埋盲孔板制作工艺规范(0610)
电路板埋盲孔的工艺

电路板埋盲孔的工艺嘿,朋友!咱们今天来聊聊电路板埋盲孔这神奇的工艺。
你知道吗?电路板就像是一座精巧复杂的城市,线路就是城市里的道路,而埋盲孔呢,就像是在这座城市里偷偷挖的一些神秘通道。
那什么是埋盲孔呢?简单来说,就是在电路板内部隐藏着的一些小孔,它们不像普通的孔那样贯穿整个板子,而是只在板子的某一层或者某几层之间连接。
这就好像是在大楼的中间楼层开了个秘密通道,让信息和电流能够在特定的楼层之间快速穿梭。
要做好这个工艺,那可得有真功夫。
首先得选对材料,这就好比盖房子得选好砖头一样,材料不好,后面的工作就全白搭啦。
然后是设计,这设计可不能马虎,得像规划城市的布局一样,仔细考虑每个盲孔的位置、大小和深度。
在制作过程中,钻孔这一步就像是在豆腐上打洞,得小心翼翼,不然稍微用力过猛,板子就废啦。
而且钻完孔还得清洗,把里面的碎屑啥的都清理干净,要不然就像道路上有垃圾,会阻碍电流的通行。
接着就是电镀,这一步就像是给这些小孔穿上一层金属的衣服,让电流能够顺畅地通过。
这可需要精准的控制,多一点少一点都不行,不然就像衣服不合身,穿着难受。
再说说检测吧,这就像是给城市做体检,一点点小毛病都不能放过。
要是有个盲孔没做好,那整个电路板说不定就会出大问题,就像城市里的一个关键通道堵塞了,会引发一系列的混乱。
你想想,如果没有埋盲孔工艺,那些复杂的电路板能实现那么多功能吗?肯定不能啊!这小小的盲孔,可是在电路板的世界里发挥着大大的作用呢。
所以说,电路板埋盲孔工艺可真是一门高深的技术,需要精湛的技艺和严谨的态度。
只有把每个环节都做到极致,才能打造出完美的电路板,让我们的电子设备更加出色。
怎么样,是不是觉得这工艺很神奇?。
盲埋孔技术

埋盲孔技术
工艺能力 层次:18层max 最小孔径:0.10mm(激光钻孔) 0.15mm(机械钻孔) 厚径比:<12:1(机械钻孔),>0.75:1(激光钻孔)
埋盲孔技术
•埋盲孔设计建议
制作难度与成本,HDI激光埋盲孔板均高与多次层压埋盲孔 板.尽量避免设计交叠埋盲孔.
多次层压盲孔板
HDI激光孔板
埋盲孔技术
•埋盲孔板设计建议
1、金属化孔与线的连接 金属化孔通过焊盘与线连接: 设计焊环宽度=最小完成焊环宽度+孔位公差+蚀刻公差 焊盘直径=钻刀直径+2 x 最小完成焊环宽度+孔位公差+蚀刻公差 最小完成焊环宽度:0.025mm (IPC二级标准) 孔位公差:+/-0.075mm 蚀刻公差:+/-0.025mm 当间距允许时常以加泪滴盘的 方式保证焊盘与线的安全电气 连接。
埋盲孔技术
•埋盲孔板设计建议
空白区设计要点 –内层不要留大面积的基材区,否则板内应 力不均匀,易翘曲,压板时铜箔易起皱; –外层线路要尽量均匀,不要留大面积的基 材区(可用铺辅助无功能的方盘填充), 否则电镀不均,PTH孔径、线路铜厚会相差 较大。
大面积基材,NG
设置铜皮,OK
埋盲孔技术
•埋盲孔板设计建议
1、层结构最好为中心对称以防止因涨缩不一致导致PCB板严重翘曲。 2、尽量使用一种芯板厚度。 3、内层尽量使用一种铜厚,芯板两面铜厚尽量一致。 4、芯板与半固化片尽量使用常用规格。 5、埋孔孔径,建议0.30mm-0.50mm,过大或过小都不利于树脂塞孔; 6、埋盲孔最小焊环0.15mm,激光盲孔,最小焊环0.10mm
埋盲孔技术
•埋盲孔板设计建议
1、层结构最好为中心对称以防止因涨缩不一致导致PCB板严重翘曲。 2、尽量使用一种芯板厚度。 3、内层尽量使用一种铜厚,芯板两面铜厚尽量一致。 4、芯板与半固化片尽量使用常用规格。 5、埋孔孔径,建议0.30mm-0.50mm,过大或过小都不利于树脂塞孔; 6、埋盲孔最小焊环0.15mm,激光盲孔,最小焊环0.10mm
盲埋孔PCB的制作细节描述
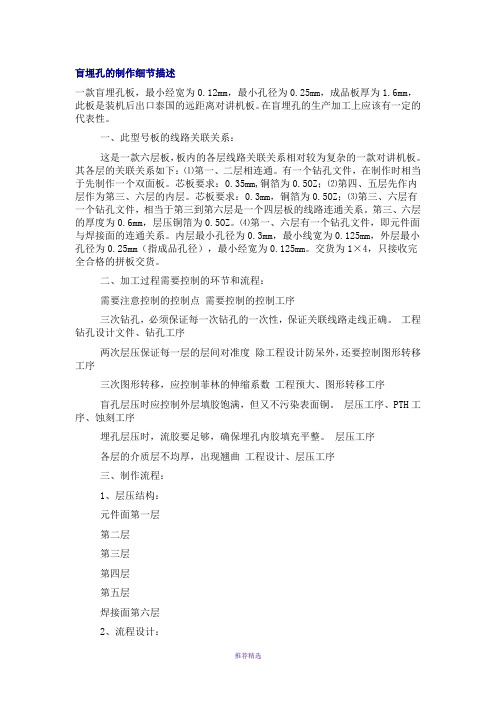
盲埋孔的制作细节描述一款盲埋孔板,最小经宽为0.12mm,最小孔径为0.25mm,成品板厚为1.6mm,此板是装机后出口泰国的远距离对讲机板。
