弯管标准化
弯管标准体系

弯管标准体系
弯管(也称弯头)是一种管道连接元件,用于改变管道的流向。
弯管的标准体系通常包括以下几个方面:
1. 尺寸标准:包括弯管的直径、弯曲半径、弯头角度等尺寸参数的标准规定,通常以英寸或毫米为单位。
2. 材质标准:规定了弯管可以采用的材质,例如碳钢、不锈钢、合金钢等,以及材质的化学成分、力学性能等要求。
3. 制造标准:包括弯管的制造工艺、加工要求、外观质量等方面的标准规定,确保弯管的制造质量符合要求。
4. 检验标准:规定了对弯管进行检验的方法、标准、验收标准等,以确保弯管的质量符合要求。
5. 标志标准:规定了弯管应当标注的信息,例如材质、尺寸、标准编号等,以便用户正确选择和使用。
6. 包装标准:规定了弯管的包装方式、包装标识、运输要求等,以确保产品在运输和储存过程中不受损坏。
这些标准体系可以根据不同国家或地区的标准制定,例如国际标准组织(ISO)、美国标准协会(ANSI)、欧洲标准化委员会(CEN)等都可能制定相应的弯管标准。
弯管公差标准

弯管公差标准
弯管公差标准是指在弯管加工过程中,允许管材尺寸和形状偏离设计要求的一定范围。
这些公差标准旨在确保弯管在满足使用要求的前提下,具有较高的尺寸稳定性和质量。
弯管公差标准主要包括以下几个方面。
1.弯曲半径公差:弯管的弯曲半径应符合设计要求。
在一般情况下,弯曲半径的公差应控制在±10%以内。
2.弯曲角度公差:弯管的弯曲角度允许偏差一般不大于±2°。
3.管径公差:管径的公差应符合国家标准GB/T15918-1994《钢制无缝钢管》的要求。
在一般情况下,管径的公差等级分为±0.5mm、±1mm、±1.5mm等。
4.壁厚公差:弯管的壁厚公差应符合国家标准GB/T13295-2013《焊接钢管》的要求。
壁厚公差等级分为±0.5mm、±1mm、±1.5mm等。
5.弯管长度公差:弯管的长度公差应根据客户要求和相关标准来确定。
一般情况下,长度公差为±10mm。
6.表面质量公差:弯管表面应光滑,无毛刺、裂纹、折叠等缺陷。
表面质量公差应符合相关标准的要求。
需要注意的是,以上公差标准仅作为一般参考。
实际生产中,弯管的公差要求会根据具体应用场景、客户要求以及
相关标准进行调整。
在实际操作中,应根据具体情况合理控制弯管的公差范围,以确保产品质量。
弯管角度公差标准

弯管角度公差标准一、角度测量方法1. 采用全角度测量设备,如光学分度仪、圆度测量仪等,对弯管的角度进行测量。
2. 测量时,将弯管放置在测量设备的工作台上,调整弯管位置使其一端固定,然后通过旋转测量设备的工作台对弯管进行测量。
3. 测量过程中,应保证测量设备的精度和稳定性,以获得准确的数据。
二、公差值确定1. 根据弯管的材料、壁厚、弯曲半径等因素,参照相关标准或设计要求,确定弯管的角度公差值。
2. 公差值的确定应考虑到制造工艺、设备精度、材料变形等因素对弯管角度的影响。
三、公差范围1. 弯管的角度公差范围应根据相关标准或设计要求进行规定。
2. 在规定的公差范围内,弯管的角度偏差应符合要求,以保证其使用性能和外观质量。
四、角度测量设备1. 用于弯管角度测量的设备应具有高精度和高稳定性,以保证测量结果的准确性。
