冲压模具课程设计
冲压模具课程设计说明书 2
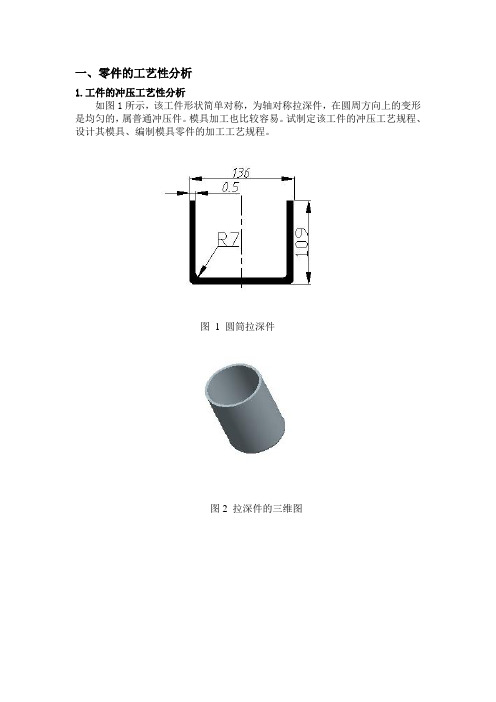
一、零件的工艺性分析1.工件的冲压工艺性分析如图1所示,该工件形状简单对称,为轴对称拉深件,在圆周方向上的变形是均匀的,属普通冲压件。
模具加工也比较容易。
试制定该工件的冲压工艺规程、设计其模具、编制模具零件的加工工艺规程。
图1 圆筒拉深件图2 拉深件的三维图2.工件材料化学成分和机械性能分析(1)材料分析工件的材料为08钢,属于优质碳素结构钢,优质沸腾钢,强度、硬度低,冷变形塑性很好,可深冲压加工,焊接性好。
成分偏析倾向大,时效敏感性大,故冷加工时应采用消除应力热处理或水韧处理,防止冷加工断裂。
08钢的主要机械性能如下:σ(兆帕) 280-390抗拉强度bσ(兆帕) 180屈服强度s抗剪强度(兆帕) 220-310延伸率δ 32%(2)结构分析工件为一窄凸缘筒形件,结构简单,圆角半径为r=7,厚度为t=0.5mm,满足筒形拉深件底部圆角半径大于一倍料厚的要求,因此,零件具有良好的结构工艺性。
(3)精度分析工件上尺寸均为未注公差尺寸,普通拉深即可达到零件的精度要求。
经上述分析,产品的材料性能符合冷冲压加工要求。
在零件工艺性分析的基础上制定其工艺路线如下:零件的生产包括落料、拉深(需计算确定拉深次数)、修边(采用机械加工)等工序,为了提高生产效率,可以考虑工序的复合,经比较决定采用落料与第一次拉深复合。
二、工件的拉深工艺分析及计算1.毛坯尺寸计算(1)计算原则相似原则:拉深前坯料的形状与拉深件断面形状相似;等面积原则:拉深前坯料面积与拉深件面积相等。
(2)计算方法由以上原则可知,旋转体拉深件采用圆形毛坯,其直径按面积相等的原则计算。
计算坯料尺寸时,先将拉深件划分为若干便于计算的简单几何体,分别求出其面积后相加,得拉深件总面积A。
图3 拉深件的坯料计算如图3所示,筒形件坯料尺寸,将圆筒件分成三个部分,每个部分面积分别为:(3)确定零件修边余量由于板料的各向异性和模具间隙不均等因素的影响,拉深后零件的边缘不整齐,甚至出现耳子,需在拉伸后进行修边。
邯郸冲压模具课程设计

邯郸冲压模具课程设计一、课程目标知识目标:1. 让学生掌握冲压模具的基本结构及其工作原理,理解模具在邯郸制造业中的应用;2. 使学生了解并掌握冲压模具的材料选择、设计要点及制造工艺;3. 帮助学生掌握模具故障分析与维修方法,提高模具使用效率。
技能目标:1. 培养学生运用CAD/CAM软件进行冲压模具设计的能力;2. 提高学生动手实践能力,能够独立完成模具的拆装、调试与维护;3. 培养学生分析实际生产问题,提出合理解决方案的能力。
情感态度价值观目标:1. 培养学生热爱制造业,增强对模具行业的职业认同感;2. 培养学生团队协作精神,提高沟通与交流能力;3. 增强学生环保意识,关注模具行业的可持续发展。
课程性质分析:本课程为实践性较强的专业课,注重理论知识与实际操作相结合。
学生特点分析:学生为高年级中职学生,具备一定的机械基础知识和动手能力。
教学要求:结合学生特点,注重启发式教学,理论联系实际,提高学生综合运用知识的能力。
通过课程学习,使学生能够达到上述具体、可衡量的学习成果,为后续教学设计和评估提供依据。
二、教学内容1. 冲压模具基础知识:- 模具的分类、结构及工作原理;- 冲压模具在邯郸制造业中的应用案例。
2. 冲压模具设计:- 模具材料的选择与性能要求;- 模具设计的基本原则与要点;- 利用CAD/CAM软件进行模具设计。