在盲埋孔的生产加工上应该有一定的代表性。
一、此型号板的线路关联关系:这是一款六层板,板内的各层线路关联关系相对较为复杂的一款对讲机板。
其各层的关联关系如下:⑴第一、二层相连通。
有一个钻孔文件,在制作时相当于先制作一个双面板。
芯板要求:0.35mm,铜箔为0.5OZ;⑵第四、五层先作内层作为第三、六层的内层。
芯板要求:0.3mm,铜箔为0.5OZ;⑶第三、六层有一个钻孔文件,相当于第三到第六层是一个四层板的线路连通关系。
第三、六层的厚度为0.6mm,层压铜箔为0.5OZ。
⑷第一、六层有一个钻孔文件,即元件面与焊接面的连通关系。
内层最小孔径为0.3mm,最小线宽为0.125mm,外层最小孔径为0.25mm(指成品孔径),最小经宽为0.125mm。
交货为1×4,只接收完全合格的拼板交货。
二、加工过程需要控制的环节和流程:需要注意控制的控制点需要控制的控制工序三次钻孔,必须保证每一次钻孔的一次性,保证关联线路走线正确。
工程钻孔设计文件、钻孔工序两次层压保证每一层的层间对准度除工程设计防呆外,还要控制图形转移工序三次图形转移,应控制菲林的伸缩系数工程预大、图形转移工序盲孔层压时应控制外层填胶饱满,但又不污染表面铜。
层压工序、PTH工序、蚀刻工序埋孔层压时,流胶要足够,确保埋孔内胶填充平整。
层压工序各层的介质层不均厚,出现翘曲工程设计、层压工序三、制作流程:1、层压结构:元件面第一层第二层第三层第四层第五层焊接面第六层2、流程设计:工程设计时先开两个芯板,第一个芯板是1-2层,按第一个钻孔文件进行钻孔盲孔。
并按普通双面板的工艺流程制作到中检经过AOI存放;第二芯板是4-5层,开好一个芯板,按普通四层板的芯板制作工艺制作到中检经过AOI。
先将第二个芯板进行层压后,再按第二个钻孔文件钻埋孔,制作第3-6层的通孔和线路,此时按普通四层板的工艺经过除胶渣,制作3-6层的线路,到中检AOI。
盲埋孔制作规范
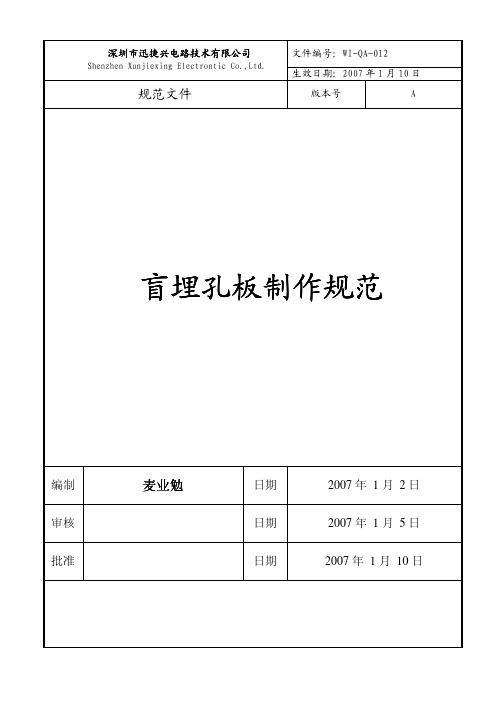
文件编号:WI-QA-012深圳市迅捷兴电路技术有限公司深圳市迅捷兴电路技术有限公司Shenzhen Xunjiexing Electrontic Co.,Ltd.生效日期:2007年1月10日规范文件版本号A盲埋孔板制作规范盲埋孔板制作规范编制麦业勉日期 2007年 1月 2日 审核 日期 2007年 1月 5日 批准日期2007年 1月 10日文件编号:WI-QA-012深圳市迅捷兴电路技术有限公司Shenzhen Xunjiexing Electrontic Co.,Ltd. 生效日期:2007年1月10日 文件名:盲埋孔板制作规范 第1页 共10页 版本号:A文件更改记录表文件更改记录表序号序号 更改内容更改内容版本号版本号 更改日期更改日期生效日期生效日期编写者编写者文件名:盲埋孔板制作规范 第2页 共10页 版本号:A 1.0 目的:为盲孔板(镭射盲孔和机械盲孔)及埋孔的制作建立规范,确保盲孔板的品质。
2.0 适用范围:适用于各类盲孔板内、外层生产流程制作及工程工具制作。
3.0 职责:工程部:负责生产流程制定以及生产工具制作;生产部:负责按此规范操作并结合工序规范的相关要求进行制作;品质部:工艺工程师负责工艺规范的制定及参数优化;品质工程师负责此类型板品质监控项目的制定并培训和监督QC员工的执行;计划部:负责相关工序的发外4.0 参考文件:各生产工序之工艺规范5.0 定义:HDI--- High Density Interconnection (高密度互连)定义:第一、凡凡机械凡孔,凡凡孔凡凡0.15mm(6mil)以下(大部分为盲孔),孔环(Annular Ring or Pad or Land)之环径凡0.25mm(10mil)以下者,称为Microvia 微导孔或微孔;第二、凡PCB具有微孔,且接点(Connection)密度凡130点/inch” 以上,布线密度凡117寸/inch” 以上者,称为HDI类PCB,其线宽/间距为3mil/3mil或更细更窄。
