水泥生产工艺流程
水泥的生产工艺流程
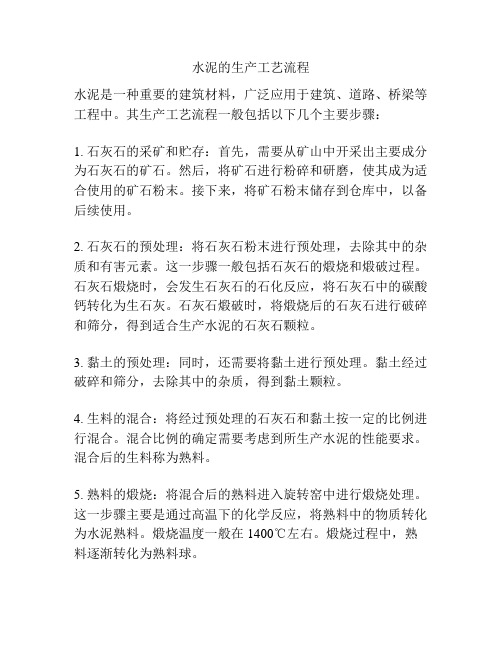
水泥的生产工艺流程水泥是一种重要的建筑材料,广泛应用于建筑、道路、桥梁等工程中。
其生产工艺流程一般包括以下几个主要步骤:1. 石灰石的采矿和贮存:首先,需要从矿山中开采出主要成分为石灰石的矿石。
然后,将矿石进行粉碎和研磨,使其成为适合使用的矿石粉末。
接下来,将矿石粉末储存到仓库中,以备后续使用。
2. 石灰石的预处理:将石灰石粉末进行预处理,去除其中的杂质和有害元素。
这一步骤一般包括石灰石的煅烧和煅破过程。
石灰石煅烧时,会发生石灰石的石化反应,将石灰石中的碳酸钙转化为生石灰。
石灰石煅破时,将煅烧后的石灰石进行破碎和筛分,得到适合生产水泥的石灰石颗粒。
3. 黏土的预处理:同时,还需要将黏土进行预处理。
黏土经过破碎和筛分,去除其中的杂质,得到黏土颗粒。
4. 生料的混合:将经过预处理的石灰石和黏土按一定的比例进行混合。
混合比例的确定需要考虑到所生产水泥的性能要求。
混合后的生料称为熟料。
5. 熟料的煅烧:将混合后的熟料进入旋转窑中进行煅烧处理。
这一步骤主要是通过高温下的化学反应,将熟料中的物质转化为水泥熟料。
煅烧温度一般在1400℃左右。
煅烧过程中,熟料逐渐转化为熟料球。
6. 煤磨和水泥辅料制备:在煅烧过程中,需要使用煤作为主要燃料。
首先,将煤矿从矿井中采出,并进行破碎和粉磨,得到煤粉。
同时,将焚烧废渣等其他材料进行破碎和粉磨,得到适合制备水泥辅料的颗粒。
7. 水泥的制备:煅烧后的熟料球经过冷却和筛分,得到水泥熟料。
然后,将水泥熟料与煤粉、水泥辅料等进行混合和研磨,得到最终的水泥产品。
这个步骤一般通过水泥磨机进行完成。
8. 包装和储存:最后,将制备好的水泥产品进行包装,以便运输和储存。
包装一般采用纸袋或者增塑塑料袋。
包装好的水泥袋使用机器进行堆放和码垛,方便地存放在仓库中。
综上所述,水泥的生产工艺流程主要包括石灰石的采矿和处理、黏土的预处理、生料的混合、熟料的煅烧、煤磨和水泥辅料制备、水泥的制备、包装和储存等步骤。
水泥生产工艺流程
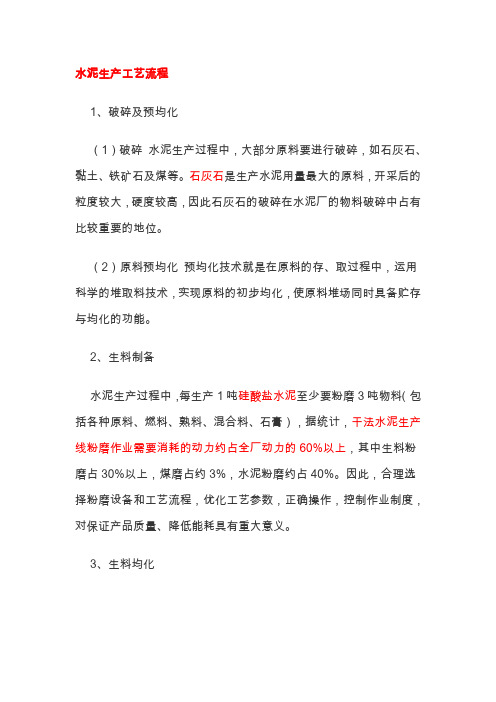
水泥生产工艺流程1、破碎及预均化(1)破碎水泥生产过程中,大部分原料要进行破碎,如石灰石、黏土、铁矿石及煤等。
石灰石是生产水泥用量最大的原料,开采后的粒度较大,硬度较高,因此石灰石的破碎在水泥厂的物料破碎中占有比较重要的地位。
(2)原料预均化预均化技术就是在原料的存、取过程中,运用科学的堆取料技术,实现原料的初步均化,使原料堆场同时具备贮存与均化的功能。
2、生料制备水泥生产过程中,每生产1吨硅酸盐水泥至少要粉磨3吨物料(包括各种原料、燃料、熟料、混合料、石膏),据统计,干法水泥生产线粉磨作业需要消耗的动力约占全厂动力的60%以上,其中生料粉磨占30%以上,煤磨占约3%,水泥粉磨约占40%。
因此,合理选择粉磨设备和工艺流程,优化工艺参数,正确操作,控制作业制度,对保证产品质量、降低能耗具有重大意义。
