电缆工艺之塑料挤出的基本原理
pvc挤出机挤出原理
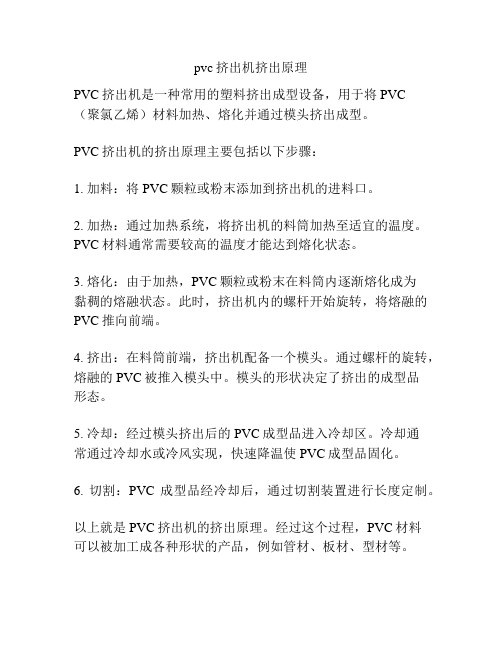
pvc挤出机挤出原理
PVC挤出机是一种常用的塑料挤出成型设备,用于将PVC
(聚氯乙烯)材料加热、熔化并通过模头挤出成型。
PVC挤出机的挤出原理主要包括以下步骤:
1. 加料:将PVC颗粒或粉末添加到挤出机的进料口。
2. 加热:通过加热系统,将挤出机的料筒加热至适宜的温度。
PVC材料通常需要较高的温度才能达到熔化状态。
3. 熔化:由于加热,PVC颗粒或粉末在料筒内逐渐熔化成为
黏稠的熔融状态。
此时,挤出机内的螺杆开始旋转,将熔融的PVC推向前端。
4. 挤出:在料筒前端,挤出机配备一个模头。
通过螺杆的旋转,熔融的PVC被推入模头中。
模头的形状决定了挤出的成型品
形态。
5. 冷却:经过模头挤出后的PVC成型品进入冷却区。
冷却通
常通过冷却水或冷风实现,快速降温使PVC成型品固化。
6. 切割:PVC成型品经冷却后,通过切割装置进行长度定制。
以上就是PVC挤出机的挤出原理。
经过这个过程,PVC材料
可以被加工成各种形状的产品,例如管材、板材、型材等。
电缆挤出工艺学

挤塑工艺塑料电线电缆的主要绝缘材料和护层材料是塑料。
热塑性塑料性能优越,具有良好的加工工艺性能,尤其是用于电线电缆挤制绝缘层和护层生产时工艺简便。
电线电缆塑料绝缘层和护层生产的基本方式是采用单螺杆挤出机连续挤压进行的。
由于挤出机具有连续挤出的特点,所以塑料绝缘和护套的生产过程也是连续进行的。
就电线电缆生查而言,产品规格的差异,挤制部件的不同,往往决定了挤制设备及工艺参数的某些变化。
但总的来讲,各种产品,各个部件的挤塑包覆工艺是大同小异的,下面以一般为主,个别为辅对挤塑原理、工艺与模具类型进行介绍。
第1节塑料的挤制塑料挤出的基本原理挤塑机的工作原理是:利用特定形状的螺杆,在加热的机筒中旋转,将由料斗中送来的塑料向前挤压,使塑料均匀的塑化(即熔融),通过机头和不同形状的模具,使塑料挤压成连续性的所需要的各种形状的塑料层,挤包在线芯和电缆上。
1. 塑料挤出过程电线电缆的塑料绝缘和护套使是采用连续挤压方式进行的,挤出设备一般是单螺杆挤塑机。
塑料在挤出前,要事先检查塑料是否潮湿或有无其它杂物,然后把螺杆预热后加入料斗内。
在挤出过程中,装入料斗中的塑料借助重力或加料螺旋进入机筒中,在旋转螺杆的推力作用下,不断向前推进,从预热段开始逐渐的向均化段运动;同时,塑料受到螺杆的搅拌和挤压作用,并且在机筒的外热及塑料与设备之间的剪切摩擦的作用下转变为粘流态,在螺槽中形成连续均匀的料流。
在工艺规定的温度作用下,塑料从固体状态转变为熔融状态的可塑物体,再经由螺杆的推动或搅拌,将完全塑化好的塑料推入机头;到达机头的料流,经模芯和模套间的环形间隙,从模套口挤出,挤包于导体或线芯周围,形成连续密实的绝缘层或护套层,然后经冷却和固化,制成电线电缆产品。
2. 挤出过程的三个阶段塑料挤出最主要的依据是塑料所具有的可塑态。
塑料在挤出机中完成可塑过程成型是一个复杂的物理过程,即包括了混合、破碎、熔融、塑化、排气、压实并最后成型定型。
大家值的注意的是这一过程是连续实现的。