埋盲孔多层印制板制作技术
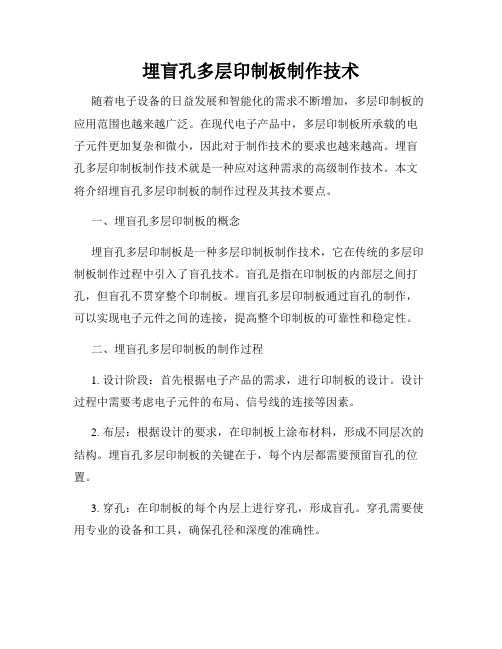
埋盲孔多层印制板制作技术随着电子设备的日益发展和智能化的需求不断增加,多层印制板的应用范围也越来越广泛。
在现代电子产品中,多层印制板所承载的电子元件更加复杂和微小,因此对于制作技术的要求也越来越高。
埋盲孔多层印制板制作技术就是一种应对这种需求的高级制作技术。
本文将介绍埋盲孔多层印制板的制作过程及其技术要点。
一、埋盲孔多层印制板的概念埋盲孔多层印制板是一种多层印制板制作技术,它在传统的多层印制板制作过程中引入了盲孔技术。
盲孔是指在印制板的内部层之间打孔,但盲孔不贯穿整个印制板。
埋盲孔多层印制板通过盲孔的制作,可以实现电子元件之间的连接,提高整个印制板的可靠性和稳定性。
二、埋盲孔多层印制板的制作过程1. 设计阶段:首先根据电子产品的需求,进行印制板的设计。
设计过程中需要考虑电子元件的布局、信号线的连接等因素。
2. 布层:根据设计的要求,在印制板上涂布材料,形成不同层次的结构。
埋盲孔多层印制板的关键在于,每个内层都需要预留盲孔的位置。
3. 穿孔:在印制板的每个内层上进行穿孔,形成盲孔。
穿孔需要使用专业的设备和工具,确保孔径和深度的准确性。
4. 镀铜:穿孔之后,进行镀铜处理。
镀铜可以加强盲孔的导电性能,以便实现电子元件之间的连接。
5. 压合:将各层印制板按照设计的布局进行压合。
这个过程需要严格控制温度和压力,以确保每个内层的位置和盲孔的对齐准确。
6. 孔壁镀铜:在压合之后,对盲孔的孔壁进行镀铜处理。
这一步可以提高盲孔的导电性能,保证电子元件之间的连接。
7. 最终加工:最后对印制板进行各种加工处理,如打磨边缘、光刻、阻焊等。
这些步骤可以增加印制板的耐久性和稳定性。
三、埋盲孔多层印制板制作技术的优势1. 提高可靠性:通过盲孔的制作,可以减少电子元件之间的接触电阻,提高电路的可靠性。
盲孔的制作还能够减少电子元件的封装面积,提高组装密度。
2. 节省空间:埋盲孔多层印制板可以在有限的空间内实现更多的电子元件的布局,避免了印制板的扩大,节省了电子产品的体积。
有关盲孔埋孔制作工艺
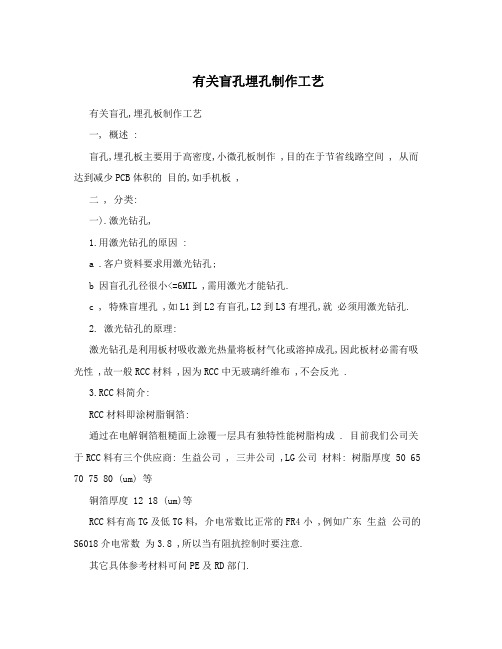
有关盲孔埋孔制作工艺有关盲孔,埋孔板制作工艺一, 概述 :盲孔,埋孔板主要用于高密度,小微孔板制作 ,目的在于节省线路空间 , 从而达到减少PCB体积的目的,如手机板 ,二 , 分类:一).激光钻孔,1.用激光钻孔的原因 :a .客户资料要求用激光钻孔;b 因盲孔孔径很小<=6MIL ,需用激光才能钻孔.c , 特殊盲埋孔 ,如L1到L2有盲孔,L2到L3有埋孔,就必须用激光钻孔.2. 激光钻孔的原理:激光钻孔是利用板材吸收激光热量将板材气化或溶掉成孔,因此板材必需有吸光性 ,故一般RCC材料 ,因为RCC中无玻璃纤维布 ,不会反光 .3.RCC料简介:RCC材料即涂树脂铜箔:通过在电解铜箔粗糙面上涂覆一层具有独特性能树脂构成 . 目前我们公司关于RCC料有三个供应商: 生益公司 , 三井公司 ,LG公司材料: 树脂厚度 50 65 70 75 80 (um) 等铜箔厚度 12 18 (um)等RCC料有高TG及低TG料, 介电常数比正常的FR4小 ,例如广东生益公司的S6018介电常数为3.8 ,所以当有阻抗控制时要注意.其它具体参考材料可问PE及RD部门.4. 激光钻孔的工具制作要求:A).激光很难烧穿铜皮,故在激光钻孔前要在盲孔位蚀出跟完成孔径等大的Cu Clearance .B). 激光钻孔的定位标记加在L2/LN-1层,要在MI菲林修改页注明。
C).蚀盲孔点菲林必须用LDI制作,开料要用LDI板材尺寸。
5.生产流程特点:A). 当线路总层数为N , L2—Ln-1 层先按正常板流程制作完毕, B). 压完板,锣完外围后流程改为:--->钻LDI定位孔--->干膜--->蚀盲孔点--->激光钻孔--->钻通孔 --->沉铜----(正常工序)。
