循环流化床干法脱硫+COA脱硝技术在CFB炉上的应用
循环流化床烟气脱硫技术在燃煤机组脱硫工程中的应用
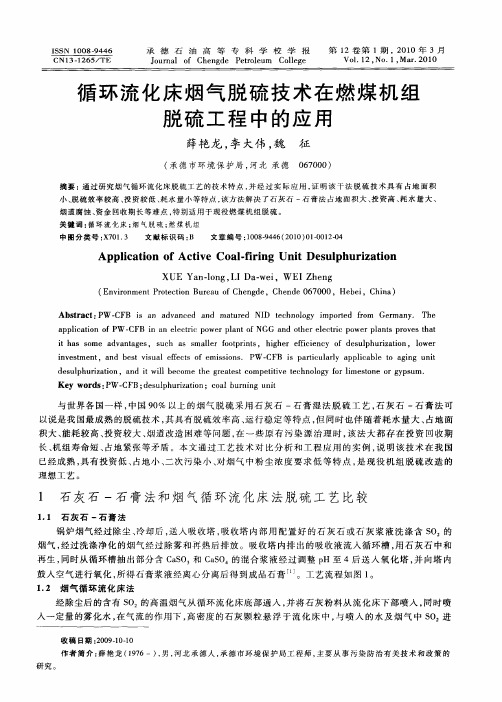
再生 , 同时从循环槽 抽 出部分 含 C S 和 C S 的混合浆 液经过调 整 p aO aO H至 4后送 人氧 化塔 , 向塔 内 并
鼓人空气进 行氧化 , 得石膏浆来自液经离 心分离后 得到成 品石膏 。工艺流 程如 图 1 所 。 1 2 烟气循环 流化床 法 .
经除尘后 的含有 S , O 的高温烟气从 循环 流化床底部 通人 , 将石灰 粉料从 流化床 下部喷人 , 时喷 并 同
i v s me t n e t v s a fe t f e s i ns PW — B s pa tc l ry a l a l o a i g u i n e t n ,a d b s iu l e f c s o mi so . CF i ri u a l pp i b e t g n n t c
长 、 组寿命短 、 机 占地 紧张 等矛盾 。本文通过 工艺技 术对 比分 析 和工 程应 用 的实 例 , 明该技 术在 我 国 说 已经成 熟 , 具有投 资低 、 占地小 、 次污染小 、 烟气 中粉 尘浓 度要 求 低 等特 点 , 现役 机 组脱 硫改 造 的 二 对 是
理想工艺 。
XUE Ya —o g. IDa we . W ElZh n h ln L . i eg
( n i n n rtcin B ra fC e g e E vr me t oe t ue u o h n d ,Ch n e0 7 0 o P o e d 6 0 0,He e ,C ia b i hn )
关 键 词 : 环 流化 床 ; 气脱 硫 ; 煤 机组 循 烟 燃
中 图分 类 号 : 7 1 3 X 0 . 文 献 标识 码 : B 文 章编 号 :0 89 4 ( 01 0 —0 20 1 0 —4 6 2 O) 10 1 -4
烟气循环流化床脱硫CFB-FGD技术使用简介

锅炉的两个装置的基本情况。
2.烟气CFB脱硫工艺简介
无论是Lurgi公司的CFB工艺, Wulff公司的RCFB工艺还是F.L. Smith的GSA工艺,它们在工作原理上都是很类似的。因此我们以Lurgi公司的CFB工艺为基础对烟气CFB脱硫工艺作简单的介绍。
要一台干消化器用来制备消石灰粉,然后用空气斜槽进行输送就可以了,从而
大大简化了工艺流程。
在各种负荷条件下,CFB烟气脱硫系统都能很好地适应.当负荷从100%变化到10%,系统称仍能很好地工作,这使得CFB工艺既能由于调峰机组,又能用于带基本负荷的机组。
CFB工艺所产生的脱硫副产品呈干粉状,非常便于处置。其化学组成与喷雾干燥工艺的副产品相类似,主要CaSO3、CaSO4以及未反应完的吸收剂(Ca(OH)2)等构成。脱硫副产品中是否含有大量的飞灰,则取决于在CFB烟气脱硫系统强是否安装了前级除尘器。CFB烟气脱硫系统的脱硫副产品的处置方法也与喷雾干燥的副产品基本相同。CFB工艺的副产品在加水后会硬化,硬化后的屈服强度可达15-18N/mm2,压实密度为1.28g/cm3,而其渗透率则与黏土类似,约为3X10-11。由此可见该副产品的强度与混凝土接近,很适合作矿井回填、道路基础。如能进一步加以开发,可能成为良好的建材工业的原料。
德国Wulff公司是一个成立较晚的设计和建造烟气CFB脱硫工程的小型企业。它的创始人R. Graf原是Lurgi公司在烟气CFB脱硫技术开发方面的主要负责人。脱离Lurgi公司后自建了Wulff公司,专门从事烟气CFB脱硫技术的开发工作,在Lurgi技术的基础上开发研制了一种叫做回流式烟气循环流化床的烟气CFB脱硫技术,对烟气CFB脱硫技术作了较大的改进,使之更加适用于动力工业(详见后)。
