塑胶件结构设计方案
塑胶产品结构设计案例
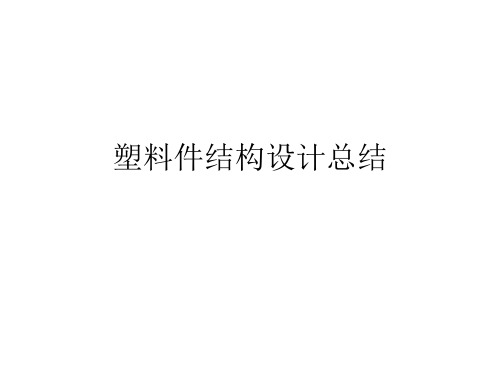
Ø 2.6 mm
Ø 3.0 mm
Ø 5.5 mm
Ø 6.0 mm
支柱的出模角一般会以支柱顶部的平面为 中性面,而且角度一般为0.5º ~1.0º 。如支 柱的高度超过15.0mm的时候,为加强支柱 的强度,可在支柱连上些加强筋,作结构 加强之用。
• 如支柱需要穿过PCB的时候,同样在支柱连上些加强筋,而且在加强 筋的顶部设计成平台形式,此可作承托PCB之用,而平台的平面与丝 筒项的平面必须要有2.0 ~ 3.0mm。
– 用途:玩具、日常用品、包装胶袋、瓶子 – 特性:有弹性、韧度强、延伸性大、但不可涂胶 水,工作温度-30℃~140℃ 。 – 应用:多数应用于一些因要接受跌落测试而拆件 的地方。
• PVC(聚氯乙烯)
– 用途:软喉管、硬喉管、软板、硬板、电线、玩 具 – 特性:柔软、坚韧而有弹性,工作温度-25℃~ 75℃ ;200 ℃ 易分解产生腐蚀、刺激性气体。 – PVC电线、电缆在制造、使用及废弃处理时, 都会产生大量的二恶英、氯氢酸、铅等有害物 质。 – 设计上的应用:多数用于玩具,或一些需要避震 或吸震的地方。
5<x≦10mm 10<x≦15mm x≦5mm 5<x≦10mm
2mm
1.4~1.5mm
10<x≦15mm 15<x≦20mm 20<x≦25mm 25<x≦30mm x≦5mm
5<x≦10mm
2.5mm 1.8mm 10<x≦15mm 15<x≦20mm 20<x≦25mm 25<x≦30mm
0.5°~1.0°
支柱套
• 跟据一般的安全规格标准,螺丝头必须收藏于不能触摸的 位置,所以高度必须有2.5mm或以上。由于加上支柱套后 会有锐边,所以在每一个支柱套上壳收螺丝的地方,必须 加上R1.0或以上的圆角。
塑胶件通用结构设计

Rev.A
P17
壁厚:
壁厚影响收缩
Rev.A
P18
壁厚:
Rev.A
壁厚影响收缩
前后模温度差异大时,冷却效率所影响,冷面先收缩,但很快固化,收缩量 固定,但热面缓慢收缩,分子有较长时间重排,收缩量会更大,所以产品会 向热的一面弯曲(产品各处温度差 大于10 ̊C以上)
P19
Rev.A
壁厚:
壁厚影响收缩
PC 6485 UL.pdf
P25
肋骨:
肋骨厚度:
Rev.A
P26
Rev.A
肋骨:
肋骨厚度推荐值:
高光泽面, 可以选择更薄的厚度: <1.5mm, 厚度推荐值 <=1.0mm, 等于壁厚
P27
Rev.A
肋骨:
加强筋厚度与塑件壁厚的关系:
P28
肋骨:
薄壁肋骨问题:
-难填充 -靠近浇口比远处更难填充 -当壁厚在填充时,薄壁滞流冻结
圆角加大,应力集中减少。 内圆角R <0.3T----应力剧增。 内圆角R >0.8T----几乎无应力集中
Rev.A
P33
肋骨:
常见加强肋设计:
Rev.A
P34
肋骨:
常见加强肋设计:
Rev.A
P35
肋骨:
常见加强肋设计:
Rev.A
P36
肋骨:
常见加强肋设计:
Rev.A
P37
Rev.A
肋骨:
Rev.A
P2
Rev.A
壁厚:
壁厚的影响: 机械性能,感观,模塑性,成本
- 壁厚的选择是各方面的平衡 *强度 VS 减轻重量 *耐久性 VS 成本
结构设计规范

塑胶件结构设计规范一.拔模1.前模面拔模斜度,光面1-1.5度,幼纹2-3度,依据蚀纹的实际要求确定拔模斜度(3-10度).2.后模面拔模斜度,为了防止产品嵌前模,可比原则比前模面小一度.3.骨位取0.25-1度,原则上骨位顶部厚度比底部小0.20mm, 如图4所示。
4.插穿位及枕位拔模斜度3度.图1 图2 拔模快速检索表二.止口及止骨,1.塑胶件因为缩水变形的影响,上下壳装配时会有段差,严重的会刮手, 做止口可以将这种影响降到最小,而且从外观看又是一条美工线。
一般止口尺寸做0.5*0.5(依壁厚而定), 如图3所示。
2.止骨最好上下壳互插,并且有挡骨限位,配合面拔模斜度2度,并倒R角, 如图3所示。
3.骨位厚度,一般为壁厚的0.4,最厚不大于壁厚的0.7, 如图4所示。
图3 图4三.螺柱连接1. 如结构允许,上下壳螺柱连接尽量采用插入限位式,如图5所示。
2.螺丝柱底孔直径D1(自攻牙)为螺丝公称直径的0.85,螺丝柱外径M1.2:D2=Φ2.2 M1.4:D2=Φ2.6 M1.7:D2=Φ3 M2.0:D2=Φ3.5 M2.3:D2=Φ4.0 M2.6:D2=Φ4.8 M3:D2=Φ5.5螺丝过孔D3大于螺丝公称直径+0.2,如图5所示。
3.为防止打螺丝时,柱子爆裂,1). 底孔做倒角;2). 底孔做沉孔;3)加加强肋,如图5所示。
4.为防止缩水,螺丝柱做火山口减胶,如图5所示。
5.橡胶垫高出骨位0.5mm, 如图5所示。
图5四.按键1.按键与壳的间隙单边0.10-0.20mm,如喷油电镀单边增加0.025mm,如其他特殊喷涂,似涂层厚度增加间隙, 如图6所示.2.按键弹片建议厚度为0.6-0.8mm,如电镀建议为0.6mm, 如图6所示.3.按键与轻触开关的间隙为0.10,且此部位原则上不能下顶针, 如图6所示.4.如是轻触开关,PCB高度定位误差控制在0.10以内, 如图6所示.5.建议设计回程0.30mm,以抵消PCB高度误差的影响, 如图6所示.6.建议原料用奇美757原料,不能用水口料.7.按键孔建议做台阶,一部份出前模,一部份出后模,如图6所示.图6五.扣位连接,上下壳适当扣位是必要的,可以减少上下壳离壳的不良,增加机器的抗跌落性能.出斜顶或行位请注意行程,以免干涉或是铲胶, 如图5所示。
塑胶件的结构设计(提纲)
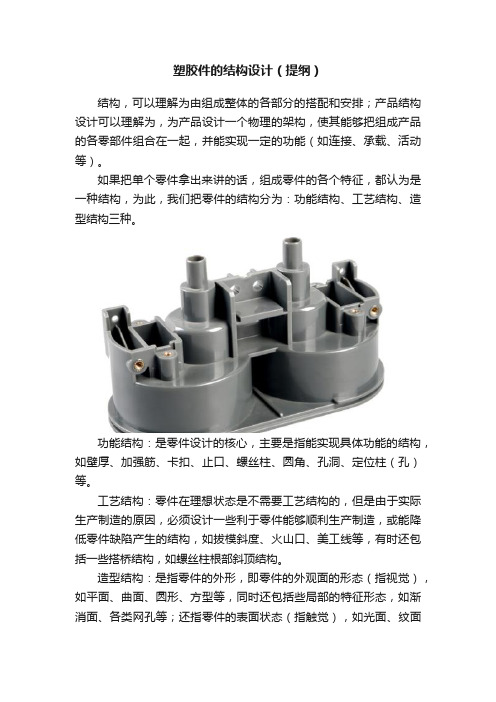
塑胶件的结构设计(提纲)结构,可以理解为由组成整体的各部分的搭配和安排;产品结构设计可以理解为,为产品设计一个物理的架构,使其能够把组成产品的各零部件组合在一起,并能实现一定的功能(如连接、承载、活动等)。
如果把单个零件拿出来讲的话,组成零件的各个特征,都认为是一种结构,为此,我们把零件的结构分为:功能结构、工艺结构、造型结构三种。