2. 设备的精度应定期进行校准和维护,以保证其测量精度和可靠性。
五、测量环境条件1. 弯管角度测量应在恒温、恒湿的环境中进行,以减少温度和湿度对测量结果的影响。
2. 环境温度和湿度的变化可能会对弯管的材料性能和测量结果产生影响,因此应尽量减少这些因素的影响。
六、角度偏差处理1. 对于不符合角度公差标准的弯管,应进行修正或调整,以使其达到规定的要求。
2. 可以采用加热、冷却、矫直等方法对弯管的角度进行修正,以满足使用要求。
七、检验报告内容1. 检验报告应包括以下内容:弯管的材料、型号、规格、批次号等信息;角度测量的具体数据及是否符合公差标准的结果;修正或调整的具体方案和实施情况等。
2. 检验报告应及时出具,并归档保存,以备后续检查和使用。
八、不合格品处理1. 对于不符合要求的弯管,应及时进行标识和隔离,以防止误用或混淆。
2. 不合格品可以进行返工或报废处理,具体应根据实际情况制定相应的处理方案。
3. 处理不合格品后,应重新进行检验,以确保产品质量符合要求。
九、测量人员资质1. 进行弯管角度测量的工作人员应经过专业培训和考核,具备相应的测量技能和经验。
焊接钢管弯头标准执行标准
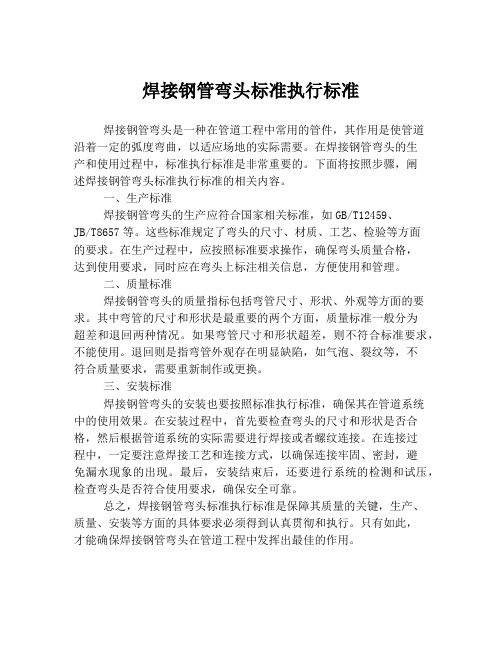
焊接钢管弯头标准执行标准焊接钢管弯头是一种在管道工程中常用的管件,其作用是使管道沿着一定的弧度弯曲,以适应场地的实际需要。
在焊接钢管弯头的生产和使用过程中,标准执行标准是非常重要的。
下面将按照步骤,阐述焊接钢管弯头标准执行标准的相关内容。
一、生产标准焊接钢管弯头的生产应符合国家相关标准,如GB/T12459、JB/T8657等。
这些标准规定了弯头的尺寸、材质、工艺、检验等方面的要求。
在生产过程中,应按照标准要求操作,确保弯头质量合格,达到使用要求,同时应在弯头上标注相关信息,方便使用和管理。
二、质量标准焊接钢管弯头的质量指标包括弯管尺寸、形状、外观等方面的要求。
其中弯管的尺寸和形状是最重要的两个方面,质量标准一般分为超差和退回两种情况。
如果弯管尺寸和形状超差,则不符合标准要求,不能使用。
退回则是指弯管外观存在明显缺陷,如气泡、裂纹等,不符合质量要求,需要重新制作或更换。
三、安装标准焊接钢管弯头的安装也要按照标准执行标准,确保其在管道系统中的使用效果。
在安装过程中,首先要检查弯头的尺寸和形状是否合格,然后根据管道系统的实际需要进行焊接或者螺纹连接。
在连接过程中,一定要注意焊接工艺和连接方式,以确保连接牢固、密封,避免漏水现象的出现。
最后,安装结束后,还要进行系统的检测和试压,检查弯头是否符合使用要求,确保安全可靠。
总之,焊接钢管弯头标准执行标准是保障其质量的关键,生产、质量、安装等方面的具体要求必须得到认真贯彻和执行。
只有如此,才能确保焊接钢管弯头在管道工程中发挥出最佳的作用。
弯管的执行标准

弯管的执行标准弯管是管道安装中常用的一个部件,其执行标准涵盖了多个方面,以确保其质量、性能和安全。
下面将详细介绍弯管的执行标准。
1.材料标准弯管应采用符合国家或行业标准的优质材料,如不锈钢、合金钢、碳钢等。
材料应具有质量保证书和合格证明文件。
