智能焊接生产线在装载机铲斗生产上的应用
挖掘机挖斗实用焊接工艺研究
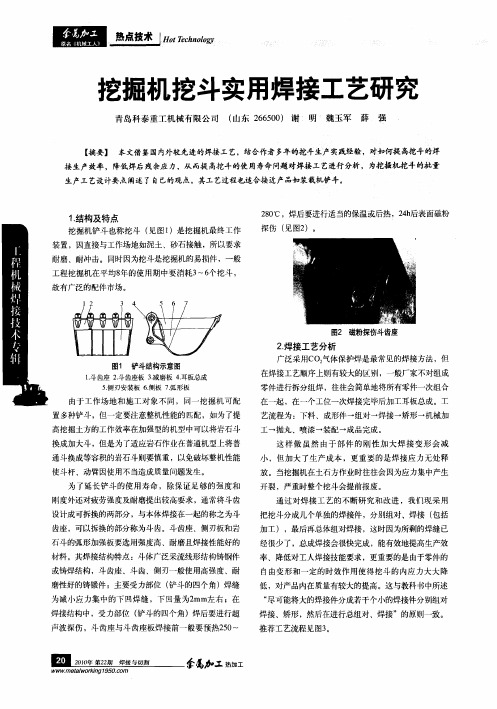
耐磨、耐冲击。同时因为挖斗是挖掘机的易损件 ,一般
工程挖掘机在平均8 年的使用期中要消耗3 个挖斗 , ~6
故有广泛 的配件 市场 。
| 国 i
\ \/ /
、/ / / ;
图2 磁粉探伤斗齿座
2焊接工艺分析 .
图1 铲斗结构示意图
1.
使斗 杆、动臂因使用不 当造成质量问题发生 。 为 了延 长铲 斗的 使用寿 命 ,除保证 足够 的强 度和
刚度外还对疲劳强度及耐磨提 出较高要求 ,通常将斗齿 设计成可拆换的两部分 ,与本体焊接在一起的称之为斗
齿座 ,可以拆换的部分称为斗齿 。斗齿座 、侧刃板和岩
把挖斗分成几个单独 的焊接件 ,分别组对 、焊接 ( 包括
图4 弧形板工件组对
图 3
需 要提 醒各位 同行 注意 的是此 流程 中没有 提 到焊 后矫形 ,这是 因为在整个工艺流程中如果焊接顺序和反
变形措施得当的话 ,无需进行焊接矫形 ,工艺的实用性
会进一步得到体现 。众所周知 ,让工件 自由收缩到我们 想要的尺寸 ,既能提高工效 ,又能大大降低焊接应力。 采取这种工艺顺序 ,将整个挖斗的焊接量分散到若干个 工位焊接 ,相当于多人共 同完成一 个工件 ,使人 力资源 得到充分利 用 ,降低 了对 员工的技 能要 求,大大提高 了
生产工 艺设计要 点阐述 了自己的观 点 ,其工艺过程也适合接近 产品如装 载机铲斗 。
1结构及特点 .
