腐蚀管道剩余寿命预测原则
油气管道腐蚀检测及剩余寿命预测
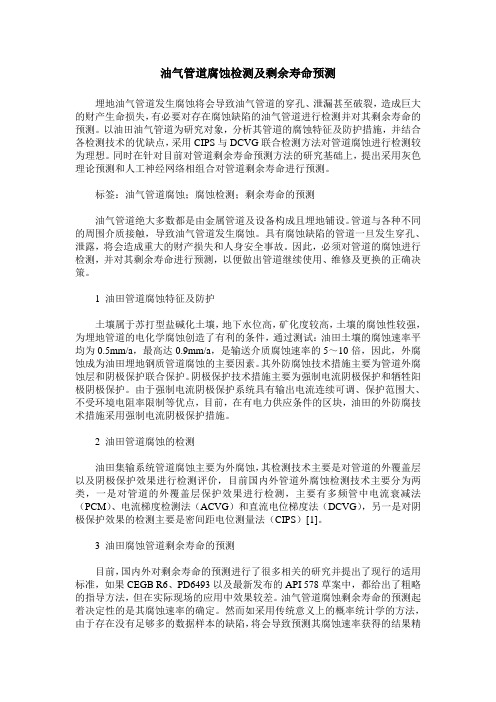
油气管道腐蚀检测及剩余寿命预测埋地油气管道发生腐蚀将会导致油气管道的穿孔、泄漏甚至破裂,造成巨大的财产生命损失,有必要对存在腐蚀缺陷的油气管道进行检测并对其剩余寿命的预测。
以油田油气管道为研究对象,分析其管道的腐蚀特征及防护措施,并结合各检测技术的优缺点,采用CIPS与DCVG联合检测方法对管道腐蚀进行检测较为理想。
同时在针对目前对管道剩余寿命预测方法的研究基础上,提出采用灰色理论预测和人工神经网络相组合对管道剩余寿命进行预测。
标签:油气管道腐蚀;腐蚀检测;剩余寿命的预测油气管道绝大多数都是由金属管道及设备构成且埋地铺设。
管道与各种不同的周围介质接触,导致油气管道发生腐蚀。
具有腐蚀缺陷的管道一旦发生穿孔、泄露,将会造成重大的财产损失和人身安全事故。
因此,必须对管道的腐蚀进行检测,并对其剩余寿命进行预测,以便做出管道继续使用、维修及更换的正确决策。
1 油田管道腐蚀特征及防护土壤属于苏打型盐碱化土壤,地下水位高,矿化度较高,土壤的腐蚀性较强,为埋地管道的电化学腐蚀创造了有利的条件,通过测试:油田土壤的腐蚀速率平均为0.5mm/a,最高达0.9mm/a,是输送介质腐蚀速率的5~10倍,因此,外腐蚀成为油田埋地钢质管道腐蚀的主要因素。
其外防腐蚀技术措施主要为管道外腐蚀层和阴极保护联合保护。
阴极保护技术措施主要为强制电流阴极保护和牺牲阳极阴极保护。
由于强制电流阴极保护系统具有输出电流连续可调、保护范围大、不受环境电阻率限制等优点,目前,在有电力供应条件的区块,油田的外防腐技术措施采用强制电流阴极保护措施。
2 油田管道腐蚀的检测油田集输系统管道腐蚀主要为外腐蚀,其检测技术主要是对管道的外覆盖层以及阴极保护效果进行检测评价,目前国内外管道外腐蚀检测技术主要分为两类,一是对管道的外覆盖层保护效果进行检测,主要有多频管中电流衰减法(PCM)、电流梯度检测法(ACVG)和直流电位梯度法(DCVG),另一是对阴极保护效果的检测主要是密间距电位测量法(CIPS)[1]。
7、剩余强度评估和剩余寿命预测计算过程
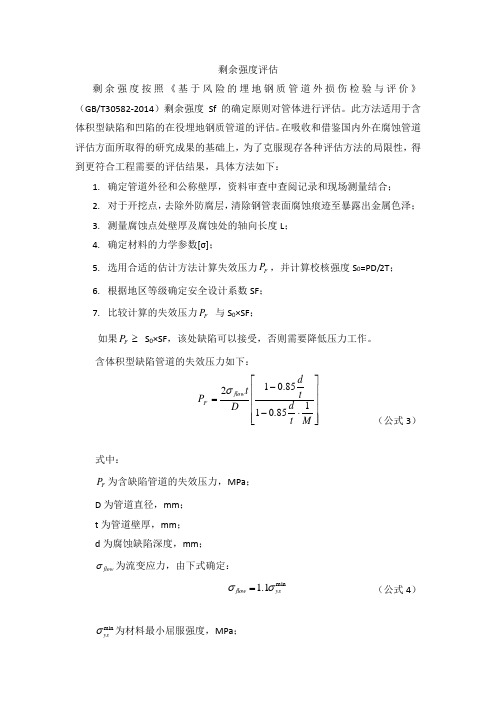
剩余强度评估剩余强度按照《基于风险的埋地钢质管道外损伤检验与评价》 (GB/T30582-2014)剩余强度Sf 的确定原则对管体进行评估。
此方法适用于含体积型缺陷和凹陷的在役埋地钢质管道的评估。
在吸收和借鉴国内外在腐蚀管道评估方面所取得的研究成果的基础上,为了克服现存各种评估方法的局限性,得到更符合工程需要的评估结果,具体方法如下:1. 确定管道外径和公称壁厚,资料审查中查阅记录和现场测量结合;2. 对于开挖点,去除外防腐层,清除钢管表面腐蚀痕迹至暴露出金属色泽;3. 测量腐蚀点处壁厚及腐蚀处的轴向长度L ;4. 确定材料的力学参数[σ];5. 选用合适的估计方法计算失效压力F P ,并计算校核强度S 0=PD/2T ;6. 根据地区等级确定安全设计系数SF ;7. 比较计算的失效压力F P 与S 0×SF ;如果≥F P S 0×SF ,该处缺陷可以接受,否则需要降低压力工作。