3、生料均化新型干法水泥生产过程中,稳定入窖生料成分是稳定熟料烧成热工制度的前提,生料均化系统起着稳定入窖生料成分的最后一道把关作用。
4、预热分解把生料的预热和部分分解由预热器来完成,代替回转窑部分功能,达到缩短回窑长度,同时使窑内以堆积状态进行气料换热过程,移到预热器内在悬浮状态下进行,使生料能够同窑内排出的炽热气体充分混合,增大了气料接触面积,传热速度快,热交换效率高,达到提高窑系统生产效率、降低熟料烧成热耗的目的。
(1)物料分散换热80%在入口管道内进行的。
喂入预热器管道中的生料,在与高速上升气流的冲击下,物料折转向上随气流运动,同时被分散。
(2)气固分离当气流携带料粉进入旋风筒后,被迫在旋风筒筒体与内筒(排气管)之间的环状空间内做旋转流动,并且一边旋转一边向下运动,由筒体到锥体,一直可以延伸到锥体的端部,然后转而向上旋转上升,由排气管排出。
(3)预分解预分解技术的出现是水泥煅烧工艺的一次技术飞跃。
它是在预热器和回转窑之间增设分解炉和利用窑尾上升烟道,设燃料喷入装置,使燃料燃烧的放热过程与生料的碳酸盐分解的吸热过程,在分解炉内以悬浮态或流化态下迅速进行,使入窑生料的分解率提高到90%以上。
水泥生产工艺流程图

水泥生产工艺流程图The document was prepared on January 2, 2021过程工业装备成套技术的工程应用实例——水泥生产工艺流程1、破碎及预均化1破碎水泥生产过程中,大部分原料要进行破碎,如石灰石、黏土、铁矿石及煤等.石灰石是生产水泥用量最大的原料,开采后的粒度较大,硬度较高,因此石灰石的破碎在水泥机械的物料破碎中占有比较重要的地位.2原料预均化预均化技术就是在原料的存、取过程中,运用科学的堆取料技术,实现原料的初步均化,使原料堆场同时具备贮存与均化的功能.2、生料制备水泥生产过程中,每生产1吨硅酸盐水泥设备至少要粉磨3吨物料包括各种原料、燃料、熟料、混合料、石膏,据统计,干法水泥生产线粉磨作业需要消耗的动力约占全厂动力的60%以上,其中生料粉磨占30%以上,煤磨占约3%,水泥粉磨约占40%.因此,合理选择粉磨设备和工艺流程,优化工艺参数,正确操作,控制作业制度,对保证产品质量、降低能耗具有重大意义.3、生料均化新型干法水泥生产过程中,稳定入窖生料成分是稳定熟料烧成热工制度的前提,生料均化系统起着稳定入窖生料成分的最后一道把关作用.4、预热分解水泥机械把生料的预热和部分分解由预热器来完成,代替回转窑部分功能,达到缩短回窑长度,同时使窑内以堆积状态进行气料换热过程,移到预热器内在悬浮状态下进行,使生料能够同窑内排出的炽热气体充分混合,增大了气料接触面积,传热速度快,热交换效率高,达到提高窑系统生产效率、降低熟料烧成热耗的目的.1物料分散换热80%在入口管道内进行的.喂入预热器管道中的生料,在与高速上升气流的冲击下,物料折转向上随气流运动,同时被分散.2气固分离当气流携带料粉进入旋风筒后,被迫在旋风筒筒体与内筒排气管之间的环状空间内做旋转流动,并且一边旋转一边向下运动,由筒体到锥体,一直可以延伸到锥体的端部,然后转而向上旋转上升,由排气管排出.3预分解预分解技术的出现是水泥设备煅烧工艺的一次技术飞跃.