循环流化床锅炉炉内喷钙脱硫技术的应用

循环流化床锅炉炉内喷钙脱硫技术的应用【摘要】介绍了炉内喷钙干法脱硫工艺和反应原理,总结了改造后的主要成果,对产生的社会和环境效益进行了分析。
炉内喷钙脱硫技术在循环流化床锅炉上的应用效果良好。
【关键词】炉内喷钙;循环流化床;干法山东兖矿国际焦化有限公司地处国家二氧化硫两控区,随着国家、地方环保政策的逐步调控,对二氧化硫排放指标要求越来越严,浓度、总量双达标已事关企业的生存与发展。
公司锅炉系统原配套脱硫装置设计简单,为在皮带上添加碎石硝,脱硫成本高、效率低、操控难度大。
为降低锅炉烟气二氧化硫排放浓度,保证锅炉烟气稳定达标排放,结合公司循环流化床锅炉的特点,公司采用炉内喷钙干法脱硫技术对锅炉脱硫系统进行了改造。
本文介绍了该技术在循环流化床锅炉上的应用和实践。
1.原脱硫设计工艺在锅炉的动力煤存放地共有两个下料口,一个用来下煤,另一个用来下细石灰石(石硝)。
当锅炉上煤时,同时开启两个下料口的振动给料机,煤和细石灰石落在同一条皮带上---1#皮带,根据细石灰石含钙量,人工控制按钙硫比4左右比例添加。
经1#皮带后,煤与细石灰石依次经过自冷除铁器、振动筛、破碎机充分混合后再依次经过2#皮带、3#皮带、煤仓,然后经给煤机进入锅炉燃烧。
公司锅炉为3台UG-75-3.82-450-41M型号的循环流化床锅炉,运行方式为两开一备。
工艺主要缺陷:1.1脱硫效率低。
脱硫剂为细石灰石,颗粒大(1-3mm),混合不均,造成脱硫效果不稳,超标现象时有发生(二氧化硫浓度指标为900mg/Nm3)。
1.2脱硫剂添加人工控制,易造成脱硫剂的浪费,为保证排放不超标,钙硫比通常保持较高水平(4左右),甚至更高。
1.3煤和脱硫剂下料口各只有一个,断煤或脱硫剂添加不及时出现问题后会影响锅炉运行和排烟浓度控制。
2.炉内喷钙脱硫工艺2.1系统基本组成包括:石灰石钢粉仓系统、石灰石输送系统、辅助设备及程控系统等。
石灰石粉(细度要求250目)由罐车运至钢粉仓附近,钢粉仓附带的快换接头与罐车连接,完毕后打开手动蝶阀,石灰石粉由罐车气源送至钢粉仓。
CFB干法烟气脱硫技术的应用

循环流化床干法烟气脱硫技术的应用1. 概况烟气脱硫技术按脱硫产物的干湿形态,可以分为湿法、半干法、干法工艺,循环流化床烟气脱硫属于干法脱硫工艺,较多运用于国内小机组的烟气脱硫改造项目中。
南昌发电厂装机容量2×125MW,配2台420t/h燃煤锅炉,采用循环流化床干法脱硫工艺、一炉一塔脱硫装置,烟气尾部安装布袋除尘器。
该装置于2007年7月完成系统调试,8月进入试运行,脱硫效率达到85%以上,烟尘出口浓度小于50mg/Nm3,目前该脱硫装置运行稳定。
2. 工艺流程循环流化床脱硫工艺采用干态的消石灰作为吸收剂,通过二氧化硫与粉状消石灰氢氧化钙在Turbosorp反应器内发生反应,去除烟气中的SO2,通过吸收剂的多次再循环,延长吸收剂与烟气的接触时间,提高烟气脱硫效率。
锅炉炉膛燃烧后的烟气通过空气预热器出口,进入静电除尘器ESP 预除尘。
经过静电除尘预除尘之后,烟气从锅炉引风机后的主烟道上引出从底部进入Turbo反应器并从上部离开。
烟气和氢氧化钙以及返回产品气流,在通过反应器下部文丘里管时, 受到气流的加速而悬浮起来,形成流化床,烟气和颗粒之间不断摩擦、碰撞,强化了气固之间的传热、传质反应。
通过向反应器内喷水,使烟气温度冷却并控制在70 ℃左右,达到最佳的反应温度与脱硫效率。
与烟气接触发生化学反应剩下的烟尘和烟气一起离开反应器并进入下游的布袋除尘器。
经过布袋除尘器净化后的烟气经增压风机和出口挡板门后排入210m高度烟囱。
工艺流程见图1 所示。
3. 设计参数3.1 煤质分析南昌电厂燃用煤种较多,矿点主要分布在萍乡、丰城、高安一带。
表1为2×125MW 机组设计燃用煤种的煤质分析结果。
