钢结构智能工厂,SBA-H型钢智能装配焊接生产线
高端钢材智能制造工厂建设方案

高端钢材智能制造工厂建设方案
随着制造业的不断发展,高端钢材的需求量不断增加。
为了满足市场需求并提高生产效率,建设一座高端钢材智能制造工厂成为了必然选择。
首先,在工厂的选址上,需要选择一个地理位置优越且交通便利的地点。
这样可以方便原材料的供应和成品的运输。
此外,工厂周边应具备完善的基础设施和配套服务,确保生产运营的顺利进行。
其次,针对高端钢材的特殊生产需求,工厂应配备先进的智能制造设备和技术。
例如,高精度的数控机床、自动化生产线以及智能化的物流系统等。
这些设备和技术可以大幅提高生产效率和产品质量,使工厂具备更高的竞争力。
第三,人工智能技术在高端钢材制造中的应用也不可忽视。
通过引入人工智能算法和机器学习技术,可以对生产过程进行精准监测和优化,提高生产过程的稳定性和可靠性。
同时,智能化的数据分析系统可以提供对生产数据的实时监控和分析,帮助企业及时做出决策和调整。
此外,为了确保工厂的可持续发展,环境保护和资源利用也应成为建设工厂的重要考虑因素。
工厂应采用清洁能源,减少对环境的污
染。
同时,回收再利用废料和废水,最大限度地减少资源浪费。
最后,为了促进工厂的发展,政府和企业应加强合作,提供相关支持和政策激励。
例如,通过减税、提供补贴或贷款支持等方式,鼓励企业投资于智能制造技术和设备的引入。
总之,高端钢材智能制造工厂的建设方案需要综合考虑选址、设备、技术、环境和政策等多个因素。
只有通过合理规划和科学管理,才能实现高效、高质量的生产,满足市场需求,并为企业带来可持续的发展。
H型钢生产线介绍
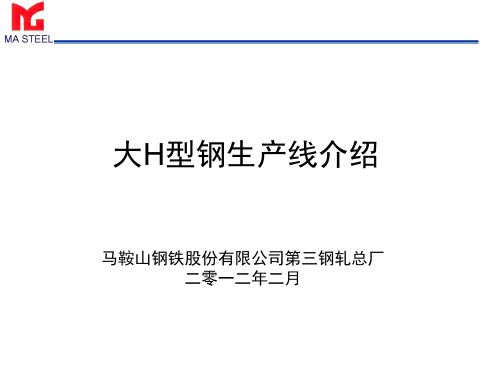
1.4 工艺流程
什么叫格林法 格林法的主要特点是采用开门式万能孔型,腰和腿部的加工是在开口式万 能孔型中同时进行的。为有效地控制腿高和腿部加工的质量,格林法认为立压 必须作用在腿端,故把腿高的压缩放在与万能机架一起连轧的二辊式机架中进 行。目前世界各国的轧边机多采用格林法。 采用格林法轧制H型钢其工艺大致如下:二辊式开坯机把钢锭轧成异形坯, 然后把异形坯送往万能粗轧机和轧边机进行往复连轧,并在万能粗轧机和轧边 机上往复连轧成成品。格林法在进行立压时只是用水平辊与轧件腿端接触(腰 部与水平辊不接触),这可使轧件腿端始终保持平直。这种方法其立辊多为圆 柱形,而水平辊两侧略有斜度,在粗轧机组中,水平辊侧面有约5度的斜度。在 精轧机组中水平辊侧面有2%~5%斜度,不过精轧机组水平辊侧面斜度应尽量 小,才能轧出平行的腿部。
500 140 1 400 1500 13 1.25
1.5 主要设备及工艺参数
万能轧机 共有三架万能轧机,两架 可逆式万能粗轧机U1和U2,一架 万能精轧机UF,其中U1、U2结构 完全一样,UF因采用了AGC,有 关参数作相应变化。机架形式为 开轭闭口式,万能轧机由两根水 平辊和两根立辊组成,水平辊为 主动辊,立辊为从动辊。既可以 轧制H型钢,也可以利用两辊轧 制普通型钢。
HW400×300
HW300×300
HW300×300