3. 冲压模具制造工艺:- 模具制造工艺流程;- 常用加工方法及设备;- 质量控制与检测。
4. 模具故障分析与维修:- 常见模具故障类型及原因;- 故障诊断与维修方法;- 模具维护与保养。
5. 实践教学环节:- 模具拆装与调试;- 模具加工与制造;- 模具故障分析与维修实践。
教材章节及内容安排:第一章:冲压模具基础知识(1课时)第二章:冲压模具设计(2课时)第三章:冲压模具制造工艺(2课时)第四章:模具故障分析与维修(2课时)第五章:实践教学环节(4课时)教学进度安排:1. 前四章节共计8课时,每周2课时,共计4周;2. 第五章节实践教学环节共计4课时,在第5周进行;3. 期末安排1课时进行课程总结与复习。
冲压模具课程设计

目录一、设计任务书 (2)二、冲压工艺性及工艺方案的确定 (3)三、主要设计计算 (4)四、模具总体设计 (8)五、主要零部件设计 (8)六、冲压设备的选定 (12)七、设计小结 (13)八、参考文献 (13)一、课程设计任务批量:大批量二、任务内容:(一)工艺设计1、工艺审查与工艺分析2、工艺计算:①毛胚计算②工序件计算或排样图3、工艺方案的确定①工序的确定基准和定位方式的选择(二)模具设计1、总图2、零件图二、冲压工艺性及工艺方案的确定一、工艺性分析1、材料零件的材料为H68普通黄铜,具有良好的冲压性能,适合冲裁。
2、结构该零件属于较典型冲裁件,形状简单对称。
3、精度材料厚度1.5mm,冲裁断面的近似表面粗糙度为6.3um4、结论可以冲裁。
二、冲压工艺方案的确定该零件包括落料、冲孔两个基本工序,可以采用以下三种工艺方案:方案①:先落料、再冲孔。
采用单工序模生产。
方案②:落料—冲孔复合冲压。
采用复合模生产。
方案③:冲孔—落料级进冲压。
采用级进模生产。
方案①模具结构简单,但需要两道工序、两套模具才能完成零件的加工,生产效率较低,难以满足零件大批量生产的需求。
方案②只需要一套模具,冲压件的形位精度和尺寸易于保证,且生产效率也高。
尽管模具结构较方案①复杂,但由于零件的几何形状简单对称,模具制造并不困难。
方案③也只需要一套模具,生产效率高,但零件的冲压精度不易保证。
通过以上三种方案的分析比较,对该冲压件生产以采用方案②为佳。
三、主要设计计算1.排样方式的确定及计算查表查得:取两工件间的最小搭边:a=1.8mm,侧面搭边值:a1=2.2mm.条料宽度公差Δ=0.5条料宽度:B=(20+2×2.2+0.5)=24.9进距:A=5+1.8=6.8可选1.5mm×900mm×2000mm的板料。
考虑到材料轧制方向,材料横裁,于是每张板料可裁条料数为n1=2000×24.9=80,余8mm单方向每条条料可冲制件数为n2=900×6.8=132,余2.4mm每张板料可冲制个数n 总=n 1×n 2=80×132=10560(件)一个步距的材料利用率:%100h n ⨯=B A η式中 A —一个冲裁件的面积,mm 2n —一个步距内的冲裁件数量;B —条料宽度,mm;h —进距, mm%1008.69.24214561⨯⨯⨯⨯⨯=)+(η=38.31% 已知条料宽度25.40-0.5mm ,步距6.8mm 。
冲压模具设计课程设计08f

冲压模具设计课程设计08f一、教学目标本课程的教学目标是使学生掌握冲压模具设计的基本原理和方法,能够运用相关软件进行模具设计,并具备一定的创新能力和团队协作能力。
