玻璃马蹄焰窑炉结构设计
第四章玻璃马蹄焰窑炉砖结构、钢结构设计与计算
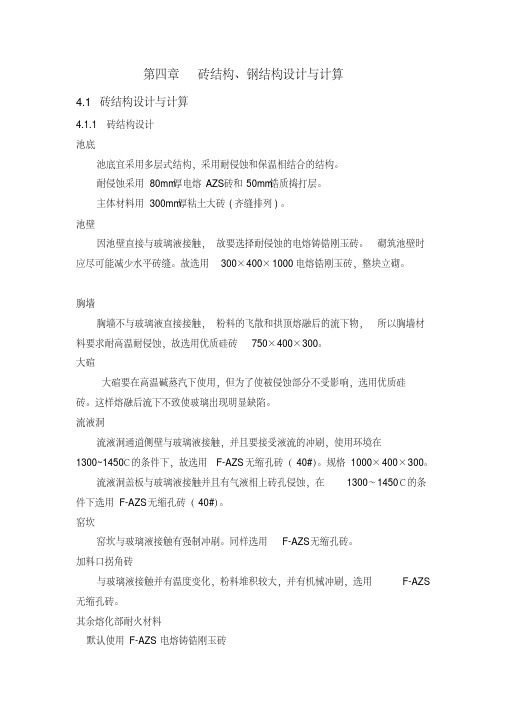
砖Ⅳ宽 B=150 mm
4.2 钢结构设计与计算
4.2.1 原始数据 5500mm 687.5mm 200mm 1150mm 500mm 5300mm 碹厚 胸墙高 池深 池壁砖厚 立柱平均间距 300mm 1500mm 1200mm 300mm 1000mm
窑炉大碹计算 已知:碹跨 b=5500 mm 求:碹砖大小头尺寸 半径 R= b
2
碹股高 f=687 mm
4f 8f
2
=
( 5500)
2
4( 687 )
2
=5847.5 mm
8 687
Байду номын сангаас
中心角 θ: sin arcsin
= 2
0
b 2R
=
7400 5847.5 2
=0.632749
2
0
=39.25
θ =78.5
ω 1=Vt+碹脚砖重 +碹脚钢重 =2.056+0.097 × 1× 1.8+0.0275 × 1=2.2581 t ω 2=胸墙重 =0.2 × 1.5 × 1× 3.3=0.99 t Q=2.2581+0.99=3.2481 t 假定立柱用 ?18a e=(0.2/2+0.18/2)=0.19 M=Qe=3.2481 × 0.19=0.617 t-m 4.2.3 拉条计算 T=[3.868 t δ 拉条取 1000 公斤 / 厘米2 F 拉条= 3737/1000 = 3.737cm2 φ 拉条=√( 4× 3.737/ Л)= 2.18 cm=21.8mm ,为了保险起见,用 Φ 25mm 4.2.4 立柱计算 × (1.57+1.83)+1.984 × 1.5-0.617]/(1.57+1.83+0.75)=3.737
玻璃马蹄焰窑炉结构设计

玻璃马蹄焰窑炉结构设计第⼆章结构设计2.1 熔化部设计2.1.1 熔化率K 值确定瓶罐玻璃池窑设计K 值在2.2 —2.6t/m 2.d 为宜。
熔化率取的过⼩,窑炉不节能,取得过⼤,熔化操作困难,或是达不到设计容量,本次取2.5t/ (m i ? d)。
理由如下:⽬前国外燃油瓶罐玻璃窑炉熔化率均在2.2 以上,⽽我国却在2.0 左右,偏低的原因: ( 1)整个池窑缺少有助于强化熔融的配套设计。
( 2)操作管理,设备,材料等使得窑后期⽣产条件恶化。
由于这些影响熔化能⼒的因素,现在瓶罐玻璃K 值偏⼩。
在全⾯改进窑炉结构和有关附属设备后,根据国内耐⽕材料配套情况和玻璃原料量与制备情况。
采取了K=2.5 t/ (nbd)。
2.1.2 熔化池设计(1)确定来了熔化率K值:熔化部⾯积100/2.5=40m2。
(2)熔化池的长、宽、深:L X B X H=8000m沐5000mr? 1200mm本设计取长宽⽐值为1.6 。
长宽⽐确定后,在具体确定窑池长度时,要保证玻璃液充分熔化和澄清,并考虑到砖窑材料的质量以及燃烧⽕焰的情况,⼀般要求⽕焰转向点在窑长的2/3处。
窑长应》4m。
在确定窑池宽度时,应考虑到⽕焰的扩展范围,此范围取决于⼩炉宽度、中墙宽度(两个⼩炉的间距,⼩炉的间距,既要便于热修,⼜不要降低⽕焰的覆盖⾯积,⼀般⼩炉之间的通道宽度取0.9~1.2 m )。
窑池宽度约为2~7m。
长宽选定后,当然具体尺⼨还要按照池底排砖情况(最好是直缝排砖)作出适量调整,池底⼀般厚为200~300m具体的池底排列会在后⾯设计的选材⽅⾯进⾏说明。
这⾥先不做细讲。
综上,本次选⽤L=8m ,B=5m。
窑池深度⼀般根据经验确定。
池深⼀般在900—1200m为宜。
池深不仅影响到玻璃液流和池底温度,⽽且影响玻璃液的物理化学均匀性以及窑炉的熔化率。
⼀般池底温度在1200 —1360 E之间较为合适。
池底温度的提⾼可使熔化率提⾼。
