位,它的原理和工艺对于提高能源利用效率和减少环境污染具有重要意义。
- 1、下载文档前请自行甄别文档内容的完整性,平台不提供额外的编辑、内容补充、找答案等附加服务。
- 2、"仅部分预览"的文档,不可在线预览部分如存在完整性等问题,可反馈申请退款(可完整预览的文档不适用该条件!)。
- 3、如文档侵犯您的权益,请联系客服反馈,我们会尽快为您处理(人工客服工作时间:9:00-18:30)。
煤气发生炉工作原理与煤气发生炉煤气成分在一般的煤气发生炉中,煤是由上而下、气化剂则是由下而上地进行逆流运动,它们之间发生化学反应和热量交换。
一、煤气发生炉内部在煤气发生炉中形成了几个区域,一般我们称为“层”。
按照煤气发生炉内气化过程进行的程序,可以将发生炉内部分为六层:1、灰渣层;2、氧化层(又称火层);3、还原层;4、干馏层;5、干燥层;6、空层。
其中氧化层和还原层又统称为反应层,干馏层和干燥层又统称为煤料准备层。
(1)灰渣层:煤燃烧后产生灰渣,形成灰渣层,它在发生炉的最下部,覆盖在炉篦子之上。
其主要作用为:A、保护炉篦和风帽,使它们不被氧化层的高温烧坏;B、预热气化剂,气化剂从炉底进入后,首先经过灰渣层进行热交换,使灰渣层温度降低,气化剂温度升高。
一般气化剂能预热达300-450℃左右。
C、灰渣层还起了布风作用,使进入的气化剂在炉膛内尽量均匀分布。
(2)氧化层:也称为燃烧层(火层)。
从灰渣中升上来的气化剂中的氧与碳发生剧烈的燃烧而生成二氧化碳,并放出大量的热量。
它是气化过程中的主要区域之一,其主要反应是:C+O2→CO2+97650大卡。
氧化层的高度一般为所有燃料块度的3-4倍,一般为100-200毫米。
气化层的温度一般要小于煤的灰熔点,控制在1200℃左右。
(3)还原层:在氧化层的上面是还原层。
赤热的碳具有很强的夺取氧化物中的氧而与之化合的本领,所以在还原层中,二氧化碳和水蒸气被碳还原成一氧化碳和氢气。
这一层也因此而得名,称为还原层。
其主要反应为:CO+C→2CO+38790大卡,H2O+C→H2+CO+28380大卡,2H2O+C→CO2+2H2+17970大卡。
由于还原层位于氧化层之上,从上升的气体中得到大量热量,因此还原层有较高的温度约800-1100℃,这就为需要吸收热量的还原反应提供了条件。
而严格地讲,还原层还有第一、第二之分,下部温度较高的地方称第一还原层,温度达950-1100℃,其厚度为300-400毫米左右;第二层为700-950℃之间,其厚度为第一还原层1.5倍,约在450毫米左右。
(4)干馏层:干馏层位于还原层的上部,由还原层上升的气体随着热量的被消耗,其温度逐渐下降,故干馏层温度约在150-700℃之间,煤在这个温度下,历经低温干馏的过程,煤中挥发份发生裂解,产生甲烷、烯烃及焦油等物质,它们受热成为汽态,即生成煤气并通过上面干燥层而逸出,成为煤气的组成部分。
干馏层的高度随燃料中挥发份含量及煤气炉操作情况而变化,一般>100毫米。
(5)干燥层:干燥层位于干馏层上面,也即是燃料的面层,上升的热煤气与刚入炉的燃料在这层相遇,进行热交换,燃料中的水分受热蒸发。
一般认为干燥温度在室温---150℃之间,这一层的高度也随各种不同的操作情况而异,没有相对稳定之层高。
(6)空层:空层即燃料层上部,炉体内的自由区,其主要作用是汇集煤气。
也有的同志认为:煤气在空层停留瞬间,在炉内温度较高时还有一些副反应发生,如:CO分解、放出一些炭黑:2CO→CO2+C 以及2H2O+CO→CO2+H2。
从上面六层简单叙述,我们可以看出煤气发生炉内进行的气化过程是比较复杂的,既有气化反应,也有干馏和干燥过程。