2.尺寸标准弯管的尺寸应符合设计图纸和相关标准的要求,包括弯管的直径、壁厚、长度等。
弯管的形状和尺寸精度应符合产品标准。
3.制造标准弯管的制造应符合国家或行业标准,如GB/T 12459-2005《钢制对焊无缝管件》、GB/T 13401-2005《钢板制对焊管件》等。
制造过程中应进行质量控制,确保弯管的制造精度和表面质量符合要求。
4.试验方法标准弯管制造完成后应按照相关标准进行试验,以检验其性能和质量。
试验方法包括但不限于压力试验、真空试验、泄漏试验、耐压试验等。
试验过程中应严格遵守相关标准和规定。
5.验收标准弯管出厂前应按照相关标准进行验收,验收项目包括但不限于尺寸、表面质量、材质、压力试验等。
验收合格后方可出厂,并附有合格证明文件。
6.安装标准弯管的安装应按照设计图纸和相关标准进行,确保安装位置准确、牢固,避免出现晃动或位移。
安装过程中应注意保护弯管,避免损伤或变形。
7.维护标准弯管使用过程中应定期进行检查和维护,确保其正常运转和安全可靠。
如发现异常应及时进行处理,防止问题扩大。
8.安全标准弯管的设计、制造、安装和维护应符合国家或行业安全标准,确保在使用过程中不会发生安全事故。
9. 性能标准:弯管的性能应符合设计要求,包括流体流量、压力损失、弯曲半径等参数。
性能测试应按照相关标准进行,以确保弯管在实际使用中能够满足要求。
10. 耐压标准:弯管的耐压性能应符合相关标准,包括静水压试验、液压试验等。
试验过程中应记录压力值、变形量等数据,以确保弯管在使用过程中能够承受预期的压力负荷。
11. 耐腐蚀标准:对于特殊介质(如酸、碱、海水等)使用的弯管,应具有耐腐蚀性能。
弯管技术规范
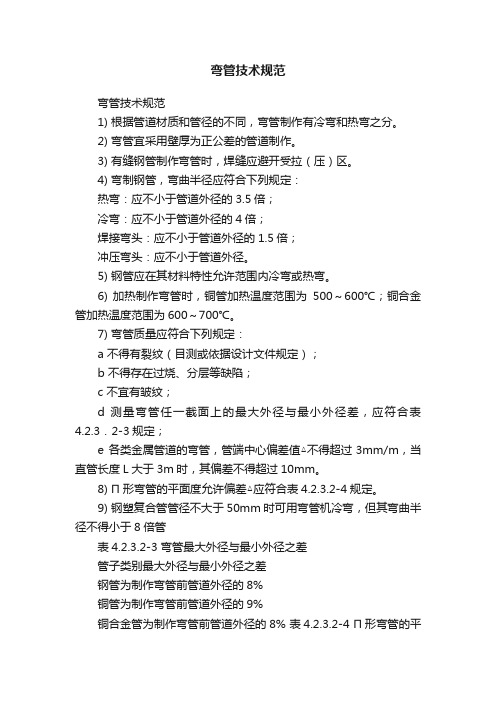
弯管技术规范弯管技术规范1) 根据管道材质和管径的不同,弯管制作有冷弯和热弯之分。
2) 弯管宜采用壁厚为正公差的管道制作。
3) 有缝钢管制作弯管时,焊缝应避开受拉(压)区。
4) 弯制钢管,弯曲半径应符合下列规定:热弯:应不小于管道外径的3.5倍;冷弯:应不小于管道外径的4倍;焊接弯头:应不小于管道外径的1.5倍;冲压弯头:应不小于管道外径。
5) 钢管应在其材料特性允许范围内冷弯或热弯。
6) 加热制作弯管时,铜管加热温度范围为500~600℃;铜合金管加热温度范围为600~700℃。
7) 弯管质量应符合下列规定:a 不得有裂纹(目测或依据设计文件规定);b 不得存在过烧、分层等缺陷;c 不宜有皱纹;d 测量弯管任一截面上的最大外径与最小外径差,应符合表4.2.3.2-3规定;e 各类金属管道的弯管,管端中心偏差值△不得超过3mm/m,当直管长度L大于3m时,其偏差不得超过10mm。
8) П形弯管的平面度允许偏差△应符合表4.2.3.2-4规定。
9) 钢塑复合管管径不大于50mm时可用弯管机冷弯,但其弯曲半径不得小于8倍管表4.2.3.2-3 弯管最大外径与最小外径之差管子类别最大外径与最小外径之差钢管为制作弯管前管道外径的8%铜管为制作弯管前管道外径的9%铜合金管为制作弯管前管道外径的8% 表4.2.3.2-4 П形弯管的平面度允许偏差△(mm)长度L <500 500—1000 >1000—1500 >1500 平面度△≤3 ≤4≤6 ≤10径,弯曲角度不得大于10°。