挖掘机 铲斗也称 挖斗 ( 图1 见 )是 挖掘机最终 工作
装置 ,因直接与工作场地如泥土 、砂石接触 ,所以要求
20 8 ̄ C,焊后要进行适 当的保温或后热 ,2 h 4 后表面 磁粉 探伤 ( 见图2 )。
无人工厂自动化装配与生产线的创新解决方案

无人工厂自动化装配与生产线的创新解决方案无人工厂自动化装配与生产线,是指利用先进的机器人、物联网和人工智能等技术,实现生产线上的自动化生产过程,以提高生产效率、降低成本,并最大程度地减少人力参与。
本文将介绍无人工厂自动化装配与生产线的创新解决方案。
一、机器人技术在装配领域的应用传统的装配过程通常需要工人进行手工操作,不仅费时费力,还容易出现人为错误。
而现在,机器人技术的应用能够取代人工操作,提高生产效率,保证装配质量。
机器人在装配过程中能够精准地进行零部件的装配,避免了人为错误,同时还能够根据预设程序进行操作,提高生产线的稳定性和一致性。
二、物联网在生产线监控中的应用物联网技术能够实现装配线上各设备之间的互联互通。
通过将各个设备与传感器连接到物联网平台上,可以实时监控生产线的运行情况。
当出现异常情况时,物联网平台会自动发出警报并提供解决方案,从而能够及时解决问题,并减少生产线停机的时间。
三、人工智能在质检过程中的应用传统的质检过程需要大量的人力投入,而且不可避免地存在主观性和一定的误判率。
而借助人工智能技术,可以实现无人化的质检过程。
通过将人工智能算法应用于质检设备中,能够准确地检测产品的质量,并且能够进行相应的判别和分类,从而大大提升质检的效率和准确性。
四、自动化仓储系统的应用传统的仓储过程通常需要人工进行操作和管理,既费时又容易出现错误。
而自动化仓储系统的应用能够实现对产品的自动分类、入库和出库等操作,大大提高了仓储效率。
此外,自动化仓储系统还能够通过物联网技术与其他装配设备进行联动,实现生产线上各个环节的无缝对接,进一步提高生产效率。
五、先进的生产调度系统为了实现无人工厂的自动化装配和生产线,需要一个先进的生产调度系统来统筹安排生产工艺和生产流程。
先进的生产调度系统能够根据订单的优先级和生产能力等因素,合理安排生产计划,并与各个机器人和设备进行实时的通信和协调,实现生产过程的无缝衔接。
这样不仅能够确保生产线的顺畅进行,还能够最大程度地利用资源,提高生产效率。
铁路货车端墙焊接机器人生产线研究

铁路货车端墙焊接机器人生产线研究作者简介:范宏宇:男(1988.3-)汉族,辽宁海城,工程师,本科,研究方向:铁路货车生产设备。
摘要:铁路货车端墙焊接机器人生产线中,不仅包含焊接机器人系统,同时还包含外围的机械系统、电控系统。
其能够对端墙所有焊缝实施焊接,并且能够获得良好成效。
工件自动传输、定位、翻转机构,具有良好的稳定性与可靠性,能够对铁路货车端墙的焊接要求进行有效满足。
文中着手于端墙技术的规格与要求,阐释端墙焊接机器人生产线的设计方案以及工作站设备组成、工件传输、工位设计方案,希望能够为相关工作者提供一些帮助。
关键词:铁路;货车;端墙;焊接机器人;生产线铁路货车实际生产中需要现代化技术手段,焊接技术具有极为关键的作用。
焊接机器人的工作柔性较好,适用于多种焊接位置的工件进行大量生产,焊接机器人操控工作站的实际组成,使用焊接机器人与外围机械系统、电控系统,其是满足国情的自动化焊接设备,同时也是实现低成本自动化的有效措施,机器人焊接中基于协调管控方式,对工件的传输系统进行构建,更好地达成端墙自动化焊接、生产,其具有良好的可靠性、适用性等。
一、技术规格与要求在端墙焊接过程当中,要求相关工作者对工件的材料与尺寸进行合理选择,通常焊缝的形式是搭接焊缝与角焊缝,同时在焊接方式方面也有相应要求。