功能结构:是零件设计的核心,主要是指能实现具体功能的结构,如壁厚、加强筋、卡扣、止口、螺丝柱、圆角、孔洞、定位柱(孔)等。
工艺结构:零件在理想状态是不需要工艺结构的,但是由于实际生产制造的原因,必须设计一些利于零件能够顺利生产制造,或能降低零件缺陷产生的结构,如拔模斜度、火山口、美工线等,有时还包括一些搭桥结构,如螺丝柱根部斜顶结构。
造型结构:是指零件的外形,即零件的外观面的形态(指视觉),如平面、曲面、圆形、方型等,同时还包括些局部的特征形态,如渐消面、各类网孔等;还指零件的表面状态(指触觉),如光面、纹面等。
在之前文章有提到,本年度主要分享结构设计的知识多一些,以上就是需要介绍的主题提纲,即由功能结构、工艺介绍、造型结构组成的零件的结构设计。
需要声明的是,是以塑胶件的角度进行介绍,其他诸如压铸件,结构上虽与塑胶件有很大相似之处,但咱不做具体的分析介绍。
以上一些列的结构知识基本上囊括了一件塑胶零件的结构设计内容,(注意:特指结构,不包含CMF相关的内容)。
所以,大家可以随意拿出一件塑胶零件,仔细观察,零件的结构基本都可以从上面提到的三种结构分类找到具体的结构。
大家不要误解零件的结构就是产品的结构,实际上,产品的具体结构设计的内容不单单是零件的结构,还应包括零件之间的分配关系(即拆件)以及配合关系(即装配),这部分内容留到以后介绍,(注意:两个零件通过有些配合关系可视为一个零件,如双色件)。
可能有些小伙伴会问,这些内容太基础了,很多资料网上都有,甚至其他公众号都有相对应的介绍。
塑胶件结构设计方案(PPT 50页)

从产品设计角度来看: 过厚的产品增加导致产生 ”空穴” 气孔的可能性, 大大削弱产品的刚性及强度 .
1. 由厚胶料的地方过渡到薄胶料的地方应尽可能顺滑, 太突然的壁厚过渡转变 会导致因冷却速度不同和产生乱流而造成尺寸不稳定和表面问题, 并且此處 模具易產生磨損.
2. 采用固化成型的生产方法时, 流道, 浇口和部件的设计应使塑料由厚胶料的 地方流向薄胶料的地方, 这样使模腔内有适当的压力以减少在厚胶料的地方 出现缩水及避免模腔不能完全充填的现象; 若塑料的流动方向是从薄胶料的 地方流向厚胶料的地方, 则应采用结构性发泡的生产方法来减低模腔压力.
加强筋的一般設計形式 角支撑的形式
材料厚度与加強筋的尺寸关系(一)
PC,PPO PA,PE PMMA,ABS PS
T’<0.6T T’<0.5T T’<0.5T T’<0.6T
肋根部厚度约为(0.5~0.7)T 肋间间距>4T 肋高L<3T
不同材质的加强筋细节有所区别 ABS
材料厚度与加強筋的关系(三)
2、在制品形状方面:能满足使用要求,有利于充模,排气,补缩,同时能适应高效冷 却硬化(热塑性塑料制品)或快速受热固化(热固性塑料制品)等.
3、在模具方面:应考虑它的总体结构,特别是抽芯与脱出制品的复杂程度;同时应 充分考虑模具零件的形状及其制造工艺,以便使制品具有较好的经济性.
4、在成本方面:要考虑注射制品的利润率,年产量,原料价格,使用寿命和更换期 限,尽可能降低成本.
