煤油冷却器的设计
煤油冷却器设计

目录第1章工艺综述 (2)1.2工艺原理 (2)1.3工艺流程 (3)第2章工艺计算 (4)2.1设计参数 (4)2.2管径和管内流速 (5)2.3 估算换热面积 (7)2.4 管程数和传热管数的计算 (7)2.5 传热管排列和分程方法的确定 (8)2.6 壳体内径以及折流板数的计算 (8)第3章结构设计 (10)3.1 封头和圆筒厚度 (10)3.2 接管 (10)3.3 折流板 (11)3.4分程隔板 (12)3.5 拉杆的数量与直径 (12)3.6判断是否安装膨胀节 (12)3.7 支座 (14)第4章强度计算 (15)4.1传热系数核算 (15)4.2 壁温核算 (17)4.3 压强降的核算 (17)第5章设计结果一览表 (20)参考文献 (21)评价表 (22)第1章工艺综述1.1 装置简介ARGG装置包括反应-再生、分馏、吸收塔、气压机、能量回收及余热锅炉、产品精制几部分租成,ARGG工艺以常压渣油等重油质油为原料,采用重油转化和抗金属能力强,选择性好的ARG催化剂,以生产富含丙烯、异丁烯、异丁烷的液化气、并生产高辛烷只汽油。
1.2工艺原理1.2.1催化裂化部分催化裂化是炼油工业中最重要的二次加工过程,是重油轻质化的重要手段。
它是使原料油在适宜的温度、压力和催化剂存在的条件下,进行分解、异构化、氢转移、芳构化、缩和等一系列化学反应,原料油转化为气体、汽油、柴油等主要产品及油浆、焦炭的生产过程。
催化裂化的原料油来源广泛,主要是常减压的馏分油、常压渣油、减压渣油及丙烷脱沥青油、蜡膏、蜡下油等。
随着石油资源的短缺和原油的日趋变重,重油催化裂化有了较快发展,处理的原料可以是全常渣甚至是全减渣。
在硫含量较高时,则需用加氢脱硫装置进行处理,提供催化原料。
催化裂化过程具有轻质油收率高、汽油辛烷值较高、气体产品中烯烃含量高等特点。
催化裂化生产过程的主要产品是气体、汽油和柴油,其中气体产品包括干气和液化石油气,干气作为本装置燃料气烧掉,液化石油气是宝贵的石油化工原料和民用燃料。
化工原理课程设计说明书-煤油冷却器的设计

课程设计任务书一、摘要换热器是将热流体的部分热量传递给冷流体的设备,以实现不同温度流体间的热能传递,又称热交换器。
换热器是实现化工生产过程中热量交换和传递不可缺少的设备。
在换热器中,至少有两种温度不同的流体,一种流体温度较高,放出热量;另一种流体则温度较低,吸收热量。
在化工、石油、动力、制冷、食品等行业中广泛使用各种换热器,且它们是上述这些行业的通用设备,占有十分重要的地位。
随着我国工业的不断发展,对能源利用、开发和节约的要求不断提高,对换热器的要求也日益增强。
换热器的设计制造结构改进以及传热机理的研究十分活跃,一些新型高效换热器相继问世。
根据不同的目的,换热器可以是热交换器、加热器、冷却器、蒸发器、冷凝器等。
由于使用条件的不同,换热器可以有各种各样的形式和结构。
在生产中,换热器有时是一个单独的设备,有时则是某一工艺设备的组成部分。
衡量一台换热器好的标准是传热效率高、流体阻力小、强度足够、结构合理、安全可靠、节省材料、成本低,制造、安装、检修方便、节省材料和空间、节省动力。
二、关键字煤油换热器列管式换热器膨胀节固定管板式封头管板目录一、概述 (1)二、工艺流程草图及设计标准 (1)2.1工艺流程草图 (1)2.2设计标准 (2)三、换热器设计计算 (2)3.1确定设计方案 (2)3.1.1选择换热器的类型 (2)3.1.2流体溜径流速的选择 (2)3.2确定物性的参数 (3)3.3估算传热面积 (3)3.3.1热流量 (3)3.3.2平均传热温差 (3)3.3.3传热面积 (3)3.3.4冷却水用量 (4)3.4工艺结构尺寸 (4)3.4.1管径和管内流速 (4)3.4.2管程数和传热管数 (4)3.4.3平均传热温差校正及壳程数 (4)3.4.4传热管排列和分程方法 (5)3.4.5壳体内径 (5)3.4.6折流板 (5)3.4.7接管 (5)3.5换热器核算 (6)3.5.1热流量核算 (6)3.5.1.1壳程表面传热系数 (6)3.5.1.2管内表面传热系数 (7)3.5.1.3污垢热阻和管壁热阻 (7)3.5.1.4计算传热系数K C (7)3.5.1.5换热器的面积裕度 (8)3.5.2换热器内流体的流动阻力 (8)3.5.2.1管程流体阻力 (8)3.5.2.2壳程阻力 (8)四、设计结果设计一览表 (10)五、设计自我评价 (11)六、参考资料 (12)七、主要符号说明 (13)一、概述在不同温度的流体间传递热能的装置称为热交换器,简称为换热器。
煤油冷却器的设计 化工原理课程设计

课程设计课程名称化工原理课程设计题目名称煤油冷却器的设计专业班级食品营养与检测学生姓名学号指导教师二O O年12 月31 日目录1.设计任务 ----------------- 12. 设计计算 ----------------- 2(1)确定设计方案 ---------------------- 2(2)确定物性系数-------------------------- 2(3)计算总传热系数 ------------------- 3 (4)计算传热面积--------------------------- 4(5)工艺结构尺寸--------------------------- 4(6)换热器核算 ------------------------ 53. 换热器主要结构尺寸和计算结果表1 9煤油冷却器的设计列管式换热器【设计任务】一、设计题目列管式换热器的设计二、设计任务及操作条件(1)处理能力: M*103 t/Y(其中:M=30+学号后两位)煤油(2)设备型式: 列管式换热器(3)操作条件①煤油:入口温度110℃,出口温度60℃。
②冷却介质:循环水,入口温度29℃,出口温度39℃。
③允许压降:不大于105 Pa。
④煤油定性温度下的物性数据:定压比热容=3.297kJ/(kg.℃)导热系数=0.0279 W/(m.0C)⑤每年按330天计,每天24小时连续运行。
(4)建厂地址蚌埠地区三、设计要求试设计一台适宜的列管式换热器完成该生产任务。
【设计计算】一、确定设计方案1.选择换热器的类型两流体温度变化情况:热流体进口为温度110℃,出口温度60℃;冷流体(循环水)进口温度29℃,出口温度39℃。
该换热器用循环水冷却,冬季操作时进口温度会降低,考虑到这一因素,估计该换热器的管壁温度和壳体温度之差较大,因此初步确定选用带膨胀节的固定管板式换热器。
2.流动空间及流速的确定由于循环冷却水较易结垢,为便于水垢清洗,应使循环水走管程,油品走壳程。
列管式煤油冷却器的设计

列管式煤油冷却器的设计设计要点:1.冷却器的材质选择:常用的冷却器材质有不锈钢、铝合金等,应根据具体的工作环境和冷却要求选择合适的材质。
材质要能抗腐蚀和耐高温。
2.冷却器的结构设计:冷却器主要由煤油入口和出口、冷却管道、冷却介质进出口等组成。
冷却管道采用列管式结构,以增加冷却面积和提高冷却效果。
3.冷却器的尺寸设计:冷却器的尺寸应根据煤油的冷却需求和设备的限制来确定。
冷却器的尺寸越大,冷却效果越好,但冷却器的体积和重量也会增加。
4.冷却介质的选择:常用的冷却介质有水、空气等。
水是一种常用的冷却介质,效果较好。
但在一些特殊环境中,如船舶上的燃油冷却器,由于水的供应受限,可以采用空气冷却方式。
5.冷却器的布置和连接方式:冷却器的布置应使得煤油能够在冷却管道中均匀流动,以达到最佳冷却效果。
同时,应注意冷却器与其他设备的连接方式和紧密度,以避免泄漏和能量损失。
设计步骤:1.确定冷却需求:首先需要确定煤油的冷却需求,包括冷却温度、煤油流量和温度变化范围等参数。
2.选择合适的冷却介质:根据冷却需求和实际情况选择合适的冷却介质,如水或空气。