但池底温度⾼于1380C 时,需要提⾼池底耐⽕材料的质量及品种,否则则会加速池底的侵蚀并降低炉龄,且会增加玻璃球的结⽯含量,这对后道拉丝⽣产是不利的,影响池底温度的决定性因素是玻璃的铁含量和玻璃⽓氛。
《玻璃工业窑炉》教学课件—02马蹄焰窑

200~400mm,大型可达500mm。 3)长度:控制玻璃液的降温程度。 越长降温越多。1.2~1.5℃/cm。
4)流液洞的流量负荷
G K流 BH
式中K流,Kg/ (cm2·h)。
G为每小时通过 流液洞的玻璃 液量;B为流液 洞宽度;H为流 液洞高度。
缝,2~3mm,R为半径,δ为碹厚。 砌拱时,插入的直型砖不要太多,否则易塌拱。 拱脚要加固紧,拱脚松动也会造成塌拱。 横推力F为
F KG ctg
22
式中,K为温度修正系数
F大小影响因素 G的大小
θ的大小 平拱θ=0,F→∞ θ=180,F=0
温度tw1≥tw2,产生附加载荷 T↑,K↑
2 马蹄焰池窑
设计步骤:先确定池窑各部位的形式、尺 寸和材料。绘出草图。热工理论计算,砖 结构排列与计算、钢结构布置与计算。
设计原则:技术先进,施工可能,操作方 便,经济合理。
平剖面Ⅲ-Ⅲ、Ⅳ-Ⅳ
平剖面Ⅰ-Ⅰ、Ⅱ-Ⅱ
蓄热式马蹄焰池窑纵立剖面A-A
横立剖面B-B、C-C
蓄热式马蹄 焰玻璃池窑 侧视图
池深H:同玻璃液质量关系很大。池深须使 窑内不形成不动层。
①池深影响窑容量,即窑内停留时间。停留 1.5~2天。
②确定因素:玻璃颜色、玻液粘度、熔化率、 制品质量、燃料种类、池底砖质量、池底 保温和新技术采用(鼓泡、电助熔)等。
池深h可按近似公式计算
h=0.4+0.5lgV V——熔化池容积,m3 池壁砖的排列,有上下层,也有整块砖,全
长L:保证玻璃液在窑内停留一段时间,
满足其澄清。 满足燃料充分燃烧,不造成大温差,不直
马蹄焰窑炉设计说明书
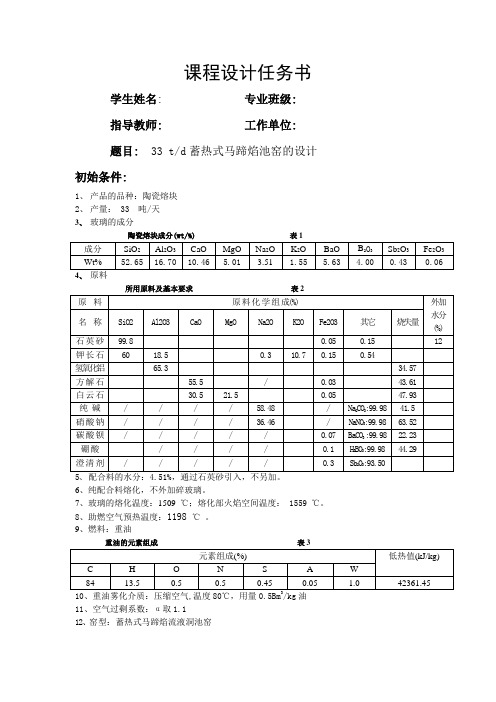
课程设计任务书学生姓名: 专业班级:指导教师:工作单位:题目: 33 t/d蓄热式马蹄焰池窑的设计初始条件:1、产品的品种:陶瓷熔块2、产量: 33 吨/天3、玻璃的成分陶瓷熔块成分(wt/%)表14、原料所用原料及基本要求表26、纯配合料熔化,不外加碎玻璃。
7、玻璃的熔化温度:1509 ℃;熔化部火焰空间温度: 1559 ℃。
8、助燃空气预热温度:1198 ℃。
9、燃料:重油重油的元素组成表310、重油雾化介质:压缩空气,温度80℃,用量0.5Bm/kg油11、空气过剩系数:α取1.112、窑型:蓄热式马蹄焰流液洞池窑要求完成的主要任务:一、撰写设计说明书,主要内容包括:1、设计依据及相关政策、法律、法规及设计规范2、物料平衡计算(列出计算过程)2.1配料计算2.2去气产物及组成计算3、热平衡计算(列出计算过程)3.1燃料燃烧计算3.2玻璃形成过程所消耗的热量计算3.3燃料消耗量近似计算4、窑炉的结构设计详细说明各部位的作用,各主要参数选择依据,并进行方案对比。
4.1熔化部设计包括熔化部的面积、长、宽、深度、火焰空间及投料口的尺寸。
4.2工作部的设计包括工作部的面积、长、宽、深度及火焰空间的尺寸。
4.3玻璃液的分隔设备的设计4.4出料口的设计4.5小炉口的计算与设计4.6蓄热室的计算与设计4.7烟道与烟囱尺寸的确定5、窑炉耐火材料的设计与选择包括池壁、池底、胸墙、大碹、蓄热室的耐火材料及保温材料的设计与选择。
要求作方案对比,阐述选择依据。
6、窑炉主要技术经济指标①熔化量:②熔化率:③熔化部面积:④冷却部面积:⑤一侧蓄热室格子砖的受热面积:⑥单位熔化部面积所占格子砖受热面积:⑦每公斤玻璃液所消耗的热量:⑧燃料消耗量:⑨玻璃熔成率。
二、用CAD绘制一张窑炉总图(3#图打印)时间安排:18周讲课、查阅资料、设计计算、绘制草图;19周 CAD制图;20周撰写设计说明书、答辩。
