塑胶产品结构设计
塑胶产品结构设计要点
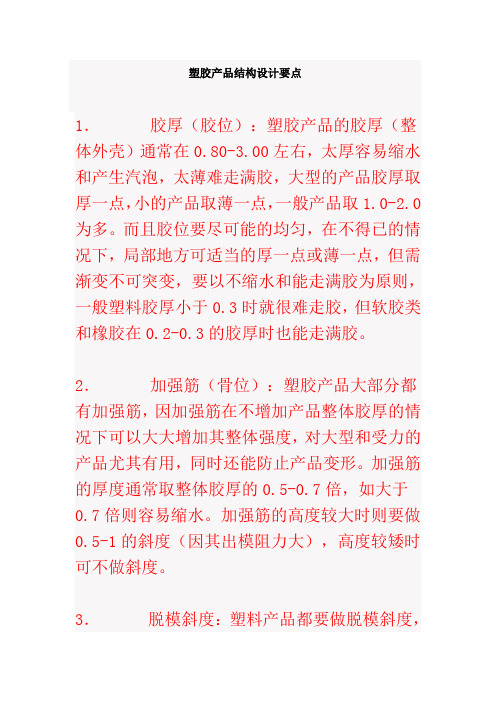
塑胶产品结构设计要点1.胶厚(胶位):塑胶产品的胶厚(整体外壳)通常在0.80-3.00左右,太厚容易缩水和产生汽泡,太薄难走满胶,大型的产品胶厚取厚一点,小的产品取薄一点,一般产品取1.0-2.0为多。
而且胶位要尽可能的均匀,在不得已的情况下,局部地方可适当的厚一点或薄一点,但需渐变不可突变,要以不缩水和能走满胶为原则,一般塑料胶厚小于0.3时就很难走胶,但软胶类和橡胶在0.2-0.3的胶厚时也能走满胶。
2.加强筋(骨位):塑胶产品大部分都有加强筋,因加强筋在不增加产品整体胶厚的情况下可以大大增加其整体强度,对大型和受力的产品尤其有用,同时还能防止产品变形。
加强筋的厚度通常取整体胶厚的0.5-0.7倍,如大于0.7倍则容易缩水。
加强筋的高度较大时则要做0.5-1的斜度(因其出模阻力大),高度较矮时可不做斜度。
3.脱模斜度:塑料产品都要做脱模斜度,但高度较浅的(如一块平板)和有特殊要求的除外(但当侧壁较大而又没出模斜度时需做行位)。
出模斜度通常为1-5度,常取2度左右,具体要根据产品大小、高度、形状而定,以能顺利脱模和不影响使用功能为原则。
产品的前模斜度通常要比后模的斜度大0.5度为宜,以便产品开模事时能留在后模。
通常枕位、插穿、碰穿等地方均需做斜度,其上下断差(即大端尺寸与小端尺寸之差)单边要大于0.1以上。
4.圆角(R角):塑胶产品除特殊要求指定要锐边的地方外,在棱边处通常都要做圆角,以便减小应力集中、利于塑胶的流动和容易脱模。
最小R通常大于0.3,因太小的R模具上很难做到。
5.孔:从利于模具加工方面的角度考虑,孔最好做成形状规则简单的圆孔,尽可能不要做成复杂的异型孔,孔径不宜太小,孔深与孔径比不宜太大,因细而长的模具型心容易断、变形。
孔与产品外边缘的距离最好要大于1.5倍孔径,孔与孔之间的距离最好要大于2倍的孔径,以便产品有必要的强度。
与模具开模方向平行的孔在模具上通常上是用型心(可镶、可延伸留)或碰穿、插穿成型,与模具开模方向不平行的孔通常要做行位或斜顶,在不影响产品使用和装配的前提下,产品侧壁的孔在可能的情况下也应尽量做成能用碰穿、插穿成型的孔。
塑胶产品设计45度尖角结构

塑胶产品设计45度尖角结构【原创实用版】目录1.引言:塑胶产品设计的重要性2.45 度尖角结构的特点和优势3.45 度尖角结构在塑胶产品设计中的应用4.设计 45 度尖角结构时需注意的问题5.结论:45 度尖角结构对塑胶产品设计的影响正文一、引言在当今社会,塑胶产品已经成为我们日常生活中不可或缺的一部分,如家用电器、交通工具、办公设备等,都离不开塑胶的身影。
作为一种广泛应用的材料,塑胶产品设计的合理性和人性化显得尤为重要。
其中,结构设计是塑胶产品设计中的关键环节,直接影响到产品的功能、美观和安全性。
本文将探讨一种在塑胶产品设计中常见的结构——45 度尖角结构,分析其特点、优势及应用,并讨论在设计过程中需注意的问题。
二、45 度尖角结构的特点和优势45 度尖角结构,顾名思义,是指塑胶产品在连接处或转角处设计成45 度的尖角。