10) 管道转弯处宜采用管件连接。
D N≤32的管材,当采用直管材折曲转弯时,其弯曲半径不应小于12 DN,且在弯曲时应套有相应口径的弹簧管。
管道弯曲部位不得有凹陷和起皱现象。
11) 铝塑复合管直接弯曲时,公称外径De不大于25mm的管道可采用在管内放置专用弹簧弯曲;公称外径De为32mm的管道宜采用专用弯管器弯管。
12) 铜管弯管:铜及铜合金管煨弯时尽量不用热煨,因热煨后管内填充物(如河砂、松香等)不宜清除。
弯管公差标准
弯管公差标准弯管是一种常用于工业管道系统中的管件,其作用是改变管道方向以适应不同的布局需求。
在制造和安装弯管时,精确的公差标准起着至关重要的作用,以确保管道系统的稳定性和流畅性。
本文将介绍弯管公差标准以及其在工程领域中的重要性。
1. 弯管公差标准的定义弯管公差标准是指在制造和安装弯管过程中所允许的尺寸偏差范围。
这些公差标准旨在确保弯管的尺寸准确性和质量可控性,从而确保管道系统的正常运行。
弯管公差标准通常涉及以下方面:1.1 直线段公差在弯管的制造过程中,弯曲之前的直线段也需要符合一定的公差要求。
这是因为直线段的不合格可能会对整体的弯管造成影响,因此需要在制造过程中进行相应的监测和控制。
1.2 弯曲角度公差弯管的角度是指管道在弯曲处的偏转角度。
弯曲角度公差是指弯管允许的偏离预定角度的范围。
例如,如果一个弯管的预定弯曲角度为90度,那么在制造过程中,该弯管可能允许的公差范围为85-95度。
1.3 外径公差外径公差是指弯管外径与预定规格外径之间允许的偏差范围。
这是因为弯管与其他管件相连接时,其外径的准确度直接影响到连接的稳定性和密封性。
1.4 壁厚公差壁厚公差是指弯管壁厚与预定规格壁厚之间允许的偏差范围。
弯管壁厚的准确度对管道系统的强度和耐用性有着重要的影响。
2. 弯管公差标准的重要性弯管公差标准在工程领域中有着重要的意义。
以下是弯管公差标准的几个重要作用:2.1 制造工艺控制弯管公差标准为制造过程提供了具体的尺寸要求和公差范围。
制造商可以根据这些标准来选择合适的工艺和设备,以确保弯管的准确性和质量稳定性。
2.2 安装配合性弯管的公差要求直接影响到其与其他管件的连接配合性。
如果公差过大,可能会导致连接松动或者密封不严,从而影响整个管道系统的正常运行。
2.3 流体通量控制弯管的公差范围会对管道内流体的通量产生影响。
若公差过大,可能会造成管道内流体的漏失或者阻力增大,降低了管道系统的工作效率。
2.4 结构稳定性弯管公差标准对于管道系统的结构稳定性至关重要。
弯管模具标准化手册详解
1---1 模具结构图
第1页,6页主视图
模具结构图
一套完整的弯管模具结构包括轮模、夹模、导模、芯棒
防皱板组成。
动作原理:芯棒进芯,夹模夹紧管材随轮模一起转动,导模压紧管材随着管材的弯曲而跟随,而防皱板固定不动,当弯管角度达到设定角度后,芯棒退出,夹模导模松开,复位完成整个动作。
1---1 轮模图
第2页平面图
1---1 夹模图
第3页平面图
1---1 导模图
第4页平面图
1---1 防皱板图
第5页平面图