指导教师签名:年月日系主任(或责任教师)签名:年月日目录1.设计依据及相关的法律法规 (1)1.1设计的依据:课程设计任务书 (1)1.2国家相关法律、法规及设计规范 (1)1.3马蹄焰窑炉的特点 (2)2.物料平衡计算 (2)2.1配料计算 (2)2.2去气产物及组成计算 (4)3.热平衡计算 (5)3.1燃料燃烧计算 (5)3.2玻璃形成过程中所消耗的热量 (6)3.3燃料消耗量近似计算 (7)4.窑炉的结构设计 (8)4.1熔化部的设计 (8)4.2工作部的设计 (11)4.3玻璃液的分隔设备(流液洞)的设计 (11)4.4出料口的设计 (12)4.5 小炉口的计算与设计 (12)4.6蓄热室的计算与设计 (13)4.7烟道与烟囱尺寸的确定 (15)5. 主要技术经济指标 (16)6. 参考文献 (16)7. 总结 (16)设计题目:33 t/d蓄热式马蹄焰池窑的设计1 设计依据及相关的法律法规设计依据及其基本原则:随着工业生产现代化水平的日益提高,能源供应日趋紧张,在本设计中,为了节约能源、降低成本,采用有效的保温措施。
马蹄焰窑炉设计说明说-大连工业大学祥解

一、原始资料1、产品:高白料机制玻璃瓶罐。
2、出料量:每天熔化玻璃60吨。
3、玻璃成分(设计)(%):SiO2Al2O3CaO+MgO BaO Na2O+K2O71% 3.5% 10.5% 0.5% 14.5%4、料方及原料组成:原料料方%原料化学组成(%)外加水分% SiO2Al2O3CaO MgO Na2O Fe2O3其它失量石英砂51.985 99.350.2 0.1 0.05 0.05 15.0长石28.858 65.1319.940.24 0.11 14.03 0.12 0.43石灰石18.926 1 0.255.260.3 0.02 碳酸钠 99.2硝酸钠 98.12硫酸钠 0.14等等纯碱18.06 57.87 7.0 硝酸钠 1.162 1.5重晶石0.524 1.16 氧化钡 63.35合计119.5155、碎玻璃数量:占配合料量的33%。
6、配合料水分:靠石英砂和纯碱的外加水分带入,不另加水。
7、玻璃熔化温度:1400℃。
8、工作部玻璃液平均温度:1300℃。
9、重油。
元素组成(%)低热值(千卡/公斤)加热温度(℃)C H O N S A W86.42 12.16 0.55 0.2 0.15 0.02 0.5 10000 125 10、雾化介质:用压缩空气,预热到120℃,用量为0.6m3/公斤油。
11、喷嘴砖孔吸入的空气量:0.5m3/公斤油。
12、助燃空气预热温度:1050℃。
13、空气过剩系数a:取1.2。
14、火焰空气内表面温度:熔化部1450℃,工作部1350℃。
15、窑体外表面平均温度(℃):窑顶侧胸墙前后胸墙电容锆砖池墙池底熔化部250 180 200 160 130 17516、熔化池内玻璃液温度(℃):液面窑池上部(平均)窑池上下部交接层窑池下部(平均)池底1400 900 1280 1265 1250池深方向玻璃液温降:窑池上部为2℃/cm,窑池下部为1℃/cm。
马蹄焰玻璃窑炉设计技术培训 ppt课件
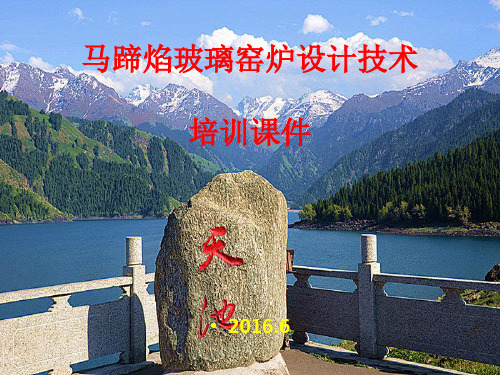
一、玻璃窑炉马蹄焰池窑简介
1.熔化池结构: 窑炉的熔化率主要取决于熔化温度,因为中碱和无碱玻璃球窑 的熔制温度比较高,如果进一步提高熔化温度来提高熔化率,会加 速对耐火材料的侵蚀,降低球质和影响炉龄。而采取鼓泡和电助熔 技术可以相应提高中下层玻璃温度,促进玻璃的均化,并且提高熔 化率。玻璃原料从熔化到澄清的行程也大,这有利于玻璃质量的控 制和提高,而长宽比又受到小炉结构设计、火焰长度及拐弯要求的 限制。池深不仅影响到玻璃液流和池底温度,而且影响玻璃液的物 理化学均匀性以及窑炉的熔化率。一般池底温度在1200—1360℃之 间较为合适。池底温度的提高可使熔化率提高。但池底温度高于 1380℃时,需要提高池底耐火材料的质量及品种,否则会加速池底 的侵蚀并降低炉龄,且会增加玻璃球的结石含量,这对后道拉丝生 产是不利的,影响池底温度的决定性因素是玻璃的铁含量和玻璃气 氛。当Fe2O3含量在0.25—0.3%范围内时,池深800—1200mm的玻 璃球窑,其垂直温降约为15—30℃/100mm。