6.其他注意事项:A).由于RCC料都未通过UL认证,故此类板暂不加UL标记. B).关于MI上的排板结构, 为避免把此类含RCC料排板当假层板排板(因为菲林房制做菲林假层板和正常板有别) ,我们在画排板结构时,要注意RCC料与L2或Ln-1层分开,例如SR2711/01排板:C).IPC-6016是HDI板标准:激光盲孔孔壁铜厚:0.4mil(min).焊锡圈要求 :允许相切如果PAD尺寸比孔径大5mil以下,要建议加TEARDROPD).板边>=0.8”二).机械钻盲/埋孔:1.适用范围:钻嘴尺寸>=0.20mm时可考虑用机械钻孔;2.关于盲埋孔的电镀方法(参照RD通告TSFMRD-113): A).正常情况下,任何层线路铜面只可1次板电镀+1次图形电镀; B). 正常情况下,全压板流程完成后,板厚>=80MIL ,通孔需板电镀+图形电镀,因此, 盲孔电镀时外层板面不能板电镀.C).满足上述两条件后,盲孔的电镀按如下方法进行:I).外层线路线宽度大于6MIL ,且通孔板厚小于80MIL时,在盲孔电镀中外层板面可整板电镀II).外层线路线宽大于6MIL , 但通孔板厚大于80MIL时,在盲孔电镀中外层板面需贴膜保护板面;III).外层线路线宽小于6MIL , 且通孔板厚>=80MIL时,在盲孔电镀中外层板面需贴膜保护板面;3. 贴膜的方式:1) 盲孔纵横比<=0.8 (L/D)时,外层板面贴干膜整板曝光,内层盲孔板面整板电镀 , 2) 盲孔纵横比>0.8时(L/D) 时,外层板面贴干膜盲孔曝光, 需制作电镀曝点菲林或LDI曝光 ,内层盲孔板面整板电镀.4. 盲孔曝点的方法:1) 盲孔<=0.4MM (16MIL)时,用LDI曝盲孔,2) 盲孔>0.4MM (16MIL)时,用菲林曝盲孔,5. 埋孔贴膜方式 :1) 当埋孔面的线宽<=4MIL时,埋孔板面需贴膜曝点,2) 当埋孔面的线宽>4MIL时 , 埋孔板面直接板电镀 ,6. 注意事项 :1) 纵横比中 L/D : L=介质厚+铜厚 , D=盲孔/埋孔直径 .2) 盲孔/埋孔电镀菲林 : * 曝光点的直径D=D-6 (MIL) .*曝光点菲林加对位点 , 其坐标与外围参考孔一致 . 3) 需贴膜的盲孔在电镀时一般使用脉冲电流 (AC) .三.盲孔板需注意的一些特别要求 :1.树脂塞盲孔: 当埋孔尺寸较大时并且孔数较多, 压板时, 填满埋孔需要很多树脂, 为防止其影响压板厚度, 经R&D要求时, 可在压板前用树脂将埋孔预先塞住, 塞孔方式应可参照绿油塞孔.2. 外层有盲孔时 ,a. 因压板时外层会有胶流出 ,所以在压板后需要有一除胶工序;b. 因外层干膜前会清洁板面,有一磨板工序,化学沉铜很薄,仅 0.05MIL 到0.1MI 故很容易在磨板时磨掉, 所以我们会加一板电镀工序,加厚铜.其相关工序如 : 压板除胶钻孔沉铜板电镀干膜图形电镀 .3. 另外在做层数高的盲孔板时可能会到用PIN-LAM压板,但要注意只有 CORE 的厚度小于30MIL时, 我们的机器才能打PIN-LAM孔 , 例如 : PR4726010 ,我们用的就是普通压板 .4. 关于盲孔板板边 ,考虑有多次压板 ,及工艺孔较多 ,所以尽量把板边留到0.8”以上.5. 在写LOT卡时 ,关于副流程 ,即要写单个副流程的排板结构 ,还要在特别要求里写上主流程的排板结构 ,为的是方便下面工序.6. 在写LOT卡时 , 在有盲孔干膜是放在内层做或外层做,举例说明一下 :L 1L 2A如CORE的A厚度大于12MIL(不含铜厚) , 就放到外层做 , 如CORE的A厚度小于12MIL(不含铜厚) , 就放到内层做 ,。
盲埋孔制作工艺
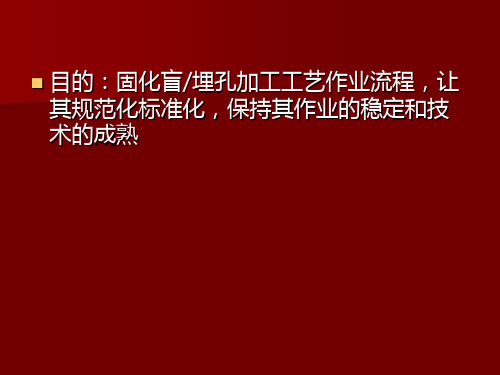
a:与通孔相对而言,通孔是指各层均钻通 的孔,盲孔则是非钻通孔。 b:盲孔细分:盲孔(BLIND HOLE),埋孔 BURIED HOLE(外层不可看见); c:从制作流程上区分: 盲孔在压合前钻 孔,而通孔是在压合后钻孔。 流程 略