具体分为以下三个部分:1.知识目标:学生需要掌握冲压模具的基本结构、工作原理、设计方法和工艺流程,以及相关软件的使用方法。
2.技能目标:学生能够运用冲压模具设计软件进行模具设计,并能够独立完成简单的模具设计项目。
3.情感态度价值观目标:学生应该培养良好的工程职业道德,具备团队合作精神,勇于创新和接受挑战。
二、教学内容本课程的教学内容主要包括冲压模具的基本原理、模具设计方法、模具制造工艺以及相关软件的使用。
具体安排如下:1.冲压模具的基本原理:介绍冲压模具的定义、分类和基本结构,以及冲压成形的基本原理。
2.模具设计方法:讲解模具设计的过程和方法,包括模具零件的设计、模具整体结构的设计和模具材料的选用。
3.模具制造工艺:介绍模具制造的整个工艺流程,包括模具加工、热处理和装配等。
4.相关软件的使用:教授如何运用冲压模具设计软件进行模具设计,包括软件的基本操作和设计方法。
三、教学方法为了提高学生的学习兴趣和主动性,本课程将采用多种教学方法相结合的方式进行教学。
具体包括:1.讲授法:通过讲解冲压模具的基本原理、设计方法和制造工艺,使学生掌握相关知识。
2.案例分析法:分析实际模具设计案例,使学生更好地理解模具设计的过程和方法。
3.实验法:学生进行模具设计实验,提高学生的动手能力和实际操作技能。
4.讨论法:学生进行小组讨论,培养学生的团队协作能力和创新思维。
四、教学资源为了支持本课程的教学内容和教学方法的实施,我们将准备以下教学资源:1.教材:选用《冲压模具设计》一书作为主要教材,为学生提供系统的理论知识。
2.参考书:提供相关领域的参考书籍,丰富学生的知识体系。
3.多媒体资料:制作课件、教学视频等,以图文并茂的形式呈现教学内容,提高学生的学习兴趣。
4.实验设备:准备模具设计实验所需的设备,为学生提供实践操作的机会。
冲压模具课程设计说明书.doc

冲压模具课程设计说明书.doc冲压模具课程设计说明书导言本文档是冲压模具课程设计的详细说明书,旨在帮助学生深入理解冲压模具的设计原理、工艺流程和相关技术要求。
本文档详细介绍了冲压模具的基本概念、设计流程、材料选择、加工工艺等内容,以及课程设计的具体要求和评估标准。
第一章冲压模具概述1.1 冲压模具的定义1.2 冲压模具的分类1.2.1 单工位模具1.2.2 多工位模具1.2.3 复合模具1.3 冲压模具的基本组成部分1.3.1 上模1.3.2 下模1.3.3 引导装置1.3.4 顶针1.3.5 顶板1.4 冲压模具的工作原理1.5 冲压模具在工业生产中的应用第二章冲压模具设计流程2.1 产品设计分析2.2 模具设计准备2.2.1 工艺方案选择2.2.2 材料选择2.2.3 设计任务书编写2.3 模具零部件设计2.3.1 上模设计2.3.2 下模设计2.3.3 引导装置设计2.3.4 顶针设计2.3.5 顶板设计2.3.6 其他相关组件设计2.4 模具总体设计2.5 模具制造与加工2.6 模具调试与试产第三章冲压模具材料选择3.1 冲压模具材料性能要求3.2 常用模具材料3.2.1 工具钢3.2.2 合金工具钢3.2.3 超硬合金3.2.4 陶瓷材料3.2.5 复合材料3.3 模具材料的选择原则第四章冲压模具加工工艺4.1 冲压模具加工流程4.2 模具零部件加工4.2.1 零部件加工设备选择4.2.2 加工工艺规程确定4.2.3 加工工艺文件编制4.3 模具装配与试验4.3.1 模具装配前准备工作4.3.2 模具装配过程4.3.3 模具试验与调试4.4 模具维护与保养4.4.1 模具使用生命周期管理4.4.2 模具保养与维护方法4.4.3 模具故障排除与处理第五章课程设计要求与评估标准5.1 课程设计要求5.2 评估标准5.2.1 设计方案合理性评估5.2.2 模具设计准确性评估5.2.3 模具加工工艺评估5.2.4 模具试验与调试评估5.2.5 学生报告书评估附件1.