二、设计方案端墙焊接机器人的生产线中有两条生产线,所有生产线都包含组装焊、待焊、机器人焊接、正面补焊、翻转、背面焊接等工位,先对端墙部件实施定位焊,之后将其自动传输至待焊工位上,等待机器人焊接工位的空闲。
在机器人焊接工位出现空闲之后,工件会自动传输至机器人焊接工位上,同时对工件进行定位夹紧,之后自动管控机器人焊接工件[1]。
机器人先寻找激光焊缝的起始点,明确了焊缝起点位置之后实施焊接,并且实际焊接中基于电弧焊缝的实时跟踪相关技术对焊缝偏差进行纠正。
完成焊接之后,自动传输至第三个焊接工位之上,对正面小部件进行焊接,并且对工件进行自动翻转,焊接工件背面的焊接缝。
智能焊接生产线技术研发方案(一)
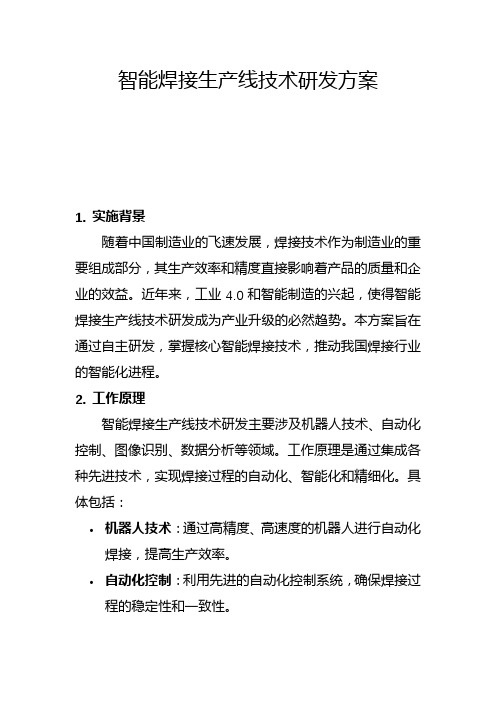
智能焊接生产线技术研发方案1. 实施背景随着中国制造业的飞速发展,焊接技术作为制造业的重要组成部分,其生产效率和精度直接影响着产品的质量和企业的效益。
近年来,工业4.0和智能制造的兴起,使得智能焊接生产线技术研发成为产业升级的必然趋势。
本方案旨在通过自主研发,掌握核心智能焊接技术,推动我国焊接行业的智能化进程。
2. 工作原理智能焊接生产线技术研发主要涉及机器人技术、自动化控制、图像识别、数据分析等领域。
工作原理是通过集成各种先进技术,实现焊接过程的自动化、智能化和精细化。
具体包括:•机器人技术:通过高精度、高速度的机器人进行自动化焊接,提高生产效率。
•自动化控制:利用先进的自动化控制系统,确保焊接过程的稳定性和一致性。
•图像识别:通过机器视觉技术,对焊缝进行高精度识别和定位,确保焊接质量。
•数据分析:通过对大量焊接数据的分析,优化焊接参数,提高产品质量。
3. 实施计划步骤1.建立研发团队,明确研发目标。
2.进行技术调研,掌握市场需求和竞争对手情况。
3.制定研发计划,明确阶段性目标和时间节点。
4.进行技术研发,包括硬件设计、软件开发和系统集成等。
5.进行原型测试和优化,确保技术的稳定性和可行性。
6.与企业合作,进行生产现场测试,验证技术的实际效果。
7.根据测试结果进行优化和完善,推广应用。
4. 适用范围本技术研发方案适用于汽车制造、航空航天、轨道交通、管道施工等领域的焊接生产。
同时,对于中小型企业而言,通过引入智能焊接生产线技术,可以提高生产效率、降低成本、提升产品质量,增强市场竞争力。
对于大型企业,则可以进一步提高生产过程的可控性、降低质量波动、提高生产效率,从而大大提升企业的综合效益。
5. 创新要点•集成多种技术:本方案通过集成机器人技术、自动化控制、图像识别和数据分析等多种技术,实现了焊接过程的全面智能化和自动化。
•数据驱动优化:通过对大量焊接数据的分析,可以持续优化焊接参数,提高产品质量和生产效率。
自动焊接工艺

自动焊接工艺嘿,朋友们!今天咱就来唠唠自动焊接工艺这档子事儿。
你说这自动焊接工艺啊,就像是个超级厉害的“焊接大师”,而且还不知疲倦呢!它能把那些金属部件严丝合缝地连接在一起,那手艺,简直绝了!想象一下,要是没有自动焊接工艺,那得多少工人师傅们辛苦地拿着焊枪一点点去焊接啊。
有了它,可就省事儿多啦。
它就像个精准的机器人,按照设定好的程序,“滋滋”几下,就把该焊接的地方都焊好了。
自动焊接工艺的好处那可多了去了。
首先呢,它的焊接质量特别高,焊缝均匀又牢固,可不是人工能随便比的哟。
而且啊,它速度快啊,那效率,蹭蹭地往上提。
这可给工厂节省了不少时间和成本呢,咱就说这多划算呀!你再看看那些大型的机械制造企业,要是没有自动焊接工艺,那得忙成啥样啊?这自动焊接工艺就像是他们的得力助手,帮着他们又快又好地完成各种焊接任务。