3.计算冷却器尺寸:根据冷却需求和冷却介质的特性计算冷却器的尺寸,包括冷却管道长度、管道直径和板片数量等。
4.设计冷却器的结构和布局:根据尺寸和冷却介质选择冷却器的结构和布局,确保煤油能够充分接触到冷却介质,并实现有效的热量交换。
5.考虑维护和清洁:在设计过程中,应考虑冷却器的维护和清洁问题,以便在使用过程中更换和清洁冷却器。
6.完善冷却系统设计:最后,根据冷却器的设计结果,完善整个煤油冷却系统的设计,包括冷却器的安装和连接方式,以确保冷却器的正常工作。
综上所述,列管式煤油冷却器的设计需要考虑多个因素,包括冷却需求、冷却介质选择、冷却器尺寸计算、结构设计和布局等。
合理的设计可以提高燃油的利用效率和延长使用寿命,同时也能确保冷却器的正常运行和维护。
管式换热器煤油冷却器的设计
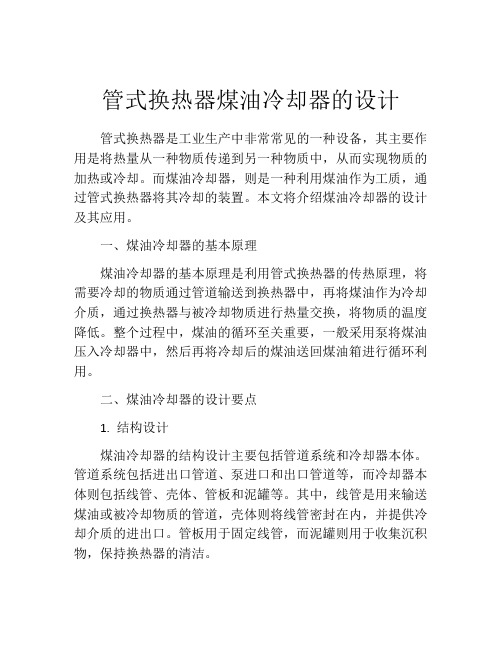
管式换热器煤油冷却器的设计管式换热器是工业生产中非常常见的一种设备,其主要作用是将热量从一种物质传递到另一种物质中,从而实现物质的加热或冷却。
而煤油冷却器,则是一种利用煤油作为工质,通过管式换热器将其冷却的装置。
本文将介绍煤油冷却器的设计及其应用。
一、煤油冷却器的基本原理煤油冷却器的基本原理是利用管式换热器的传热原理,将需要冷却的物质通过管道输送到换热器中,再将煤油作为冷却介质,通过换热器与被冷却物质进行热量交换,将物质的温度降低。
整个过程中,煤油的循环至关重要,一般采用泵将煤油压入冷却器中,然后再将冷却后的煤油送回煤油箱进行循环利用。
二、煤油冷却器的设计要点1. 结构设计煤油冷却器的结构设计主要包括管道系统和冷却器本体。
管道系统包括进出口管道、泵进口和出口管道等,而冷却器本体则包括线管、壳体、管板和泥罐等。
其中,线管是用来输送煤油或被冷却物质的管道,壳体则将线管密封在内,并提供冷却介质的进出口。
管板用于固定线管,而泥罐则用于收集沉积物,保持换热器的清洁。
2. 材料选择在选择煤油冷却器的材料时,需要考虑煤油的化学性质和冷却介质的耐腐性。
一般来说,冷却器的材料可以选用碳钢、不锈钢、铜等材料。
碳钢的价格相对较低,但容易被腐蚀,不锈钢则具有较好的耐腐蚀性能,但价格较高。
选择时需要根据实际需要进行综合考虑。
3. 换热面积和流量计算煤油冷却器的换热面积和流量计算是设计过程中的重要环节。
首先需要确定被冷却物质的流量和温度,以及要达到的冷却效果。
然后,通过热力学计算,确定煤油冷却器的换热面积和煤油的循环流量,以保证冷却效果达到设计要求。
三、煤油冷却器的应用煤油冷却器广泛应用于各种工业生产过程中,如钢铁生产、化工生产、造纸生产等。
例如,在钢铁生产中,煤油冷却器可以用于冷却钢水和铁水,控制铸件的温度,保证质量。
在化工生产中,煤油冷却器可以用于冷却化学反应过程中产生的热量,保护反应釜不受过热损坏。
在造纸生产中,煤油冷却器可以用于冷却生产过程中的水蒸气,保证造纸机的正常运转。
煤油冷却器毕业设计

煤油冷却器毕业设计毕业设计:煤油冷却器设计摘要:本文介绍了一种基于煤油的冷却器设计,该设计主要用于冷却热水器、发动机等设备。
本设计中采用了顶盖螺丝、底座、热管、铝鳍片等部件。
通过改变顶盖螺丝的材料、直径,底座的形状、尺寸,铝鳍片的数量、厚度,优化了冷却器的导热、换热性能。
最终实验结果表明,该煤油冷却器的性能稳定可靠,可广泛应用于不同领域的冷却需求。
关键词:煤油冷却器、热管、铝鳍片、导热、换热1. 引言随着科技的发展和工业的进步,越来越多的设备需要进行降温或冷却。
冷却器作为一种实用的降温设备,广泛应用于发动机、热水器、空调等各类设备中。
本文介绍了一种基于煤油的冷却器设计,旨在提高冷却器的效率和稳定性。
2. 冷却器设计本设计采用了顶盖螺丝、底座、热管、铝鳍片等部件。
其中,热管是冷却器的核心部件,其内部填充着煤油等导热介质。
铝鳍片的作用是增大冷却器的散热面积,提高散热效率。