材料厚度与加強筋的关系(二)
材料厚度与加強筋的关系(四)
如果对外观要求不是很严格的话可以在此处 加一个槽防止缩水和产生气泡
三 塑胶零件及产品设计---卡扣篇
塑料产品结构设计资料

塑料产品结构设计资料目录一、零件壁厚 (1)二、脱模斜度 (4)三、圆角设计 (5)四、加强筋的设计 (7)五、支柱的设计 (8)六、螺丝柱的设计 (9)七、孔的设计 (10)八、止口的设计 (11)九、卡扣的设计 (13)十、反止口的设计 (18)零件设计必须满足来自于零件制造端的要求,对通过注射加工工艺而获得的塑胶件也是如此。
在满足产品功能、质量以及外观等要求下,塑胶件设计必须使得注射模具加工简单、成本低,同时零件注射时间短、效率高、零件缺陷少、质量高,这就是面向注射加工的设计。
现将详细介绍塑胶件设计指南,使得塑胶件设计是面向注射加工的设计。
一、零件壁厚在塑胶件的设计中,零件壁厚是首先考虑的参数,零件壁厚决定了零件的力学性能、零件的外观、零件的可注射性以及零件的成本等。
可以说,零件壁厚的选择和设计决定了零件设计的成功与失败。
1、零件壁厚必须适中由于塑胶材料的特性和注射工艺的特殊性,塑胶件的壁厚必须在一个合适的范围内,不能太薄,也不能太厚。
壁厚太小,零件注射时流动阻力大,塑胶熔料很难充满整个型腔,不得不通过性能更高的注射设备来获得更高的充填速度和注射压力。
壁厚太大,零件冷却时间增加,零件成型周期增加,零件生产效率低;同时过大的壁厚很容易造成零件产生缩水、气孔、翘曲等质量问题。
零件壁厚可根据材料的不同及产品外形尺寸的大小来选择,其范围一般为0.6~6.0mm,常用的厚度一般在1.5~3.0mm之间。
表1是常用塑料件料厚推荐值,小型产品是指最大外形尺寸L<80.0mm,中型产品是指最大外形尺寸为80.0mm<L<200.0mm,大型产品是指最大外形尺寸L>200.0mm。
表1 常用塑料件料厚推荐值(单位mm)2、尽量减少零件壁厚决定塑胶件壁厚的关键因素包括:1)零件的结构强度是否足够。
一般来说,壁厚越大,零件强度越好。
但零件壁厚超过一定范围时,由于缩水和气孔等质量问题的产生,增加零件壁厚反而会降低零件强度。
塑胶产品结构设计

塑胶产品结构设计要点1.胶厚(胶位):塑胶产品的胶厚(整体外壳)通常在0.80-3.00左右,太厚容易缩水和产生汽泡,太薄难走满胶,大型的产品胶厚取厚一点,小的产品取薄一点,一般产品取1.0-2.0为多。
而且胶位要尽可能的均匀,在不得已的情况下,局部地方可适当的厚一点或薄一点,但需渐变不可突变,要以不缩水和能走满胶为原则,一般塑料胶厚小于0.3时就很难走胶,但软胶类和橡胶在0.2-0.3的胶厚时也能走满胶。
2.加强筋(骨位):塑胶产品大部分都有加强筋,因加强筋在不增加产品整体胶厚的情况下可以大大增加其整体强度,对大型和受力的产品尤其有用,同时还能防止产品变形。
加强筋的厚度通常取整体胶厚的0.5-0.7倍,如大于0.7倍则容易缩水。
加强筋的高度较大时则要做0.5-1的斜度(因其出模阻力大),高度较矮时可不做斜度。
3.脱模斜度:塑料产品都要做脱模斜度,但高度较浅的(如一块平板)和有特殊要求的除外(但当侧壁较大而又没出模斜度时需做行位)。
出模斜度通常为1-5度,常取2度左右,具体要根据产品大小、高度、形状而定,以能顺利脱模和不影响使用功能为原则。