防皱板标准化
防皱板主要用在薄壁(T≦1MM),管径(¢≧10MM)的管材上,主要防止管子弯曲处起皱。
防皱板一方面起着对管子支撑作用,另一方面围绕轮模相对滑动。
因此,防皱板需根据轮模半径设计
防皱板尺寸按图纸设计统一:其它尺寸按图纸零件设计
1---1 芯棒图
第6页平面图
芯棒标准化
1、芯棒尺寸按图纸设计统一:除以下尺寸外
A:根据原材料内径设计,一般比内径偏小0.5~0.8 B:根据原材料内径设计,一般比内径偏小0.2~0.5。
钢管弯制技术要求
钢管弯制技术要求
钢管的弯制分:冷煨弯、热煨弯。
弯管截面最大与最小外径差控制(弯前外径的5%~10%)。
弯前与弯后管壁厚度之差控制(特殊管道≤弯前管壁厚的10% 或一般≤15% )。
管端中心偏差Δ控制(特殊管道≤1.5mm/m,当L超过3 m时,Δ≤5 mm;一般≤3mm/m,当L超过3 m时,Δ≤10 mm。
弯管采用正公差,当采用负公差时,弯前管子壁厚应为设计壁厚1.06~1.25倍,弯曲半径越小倍数越大。
高压钢管弯曲半径宜>管外径5倍,其它宜>3.5倍。
钢管弯后的热处理温度为600~650℃,且加热速率、恒温时间和冷却速率应按规范控制。
GB151-1999
U形弯管段的圆度偏差,应不大于换热管名义外径的10%,但弯曲半径小于2.5倍换热管名义外径的U形弯管段可以按15%验收。
U形管不宜热弯
当有耐应力腐蚀要求时,冷弯U形管的弯管段至少包括150mm的直管段应进行热处理。
碳钢、低合金钢钢管进行消除应力热处理。
钢管的弯曲减薄量为:
应该指出换热管是否允许拼接。
GB150.2-2010
GB/T8163中10、20、Q345D钢管的使用规定如下:
不得用于换热管
设计压力不大于4Mpa
使用温度下限分别为-10、0、-20摄氏度
钢管壁厚不大于10mm。
弯管模具标准化手册
弯管模具标准化手册弯管模具标准化手册1、弯管模具的定义和作用1.1 弯管模具的定义弯管模具是一种用于制造弯管的专用工具,用于将弹性材料弯曲成所需的形状,常用于管道工程、汽车制造、航空航天等领域。
1.2 弯管模具的作用弯管模具通过施加力和压力来改变弹性材料的形状,实现对管道弯曲过程的控制,从而满足各种工程项目对管道形状的要求。
2、弯管模具的分类和结构2.1 弯管模具的分类根据弯管的材料和工艺要求,弯管模具可以分为金属弯管模具、铝合金弯管模具、塑料弯管模具等。
2.2 弯管模具的结构弯管模具主要由模具座、模具块、定位销、模具夹紧机构等部分组成。
其中,模具座是安装模具块的基础,定位销用于确保模具块的位置准确,模具夹紧机构用于紧固模具块使其不发生移动。
3、弯管模具的设计和制造3.1 弯管模具设计的准备工作弯管模具设计前需要确定管道的材料、尺寸和形状要求,以及模具材料的选择等准备工作。
3.2 弯管模具设计的步骤弯管模具设计的步骤包括模具结构设计、模具材料选择、模具尺寸计算、模具加工工艺确定等。
3.3 弯管模具的制造弯管模具的制造包括材料采购、加工制造、热处理、表面处理等工艺环节,确保模具的质量和可靠性。
4、弯管模具的使用和维护4.1 弯管模具的使用注意事项在使用弯管模具时,需要注意操作规程、安全操作、避免过载等注意事项,以保证模具的正常使用和使用寿命。