产品设计分析报告范本2.模具零部件设计图纸范本3.模具装配图范本4.模具加工工艺文件范本5.模具试验与调试记录范本法律名词及注释1.冲压模具:指用于冲压加工的模具,用于将板材等材料加工成具有一定形状和尺寸的零件。
冲压模具设计卡班课程设计
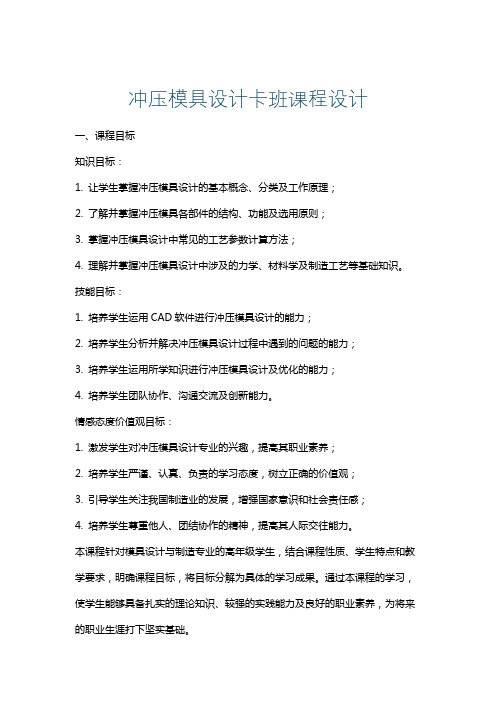
冲压模具设计卡班课程设计一、课程目标知识目标:1. 让学生掌握冲压模具设计的基本概念、分类及工作原理;2. 了解并掌握冲压模具各部件的结构、功能及选用原则;3. 掌握冲压模具设计中常见的工艺参数计算方法;4. 理解并掌握冲压模具设计中涉及的力学、材料学及制造工艺等基础知识。
技能目标:1. 培养学生运用CAD软件进行冲压模具设计的能力;2. 培养学生分析并解决冲压模具设计过程中遇到的问题的能力;3. 培养学生运用所学知识进行冲压模具设计及优化的能力;4. 培养学生团队协作、沟通交流及创新能力。
情感态度价值观目标:1. 激发学生对冲压模具设计专业的兴趣,提高其职业素养;2. 培养学生严谨、认真、负责的学习态度,树立正确的价值观;3. 引导学生关注我国制造业的发展,增强国家意识和社会责任感;4. 培养学生尊重他人、团结协作的精神,提高其人际交往能力。
本课程针对模具设计与制造专业的高年级学生,结合课程性质、学生特点和教学要求,明确课程目标,将目标分解为具体的学习成果。
通过本课程的学习,使学生能够具备扎实的理论知识、较强的实践能力及良好的职业素养,为将来的职业生涯打下坚实基础。
二、教学内容1. 冲压模具设计基础理论- 冲压模具概述、分类及工作原理;- 冲压模具各部件结构、功能及选用原则;- 冲压模具设计中涉及的力学、材料学及制造工艺基础知识。
2. 冲压模具设计方法及步骤- 冲压模具设计的一般步骤及注意事项;- 常见冲压模具设计计算方法及实例;- 冲压模具设计中的CAD软件应用。
3. 冲压模具设计实例分析- 分析冲压模具设计案例,了解实际设计过程中的问题及解决方法;- 针对不同类型的冲压模具,进行设计实践及优化;- 探讨冲压模具设计的新技术、新趋势。
4. 教学大纲及进度安排- 第1周:冲压模具设计基础理论;- 第2周:冲压模具设计方法及步骤;- 第3周:冲压模具设计计算方法及实例;- 第4周:冲压模具设计CAD软件应用;- 第5周:冲压模具设计实例分析与实践;- 第6周:课程总结、讨论与拓展。
大学冲压模具课程设计

大学冲压模具课程设计一、课程目标知识目标:1. 学生能掌握冲压模具的基本结构及其工作原理,理解冲压模具在制造业中的应用。
2. 学生能了解并描述冲压模具的设计流程,掌握模具设计的基本原则和关键参数。
3. 学生能够运用专业软件进行冲压模具的初步设计和分析。
技能目标:1. 学生能够运用理论知识,解决实际冲压模具设计与制造中的问题。
2. 学生能够通过实际操作,掌握冲压模具的拆装、调试及维护的基本技能。
3. 学生能够通过课程学习,提高团队协作和沟通能力,形成良好的工程实践素养。
情感态度价值观目标:1. 学生能够增强对冲压模具设计与制造专业的认同感,培养对制造业的热爱。