含体积型缺陷管道的失效压力如下:(公式3)式中:F P 为含缺陷管道的失效压力,MPa ;D 为管道直径,mm ;t 为管道壁厚,mm ;d 为腐蚀缺陷深度,mm ;flow σ为流变应力,由下式确定:(公式4)min ysσ为材料最小屈服强度,MPa ; ⎥⎥⎥⎥⎦⎤⎢⎢⎢⎢⎣⎡⋅--=M t d t d D t P flow F 185.0185.012σmin 1.1ys flow σσ=M 为Folias 膨胀系数,由下式确定: 50)/(2>Dt L (公式5) 50)/(2≤Dt L (公式6)L 为缺陷长度,mm 。
管道运行压力不得超过最大允许工作压力,最大允许工作压力为:F P K p ⋅=p 为管道最大允许工作压力,MPa ;K 为设计系数,应根据管道内的介质类型、缺陷及所在处的地区级别等确定。
本次受检埋地管道共发现防腐层漏电点21处。
受检单位对15个已打孔检漏处理的漏电点处进行了燃气泄漏检测,结果未发现燃气泄漏;对4处漏电点进行了开挖修复;其余2处漏电点处于水中,无法打孔检漏,观察水面未发现泄漏气泡。
腐蚀管道的失效概率和剩余寿命预测方法

对于埋地管道 ,腐蚀导致管壁减薄和引起局部 应力集中 ,是影响系统可靠性及使用寿命的关键因 素 ,由于存在着许多不确定因素 ,管道失效概率和腐 蚀剩余寿命的预测工作有很大难度 。最近的研究结 果表明 ,可靠性评估方法不失为一种理想的失效概 率和腐蚀剩余寿命的预测方法 。
-
n
∑
i=1
-
5g
5
∧
xi
P 3 ·x∧i3
+ g σ x∧13 x1 +μx1 , …, x∧n3σx n +μx n
=0
n
∑
i=1
5g
5
∧
xi
P3
2
n
∑
5g
i =1 5 xi
P3
2
(14)
式 (14) 第二项的绝对值即坐标原点 0′至切平 面的最短距离β, 点 P3 ( x∧13 , x∧23 …, x∧n3 ) 在极限状
+μx2
,
…,
σ ∧
x n xn
+μxn )
= 0 。该方程表示在
新坐标系下的极限状态超曲面中 ( 见图 1) , 该曲面
将
∧
xi
空间分为安全区和失效区
。
图 1 可靠度与极限状态曲面的关系
由新坐标系的原点 0′向极限状态曲面引一条
垂线 ,交曲面上一点
P3
∧∧
( x1 , x2 ,
…,
∧
xn
)
, 该交点称
图 3 可靠性指标与管道服役时间的关系
图 2 一阶二次矩方法求解β程序框图
三 、工程实例
我国北方某管道钢管为 16Mn 螺旋焊管 ,屈服 强度为 353 M Pa ,管径为 529 mm ,壁厚为 7 mm ,已 运行近 30 年 。根据工程的需要 ,对该管道进行了安