电线电缆挤塑工艺

电线电缆挤塑工艺电线电缆挤塑工艺是一种重要的制造工艺,用于将金属、合金、塑料等材料挤压成各种形状的电线电缆产品。
挤塑工艺已经被广泛应用于各个行业,包括电子、电气、通讯、建筑、汽车、航空等领域。
本文将详细介绍电线电缆挤塑工艺的基本原理、工艺步骤和发展趋势。
一、电线电缆挤塑工艺的基本原理挤塑是一种通过施加高压将材料注入模具中,以形成所需的形状的加工方法。
电线电缆挤塑工艺就是利用挤塑工艺将金属、合金、塑料等材料挤压成各种电线电缆产品。
挤塑工艺基本上分为单挤塑和双挤塑两种形式。
单挤塑是将材料加热至软化温度,然后注入模具中,通过模具的形状来决定最终产品。
而双挤塑则需要预先制造一个内芯,然后将预热的材料包围在外面,再进行挤压。
这种挤塑工艺相对费时费力,但更加精细,制造出来的产品更加规整。
二、电线电缆挤塑工艺的工艺步骤电线电缆挤塑工艺的工艺步骤主要包括原材料准备、挤出、冷却、后处理和包装等五个步骤。
下面将逐步进行介绍:1、原材料准备:根据所需产品的材料特性,在生产线前段的料筒中添加相应材料,如聚乙烯、聚氯乙烯、聚酯等。
2、挤出:料筒中的材料由螺杆带动,在加热的环境下被挤出,通过挤压机头排出预定形状的产品。
3、冷却:挤出后的产品经过冷却装置冷却,以保持其形态和尺寸。
4、后处理:在产品冷却后,进行切断、拉伸和其他后处理操作。
这些操作可以根据具体产品的不同要求而有所不同。
5、包装:根据产品规格和要求进行包装,以便运输或储存。
三、电线电缆挤塑工艺的发展趋势随着科技进步和市场需求的日益增长,电线电缆挤塑工艺的发展正朝着更加智能、高效的方向发展。
1、自动化程度的提高:在挤塑生产线中,集成化与机械化设备的使用将使得挤塑工艺的效率、精度和稳定性更高。
2、新材料的应用:为了满足市场对新型电线电缆材料的需求,工艺中将逐渐引入具有特殊材质和具有特殊功能的材料,如防火、防水、抗电磁干扰等材料。
3、工艺的创新:采用新技术和新工艺,可以提高生产效率和产品质量,如挤出柔性电缆、挤出光导纤维等。
挤出成型工作原理

挤出成型工作原理
挤出成型是一种常见的塑料加工工艺,通过将加热熔化的塑料材料从模具的形核中挤出,使其形成所需的截面形状,然后冷却固化成型的工艺方法。
挤出成型工作原理简单而有效,被广泛应用于塑料制品的生产领域。
在挤出成型的工艺过程中,首先将塑料颗粒或粉末加入到挤出机的料斗中,通过螺杆转动推动料物向前。
在螺杆的作用下,塑料颗粒被逐渐加热熔化,并在螺杆作用力下形成高压熔体。
在螺杆和筛头的共同作用下,熔体通过模具的成型孔排出,使得熔体呈现出与模具截面相对应的形状。
同时,通过冷却水或风冷系统的作用,塑料熔体在模具中快速冷却固化,最终形成所需的挤出产品。
挤出成型工艺中的主要设备是挤出机,挤出机包括供料系统、螺杆和筛头、加热系统、传动系统等部分。
供料系统负责将塑料原料输送至螺杆中,螺杆和筛头起到将塑料熔体挤压成型的作用,加热系统用于提供足够的热能使塑料熔化,传动系统则保证挤出机各部件协调运转。
通过这些部件的有序协作,实现了挤出成型工艺的高效生产。
挤出成型具有工艺简单、生产效率高、制品精度高等优点,广泛应用于管材、板材、型材、各种塑料制品的生产中。
