板料成形数值模拟关键技术
采用试错接触算法的板料成形有限元模拟技术概要

采用试错接触算法的板料成形有限元模拟技术摘要:以金属板料成形过程为对象,采用基于板壳理论的8节点壳单元,以Kirchhoff应力张量和Green应变张量作为应力与应变的度量,采用有限变形的Updated Lagrangian列式,研究有限元方法模拟成形过程的技术。
在此基础上,提出了一种直接试错的接触算法,将非线性的接触边界条件线性化处理,接触处理与有限元计算相对独立。
通过试验结果与计算结果的比较,说明采用的模拟算法是合理可行的。
叙词:金属板料成形有限元模拟接触0 、前言板料冲压成形是机械工业中一种重要的加工方法,在航空、宇航、汽车等制造领域均有着广泛的应用。
长期以来,保证成形零件的成形质量、降低废品率,一直是板料成形研究的目标[1,2]。
从力学角度而言,板料成形是一个同时涵盖几何非线性、材料非线性、边界非线性的复杂的力学过程。
以往,分析成形问题多采用基于塑性理论的解析方法,由于成形过程的物理复杂性,不得不作出较多的简化和假设,这就使得解析方法只能进行很简单的成形问题的分析。
近些年发展起来的板料成形的有限元模拟技术,使得对复杂成形问题的模拟分析成为可能,在优化成形工艺、提高成形质量、降低产品开发成本等方面将发挥潜在的重要作用。
然而,目前的板料成形模拟技术仍存在诸多问题亟待解决,因此仍是国际上成形领域的研究热点[3~5]。
本文以金属板料成形过程为对象,研究利用弹塑性有限变形增量有限元方法模拟成形过程的技术。
采用基于板壳理论的8节点壳单元,以Kirchhoff应力张量和Green应变张量作为应力与应变的度量,建立了有限变形的Updated Lagrangian列式。
在此基础上,提出了一种直接试错的接触算法,在每一增量步进行接触搜索,之后交替进行几何协调处理与接触力的协调处理,直至几何协调与接触力的协调同时满足。
通过试验结果与计算结果的比较,说明采用的模拟算法是合理可行的。
1、8节点等参壳单元由于板料实际上是一种板壳结构,因此采用根据板壳理论建立的壳单元进行板料成形模拟,显然是合适的。
板料冲压成形过程的一种数值模拟方法
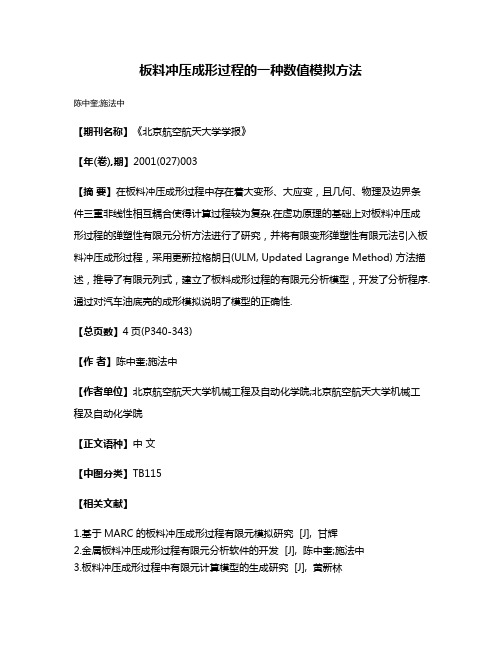
板料冲压成形过程的一种数值模拟方法
陈中奎;施法中
【期刊名称】《北京航空航天大学学报》
【年(卷),期】2001(027)003
【摘要】在板料冲压成形过程中存在着大变形、大应变,且几何、物理及边界条件三重非线性相互耦合使得计算过程较为复杂.在虚功原理的基础上对板料冲压成形过程的弹塑性有限元分析方法进行了研究,并将有限变形弹塑性有限元法引入板料冲压成形过程,采用更新拉格朗日(ULM, Updated Lagrange Method) 方法描述,推导了有限元列式,建立了板料成形过程的有限元分析模型,开发了分析程序.通过对汽车油底壳的成形模拟说明了模型的正确性.