1.5 主要设备及工艺参数
开坯机孔型
1.5 主要设备及工艺参数
1.5 主要设备及工艺参数
1.5 主要设备及工艺参数
开坯机孔型设计 在设计开坯机孔型时, 需要兼顾坯料尺寸及成品规格的要求。 开坯机成型孔孔型设计: (1) 成型孔腹板厚度设计 开坯机成型孔腹板厚度的设计, 应兼顾万能区域腹板翼缘延伸关系、开坯机孔型数目、 开坯机及万能区域生产节奏等多方面因素的影响。 万能区域腹板翼缘延伸关系: 开坯机成型孔翼缘厚度/ 开坯机成型孔腹板厚度: 成品翼缘厚度/ 成品腹板厚度= 0.9~1.5∶1。对于成品轧件翼缘宽度较宽, 需要在万能区域给予一定不均匀变形来 强迫展宽的H 型钢产品, 选上限; 对于成品翼缘宽度较窄, 且生产中较易出现翼缘波 浪等缺陷的, 选下限。 (2) 开坯机成型孔平均翼缘厚度设计 根据成型孔轧件腹板厚度及万能区域腹板翼缘延伸关系, 确定开坯机成型孔平均翼缘 厚度及开坯机所需要的孔型数。一般孔型侧压量设计为5~20mm。 (3) 开坯机成型孔开槽深度设计在设计开坯机成型孔开槽深度时, 应考虑万能区域腹 板翼缘延伸关系、成品材深度等因素。成品材深度与开坯机成型孔槽深度之差为0 ~30mm。
智能焊接生产线技术研发方案(一)
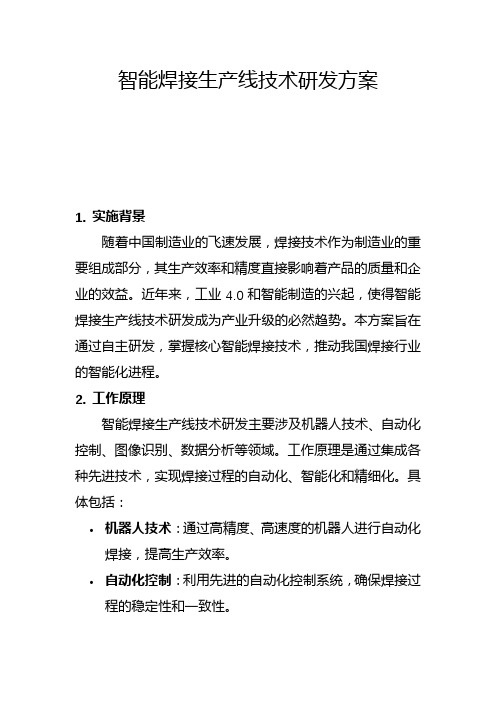
智能焊接生产线技术研发方案1. 实施背景随着中国制造业的飞速发展,焊接技术作为制造业的重要组成部分,其生产效率和精度直接影响着产品的质量和企业的效益。
近年来,工业4.0和智能制造的兴起,使得智能焊接生产线技术研发成为产业升级的必然趋势。
本方案旨在通过自主研发,掌握核心智能焊接技术,推动我国焊接行业的智能化进程。
2. 工作原理智能焊接生产线技术研发主要涉及机器人技术、自动化控制、图像识别、数据分析等领域。
工作原理是通过集成各种先进技术,实现焊接过程的自动化、智能化和精细化。
具体包括:•机器人技术:通过高精度、高速度的机器人进行自动化焊接,提高生产效率。
•自动化控制:利用先进的自动化控制系统,确保焊接过程的稳定性和一致性。
•图像识别:通过机器视觉技术,对焊缝进行高精度识别和定位,确保焊接质量。
•数据分析:通过对大量焊接数据的分析,优化焊接参数,提高产品质量。
3. 实施计划步骤1.建立研发团队,明确研发目标。
2.进行技术调研,掌握市场需求和竞争对手情况。
3.制定研发计划,明确阶段性目标和时间节点。
4.进行技术研发,包括硬件设计、软件开发和系统集成等。
5.进行原型测试和优化,确保技术的稳定性和可行性。
6.与企业合作,进行生产现场测试,验证技术的实际效果。
7.根据测试结果进行优化和完善,推广应用。
4. 适用范围本技术研发方案适用于汽车制造、航空航天、轨道交通、管道施工等领域的焊接生产。
同时,对于中小型企业而言,通过引入智能焊接生产线技术,可以提高生产效率、降低成本、提升产品质量,增强市场竞争力。
对于大型企业,则可以进一步提高生产过程的可控性、降低质量波动、提高生产效率,从而大大提升企业的综合效益。