3.2 设计烟气参数烟气主要参数见表2。
3.3 生石灰参数石灰成分见表3。
4. 影响脱硫效率的因素及对策4.1 反应温度运行过程中反应塔的温度变化对脱硫效率的影响较大,反应塔烟气温度越低,脱硫效率越高。
控制脱硫反应温度是通过向反应塔内喷入工艺水来调节的。
循环流化床在脱硫技术中的应用
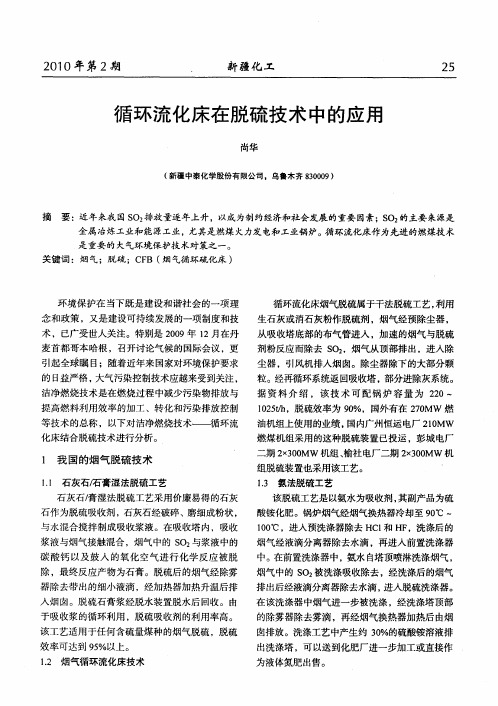
本工艺流程 由排烟预除尘、 烟气冷却 、 氨的充 人、电子束照射和副产品捕集等工序所组成 。锅 炉烟气经过除尘器粗滤处理之后进人冷却塔 ,冷
脱硫成本中等 ;
却塔 内喷射冷却水将烟气冷却 到适合于脱硫 、脱
硝处理的温度( 7 ℃) 约 O 。在反应器进 口处将一定 的氨气 、压缩空气和软水混合 喷人,冷却后的烟
1 烟气 循环 流化 床技 术 . 2
为液体氮肥出售。
2 6
1 喷雾干 燥法脱 硫工艺 . 4
新疆化工
21 0 0年第 2 期
() 3 丹麦 F . i 公司开发的气体悬浮吸收 .S t L mh
喷雾干燥法脱硫工艺以石灰为脱硫吸收剂, 石
灰 经消化 加 水制 成消 石灰乳 ,消石灰 乳在 吸收塔 内被 雾化成 细小 液滴 ,与烟 气 中的 S 2 0 发生化学 反应 生成 C S 3 C S , a O 和 aO4达到脱 除烟气 中的 S 2 O
(S ) G A 烟气脱硫技术。
21 工艺特 点 .
C B 工 艺具 有 以下 主 要 特点 :脱 硫 率 高 F ( a = .~1 时 , 8% ,与湿法相接近 , C/ 1 S 2 . 5 >5 ) 容易 选择最佳的 C B 操作气速 ,使得气固两相流在 F
的 目的。脱硫反应产物及未被利用的吸收剂 以干 燥的颗粒物形式随烟气带出吸收塔 , 进人除尘器 被收集下来 。除尘后的烟气经烟囱排放 。
的 1益严格 , 3 大气污染控制技术应越来受到关注 , 洁净燃烧技术是在燃烧过程中减少污染物排放与 提高燃料利用效率的加工、转化和污染排放控制 等技术的总称 ,以下对洁净燃烧技术——循 环流 化床结合脱硫技术进行分析。
据 资料 介 绍 ,该 技 术 可 配锅 炉 容 量 为 20 2
CFB锅炉烟气脱硫方式的比较
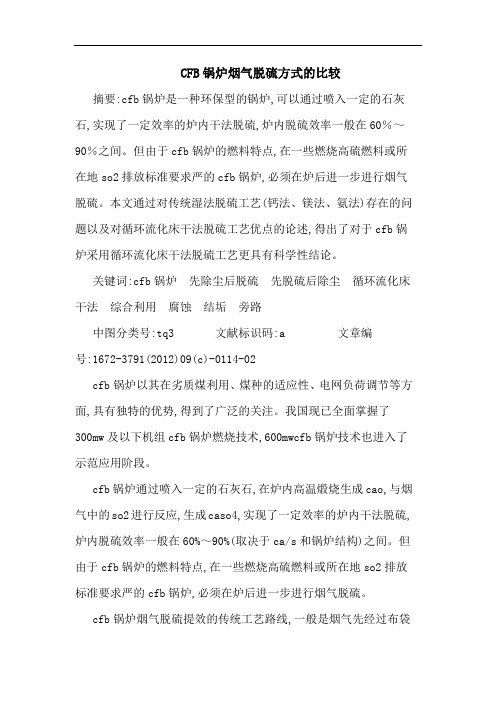
CFB锅炉烟气脱硫方式的比较摘要:cfb锅炉是一种环保型的锅炉,可以通过喷入一定的石灰石,实现了一定效率的炉内干法脱硫,炉内脱硫效率一般在60%~90%之间。
但由于cfb锅炉的燃料特点,在一些燃烧高硫燃料或所在地so2排放标准要求严的cfb锅炉,必须在炉后进一步进行烟气脱硫。
本文通过对传统湿法脱硫工艺(钙法、镁法、氨法)存在的问题以及对循环流化床干法脱硫工艺优点的论述,得出了对于cfb锅炉采用循环流化床干法脱硫工艺更具有科学性结论。
关键词:cfb锅炉先除尘后脱硫先脱硫后除尘循环流化床干法综合利用腐蚀结垢旁路中图分类号:tq3 文献标识码:a 文章编号:1672-3791(2012)09(c)-0114-02cfb锅炉以其在劣质煤利用、煤种的适应性、电网负荷调节等方面,具有独特的优势,得到了广泛的关注。
我国现已全面掌握了300mw及以下机组cfb锅炉燃烧技术,600mwcfb锅炉技术也进入了示范应用阶段。
cfb锅炉通过喷入一定的石灰石,在炉内高温煅烧生成cao,与烟气中的so2进行反应,生成caso4,实现了一定效率的炉内干法脱硫,炉内脱硫效率一般在60%~90%(取决于ca/s和锅炉结构)之间。
但由于cfb锅炉的燃料特点,在一些燃烧高硫燃料或所在地so2排放标准要求严的cfb锅炉,必须在炉后进一步进行烟气脱硫。
cfb锅炉烟气脱硫提效的传统工艺路线,一般是烟气先经过布袋除尘器(或电除尘器)除尘后,再旁路进入湿法脱硫装置进行烟气的提效脱硫。