2. 学生能够认识到冲压模具在现代制造业中的重要作用,增强社会责任感。
3. 学生通过课程学习,培养严谨的科学态度、创新思维和持续学习的意识。
课程性质:本课程为专业核心课程,以理论教学与实践操作相结合的方式进行。
学生特点:学生已具备一定的机械基础知识和制图能力,具有较强的学习兴趣和动手能力。
教学要求:教师需结合课程特点,采用案例教学、实践教学等多元化教学方法,引导学生主动参与,提高学生的综合应用能力。
同时,注重培养学生的创新意识和团队协作精神,将课程目标分解为具体的学习成果,以便于教学设计和评估。
二、教学内容1. 冲压模具概述- 冲压模具的定义、分类及特点- 冲压模具在制造业中的应用与发展2. 冲压模具结构及工作原理- 冲压模具的基本结构及其功能- 冲压模具工作原理及关键参数分析3. 冲压模具设计原则及流程- 模具设计的基本原则与要求- 冲压模具设计流程及各阶段任务4. 冲压模具设计关键技术- 冲模结构设计及参数选择- 冲模材料的选择与应用- 模具的导向、定位及固定方式5. 冲压模具分析与优化- 运用专业软件进行模具分析与优化- 常见冲压模具故障分析与解决方案6. 冲压模具制造与工艺- 冲压模具的加工方法及工艺流程- 模具制造中的质量控制与检测7. 冲压模具的装配与调试- 模具装配的工艺要求与方法- 模具调试及试模过程中的注意事项8. 冲压模具的维护与管理- 冲压模具的日常维护与保养- 模具库存管理与使用记录教学大纲安排:本课程共计32学时,按照以上教学内容进行系统授课。
冲压模具课程设计说明书

冲压模具的动 作过程:包括 送料、冲压、 卸料、回程等
步骤
冲压模具的设 计要点:考虑 模具的强度、 刚度、耐磨性、
热处理等
冲压模具的应 用领域:汽车、 家电、电子等
行业
模具强度和刚度校核
刚度校核:确保模具在冲压过 程中不会发生过大的弹性变形
校核方法:有限元分析、实 验测试等
强度校核:确保模具在冲压 过程中不会发生断裂或变形
模具结构设计
模具类型: 根据冲压 工艺选择 合适的模 具类型
模具材料: 选择合适 的模具材 料,如钢、 铝等
模具尺寸: 根据冲压 件的尺寸 和精度要 求确定模 具尺寸
模具结构: 包括型腔、 型芯、模 架、导柱、 导套等部 件的设计 和布局
模具精度: 根据冲压 件的精度 要求确定 模具的精 度
模具寿命: 根据冲压 件的生产 数量和冲 压速度确 定模具的 寿命
感谢您的观看
伸等步骤
操作规程制定: 根据工艺流程
制定操作规程, 包括设备操作、
模具安装、材 料准备等
安全操作规程: 确保操作安全, 包括设备安全、 模具安全、材
料安全等
质量控制规程: 确保产品质量, 包括尺寸精度、 表面质量、材
料性能等
设计图纸和说明书编制
设计图纸:包括模具结构图、零件图、装配图等 说明书编制:包括设计目的、设计原理、设计过程、设计结果等 设计图纸和说明书的格式要求:符合国家标准或行业标准 设计图纸和说明书的审核:由专业人员进行审核,确保设计质量和准确性
工装选择: 根据冲压 工艺要求, 选择合适 的模具和 工装
模具设计: 考虑模具 的尺寸、 形状、材 料等因素
工装设计: 考虑工装 的尺寸、 形状、材 料等因素
- 1、下载文档前请自行甄别文档内容的完整性,平台不提供额外的编辑、内容补充、找答案等附加服务。
- 2、"仅部分预览"的文档,不可在线预览部分如存在完整性等问题,可反馈申请退款(可完整预览的文档不适用该条件!)。
- 3、如文档侵犯您的权益,请联系客服反馈,我们会尽快为您处理(人工客服工作时间:9:00-18:30)。