在实际生产中,挤出模具的设计和选材、挤出机的操作控制、制品的后续处理等环节都对挤出成型工艺起着至关重要的作用。
总的来说,挤出成型工作原理是利用挤出机将加热熔化的塑料通过模具挤出,再经过冷却固化形成成型的工艺过程。
挤出成型工艺简单高效,被广泛应用于各种塑料制品的生产中,推动了塑料加工行业的发展与进步。
1。
挤出原理简介

挤出原理简介!1、什么是塑料:塑料是高分子合成材料中凡是性能上具有可塑性变化的材料的总称,是以合成树脂为基本成份,再添加配合剂经捏合、造粒塑制成一定形状的材料。
塑料又分为热塑性塑料和热固性塑料。
热塑性塑料—线性结构、加热可重复软化。
如PVC、PE、PP等。
热固性塑料—立体网状结构、加热软化,冷却变硬,不可重复软化。
如XLPE等2、挤出机组的构成:放线装置、支撑架、校直或辅助牵引装置、主机(塑料挤出机)、冷却水槽、火花机、牵引机、计米器、收排线装置;机械传动部分;电器控制部分。
3、挤出机的构成:传动系统;加料装置及料斗、机筒、螺杆、加热装置、冷却装置、滤板、连接法兰、机头、模具;电器控制部分。
4、螺杆:4.1 螺杆的型式:螺杆是挤出机的心脏,主要有等距不等深型(45机用)、分离型(65、90机用)、销钉型、BM型等等。
4.2 螺杆的作用:螺杆的旋转产生剪切力使塑料破碎;螺杆的转动产生推动力使破碎的塑料连续前进并因此产生挤出压力;在挤出压力作用下,过滤板和压力所及的其它部位产生反作用力,造成塑料的迥流和搅拌,从而实现挤塑过程的全面均衡。
这一作用过程正是塑料实现均匀塑化的必要条件和充分条件。
4.3 螺杆的主要参数:压缩比、长径比;螺纹节距、螺峰宽度、螺旋角、圆弧角等4.3.1 压缩比:螺杆进出料端螺槽容积之比。
压缩比的存在是产生挤出压力的前提。
4.3.2 长径比:螺杆有效长度和其直径之比。
因为某一塑料的塑化温度是一个变化不大的温度区域,在一定温度下,决定塑化程度就是受热时间。
所以长径比大,可以有利于塑化、提高产量,但给制造、安装、使用都带来不便。
新型螺杆就是为了在满足塑料塑化的前提下,提高螺杆转速的。
5、过滤板:又叫筛板,往往与40目到80目的过滤网同时使用。
部件虽小,作用甚大:5.1 过滤作用:过滤掉含于塑料中的一切颗粒状杂质。
5.2 压力调节使用:产生挤出推力的反作用力,促使胶料产生迥流,而实现充分塑化。
塑料挤出的基本原理

塑料挤出的基本原理挤出机的工作原理是:利用特定形状的螺杆,在加热的机筒中旋转,将由料斗中送来的塑料向前挤压,使塑料均匀的塑化(即熔融),通过机头和不同形状的模具,使塑料挤压成连续性的所需要的各种形状的塑料层,挤包在线芯和电缆上。
1.塑料挤出过程电线电缆的塑料绝缘和护套使是采用连续挤压方式进行的,挤出设备一般是单螺杆挤出机。
塑料在挤出前,要事先检查塑料是否潮湿或有无其它杂物,然后把螺杆预热后加入料斗内。
在挤出过程中,装入料斗中的塑料借助重力或加料螺旋进入机筒中,在旋转螺杆的推力作用下,不断向前推进,从预热段开始逐渐的向均化段运动;同时,塑料受到螺杆的搅拌和挤压作用,并且在机筒的外热及塑料与设备之间的剪切摩擦的作用下转变为粘流态,在螺槽中形成连续均匀的料流。