4.2 弯管模具的维护为保持弯管模具的良好状态,需要定期清洁模具、润滑模具、定期检查模具的损坏和磨损情况,并及时进行维修和更换。
附件:相关图纸和模具技术参数表。
法律名词及注释:1、弯管模具:根据《模具制造工艺规范》中的定义,指用于将弹性材料弯曲成所需形状的专用工具。
2、模具座:指弯管模具上的承载结构,用于安装模具块,确保模具的稳定性和准确性。
3、定位销:指用于确定弯管模具位置的紧固件,以确保模具块的位置准确。
4、模具夹紧机构:指用于固定弯管模具的紧固装置,以确保模具块不发生移动。
- 1、下载文档前请自行甄别文档内容的完整性,平台不提供额外的编辑、内容补充、找答案等附加服务。
- 2、"仅部分预览"的文档,不可在线预览部分如存在完整性等问题,可反馈申请退款(可完整预览的文档不适用该条件!)。
- 3、如文档侵犯您的权益,请联系客服反馈,我们会尽快为您处理(人工客服工作时间:9:00-18:30)。
弯管标准化
一:模具设计选型简介
1.一管一模
对于一根管子来说,无论有几个弯,不管弯曲角度如何(不应大于180°),其弯曲半径最好统一。
既然一管一模,那么,对于不同直径规格的管子,应该选取多大的弯曲半径才适宜呢?最小弯曲半径取决于材料特性、弯曲角度、弯曲后的管壁外侧的变薄允许量和内侧起皱的大小、以及弯曲处的椭圆度的大小。
一般说来,最小弯曲半径不应小于管子外径的2—2.5倍,最短直线段不应小于管子外径的1.5—2倍,特殊情况除外。
2.一管二模(复合模或多层模)
对于不能实现一管一模的情况,譬如客户的装配界面空间狭小,管路走向布局有限,导致一管多半径或直线段较短的情况出现,这时,在设计弯管模时,考虑双层模或多层模(目前我司的弯管设备最多支持3层模的设计),甚至是多层复合模。
双层或多层模:一管出现双半径或者三半径的情况,如下实例:
双层或多层复合模:直线段短,不利于夹持的情况,如下实例:
3.多管一模
我司所用的多管一模,就是同一直径规格的管子应尽量采用同一种弯曲半径。
也就是使用同一套模具弯制不同形状的管件。
这样,才能有利于最大限度地压缩专用工艺设备,减少弯模的制造量,从而降低生产成本。
在一般情况下,同一直径规格的管子只采用一种弯曲半径不一定能够满足
实际位置的装配需要。
因此,相同直径规格的管子可以选取2—4种弯曲半径,以适应实际的需要。
如果弯曲半径取2D(这里D为管子外径),那么2D、2.5D、3D、4D即可。
当然,这种弯曲半径的比例不是固定不变的,应按发动机空间布局的实际情况选定,但是半径不宜选取过大。
而弯曲半径的规格也不宜过多,否则会失去多管一模所带来的利益。
一根管子上采用同一个弯曲半径(即一管一模)和同规格管子的弯曲半径标准化(多管一模),这是当前国外弯管设计造型的特点和总的趋势,是机械化和自动化代替手工劳动的必然结果,也是设计适应先进的加工工艺和先进的加工工艺促进设计的两者的结合。
二:弯管椭圆度计算
弯管机在进行工作运行时,在内压应力作用下,(内压应力状态参考配管力学)将使圆形的横截面趋于椭圆,产生短轴及长轴。
在长轴处产生附加应力,此应力属于局部应力。