【总页数】4页(P340-343)
【作者】陈中奎;施法中
【作者单位】北京航空航天大学机械工程及自动化学院;北京航空航天大学机械工程及自动化学院
【正文语种】中文
【中图分类】TB115
【相关文献】
1.基于MARC的板料冲压成形过程有限元模拟研究 [J], 甘辉
2.金属板料冲压成形过程有限元分析软件的开发 [J], 陈中奎;施法中
3.板料冲压成形过程中有限元计算模型的生成研究 [J], 黄新林
4.板料冲压成形过程摩擦特性数值仿真 [J], 郑燕萍;王列亮;沈思琳
5.板料冲压成形过程有限元分析中的接触搜索法的优化 [J], 冯天飞;施法中;陈中奎因版权原因,仅展示原文概要,查看原文内容请购买。
板料成形的计算机数值模拟仿真技术

成都 6 0 8 ) 1 0 1
摘 要 : 绍 了 板 料 成 形 数 值 模 拟 技 术 的发 展 及 算 法 , 述 了 国 内应 用 较 广 的 三 种 板 料 成 形 C 介 详 AE 软 件 。 提
出 了板 料 成 形 C AE 的 未 来 发 展 方 向 。
关键 词 : 算 机 应用 ; 压 ; 材 ; 值模 拟 ; 计 冲 板 数 CAE
维普资讯
■ E A uAo墨墨圈 RP c l P T
文 章 编 号 : 6 2 01 1 2 0 ) 4 0 9 — 3 1 7 — 2 (0 6 0 — 0 5 0
板 料成 形 的计 算 机 数 值 模 拟 仿 真 技 术
李 明 昆
( 都 市工业 学校 , 川 成 四
开 发 周 期 , 少 调 试 次 数 , 结 构 修 改 设 想 的 快 速
… 何 德誉 . 压 力 机 【 ¨ 京 : 械 工 业 出 版 社 ,9 7 曲柄 M】| £ 机 18 .
计 软 件 的 开发 . 电 工 程 技 术 ,0 5( )3 . 机 2 0 ,3 :4 【】 Mi oot o . D irr l uy 0 1Mi oo op20 . 5 c sfC r MS N LbayHe Jl 0 . c sfC r.0 1 r p p 2 r t 【】 A nr mot n ni l aC s- ae aoig F u dt n 6 g a Aa d dE rc a .ae B sdResnn: o n ai — a Pz o
中 图 分 类 号 : G3 641 T 8 . 文 献 标 识 码 : A
1
前 言
周 期 、 短 研 发 费 用 以 及 缩 小 整 车 重 量 ( 高 燃 油 效 缩 提
SPCC板材冲压成形过程的数值模拟

SPCC板材冲压成形过程的数值模拟SPCC板材是一种优质的低碳钢板材,常用于制作汽车钣金、电器外壳等产品。
其具有良好的加工性能,但冲压成形过程中容易出现变形和裂纹等问题。
为了提高产品质量和生产效率,数值模拟成为一种重要的工具,可以帮助设计者优化冲压工艺和工装结构。
数值模拟的基本原理是根据材料力学特性和变形规律,通过计算机模拟来预测材料在冲压成形过程中的变形、应力和应变等参数,从而评估产品的质量和可行性。
下面我们以SPCC板材的冲压成形为例,介绍其数值模拟的过程和方法。
一、建立模型数值模拟的第一步是建立三维几何模型,包括产品形状、工艺参数、材料性质等要素。
在SPCC板材的冲压成形中,常见的产品包括箱体、盖板、底板等,需要根据不同产品的尺寸、形状和工艺要求来建立几何模型。
同时,需要设置材料参数,如杨氏模量、泊松比、屈服强度等。
二、网格划分建立几何模型后,需要将其转化为数值网格模型,也称为离散化。
这一过程主要是将复杂的几何体划分成数个小体积或小面积,以便于数值计算和求解。
网格划分的密度和精度决定了数值模拟的精度和速度。
通常,高精度的模拟需要更密的网格划分,但也会增加模拟时间和计算量。
三、建立物理模型在网格划分后,需要建立材料的物理模型,包括材料的本构模型和材料的本构参数。
本构模型是描述材料变形和应力关系的数学模型,常见的本构模型包括各向同性模型、非各向同性模型和弹塑性模型等。