由于cfb锅炉烟气含尘浓度高,加上炉内脱硫后的烟尘比电阻高。
因此,传统的cfb锅炉烟气除尘净化一般采取配套布袋除尘器的方案。
笔者认为这种传统的先除尘后脱硫的工艺方案,应用于cfb锅炉烟气的二次脱硫,是一种不合理的工艺路线,特别是随着取消脱硫旁路的要求日益得到落实,这种先除尘后脱硫的工艺方案所暴露的问题将更加严重。
这种传统的先除尘后脱硫的工艺方案存在的问题简述如下。
循环流化床锅炉脱硫灰的利用
CFB循环流化床锅炉脱硫灰的利用循环流化床锅炉具有燃料适应性好的优势,它可以燃烧劣质煤,如煤矸石,和可以燃烧生活垃圾和多种工业废弃物,其次由于燃烧温度低(850度左右)其燃烧进程NO排放量也较低,是一种比较环保的燃烧方式。
同时可以在锅炉内添加石灰石进行炉内脱硫,实现燃烧与脱硫同时进行等诸多长处。
该燃烧技术目前在国内有较多应用,也是我国大力推行的一种清洁燃烧技术。
目前粉煤灰已被水泥建材行业普遍利用,而循环流化床锅炉炉内加钙脱硫后所排放的脱硫灰与普通锅炉排放的粉煤灰存在明显不同,因此无法取得普遍利用。
流化床脱硫灰(CFB脱硫灰)与流化床粉煤灰(CFB灰),粉煤炉粉煤灰(PC灰)化学成份对比表:由表中可见CFB脱硫灰其特性为三高两低,CaO(f-CaO游离氧化钙),SO3,C含量高,SiO2,Al2O3含量低。
CFB脱硫灰所含化学成份对水泥制品的影响:1.粉煤灰的活性来自于Fe2O3、SiO2、Al2O3在必然碱性条件下的水化作用,CFB脱硫灰上述三种化学成份含量较低,活性小于PC灰。
脱硫灰含钙高,CaO水化生成Ca(OH)2给水泥制品带来较大体积膨胀,严重影响体积安宁性,是建筑致命隐患,高含量的f-CaO 也是影响砼体安宁性因素之一。
脱硫灰含硫高,CO3会生成体积膨胀较大的钙矾石,是引发砼体体积膨胀,安宁性不良,最终致使制品强度降低的主要因素,这也是CFB脱硫灰利用率较低的主要原因。
同时硫对钢筋具有侵蚀作用。
脱硫灰含碳高,CFB锅炉炉温低,大量惰性碳未充分燃烧,未燃尽的碳粒疏松多孔,与其他物质结合能力差,对一些外加剂利用效果产生不利影响,在制作水泥、混凝土掺合料时有较大技术障碍。
脱硫灰堆积密度小,灰堆积密度反映其颗粒排列松紧度,密度大孔隙率低,反之孔隙率大,它是工程设计和施工的重要指标。
CFB脱硫灰密度低于常规灰的标准,在工程利用中受限制。
同时密度小在砼体浇筑中粉煤灰容易浮在上层混凝土中使砼体强度上下不一致。
COA脱硝技术的应用分析及优化建议
COA脱硝技术的应用分析及优化建议厦门国贸中顺环保能源股份有限公司原有3×75t/h循环流化床锅炉在原有炉外半干法脱硫除尘装置基础上,采用福建某上市环保公司自主研发的COA脱硝技术,实施脱硝改造,实现锅炉尾部烟气中NOx具备超低排放能力(即NOx≤35mg/m3),是火电行业首个使用COA 脱硝技术的工程案例,并与该技术研发单位进行不断合作摸索及工艺改进。
1COA脱硝技术工艺原理及特点1.1脱硝工艺原理COA脱硝主要是将锅炉尾部烟气中难溶于水、不易被碱性吸收剂反应吸收的NO,通过脱硝剂(NaClO2)作用,增强将其转化为易于反应吸收的NO2机率,再利用炉外(半)干法脱硫塔利用消石灰进行中和反应完成脱硝。
其脱硝主要化学反应为:NaClO2+2NO→2NO2+NaCl2NO2+NaClO2+Ca(OH)2→Ca(NO3)2+NaCl+H2ONaClO2作为脱硝剂,在前一个反应中主要起强氧化作用,而在后一个Ca(OH)2与NO2吸收反应中起催化作用。
相关生成物均为无毒害的Ca(NO3)2、NaCl和H2O,对原有脱硫系统无其他危害。