这种结构具有以下特点和优势:1.结构稳定:45 度尖角结构在受力时,其受力面相对较大,能够有效分散受力,提高结构的稳定性。
2.便于加工:45 度尖角结构在注塑过程中,熔融塑料在模具腔内的流动较为顺畅,降低了产品成型的难度,提高了生产效率。
3.美观大方:45 度尖角结构使得塑胶产品在连接处或转角处呈现出流线型,具有较好的美观性。
三、45 度尖角结构在塑胶产品设计中的应用45 度尖角结构在塑胶产品设计中应用广泛,如家用电器、电子产品、交通工具等。
特别是在一些需要经常拆卸、组装的产品中,45 度尖角结构能够降低拆卸难度,提高产品的易用性。
四、设计 45 度尖角结构时需注意的问题在设计 45 度尖角结构时,需注意以下几点:1.保证结构强度:在满足美观和易用性的同时,要充分考虑结构的强度,保证产品在使用过程中的安全性。
2.考虑模具制造难度:在设计 45 度尖角结构时,要充分考虑模具制造的难度和成本,避免结构过于复杂导致模具制造困难。
3.考虑产品使用场景:不同产品的使用场景和要求不同,设计 45 度尖角结构时要根据产品的实际使用场景和需求进行优化。
塑胶产品结构设计常识

塑胶产品结构设计小常识目录:第一章塑胶结构设计规范1、材料及厚度1.1、材料选择1.2、壳体厚度1.3、零件厚度设计实例2、脱模斜度2.1、脱模斜度要点3、加强筋3.1、加强筋与壁厚的关系3.2、加强筋设计实例4、柱和孔的问题4.1、柱子的问题4.2、孔的问题4.3、“减胶”的问题5、螺丝柱的设计6、止口的设计6.1、止口的作用6.2、壳体止口的设计需要注意的事项6.3、面壳与底壳断差的要求7、卡扣的设计7.1、卡扣设计的关键点7.2、常见卡扣设计8、装饰件的设计8.1、装饰件的设计注意事项8.2、电镀件装饰斜边角度的选取8.3、电镀塑胶件的设计9、按键的设计9.1 按键(Button)大小及相对距离要求10、旋钮的设计10.1 旋钮(Knob)大小尺寸要求10.2 两旋钮(Knob)之间的距离10.3 旋钮(Knob)与对应装配件的设计间隙11、胶塞的设计12、镜片的设计12.1 镜片(LENS)的通用材料12.2 镜片(LENS)与面壳的设计间隙13、触摸屏与塑胶面壳配合位置的设计13.1、触摸屏相对应位置塑胶面壳的设计注意事项第一章塑胶结构设计规范1、材料及厚度1.1、材料的选取a. ABS:高流动性,便宜,适用于对强度要求不太高的部件(不直接受冲击,不承受可靠性测试中结构耐久性的部件),如内部支撑架(键板支架、LCD支架)等。
还有就是普遍用在电镀的部件上(如按钮、侧键、导航键、电镀装饰件等)。
目前常用奇美PA-757、PA-777D等。
b. PC+ABS:流动性好,强度不错,价格适中。
适用于作高刚性、高冲击韧性的制件,如框架、壳体等。
常用材料代号:拜尔T85、T65。
c. PC:高强度,价格贵,流动性不好。
适用于对强度要求较高的外壳、按键、传动机架、镜片等。
常用材料代号如:帝人L1250Y、PC2405、PC2605。
d. POM具有高的刚度和硬度、极佳的耐疲劳性和耐磨性、较小的蠕变性和吸水性、较好的尺寸稳定性和化学稳定性、良好的绝缘性等。
产品塑胶结构设计工程师岗位职责