椭圆度愈大,此附加应力也愈大,甚至形成高应力区,出现局部塑性变形,达到一定值后,将导致弯管承载能力减低而破坏。
所以,目前在技术规范中对弯管的椭圆度都有严格的规定。
规定如下:
本规范适用于弯管工段,用于指导弯管工艺检验弯管质量
1.弯管调整弯管模时,对有造型尺寸的弯管端必须予以保护,不允许
破坏造型尺寸。
首件检验时必须检测造型尺寸完好。
2.弯管时适度控制速率,以防止硬管破裂、起皱及严重变形。
(目视
检测)
3.弯曲变形量测量。
3.1 在弯曲后,挑选变形最大的位置,用游标卡尺测量短轴尺寸,以下
为计算公式:
变形量=(管径-短轴m )/管径×100%
3.2 对于壁厚≥1.0的硬管,变形量≤10%
对于壁厚<1.0的硬管,变形量≤15%
4. 弯后的硬管应能轻松放入弯管检具,不得使用硬力压入弯管检具定
位槽。
三:弯管模设计简介
1. 模具结构形式
弯管机标准模具包括:弯管模、夹紧块、导板(或滚轮)。
多节活芯、防皱块为选件
D (管件外径),t (管件壁厚),R (弯曲半径)
管件外径D 仅反映管件大小,管件弯曲加工的易难程度取决于管件的壁厚和弯曲半径,管件壁厚越小,半径越小加工难度越大。
一般我们用相对壁弯曲模
防皱块
厚,相对弯曲半径作为弯管的工艺参数相对壁厚tx=t/D,相对弯曲半径Rx=R/D 弯管机对于Rx>3D,tx>0.04的管件使用标准模具即可,对于Rx<3D,tx<0.04D 的管件,弯管机可加上防皱块, 多节芯棒等工艺措施来保证管件弯曲质量
弯管机主要采用缠绕弯管工艺,即夹紧管件直线段,通过弯曲模的旋转使管件塑性变形的加工工艺,缠绕弯管工艺可以比较容易在弯管模具加上各种措施以得到较好的管件质量。
另外一种弯管工艺为滚弯,原理是弯曲模保持静止状态,通过弯曲轮沿弯曲模的中心做圆周运动使管件塑性变形,这种弯管工艺对于管件规格的选择有局限性,适用于小口径管件,且材料的要求比较高,一般不采用。
还有一种动力弯管工艺,即俗称的“顶弯工艺”,由于它是属于专机,材料规格限定,管材长度也是限定的,同时,弯曲角度、弯曲半径、旋转角度等一些参数都是固定的,所以,相对于其它弯管工艺,它比较稳定,效率也非常高,这类的弯管工艺比较适合小口径管件大批量的制造。
但是,一旦产品的结构有调整,会导致顶弯设备报废。
所以在选取弯管工艺时,对产品的开发成熟度要求很高。
模具型腔内径选取列表:
2.弯管工艺
管径从DN6~DN32,壁厚1~1.5mm,其弯曲半径一般为1.5~2D。
弯管最难处理的就是内圆弧,弯曲半径小了容易起皱,这时就需要加入防皱块的使用了,防皱块的材料很讲究,太硬了,会磨伤工件,太软了,不起作用。
我们一般选用的是一种铜合金。
在纯弯曲的情况下,外径为D、壁厚为S的管子受外力矩M的作用发生弯曲时,中性层外侧的管壁受拉应力σ1的作用而减薄,内侧管壁受压应力σ2的作用而增厚(见图a)。
同时,合力F1和F2又使管子弯曲处的横截面发生变形而成为近似椭圆形(见1b),内侧管壁在σ2的作用下还可能出现失稳而起皱(见图c),为弯制出理想的管件,就应采取相应的措施来防止上述这些缺陷的产生,其中有芯弯管就是最常用的有效方法之一。
图1管子弯曲时的受力及变形情况
(a)管子弯曲时的受力情况(b)管子弯曲时的截面变形(c)管子弯曲时的