在工艺规定的温度作用下,塑料从固体状态转变为熔融状态的可塑物体,再经由螺杆的推动或搅拌,将完全塑化好的塑料推入机头;到达机头的料流,经模芯和模套间的环形间隙,从模套口挤出,挤包于导体或线芯周围,形成连续密实的绝缘层或护套层,然后经冷却和固化,制成电线电缆产品。
2.挤出过程的三个阶段塑料挤出最主要的依据是塑料所具有的可塑态。
塑料在挤出机中完成可塑过程成型是一个复杂的物理过程,即包括了混合、破碎、熔融、塑化、排气、压实并最后成型定型。
大家值的注意的是这一过程是连续实现的。
然而习惯上,人们往往按塑料的不同反应将挤塑过程这一连续过程,人为的分成不同阶段,即为:塑化阶段(塑料的混合、熔融和均化);成型阶段(塑料的挤压成型);定型阶段(塑料层的冷却和固化)。
第一阶段是塑化阶段。
也称为压缩阶段。
它是在挤塑机机筒内完成的,经过螺杆的旋转作用,使塑料由颗粒状固体变为可塑性的粘流体。
塑料在塑化阶段取得热量的来源有两个方面:一是机筒外部的电加热;二是螺杆旋转时产生的摩擦热。
起初的热量是由机筒外部的电加热产生的,当正常开车后,热量的取得则是由螺杆选装物料在压缩、剪切、搅拌过程中与机筒内壁的摩擦和物料分子间的内摩擦而产生的。
电缆塑料绝缘挤出机的基本原理(doc 7页)

电缆塑料绝缘挤出机的基本原理(doc 7页)电缆塑料绝缘挤出机基本原理挤塑机的工作原理是:利用特定形状的螺杆,在加热的机筒中旋转,将由料斗中送来的塑料向前挤压,使塑料均匀的塑化(即熔融),通过机头和不同形状的模具,使塑料挤压成连续性的所需要的各种形状的塑料层,挤包在线芯和电缆上。
塑料挤出过程电线电缆的塑料绝缘和护套使是采用连续挤压方式进行的,挤出设备一般是单螺杆挤塑机。
塑料在挤出前,要事先检查塑料是否潮湿或有无其它杂物,然后把螺杆预热后加入料斗内。
在挤出过程中,装入料斗中的塑料借助重力或加料螺旋进入机筒中,在旋转螺杆的推力作用下,不断向前推进,从预热段开始逐渐的向均化段运动;同时,塑料受到螺杆的搅拌和挤压作用,并且在机筒的外热及塑料与设备之间的剪切摩擦的作用下转变为粘流态,在螺槽中形成连续均匀的料流。
在工艺规定的温度作用下,塑料从固体状态转变为熔融状态的可塑物体,再经由螺杆的推动或搅拌,将完全塑化好的塑料推入机头;到达机头的料流,经模芯和模套间的环形间隙,从模套口挤出,挤包于导体或线芯周围,形成连续密实的绝缘层或护套层,然后经冷却和固化,制成电线电缆产品。
挤出过程的三个阶段塑料挤出最主要的依据是塑料所具有的可塑态。
塑料在挤出机中完成可塑过程成型是一个复杂的物理过程,即包括了混合、破碎、熔融、塑化、排气、压实并最后成型定型。
大家值的注意的是这一过程是连续实现的。
然而习惯上,人们往往按塑料的不同反应将挤塑过程这一连续过程,人为的分成不同阶段,即为:塑化阶段(塑料的混合、熔融和均化);成型阶段(塑料的挤压成型);定型阶段(塑料层的冷却和固化)。
第一阶段是塑化阶段。
也称为压缩阶段。
它是在电线电缆挤塑机机筒内完成的,经过螺杆的旋转作用,使塑料由颗粒状固体变为可塑性的粘流体。
塑料在塑化阶段取得热量的来源有两个方面:一是机筒外部的电加热;二是螺杆旋转时产生的摩擦热。
起初的热量是由机筒外部的电加热产生的,当正常开车后,热量的取得则是由螺杆选装物料在压缩、剪切、搅拌过程中与机筒内壁的摩擦和物料分子间的内摩擦而产生的。