它是在预热器和回转窑之间增设分解炉和利用窑尾上升烟道,设燃料喷入装置,使燃料燃烧的放热过程与生料的碳酸盐分解的吸热过程,在分解炉内以悬浮态或流化态下迅速进行,使入窑生料的分解率提高到90%以上.将原来在回转窑内进行的碳酸盐分解任务,移到分解炉内进行;燃料大部分从分解炉内加入,少部分由窑头加入,减轻了窑内煅烧带的热负荷,延长了衬料寿命,有利于生产大型化;由于燃料与生料混合均匀,燃料燃烧热及时传递给物料,使燃烧、换热及碳酸盐分解过程得到优化.因而具有优质、高效、低耗等一系列优良性能及特点.5、水泥熟料的烧成生料在旋风预热器中完成预热和预分解后,下一道工序是进入回转窑中进行熟料的烧成.在回转窑中碳酸盐进一步的迅速分解并发生一系列的固相反应,生成水泥熟料中的等矿物.随着物料温度升高,等矿物会变成液相,溶解于液相中的物质进行反应生成大量熟料.熟料烧成后,温度开始降低.最后由水泥熟料冷却机将回转窑卸出的高温熟料冷却到下游输送、贮存库和水泥机械所能承受的温度,同时回收高温熟料的显热,提高系统的热效率和熟料质量.6、水泥粉磨水泥机械是水泥制造的最后工序,也是耗电最多的工序.其主要功能在于将水泥熟料及胶凝剂、性能调节材料等粉磨至适宜的粒度以细度、比表面积等表示,形成一定的颗粒级配,增大其水化面积,加速水化速度,满足水泥浆体凝结、硬化要求.7、水泥包装水泥出厂有袋装和散装两种发运方式.图1. 新型干法水泥生产工艺流程图图2. 新型干法水泥生产工艺流程简述图3.新型干法水泥生产工艺流程图图4. 新型干法水泥生产现场。
水泥的生产工艺
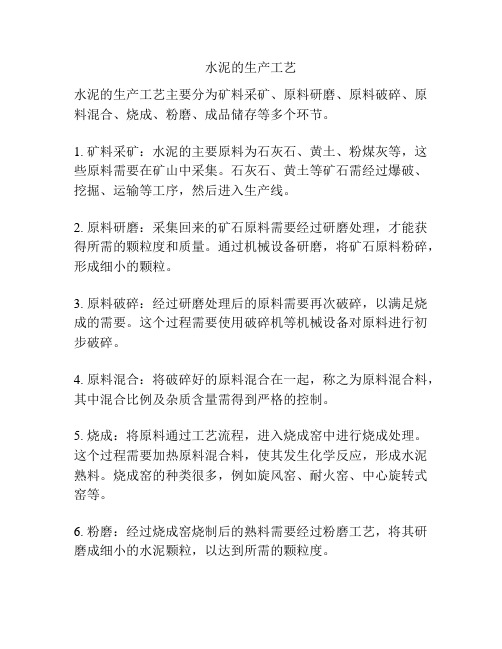
水泥的生产工艺
水泥的生产工艺主要分为矿料采矿、原料研磨、原料破碎、原料混合、烧成、粉磨、成品储存等多个环节。
1. 矿料采矿:水泥的主要原料为石灰石、黄土、粉煤灰等,这些原料需要在矿山中采集。
石灰石、黄土等矿石需经过爆破、挖掘、运输等工序,然后进入生产线。
2. 原料研磨:采集回来的矿石原料需要经过研磨处理,才能获得所需的颗粒度和质量。
通过机械设备研磨,将矿石原料粉碎,形成细小的颗粒。
3. 原料破碎:经过研磨处理后的原料需要再次破碎,以满足烧成的需要。
这个过程需要使用破碎机等机械设备对原料进行初步破碎。
4. 原料混合:将破碎好的原料混合在一起,称之为原料混合料,其中混合比例及杂质含量需得到严格的控制。
5. 烧成:将原料通过工艺流程,进入烧成窑中进行烧成处理。
这个过程需要加热原料混合料,使其发生化学反应,形成水泥熟料。
烧成窑的种类很多,例如旋风窑、耐火窑、中心旋转式窑等。
6. 粉磨:经过烧成窑烧制后的熟料需要经过粉磨工艺,将其研磨成细小的水泥颗粒,以达到所需的颗粒度。
7. 成品储存:经过粉磨后的水泥颗粒被存储在仓库中,等待包装及使用。
以上就是水泥的主要生产工艺。
水泥生产所需的工艺流程较为复杂,需要机械设备、熟练的操作技术及良好的管理质量,以确保生产出质量稳定的水泥。