5. 创新要点•集成多种技术:本方案通过集成机器人技术、自动化控制、图像识别和数据分析等多种技术,实现了焊接过程的全面智能化和自动化。
•数据驱动优化:通过对大量焊接数据的分析,可以持续优化焊接参数,提高产品质量和生产效率。
固建机器人建筑钢结构智能生产线详情
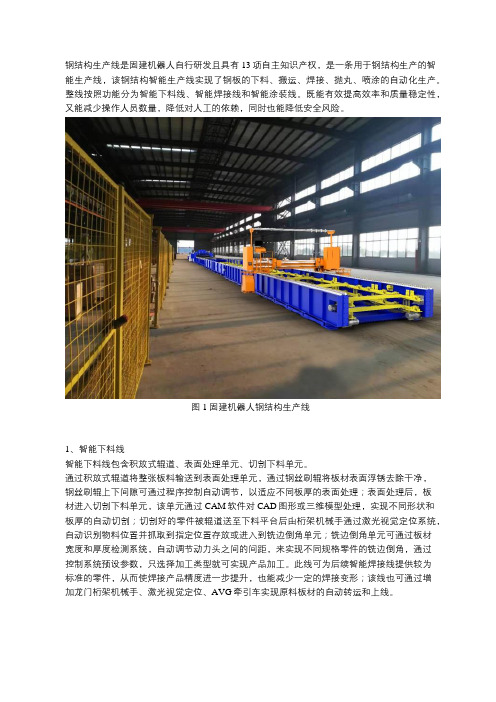
钢结构生产线是固建机器人自行研发且具有13项自主知识产权,是一条用于钢结构生产的智能生产线,该钢结构智能生产线实现了钢板的下料、搬运、焊接、抛丸、喷涂的自动化生产。
整线按照功能分为智能下料线、智能焊接线和智能涂装线。
既能有效提高效率和质量稳定性,又能减少操作人员数量,降低对人工的依赖,同时也能降低安全风险。
图 1固建机器人钢结构生产线1、智能下料线智能下料线包含积放式辊道、表面处理单元、切割下料单元。
通过积放式辊道将整张板料输送到表面处理单元,通过钢丝刷辊将板材表面浮锈去除干净,钢丝刷辊上下间隙可通过程序控制自动调节,以适应不同板厚的表面处理;表面处理后,板材进入切割下料单元,该单元通过CAM软件对CAD图形或三维模型处理,实现不同形状和板厚的自动切割;切割好的零件被辊道送至下料平台后由桁架机械手通过激光视觉定位系统,自动识别物料位置并抓取到指定位置存放或进入到铣边倒角单元;铣边倒角单元可通过板材宽度和厚度检测系统,自动调节动力头之间的间距,来实现不同规格零件的铣边倒角,通过控制系统预设参数,只选择加工类型就可实现产品加工。
此线可为后续智能焊接线提供较为标准的零件,从而使焊接产品精度进一步提升,也能减少一定的焊接变形;该线也可通过增加龙门桁架机械手、激光视觉定位、AVG牵引车实现原料板材的自动转运和上线。
图 2固建机器人钢结构生产线-智能下料线2、智能焊接线智能焊接线包含框架组立单元、框架焊接单元、整形矫正单元、下料单元、辅件焊接单元。
单个零件通过积放式辊道将不同零件安顺序送入组立单元后,夹紧机构将其加紧后根据主体框架形状旋转角度,完成组装后可由光构相机检测各零件之间的间隙,如有异常,夹紧机构可实现自动调节,确保间隙均匀、对称,可有效减少焊接变形,组装完成后焊接机器人开始埋弧焊接(包含点焊和满焊),同时通过激光焊缝跟踪,对偏离轨迹自动修正,确保焊接质量稳定;由于焊接变形较大,在焊接辅件之前需要通过液压整形矫正;整形完成后积放式辊道将框架主体输送到指定位置,由下料单元裁成不同长度,然后准备辅件的焊接;搬运机器人通过激光视觉系统自动寻找并识别辅件;将各个辅件依次抓取至指定位置并焊接,搬运机器人上的抓取夹具可根据不同的辅件安装方式和形状实现夹具的自动快速更换(类似加工中心刀具自动更换)。
焊接材料工厂智能化转型案例

焊接材料工厂智能化转型案例焊接材料工厂智能化转型案例:1. 传统焊接材料工厂面临的挑战:随着市场竞争的加剧和消费者需求的多样化,传统的焊接材料工厂面临着生产效率低下、质量不稳定、环境污染严重等问题。
为了适应市场的变化和满足环保要求,焊接材料工厂需要进行智能化转型。
2. 智能化转型的措施:引入智能制造技术:焊接材料工厂引入智能制造技术,如工业互联网、物联网、大数据、人工智能等,实现生产过程的自动化和智能化。