工艺及控制要点内容: 工程文件的制作:工程文件制作时,注意 设臵好层间对位孔,否则在对位时会出现 配对错误的情况。甚至不能分辩哪一层是 哪一层。建议采用:第二层有两个识别点, 第三层有三个识别点,依次类推…菲林上 的识别点与钻孔文件一致。
外层线路 台面、米拉、菲林的清洁及菲林的使用寿 命需严格控制,详细执行《细密线路操作 规范》
图形电镀 特别强调内层图形电镀:内层图形电镀: 1.内层最好放在一个飞巴两个整流器, 单面给电流,同方向上挂具,光铜面统一 给2.0ASD打电流,另一面按1.2ASD的电流 电镀60分钟,确保孔铜厚12-15微米。
2.拷贝菲林时药膜面不能拷反,一旦 拷贝反,则线路关联全部倒臵。其次是对 位时看清楚对位识别孔,不能“张冠李 戴”,始终掌握看对位标识点就可避免对 错层数的现象。
3.内层芯板薄,依照公司薄板的工艺流程。 控制板面不要有折痕。板面会给层压带来 局部填胶不满出现盲孔失效。
压合 棕化良好,充分考虑压合厚度、内层铜厚、 残铜率之间的关系,防止因为PP配臵不当 导致内层短路,并铆钉定位, 8曾以上盲 埋孔订单尽量选择销钉模板定位生产,防 止层偏及滑板,每次层压保证每一层的层 间对准度 除工程设计防呆外,还要控制图 形转移工序的对准度,压合时流胶要足够, 确保埋孔内胶填充平整。
内层 注意识别方向标识孔,区分层次进行内层 制作,切不可将层次制作错误,各层镜像 要特别留意,否则就将线路的关联关系全 部搞反,生产前全检菲林,并确保内层线 路重合完好,重合偏差小于0.05MM,菲林 需控制菲林的伸缩系数,排版12*12英寸以 上的,菲林须作适当的放大。
6层埋盲孔的工艺流程
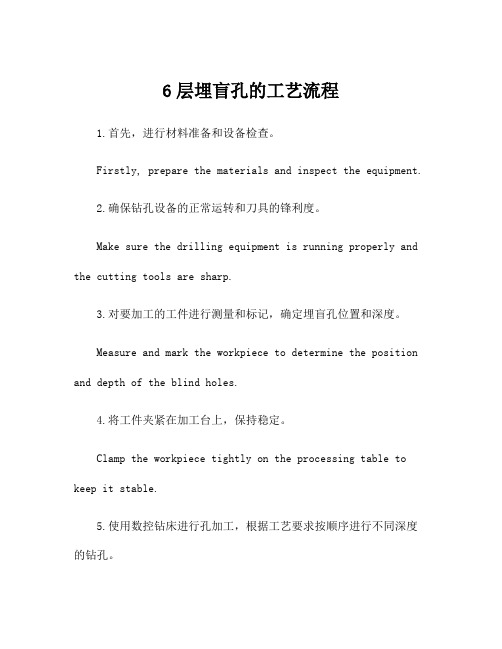
6层埋盲孔的工艺流程1.首先,进行材料准备和设备检查。
Firstly, prepare the materials and inspect the equipment.2.确保钻孔设备的正常运转和刀具的锋利度。
Make sure the drilling equipment is running properly and the cutting tools are sharp.3.对要加工的工件进行测量和标记,确定埋盲孔位置和深度。
Measure and mark the workpiece to determine the position and depth of the blind holes.4.将工件夹紧在加工台上,保持稳定。
Clamp the workpiece tightly on the processing table to keep it stable.5.使用数控钻床进行孔加工,根据工艺要求按顺序进行不同深度的钻孔。
Use the CNC drilling machine to process the holes,drilling the holes to different depths according to the process requirements.6.将加工后的工件进行清洁和检查。
Clean and inspect the processed workpiece.7.如果有残留的毛刺或异物,需要及时清理。
If there are any burrs or foreign objects remaining, they need to be cleaned up in time.8.对埋盲孔进行尺寸和深度的检验。
Inspect the dimensions and depths of the blind holes.9.用合适的工具检查埋盲孔的内部质量。
Inspect the internal quality of the blind holes with appropriate tools.10.确认埋盲孔的加工质量符合要求,进行记录和归档。