还有啊,自动焊接工艺对于一些高难度的焊接工作也不在话下。
什么厚板焊接啦,异种金属焊接啦,它都能搞定。
这就好比一个武林高手,什么招式都能应对自如。
当然啦,要想让自动焊接工艺发挥出最大的作用,那可得好好对待它。
就像你养个宠物,得给它吃好喝好照顾好呀。
得定期给它做维护,检查检查这儿,看看那儿,可不能让它出啥毛病。
要是它“生病”了,那可不得了,耽误生产不说,还得花时间和精力去修它呢。
咱再说说这自动焊接工艺的操作吧。
这可不是谁都能随便上手的,得经过专门的培训才行。
你可不能小瞧了这培训,这就像是学武功,得一步一个脚印地学,才能掌握其中的精髓。
等你学会了,就能熟练地操作这个“焊接大师”啦,让它乖乖听你的话,为你干活。
在实际应用中,自动焊接工艺的发展前景那是一片光明啊。
随着科技的不断进步,它肯定会变得越来越智能,越来越厉害。
说不定以后啊,它都能自己检测焊接质量,自己调整焊接参数了呢,那可就牛了啊!总之呢,自动焊接工艺就是个宝,给我们的生产生活带来了巨大的便利和好处。
咱可得好好珍惜它,让它为我们创造更多的价值。
你们说是不是这个理儿呀?。
装载机铲斗销孔双头数控镗床的设计与开发
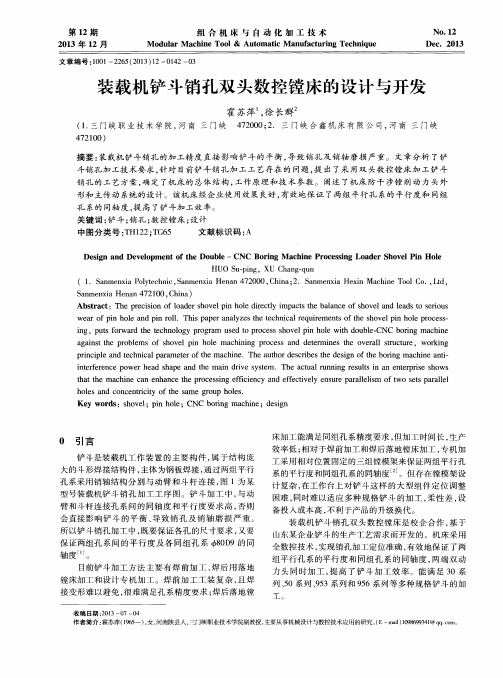
工
作 者简 介 : 霍 苏萍 ( 1 9 6 5 一) , 女, 河 南陕县人 , 三门峡 职业技术 学院副 教授 , 主要 从事机 械设计与数 控技术应 用的研究 , ( E—m a i l ) 1 O 9 8 6 9 9 3 4 l @q q . C O n。 r
i n g,p u t s f o r wa r d t h e t e c h n o l o g y p r o g r a m u s e d t o p r o c e s s s h o v e l p i n h o l e wi t h d o u b l e — CN C b o in r g ma c h i n e
4 7 2 0 0 0; 2 .三 门 峡 合 鑫 机 床 有 限公 司 , 河 南 三 门峡
摘要: 装载机 铲斗销 孔 的加 工精 度 直接 影 响 铲 斗 的平衡 , 导致 销 孔及 销 轴磨 损 严 重 。文 章 分析 了铲
斗销 孔加 工技 术要 求 , 针 对 目前铲 斗销 孔 加 工 工 艺存 在 的 问题 , 提 出了采 用双 头数 控 镗床 加 工铲 斗 销 孔 的工 艺方案 , 确定 了机床 的 总体 结 构 , 工作 原 理和 技 术参 数 。 阐述 了机 床 防 干 涉镗 削动 力 头外
轴 度 。
目前铲 斗加 工方 法 主要有 焊前 加 工 、 焊后 用 落地 镗床加工 和设计 专 机加 工 。焊 前加 工工 装复 杂 , 且 焊
接 变形难 以避 免 , 很难满足孑 L 系精度要求 ; 焊后落 地镗
收 稿 日期 : 2 0 1 3—0 7— 0 4
装载机铲斗刀板断裂原因分析

装载机铲斗刀板断裂原因分析刘祖强;刘毅敏;廖桓萱【摘要】通过对断口形貌、化学成分、金相组织、扫描电镜、冲击韧性、硬度等理化检验和分析,最终确定了装载机铲齿与刀板连接处的焊接薄弱区是刀板断裂的裂纹源,断裂刀板硬度和冲击性能不符合要求,显著降低了刀板的使用寿命.【期刊名称】《四川冶金》【年(卷),期】2016(038)002【总页数】5页(P67-71)【关键词】装载机;铲斗刀板;断裂;理化检验【作者】刘祖强;刘毅敏;廖桓萱【作者单位】广西柳州钢铁集团公司技术中心,广西柳州5450021;广西柳州钢铁集团公司技术中心,广西柳州5450021;广西柳州钢铁集团公司技术中心,广西柳州5450021【正文语种】中文【中图分类】U653装载机的铲斗刀板在装载作业中直接与物料接触,主要承受摩擦力及冲击力的共同作用,容易产生磨损,因而要求刀板材料既要有较高的强度、韧性和耐磨性,从装配要求来看,还要有较高的可焊性[1]。