一、玻璃窑炉马蹄焰池窑简介
6. 小炉: 目前小炉设计仍以实践经验为主,一个成功的设计者 应能用燃烧理论、火焰传热理论去分析、应用和总结实践经验。
(1) 小炉下倾角一般在18—35°范围内选用,燃油小炉一般 选用22—25°,燃烧天然气和干气的小炉下倾角可以大些。在实际 生产行中油枪有5°左右的上仰角,在采用天然气和干气时的仰角 还要更大些,其目的是让火焰与玻璃液面平行。
(2) 小炉喷出口速度(或小炉出口面积),由于燃油雾化后 喷入窑炉空间的燃烧过程中伴随着油雾的气化过程,因此燃料混合 物喷出的速度大,气化膨胀的阻力也大,油类燃料在窑内的停留时 间一般比天然气燃料的时间长,因此燃油小炉喷出的速度可以稍低。 当改用天然气时,如果喷出速度太低,会造成燃烧不完全。小炉喷 出口速度一般参照小炉喷出口处相应温度的空气速度来进行计算比 较合适。小炉喷出的助燃空气要有一定的容积厚度,取其宽高比为 2—3.5。 为了使火焰不直接冲刷胸墙,两座小炉内侧间距应不小于 0.6,小炉外侧与胸墙间距不小于0.3。
马蹄焰窑炉的司炉操作要点
马蹄焰窑炉的司炉操作要点摘要:马蹄焰窑炉的整个运行中,司炉操作是重中之重,特别是窑炉投产之初的工艺摸索及工艺参数的设定,笔者参加过多次马蹄焰窑炉投产之初的司炉操作设计,再此进行总结,以供从事相关专业的人员进行交流切磋。
关键词:马蹄焰窑炉操作要点一、前言马蹄焰窑炉是玻璃窑炉的一种,因其结构与其他玻璃窑炉有着明显的不同,其主要构成有烟道、蓄热室、小炉、熔化池、流液洞、工作池、(料道、马弗炉)等,简要示意如下:马蹄焰窑炉结构示意图二、马蹄焰窑炉的司炉操作要点说明1.燃烧火焰状态的调整窑炉投产运行以后,加料使玻璃液面达到规定的高度,开始调整燃烧火焰的状态。
首先调整窑压,以加料口观察为基准调节总烟道闸板,使窑压处于理想的微正压(5Pa)状态。
调整喷枪,使火焰覆盖面积大而稳定。
调整过程中及时在工作池上方观察孔判断熔化池火焰状态。
燃烧火焰应满足明亮但不透明;贴近液面处的火焰不发卷、不发黑,而且流股平稳;火焰尾部能顺利转向,而没有明显上飘现象。
通过蓄热室换向操作,观察调整的状态要稳定一致2.窑炉熔化温度的测量一般窑炉为监控熔化温度,在窑炉的不同部位设置不同的测温装置,通过显示和操作实现控制。
(1)在加料口近侧设置辐射温度计,测量火焰的温度。
此温度测量值因受火焰直接影响有不稳定现象,但应大致稳定在一定的范围内。
这一温度值表明火焰的燃烧状态,并影响配合料的熔化效果。
(2)在窑炉中后部安装另一辐射高温计,测量窑炉中部低层空间的温度。
这一温度值应相对稳定。
熔化池的控制温度可依此作为参考。
这一温度的高低和变化直接影响玻璃液的澄清和均化过程。
在半分隔玻璃窑炉中,这一温度值同时影响工作池的温度,对玻璃的均化和产品的质量具有实际意义。
(3)在窑炉后2/3碹顶的中央安装热电隅测温装置,测量窑内空间上部温度。
依此作为全窑温度的测量控制点。
此温度因受火焰干扰较小,温度较为稳定。
实测的结果显示温度值略低于玻璃液面实际温度。
另外,这一温度也反映碹顶硅砖的工作温度,大碹的安全情况依此温度实施监控。
燃煤气马蹄焰玻璃窑炉小炉和喷火口的设计及工艺操作控制
燃煤气马蹄焰玻璃窑炉小炉和喷火口的设计及工艺操作控制朱柏杨马蹄焰玻璃窑炉的小炉是窑炉的关键部位,它承担组织燃料产生火焰的任务,是窑炉火焰的初始燃烧部位;它还是连接熔化池和回收高温废气热回收的通道。
小炉和喷火口的设计尺寸大小、角度和火焰喷出的速度对燃料燃烧和火焰形状有重要的影响,小炉、喷火口的不合理设计会使燃料燃烧不合理,会使火焰冲击胸墙和大碹,并造成燃料不完全燃烧和废气中氮氧化合物升高,对玻璃窑炉的节能环保运行不利。