1.2脱硝工艺特点COA脱硝技术将脱硝方式从催化还原的传统模式转为氧化吸收方向,有别于常用的低氮燃烧、SNCR、SCR等,具有以下优点:(1)对脱硝温度、粉尘浓度等没有特别的限制要求,属炉外脱硝,受锅炉运行工况、温度场等影响小,特别适合难以实施SNCR、SCR脱硝工艺的中小型锅炉;(2)结合已有炉外脱硫吸收塔进行协同处置,只需增加脱硝添加剂给料装置,改造投资金额和运行维护费用少;(3)脱硝副产物为无毒害,无废水排放及二次污染;(4)系统简洁,一般由脱硝剂进料模块、溶液配置与存储模块、溶液输送及喷射模块组成,启停方便,设备占地小、运行可靠;(5)根据NOx浓度变化,可通过调解吸收剂和脱硝剂的耗量来实现良好适应性;(6)脱硝效率高,可实现60%以上。
2COA脱硝工艺当前存在的不足2.1须配合炉外吸收装置使用COA脱硝技术主要起氧化和催化吸收作用,仅靠COA脱硝工艺并不能完成对氮氧化物的脱除,须配合炉外吸收塔使用才能实现脱硝。
“循环流化床吸收塔(CFB-FGD)”工艺进行烟气脱硫技术
“循环流化床吸收塔( CFB-FGD)”工艺进行烟气脱硫技术摘要:干法烟气脱硫装置所采用的技术是在引进国外先进的干法脱硫工艺循环流化床干法烟气脱硫(CFB-FGD)技术的基础上经不断完善、改进,形成了适合我国国情的干法脱硫技术,它具有结构简单、运行可靠、脱硫效率高(大于90%)、投资小的特点。
循环流化床烟气干法脱硫技术是目前商业应用中单塔处理能力最大、脱硫综合效益最优越的唯一一种干法烟气脱硫技术。
关键词:干法烟气脱硫;循环流化床吸收塔(CFB-FGD);烟气脱硫技术脱硫反应塔内的气固最大滑落速度是否能在不同的烟气负荷下始终得以保持不变,是衡量一个循环流化床干法脱硫工艺先进与否的一个重要指标,也是一个鉴别干法脱硫能否达到较高脱硫率的一个重要指标。
喷入的用于降低烟气温度的水[1],以激烈湍动的、拥有巨大的表面积的颗粒作为载体,在塔内得到充分的蒸发,保证了进入后续除尘器中的灰具有良好的流动状态。
由于流化床中气固间良好的传热、传质效果[2],绝大部分SO2得以去除,加上排烟温度始终控制在高于露点温度20℃以上,因此排烟不需要再加热,同时系统无需采取特殊的防腐处理。
净化后的含尘烟气从吸收塔顶部侧向排出,然后转向进入脱硫除尘器[3],再通过引风机排入烟囱。
经除尘器捕集下来的固体颗粒,通过除尘器下的再循环系统,返回吸收塔继续参加反应,如此循环,多余的少量脱硫灰渣通过物料输送至脱硫灰仓内,再通过罐车运出厂外综合利用。
在循环流化床吸收塔中,Ca(OH)2与烟气中的SO2和几乎全部的SO3,HCl,HF等,完成化学反应,主要化学反应方程式如下:Ca(OH)2+ SO2=CaSO3·1/2 H2O +1/2 H2OCa(OH)2+ SO3=CaSO4·1/2 H2O +1/2 H2OCaSO3·1/2 H2O+ 1/2O2=CaSO4·1/2 H2OCa(OH)2+ CO2=CaCO3 + H2OCa(OH)2+ 2HCl=CaCl2·2H2O(~75℃)(强吸潮性物料)2Ca(OH)2+ 2HCl=CaCl2·Ca(OH)2·2H2O(>120℃)Ca(OH)2+ 2HF=CaF2 + 2H2O(从上述化学反应方程式可以看出,Ca(OH)2应尽量避免在75℃左右与HCl 反应)具有以下工艺及结构特点:1)去除重金属、有机污染物等有害物质利用吸附剂及塔内物料的巨大比表面积,使烟气中的重金属、有机污染物(主要是二噁英(PCDD)和呋喃(PCDF))等大部分被去除。
循环流化床干法脱硫+COA脱硝技术在CFB炉上的应用
循环流化床干法脱硫+COA 脱硝技术在CFB 炉上的应用董晨光(山东齐鲁石化工程有限公司,山东 淄博 255400)摘要 xxx 公司三台CFB 炉前期经过SNCR 改造,烟气中NOx 浓度≤100mg/Nm 3;脱硫采用炉内加钙方式,烟气中SO 2浓度≤200mg/Nm 3;本次改造采用循环流化床干法脱硫+COA 协同氧化脱硝技术,使烟气中NOx 浓度≤50mg/Nm 3,SO 2浓度≤35mg/Nm 3,从而满足天然气锅炉排放标准之要求。