- 1、下载文档前请自行甄别文档内容的完整性,平台不提供额外的编辑、内容补充、找答案等附加服务。
- 2、"仅部分预览"的文档,不可在线预览部分如存在完整性等问题,可反馈申请退款(可完整预览的文档不适用该条件!)。
- 3、如文档侵犯您的权益,请联系客服反馈,我们会尽快为您处理(人工客服工作时间:9:00-18:30)。
盲埋孔板制作工艺规范1.0 目的:保证盲埋孔板生产流程设计的合理、以利于生产2.0适用范围:不同机械盲埋结构的盲埋孔板的制作方法3.0 职责:3.1工程部:负责对盲埋孔板的工艺流程及各参数工程的制定,ERP的编写。
3.2工艺部:负责评审埋盲孔板的制作能力和工艺参数。
3.3生产部:各生产工序按流程指示生产。
4.0 制作要求4.1检查客户文件,仔细分清客户的具体盲埋结构,按规范提供的结构模式设计制作4.2 确定各层所采用的正、负片效果,确定底片镜向的正确性以及底片编号指示的正确性4.3 各生产工序严格按照流程生产,仔细读明到序生产时的具体要求与注意事项4.4 工程制作4.4.1镀孔和掩孔流程的选择:4.4.1.1若是重复盲埋有同一层的,如L1-2、L1-3、L1-4等,则必须采用正片的效果,用镀孔工艺来完成线路图形与盲埋孔的制作。
4.4.1.2对于同一层线宽小于8mil要重复盲埋二次以上的必须采用镀孔工艺来完成,镀孔底片要比钻孔刀径大3mil。
4.4.1.3对于芯板直接层压的板,如果需要进行电镀流程,内层芯板可采用阴阳铜的设计流程。
4.4.1.4根据要求顾客要求铜厚,对于内层芯板的制作尽量采用掩孔电镀的方式一次性把铜厚镀够,减少镀孔流程带来的流程复杂。
例如对于铜厚要求35um,可采用18um的基铜,开料需减薄至10-12um;对于铜厚要求70um,可采用35um 的基铜直接采用掩孔电镀的方式。
4.4.1.5对于不是重复盲埋同一层的如L12、L34、L56….可采用负片效果,直接成像蚀刻压合,此时采用的直接板面电镀完工成盲埋孔的制作,所以要求铜厚进行减溥后才进行钻孔。
4.4.1.6镀孔菲林的设计需要在附边设计定位孔,以保证镀孔干膜对位的准确度。
4.4.2菲林命名:根据盲埋孔的结构将各层命名。
工程在制作资料时,在GENESIS 软件中的命名如下:4.4.2.1假如现在1、2层有机械盲孔,我们将1、2层开一张料,那么现在线路层的命名就是“CS、—2b”。
也就是说我们要根据盲埋结构来判断层的命名是“T”还是“B”。
其实“T”就是“TOP”,“B”就是“Bottom”,这样命名主要是为了在输出光绘文件时确保镜像关系正确。
4.4.2.2镀孔菲林的命名采用“DK+层名+T/B”的格式:1-2层需要镀孔,那CS 面的镀孔菲林命名为:DK1-2T,SS面的就为:DK1-2B。
4.4.2.3辅助菲林:“FZ+层”,例如:现在1、2开一张料,只要做出第2层线路,那么就需要通过第一层的辅助菲林那做第二层的线路,辅助菲林的命名就为:FZ1-2。
镀孔菲林和辅助菲林的属性都是MISC的属性;4.4.2.4盲埋的钻带命名为:DRL+层,例如1-2层的钻带,命名就为:DRL1-2,属性还是BOARD中钻孔属性。
4.4.3干膜封孔要求:采用干膜封孔蚀刻必须保证有5mil以上的封孔环。
4.4.4靶位孔设计要求:因采用的是传统的制作方法,其涉及多次的压合与钻孔,这就要求分次采用不同的定位孔来管制定位,所以必须每次采用不同的定位孔来做钻孔的定位。
依据所需钻孔的次数来确定定位孔数目在二层专用的靶位底片,第一次全做好,以后逐次使用。
各层相应位置不能有阻流点,影响其冲靶位孔的效果。
4.4.4.1根据钻孔顺序,把第一次钻孔的线路层定义为对位层,定位孔设计位于此层,第一次全做好,以后逐次使用。
4.4.4.2所有芯板的第一次线路层均需要设计所有定位靶标,此层也就是对位层,其他层不用设计而且在对应的靶位处需掏铜处理。
4.4.4.3附边共设计四套钻孔用定位孔和层压用铆合孔,具体设计如下图:4.4.4.4靶标设计如下图:A、方形靶标为通用靶标,其中“数字序号”靶位用于不同钻孔次数用,“英文序号”靶位用于不同次数层压用。