这包括自动化生产线、智能仓储系统、智能物流系统等。
建立数字化工厂:通过数字化技术,实现工厂的数字化建模、仿真和优化。
这有助于提高生产效率、减少能耗和排放,提高产品质量和降低成本。
引入环保技术:焊接材料工厂引入环保技术,如废气处理、废水处理等,实现清洁生产和绿色制造。
这有助于降低环境污染,满足环保要求。
建立智能化管理体系:焊接材料工厂建立智能化管理体系,实现生产过程的可视化、可追溯和可预测。
这有助于提高管理效率和生产效率,降低运营成本。
3. 转型效果:通过智能化转型,焊接材料工厂实现了生产效率的提高、质量稳定性的提高、能耗和排放的降低以及环境污染的减少。
同时,工厂的管理效率和生产效率也得到了提高,降低了运营成本。
这些变化使得焊接材料工厂更具市场竞争力,能够更好地满足消费者需求。
结论:智能化转型是焊接材料工厂适应市场变化和满足环保要求的必然选择。
通过引入智能制造技术和环保技术,建立数字化工厂和智能化管理体系,焊接材料工厂可以实现生产效率的提高、质量稳定性的提高、能耗和排放的降低以及环境污染的减少。
这将有助于提高焊接材料工厂的市场竞争力,促进其可持续发展。
型材(槽钢、扁钢、角钢)智能下料,焊接组合装备生产线技术方案
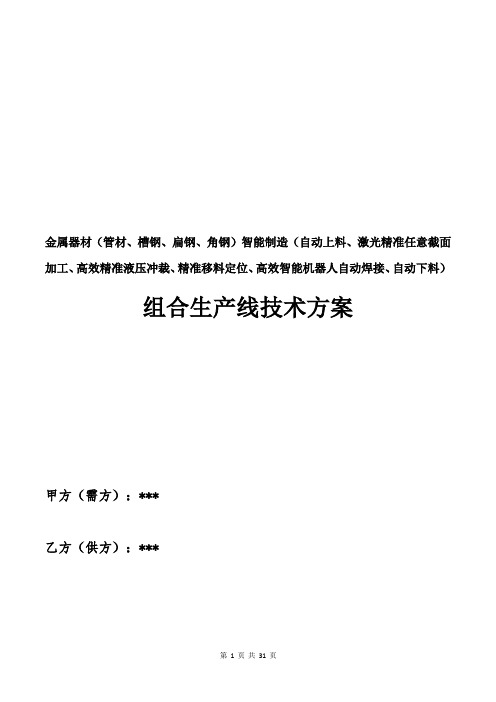
金属器材(管材、槽钢、扁钢、角钢)智能制造(自动上料、激光精准任意截面加工、高效精准液压冲裁、精准移料定位、高效智能机器人自动焊接、自动下料)组合生产线技术方案甲方(需方):***乙方(供方):***一、设备名称金属器材(管材、槽钢、扁钢、角钢)智能制造(自动上料、激光精准任意截面加工、高效精准液压冲裁、精准移料、定位、高效智能机器人自动焊接、自动下料)组合生产线产品图纸①:产品图纸②:◎产品要求:采用二氧化碳保护焊,焊缝高度不小于6mm。
需1人工将槽钢吊过来摆好后2个人使用挡板定长,人工送料后冲断。
1、每道工序需一至三名熟练工操作。
人工摆料、定尺、火焰切割。
2、裁口精度误差大、效率不一,下道工序无法实现自动化焊接,具有安全生产隐患。
(1人将冲断后的半成品转运,而后4人使用火焰割割断。
工件断面凹凸不平,尺寸偏差极大。
)需1人工核对清单,核对已加工数量。
槽钢加工智能化生产线工艺槽钢/扁钢/角钢全自动加工组合线传统生产工艺槽钢的传统加工工序共需7-8人,单片水平桁架槽钢的加工时间约为25分钟。
上下料工序对工人的体力消耗极大,有安全生产隐患。
自动化生产工艺将整包料放上储料装置后,1人操作本机即可实现自动化加工,单片水平桁架槽钢的加工时间约为5分钟,单人生产效率提升了35倍以上。
精准高效安全。
单人效率综合对比三、工艺对比人工离散生产工艺单人效率综合对比工件断面凹凸不平,尺寸偏差极大。
且需1人校对加工产品数量及类别。
1、每道工序需一至四名熟练工操作。
人工摆料、定尺、冲压。
2、送料精度误差大、效率不一,下道工序无法实现自动化焊接,具有安全生产隐患。
(需1人工将扁钢吊过来摆好后,需4人使用挡板定长,人工依次送料后冲断。
)需1人将冲断后的半成品转运,而后需2人操作两台冲床冲裁。