某用户使用某工程机械公司生产的装载机进行铲掘作业,铲斗刀板在达到预期使用寿命10%时出现开裂,用户拒绝使用。
为了解装载机铲斗刀板开裂产生原因,对断裂刀板进行了化学成分、金相组织、扫描电镜、冲击韧性、硬度等理化检验和分析。
2.1 宏观形貌观察刀板从靠近铲齿角部处发生断裂,裂纹平直且贯穿刀板整个截面,在扩展过程中无次生裂纹产生(见图1)。
2.2 超声波探伤用CTS-4020超声检测仪对整个刀板表面进行扫查,结果显示刀板内部质量较好,未发现裂纹、白点、缩孔等冶金缺陷,主裂纹两侧无次生裂纹的扩展。
2.3 断口分析利用机械切割方法打开裂纹,裂纹截面平齐,无明显塑性变形特征(见图2a),断裂面已被腐蚀和污染,局部存在凹坑。
利用自制电解腐蚀装置清除断裂面铁锈,酸液成分是体积分数为17%的工业盐酸水溶液,使用电流为380 A,电蚀时间为15 min,电蚀后的断口形貌(见图2b),断口局部位置放大形貌见图2c。
刀板表面未见结疤、裂纹等缺陷,断裂分为裂纹源、放射区、剪切唇三个区域,裂纹源位于凹坑位置。
智能焊接技术在机械制造中的应用
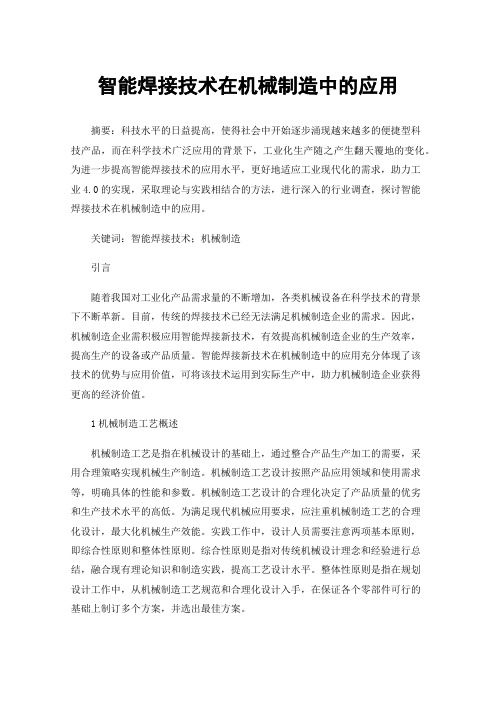
智能焊接技术在机械制造中的应用摘要:科技水平的日益提高,使得社会中开始逐步涌现越来越多的便捷型科技产品,而在科学技术广泛应用的背景下,工业化生产随之产生翻天覆地的变化。
为进一步提高智能焊接技术的应用水平,更好地适应工业现代化的需求,助力工业4.0的实现,采取理论与实践相结合的方法,进行深入的行业调查,探讨智能焊接技术在机械制造中的应用。
关键词:智能焊接技术;机械制造引言随着我国对工业化产品需求量的不断增加,各类机械设备在科学技术的背景下不断革新。
目前,传统的焊接技术已经无法满足机械制造企业的需求。
因此,机械制造企业需积极应用智能焊接新技术,有效提高机械制造企业的生产效率,提高生产的设备或产品质量。
智能焊接新技术在机械制造中的应用充分体现了该技术的优势与应用价值,可将该技术运用到实际生产中,助力机械制造企业获得更高的经济价值。
1机械制造工艺概述机械制造工艺是指在机械设计的基础上,通过整合产品生产加工的需要,采用合理策略实现机械生产制造。
机械制造工艺设计按照产品应用领域和使用需求等,明确具体的性能和参数。
机械制造工艺设计的合理化决定了产品质量的优劣和生产技术水平的高低。
为满足现代机械应用要求,应注重机械制造工艺的合理化设计,最大化机械生产效能。
实践工作中,设计人员需要注意两项基本原则,即综合性原则和整体性原则。
综合性原则是指对传统机械设计理念和经验进行总结,融合现有理论知识和制造实践,提高工艺设计水平。
整体性原则是指在规划设计工作中,从机械制造工艺规范和合理化设计入手,在保证各个零部件可行的基础上制订多个方案,并选出最佳方案。
2机械制造加工现状2.1机械加工工艺落后机械制造加工工艺直接决定了机械产品的质量,加工工艺的规范性和合理性会直接反映到机械加工水平上。
相比于发达国家,我国的机械加工受传统观念影响比较严重,管理系统相对落后,工人素质不高,整个机械加工工艺存在制造程序不规范、不合理的问题。
在这种情况下,机械加工产品竞争力不足,无法达到国际先进水平。