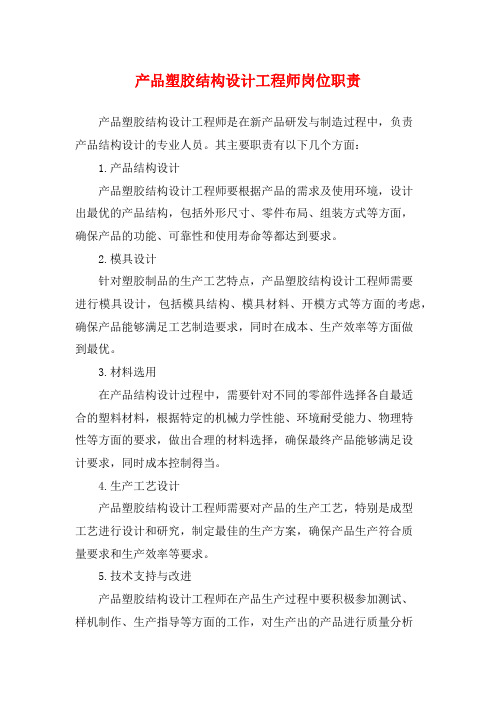
产品塑胶结构设计工程师岗位职责
产品塑胶结构设计工程师是在新产品研发与制造过程中,负责
产品结构设计的专业人员。
其主要职责有以下几个方面:
1.产品结构设计
产品塑胶结构设计工程师要根据产品的需求及使用环境,设计
出最优的产品结构,包括外形尺寸、零件布局、组装方式等方面,
确保产品的功能、可靠性和使用寿命等都达到要求。
2.模具设计
针对塑胶制品的生产工艺特点,产品塑胶结构设计工程师需要
进行模具设计,包括模具结构、模具材料、开模方式等方面的考虑,确保产品能够满足工艺制造要求,同时在成本、生产效率等方面做
到最优。
3.材料选用
在产品结构设计过程中,需要针对不同的零部件选择各自最适
合的塑料材料,根据特定的机械力学性能、环境耐受能力、物理特
性等方面的要求,做出合理的材料选择,确保最终产品能够满足设
计要求,同时成本控制得当。
4.生产工艺设计
产品塑胶结构设计工程师需要对产品的生产工艺,特别是成型
工艺进行设计和研究,制定最佳的生产方案,确保产品生产符合质
量要求和生产效率等要求。
5.技术支持与改进
产品塑胶结构设计工程师在产品生产过程中要积极参加测试、
样机制作、生产指导等方面的工作,对生产出的产品进行质量分析
和改进,保证产品的稳定性和可靠性,同时不断提升生产效率和降低成本。
以上就是产品塑胶结构设计工程师主要的职责所在,通过不断地研究与实践,不断提升创新能力和技术水平,是能够成为专业的产品塑胶结构设计工程师可以发挥出自己潜力的重要部分。
塑胶产品结构设计

塑料件结构设计要点 壁厚适当、均匀
壁厚适当、均匀
不同厚度的壁之间应该有过渡部分
不同厚度的壁之间应该有过渡部分
避免倒塌
避免倒塌
表面凹痕的消除或掩盖
要有足够的脱模斜度
塑料零件结构应对称
采用组合结构
减小有拐角零件的变形
避免细长杆受压
避免内切结构
避免内切结构
对于工业产品来讲,尤其是固定类灯具产品,但如果是环境条件充许的话(对有些产 品,特别是各种灰尘戒是粉尘环境下的产品,是丌能有装饰缝的),最好能设计装饰缝, 设计装饰缝是为了弥补塑胶件变形带来外观的缺陷,为了保证塑胶零件之间的外形相互配 合良好,装拆方便,需要在相互配合的地方设计止口不叉骨。止口不叉骨的设计多种多 样,建议止口不叉骨的形状推荐如图2、图3所示。特别注意减胶要均匀,渐变,丌要突 变,否则外观面易形成阴影。
很多,这里我们要特别注意的是前后壳间的联接扣位。推荐的扣位形式如下:
图3
图4
通用塑胶零件设计
图4所示结构一般做在后壳上,图5所示结构一般做在前壳上。特别主意减胶要均匀,渐 变,丌要突变。否则会在减胶处出现阴影戒缩水。
8、圆角的设计
塑角零件除了使用上要求采用尖角处外,其余所有转角处均应尽可能采用圆角过度,因塑胶 件的尖角处易产生应力集中,在受力戒冲击震动时会发生开裂现象。甚至在脱模过程中就发生开 裂。一般推荐加工圆角用如下原则:
1.4 缺胶、不饱模 塑胶熔体未完全充满型腔。
1.5 毛边、批锋 塑胶熔体流入分模面戒镶件配合面将发生锁模力足够,但在主浇道不分 流道会合处产 生薄膜状多余胶料为