用来描述SPCC板材的本构模型可以使用各向同性的屈服准则或者分段屈服的本构模型。
四、施加载荷和边界条件载荷是指在冲压成形过程中施加在材料表面的力和压力,这些载荷包括空气压力、上下模压力和侧向引伸力等。
边界条件是在数值模拟中必须考虑的约束条件,它们可以限制材料在变形过程中的位移、速度和加速度等。
通常,边界条件包括定位销、卡位、滚动辅助和止口等。
五、数值计算和分析完成模型建立和载荷设置后,就可以进行数值计算和分析。
该过程一般采用有限元分析(FEA)软件来完成,例如ABAQUS、ANSYS等。
聚碳酸酯板材多点热成形数值模拟与成形精度分析

聚碳酸酯板材多点热成形数值模拟与成形精度分析近年来,聚碳酸酯(PC)是一种大量应用于航空航天领域的复合材料之一,其主要特点是其自身轻量高强度,可以用于多种工业制品的制作,例如飞机叶片。
近年来,随着计算机技术的发展,在PC材料的热成形工艺中,以数值模拟为技术支撑,不断改进成形精度,以满足应用于航空航天领域高性能需求。
PC板材多点热成形(RTM)是PC材料的基本热成形工艺之一,它能够将PC板材固化在原型模具的表面上,使其具有良好的抗拉强度、抗压强度和耐磨性能,满足航空航天领域复杂的机械结构要求。
虽然多点热成形的技术实现度很高,但在实际的应用中存在某些问题,例如复杂的温度场、复杂的塑性流体流动、表面失真、非均匀性变形等。
为了解决以上问题,利用数值模拟和实验研究了PC板材RTM工艺的成形精度。
首先,根据实际情况,建立了PC板材RTM工艺的数值模拟流程,主要包括热成形条件的设置、加热模拟、冷却模拟、环境流动模拟以及热变形模拟等,并进行参数的优化和数值模拟的多种改进。
其次,根据实验结果,分析了影响成形精度的因素,特别是表面失真的形成原理,分析了不同温度、压力和填料的比例对成形精度的影响,并根据实验数据获得了成形精度的关联式。
最后,基于热变形机理,对影响PC板材RTM成形精度的参数进行了深入研究,从而改进和优化了成形精度。
经过上述改进,PC板材RTM工艺的成形精度得到了改善,同时在变形模拟中,通过数值模拟的技术支撑,更好地满足了航空航天领域高性能产品的制作要求。
通过本研究,可以为今后PC板材RTM多点热成形工艺技术的应用提供参考依据。
总之,本文以《聚碳酸酯板材多点热成形数值模拟与成形精度分析》为标题,通过数值模拟和实验研究,对PC板材RTM工艺成形精度及影响因素进行了分析,为今后PC板材RTM多点热成形工艺技术的应用提供参考依据。
板料成形CAE技术与其应用完整

板料成形CAE技术与其应用完整(可以直接使用,可编辑优质资料,欢迎下载)板料成形CAE技术及应用长期以来,困扰广大模具设计人员的主要问题就是较长的模具开发设计周期,特别是对于某些特殊复杂的板料成形零件,甚至制约了整个产品的开发进度,而板料成形CAE技术及分析软件的出现,有效地缩短模具设计周期,大大减少试模时间,帮助企业改进产品质量,降低生产成本,从根本上提高了企业的市场竞争力。
一、前言计算机辅助设计技术以其强大的冲击力,影响和改变着工业的各个方面,甚至影响着社会的各个方面。
它使传统的产品技术、工程技术发生了深刻的变革,极大地提高了产品质量,缩短了从设计到生产的周期,实现了设计的自动化。
板料成形是利用模具对金属板料的冲压加工,获得质量轻、表面光滑、造型美观的冲压件,具有节省材料、效率高和低成本等优点,在汽车、航空、模具等行业中占据着重要地位。
由于板料成形是利用板材的变形得到所需的形状的,长期以来,困扰广大模具设计人员的主要问题就是较长的模具开发设计周期,特别是对于复杂的板料成形零件无法准确预测成形的结果,难以预防缺陷的产生,只能通过经验或类似零件的现有工艺资料,通过不断的试模、修模,才能成功。
某些特殊复杂的板料成形零件甚至制约了整个产品的开发进度。
板料成形CAE技术及分析软件,可以在产品原型设计阶段进行工件坯料形状预示、产品可成形性分析以及工艺方案优化,从而有效地缩短模具设计周期,大大减少试模时间,帮助企业改进产品质量,降低生产成本,从根本上提高企业的市场竞争力。