水泥生产工艺流程

水泥生产工艺流程1、破碎及预均化(1)破碎水泥生产过程中,大部分原料要进行破碎,如石灰石、黏土、铁矿石及煤等。
石灰石是生产水泥用量最大的原料,开采后的粒度较大,硬度较高,因此石灰石的破碎在水泥厂的物料破碎中占有比较重要的地位。
(2)原料预均化预均化技术就是在原料的存、取过程中,运用科学的堆取料技术,实现原料的初步均化,使原料堆场同时具备贮存与均化的功能。
2、生料制备水泥生产过程中,每生产1吨硅酸盐水泥至少要粉磨3吨物料(包括各种原料、燃料、熟料、混合料、石膏),据统计,干法水泥生产线粉磨作业需要消耗的动力约占全厂动力的60%以上,其中生料粉磨占30%以上,煤磨占约3%,水泥粉磨约占40%。
因此,合理选择粉磨设备和工艺流程,优化工艺参数,正确操作,控制作业制度,对保证产品质量、降低能耗具有重大意义。
3、生料均化新型干法水泥生产过程中,稳定入窖生料成分是稳定熟料烧成热工制度的前提,生料均化系统起着稳定入窖生料成分的最后一道把关作用.4、预热分解把生料的预热和部分分解由预热器来完成,代替回转窑部分功能,达到缩短回窑长度,同时使窑内以堆积状态进行气料换热过程,移到预热器内在悬浮状态下进行,使生料能够同窑内排出的炽热气体充分混合,增大了气料接触面积,传热速度快,热交换效率高,达到提高窑系统生产效率、降低熟料烧成热耗的目的。
(1)物料分散换热80%在入口管道内进行的.喂入预热器管道中的生料,在与高速上升气流的冲击下,物料折转向上随气流运动,同时被分散。
(2)气固分离当气流携带料粉进入旋风筒后,被迫在旋风筒筒体与内筒(排气管)之间的环状空间内做旋转流动,并且一边旋转一边向下运动,由筒体到锥体,一直可以延伸到锥体的端部,然后转而向上旋转上升,由排气管排出.(3)预分解预分解技术的出现是水泥煅烧工艺的一次技术飞跃.它是在预热器和回转窑之间增设分解炉和利用窑尾上升烟道,设燃料喷入装置,使燃料燃烧的放热过程与生料的碳酸盐分解的吸热过程,在分解炉内以悬浮态或流化态下迅速进行,使入窑生料的分解率提高到90%以上.将原来在回转窑内进行的碳酸盐分解任务,移到分解炉内进行;燃料大部分从分解炉内加入,少部分由窑头加入,减轻了窑内煅烧带的热负荷,延长了衬料寿命,有利于生产大型化;由于燃料与生料混合均匀,燃料燃烧热及时传递给物料,使燃烧、换热及碳酸盐分解过程得到优化。
{生产工艺流程}水泥厂的工艺流程

{生产工艺流程}水泥厂的工艺流程水泥是一种重要的建筑材料,广泛应用于房屋建设、道路修建和桥梁建设等领域。
水泥的生产工艺流程是一个复杂的过程,它涉及到多个步骤和设备。
下面将详细介绍水泥厂的工艺流程。
1.原材料采购和储存:水泥的主要原料包括石灰石、粘土、铁矿石和煤炭。
石灰石和粘土是主要的原料,并且它们的比例会根据不同类型的水泥而有所不同。
原材料会通过运输设备运送到水泥厂,并经过储存和预处理以准备用于后续的生产工艺。
2.破碎和预混合:石灰石和粘土经过破碎机的破碎和研磨,成为粒径较小的粉末。
然后将粉末混合在一起,形成预混合料。