电缆塑料绝缘挤出机的基本原理
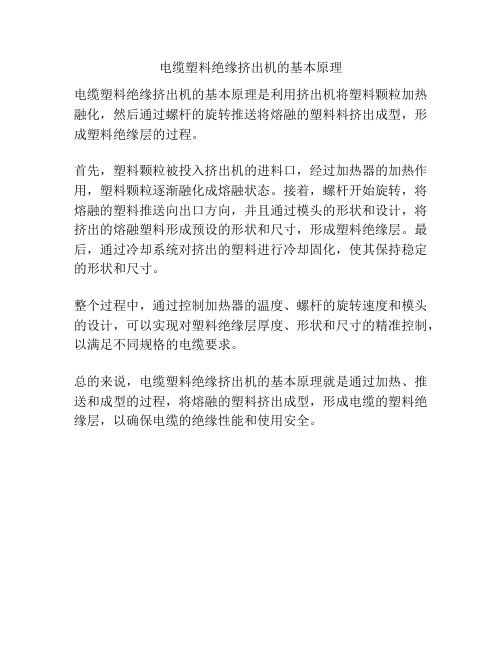
电缆塑料绝缘挤出机的基本原理
电缆塑料绝缘挤出机的基本原理是利用挤出机将塑料颗粒加热融化,然后通过螺杆的旋转推送将熔融的塑料料挤出成型,形成塑料绝缘层的过程。
首先,塑料颗粒被投入挤出机的进料口,经过加热器的加热作用,塑料颗粒逐渐融化成熔融状态。
接着,螺杆开始旋转,将熔融的塑料推送向出口方向,并且通过模头的形状和设计,将挤出的熔融塑料形成预设的形状和尺寸,形成塑料绝缘层。
最后,通过冷却系统对挤出的塑料进行冷却固化,使其保持稳定的形状和尺寸。
整个过程中,通过控制加热器的温度、螺杆的旋转速度和模头的设计,可以实现对塑料绝缘层厚度、形状和尺寸的精准控制,以满足不同规格的电缆要求。
总的来说,电缆塑料绝缘挤出机的基本原理就是通过加热、推送和成型的过程,将熔融的塑料挤出成型,形成电缆的塑料绝缘层,以确保电缆的绝缘性能和使用安全。
- 1、下载文档前请自行甄别文档内容的完整性,平台不提供额外的编辑、内容补充、找答案等附加服务。
- 2、"仅部分预览"的文档,不可在线预览部分如存在完整性等问题,可反馈申请退款(可完整预览的文档不适用该条件!)。
- 3、如文档侵犯您的权益,请联系客服反馈,我们会尽快为您处理(人工客服工作时间:9:00-18:30)。
挤塑机的工作原理是:利用特定形状的螺杆,在加热的机筒中旋转,将由料斗中送来的塑料向前挤压,使塑料均匀的塑化(即熔融),通过机头和不同形状的模具,使塑料挤压成连续性的所需要的各种形状的塑料层,挤包在线芯和电缆上。
塑料挤出过程
电线电缆的塑料绝缘和护套使是采用连续挤压方式进行的,挤出设备一般是单螺杆挤塑机。
塑料在挤出前,要事先检查塑料是否潮湿或有无其它杂物,然后把螺杆预热后加入料斗内。
在挤出过程中,装入料斗中的塑料借助重力或加料螺旋进入机筒中,在旋转螺杆的推力作用下,不断向前推进,从预热段开始逐渐的向均化段运动;同时,塑料受到螺杆的搅拌和挤压作用,并且在机筒的外热及塑料与设备之间的剪切摩擦的作用下转变为粘流态,在螺槽中形成连续均匀的料流。
在工艺规定的温度作用下,塑料从固体状态转变为熔融状态的可塑物体,再经由螺杆的推动或搅拌,将完全塑化好的塑料推入机头;到达机头的料流,经模芯和模套间的环形间隙,从模套口挤出,挤包于导体或线芯周围,形成连续密实的绝缘层或护套层,然后经冷却和固化,制成电线电缆产品。
挤出过程的三个阶段
塑料挤出最主要的依据是塑料所具有的可塑态。
塑料在挤出机中完成可塑过程成型是一个复杂的物理过程,即包括了混合、破碎、熔融、塑化、排气、压实并最后成型定型。
大家值的注意的是这一过程是连续实现的。
然而习惯上,人们往往按塑料的不同反应将挤塑过程这一连续过程,人为的分成不同阶段,即为:塑化阶段(塑料的混合、熔融和均化);成型阶段(塑料的挤压成型);定型阶段(塑料层的冷却和固化)。
第一阶段是塑化阶段。
也称为压缩阶段。
它是在挤塑机机筒内完成的,经过螺杆的旋转作用,使塑料由颗粒状固体变为可塑性的粘流体。
塑料在塑化阶段取得热量的来源有两个方面:一是机筒外部的电加热;二是螺杆旋转时产生的摩擦热。