在设计中,我们改变了顶盖螺丝的材料、直径,底座的形状、尺寸,铝鳍片的数量、厚度等因素,通过优化这些因素,提高了冷却器的导热、换热性能。
3. 实验结果本设计的煤油冷却器经过多组实验测试,其性能稳定可靠。
在实验中,我们将冷却器接入发动机冷却回路进行测试,测试结果表明,冷却器的降温效果明显,能够使发动机工作温度下降10℃左右,并能够稳定工作长达100小时以上。
4. 结论本文介绍了一种基于煤油的冷却器设计,优化了冷却器的导热、换热性能,通过实验验证了该设计的可靠性和稳定性。
该煤油冷却器的技术应用前景广阔,可以应用于不同领域的冷却需求。
煤油卧式列管式冷却器的设计
煤油卧式列管式冷却器的设计冷却器是一种常见的热交换设备,用于将热量从一个介质传递到另一个介质,以实现冷却效果。
煤油卧式列管式冷却器是一种常见的冷却器类型,特点是结构简单、性能可靠。
下面将对煤油卧式列管式冷却器的设计进行详细探讨。
一、设计要求:1.设计工作温度:煤油的设计工作温度为30℃。
2.设计工作压力:煤油的设计工作压力为0.2MPa。
3.散热面积:根据需要散热的热量计算得出。
4.设计材料:列管、壳体采用碳钢材料。
二、设计步骤:1.确定散热面积:根据给定的冷却效果和需要散发的热量计算出所需的散热面积。
常用的计算公式如下:Q=U×A×ΔT其中,Q为所需散发的热量,U为传热系数,A为散热面积,ΔT为温度差。
通过已知条件计算得出散热面积后,我们可以确定冷却器的尺寸。
2.确定传热系数:传热系数是指单位时间内通过单位面积的热量,它是冷却器设计中一个重要的参数。
传热系数的大小取决于流体的性质、流速、管道结构等因素。
一般可以通过经验公式来计算传热系数。
3.选取列管:列管是冷却器的核心部分,采用高导热性能的金属材料,如铜、不锈钢等。
根据散热面积和设计工作温度确定列管的数量和布置方式。
通常可以选择U型管或者平直管作为列管。
4.确定壳体尺寸:壳体是冷却器的外部结构,起到支撑和保护列管的作用。
根据列管的数量和布置方式,确定壳体的尺寸和结构。
5.设计壳体配件:壳体配件包括进出口管道、阀门、泄压装置等。
根据设计要求和实际应用情况,选择合适的壳体配件。
6.设计支座和支撑:冷却器需要有支座和支撑结构来支撑整个设备。
根据冷却器的尺寸和重量,设计合适的支座和支撑结构。
7.进行计算和分析:在设计完成后,需要进行计算和分析,验证设计结果的可行性和合理性。
通过应力、热力、振动等方面的计算和分析,确保冷却器的安全可靠。
8.绘制图纸和制作样品:最后,根据设计结果绘制详细的图纸,并制作冷却器的样品。
样品经过测试和实验验证后,可以进行批量生产。
煤油冷却器的设计
煤油冷却器的设计摘要煤油冷却器是利用流体易导热原理,将煤油的热量向环境转移,冷却其受热部件的装置。
本文介绍了煤油冷却器的结构与设计及其性能的研究。
本文主要从流体流动系统、热交换系统、控制系统以及特殊设备等方面介绍了煤油冷却器的设计,研究了冷却器的结构性能及实际工作条件下的性能,并探讨了冷却器在操作过程中的安全措施。
本文所讨论的煤油冷却器的性能高,安全可靠,能够满足大多数用户的使用要求。
关键词:煤油冷却器;结构设计;性能研究;安全措施IntroductionFlow SystemThe flow system is the main part of oil coolers, which provides the means for the fuel oil and cooling fluid to enter and exit the heat exchanger. The oil coolers generally include two oil inlets and two oil outlets and two cooling inlets andtwo cooling outlets, as shown in Figure 1. The oil inlet is connected to the fuel