预混合料会进一步混合和搅拌,以确保原材料的均匀性和稳定性。
3.烧结:预混合料进入烧结炉。
烧结炉是一个高温设备,通过高温熟化原料,使其发生化学反应。
在烧结过程中,石灰石中的钙碳酸盐会分解,并生成烧结石。
这个过程还包括其他一些化学反应,如硅酸盐的烧结和铝酸盐的转化。
4.磨矿:烧结石经过烧结炉后,称为熟料。
熟料会经过矿磨机的研磨,成为更细的粉末。
这个过程能提高水泥的活性和均一性。
5.产成品制备:磨矿后的粉末会被称为水泥。
水泥可以根据不同要求进行分装,通常以包装或散装的形式出售。
此外,水泥也可以根据特定需要添加其他材料,如缓凝剂、增塑剂和颜料,以满足特定工程要求。
6.废气处理:水泥生产过程中会产生大量的废气,这些废气中含有有害物质,例如二氧化硫和一氧化碳。
为了保护环境,水泥厂需要建立废气处理设施,对废气进行处理和净化,以降低对环境的影响。
7.能耗管理:水泥生产是一个能源密集型的过程,需要大量的燃料和电力。
为了提高能源利用效率和降低生产成本,水泥厂需要建立有效的能耗管理体系,并采用节能技术和设备来降低能源消耗。
8.质量管理:水泥的质量是保证工程质量的关键因素。
水泥厂需要建立严格的质量控制体系,确保生产的水泥符合相关的国家和行业标准,并经过质检部门的检验和验证。
总结:水泥厂的生产工艺流程涉及到原材料采购和储存、破碎和预混合、烧结、磨矿、产成品制备、废气处理、能耗管理和质量管理等多个步骤。
水泥生产工艺流程

水泥生产工艺流程
水泥是建筑行业中不可或缺的材料,它通过一系列复杂的工艺
流程生产出来。
水泥生产工艺流程主要包括原材料准备、熟料生产、水泥磨矿和水泥包装四个主要环节。
首先,原材料准备是水泥生产的第一步。
水泥的主要原料包括
石灰石、粘土、铁矿石和煤矿石。
这些原料需要经过粉碎、混合等
工艺处理,以确保原料的化学成分和物理性质符合水泥生产的要求。
其次,熟料生产是水泥生产的核心环节。
原料经过混合后,进
入回转窑进行煅烧。
在高温下,原料中的水分和有机物质被挥发,
形成熟料。
熟料是水泥的主要成分,其品质直接影响到水泥的最终
质量。
接下来是水泥磨矿环节。
熟料经过磨矿机研磨成为水泥粉,同
时加入适量石膏调节水泥的凝固时间和硬化速度。
经过磨矿后的水
泥粉称为水泥熟料,它是水泥生产的最终产品。
最后是水泥包装环节。
水泥熟料经过包装机包装成不同规格的
水泥袋,然后通过输送带运输到仓库,等待销售和使用。
整个水泥生产工艺流程需要严格控制原料的成分和比例,严格控制熟料的煅烧温度和时间,以及磨矿机的运行参数等。
只有严格按照工艺要求进行生产,才能生产出优质的水泥产品。
总的来说,水泥生产工艺流程是一个复杂而又精密的过程,需要各个环节紧密配合,确保生产出符合标准的水泥产品。
只有不断优化工艺流程,提高生产效率和产品质量,才能满足不断增长的市场需求,为建筑行业的发展做出贡献。
水泥制作工艺流程

水泥制作工艺流程水泥是一种常见的建筑材料,用于制作混凝土、砂浆等。
下面将介绍水泥的制作工艺流程。
一、原料准备水泥的主要原料是石灰石和粘土。