因此,如何设计好小炉和喷火口,或者对已经定型运行的马蹄焰窑炉如何合理组织小炉火焰的燃烧工艺,下面作如下几个方面的分析和探讨:一、马蹄焰玻璃窑炉小炉和喷火口的设计:燃料在玻璃窑炉大璇内的燃烧属于扩散式燃烧,助燃空气从舌拱上部和燃气在舌拱下部喷入小炉的速度、厚度及与喷出的交角、燃气与空气的温度、燃气与空气在小炉的合理配比程度等等;首先取决于小炉和喷火口的原始工艺计算和设计布置,而后续的工艺操作控制管理水平决定了出小炉和喷火口火焰形状、燃料在大璇内的燃烧状况,进而影响到火焰对玻璃熔池的热辐射和玻璃配合料的熔制。
目前小炉和喷火口的设计仍以实践经验设计为主,设计和使用管理人员应能用燃烧理论、火焰传热理论去分析、应用和总结实践经验,下面是一些经验设计数据:1、燃煤气小炉下倾角一般在18°—25°范围内选用,燃油小炉一般选用22°—25°,燃烧焦炉煤气、碳氢化合物含量较高的混合煤气和天然气的小炉下倾角可以大些。
在实际生产行中使用重油和石油焦粉的喷火口处的烧嘴砖喷火口枪有5°左右的上仰角,在采用天然气和焦炉煤气时的仰角还要更大些,其目的是让火焰与玻璃液面平行,烧嘴砖一般安装在距喷火口砖0~600mm的位置。
2、小炉喷火焰出口速度(或喷火口面积),小炉喷出口速度一般参照小炉喷出口处相应温度的空气速度来进行计算比较合适。
同时,小炉内煤气火焰的初期着火燃烧点应控制在小炉长度的1/2~2/3,火焰在喷火口的速度控制在8~10m/s之间,对于碳氢化合物含量较高的混合煤气,小炉的设计宽度以取较大值为好。
燃煤气马蹄焰玻璃窑炉小炉和喷火口的设计及工艺操作控制
燃煤气马蹄焰玻璃窑炉小炉和喷火口的设计及工艺操作控制朱柏杨马蹄焰玻璃窑炉的小炉是窑炉的关键部位,它承担组织燃料产生火焰的任务,是窑炉火焰的初始燃烧部位;它还是连接熔化池和回收高温废气热回收的通道。
小炉和喷火口的设计尺寸大小、角度和火焰喷出的速度对燃料燃烧和火焰形状有重要的影响,小炉、喷火口的不合理设计会使燃料燃烧不合理,会使火焰冲击胸墙和大碹,并造成燃料不完全燃烧和废气中氮氧化合物升高,对玻璃窑炉的节能环保运行不利。
因此,如何设计好小炉和喷火口,或者对已经定型运行的马蹄焰窑炉如何合理组织小炉火焰的燃烧工艺,下面作如下几个方面的分析和探讨:一、马蹄焰玻璃窑炉小炉和喷火口的设计:燃料在玻璃窑炉大璇内的燃烧属于扩散式燃烧,助燃空气从舌拱上部和燃气在舌拱下部喷入小炉的速度、厚度及与喷出的交角、燃气与空气的温度、燃气与空气在小炉的合理配比程度等等;首先取决于小炉和喷火口的原始工艺计算和设计布置,而后续的工艺操作控制管理水平决定了出小炉和喷火口火焰形状、燃料在大璇内的燃烧状况,进而影响到火焰对玻璃熔池的热辐射和玻璃配合料的熔制。
目前小炉和喷火口的设计仍以实践经验设计为主,设计和使用管理人员应能用燃烧理论、火焰传热理论去分析、应用和总结实践经验,下面是一些经验设计数据:1、燃煤气小炉下倾角一般在18°—25°范围内选用,燃油小炉一般选用22°—25°,燃烧焦炉煤气、碳氢化合物含量较高的混合煤气和天然气的小炉下倾角可以大些。
在实际生产行中使用重油和石油焦粉的喷火口处的烧嘴砖喷火口枪有5°左右的上仰角,在采用天然气和焦炉煤气时的仰角还要更大些,其目的是让火焰与玻璃液面平行,烧嘴砖一般安装在距喷火口砖0~600mm的位置。
2、小炉喷火焰出口速度(或喷火口面积),小炉喷出口速度一般参照小炉喷出口处相应温度的空气速度来进行计算比较合适。
同时,小炉内煤气火焰的初期着火燃烧点应控制在小炉长度的1/2~2/3,火焰在喷火口的速度控制在8~10m/s之间,对于碳氢化合物含量较高的混合煤气,小炉的设计宽度以取较大值为好。
第二章玻璃马蹄焰窑炉结构设计
第二章玻璃马蹄焰窑炉结构设计
玻璃马蹄焰窑炉是一种用于玻璃加工的特殊类型玻璃熔融装置,具有
高温、高效、节能等优点。
它的结构设计对于降低能耗、提高产能和改善
产品质量具有重要意义。
本文将从炉体结构、炉墙结构和燃烧系统三个方