产品的前模斜度通常要比后模的斜度大0.5度为宜,以便产品开模事时能留在后模。
通常枕位、插穿、碰穿等地方均需做斜度,其上下断差(即大端尺寸与小端尺寸之差)单边要大于0.1以上。
4.圆角(R角):塑胶产品除特殊要求指定要锐边的地方外,在棱边处通常都要做圆角,以便减小应力集中、利于塑胶的流动和容易脱模。
最小R通常大于0.3,因太小的R模具上很难做到。
5.孔:从利于模具加工方面的角度考虑,孔最好做成形状规则简单的圆孔,尽可能不要做成复杂的异型孔,孔径不宜太小,孔深与孔径比不宜太大,因细而长的模具型心容易断、变形。
孔与产品外边缘的距离最好要大于1.5倍孔径,孔与孔之间的距离最好要大于2倍的孔径,以便产品有必要的强度。
与模具开模方向平行的孔在模具上通常上是用型心(可镶、可延伸留)或碰穿、插穿成型,与模具开模方向不平行的孔通常要做行位或斜顶,在不影响产品使用和装配的前提下,产品侧壁的孔在可能的情况下也应尽量做成能用碰穿、插穿成型的孔。
巧妙的塑胶结构设计教案
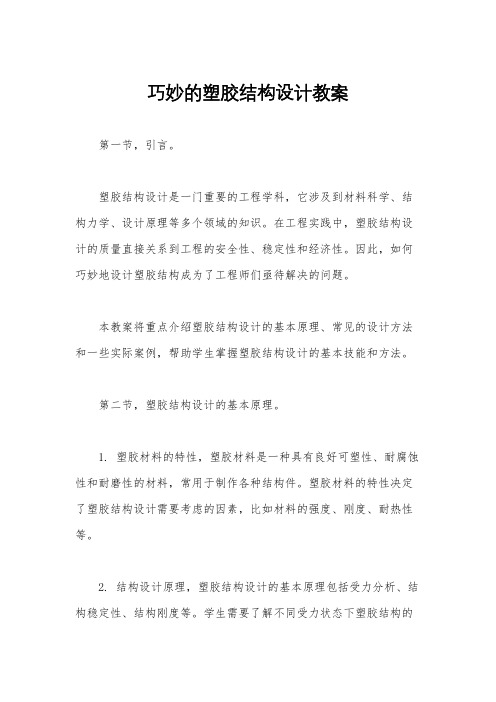
巧妙的塑胶结构设计教案第一节,引言。
塑胶结构设计是一门重要的工程学科,它涉及到材料科学、结构力学、设计原理等多个领域的知识。
在工程实践中,塑胶结构设计的质量直接关系到工程的安全性、稳定性和经济性。
因此,如何巧妙地设计塑胶结构成为了工程师们亟待解决的问题。
本教案将重点介绍塑胶结构设计的基本原理、常见的设计方法和一些实际案例,帮助学生掌握塑胶结构设计的基本技能和方法。
第二节,塑胶结构设计的基本原理。
1. 塑胶材料的特性,塑胶材料是一种具有良好可塑性、耐腐蚀性和耐磨性的材料,常用于制作各种结构件。
塑胶材料的特性决定了塑胶结构设计需要考虑的因素,比如材料的强度、刚度、耐热性等。
2. 结构设计原理,塑胶结构设计的基本原理包括受力分析、结构稳定性、结构刚度等。
学生需要了解不同受力状态下塑胶结构的受力情况,以及如何设计合理的结构形式和尺寸。
第三节,常见的塑胶结构设计方法。
1. 结构分析方法,塑胶结构的分析方法包括有限元分析、弹性力学分析、等效应力法等。
这些方法可以帮助工程师们快速准确地分析塑胶结构的受力情况,为设计提供依据。
2. 结构设计方法,在塑胶结构设计中,常用的设计方法包括材料选型、结构形式设计、尺寸优化等。
学生需要了解不同材料的特性和适用范围,以及如何根据结构的受力情况设计合理的结构形式和尺寸。
第四节,实际案例分析。
1. 塑胶桥梁设计案例,某工程项目需要设计一座跨越河流的塑胶桥梁,要求结构轻巧、耐腐蚀、易于安装。
工程师们通过有限元分析和材料选型,设计出了一种新型的塑胶桥梁结构,成功地解决了项目需求。
2. 塑胶管道设计案例,某化工厂需要设计一套输送化学品的塑胶管道系统,要求耐腐蚀、耐高温、易于维护。
工程师们通过弹性力学分析和结构形式设计,设计出了一套符合要求的塑胶管道系统,为工厂的生产提供了可靠的输送保障。
第五节,总结与展望。
通过本教案的学习,学生们可以掌握塑胶结构设计的基本原理和常见方法,为将来的工程实践打下坚实的基础。
- 1、下载文档前请自行甄别文档内容的完整性,平台不提供额外的编辑、内容补充、找答案等附加服务。
- 2、"仅部分预览"的文档,不可在线预览部分如存在完整性等问题,可反馈申请退款(可完整预览的文档不适用该条件!)。