而且在实际生产的发生炉中,分层也不是很严格的,相邻两层往往是相互交错的,各层的温度也是逐步过渡的,很难具体划分,各层中气体成份的变化就更加复杂了,即使在专门的研究中,看法也是分歧的。
二、煤气炉的结构对于固定床煤气炉有多种结构型式,按不同部位分述如下:1、加煤装置:间歇式加煤罩、双料钟、振动给煤机、拨齿加煤机。
2、炉体结构:带压力全水套、半水套、无水套(耐火材料炉衬)、常压全水套。
3、炉篦:宝塔型、型钢焊接型。
4、灰盘传动结构:拨齿型、蜗轮蜗杆型。
三、煤气发生炉煤气成分所谓煤气发生炉炉出煤气,是指煤在煤气发生炉内气化反应所产生的,自煤气发生炉出口导出未经净化的煤气。
该煤气由单一可燃气体成分(CO、H2、CH4)、气态烷烃类化合物(C m H n)、H2S、不可燃气体成分(CO2、N2、O2)以及焦油蒸汽、粉尘固体微粒和水蒸汽所组成。
1、煤气气体组成及煤气热值气化烟煤时,煤中的CO含量较高,而且还会有少量的C m H n,煤气热值也较高;气化无烟煤时,CO和CH4含量都较气化烟煤时要低,煤气热值也即较低;气化褐煤时,CO含量较低,但H2和CH4相对也要高一些,煤气热值也较高,但是,褐煤的气化产率较低,仅为2Nm3/kg(煤)左右,而气化烟煤或无烟煤时,气化产率可达3~3.5Nm3/kg(煤)。
表1 几种煤气化时煤气组成及煤气热值2、煤气中的H2S煤气中的H2S含量多少与气化用煤中的含硫多少有关,一般煤中硫分的80%以H2S状态转入煤气中,20%的硫分残留在灰渣中。
3、煤气中的焦油煤气中的焦油含量多少与煤中的挥发分多少有关,气化无烟煤时煤气中的焦油含量很少,气化烟煤时煤气中的焦油产率为入炉煤重量的2%~6%,标准状态下每m3干煤气中含焦油量为0.01~0.02kg。
4、煤气中的水分煤气中的水分来源于蒸汽的未分解部分、煤的低温干馏热解水以及煤中的水分,一般来说,气化烟煤、无烟煤时煤气中的水分约为0.06kg/Nm3,而气化褐煤时,煤气中的水分较高,可达0.13~0.27kg/Nm3。
5、煤气中的粉尘固体颗粒煤气中的粉尘固体颗粒(即带出物),它与煤的热稳定性、入炉块煤中的含粉末率、以及炉内的气化强度、入炉煤的粒度分布、煤层厚薄等因素有关,一般情况下,煤气中的粉尘固体颗粒量为入炉煤重量的4%~6%。
表2 气化不同煤种煤气中的水分、焦油、粉尘固体颗粒含量四、煤焦油(又称煤膏、煤馏油、煤焦油溶液)煤干馏过程中所得到的一种液体产物,黑色粘稠液体,具有特殊臭味,易燃,有腐蚀性,为致癌物。
相对密度(水=1):1.18-1.23 闪点(℃):<23 沸点:380℃溶解性:微溶于水,溶于苯、乙醇、乙醚、氯仿、丙酮等多数有机溶剂。
主要用途:可分馏出各种芳香烃、烷烃、酚类等,也可制取油毡、燃料和炭黑。
健康危害:作用于皮肤,引起皮炎、痤疮、毛囊炎、光毒性皮炎、中毒性黑皮病、疣赘及癌肿。
可引起鼻中隔损伤。
环境危害:对环境有危害,对大气可造成污染。
危险特性:其蒸气与空气可形成爆炸性混合物,遇明火、高热极易燃烧爆炸。
与氧化剂接触猛烈反应。
若遇高热,容器内压增大,有开裂和爆炸的危险。
制备:由煤在隔绝空气加强热时干馏制得。
高温干馏煤焦油(简称高温煤焦油)高温干馏(即焦化)得到的焦油。
黑色粘稠液体,相对密度大于1.0,含大量沥青,其他成分是芳烃及杂环有机化合物。
包含的化合物已被鉴定的达 400余种。
工业上将煤焦油集中加工,有利于分离提取含量很少的化合物。
加工过程首先按沸点范围蒸馏分割为各种馏分,然后再进一步加工。
各馏分的加工采用结晶方法可得到萘、蒽等产品;用酸或碱萃取方法可得到含氮碱性杂环化合物(称焦油碱),或酸性酚类化合物(称焦油酸)。
焦油酸、焦油碱再进行蒸馏分离可分别得到酚、甲酚、二甲酚和吡啶、甲基吡啶、喹啉。