埋地输油管道腐蚀原因分析及剩余寿命预测方法概述
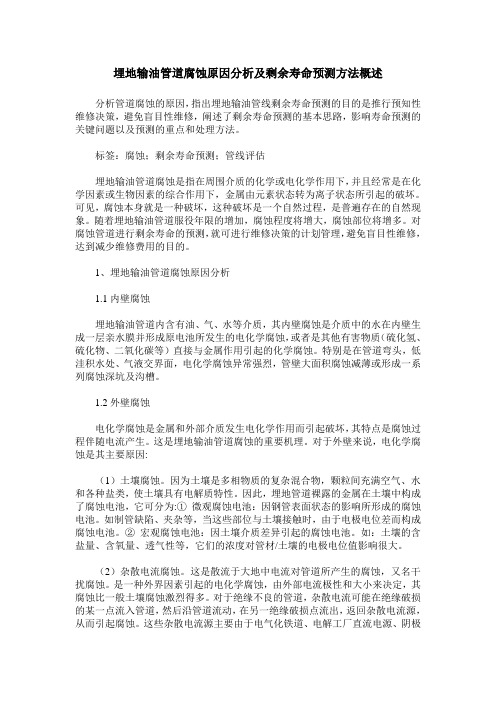
埋地输油管道腐蚀原因分析及剩余寿命预测方法概述分析管道腐蚀的原因,指出埋地输油管线剩余寿命预测的目的是推行预知性维修决策,避免盲目性维修,阐述了剩余寿命预测的基本思路,影响寿命预测的关键问题以及预测的重点和处理方法。
标签:腐蚀;剩余寿命预测;管线评估埋地输油管道腐蚀是指在周围介质的化学或电化学作用下,并且经常是在化学因素或生物因素的综合作用下,金属由元素状态转为离子状态所引起的破坏。
可见,腐蚀本身就是一种破坏,这种破坏是一个自然过程,是普遍存在的自然现象。
随着埋地输油管道服役年限的增加,腐蚀程度将增大,腐蚀部位将增多。
对腐蚀管道进行剩余寿命的预测,就可进行维修决策的计划管理,避免盲目性维修,达到减少维修费用的目的。
1、埋地输油管道腐蚀原因分析1.1内壁腐蚀埋地输油管道内含有油、气、水等介质,其内壁腐蚀是介质中的水在内壁生成一层亲水膜并形成原电池所发生的电化学腐蚀,或者是其他有害物质(硫化氢、硫化物、二氧化碳等)直接与金属作用引起的化学腐蚀。
特别是在管道弯头,低洼积水处、气液交界面,电化学腐蚀异常强烈,管壁大面积腐蚀减薄或形成一系列腐蚀深坑及沟槽。
1.2外壁腐蚀电化学腐蚀是金属和外部介质发生电化学作用而引起破坏,其特点是腐蚀过程伴随电流产生。
这是埋地输油管道腐蚀的重要机理。
对于外壁来说,电化学腐蚀是其主要原因:(1)土壤腐蚀。
因为土壤是多相物质的复杂混合物,颗粒间充满空气、水和各种盐类,使土壤具有电解质特性。
因此,埋地管道裸露的金属在土壤中构成了腐蚀电池,它可分为:①微观腐蚀电池:因钢管表面状态的影响所形成的腐蚀电池。
如制管缺陷、夹杂等,当这些部位与土壤接触时,由于电极电位差而构成腐蚀电池。
②宏观腐蚀电池:因土壤介质差异引起的腐蚀电池。
如:土壤的含盐量、含氧量、透气性等,它们的浓度对管材/土壤的电极电位值影响很大。
(2)杂散电流腐蚀。
这是散流于大地中电流对管道所产生的腐蚀,又名干扰腐蚀。
是一种外界因素引起的电化学腐蚀,由外部电流极性和大小来决定,其腐蚀比一般土壤腐蚀激烈得多。
腐蚀管道剩余寿命预测原则
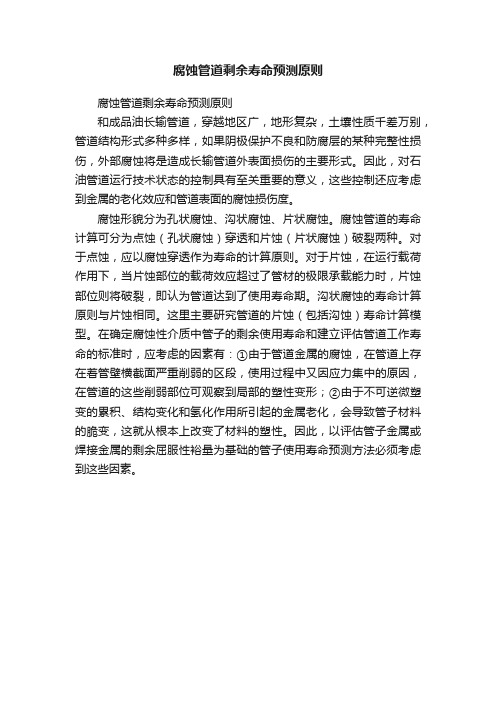
腐蚀管道剩余寿命预测原则
腐蚀管道剩余寿命预测原则
和成品油长输管道,穿越地区广,地形复杂,土壤性质千差万别,管道结构形式多种多样,如果阴极保护不良和防腐层的某种完整性损伤,外部腐蚀将是造成长输管道外表面损伤的主要形式。
因此,对石油管道运行技术状态的控制具有至关重要的意义,这些控制还应考虑到金属的老化效应和管道表面的腐蚀损伤度。
腐蚀形貌分为孔状腐蚀、沟状腐蚀、片状腐蚀。
腐蚀管道的寿命计算可分为点蚀(孔状腐蚀)穿透和片蚀(片状腐蚀)破裂两种。