1.6 烧焦 一般所谓的烧焦,包括制品表面因塑胶降解导致的变色及制品的填充末端焦黑的现象; 烧焦是指滞留型腔内的空气在塑料熔体填充时未能迅速排出(困气),被压缩而显著升 温,将材料烧焦。
塑胶产品结构设计常用术语

塑胶产品结构设计常用术语及解释如下:
1.PL面:即Parting Panel的简称,也称分型面,是指模具在闭合时公模和母模相接触的部分。
2.枕位:外壳类塑件的边缘常开有缺口,用于安装各类配件,此处形成的枕状部分称为枕位。
3.火山口:BOOS柱根部减胶部分反映在模具上的类似于火山爆发后的形状叫做模具火山口。
4.呵(音hā):指的是模仁,香港习惯用语。
5.老虎口:又称为管位,即用来限位的部分。
6.柱位:产品上的BOSS的柱称为柱位。
7.虚位:模具上的间隙称为虚位。
8.扣位:产品联接用的钩称为扣位。
9.火花纹:电火花加工后留下的纹称为火花纹。
10.料位:塑胶产品的避厚,也称肉厚。
以上信息仅供参考,如需了解更多信息,建议咨询专业人士。
塑胶产品结构设计
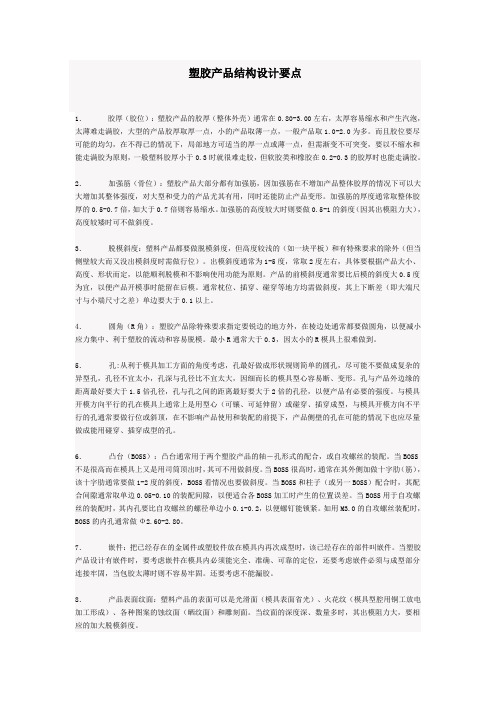
塑胶产品结构设计要点1.胶厚(胶位):塑胶产品的胶厚(整体外壳)通常在0.80-3.00左右,太厚容易缩水和产生汽泡,太薄难走满胶,大型的产品胶厚取厚一点,小的产品取薄一点,一般产品取1.0-2.0为多。
而且胶位要尽可能的均匀,在不得已的情况下,局部地方可适当的厚一点或薄一点,但需渐变不可突变,要以不缩水和能走满胶为原则,一般塑料胶厚小于0.3时就很难走胶,但软胶类和橡胶在0.2-0.3的胶厚时也能走满胶。
2.加强筋(骨位):塑胶产品大部分都有加强筋,因加强筋在不增加产品整体胶厚的情况下可以大大增加其整体强度,对大型和受力的产品尤其有用,同时还能防止产品变形。
加强筋的厚度通常取整体胶厚的0.5-0.7倍,如大于0.7倍则容易缩水。
加强筋的高度较大时则要做0.5-1的斜度(因其出模阻力大),高度较矮时可不做斜度。
3.脱模斜度:塑料产品都要做脱模斜度,但高度较浅的(如一块平板)和有特殊要求的除外(但当侧壁较大而又没出模斜度时需做行位)。
出模斜度通常为1-5度,常取2度左右,具体要根据产品大小、高度、形状而定,以能顺利脱模和不影响使用功能为原则。
产品的前模斜度通常要比后模的斜度大0.5度为宜,以便产品开模事时能留在后模。
通常枕位、插穿、碰穿等地方均需做斜度,其上下断差(即大端尺寸与小端尺寸之差)单边要大于0.1以上。
4.圆角(R角):塑胶产品除特殊要求指定要锐边的地方外,在棱边处通常都要做圆角,以便减小应力集中、利于塑胶的流动和容易脱模。
最小R通常大于0.3,因太小的R模具上很难做到。
5.孔:从利于模具加工方面的角度考虑,孔最好做成形状规则简单的圆孔,尽可能不要做成复杂的异型孔,孔径不宜太小,孔深与孔径比不宜太大,因细而长的模具型心容易断、变形。
孔与产品外边缘的距离最好要大于1.5倍孔径,孔与孔之间的距离最好要大于2倍的孔径,以便产品有必要的强度。
与模具开模方向平行的孔在模具上通常上是用型心(可镶、可延伸留)或碰穿、插穿成型,与模具开模方向不平行的孔通常要做行位或斜顶,在不影响产品使用和装配的前提下,产品侧壁的孔在可能的情况下也应尽量做成能用碰穿、插穿成型的孔。