- 1、下载文档前请自行甄别文档内容的完整性,平台不提供额外的编辑、内容补充、找答案等附加服务。
- 2、"仅部分预览"的文档,不可在线预览部分如存在完整性等问题,可反馈申请退款(可完整预览的文档不适用该条件!)。
- 3、如文档侵犯您的权益,请联系客服反馈,我们会尽快为您处理(人工客服工作时间:9:00-18:30)。
摘要:采用可直角换轨式RGV ,将多个机器人焊接工作站与前后工序连接起来,在LCS 和DCS 调度系统控制下,实现装载机铲斗生产的自动上下料、自动装夹、焊接程序自动调用、自动焊接、自动报工。
构成了智能制造车间,减少人工干预、降低劳动强度、提升生产效率、提高焊接质量、满足节拍生产要求,实现了车间整体运营的效益最大化。
关键词:RGV ;机器人焊接工作站;DCS 控制系统;自动装夹;调度中图分类号:TG409文献标志码:B 文章编号:1001-2303(2014)02-0043-06DOI :10.7512/j.issn.1001-2303.2014.02.09第44卷第2期2014Vol.44No.2Feb .2014收稿日期:2012-09-11作者简介:贾方庆(1980—),男,江苏徐州人,工程师,学士,主要从事自动化设备的设计和研发工作。
贾方庆,董文宁,张传根,曹强(徐州华恒机器人系统有限公司,江苏徐州221000)粤pplication of intelligent robot welding line for the loader bucket productionJIA Fang-qing ,DONG Wen-ning ,ZHANG Chuan-gen ,CAO Qing(Xuzhou Huaheng Robot System Co.,Ltd.,Xuzhou 221000,China )Abstract :With the right angle for rail type RGV,a plurality of welding robot workstation before and after the working procedure isconnected,in the control of LCS and DCS scheduling system,realize the loader bucket production of automatic feeding,automatic clamping,welding procedure calls automatically,automatic welding,automatic timesheet.This constitutes a smart little humanizedmanufacturing workshop,reduce the manual intervention,reduce labor intensity,improve production efficiency,improve the welding quality,to meet the requirements of production,the beat realizes maximum benefit overall workshop operation.Key words :RGV ;robot welding workstation ;the control system of DCS ;automatic clamping ;discrete curvature ;line drawing 0前言在工程机械行业已广泛使用机器人焊接代替人工焊接,目前应用较多的是采用单个机器人焊接工作站完成特定工件的焊接。