1 锁挡零件图及工艺方案的拟订零件图锁档零件如图1-1所示,材料选用优质碳素结构钢薄钢板,牌号为08F ,抗剪强度(/)MPa τ:220~310;抗拉强度(/)b MPa σ:280~390;屈服强度(/s MPa σ):180;伸长率(/%)δ:32[1];料厚2mm ,大批量生产,制造精度要求IT10~IT12,要求零件表面无划伤,周边无毛刺,不允许出现起皱、拉裂、缺料等缺陷。
由于该零件形状较复杂,部分尺寸有精度要求,因此必须在仔细分析零件冲压工艺的基础上合理进行模具结构设计。
图 1-1 锁挡零件The lock stopper 零件的结构工艺分析该零件属带凸缘拉深件,除采用拉深工艺外,还包括冲孔、落料及切舌加工工序。
由于其尺寸较小,两凸缘孔和底部的切舌部位尺寸均不超过4 mm ,离筒壁很近,且对两端凸缘4 mm 孔有位置精度要求,所以加工困难,在设计成形工序时必须仔细考虑。
1.2.1 冲裁部位成形工艺性冲裁件孔径因受冲孔凸模强度和刚度的限制,不宜过小,否则容易折断或压弯,冲孔的最小尺寸取决于冲压材料的力学性能、凸模强度和模具结构。
该工件初步拟定采用无保护套冲孔,冲孔的最小尺寸必须满足以下条件:圆孔(τ<390 MPa),d(直径)≥ t(料厚);方孔,b(边宽)≥0.9t 。
对该工件t=2 mm ,圆孔处d=4 mm>t 满足;方孔处b=4 mm>满足。
冲孔件孔与孔,孔与边缘的距离不能过小,以避免工件变形,模壁过薄或因材料易被拉人凹模而影响模具寿命,一般最小孔边距取值范围为:圆孔取a≥(1~1.5)t ;矩形孔取a≥(1.5~2)t 。
对该工件,凸缘孔处:a=4 mm>;方孔与筒底孔边距:a=4 mm> ,均满足要求。
1.2.2 拉深部位成形工艺性拉深件各部分的尺寸比例要恰当,应尽量避免宽凸缘(d 凸>3d)和深度大的拉深件(h≥2d),该工件:d 凸=34mm ,h=10 mm ,1d =26 mm ,均在易成形拉深参数范围内。
在拉深件上冲孔时,为避免凸模受水平推力而折断,孔壁与工件壁应保持一定距离,以避开拉深圆角。
拉深件凸缘上的孔距应满足:1D ≥ (1d +22r +d 凸缘孔) (1-1)拉深件底部孔径应满足:d 底孔≤1d -21r -t (1-2) 对该工件(如图1-2所示):1D =40 mm ,1d =26mm ,t=2 mm ,2r =5 mm ,1r =2 mm ,d 凸缘孔=4 mm ,d 底孔=8 mm ,则:(1d +22r +d 凸缘孔)=40 mm=1D1d -21r -t=20 mm> 8 mm=d 底孔均符合要求。
图1-2 拉深件上孔的位置要求Position of the hole in drawing work-piece拉深件的圆角半径在保证尺寸要求情况下应尽量大些,以利于成形和减少拉深次数,拉深件底与壁、凸缘与壁圆角半径应满足[1]:r 1≥t,r 2≥2t,否则应增加整形工序。
对该工件:r 1=2 mm ,r 2=5 mm ,拉深部位圆角半径满足要求,无需增加整形工序。
采用拉深加工,必须计算其拉深次数,并确定是否增加切口工序。