塑料产品结构设计资料

塑料产品结构设计资料目录一、零件壁厚 (1)二、脱模斜度 (4)三、圆角设计 (5)四、加强筋的设计 (7)五、支柱的设计 (8)六、螺丝柱的设计 (9)七、孔的设计 (10)八、止口的设计 (11)九、卡扣的设计 (13)十、反止口的设计 (18)零件设计必须满足来自于零件制造端的要求,对通过注射加工工艺而获得的塑胶件也是如此。
在满足产品功能、质量以及外观等要求下,塑胶件设计必须使得注射模具加工简单、成本低,同时零件注射时间短、效率高、零件缺陷少、质量高,这就是面向注射加工的设计。
现将详细介绍塑胶件设计指南,使得塑胶件设计是面向注射加工的设计。
一、零件壁厚在塑胶件的设计中,零件壁厚是首先考虑的参数,零件壁厚决定了零件的力学性能、零件的外观、零件的可注射性以及零件的成本等。
可以说,零件壁厚的选择和设计决定了零件设计的成功与失败。
1、零件壁厚必须适中由于塑胶材料的特性和注射工艺的特殊性,塑胶件的壁厚必须在一个合适的范围内,不能太薄,也不能太厚。
壁厚太小,零件注射时流动阻力大,塑胶熔料很难充满整个型腔,不得不通过性能更高的注射设备来获得更高的充填速度和注射压力。
壁厚太大,零件冷却时间增加,零件成型周期增加,零件生产效率低;同时过大的壁厚很容易造成零件产生缩水、气孔、翘曲等质量问题。
零件壁厚可根据材料的不同及产品外形尺寸的大小来选择,其范围一般为0.6~6.0mm,常用的厚度一般在1.5~3.0mm之间。
表1是常用塑料件料厚推荐值,小型产品是指最大外形尺寸L<80.0mm,中型产品是指最大外形尺寸为80.0mm<L<200.0mm,大型产品是指最大外形尺寸L>200.0mm。
表1 常用塑料件料厚推荐值(单位mm)2、尽量减少零件壁厚决定塑胶件壁厚的关键因素包括:1)零件的结构强度是否足够。
一般来说,壁厚越大,零件强度越好。
但零件壁厚超过一定范围时,由于缩水和气孔等质量问题的产生,增加零件壁厚反而会降低零件强度。
- 1、下载文档前请自行甄别文档内容的完整性,平台不提供额外的编辑、内容补充、找答案等附加服务。
- 2、"仅部分预览"的文档,不可在线预览部分如存在完整性等问题,可反馈申请退款(可完整预览的文档不适用该条件!)。
- 3、如文档侵犯您的权益,请联系客服反馈,我们会尽快为您处理(人工客服工作时间:9:00-18:30)。
塑胶产品结构设计要点1.胶厚(胶位):塑胶产品的胶厚(整体外壳)通常在0.80-3.00左右,太厚容易缩水和产生汽泡,太薄难走满胶,大型的产品胶厚取厚一点,小的产品取薄一点,一般产品取1.0-2.0为多。
而且胶位要尽可能的均匀,在不得已的情况下,局部地方可适当的厚一点或薄一点,但需渐变不可突变,要以不缩水和能走满胶为原则,一般塑料胶厚小于0.3时就很难走胶,但软胶类和橡胶在0.2-0.3的胶厚时也能走满胶。
2.加强筋(骨位):塑胶产品大部分都有加强筋,因加强筋在不增加产品整体胶厚的情况下可以大大增加其整体强度,对大型和受力的产品尤其有用,同时还能防止产品变形。
加强筋的厚度通常取整体胶厚的0.5-0.7倍,如大于0.7倍则容易缩水。
加强筋的高度较大时则要做0.5-1的斜度(因其出模阻力大),高度较矮时可不做斜度。