大量使用焊接机器人可以提升生产效率,提高产品质量,降低生产成本和减轻工人劳动强度。
单个机器人焊接系统虽然能够在单一焊接工序中达到以上目的,但是对整个生产过程效率的提升作用较小。
因为单个机器人焊接系统在整个生产过程中一般都有物流不畅、人工干预过多、存在安全隐患、效率低等问题。
通过实地考察,拥有20~100套机器人焊接系统的制造工厂,主要存在以下问题:(1)由于物流单一依赖行车,往往出现机器人焊接完成后无人下料,或者机器人工位空闲无人上料的情况,生产出现停顿,设备利用率不高。
(2)由于上下料使用人工方式,机器人程序选择受到人工干预,偶尔出现程序选择错误导致碰撞等生产事故。
(3)由于生产停顿和人工干预导致的误操作,生产节拍不能固定,很难保证生产计划有效实施。
(4)由于完成的工件不能实现有效转运,车间在制品数量上得不到有效控制。
(5)机器人布局或者靠墙或者靠立柱,而车间中部黄金地带用于行车转运工件,车间面积不能有效利用。
(6)使用行车、KBK、人工吊运、转运大型工件始终存在安全隐患。
因此,使用智能制造技术将机器人系统和上下游工序有机并紧密地联系在一起,构成无人化或少人化的智能制造车间已成为应用趋势。
1方案介绍智能焊接生产线主要包括直角换轨式RGV (Rail Guide Vehicle)搬运小车、步进式板链缓存台、机器人焊接工作站系统、DCS(Distributed Control System)调度系统、LCS上位机管理系统、视频监控系统六个部分。
在DCS控制系统的调度下,RGV小车可以自动上下料、自动装夹、焊接程序自动调用、自动焊接、自动报工,无需人工干预。
同时LCS上位机管理系统将工件信息、完工情况等信息与MES 系统对接,完成了生产制造过程中的信息流转。
2工艺流程在铲斗的生产过程中,首先是应用铲斗拼点工装将各组件拼装、点焊,将成型待焊的铲斗放置到料台上,利用料台上限位块、卡槽对铲斗进行定位,组对区DCS召唤该区域RGV,自动将工件转运至步进式上料缓存台存放。
在RGV主轨道两侧分布多台机器人焊接工作站,机器人焊接工作站区DCS调度系统采集各工作站的信息、上下料RGV 信息、步进式上下料缓存台信息等,对所有工作站的上下料请求进行排序、穿插、优化,控制上料RGV将工件转运至相应的机器人焊接工作站。
工作站工装对工件自动装夹,根据工件型号调用焊接程序,启动焊接。
焊接结束后,自动向DCS调度系统请求下料,DCS响应请求,控制下料RGV将焊接完的工件转运至步进式下料缓存台。
人工补焊区、镗加工区DCS调度本区RGV完成物料在后续加工区域的流转。
一个完整的上料、下料过程如图1所示。
3系统构成和功能3.1直角换轨式RGV作为智能物流生产线的主要搬运工具,直角换轨式RGV小车不仅可以在主轨上行驶,还可以直角换轨后在垂直于主轨的辅轨上行驶,这样就可以将工件分别送往主轨道两侧多个机器人焊接工作站。
采用CX系列控制器为控制核心,TwinCAT NC PTP 控制系统、AX5000伺服驱动器和AM3000伺服电机构成驱动方案;采用Profibus DP接口的条码扫描器加防尘、耐油污的条码带作位置检测;采用WLAN 控制器作无线接入点,通过TwinCAT ADS协议实现RGV与DCS的无线数据交换。
该RGV结构紧凑、运送速度快(达到27m/min)、行走平稳、定位精度高(<1mm),保证RGV在各主辅轨交叉点精确换轨、快速的将待焊工件送往工作站焊接或将工作站内焊接完的工件转运至下一个工序。
该RGV可在主副轨任意位置设置站点,其站点坐标可在RGV中灵活设置,无需更改程序,配置灵活,使用方便。