由图1所给的尺寸:d 凸=34mm ,d 1=26mm ,t=2 mm ,D 为零件毛坯展开直径,由于材料厚度t=2mm ,故按中线尺寸计算[1],根据下式初步计算:(1)确定修边余量:根据制件尺寸查表4-5得修边余量R ∆=,故实际凸缘直径t d =d 凸+2R ∆=34+2×=39mm. (1-3)(2)预算坯料直径:由表4-7查得带凸缘筒形件的坯料直径计算公式为:D =(1-4) 将中线尺寸t d =22mm ,R=6mm ,r=3mm ,2d =28mm ,1h = 1mm ,3d =40mm , 4d =39mm.代入上式得:D = 47.16mm =则:2/34/28 1.2d d =≈凸/2/47.16 4.2%t D =≈2/28/47.160.59m d D ==≈2/10/280.357h d =≈根据表4-12和表4-13[1]查得凸缘件首次拉深的极限拉深系数[m]=,带凸缘筒形件第一次拉深的最大相对高度:[h/d]=~,则m=>[m],/h d=<[h/d]。
由计算结果可知拉深可一2次完成,无需增加切口工序。
此外根据零件图可知该工度要求不高,对平面度及垂直度也没要求,所以无需采用弯曲整形。
但对于该模具为了使条料在拉深工序后,条料收缩不影响条料的正常定位,故在拉深工序前加道切口工序,切口为以D=为内边,宽为b=2mm的两个扇形环,所以坯料的实际直径:=D+2b=+2×2=。
D实际1.2.3 切舌部位弯曲成形工艺性弯曲件的相对圆角半径若过小会使弯曲件外表面纤维的拉伸应变超过材料所允许的极限而出现裂纹或折断,所以在保证坯料外表面纤维不发生破坏的前提下,工件能够弯成≤为压弯线与轧制纹向垂直的最小弯曲半径,0.4t为压的内表面最小圆角半径为≤rm in弯线与轧制纹向平行的最小弯曲半径[2])。
该工件弯曲处内表面圆角半径为:r=1>,故可以弯曲。
弯曲部位直边高度不能过小,弯曲直角时,弯曲件直边高度h必须大于或等于最小弯边高度:h=2t,该工件弯曲部位直边高度为:h=4 mm,符合要求。
m in1.3 冲压工艺方案确定模具类型的选用主要取决于冲压件的生产批量、尺寸大小和精度要求等因素。
对尺寸较小的冲压件,考虑到单工序模上料不方便和生产率低,加上存在安全隐患,常选用复合模或级进模生产。
若选用自动送料,一般用连续冲压,为避免多次冲压的定位误差,常选用复合模生产。
复合模的冲压精度比级进模高,结构紧凑,模具轮廓比级进模小,但级进模的生产效率更高,操作比较安全,容易实现单机自动化生产。
若安装自动送料装置,可实现小件的自动冲压生产,这主要是针对薄件(料厚不超过2mm)。
级进模设计时,工序可以分散,采用空工位,不必集中在一个工位,不存在复合模的“最小壁厚问题”,因而模具强度较高,寿命较长。
使用级进模可以减少压力机数量,减少半成品的运输,可大大减少车间和仓库面积。
对于该零件,生产批量大,零件尺寸小,最大径向尺寸为52 mm,料厚为2 mm,较薄,尺寸精度要求IT12级。
鉴于此,采用自动送料出件的级进模生产最合适。
根据所选用的模具类型为级进模及所确定的冲压工序,拟定以下几种工艺方案。
1)方案1:冲中心孔—切口--拉深--切舌--冲两凸缘孔--落料2)方案2:冲中心孔—切口--拉深--冲两凸缘孔--切舌--落料3)方案3:切口--拉深--冲中心孔--冲两凸缘孔--切舌--落料4)方案4:切口--拉深--冲中心孔与两凸缘孔复合--切舌--落料对以上各方案比较分析如下。
方案1复合程度低,为简单工序的连续冲压,模具结构简单,安装调试容易,但该方案第2工步的定位不便。
若采用导正销,则结构较复杂,因为拉深件在精度要求不高的情况下一般靠外形定位,此外,切舌工步底部必须有方孔的存在以容纳弯曲直边,到后续工序也必须存在,以便条料放置(落料除外),增加了模具零件的加工难度。