对于点蚀,应以腐蚀穿透作为寿命的计算原则。
对于片蚀,在运行载荷作用下,当片蚀部位的载荷效应超过了管材的极限承载能力时,片蚀部位则将破裂,即认为管道达到了使用寿命期。
沟状腐蚀的寿命计算原则与片蚀相同。
这里主要研究管道的片蚀(包括沟蚀)寿命计算模型。
在确定腐蚀性介质中管子的剩余使用寿命和建立评估管道工作寿命的标准时,应考虑的因素有:①由于管道金属的腐蚀,在管道上存在着管壁横截面严重削弱的区段,使用过程中又因应力集中的原因,在管道的这些削弱部位可观察到局部的塑性变形;②由于不可逆微塑变的累积、结构变化和氢化作用所引起的金属老化,会导致管子材料的脆变,这就从根本上改变了材料的塑性。
因此,以评估管子金属或焊接金属的剩余屈服性裕量为基础的管子使用寿命预测方法必须考虑到这些因素。
石油集输管道腐蚀剩余预测研究
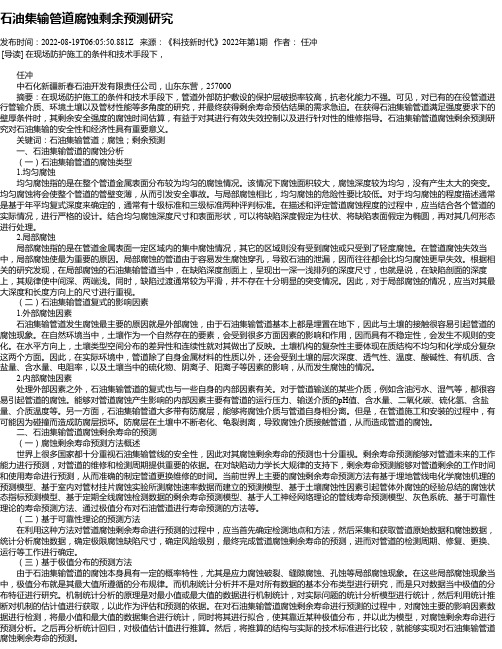
石油集输管道腐蚀剩余预测研究发布时间:2022-08-19T06:05:50.881Z 来源:《科技新时代》2022年第1期作者:任冲[导读] 在现场防护施工的条件和技术手段下,任冲中石化新疆新春石油开发有限责任公司,山东东营,257000摘要:在现场防护施工的条件和技术手段下,管道外部防护敷设的保护层破损率较高,抗老化能力不强。
可见,对已有的在役管道进行管输介质、环境土壤以及管材性能等多角度的研究,并最终获得剩余寿命预估结果的需求急迫。
在获得石油集输管道满足强度要求下的壁厚条件时,其剩余安全强度的腐蚀时间估算,有益于对其进行有效失效控制以及进行针对性的维修指导。
石油集输管道腐蚀剩余预测研究对石油集输的安全性和经济性具有重要意义。
关键词:石油集输管道;腐蚀;剩余预测一、石油集输管道的腐蚀分析(一)石油集输管道的腐蚀类型 1.均匀腐蚀均匀腐蚀指的是在整个管道金属表面分布较为均匀的腐蚀情况。
该情况下腐蚀面积较大,腐蚀深度较为均匀,没有产生太大的突变。
均匀腐蚀将会使整个管道的管壁变薄,从而引发安全事故。
与局部腐蚀相比,均匀腐蚀的危险性要比较低。
对于均匀腐蚀的程度描述通常是基于年平均复式深度来确定的,通常有十级标准和三级标准两种评判标准。
在描述和评定管道腐蚀程度的过程中,应当结合各个管道的实际情况,进行严格的设计。
结合均匀腐蚀深度尺寸和表面形状,可以将缺陷深度假定为柱状、将缺陷表面假定为椭圆,再对其几何形态进行处理。
2.局部腐蚀局部腐蚀指的是在管道金属表面一定区域内的集中腐蚀情况,其它的区域则没有受到腐蚀或只受到了轻度腐蚀。
在管道腐蚀失效当中,局部腐蚀使最为重要的原因。
局部腐蚀的管道由于容易发生腐蚀穿孔,导致石油的泄漏,因而往往都会比均匀腐蚀更早失效。
根据相关的研究发现,在局部腐蚀的石油集输管道当中,在缺陷深度剖面上,呈现出一深一浅排列的深度尺寸,也就是说,在缺陷剖面的深度上,其规律使中间深、两端浅。
同时,缺陷过渡通常较为平滑,并不存在十分明显的突变情况。