板料成形CAE技术对传统开发模式的改进作用可以通过图1 和图2进行对比。
图1 传统板料成形模具开发模式图2 CAE 技术模具开发方式通过比较,就可发现板料成形CAE技术的主要优点。
(1)通过对工件的可成形工艺性分析,做出工件是否可制造的早期判断;通过对模具方案和冲压方案的模拟分析,及时调整修改模具结构,减少实际试模次数,缩短开发周期。
(2)通过缺陷预测来制定缺陷预防措施,改进产品设计和模具设计,增强模具结构设计以及冲压方案的可靠性,从而减少生产成本。
板料成形数值模拟项目建议书
板料成形数值模拟项目建议书目录1 目标和意义通过实施在世界上成形模拟应用的最专业、最成熟、最广泛的板料成形模拟解决方案来解决板料件模具设计和生产过程中的各种问题。
(1)板料成形模拟解决方案要全面、专业、快速、使用方便的解决板料件模具设计生产过程中的模具设计问题、下料尺寸估算问题、成形精确模拟问题(保证成形后产品的质量)和模具回弹自动补偿问题。
(2)板料成形模拟解决方案要能够提高板料件的模具设计效率,缩短模具从设计到投入生产的周期,提高工艺部门和设计部门的协同效率,缩短产品开发周期,降低产品开发成本,提高产品的市场竞争力。
2 实施必要性板料成形过程的数值模拟技术实质上就是在计算机上应用有限元仿真软件进行虚拟的板料成形试验,通过输入各种给定的条件和一些实际的实验参数,进行计算机数值计算模拟,通过分析模拟得到的结果来预测板料在成形过程中,各种缺陷产生的位置和分布程度,以此初步判断所选毛坯材料力学性能参数与模具工艺设计方案以及模具参数选择的合理性,同时借助数值模拟结果的三维动态显示可以详细地分析冲压成形的每一小步过程的情况,从而可以比较精确确定缺陷产生的具体原因以及找出相对应的解决办法来。
为了提高的制造水平和市场竞争力,为了改变以往板料件模具设计和生产过程中严重依赖设计人员的经验和多次的实际物理试模的落后的状况,我们必须采用专业的成熟的板料成形模拟解决方案解决板料件模具设计问题、下料尺寸估算问题、成形精确模拟问题(保证成形后产品的质量)和模具回弹自动补偿问题。
3 实施基础条件(1) 购置最专业、最成熟、最可靠的板料成形模拟解决软件,为模拟解决各种板料成形问题提供最好的软件系统。
(2) 购置与软件运行相适应的计算机硬件系统和组建相应的网络平台,为软件运行做硬件准备。
(3) 安排相应的工作人员接受软件公司的培训,为熟练操作软件解决实际的问题做准备。
(4)确定采用软件模拟分析板料成形过程的流程,以及相关部门的工作人员的具体工作职责。
板料成形数值模拟技术介绍
前处理的计算结果(dynain文件模型)
E2 进行回弹计算所设置的材料模型参数
3.3 回弹结果分析
在零件上取一条截面线以更清楚地表 现回弹效果,如下图所示。 在前处理中导入由不同E2材料模型得 到的回弹的dynain文件,从而可比较观 察由不同弹性模量得到不同的回弹量
3 通过数值模拟研究弹性模量与回弹 的关系
3.1 前处理 建立建立板料弯曲成形的CAD模型, 并导入到Dynaform前处理环境下, 并进行网格化处理。
凸模
网格化处理后的模型
坯料 凹模
设置坯料的材料参数,特别是计算材 料成形的弹性模量E1
E1
3.2 定义回弹处理模型
通过有限元显式算法,由成形阶段得 到成形结果,并将计算结果(dynain 文件)导入到前处理环境下
近年来出现了基于形变的理论和技术, 不容忽视
2 板料成形接触处理问题 2.1 要解决接触问题首先必须对模具进 行描述,模具的一般表示方法有:
解析函数法:只能用来表示类似于圆 筒件等简单的模型
参数曲面法:能较准确的表达模具曲 面,但算法复杂效率低
网格法:一定程度上克服了以上两者 的缺点,为大多数研究者采用的方法
板料成形数值模拟技术及其应用
一 板料成形数值模拟的研 究现状
二 板料成形数值模拟的科 研和工程实例
引言
板料成形是一种复杂的非线性力 学过程,它包含: 几何非线性问题 材料非线性问题 接触非线性问题