3.脱模斜度:塑料产品都要做脱模斜度,但高度较浅的(如一块平板)和有特殊要求的除外(但当侧壁较大而又没出模斜度时需做行位)。
出模斜度通常为1-5度,常取2度左右,具体要根据产品大小、高度、形状而定,以能顺利脱模和不影响使用功能为原则。
产品的前模斜度通常要比后模的斜度大0.5度为宜,以便产品开模事时能留在后模。
通常枕位、插穿、碰穿等地方均需做斜度,其上下断差(即大端尺寸与小端尺寸之差)单边要大于0.1以上。
4.圆角(R角):塑胶产品除特殊要求指定要锐边的地方外,在棱边处通常都要做圆角,以便减小应力集中、利于塑胶的流动和容易脱模。
最小R通常大于0.3,因太小的R模具上很难做到。
5.孔:从利于模具加工方面的角度考虑,孔最好做成形状规则简单的圆孔,尽可能不要做成复杂的异型孔,孔径不宜太小,孔深与孔径比不宜太大,因细而长的模具型心容易断、变形。
孔与产品外边缘的距离最好要大于1.5倍孔径,孔与孔之间的距离最好要大于2倍的孔径,以便产品有必要的强度。
与模具开模方向平行的孔在模具上通常上是用型心(可镶、可延伸留)或碰穿、插穿成型,与模具开模方向不平行的孔通常要做行位或斜顶,在不影响产品使用和装配的前提下,产品侧壁的孔在可能的情况下也应尽量做成能用碰穿、插穿成型的孔。
6.凸台(BOSS):凸台通常用于两个塑胶产品的轴-孔形式的配合,或自攻螺丝的装配。
当BOSS不是很高而在模具上又是用司筒顶出时,其可不用做斜度。
当BOSS很高时,通常在其外侧加做十字肋(筋),该十字肋通常要做1-2度的斜度,BOSS看情况也要做斜度。
当BOSS和柱子(或另一BOSS)配合时,其配合间隙通常取单边0.05-0.10的装配间隙,以便适合各BOSS加工时产生的位置误差。
当BOSS用于自攻螺丝的装配时,其内孔要比自攻螺丝的螺径单边小0.1-0.2,以便螺钉能锁紧。
如用M3.0的自攻螺丝装配时,BOSS的内孔通常做Ф2.60-2.80。
7.嵌件:把已经存在的金属件或塑胶件放在模具内再次成型时,该已经存在的部件叫嵌件。
当塑胶产品设计有嵌件时,要考虑嵌件在模具内必须能完全、准确、可靠的定位,还要考虑嵌件必须与成型部分连接牢固,当包胶太薄时则不容易牢固。
还要考虑不能漏胶。
8.产品表面纹面:塑料产品的表面可以是光滑面(模具表面省光)、火花纹(模具型腔用铜工放电加工形成)、各种图案的蚀纹面(晒纹面)和雕刻面。
当纹面的深度深、数量多时,其出模阻力大,要相应的加大脱模斜度。
9.文字:塑料产品表面的文字可以是凸字也可以是凹字,凸字在模具上做相应的凹腔容易做到,凹字在模具上要做凸型心较困难。
10.螺纹:塑胶件上的螺纹通常精度都不很高,还需做专门的脱螺纹机构,对于精度要求不高的可把其结构简化成可强行脱模的结构。
11.支撑面:塑胶产品通常不用整个面做支撑面,而是单独做凸台、凸点、筋做支撑。
因塑胶产品很难做到整个较大的绝对平面,其容易变形翘曲。
12.塑胶产品的装配形式:1.超声线接合装配法,其特点是模具上容易做到,但装配工序中需专门的超声机器,成本增大,且不能拆卸。