3.2DCS(Distributed Control System)调度系统在该智能物流生产线上,DCS调度系统起着中图1铲斗智能焊接生产线的工艺流程焊接设备第源4卷枢神经系统的作用。
它既要通过分布式I/O 获取各个机器人焊接工作站的请求信号、液压夹具的装夹完成信号和料台的工件到位信号等,还要控制和调度小车进行上、下料。
在DCS 控制下,自动将待焊工件转运至机器人焊接工作站,RGV 与工作站工装紧密配合完成工件的自动装夹。
焊接完成后,自动将焊接完成的工件转运至步进式下料缓存台。
3.2.1DCS 调度系统组成DCS 调度系统由CX 系列控制器、EtherCAT 总线扩展模块、耦合器模块、I/O 模块、无线路由器、交换机、HMI 组成。
CX 系列控制器作主站,总线扩展模块用于扩展EtherCAT 总线。
每一个耦合器模块下挂I/O 模块作从站,构成一个环型网络,实现了EtherCAT 网络冗余功能。
每一个从站通过I/O 模块与机器人焊接工作站、步进式上下料缓存台交互信号,为了防止电源干扰,这些输入输出信号均采取继电隔离。
耘therCAT网络拓扑结构如图2、图3所示。
图3EtherCAT 网络连接主站将收集到的各机器人焊接工作站的信息进行处理,根据处理结果将信息以无线方式通过交换机、无线路由器发送给RGV ,指挥RGV 完成上下料任务,并实现避让避碰、任务排列、任务穿插、任务等待等功能。
同时将RGV 的各种信息通过无线通讯传递给主站控制器,主站控制器通过基于Modbus TCP 协议的以太网通讯将相关数据显示在HMI 上,并读取HMI 上的输入信息。
3.2.2DCS 调度系统特点(1)安全。
RGV 附带障碍物检测传感器用于检测运行前方的障碍物,防止碰撞、伤人事件发生。
该传感器可根据外来信号选择检测区域,对不同的路线路况设置不同的检测区域,同时可以借助辅助传感器拓展检测区域。
每个区域的灵敏度均可以灵活设置。
限制RGV 在某些位置的动作,防止碰撞事件发生。
设置两RGV 安全距离,当两RGV 距离小于安图2EtherCAT 网络拓扑结构全距离时,调用暂停功能暂停RGV,防止两车碰撞和同向追尾[1];当两车距离大于安全距离时,被暂停的RGV会继续自动运行。
(2)高效。
生产线上的两个RGV分别执行上、下料任务,系统根据FCFS(First Come,First Served)对上料任务、下料任务进行排列,对排列完的任务自动判断是否路径冲突,若不冲突,则同时执行上下料任务;若冲突,则会在任务中往后搜索,挑拣出路径不冲突的任务与另一任务同时执行;若搜索不到,则等待先执行任务的RGV运行至路径不冲突的位置,响应此RGV的任务,同时执行上下料任务。
这样避免了单轨单RGV系统[2]执行上(下)料任务时,众多的下(上)料任务必须等待的情况,特别是机器人焊接工作站较多时,RGV在给一个工作站上料或者下料的过程中,其他有上、下料请求的工作站只能等待,设备利用率不高,生产效率低下,无法满足物料连续流转的要求。
在两RGV运行路径规划上做到了动作流畅、精简,保证了流水线高效运行,严格控制各个工序用时,满足节拍生产要求。
(3)故障自恢复能力强。
主站控制器带有两个具有独立网卡的以太网口,与各从站采用EtherCAT总线通讯,物理上构成环型网络拓扑结构,构成了双环网,实现了网络冗余功能[3]。
对系统可能出现的单点故障,能够将数据自动环回,防止丢站故障的发生。
对可能出现的某个机器人焊接工作站故障,系统可以绕过该故障工作站降级运行。
同时系统也有半自动运行模式,使用遥控器,通过几个简单的按键动作,即可轻松完成上下料任务。