首先,需要对石灰石和粘土进行采集,并进行质量检测。
然后,将石灰石和粘土分别送入破碎机进行粉碎,得到粉末状的原料。
二、原料混合将石灰石和粘土的粉末按照一定比例加入到混合机中。
在混合机中,原料经过充分搅拌和混合,确保各种成分均匀分布。
三、煅烧将混合好的原料送入旋转窑中进行煅烧。
在煅烧过程中,原料在高温下发生化学反应,形成熟料。
煅烧温度通常在1400℃左右。
煅烧后的熟料具有较高的熟料球度和强度。
四、熟料磨磨将煅烧后的熟料送入熟料磨进行细磨。
熟料磨是一种重要的设备,能够将熟料磨成细度适中的水泥粉末。
熟料经过细磨后,可以提高水泥的活性和强度。
五、石膏控制为了调节水泥的凝结时间和硬化速度,通常在熟料磨时,将适量的石膏加入到熟料中。
石膏可以控制水泥的凝结反应,使水泥具有适当的强度和工艺性能。
六、包装与储存经过磨磨和石膏控制后的水泥粉末被送至包装机进行包装。
包装好的水泥袋装袋封存,储存在干燥通风的仓库中。
水泥储存期一般为三个月左右。
以上就是水泥的制作工艺流程。
通过原料准备、原料混合、煅烧、熟料磨磨、石膏控制、包装与储存等步骤,最终得到优质的水泥产品。
水泥在建筑行业中有着广泛的应用,能够满足人们对于建筑材料强度和耐久性的要求。
水泥的制作工艺流程在不断地改进和完善,以提高水泥的品质和性能。
未来,随着科技的进步和工艺的创新,水泥的制作工艺也将不断地发展,为建筑行业的发展做出更大的贡献。
- 1、下载文档前请自行甄别文档内容的完整性,平台不提供额外的编辑、内容补充、找答案等附加服务。
- 2、"仅部分预览"的文档,不可在线预览部分如存在完整性等问题,可反馈申请退款(可完整预览的文档不适用该条件!)。
- 3、如文档侵犯您的权益,请联系客服反馈,我们会尽快为您处理(人工客服工作时间:9:00-18:30)。
水泥生产工艺流程
水泥生产的工艺流程大致包括以下几个步骤:
1. 采矿和原料准备:首先需要从采矿场开采出适合用于水
泥生产的原料,主要是石灰岩和粘土。
然后将原料送至破
碎机进行破碎和混合,以得到适合生产水泥的均质原料。
2. 原料磨和混合:将破碎后的原料送入磨机中进行磨细,
以得到粉状的原料。
然后将粉状原料混合在一起,以达到
所需的化学成分和物理性能。
3. 烧成过程:将混和后的原料送入旋转窑或立窑进行烧成。
在烧成过程中,原料在高温下发生化学反应,形成称为熟
料的物质。
4. 熟料磨和混合:将烧成后的熟料送入磨机进行磨细,以
得到适合用于生产水泥的粉状物质。
然后将磨细后的熟料
混合适量的石膏(控制凝结时间)和一些辅助材料,形成
称为水泥的终产品。
5. 煅烧和制备:将水泥熟料送入煅烧窑中进行煅烧,将水泥熟料在高温下煅烧,使其结晶、熔融、冷却和固化,形成硅酸盐水泥。
6. 筛分和包装:将煅烧后的水泥进行筛分,去除不合格的颗粒。
然后将合格的水泥通过自动包装机进行包装,最常见的是将水泥装入袋中。
上述是水泥生产的主要工艺流程,不同的水泥生产厂家可能会有一些细微的差异。
同时,为了提高生产效率和降低能耗,还可以采用一些先进的技术和设备,如干法生产工艺、回转窑技术等。