oil supply pipe and the oil outlet is connected to the oil return pipe. The cooling inlet is connected to the water supply pipe, and the cooling outlet is connected to the water return pipe. Both cooling inlets and cooling outlets are equipped with high-pressure relief valves to prevent overpressure of the coolant.Figure 1. Oil cooler structureHeat Exchange System。
管式换热器(煤油冷却器)的设计
课程设计课程名称化工原理课程设计题目名称煤油冷却器的设计专业班级09级生物工程(2)班学生姓名学号指导教师孙兰萍二O一一年十二月二十日1 设计任务书1.1 设计题目煤油冷却器的设计1.2 设计任务及操作条件(1)处理能力: M ⨯104 t/Y 煤油(2)设备型式: 列管式换热器(3)操作条件①煤油:入口温度140℃,出口温度40℃。
②冷却介质:循环水,入口温度30℃,出口温度40℃。
③允许压降:不大于105 Pa 。
④煤油定性温度下的物性数据:3/825m kg C =ρ;s Pa C ⋅⨯=-41015.7μ;pC c =2.22kJ/(kg.℃);C λ=0.14 W/(m.℃)⑤每年按330天计,每天24小时连续运行。
(4)建厂地址 天津地区1.3 设计要求试设计一台适宜的列管式换热器完成该生产任务。
1.4 工作计划1、领取设计任务书,查阅相关资料(1天);2、确定设计方案,进行相关的设计计算(2天);3、校核验算,获取最终的设计结果(1天);4、编写课程设计说明书(论文),绘制草图等(1天)。
1.5 设计成果要求1、通过查阅资料、设计计算等最终提供课程设计说明书(论文)电子稿及打印稿1份,并附简单的设备草图。
2、课程设计结束时,将按以下顺序装订的设计成果材料装订后交给指导教师:(1)封面(具体格式见附件1)(2)目录(3)课程设计任务书(4)课程设计说明书(论文)(具体格式见附件2)(5)参考文献(6)课程设计图纸(程序)1.6 几点说明1、本设计任务适用班级:09生物工程(本)2班(其中:学号1-15号,M=15;学号16-30号,M=25;学号31-46号,M=40);2、课程设计说明书(论文)格式也可参阅《蚌埠学院本科生毕业设计(论文)成果撰写规范》中的相关内容。
指导教师:教研室主任:系主任:2 确定设计方案2.1 选择换热器的类型两流体的温度变化情况:热流体即煤油的进口温度140℃,出口温度40℃;冷流体即循环水进口温度30℃,出口温度40℃。
浅谈煤油冷却器的设计
浅谈煤油冷却器的设计引言煤油冷却器是一种常用的热交换设备,用于将高温流体(通常是煤油)的热量传递给冷却介质(通常是水)以降低煤油的温度。
在工业生产过程中,大量的热能产生,煤油冷却器通过高效的热交换设计,能够有效地控制流体温度,确保设备的正常运行。
本文将从设计原则、材料选型和结构设计等方面对煤油冷却器的设计进行浅谈,旨在为工程师们提供一些有益的参考和指导。
设计原则热力学平衡煤油冷却器的设计首要考虑是实现热力学平衡。
合理的冷却器设计应该确保煤油在流经冷却器的过程中,能够充分地与冷却介质接触,实现热量的传递和吸收。
同时,冷却介质的流速和温度也需要进行合理的控制,以保证煤油的冷却效果。
材料的选择由于煤油冷却器在使用过程中需要处理高温流体,对材料的选择具有重要意义。
一般来说,优质的不锈钢具有较好的耐高温性能和抗腐蚀性,因此常被选用作煤油冷却器的材料。
结构设计煤油冷却器的结构设计应考虑到流体的压降和均匀分布,以增加煤油与冷却介质之间的接触面积,并减小热阻。