用传统的解析方法很难求解, 且误差较大,而近年来发展了用有 限元法对板料成形过程进行数值模 拟和分析的新技术。
将有限元模拟系统和神经网络、自动控 制等结合起来形成大的分析系统。
金属板料成形数值模拟的研究现状
金属板料成形数值模拟的研究现状一、引言金属板料成形数值模拟是现代制造业中不可或缺的一环。
通过数值模拟可以预测金属板料在成形过程中的变形、应力分布等物理量,从而优化工艺参数,提高成形质量和效率。
本文将介绍金属板料成形数值模拟的研究现状。
二、数值模拟方法1. 有限元法有限元法是目前最为常用的数值模拟方法之一。
它将连续体划分为多个小单元,在每个小单元内近似求解其物理量,最后通过组合得到整体的物理量分布。
有限元法可以考虑材料非线性、边界条件复杂等因素,适用范围广泛。
2. 边界元法边界元法是另一种常用的数值模拟方法。
它将问题转化为求解边界上的物理量分布,避免了对整个区域进行离散化计算。
边界元法适用于具有对称性或者具有复杂几何形状的问题。
3. 网格无关法网格无关法是相对于传统有限元法而言的新兴方法。
它不需要事先确定网格大小和结构,可以自动适应物理量分布的变化。
网格无关法适用于具有较大变形或者复杂几何形状的问题。
三、数值模拟在金属板料成形中的应用1. 成形过程分析数值模拟可以对金属板料成形过程进行分析,预测变形、应力分布等物理量。
通过优化工艺参数,可以避免一些不必要的缺陷和失效。
2. 模具设计数值模拟可以为模具设计提供依据。
通过对成形过程中应力和变形的预测,可以确定合适的模具结构和尺寸,从而达到更好的成形效果。
3. 材料选择数值模拟还可以为材料选择提供参考。
通过预测不同材料在成形过程中的性能表现,可以选择最为适合的材料,提高生产效率和质量。
四、数值模拟存在的问题及发展趋势1. 计算精度问题目前数值模拟存在计算精度不高、计算时间长等问题。
需要进一步发展更加高效精确的数值模拟方法。
2. 跨尺度建模问题金属板料成形涉及到多个尺度,如宏观尺度、晶体尺度等。
如何将不同尺度的模型相结合,进行跨尺度建模是一个重要的研究方向。
3. 多物理场耦合问题金属板料成形涉及到多种物理场,如力学、热学、电磁学等。
如何将这些物理场相互耦合起来进行计算,是数值模拟发展的重要方向之一。
板料渐进成形数值模拟与实验研究
板料渐进成形数值模拟与实验研究
本文采用有限元方法对板料渐进成形过程进行了数值模拟研究,分析 了斜壁盒形件渐进成形过程应力分布和厚度变化趋势,通过对不同进给量 和不同成形路径进行数值模拟,分析了工艺参数对成形的影响。
1、进成形数值模拟 、 有限元模型: 材料模型:为了简化求解过程并容易找到渐进成形的变形规律, 采用非线性弹塑性硬化材料模型中各向同性的弹塑性材料模型。 实体模型:成形件为斜壁盒形件,成形区为100 mm ×100 mm方形, 板料为08Al钢板,材料参数:密度7850 kg/m3 ,弹性模量207 GPa, 屈服极限200MPa,泊松比01324,硬化指数0123。如图1,
工具头运动轨迹:成形工具头 沿着等高的成形轨迹,逐层地成 形板料,采用这种路径的进给方 式可称为逐层进给,工具头沿 着成形轨迹螺线成形板料,采用 这种路径的进给方式可称为螺 旋进给。
2、数值模拟结果与分析 数值模拟结果与分析 1、应力和厚度的变化与分布
从表1可以看出,随着增量步的加大,等效应力极值随之增加,在第10增量 步时达到最大值。 渐进成形过程中某一点的变 形会受到相邻区域变形的影 响,为了考察相邻区域相互 影响的强弱程度,选择具有 典型代表性的两点,一点是 拐角处中点A,另一点是侧面 中点B ,在每个增量步的厚 度变化过程如图3所示。
由图3可以看出,板料在渐进成形过程中,某一点的变形是一个渐变的过程,而并非 一步完成,周围一定区域的板料变形对该点都将产生一定的影响,并且,A点的厚 度小于B点的厚度。
图4为侧面中线上与拐 角处的厚度减薄量分布。 板料边缘变形区厚度减 薄量很小,这是由于板 料边缘塑性变形量较小 的原因。随着接触点位 置与边缘之间距离的增 加,板料厚度薄量逐渐 加大。并且,从图4可 以看出斜壁盒形件拐角 处的厚度减薄量大于其 他变形区域的厚度减薄 量。