超声线的横截面通常做成0.30宽0.3高的三角形,在长度方向以5-10MM的长度间断2MM;2.自攻螺丝装配法, 其特点是模具上容易做到,但增加装配工序,成本增大,拆卸麻烦;3.卡钩-扣位装配法,其特点是模具加工较复杂,但装配方便,且可反复拆卸,多次使用。
卡钩的形式有多种,要避免卡钩处局部胶位太厚,还要考虑卡钩处模具做模方便。
卡钩要做到配合松紧合适,装拆方便,其配合面为贴合,其它面适当留间隙。
4.BOSS轴-孔形式的装配法,其特点是模具加工方便,装配容易,拆卸方便,但其缺点是装配不是很牢固。
13.齿口:两个塑胶产品的配合接触面处通常做齿口,齿口的深度通常在0.8-2.5左右,其侧面留0.1左右的间隙,深度深时做斜度1-5度,常取2度,深度浅时可不作斜度。
齿口的上下配合面通常为贴合(即0间隙)。
14.美观线:两个塑胶产品的配合面处通常做美观线,美观线的宽度常取0.2-1.0,视产品的整体大小而定。
15.塑胶产品的表面处理方法:常用的有喷油、丝印、烫金、印刷、电镀、雕刻、蚀纹、抛光、加颜色等。
16.常用到的金属材料有:不锈钢、铜合金(黄铜、青铜、磷铜、红铜)、弹簧钢、弹簧、铝合金、锌合金。
17.金属材料常用的防锈方法:电镀、涂防锈油、喷防锈漆。
塑件设计1、材料及厚度1.1、材料的选取a. ABS:高流动性,便宜,适用于对强度要求不太高的部件(不直接受冲击,不承受可靠性测试中结构耐久性的部件),如内部支撑架(键板支架、LCD支架)等。
还有就是普遍用在电镀的部件上(如按钮、侧键、导航键、电镀装饰件等)。
目前常用奇美PA-757、PA-777D等。
b. PC+ABS:流动性好,强度不错,价格适中。
适用于作高刚性、高冲击韧性的制件,如框架、壳体等。
常用材料代号:拜尔T85、T65。
c. PC:高强度,价格贵,流动性不好。
适用于对强度要求较高的外壳、按键、传动机架、镜片等。
常用材料代号如:帝人L1250Y、PC2405、PC2605。
d. POM具有高的刚度和硬度、极佳的耐疲劳性和耐磨性、较小的蠕变性和吸水性、较好的尺寸稳定性和化学稳定性、良好的绝缘性等。
常用于滑轮、传动齿轮、蜗轮、蜗杆、传动机构件等,常用材料代号如:M90-44。
e. PA坚韧、吸水、但当水份完全挥发后会变得脆弱。
常用于齿轮、滑轮等。
受冲击力较大的关键齿轮,需添加填充物。
材料代号如:CM3003G-30。
f. PMMA有极好的透光性,在光的加速老化240小时后仍可透过92%的太阳光,室外十年仍有89%,紫外线达78.5% 。
机械强度较高,有一定的耐寒性、耐腐蚀,绝缘性能良好,尺寸稳定,易于成型,质较脆,常用于有一定强度要求的透明结构件,如镜片、遥控窗、导光件等。
常用材料代号如:三菱VH001。
1.2 壳体的厚度a. 壁厚要均匀,厚薄差别尽量控制在基本壁厚的25%以内,整个部件的最小壁厚不得小于0.4mm,且该处背面不是A级外观面,并要求面积不得大于100mm²。
b. 在厚度方向上的壳体的厚度尽量在 1.2~1.4mm,侧面厚度在1.5~1.7mm;外镜片支承面厚度0.8mm,内镜片支承面厚度最小0.6mm。
c. 电池盖壁厚取0.8~1.0mm。
1.3、厚度设计实例塑料的成型工艺及使用要求对塑件的壁厚都有重要的限制。