扁钢加工智能化生产工艺槽钢/扁钢/角钢全自动加工组合线传统生产工艺扁钢的传统加工工序共需6-7人,单片水平桁架所需4片扁钢的加工时间约为1.5分钟。
无人工厂中的自动化装配与生产线设计

无人工厂中的自动化装配与生产线设计自动化技术的快速发展正在引领着工业生产的革命性转变,无人工厂作为自动化领域的一项重要应用,在提高生产效率和降低人力成本方面具有巨大的潜力。
在无人工厂中,自动化装配与生产线设计起着关键的作用,本文将深入探讨这一主题,分析其背后的原理和实施方法。
一、自动化装配技术的原理与应用自动化装配技术是实现产品快速、高效装配的关键。
它通过引入智能机器人、传感器、视觉系统等先进设备,实现对零件的抓取、定位、拧紧等操作,完成产品组装的自动化过程。
在无人工厂中,自动化装配技术可以大幅度提高生产效率,减少人力投入,降低产品质量风险。
在自动化装配技术中,机器人是核心的执行器。
它们具有高度灵活性和精准性,可以根据预设的程序和算法,完成各种装配动作。
例如,柔性装配机器人可以根据产品不同的形状和尺寸,灵活调整夹爪的位置和力度,实现精准的零件抓取和组装。
而视觉系统则通过图像识别和图像处理,对产品零件进行检测和定位,保证装配过程的准确度和一致性。
除了机器人和视觉系统,自动化装配还离不开传感器技术的支持。
传感器可以实时感知装配过程中的力度、温度、压力等参数,并将这些数据反馈给控制系统,实现对装配过程的监控和调节。
通过传感器的智能化应用,可以实现装配过程的自适应和优化,提高产品质量和装配效率。
二、无人工厂生产线设计的关键考虑因素无人工厂的生产线设计需要综合考虑多个关键因素,包括生产效率、设备配置、流程优化等。
下面将分别进行探讨:1. 生产效率:无人工厂的目标是实现高效的自动化生产,因此生产线的设计应追求最大的生产效率。
这涉及到对产品工艺流程的深入分析和优化,合理划分工作站和任务分配,并借助仿真软件进行模拟和验证,找到最佳的生产线布局和工艺流程。
2. 设备配置:选择合适的设备对无人工厂的生产效率和产品质量至关重要。
在设计无人工厂的生产线时,需要充分考虑设备的稳定性、可靠性和适应性,以满足不同产品的装配要求。
钢结构制造中的自动化生产线

钢结构制造中的自动化生产线自动化生产线已经成为现代制造业中不可或缺的一部分,在钢结构制造领域也不例外。
随着科技的不断进步和自动化技术的成熟应用,钢结构制造中的自动化生产线已取得了显著的成果。
本文将就钢结构制造中自动化生产线的应用及其带来的优势进行探讨,并展望未来的发展趋势。
一、自动化生产线在钢结构制造中的应用在钢结构制造中,自动化生产线广泛应用于各个环节,包括材料加工、焊接、喷涂、装配等。
首先,自动化生产线在材料加工方面发挥了重要作用。
通过自动化设备对钢材进行切割、冲孔、弯曲等加工,可以提高生产效率和质量,并减少人力投入。
其次,自动化焊接系统在钢结构制造中起到了至关重要的作用。
传统的手工焊接不仅效率低下,质量难以保证,还存在一定的安全隐患。
而自动化焊接设备的应用,不仅可以提高焊接速度,还能够确保焊接质量和工人的安全。
再者,自动化喷涂系统可以提高喷涂效率和均匀度,减少喷涂环境对工人的伤害,确保钢结构的防腐蚀性能。