此外,还需要合理设计进出口口径,以保证流体的流速和流量,从而达到更好的冷却效果。
材料选型煤油冷却器的材料选型应考虑到耐高温和抗腐蚀性能。
推荐选用不锈钢材料,如304不锈钢和316不锈钢等。
这些材料具有优良的耐高温性能和抗腐蚀性,能够在高温和腐蚀环境中保持较好的稳定性。
在材料选型过程中,还需考虑材料的成本因素。
根据实际应用情况和预算要求,可以选择适当的不锈钢材料。
另外,需注意材料的可焊接性,以便进行冷却器的制造和维护。
结构设计流体分布设计为了增加煤油与冷却介质之间的接触面积,煤油冷却器的流体分布设计尤为重要。
一般采用多管并联的方式,通过将煤油分流到多个管道中,使其能够均匀地在整个冷却器中流动。
这样能够有效地提高煤油的冷却效果,减小热阻。
进出口设计进出口的设计直接影响着流体的流速和流量。
如果进出口口径过小,会增加流体的压降,降低流速和流量,影响冷却效果。
因此,进出口的设计应充分考虑流体的流动性,选择适当的口径和连接方式,确保流体能够顺利流通。
- 1、下载文档前请自行甄别文档内容的完整性,平台不提供额外的编辑、内容补充、找答案等附加服务。
- 2、"仅部分预览"的文档,不可在线预览部分如存在完整性等问题,可反馈申请退款(可完整预览的文档不适用该条件!)。
- 3、如文档侵犯您的权益,请联系客服反馈,我们会尽快为您处理(人工客服工作时间:9:00-18:30)。
南京工业大学《材料工程原理B》课程设计设计题目: 煤油冷却器的设计专业:高分子材料科学与工程班级:高材0801学号: ************: *******: ***日期: 2010/12/30设计成绩:目录一.任务书 (3)1.1.设计题目1.2.设计任务及操作条件1.3.设计要求二.设计方案简介 (3)2.1.换热器概述2.2列管式换热器2.3.设计方案的拟定2.4.工艺流程简图三.热量设计 (5)3.1.初选换热器的类型3.2.管程安排(流动空间的选择)及流速确定3.3.确定物性数据3.4.计算总传热系数3.5.计算传热面积四.工艺结构设计…………………………………………………………………………………………..-8-4.1.管径和管内流速4.2.管程数和传热管数4.3.平均传热温差校正及壳程数4.4.传热管排列和分程方法4.5.壳程内径及换热管选型汇总4.6.折流板4.7.接管五.换热器核算………………………………………………………………………………………….-13-5.1.热量核算5.2.压力降核算六.辅助设备的计算和选择……………………………………………………………………………176.1.水泵的选择6.2.油泵的选择七.设计结果表汇 (20)八.参考文献. (20)九.心得体会………………………………………………………………………………….…………… 21附图:(主体设备设计图,工艺流程简图)§一.化工原理课程设计任务书1.1设计题目煤油冷却换热器设计1.2设计任务及操作条件1、处理能力 15.8×104t/y2、设备型式列管式换热器3、操作条件(1)煤油: 入口温度140℃,出口温度40℃(2)冷却介质:工业硬水,入口温度20℃,出口温度40℃(3)油侧与水侧允许压强降:不大于105 Pa(4)每年按330天计,每天24小时连续运行(5)煤油定性温度下的物性参数:1.3设计要求选择合适的列管式换热器并进行核算1.4绘制换热器装配图(见A4纸另附)§二.设计方案简介2.1换热器概述换热器是化工,炼油工业中普遍应用的典型的工艺设备。
在化工厂,换热器的费用约占总费用的10%~20%,在炼油厂约占总费用35%~40%。
换热器在其他部门,如动力、原子能、冶金、食品、交通、环保、家电等也有着广泛的应用。
因此,设计和选择得到使用、高效的换热器对降低设备的造价和操作费用具有十分重要的意义。
在不同温度的流体间传递热能的装置称为热交换器,即简称换热器,是将热流体的部分热量传递给冷流体的设备。