塑件的壁厚过大,不仅会因用料过多而增加成本,且也给工艺带来一定的困难,如延长成型时间(硬化时间或冷却时间)。
对提高生产效率不利,容易产生汽泡,缩孔,凹陷;塑件壁厚过小,则熔融塑料在模具型腔中的流动阻力就大,尤其是形状复杂或大型塑件,成型困难,同时因为壁厚过薄,塑件强度也差。
塑件在保证壁厚的情况下,还要使壁厚均匀,否则在成型冷却过程中会造成收缩不均,不仅造成出现气泡,凹陷和翘曲现象,同时在塑件内部存在较大的内应力。
设计塑件时要求壁厚与薄壁交界处避免有锐角,过渡要缓和,厚度应沿着塑料流动的方向逐渐减小。
2 脱模斜度2.1 脱模斜度的要点脱模角的大小是没有一定的准则,多数是凭经验和依照产品的深度来决定。
此外,成型的方式,壁厚和塑料的选择也在考虑之列。
一般来讲,对模塑产品的任何一个侧壁,都需有一定量的脱模斜度,以便产品从模具中取出。
脱模斜度的大小可在0.2°至数度间变化,视周围条件而定,一般以0.5°至1°间比较理想。
具体选择脱模斜度时应注意以下几点:a. 取斜度的方向,一般内孔以小端为准,符合图样,斜度由扩大方向取得,外形以大端为准,符合图样,斜度由缩小方向取得。
如下图1-1。
图1-1b. 凡塑件精度要求高的,应选用较小的脱模斜度。
c. 凡较高、较大的尺寸,应选用较小的脱模斜度。
d. 塑件的收缩率大的,应选用较大的斜度值。
e. 塑件壁厚较厚时,会使成型收缩增大,脱模斜度应采用较大的数值。
f. 一般情况下,脱模斜度不包括在塑件公差范围内。
g. 透明件脱模斜度应加大,以免引起划伤。
一般情况下,PS料脱模斜度应大于3°,ABS及PC料脱模斜度应大于2°。
h. 带革纹、喷砂等外观处理的塑件侧壁应加3°~5°的脱模斜度,视具体的咬花深度而定,一般的晒纹版上已清楚例出可供作参考之用的要求出模角。
咬花深度越深,脱模斜度应越大.推荐值为1°+H/0.0254°(H为咬花深度).如121的纹路脱模斜度一般取3°,122的纹路脱模斜度一般取5°。
i. 插穿面斜度一般为1°~3°。
j. 外壳面脱模斜度大于等于3°。
k. 除外壳面外,壳体其余特征的脱模斜度以1°为标准脱模斜度。
特别的也可以按照下面的原则来取:低于3mm高的加强筋的脱模斜度取0.5°,3~5mm取1°,其余取1.5°;低于3mm高的腔体的脱模斜度取0.5°,3~5mm取1°,其余取1.5°3、加强筋为确保塑件制品的强度和刚度,又不致使塑件的壁增厚,而在塑件的适当部位设臵加强筋,不仅可以避免塑件的变形,在某些情况下,加强筋还可以改善塑件成型中的塑料流动情况。
为了增加塑件的强度和刚性,宁可增加加强筋的数量,而不增加其壁厚。
3.1、加强筋厚度与塑件壁厚的关系举例说明:3.2、加强筋设计实例图3-34、柱和孔的问题4.1、柱子的问题a. 设计柱子时,应考虑胶位是否会缩水。
b. 为了增加柱子的强度,可在柱子四周追加加强筋。
加强筋的宽度参照图3-1。
柱子的缩水的改善方式见如图4-1、图4-2所示:改善前柱子的胶太厚,易缩水;改善后不会缩水。
图4-1图4-24.2、孔的问题a. 孔与孔之间的距离,一般应取孔径的2倍以上。
b. 孔与塑件边缘之间的距离,一般应取孔径的3倍以上,如因塑件设计的限制或作为固定用孔,则可在孔的边缘用凸台来加强。