方案2与方案l一样复合程度低,也同样存在第2工步的定位问题,其不同点在于调换了切舌与冲凸缘孔两工步,解决了前面模具零件加工的问题。
方案3复合程度较低,但这对级进模而言并不是问题,而是其特点所在。
其与方案4的主要区别在于后者将冲中心孔与冲凸缘孔复合,这样设计可以保证三孔的中心位于同一条基准线,符合零件的技术要求,但是可能存在最小壁厚问题。
确切一点说,壁厚问题存在的关键不是在底孔,也不是复不复合的问题,而在于两凸缘孔本身。
因为凸缘孔离拉深筒壁较近,若存在问题,方案3同样不可行,这一点由后续的排样设计及模具设计过程可以看出并不存在问题,所以方案4与方案3同样是可行的,但是其复合程度相对较高,而且也不影响级进拉深过程。
总体而言方案4优于方案3。
综合以上比较分析,方案4更经济合理可行,符合生产要求,故采用方案4。
模具类型及结构形式的选择1.4.1 模具结构形式要求根据确定的工艺方案和零件的形状特点,精度要求,预选设备的主要技术参数,模具的制造条件及安全生产等,选定模具类型及结构形式。
确定加工工艺后,应通过分析比较,选择合适的模具结构形式,使其尽量满足以下要求:(1)能冲出符合技术要求的工件;(2)能提高生产率;(3)模具制造和维修方便;(4)模具有足够的寿命;(5)模具易于安装调整,且操作方便、安全。
1.4.2 模具整体结构按照模具设计原则,根据带料排样图,结合零件特点,在上述分析计算的基础上,进行模具结构的总体设计。
模具采用整体式弹压卸料板,凹模均采用组合式镶块结构,送料采用人工送料,导料板粗定位,导正销精定位。
该零件精度要求不高,因此模具主要靠侧压装置和侧刃定位,故采用始用挡料销、导料板、导料销导料]3[。
切舌工步因凸模细长采用护套结构,最后工步因是拉深件落料,必须进行导正,故采用导正销。
该多工位级进模的模具结构如图6所示。
Φ⨯1.上模座 2.导套(25mm)3.垫板 4.切舌凸模 5.凸模固定板 6.拉深凸模 7.模柄 8.防转销8149.切舌凸模 10.防转销26Φ⨯ 11.防转销47Φ⨯ 12.开槽螺钉 13.落料凸模 14.防转销610Φ⨯ 15.导套(25mm ) 16.卸料板 17.瓦轴 18.导柱(28mm )19.凹模固定板 20.内六角螺钉 21.落料凹模 22.导正销 23.切舌凹模 24.弹簧 25.顶杆 26.切舌护套 27.冲孔凹模 28.拉深凹模29.顶件块 30.导柱(25mm )31.下模座 32.导料板 33.侧刃 34.侧刃挡块 35.导料销 36.始用挡料销37.冲凸缘孔凸模 38.冲中心孔凸模 39.卸料螺钉 40.圆柱销1060Φ⨯ 41.橡胶 42.圆柱头螺钉 43. 圆柱销1070Φ⨯图1-3 模具结构Die structure1.4.3 模具工作过程首先是板料进入第1个工位,利用始用挡料销进行定位,此时压力机滑块下行,带动切口凸模4压入切口凹模中,完成切口工步,然后滑块上行,人工进料一个步距,制件进入第2工步,侧刃定位,紧接着压力机滑块下行,带动拉深凸模6压入拉深凹模27中,完成拉深工步;然后滑块上行,凸凹模分离,制件由顶件块28顶出,此时人工送料一个步距,制件进入第3工位冲出中心孔及凸缘孔;再由顶件块顶出后送入第4工位进行切舌,在此工位由切舌凸模护套对拉深部位导正后冲裁及弯曲;最后工件进入落料模,先由导正销2l 导正,再由落料凸模13和落料凹模20完成冲裁落料,使制件与板料完全分离,制件从凹模孔中落下,完成落料工序。