面讨论玻璃马蹄焰窑炉的结构设计。
首先,炉体结构是玻璃马蹄焰窑炉的基础部分,它直接关系到炉膛的
稳定性和工作效果。
炉体结构应该采用耐火材料,以抵御高温和化学侵蚀。
常用的耐火材料有高铝砖、硅酸盐砖等。
此外,炉体结构还应具备一定的
隔热性能,以减少散热损失。
为了提高炉膛的稳定性,可以在炉体内部设
置加强筋或钢结构支撑,增加整体的承载能力。
其次,炉墙结构对于炉膛的保温和传热有着重要的影响。
炉墙结构通
常由内壁、外壁和隔热层组成。
内壁常用耐火砖,用于抵御玻璃的高温冲
击和化学侵蚀。
外壁通常采用碳钢材料,并带有冷却装置,用于冷却炉壁
和减少外界对炉体的热辐射。
隔热层通常由耐火纤维或耐火浇注料构成,
其作用是减少炉体的热传导和散热损失,提高炉膛的热效率。
综上所述,玻璃马蹄焰窑炉的结构设计对于提高生产效率、降低能耗
和改善产品质量具有重要意义。
炉体结构、炉墙结构和燃烧系统是重要的
设计要素,需要考虑耐火性能、隔热性能、稳定性和高效率等因素。
在设
计过程中,还需要根据具体的生产要求和工艺流程进行优化和调整,以实
现最佳的设计效果。
- 1、下载文档前请自行甄别文档内容的完整性,平台不提供额外的编辑、内容补充、找答案等附加服务。
- 2、"仅部分预览"的文档,不可在线预览部分如存在完整性等问题,可反馈申请退款(可完整预览的文档不适用该条件!)。
- 3、如文档侵犯您的权益,请联系客服反馈,我们会尽快为您处理(人工客服工作时间:9:00-18:30)。
第二章结构设计2.1熔化部设计2.1.1熔化率K值确定瓶罐玻璃池窑设计K值在2.2—2.6t/m2.d为宜。
熔化率取的过小,窑炉不节能,取得过大,熔化操作困难,或是达不到设计容量,本次取2.5t/(m2·d)。
理由如下:目前国外燃油瓶罐玻璃窑炉熔化率均在2.2以上,而我国却在2.0左右,偏低的原因:(1)整个池窑缺少有助于强化熔融的配套设计。
(2)操作管理,设备,材料等使得窑后期生产条件恶化。
由于这些影响熔化能力的因素,现在瓶罐玻璃K值偏小。
在全面改进窑炉结构和有关附属设备后,根据国内耐火材料配套情况和玻璃原料量与制备情况。
采取了K=2.5 t/(m2·d)。
2.1.2熔化池设计(1)确定来了熔化率K值:熔化部面积 100/2.5=40m2。
(2)熔化池的长、宽、深:L×B×H=8000mm×5000mm×1200mm本设计取长宽比值为1.6。
长宽比确定后,在具体确定窑池长度时,要保证玻璃液充分熔化和澄清,并考虑到砖窑材料的质量以及燃烧火焰的情况,一般要求火焰转向点在窑长的2/3处。
窑长应≥4m 。
在确定窑池宽度时,应考虑到火焰的扩展范围,此范围取决于小炉宽度、中墙宽度(两个小炉的间距,小炉的间距,既要便于热修,又不要降低火焰的覆盖面积,一般小炉之间的通道宽度取0.9~1.2 m )。
窑池宽度约为2~7m。
长宽选定后,当然具体尺寸还要按照池底排砖情况(最好是直缝排砖)作出适量调整,池底一般厚为200~300m。
具体的池底排列会在后面设计的选材方面进行说明。
这里先不做细讲。
综上,本次选用L=8m ,B=5m。
窑池深度一般根据经验确定。
池深一般在900—1200mm为宜。
池深不仅影响到玻璃液流和池底温度,而且影响玻璃液的物理化学均匀性以及窑炉的熔化率。
一般池底温度在1200—1360℃之间较为合适。
池底温度的提高可使熔化率提高。
但池底温度高于1380℃时,需要提高池底耐火材料的质量及品种,否则则会加速池底的侵蚀并降低炉龄,且会增加玻璃球的结石含量,这对后道拉丝生产是不利的,影响池底温度的决定性因素是玻璃的铁含量和玻璃气氛。
当Fe2O3含量在0.25—0.3%范围内时,池深800—1200mm的玻璃球窑,其垂直温降约为15—30℃/100mm[6]。
表2-1 中国池窑熔化池池宽注:池底保温时,表1-2中池深值增加20%-30%[6]。
故熔化池深度预先取:H=1.2m 。