腐蚀管道剩余寿命预测方法

中 图 分 类 号 :E 8 T 8 文 献 标 识 码 : A 文 章 编 号 :04 64 20 )5 0 7 0 10 —9 1(060 —0 3 — 3
Ab ta t B s d o e rl b ly te r , rs n e e to rte rmann f rdcin o o rd d p p l e T e meh d s r c : a e n t ei it h o y p ee td a n w meh d f e iig l ep e it fc r e i ei . h t h a i o h i o o n o
icu e s bi ig tel t a efn t n o or d d p p l e h r b b ly ds iu i d l f aibe u h a o rs n v lc n l s e t l hn mi d s t ci f r e iei ,tep o a i t it b t n mo e o r lss c sc r i e . d a s h i e l u o c o n i r o s v a oo o i n h al ep o a i t r eibl yv r e 8 lie t fc r d d pp l e h e iig le p n o o rd d pp l e( 3 b t a d te fi r r b b ly o l i t es t  ̄'e me o or e iei .T e rmann fs a f ro e iei  ̄ 1 e y u i r a i e h v i o n i c n 8 c luae . sln s te a c pa l alr rb bl y O ag t eibly i d tr n d a c r ig t h n io me tlc n i o s a d ac ltd a g a h c e tbe fi e p o a i t r tre l i t s e mie c o dn o t e e vrn na o dt n n o u i r a i e i
输油管道腐蚀缺陷评估与剩余寿命预测

蚀 速 率计 算 公 式 。 结合 容 限尺 寸模 型对 腐蚀 缺 陷部位 的剩 余 强度 进 行 了评 价 ,采 用概 率 的 方 法
对局部管道进行 了失效概率的预测计算。结果表 明:该输 油管道 的腐蚀较 为严重 ,在 目前的工 作压力下,管段 上的中度缺 陷有一定的安全余量 ,对管道的安全操作不构成威胁 ;但在设 计压 力下 ,一 些 中度 缺 陷 的剩余 强度 不 能满 足要 求 ,需要 进一 步评 估 。
第3 4 卷第 8 期 ( 2 0 1 5 . 0 8 )( 试验 研 究)
输油管道腐蚀缺陷评估与剩余寿命预测
代辉 ’ 杨磊 李涛。 田知 密 徐 方