起初的热量是由机筒外部的电加热产生的,当正常开车后,热量的取得则是由螺杆选装物料在压缩、剪切、搅拌过程中与机筒内壁的摩擦和物料分子间的内摩擦而产生的。
第二阶段是成型阶段。
它是在机头内进行的,由于螺杆旋转和压力作用,把粘流体推向机头,经机头内的模具,使粘流体成型为所需要的各种尺寸形状的挤包材料,并包覆在线芯或导体外。
第三阶段是定型阶段。
它是在冷却水槽或冷却管道中进行的,塑料挤包层经过冷却后,由无定型的塑性状态变为定型的固体状态。
塑化阶段塑料流动的变化
在塑化阶段,塑料沿螺杆轴向被螺杆推向机头的移动过程中,经历着温度、压力、粘度,甚至化学结构的变化,这些变化在螺杆的不同区段情况是不同的。
塑化阶段根据塑料流动时的物态变化过程又人为的分成三个阶段,即加料段、熔融段、均化段,这也是人们习惯上对挤出螺杆的分段方法,各段对塑料挤出产生不同的作用,塑料在各段呈现不同的形态,从而表现出塑料的挤出特性。
在加料段,首先就是为颗粒状的固体塑料提供软化温度,其次是以螺杆的旋转与固定的机筒之间产生的剪切应力作用在塑料颗粒上,实现对软化塑料的破碎。
而最主要的则是以螺杆旋转产生足够大的连续而稳定的推力和反向摩擦力,以形成连续而稳定的挤出压力,进而实现对破碎塑料的搅拌与均匀混合,并初步实行热交换,从而为连续而稳定的挤出提供基础。
在此阶段产生的推力是否连续均匀稳定、剪切应变率的高低,破碎与搅拌是否均匀都直接影响着挤出质量和产量。
在熔融段,经破碎、软化并初步搅拌混合的故态塑料,由于螺杆的推挤作用,沿螺槽向机头移动,自加料段进入熔融段。
在此段塑料遇到了较高温度的热作用,这是的热源,除机筒外部的点加热外,螺杆旋转的摩擦热也在起着作用。
而来自加料段的推力和来自均化段的反作用力,使塑料在前进中形成了回流,这
回流产生在螺槽内以及螺杆与机筒的间隙中,回流的产生不但使物料进一步均匀混合,而且使塑料热交换作用加大,达到了表面的热平衡。
由于在此阶段的作用温度已超过了塑料的流变温度,加之作用时间较长,致使塑料发生了物态的转变,与加热机筒接触的物料开始熔化,在机筒内表面形成一层聚合物熔膜,当熔膜的厚度超过螺纹顶与机筒之间的间隙时,就会被旋转的螺纹刮下来,聚集在推进螺纹的前面,形成熔池。
由于机筒和螺纹根部的相对运动,使熔池产生了物料的循环流动。
螺棱后面是固体床(固体塑料),物料沿螺槽向前移动的过程中,由于熔融段的螺槽深度向均化段逐渐变浅,固体床不断被挤向机筒内壁,加速了机筒向固体床的传热过程,同时螺杆的旋转对机筒内壁的熔膜产生剪切作用,从而使熔膜和固体床分界面的物料熔化,固体床的宽度逐渐减小,知道完全消失,即由固态转变为粘流态。
此时塑料分子结构发生了根本的改变,分子间张力极度松弛,若为结晶性高聚物,则其晶区开始减少,无定形增多,除其中的特大分子外,主体完成了塑化,即所谓的“初步塑化”,并且在压力的作用下,排除了固态物料中所含的气体,实现初步压实。
在均化段,具有这样几个突出的工艺特性:这一段螺杆螺纹深度最浅,即螺槽容积最小,所以这里是螺杆与机筒间产生压力最大的工作段;另外来自螺杆的推力和筛板等处的反作用力,是塑料“短兵相接”的直接地带;这一段又是挤出工艺温度最高的一段,所以塑料在此阶段所受到的径向压力和轴向压力最大,这种高压作用,足以使含于塑料内的全部气体排除,并使熔体压实,致密。