熔化池的深度,在本设计中我们一改以往国内设计的传统经验即:熔化区与澄清区池深一致的设计观点,改为更科学有效的加深澄清区,加深幅度为200mm ,加深到1400mm,即H=1400mm,后面会进行复核。
同时加设窑坎和鼓泡装置。
2.1.3 火焰空间本次设计:采用B火=5400mm,B熔=24 KJ/m3·h。
本次设计:采用火焰高度为1500mm,火焰空间宽度为5400mm,煊升高1/8,为675mm。
火焰空间长度为窑炉长度8000mm。
从理论上解释:扩大火焰空间,有利于燃料完全燃烧,稳定火焰,在窑体保温的情况下扩大火焰空间对该部位的散热损失,影响极小,相反,由于燃料完全燃烧,使得燃料在窑池空间内的燃烧技术效率提高也即有更多的热量用于加热熔池和玻璃液。
其次,以气流动力流型来考虑,也要求在火焰与大碹之间有一股循环气流来保护大碹,并有助于把火焰流股压向液面。
本设计采用大的火焰空间结构,因为尽量大的火焰空间适合燃油火焰的刚性好,不发飘的特点,有利于充分燃烧。
所以在窑宽5000mm的基础上,两边总共加宽400mm即这样可以保证在高的熔化率的同时降低熔化部的热负荷。
2.1.4 加料口的设计投料时熔制过程中的重要工艺环节之一,它关系到配合料的熔化速度、熔化区的热点位置、泡界线的稳定,最终会影响到产品的质量和产量。
加料口是马蹄焰玻璃池窑的重要部位之一。
熔化工艺和所选用的加料机对加料口的要求,其设计必须能使配合料呈薄层或小堆状均匀稳定地进入熔化池,形成一个便于熔化作业调节的“圈式”配合料流型,均布在熔化部玻璃表面,加料口是池窑结构上的薄弱环节,容易损坏,设计时应合理加大、加长配合料进入熔化池的通道,以减少玻璃液因接触耐火材料的损坏。
同时,还要对火焰有较好的密封,防止火焰对加料口上部材料造成损坏并减少滋流热量损失[3]。
设一个加料池, 单侧加料,加料口呈斜喇叭形, 向前墙倾斜10°,向后墙倾斜3°,预熔池长1600mm。
配以悬挂式密封加料机, 既减少了料粉飞扬, 又减少了辐射热损失, 同时还加速了配合料的熔化。
(1)采用单侧加料与采用两侧加料相比,可相应减少窑头仓,使配合料的输送和贮存更为简单,同时也减少加料口的热损失,降低投资成本[15]。
(2).加料池加料池采用大的预熔池,使配合料在预熔池中的到充分加热,提高熔制效率,梯形的池型有助于配合料形成“圈式”料流。
从而提高熔融效果,提高配合料在窑炉中的路程距离,得到更多来自火焰的热量,提高熔化率,能量的利用率和熔化效果,j加料口采用内宽外窄型,内开口1300mm,外开口800mm。
2.1.5 窑坎与鼓泡设计窑坎高为1/2D=600mm,宽400mm,用二层200mm厚的砖错缝。
熔窑坎设置在熔池中鼓泡点(窑炉的2/3处)以后766.7mm处,窑坎高度600mm,为双层砖铺排,总宽度为400mm。
熔化区内底部玻璃液通过窑坎是有一个爬升过程。
这样增强了热量的交换,使玻璃液温度升高,黏度降低,有助于玻璃液中气泡的排出。
此外,减少澄清区玻璃液回流量,降低热损失。
2.2 分隔装置设计2.2.1火焰空间分隔装置火焰空间的分隔采用全分隔结构(两道墙),全分隔能消除熔化部温度的波动对工作池的影响,这样比较稳定的控制了工作池内玻璃液的温度,保证了制瓶机成型温度的稳定。
2.2.2 玻璃液分隔装置用倾斜式流液洞,熔化部与工作部两道墙完全分隔流液洞尺寸。
流液洞长×宽×高=1200×400×300mm。
2.3冷却部的设计(工作池)一般工作池半径小于等于熔化池池宽,工作池深度浅于熔化池池深300—400mm[8]。
工作池面积占熔化面积20-25%。
本次设计:矩形工作池,长×宽×高=1200×5000×600mm工作池面积:6.0m2,占熔化部面积的15%。
现在的工作池正在朝着小面积浅工作池发展,工作池由于与熔化池相对独立,所以其形状不受其他因素影响,一般马蹄焰池窑工作部占熔化面积的10—15%,深度一般为0.6~0.9m。