1长庆 油 田采油 八 厂 2新 疆 油 田分 公 司 陆梁油 田作 业 区 3新疆 油 田分公 司石西 服极 限 ( MP a ) 。
2 腐蚀缺 陷的评估
2 . 1 剩 余强 度评 估 方法
2 . 2 容 限尺 寸 曲线
管道设计压力为 6 MP a ,当前工作 压力为 4 . 6 MP a ,
管道的腐蚀主要受环境和结构因素的影 响,缺 比设 计压力低 。图 2 为建立 的管 道 的容 限尺寸 曲 陷 的长 度 和 深度 是 估 算 失 效 程 度 的两 个 关 键 参 数 。 线 ,在 曲线 下 方为 安全 区域 ,如 果 缺 陷位置 在 曲线 图1 所示为理想缺陷的截面示意图闭 。 以下 ,说明该缺陷可在管道容忍 的位置上 ,即正常
式 中 为 管 材 的流 变应 力 ( MP a ) ; D为 直 径 也就是在管道 的上顶部附近 ;绝大部分缺陷集 中在 ( mm) ;t 为壁 厚 ( mm) ; d为 缺 陷深 度 ( m i l 1 ) ;Z 中 间 ,即管 道 下 部 4  ̄ 7 时钟 点位 置 ,这是 由于底 部 为 缺 陷长度 ( mm) ; M 为 鼓胀 因子 ; S MY S为对 管 的管道容易积水 ,从而导致电化学腐蚀的缘故 。
- 1、下载文档前请自行甄别文档内容的完整性,平台不提供额外的编辑、内容补充、找答案等附加服务。
- 2、"仅部分预览"的文档,不可在线预览部分如存在完整性等问题,可反馈申请退款(可完整预览的文档不适用该条件!)。
- 3、如文档侵犯您的权益,请联系客服反馈,我们会尽快为您处理(人工客服工作时间:9:00-18:30)。
腐蚀管道剩余寿命预测原则
和成品油长输管道,穿越地区广,地形复杂,土壤性质千差万别,管道结构形式多种多样,如果阴极保护不良和防腐层的某种完整性损伤,外部腐蚀将是造成长输管道外表面损伤的主要形式。
因此,对石油管道运行技术状态的控制具有至关重要的意义,这些控制还应考虑到金属的老化效应和管道表面的腐蚀损伤度。
腐蚀形貌分为孔状腐蚀、沟状腐蚀、片状腐蚀。
腐蚀管道的寿命计算可分为点蚀(孔状腐蚀)穿透和片蚀(片状腐蚀)破裂两种。
对于点蚀,应以腐蚀穿透作为寿命的计算原则。
对于片蚀,在运行载荷作用下,当片蚀部位的载荷效应超过了管材的极限承载能力时,片蚀部位则将破裂,即认为管道达到了使用寿命期。
沟状腐蚀的寿命计算原则与片蚀相同。
这里主要研究管道的片蚀(包括沟蚀)寿命计算模型。
在确定腐蚀性介质中管子的剩余使用寿命和建立评估管道工作寿命的标准时,应考虑的因素有:①由于管道金属的腐蚀,在管道上存在着管壁横截面严重削弱的区段,使用过程中又因应力集中的原因,在管道的这些削弱部位可观察到局部的塑性变形;②由于不可逆微塑变的累积、结构变化和氢化作用所引起的金属老化,会导致管子材料的脆变,这就从根本上改变了材料的塑性。
因此,以评估管子金属或焊接金属的剩余屈服性裕量为基础的管子使用寿命预测方法必须考虑到这些因素。