B、圆形靶标为备用靶标,分别为钻孔和层压保留一套,用于打错靶位补救用。
C、方形靶位和圆形靶标设计示意图4.4.4.5生产中根据层压和钻孔的次数根据序号依次选择铆合孔和定位孔。
其中“A、B、C、D”为层压用铆合孔,“1、2、3、4”为钻孔用定位孔。
4.4.4.6其他工艺边的相关要求不做调整。
4.4.5阻焊层制作:在制作喷锡板的盲孔时,要将盲孔对应的阻焊开窗删除,避免喷锡时孔被锡堵住。
4.4.6辅助菲林的设计:4.4.6.1辅助菲林与附边定位孔对应的位置需要淘铜设计为基材区。
4.4.6.2辅助菲林为了便于对于需要在附边设计对位孔,同时需要在层压用和钻孔用铆合孔对应的位置标注好序号,以便于生产时识别。
4.4.6.3辅助菲林同时需要注意板边干膜碎,板边需做3mm的掏铜区。
4.4.7菲林夹边:4.4.7.1无盲埋孔设计的芯板其线路菲林制作时需要进行夹边。
4.4.7.2资料室根据工程的指示进行夹边。
4.4.8内层线路菲林拉伸补偿:芯板拉伸系数以普通刚性板以普通刚性板为准,如果有不同芯板厚度,拉伸系数统一采用最大拉伸系数。
4.4.9拼板:对于埋盲孔的制作,最大拼板尺寸为16英寸。
4.5制作能力:4.5.1非交叉盲埋结构,有交叉盲埋结构的目前公司无法生产。
如图所示4层板盲埋结构无法生产:4.5.2三次层压钻孔制作,超此能力需提出评审。
4.5.3最小盲埋结构芯板厚度要求>0.13mm。
4.5.4层数小于等于8层,超过此结构需要评审,具体参考6.0中内容。
4.5.5盲埋孔板叠层对程翘曲度≥0.7%,对于叠层不对称翘曲度≥1.0%。
4.6其他工程制作要求参考《CAM制作规范》。
5.0生产制作5.1各序按ERP生产流程指示进行生产。
5.2各层制作需核对相应的板厚和铜厚,确认底片,仔细检查其编号的正确性。
5.3板面电镀参数:根据厚径比采用18ASF、20分钟或16ASF、30分钟电流参数。
5.4镀孔参数:参考《图形电镀工艺规范》中关于镀孔板的要求,首板确认铜厚。
5.5镀孔后打磨:采用360目的砂纸打磨,打磨至与铜面平即可,防止打磨过度,然后过火山灰磨板机,为了去掉打磨到孔内的杂物和均匀磨平板面。
5.6层压:5.6.1对于盲孔板在层压时需要采用铜箔保护,用铜箔光面盖住盲孔面,防止流胶到钢板上,方便层压后离型。
5.6.2对于经过电镀后的芯板在棕化后层压前120度烘板1个小时。
5.6.3层压后的板需要进行退应力,要求150度4个小时。
5.7除胶:用98%的浓硫酸擦洗,30S—60S,要求:不要除胶过度,孔内的胶与孔平。
5.8去毛刺:如果是单面盲孔,去毛刺时要有盲孔的一面朝下,主要是为了使盲孔中的钻污祛除的更彻底。
5.9电镀孔壁铜厚确认:镀孔、掩孔电镀、图形电镀后,要求最小铜厚20um,平均23um。
5.10蚀刻工序要认真做好首板因铜厚通过板面电镀有不均的现象5.11检查时用干膜盖住的大铜面不通有露铜点、盲孔偏破不要理会。
5.12字符时要仔细对位确认,因不同的盲埋结构其板曲不一样,易出现偏位上焊盘。
6.0各种板的盲埋结构及工艺流程6.1三层板6.1.1第一种结构工艺流程:开料(L1/2)、钻孔(L1/2)、去毛刺、沉铜、板面电镀、镀孔干膜、镀孔、退膜、打磨、火山灰磨板、内层图形(L1/2)、内层蚀刻、内层AOI、棕化、层压(L1/3)、除胶、钻孔(L1/3)、正常流程6.2四层板6.2.1第一种结构工艺流程:开料、钻孔(L1-2、L3-4)、去毛刺、沉铜、板面电镀、镀孔干膜(L1-2、L3-4)、镀孔、退膜、打磨、火山灰磨板、内层干膜(L2、L3)、内层蚀刻、内层AOI、棕化、层压、除胶、钻孔(L1-4)、正常流程6.2.2第二种结构工艺流程:开料、钻孔(L1-2)、去毛刺、沉铜、板面电镀、镀孔干膜、镀孔、退膜、打磨、火山灰磨板、内层图形(L2)、内层蚀刻、内层AOI、棕化、层压、除胶、钻孔(L1-3)、去毛刺、沉铜、板面电镀、镀孔干膜、镀孔、退膜