关键词 CFB 锅炉;SNCR 脱硝;循环流化床干法脱硫;COA 协同氧化脱硝一 引言XXX 公司现有3台额定出力为240t/h 高温高压循环流化床燃煤锅炉,于2006年建成投产。
2014年,公司对该三台CFB 炉进行了SNCR 脱硝改造,使锅炉烟气中NOx 浓度值降低到100mg/Nm 3以下。
锅炉脱硫采用炉内加钙方式,脱硫效率90%左右,锅炉烟气中SO 2浓度低于200mg/Nm 3,基本满足了《火电厂大气污染排放标准》[1](一般地区)和《山东省区域性大气污染物综合排放标准》[2]第三时段规定的要求。
然而,随着环保标准的不断升级,该三台CFB 炉的烟气污染物排放浓度不能达到国家标准《火电厂大气污染排放标准》重点地区特别排放限值、《山东省区域性大气污染物综合排放标准》第四时段(2020年1月起)、“天然气锅炉排放标准”的要求。
因此,对该三台CFB 锅炉采用循环流化床干法脱硫+COA 协同氧化脱硝技术改造,使烟气中NOx 浓度≤50mg/Nm 3,SO 2浓度≤35mg/Nm 3,以满足新环保标准之要求。
二 循环流化床干法脱硫(一)工艺原理烟气循环流化床干法脱硫技术主要是根据循环流化床理论,使吸收剂在吸收塔内悬浮、反复循环,与烟气中的SO 2充分接触反应来实现脱硫。
系统以消石灰粉(Ca(OH)2)作脱硫吸收剂,以锅炉飞灰、消石灰等混合物作循环物料,在反应器内直接喷水增湿,使循环物料生成一定大小的带有一定量水分的颗粒,这样在反应器中由于颗粒的水分蒸发与水分吸附和固体颗粒之间强烈接触摩擦,使反应器中气、固、液三相之间具有极大的反应活性和反应表面积,可有效去除SO 2、HCl 、二恶英与其它有害物质。
- 1、下载文档前请自行甄别文档内容的完整性,平台不提供额外的编辑、内容补充、找答案等附加服务。
- 2、"仅部分预览"的文档,不可在线预览部分如存在完整性等问题,可反馈申请退款(可完整预览的文档不适用该条件!)。
- 3、如文档侵犯您的权益,请联系客服反馈,我们会尽快为您处理(人工客服工作时间:9:00-18:30)。
循环流化床干法脱硫+COA脱硝技术在CFB炉上的应用董晨光(山东齐鲁石化工程有限公司,山东淄博 255400)摘要xxx公司三台CFB炉前期经过SNCR改造,烟气中NOx浓度≤100mg/Nm3;脱硫采用炉内加钙方式,烟气中SO2浓度≤200mg/Nm3;本次改造采用循环流化床干法脱硫+COA协同氧化脱硝技术,使烟气中NOx浓度≤50mg/Nm3,SO2浓度≤35mg/Nm3,从而满足天然气锅炉排放标准之要求。
关键词 CFB锅炉;SNCR脱硝;循环流化床干法脱硫;COA协同氧化脱硝一引言XXX公司现有3台额定出力为240t/h高温高压循环流化床燃煤锅炉,于2006年建成投产。
2014年,公司对该三台CFB炉进行了SNCR脱硝改造,使锅炉烟气中NOx浓度值降低到100mg/Nm3浓度低于200mg/Nm3,以下。
锅炉脱硫采用炉内加钙方式,脱硫效率90%左右,锅炉烟气中SO2基本满足了《火电厂大气污染排放标准》[1](一般地区)和《山东省区域性大气污染物综合排放标准》[2]第三时段规定的要求。
然而,随着环保标准的不断升级,该三台CFB炉的烟气污染物排放浓度不能达到国家标准《火电厂大气污染排放标准》重点地区特别排放限值、《山东省区域性大气污染物综合排放标准》第四时段(2020年1月起)、“天然气锅炉排放标准”的要求。
因此,对该三台CFB锅炉浓度采用循环流化床干法脱硫+COA协同氧化脱硝技术改造,使烟气中NOx浓度≤50mg/Nm3,SO2≤35mg/Nm3,以满足新环保标准之要求。
二循环流化床干法脱硫(一)工艺原理烟气循环流化床干法脱硫技术主要是根据循环流化床理论,使吸收剂在吸收塔内悬浮、反复循环,与烟气中的SO2充分接触反应来实现脱硫。