换热器的类型按传热方式的不同可分为:混合式、蓄热式和间壁式。
其中间壁式换热器应用最广泛。
2.2列管式换热器因设计需要,下面简单介绍下列管式换热器列管式换热器又称管壳式换热器,在化工生产中被广泛应用。
它的结构简单、坚固、制造较容易,处理能力大,适应性能,操作弹性较大,尤其在高温、高压和大型装置中使用更为普遍。
2.2.1固定管板式固定管板式即两端管板和壳体连结成一体,因此它具有结构简单造价低廉的优点。
但是由于壳程不易检修和清洗,因此壳方流体应是较为洁净且不易结垢的物料。
当两流体的温度差较大时,应考虑热补偿。
有具有补偿圈(或称膨胀节)的固定板式换热器,即在外壳的适当部位焊上一个补偿圈,当外壳和管束的热膨胀程度不同时,补偿圈发生弹性形变,以适应外壳和管束的不同的热膨胀程度。
这种热补偿方法简便,但不宜用于两流体温度差太大和壳方流体压强过高的场合。
1-挡板 2-补偿圈 3-放气嘴图2.2.1.固定管板式换热器的示意图2.2.2浮头式这种换热器有一段管板不与壳体相连,可沿轴向自由伸缩。
这种结构不但可完全消除热应力,而且在清洗和检修时,整个管束可以从壳体中抽出。
因此,尽管其架构较复杂,造价较高,但应用仍较普遍。
2.2.3U形管式每根管子都弯成U形,两端固定在同一个管板上,因此,每根管子皆可自由伸缩,从而解决热补偿问题。
这种结构较简单,质量轻,适用于高温高压条件。
其缺点是管内不易清洗,并且因为管子要有一定的弯曲半径,其管板利用率较低。
2.3设计方案的拟定根据任务书给定的冷热流体的温度,来选择设计列管式换热器的固定管板式换热器;再根据冷热流体的性质,判断其是否容易结垢,来选择管程走什么,壳程走什么。
本设计中选择使循环工业硬水走管程,煤油走壳程。
从资料中查得冷热流体的物性数据,如比热容,密度,粘度,导热系数等。
计算出总传热系数,再计算传热面积。
根据管径,管内流速确定传热管数,算出传热管程,传热管总根数等。
然后校正传热温差及壳程数,确定传热管排列方式和分程方法。
根据设计步骤,计算出壳体内径,选择折流板,确定板间距,折流板数等;接着再对换热器的热量,官称对流传热系数,传热系数,传热面积进行核算,再算出面积裕度,最后,对流体的流动阻力进行计算。
2.4工艺流程简图(见附图)§三.工艺计算和主体设备设计3.1 初选换热器类型两流体的温度变化情况如下:(1)煤油:入口温度140℃,出口温度40℃;(2)冷却介质:自来水,入口温度30℃,出口温度40℃;该换热器用循环冷却自来水进行冷却,冬季操作时,其进口温度会降低,考略到这一因素, 估计所需换热器的管壁温度和壳体温度之差较大,需考虑热膨胀的影响,相应地进行热膨胀的补偿,故而初步确定选用带有膨胀节的管板式换热器。
3.2 管程安排及流速确定已知两流体允许压强降不大于100kPa;两流体分别为煤油和自来水。
与煤油相比,水的对流传热系数一般较大。
由于循环冷却水较易结垢,若其流速太低,将会加快污垢增长速度,使换热器的热流量下降,考虑到散热降温方面的因素,应使循环自来水走管程,而使煤油走壳程。
选用Φ25×2.5的碳钢管,管内流速取u i =0.5m/s 。
3.3确定物性数据定性温度:对于一般气体和水等低黏度流体,其定性温度可取流体进出口温度的平均值。
壳程流体(煤油)的定性温度为:℃90240140=+=T 管程流体(硬水)的定性温度为:℃3024020=+=t 根据定性温度,分别查取壳程和管程流体的有关物性数据。
3.4计算总传热系数(1).煤油的流量已知要求处理能力为15.8万吨煤油每年(每年按330天计,每天24小时连续运行),则煤油的流量为:h Kg t W h /5.19949)24330/(158000=⨯⋅=W h----热流体的流量,kg /h; (2).热流量由以上的计算结果以及题目已知,代入下面的式子,有:Q=W h Cph (T 1-T 2)=19949.5Kg/h×2.22kJ/kg .℃×(140-40)℃=4428789KJ /h =1230219W (3).平均传热温差计算两流体的平均传热温差 ,暂时按单壳程、多管程计算。