这些化合物是染料、医药、香料、农药的重要原料。
煤焦油蒸馏所得的馏分油也可不经分离而直接利用,如沥青质可制电极焦、碳素纤维等各种重要产品,酚油可用于木材防腐,洗油用作从煤气中回收粗苯的吸收剂,轻油则并入粗苯一并处理。
低温干馏煤焦油(简称低温煤焦油)低温干馏(见煤低温干馏)得到的焦油。
黑色粘稠液体,其不同于高温煤焦油是相对密度通常小于1.0,芳烃含量少,烷烃含量大,其组成与原料煤质有关。
低温干馏焦油是人造石油的重要来源之一,经高压加氢制得汽油、柴油等产品。
高温煤焦油和低温煤焦油两者的组成和性质不同,其加工利用方法各异。
五、分类2、按制气工艺分类煤气发生炉按不同的制气工艺和所产煤气的质量分为单段煤气发生炉、双段煤气发生炉、双段热脱焦油煤气发生炉、双段冷净煤气发生炉。
A、单段单段煤气发生炉设备简单,只有水夹套和炉顶装置,出渣系统组成,所产煤气为热粗煤气,适应于输送距离不远,对煤气的洁净度要求不高的炉窑。
B、双段双段煤气发生炉是在单段煤气发生炉的基础上增加一个干馏段,使煤在气化之前通过充分干馏,将煤中挥发分在进入氧化还原之前大部分析出,并且随上段煤气引出炉体。
而进入下段参与反应的煤基本为焦煤或者半焦基本不含焦油,通过水冷箱体经下段炉出口排出炉外,经煤气净化除尘装置与上段炉所产经电捕焦油器除焦油后的上段煤气汇合经管道输送至窑炉。
双段煤气发生炉所产煤气比较干净,并且输送距离长,对煤质的要求没有单段炉高。
有经过净化冷却装置的双段冷煤气站所产煤气可以按用户要求,进行加压后远距离输送,不受场地限制,冷净煤气质量比较洁净,主要使用与对煤气质量要求较高的化工、陶瓷等行业。
3、按出渣方式分类煤气发生炉按出渣方式的不同,比较常用的分为内出渣煤气发生炉、外出渣煤气发生炉。
其他刮板内出渣煤气发生炉、顶齿外出渣煤气发生炉基本被淘汰。
其中外出渣煤气发生炉由于传动方式不同分为蜗轮蜗杆出渣和液压棘轮出渣两种。
六、造气过程1、固态物质行程利用提升机构将煤加入储煤仓,通过加煤机将储煤仓中的煤分批次注入煤气发生炉。
加入煤气发生炉中的煤首先进入干馏段,煤在干馏段中缓慢下移,在此经历干燥、干馏过程。
首先煤炭中的水份被干燥出来,随着煤炭的不断下移,温度进一步升高,焦油及大部分硫化物也被干馏出来,形成碳氢化合物和轻质焦油被上段煤气携出炉外。
经过干燥干馏后呈半焦性质的煤继续下移,进入气化段,在气化段经过氧化还原反应,形成以一氧化碳和氢气为主要成分的煤气。
煤炭中的灰分及极少部分未参与反应的煤炭以灰渣形式继续下移,由灰刀将其清出炉外。
2、气态物质行程作为气化剂的空气和水蒸汽自炉底鼓入炉内,在1100-1200℃条件下,与进入气化段的呈半焦性质的煤发生氧化还原反应,形成以一氧化碳和氢气为主要成分的煤气。
煤气分两部分向上运行,其中一部分通过下段煤气夹层通道上移约4米,将其热量通过耐火材料间接传给煤层,辅助干馏和干燥过程的完成,确保煤在下落过程中能够充分的被干燥和干馏,最后这部分煤气从下段煤气出口导出被称为下段煤气;而另一部分煤气则在煤气发生炉料层内上行进入干馏段,通过与缓慢下移的气化用煤直接接触,将其热量直接传给气化用煤,进行上面叙述的干馏、干燥的过程,同时产生一部分以烷烃类高热值气体为主的干馏煤气。
这部分上行煤气及干馏过程中产生的干馏煤气一起由上段煤气出口导出,形成上段煤气。
七、环保达标(1)设置水封水池(循环利用),保证水封污水不外排。
(2)冷凝含酚废水集中收集并汽化后再利用。
(3)对噪声较高的设备,采取建筑隔音的方式,治理噪声污染。
(4)固体废弃物集中回收,综合利用。
合理设计烘炉送气工艺,设置煤气放散点火器,保证放散烟气达标排放。