系统以消石灰粉(Ca(OH)2)作脱硫吸收剂,以锅炉飞灰、消石灰等混合物作循环物料,在反应器内直接喷水增湿,使循环物料生成一定大小的带有一定量水分的颗粒,这样在反应器中由于颗粒的水分蒸发与水分吸附和固体颗粒之间强烈接触摩擦,使反应器中气、固、液三相之间具有极大的反应活性和反应表面积,可有效去除SO2、HCl、二恶英与其它有害物质。
固体物料经袋式除尘器收集,再由空气斜槽回送至反应器,使未反应的吸收剂反复循环,故使得吸收剂在反应器内的停留时间延长,从而提高了吸收剂的利用率,降低了运行成本。
其主要反应化学方程式如下:SO 2+H 2O→H 2SO 3Ca(OH)2+H 2SO 3→CaSO 3+2H 2OCaSO 3+1/2O 2→CaSO 4(二)工艺系统循环流化床干法脱硫系统由预电除尘器系统、干法脱硫塔、塔后除尘器、灰循环系统、吸收剂储存及输送系统、脱硫灰库及输灰、工艺水、压缩空气系统等组成,采用1炉1塔脱硫方案。
主要的工艺系统组成如图1所示:图1循环流化床干法烟气脱硫工艺示意图1.预电除尘器系统预电除尘器由两大部分组成,一部分是产生高压直流电的高压电源装置和维持电除尘器正常运行必不可少的低压控制系统;另一部分是电除尘器本体,它是对烟气进行净化的装置。
2.干法脱硫塔烟气通过脱硫塔底部的文丘里管加速,进入干法脱硫塔体,物料在塔体里气流的作用下产生激烈的湍动与混合,与气流充分接触,在上升的过程中,不断形成絮状物向下返回,而絮状物在激烈湍动中又不断解体重新被气流提升,使得气固间的滑落速度高达单颗粒滑落速度的数十倍;脱硫塔顶部结构进一步强化了絮状物的返回,进一步提高了塔内颗粒的床层密度,使得床层内的Ca/S 比高达50以上。
这样循环流化床内气固两相流机制,极大地强化了气固间的传质与传热,为实现高脱硫率提供了根本的保证。
图2 吸收塔示意图3.塔后除尘器烟气由进口烟道进入过滤室,粉尘被阻留在滤袋表面,净化后的气体经滤袋口(花板孔上)进入净气室,由出风道经引风机排至烟囱。
除尘器周期性地对滤袋清灰,清灰喷吹时,粉尘振落掉入灰斗,除尘器底部灰斗中的灰经空气斜槽分两路排出。
考虑到烟气的组分特殊,酸露点较高,故在除尘器灰斗外设有蒸汽加热和保温,在停炉、开车和环境温度较低情况下启动,保证布袋除尘器本体内壁不至于出现酸结露和板结现象。
烟气经布袋除尘器除尘后,由引风机引至烟囱排放。
4.灰循环系统为提高吸收剂Ca(OH)2的利用率及脱硫效率,保证系统正常运行,设有灰循环系统。
根据反应器中烟尘的浓度和脱硫效率来调节循环倍率。
布袋除尘器灰斗中的灰经灰斗底部空气斜槽流化后分两部分输送:一部分为循环灰,经流量控制阀调节循环灰量由空气斜槽输送至反应器内,与烟气充分混合继续参加反应,循环利用;另一部分为外排灰,经手动插板阀输送至中间灰仓,通过仓泵输送至灰库。
循环灰空气斜槽的送风由流化风机供给,并通过蒸汽加热器加热,达到运行所需温度。
5.吸收剂储存及输送系统吸收剂存储及输送系统包括生石灰仓、消化器、消石灰仓、称重设备、给料设备、喷射器、罗茨风机等。
6.脱硫灰库及输灰系统工艺产生的干态脱硫灰采用正压密相仓泵输送至脱硫灰库。
三台炉共用一套脱硫灰库系统。
三 COA协同氧化脱硝(一)工艺原理COA脱硝技术是以特有的循环流化床反应器内激烈湍动的、拥有巨大的表面积的吸附剂颗粒作为载体,通过额外添加强氧化剂亚氯酸钠,增强烟气中难溶于水的NO转化为NO2机率,并最终与钙基吸收剂反应脱除。
其主要反应化学方程式如下:NaClO2 + NO → NO2+ NaClNO2 + NaClO2+ Ca(OH)2→ Ca(NO3)2+ NaCl + H2O图3 COA协同氧化吸收工艺流程本COA脱硝系统采用脱硝溶液喷射的液相脱硝方式,通过分段协同使用,形成双级氧化机制,提高了系统的脱硝效率和稳定性,降低脱硝的运行成本。