逆流时,我们有ﻩ煤油: 140℃→40℃ ﻩ水: 40℃←20℃从而'm t ∆=7.49204040140)2040()40140(=-----In℃此时P==--1112t T t t 17.0201402040=--R==--1221t t T T 5204040140=-- 式子中:21,T T ——热流体(煤油)的进出口温度,K 或℃; 21t t ,——冷流体(自来水)的进出口温度,K 或℃;由图4-25(参见化学工业出版社的《化工原理(第四版)》147页,可查得:t ∆ψ=0.83﹥0.8,所以,修正后的传热温度差为:m t ∆= 'm t ∆t ∆ψ3.4183.07.49=⨯=℃ (4).冷却水用量ﻩ由以上的计算结果以及已知条件,很容易算得:W c=)(12t t C Qpc -=53052)2040(174.44428789=-⨯kg /h (5).总传热系数K选择时,除要考虑流体的物性和操作条件外,还应考虑换热器的类型。
1.管程传热系数: Re 1=124390008007.09965.002.0=⨯⨯=iii i u d μρPr 1=41.56176.00008007.04174=⨯=iip c λμαi=0.0234.08.0)()(ii p i i i i i i c u d d λμμρλ =0.0234.08.04.018.01e 41.51243902.06176.0023.0)(Pr )(R ⨯⨯⨯=i id λ =2633W/m2•℃ 2.壳程传热系数:假设壳程的传热系数是: o α=700 W /m 2•℃污垢热阻: R s i=0.000344m 2℃/W R so =0.000172 m2℃/W 管壁的导热系数: λ=45 m 2℃/W 管壁厚度: b =0.0025 内外平均厚度: dm=0.0225 在下面的公式中,代入以上数据,可得oso i o i o si i i o R d bd d d R d d K αλα11++++=℃)⋅=2/(392m W(6).计算传热面积由以上的计算数据,代入下面的公式,计算传热面积:20.763.413921230219'm t K Q S m =⨯=∆=考虑15%的面积裕度,则: 24.87'15.1m S S ==§四. 工艺结构设计4.1.管径和管内流速选用Φ25×2.5的碳钢管,管长6m ,管内流速取ui=0.5m/s 。
4.2.管程数和传热管数根据传热管的内径和流速,可以确定单程管子根数:ns =)(952.945.002.0785.0)9963600/(53052422根≈=⨯⨯⨯=ii iu d V π按单程计算,所需传热管的长度是:ﻩm n d S L s o 7.1195025.014.34.87=⨯⨯==π若按单程管计算,传热管过长,宜采用多管程结构,可见取传热管长l=6m ,则该传热管程数为: ﻩ(管程)267.11≈==l L N p ﻩ则传热管的总根数为:)(190952根=⨯=⨯=s P n N N4.3.平均传热温差校正及壳程数'm t ∆=7.49204040140)2040()40140(=-----In℃此时:P==--1112t T t t 17.0201402040=--R==--1221t t T T 5204040140=-- 由图4-25(参见化学工业出版社的《化工原理(第四版)》147页,可查得:t ∆ψ=0.83﹥0.8,所以,修正后的传热温度差为:m t ∆= 'm t ∆t ∆ψ3.4183.07.49=⨯=℃于是,校正后的平均传热温差是41.3℃,壳程数为单程,管程数为2。
4.4.传热管排列和分程方法采用组合排列法,即每程内均按正三角形排列,隔板两侧采用正方形排列。