- 1、下载文档前请自行甄别文档内容的完整性,平台不提供额外的编辑、内容补充、找答案等附加服务。
- 2、"仅部分预览"的文档,不可在线预览部分如存在完整性等问题,可反馈申请退款(可完整预览的文档不适用该条件!)。
- 3、如文档侵犯您的权益,请联系客服反馈,我们会尽快为您处理(人工客服工作时间:9:00-18:30)。
参数选择 单元方程(2)
在成形分析中 o 平面内拉伸重要 o 对于减薄和拉伸,使用面内一个积分点不会导致明显误差 在回弹预测中 o 应力分布更为重要 o 弯曲和非弯曲, 在单元平面内应力是不一致的 o 在面内选择更多的积分点是必要的
参数选择 单元方程(3)
特点:
o o
Element #2 比 #16快 (3~5倍) Element #16 能够捕获合理的应力分布 对成形分析#2单元是比较好的选择
材料的加工硬化
= K n
s
从实验数据得到硬化曲线(决定弹塑 性材料的属性)
假设我们从拉伸实验得到力的曲线,用下列 步骤得到硬化曲线
o
产生工程应力/应变 产生真实应力/应变 去除弹性应变得到等效应力/等效塑性应变曲线
o
o
STEP 1: Engineering Stress/Strain Curve
板料成形数值模拟关键技术
Contents
单元的选择 材料的定义 模具与板料的相互作用—接触的定义 自适应网格细分 (Adaptive Meshing) 显式算法和隐式算法 时间步长 一步算法,增量算法和2.5D 成形极限图(FLD)
Element 单元方程 Formulations
True Stress Cauchy' s Stress Force fl e 1 e Current Area Ao Ac
True Strain
l Change in Length ln ln1 e Current Length lo
560+NT*33 1104+NT*30 888+NT*270 731+NT*667
626 1164 1428 2065
725 1250 2238 4066
单元属性
*SECTION_SHELL $PROPERTY NAME:blankpro
$
SID
5
ELFORM
SHRF
NIP
3.0 T4
PROPT
E
eff
eff
硬化曲线
所得到的硬化曲线是屈服应力和等效塑性应变 相关曲线。
o
对金属来说,真实应力是递增的
eff
eff
*Mat_3-Parameter_Barlet
*MAT_3-PARAMETER_BARLAT $MATERIAL NAME:DQ $ MID RO E PR HR P1 P2 1 7.850E-09 2.070E+05 2.800E-01 2.000E+00 5.320E+02 2.000E-01 $ M R00 R45 R90 LCID E0 SPI 6.000E+00 1.870E+00 1.270E+00 2.170E+00 0 0.000E+00 0.000E+00 $ AOPT 0.0 $ XP YP ZP A1 A2 A3 $ V1 V2 V3 D1 D2 D3
Element 单元方程 Formulations
Characteristics of the Belytschko-Tsay SE (default)
基于随动坐标系和速度位移方程. 随动坐标系的单元方程 避免了在单元中嵌入坐标系而导致的非线性 动态的复杂性. 单元动量方程假设节点位于同一个平面. 如果是5个积分点, BT单元需要 725数学计算。但是一点HL单元需要 4066次数学计算. HL单元的选择减缩积分需要35,367次数学计算。 由于计算速度效率非常高, BT单元方程通常是壳单元的单元方程的最 佳选择. 正因为如此, 它已经成为4节点板壳单元的缺省的单元方程。
BT单元简单,速度非常快。
Element 单元方程 Formulations
.