、打磨、火山灰磨板、内层图形(L3)、内层蚀刻、内层AOI、棕化、层压(L1-4)、除胶、钻孔、正常流程6.2.3第三种结构工艺流程:开料、钻孔(L2-3)、去毛刺、沉铜、板面电镀、内层图形、内层蚀刻、正常流程6.3六层板结构6.3.1第一种结构工艺流程:(1)L1-2、L5-6制作流程:开料、钻孔(钻L1-2、L5-6)、去毛刺、沉铜、板面电镀、镀孔干膜(L1-2、L5-6),镀孔、退膜、打磨、火山灰磨板、内层干膜(L2、L5),内层蚀刻、内层AOI、棕化、(2)L3-4制作流程:开料、内层干膜(L3-4)、内层蚀刻(L3-4)、内层AOI、棕化(3)L1-6制作流程:层压、除胶、钻孔、正常流程。
6.3.2第二种结构工艺流程:开料、内层干膜(L2、L5)、内层蚀刻、内层AOI、棕化、层压、钻孔(L1-3、L4-6)、去毛刺、沉铜、板面电镀、镀孔干膜、镀孔、退膜、打磨、火山灰磨板、内层干膜(L3、L4)、内层蚀刻、内层 AOI、棕化、层压、除胶、钻孔、正常流程6.3.3第三种结构工艺流程:开料、钻孔(L2-3、L4-5)、去毛刺、沉铜、板面电镀、镀孔干膜、镀孔、退膜、打磨、火山灰磨板、内层图形(L2-3、L4-5)、内层蚀刻、内层AOI、棕化、层压、正常流程6.3.4第四种结构:工艺流程:开料、钻孔(L2-3、L4-5)、去毛刺、沉铜、板面电镀、镀孔干膜、镀孔、退膜、打磨、火山灰磨板、内层干膜(L3、L4)、内层蚀刻、内层AOI、棕化、层压(L2-5)、除胶、钻孔(L2-5)、去毛刺、沉铜、板面电镀、外层成像(L2、L5)、图形电镀、外层蚀刻、AOI、棕化、层压、正常流程。
6.3.5第五种结构(制作需要评审)工艺流程:开料、钻孔(L1-2)、去毛刺、沉铜、板面电镀、镀孔干膜(L1-2)、镀孔、退膜、打磨、火山灰磨板、内层干膜(L2)、内层蚀刻、内层AOI、棕化、层压(L1-3)、除胶、钻孔(L1-3)、去毛刺、沉铜、板面电镀、镀孔干膜(L1-3)、镀孔、退膜、打磨、火山灰磨板、内层干膜(L3)、内层蚀刻、内层AOI、棕化、层压(L1-4)、除胶、钻孔(L1-4)、去毛刺、沉铜、板面电镀、镀孔干膜(L1-4)、镀孔、退膜、打磨、火山灰磨板、内层干膜(L4)、内层蚀刻、内层AOI、棕化、层压(L1-5)、除胶、钻孔(L1-5)、去毛刺、沉铜、板面电镀、镀孔干膜(L1-5)、镀孔、退膜、打磨、火山灰磨板、内层干膜(L5)、内层蚀刻、内层AOI、棕化、层压、除胶、钻孔、正常流程。
6.3.6第六种结构工艺流程:(1)L1-2和L5-6制作流程:开料、钻孔(L1-2、L5-6)、去毛刺、沉铜、板面电镀、镀孔干膜(L1-2、L5-6)、镀孔、退膜、打磨、火山灰磨板、内层干膜(L2、L5)、内层蚀刻、内层AOI、棕化、(2)L3-4制作流程:开料、钻孔(L3-4)、去毛刺、沉铜、板面电镀、镀孔干膜(L3-4)、镀孔、退膜、打磨、火山灰磨板、内层干膜(L3-4)、内层蚀刻、内层AOI、棕化(3)L1-8制作流程:层压(L1-8)、除胶、钻孔、正常流程6.4八层板结构6.4.1第一种结构工艺流程:开料、内层干膜(L2-3、L6-7)、内层蚀刻、内层AOI、棕化、层压(L1-4、L5-8)、钻孔(L1-4、L5-8)、去毛刺、沉铜、板面电镀、镀孔干膜(L1-4、L4;L8-5、L5)、镀孔、退膜、打磨、火山灰磨板、内层干膜(L4、L5)、内层蚀刻、内层AOI、棕化、层压、除胶、钻孔、正常流程6.4.2第二种结构:工艺流程:开料、钻孔(L1-2、L3-4、L5-6、L7-8)、去毛刺、沉铜、板面电镀、镀孔干膜(L1-2、L3-4、L5-6、L7-8)、镀孔、退膜、打磨、火山灰磨板、内层干膜(L2、L3、L6、L7)、内层蚀刻、内层AOI、棕化、层压(L1-4、L5-8)、除胶、钻孔(L1-4、L5-8)、去毛刺、沉铜、板面电镀、镀孔干膜(L1-4、L5-8)、镀孔、退膜、打磨、火山灰磨板、内层干膜(L4、L5)、内层蚀刻、内层AOI、棕化、层压、除胶、钻孔、正常流程。