- 3、如文档侵犯您的权益,请联系客服反馈,我们会尽快为您处理(人工客服工作时间:9:00-18:30)。
塑胶件结构设计方案
引言
塑胶件在各个工业领域广泛应用,其结构设计方案对产品质量和成本控制有着重要影响。
本文将针对塑胶件结构设计方案进行详细讨论,探讨结构设计原则、注意事项以及常用的设计方法。
结构设计原则
1. 符合产品功能和使用要求
在进行塑胶件的结构设计时,首先需要确保塑胶件能够满足产品所需的功能要求。
例如,如果塑胶件用于承载重量,则需要考虑其强度和刚度;如果用于密封材料,则需要考虑其密封性能。
2. 合理利用材料
在塑胶件的结构设计过程中,要充分利用材料的性能,尽量减少材料的浪费。
通过合理的形状设计、壁厚控制和孔洞设置等手段,达到最佳的材料利用效果。
3. 提高设计可生产性
在塑胶件结构设计中,需要考虑到产品的可生产性。
合理的结构设计能够简化生产工艺、降低制造成本,并且提高产品的生产效率。
4. 考虑装配和维修性
在塑胶件的结构设计过程中,需要考虑到产品的装配和维修性。
合理的结构设计可以使得塑胶件易于装配,并且方便进行维修和更换。
结构设计注意事项
1. 壁厚控制
塑胶件的壁厚对其性能和生产工艺有着重要影响。
过厚的壁厚会增加材料的消耗,并降低塑胶件的强度和刚度;而过薄的壁厚则容易导致塑胶件的变形和破裂。
因此,在结构设计过程中,需要合理控制塑胶件的壁厚,以实现最佳的性能和生产效果。
2. 强度和刚度要求
根据不同的使用场景和功能要求,需要合理设计塑胶件的强度和刚度。
通过在
关键部位增加加强结构或调整几何形状,可以满足产品的强度和刚度要求。
3. 模具设计
在进行塑胶件结构设计时,需要考虑到制造过程中所需的模具设计。
合理的塑
胶件结构设计能够简化模具结构,降低模具制造成本,并提高生产效率。
4. 表面处理和装饰
塑胶件在设计过程中需要考虑到表面处理和装饰要求。
通过合理的设计,可以
方便后续的表面处理(如喷塑、镀银等)和装饰操作,提高产品的美观性和附加值。
塑胶件结构设计方法
1. 结构拓扑优化
结构拓扑优化是一种常用的塑胶件结构设计方法。
通过应用有限元分析和优化
算法,将原始的结构进行优化,以实现最佳的结构形式和性能。
拓扑优化可以帮助设计师在不改变功能和强度要求的情况下,减少材料的使用并优化结构的重量和成本。
2. 特征参数设计
特征参数设计是一种基于经验的设计方法,在塑胶件结构设计中常常使用。
通
过提取和分析已有成功案例中的特征参数,设计师可以快速确定塑胶件的结构形式和尺寸。
这种方法在设计周期紧张且功能要求简单的情况下特别适用。
3. 模拟仿真和验证
模拟仿真和验证是一种有效的塑胶件结构设计方法。
通过使用CAD软件和有
限元分析软件对塑胶件进行模拟仿真,可以预测塑胶件的性能、破坏情况和制造工艺,并及早发现和解决潜在的问题。
这种方法可以提高设计效率,降低试验成本,减少设计调整的次数。
结论
在塑胶件结构设计过程中,需要考虑产品的功能要求、材料利用、可生产性、
装配和维修性等因素。
合理的设计原则和注意事项可以帮助设计师实现最佳的设计方案。
在具体的设计方法上,结构拓扑优化、特征参数设计和模拟仿真验证是常用的方法。
通过合理应用这些方法,可以提高设计效率和产品质量,降低成本,满足市场需求。