最后,自动化装配线可确保钢结构的准确拼装和良好的尺寸精度,提高生产效率和产品质量。
二、自动化生产线在钢结构制造中的优势引入自动化生产线在钢结构制造中具有诸多优势。
首先,自动化生产线可以提高生产效率。
相比于传统的手工操作,自动化设备能够实现连续、高速的加工和操作,大大提高了生产的效率。
其次,自动化生产线可以提高产品质量。
自动化设备的精度和稳定性较高,人工操作所引起的误差可以有效避免,从而保证产品的质量。
此外,自动化生产线还能够减少人力投入,缓解劳动力短缺的问题,并降低因工人操作不当而带来的安全隐患。
另外,自动化生产线还能够减少能源消耗和环境污染,提高工作环境的舒适度和安全性。
三、钢结构制造中自动化生产线的未来发展趋势随着科技的不断进步和自动化技术的不断发展,钢结构制造中的自动化生产线也在不断优化和升级。
未来,钢结构制造中的自动化生产线将呈现以下几个发展趋势。
首先,智能化将成为自动化生产线的主流。
- 1、下载文档前请自行甄别文档内容的完整性,平台不提供额外的编辑、内容补充、找答案等附加服务。
- 2、"仅部分预览"的文档,不可在线预览部分如存在完整性等问题,可反馈申请退款(可完整预览的文档不适用该条件!)。
- 3、如文档侵犯您的权益,请联系客服反馈,我们会尽快为您处理(人工客服工作时间:9:00-18:30)。
SBA(Steel Beam Assembler)-H型智能钢装配焊接生产线
钢结构企业,无论轻钢、重钢还是装配式钢结构,其梁(H型钢梁、箱型梁)、柱(H型钢柱、箱型柱、圆管柱)上面都要焊接上各种加劲板、连接板、牛腿等各种部件,这些作业需要在工厂严格按照设计图纸预制,然后到工地现场组装连接。
在钢构件生产制作过程中,焊接作业占有很大比例。
H型钢成型焊接如平腹板H型钢的埋弧自动焊、波浪腹板H型钢的气保焊,因为其焊接过程自动化程度较高,生产节拍好计划也好控制。
但往H型钢上面焊接加劲板、连接板、牛腿等装配焊接作业因为焊接量大,通常又都是人工组对焊接,则很难计划其生产节拍,只能根据实际进度调整人力的投入量和加班时间。
该环节的大量的焊接作业往往成为钢构企业生产进度的瓶颈,影响交货周期的原因十之八九出在这里。
人力成本的高企越来越让企业感到难以承受,但又无法回避。
而焊接工的成本尤其沉重和直接,按天计酬,几百块一天,且人员流动大,企业管理成本也必然因此增加。
现状如此,企业只有叹息,残喘招架。
工业4.0、工业制造2025、机器人换人、工业化生产的概念可谓应运而生,现状逼迫企业要么转型要么升级。
转型谈何容易,小企业具备游击式灵活,但已成规模的企业船大难掉头,往往就只有升级这一条路可走,不走就死,走了可能暂时困难,但前景光明。
本人带着如何实现钢结构的智能化生产这样一个课题去欧洲考察。
在波兰看到了奥地利之门(Zeman)公司生产的SBA的生产过程,顿时眼前一亮。
钢结构智能化生产是可以实现的。
H型钢装配焊接作业能实现机器人换人。
能做到提高效率和精度,又能降低人力成本。
希望国内装备制造企业能尽快研发出SBA类的产品,以促进钢结构企业的顺利升级。