小面积的工作池设计,池深较浅,静压小,从而减少了玻璃液的回流,保证玻璃液的质量。
2.4热源供给部分的设计(小炉)本次设计综合考虑改进:第一,小炉长度取3m;小炉下倾角为23°;小炉底的下倾角为18°。
第二,小炉底下操作空间尺寸,由于该处的操作环境差,故取大一点的数据,当然也不能太大,取4.0m;小炉底外表面到操作走台的高度,以操作员走路不低头为准,取1.8m。
第三,小炉口的尺寸,小炉出口煊的股跨比最好为1/8,小炉口出口煊的煊砖厚度为0.4m,小炉出口煊的长度为0.6m。
综合来说:(1)油喷嘴安装在小炉口下面,喷嘴中心离液面高度约为200mm,油枪上倾5o。
(2)油喷嘴一般距池墙外壁为400mm,小炉口安装2支油喷嘴时,喷嘴直径为4.0mm,油喷嘴间距为600mm。
(3)蓄热式马蹄焰池窑空气出口速度为8m/s,一般空气的平均预热温度以1300℃为考虑。
回火速度为13m/s;喷口的总面积占熔化池面积的3%——空气出口面积为0.2m。
(4)首先小炉口要扁而宽,宽的小炉口可以在熔化区形成一宽而热量集中的火焰覆盖面,有利于对于配合料的加热。
马蹄焰空气出口宽高比取4.2,出口宽取1500mm,高取357mm;油喷嘴下倾角为25%;补充来说,为使空气与油雾混合良好,可使小炉地板下斜5°,同时适当加长水平通道,水平通道长度为2750mm[6]。
(5)再次,小炉中心线与熔化池中心线要有一定的夹角3~6度。
这样可以避免火焰冲刷胸墙,也有利于火焰的转向。
最后,小炉通道后部用竖向缝与蓄热室分开。
这样可以确保窑炉与蓄热室这两部分结构的热膨胀不受阻碍[17]。
2.5余热回收部分的设计(蓄热室)本次设计:采取在国内外普遍使用的多通道箱型蓄热式,使空气获得较高的预热温度,死角较少,也可选用最适宜的耐火材料,经济实惠。
先进蓄热室首先要具有高的蓄熔比和高的预热温度,高的余热回收效率。
为了实现这些目标设计中采用了各项性能指标优越的八角筒形格子砖,增加了格子体高度使,使通道内气体保持了最有利的速度。
蓄熔比为51:1左右,格子体体积/熔化面积=3.07m3/m2。
格子体体积为122.8 m3,细长比2.56,采用八角筒形状为格子体,格子体主要尺寸:4180×3200×9600mm,格孔尺寸160×160mm。
经验设计:蓄熔比:51:1,F=51×40=2040m2 F=2040 m2格子体当量直径 d=[4×(160×160)]/[2×(160+160)]=160 mmG单位格子体受热表面积为:14.94 m2格子体体积为:V=2040/14.94=136.455 m3细长比取H/LB=2.56 H/LB=20.56 H×LB=136.55所以:H=9.64 m LB=14.17 m长宽比1.3 宽=3.2m=3200 mm排13块格子体即:3120 mm,预留80 mm膨胀。
所以实际蓄热室宽为3200 mm长=4.32m=4320 mm 布17块格子体即:4080 ,预留100 mm膨胀所以实际蓄热室长为:4180 mm格子体为间歇层错位码砌。
格子体砖高120 mm 所以格子体为80层,格子体高度为9.6 m。
[6]2.6 排烟供气部分的设计为使窑炉作业连续、正常、有效的进行,设置了马蹄焰池窑排烟供气部分,它包括:支烟道、总烟道、换向设备闸板及烟囱等[6]。
由于烟道内的烟气温度较低(烟气出蓄热室的温度约为600℃左右,到烟囱根的温度约为400℃左右),因此烟道内墙、底和碹均采用粘土质耐火砖砌筑。
眼到底,墙和碹都进行保温,地下水位高的地方或室外烟道还应做防水层。
玻璃熔炉的烟囱现在多用钢筋混凝土浇注,内衬粘土质耐火砖。
烟囱高度采用40m,玻璃池窑采用高度﹤50m的砖烟囱。
烟道中废气流速取2(标)/s;烟道截面高度取700mm,宽度取600mm。
爬坡高度取30°。
2.7结论实践证明,引进窑的熔化率、能耗及炉龄等主要技术指标与国内自行设计的池窑相比确实有明显的优点。