其中第一级脱硝溶液喷射装置设置于吸收塔入口烟道,在烟气进入吸收塔前完成部分预氧化功能,第二级脱硝溶液喷射装置设置于吸收塔锥形段,进一步提高氧化效率,并在吸收塔内完成最终的吸收反应。
脱硝系统可根据入口氮氧化物浓度情况单独开启一级脱硝溶液喷射装置,也可同时开启两级脱硝喷射装置,进一步提高脱硝效率。
(二)工艺系统COA脱硝工艺系统主要由脱硝剂进料模块、脱硝溶液制备与存储模块、脱硝溶液输送及喷射模块等组成。
主体设备集中布置于干法烟气脱硫系统旁空地的脱硝间内,在脱硝间内完成脱硝剂的进料及脱硝溶液配制。
每台炉设置一套COA脱硝系统。
1.脱硝剂进料模块脱硝剂输送至脱硝溶液搅拌罐设置的脱硝剂进料缓冲罐。
脱硝剂输送采用真空进料方式,真空进料装置通过系统内形成的真空吸力来传送颗粒和粉末状物料的无尘密闭管道输送设备,通过利用管路与环境空间形成的气压差,使管道内气体流动,带动粉状物料在管道内完成密闭输送。
脱硝剂进料模块采用就地PLC控制模式,实现脱硝剂的进料输送。
2.脱硝溶液制备与存储模块设置1台脱硝溶液搅拌罐。
脱硝溶液给料泵设置2台,1用1备。
通过脱硝剂进料模块输送来的脱硝剂于脱硝溶液搅拌罐内配制成一定浓度的脱硝溶液,配制完成后通过脱硝溶液给料泵输送至脱硝溶液存储罐内待用。
3.脱硝溶液输送及喷射模块设置1台脱硝溶液存储罐。
脱硝溶液输送泵设置2台,1用1备。
脱硝专用的双流体式水喷枪独特设计,确保脱硝溶液最佳雾化及覆盖效果。
脱硝溶液喷入量主要是根据装置出口NOx排放要求进行控制,脱硝溶液输送泵为变频泵,可通过排放浓度要求相应调整输送泵频率。
四脱硫脱硝效果XXX公司3台额定出力为240t/h高温高压循环流化床燃煤锅炉超洁净排放改造工程正在进行,其中1号炉已实现整套系统试投运,经测试:循环流化床干法脱硫+COA协同氧化脱硝技术值由200 mg/Nm3下降到20 mg/Nm3,改造投运后,1号炉NOx值由80 mg/Nm3下降到36 mg/Nm3,SO2见图4;a)改造前后NOx浓度值b)改造前后SO2浓度值图4 循环流化床干法脱硫+COA脱硝改造前后NOx、SO2浓度变化五结论循环流化床干法烟气脱硫技术[3-4]是近几年国际上新兴起的比较先进的烟气脱硫技术,兼有干法与湿法的一些特点,其既具有湿法脱硫反应速度快、脱硫效率高的优点,又具有干法无污水排放、脱硫后产物易于处理的好处,设备可靠性高,运行费用较低。
COA脱硝技术[5-6]适用于烟气循环流化床干法脱硫工艺,只需要在脱硫装置上预留接口,即可在脱硫装置运行的同时进行脱硝。
同时由于该三台CFB锅炉前期已实施SNCR脱硝技术改造,COA脱硝技术完全能够达到预期的脱硝效果,并且设备简单,改造工程量小。
因此,对于前期已实施过SNCR脱硝改造的CFB 锅炉,采用循环流化床干法脱硫+COA协同氧化脱硝技术,可节省投资及运行费用,有效降低锅的排放质量浓度。
炉烟气中NOx、SO2本文通过工程实践证明,采用循环流化床干法脱硫+COA协同氧化脱硝技术,将XXX公司额定出力为240t/h高温高压循环流化床燃煤锅炉烟气NOx排放质量浓度从80 mg/Nm3降低至36 排放质量浓度由200 mg/Nm3下降到20 mg/Nm3左右,从而达到“天然气锅炉排mg/Nm3左右,SO2放标准”的要求。
参考文献[1] 《火电厂大气污染排放标准》,GB13223-2011.[2] 《山东省区域性大气污染物综合排放标准》,DB37/2376-2013.[3] 林驰前,林春源.烟气循环流化床干法脱硫系统的设计与调试[J].中国环保产业,2007,(6).[4] 张祥,王强.火电厂湿法脱硫与烟气循环流化床干法脱硫工艺比较[J].科技视界,2012,(26).[5] 黄光明.SNCR+COA脱硝技术在循环流化床锅炉应用[J].广东化工,2015,42(7).[6] 马德华.CFB锅炉超洁净排放升级改造及运行优化[J].石油石化节能与减排,2015,5(2).。