内侧失稳起皱所谓有芯棒弯管,就是当被弯制的管子相对弯曲半径R
/D或相对壁厚S/D较小时,为了获得高质量的管件,在管子被弯
制过程中,在其内部插入一根合适的芯棒,以防止管子弯曲时圆弧
处出现变扁及起皱现象的方法(见图2)。
1.弯曲模
2.芯棒头
3.防皱块
4.管子
5.芯棒杆
6.夹紧块
7.助推模
四、弯管方式的选择
一般来说,冷态弯管有两种方式:一种为无芯弯管,一种为有芯弯管。
对于
在什么情况下采用无芯弯管,什么情况下采用有芯弯管以及在有芯弯管时选用何种芯棒,需要对弯制管件的相对弯曲半径R/D及相对壁厚S/D、弯曲角度α数值的大小进行分析之后来确定。
R/D、S/D及α各值与弯管方式及芯棒形状之间的相互关系如表1所示,弯管时参照此表可达到满意的效果。
从表1可以看出,对于相同外径D、壁厚S的管子,在弯制不同的圆弧半径R时,由于其相对弯曲半径R /D、相对壁厚S/D以及弯曲角度α的不同,可分别选用下列方式进行弯管:①无芯弯管、②使用硬式芯棒弯管、③使用软式芯棒(多节芯棒)弯管等。
当R/D ≥3、S/D≥0.05时,采用无芯弯管即可;当R/D≤2.5、S/D≥0.05或R/D≥3、S/D≥0.025时,使用硬式芯棒可达到预期的效果;当R/D与S/D两者都较小而弯曲角度α较大时,弯管过程中必须使用软式芯棒。
注:1.选择虚线下面的方式进行弯管时,应配防皱块;2.N—表示可以不使用芯棒(即无芯弯管);3.H—表示可以使用硬式芯棒弯管;4.F—表示需使用软式芯棒弯管,后面的数字为推荐的球节数。
五、芯棒的选用
芯棒的形状是多种多样的,对于具有不同相对弯曲半径或相对壁厚的管件,以及对其加工要求的不同,应选用不同的形状芯棒。
一般情况下,可将芯棒分为两大类:一种为硬式芯棒(见图3a、b、c),一种为软式芯棒(见图3d、e、f)
(a)圆柱芯棒(b)球头芯棒(c)爪形芯棒(d)链式芯棒(e)软轴芯棒(f)球窝节芯棒
在选用硬式芯棒时,由于圆柱形芯棒(或球头芯棒)形状简单、制造方便、所使用场合比爪形芯棒更普遍;而在选用软式芯棒时,由于球窝节芯棒能够多方挠曲,各球节之间是球面铰接,能适应各种变形,因此,在弯薄壁或相对弯曲半径较小的管件时经常采用,同时,选用球窝节芯棒还要根据不同的相对弯曲半径、相对管壁厚度和弯曲角度考虑选用不同的球节数,球节数目的多少可参考表1选取。
若球节数少,则达不到预期的效果;球节数多,则制造困难且不便于管子穿入。
对于R/D、S/D及α在表1所列各值之间的数值,可参照此表折衷取值来选取芯棒和确定弯管方式。
芯棒形状选定后,还不能保证弯出高质量的管件,芯棒与管子内径之间的间隙大小也是影响弯管质量的重要因素。
如果芯棒的球节直径偏小,管子弯曲时圆弧内侧有可能产生波浪形皱折(见图4A处),而且还可能起不到防止圆弧外侧变
扁的作用;直径偏大或者球节外径不够光滑时,会拉伤管壁,管子圆弧外侧还有可能起鼓包甚至破裂。
选择合理的芯棒直径及对其充分润滑是保证弯管质量不可缺少的要素。
图4球节直径偏小时出现内侧起皱、外侧变扁
芯棒直径尺寸d可参照下列经验公式选取: d≈(0.94~0.98)D
式中d—芯棒直径,mm
D—管子内径名义尺寸,mm。