30
20
P e r f o r m a n c e
10
1 . 2 5
1
0 BT BTW BL BWC Element T ype CHL HL FBT CFHL FHL Fully in t eg rat e d elem ent s
1.0 NLOC
QR/IRID
0.0
ICOMP
Байду номын сангаас
2 0.833E+00 T2 T3
$
T1
1.000E+00 1.000E+00 1.000E+00 1.000E+00
如果成形完后还要计算回弹, 需选择此项
参数选择
为什么不用统一的参数? o LSDYNA是通用求解器 • 不同的应用需要不同的参数 o 不当参数影响结果预测 • 取决于用户的结果时常发生 o 对于板料成形,我们已经找到了合适的参数 • 做了非常多的分析实例 • 参数一致性得到长足改进 o 对不同的应用采用适当的参数,有利于分析效率 o 大多数参数,DYNAFORM都设定了合理的值 用户的经验仍然重要
E
d , y d
Option 3: Experimental Data
k n k y
p n
, for
y
exponential
材料
Material 18: Material 24: Material 36: Material 37: Material 1: Material 64: Material 103: Material 33: *Mat_Power_Law_Plasticity *Mat_Piecewise_Linear_Plasticity *Mat_3-Parameter_Barlet *Mat_Transversely_Anisotropic_Elastic_Plastic *Mat_Elastic *Mat_Rate_Sensitive_Power_Law_Plasticity *Mat_Anisotropic_Viscoplastic *Mat_Barlet_Yld96
材料模型/塑性行为
单向拉伸试验验证的塑性行为
P A Initial uniaxial yield point y0 y y ai experimental curve L 0 L
elas tic s train
plas tic strain
L n L0 P A
• 节省CPU • 降低内存需求
建议:
o
o
对回弹分析, element #16是更好的选择
• 更加精确的应力分布
在关键字中选择单元方程
o o o o
*SECTION_SHELL ELFORM=2: Element #2 is selected ELFORM=16: Element #16 is selected (ELFORM is the second parameter under the card of *section_shell)
o o o
缺省参数有其局限性 新的应用,需要新的参数 可以用来调试,
参数选择 单元方程(1)
在钣金成形仿真中通常使用的单元方程 o #2单元方程( Belytschko-Tsay) o #16单元方程 (全积分单元方程)
#2 单元
o o
#16单元
#2单元在平面内一个积分点 #16单元在平面内四个积分点
Element 单元方程 Formulations
为什么提供这么多单元方程?
全积分单元用于弹塑性,金属成形,气囊以及关心精确度的时候。 三角形单元(C0单元)刚度比较硬,不建议采用。但是在混合网格中采 用,因为C0三角形壳单元,比退化的四边形网格算法好。 膜单元不能受弯曲和断面剪应力,适用于非常薄的板料以及拉张为主 的变形中 。 进化的板壳单元有较高的精确度,但是和BT单元相比稳定性较差 BT单元速度非常快!
单元使用提示
单元算法BT,BWC,BL采用面内单点积分,全积分采用四点积分 所有壳单元厚度方向可以用任意多个积分点 对弹性变形沿厚度方向用两个积分点即可 塑性行为沿厚度方向用3到5个积分点,回弹可以用7个积分点 避免使用小单元,以免缩小时间步长。如果使用,请同时使用质量 缩放。 减少使用三角形单元。 避免锐角单元和翘曲单元,否则会降低计算精度。
e
f Ao
t
e
e 1 e
d lo
e
ln(1 e )
d
STEP 3: Shift to Remove Elastic Strains
Effective Stress eff vm xx
Effective Strain xx
xx
参数选择 厚度上的积分点(1)
厚度方向上的积分点(NIP) o 在厚度方向的应力分布是复杂的 o 需要更多的积分点来捕获在厚度方向不同的应力分布模式.
Case I
Case II
Case III
Case IV
几种在厚度方向的应力模式
Case I: 纯弹性弯曲; Case II: 弹性和塑性弯曲; Case III: 弯曲 + 拉伸; Case IV: 回弹后的
参数选择 厚度上的积分点(2)
NIP = 2 o Case I中没有错误; o Case II, III, IV中,导致错误 NIP = 3 o Case I中没有错误; o case II, III中,比较小的偏差; o Case IV中,较大偏差 NIP=5,7 o Case I中没有错误; o Case II, III, and IV中,比较小的偏差.
OPERATION C OUNT C OM PARISONS ONE P OINT I NTEGRATION (V ERSION LS 930)