该段所具有的“均压段”之称即由此而得。
而由于高温的作用,使得经过熔融段未能塑化的高分子在此段完成塑化,从而最后消除“颗粒”,使塑料塑化充分均匀,然后将完全塑化熔融的塑料定量、定压的由机头均匀的挤出。
挤出过程中塑料的流动状态
在挤出过程中,由于螺杆的旋转使塑料推移,而机筒是不动的,这就在机筒和螺杆之间产生相对运动,这种相对运动对塑料产生摩擦作用,使塑料被拖着前进。
另外,由于机头中的模具、多孔筛板和滤网的阻力,又使塑料在前进中产生反作用力,这就使塑料在螺杆和机筒中的流动复杂化了。
通常将塑料的流动状态看成是由以下四种流动形式组成的:
正流――是指塑料沿着螺杆螺槽向机头方向的流动。
它是螺杆旋转的推挤力产生的,是四种流动形式中最主要的一种。
正流量的大小直接决定着挤出量。
倒流――又称逆流,它的方向与正流的流动方向整好相反。
它是由于机头中的模具、筛板、和滤网等阻碍塑料的正向运动,在机头区域里产生的压力(塑料前进的反作用力)造成的。
由机头至加料口形成了“压力下的回流”,也称为“反压流动”。
它能引起生产能力的损失。
横流――它是沿着轴的方向,即与螺纹槽相垂直方向的塑料流动。
也是由螺杆旋转时的推挤所形成的。
它的流动受到螺纹槽侧壁的阻力,由于两侧螺纹的相互阻力,而螺杆是在旋转中,使塑料在螺槽内产生翻转运动,形成环状流动,所以横流实质是环流。
环流对塑料在机筒中的混合、塑化成熔融状态,是和环流的作用分不开的。
环流使物料在机筒中产生搅拌和混合,并且利于机筒和物料的热交换,它对提高挤出质量有重要的意义,但对挤出流率的影响很小。
漏流――它也是由机头中模具、筛板和滤网的阻力产生的。
不过它不是螺槽中的流动,而是在螺杆与机筒的间隙中形成的倒流。
它也能引起生产能力的损失。
由于螺杆与机筒的间隙通常很小,故在正常情况下,漏流流量要比正流和倒流小的多。
在挤出过程中,漏流将影响挤出量,漏流量增大,挤出量将减小。
塑料的四种流动状态不会以单独的形式出现,就某一塑料质点来说,既不会有真正的倒流,也不会有封闭的环流。
熔体塑料在螺纹槽中的实际流动是上述四种流动状态的综合,以螺旋形轨迹向前的一种流动。
挤出质量
挤出质量主要指塑料的塑化情况是否良好,几何尺寸是否均一,即径向厚度是否一致,轴向外径是否均匀。
决定塑化情况的因袭除塑料本身外,主要是温度和剪切应变率及作用时间等因素。
挤出温度过高不但造成挤出压力的波动,而且导致塑料的分解,甚至可能酿成设备事故。
而减小螺槽深度,增大螺杆长径比,虽然有利于塑料的热交换和延长受热时间,满足塑化均匀要求,但将影响挤出量,又为螺杆制造和装配造成困难。
所以确保塑化的重要因素应是提高螺杆旋转对塑料所产生的剪切应变率,以达到机械混合均匀,挤出热交换均衡,并由此为塑化均匀提供保障。
这个应变率的大小由螺杆与机筒间的剪切应变力所决定,在保证挤出量的要求下,可以在提高转速的情况下加大螺槽深度。
此外,螺杆与机筒的间隙也对挤出质量有影响,间隙过大时则塑料的倒流、漏流增加,不但引起挤出压力波动,影响挤出量;而且由于这些回流的增加,使塑料过热而导致塑料焦烧或成型困难。