产品可靠度试验程序文件
可靠性测试标准
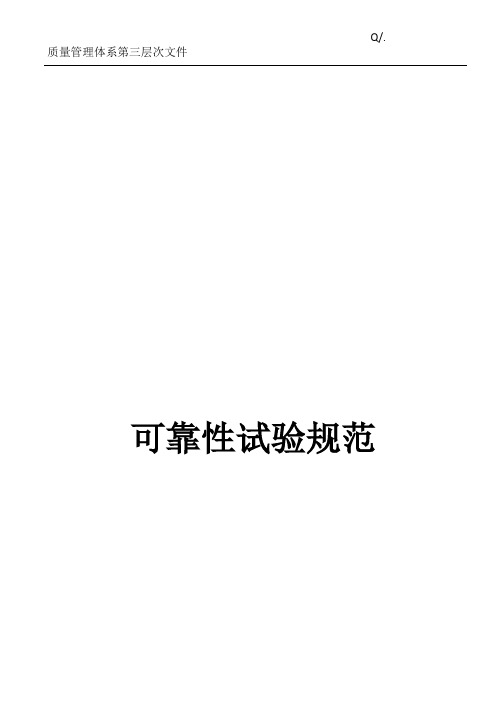
Q/.质量管理体系第三层次文件可靠性试验规范拟制:审核:批准:海锝电子科技有限公司版次:C版可靠性试验规范1. 主题内容和适用范围本档规定了可靠性试验所遵循的原则,规定了可靠性试验项目,条件和判据。
2. 可靠性试验规定根据IEC国际标准,国家标准及美国军用标准,目前设立了14个试验项目(见后目录〕。
根据本公司成品标准要求,用户要求,质量提高要求及新产品研制、工艺改进等加以全部或部分采用上述试验项目。
常规产品规定每季度做一次周期试验,试验条件及判据采用或等效采用产品标准;新产品、新工艺、用户特殊要求产品等按计划进行。
采用LTPD的抽样方法,在第一次试验不合格时,可采用追加样品抽样方法或采用筛选方法重新抽样,但无论何种方法只能重新抽样或追加一次。
若LTPD=10%,则抽22只,0收1退,追加抽样为38只,1收2退。
抽样必须在OQC检验合格成品中抽取。
3.可靠性试验判定标准。
(各电气性能的测试条件,参照器件各自的说明书所载内容)环境条件(1)标准状态标准状态是指预处理, 后续处理及试验中的环境条件。
论述如下:环境温度: 15~35℃相对湿度: 45~75%(2)判定状态判定状态是指初测及终测时的环境条件。
论述如下:环境温度: 25±3℃相对湿度: 45~75%4.试验项目。
目录高温反向偏压试验------------------------------------第4页压力蒸煮试验------------------------------------第6页正向工作寿命试验------------------------------------第7页高温储存试验------------------------------------第8页低温储存试验------------------------------------第9页温度循环试验------------------------------------第10页温度冲击试验------------------------------------第11页耐焊接热试验------------------------------------第12页可焊性度试验------------------------------------第13页拉力试验------------------------------------第14页弯曲试验------------------------------------第15页稳态湿热试验------------------------------------第16页变温变湿试验------------------------------------第17页正向冲击电流(浪涌电流)试验--------------------------第18页高温反向偏压试验一、工作原理:整流二极管在高温下加上反向偏压是一种严酷的工作方式,由于高温下漏电生产批的质量好坏。
产品可靠度试验程序(含表格)
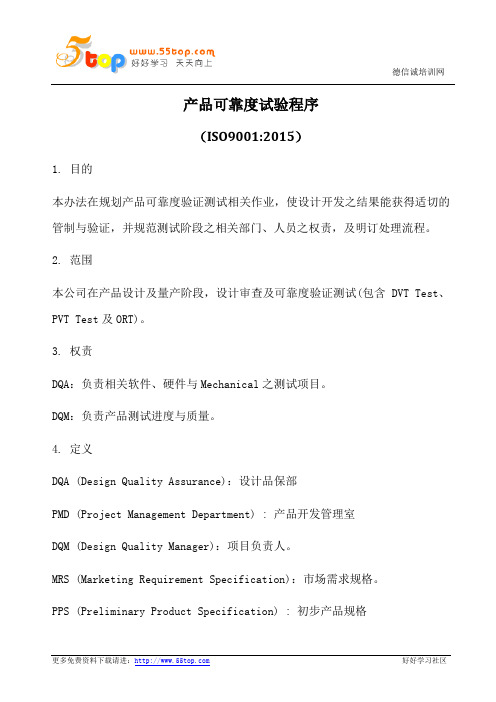
产品可靠度试验程序(ISO9001:2015)1. 目的本办法在规划产品可靠度验证测试相关作业,使设计开发之结果能获得适切的管制与验证,并规范测试阶段之相关部门、人员之权责,及明订处理流程。
2. 范围本公司在产品设计及量产阶段,设计审查及可靠度验证测试(包含DVT Test、PVT Test及ORT)。
3. 权责DQA:负责相关软件、硬件与Mechanical之测试项目。
DQM:负责产品测试进度与质量。
4. 定义DQA (Design Quality Assurance):设计品保部PMD (Project Management Department) : 产品开发管理室DQM (Design Quality Manager):项目负责人。
MRS (Marketing Requirement Specification):市场需求规格。
PPS (Preliminary Product Specification) : 初步产品规格ES (Engineering Specification ) : 工程规格ORT (On-going Reliability Test):制程中的可靠度测试。
5. 内容5.1 DQA于DVT Test进行前,由部门主管指定一DQM、两位协助人员及相关测试人员,该DQM需于DVT Test开始前提出下列数据:5.1.1 工程文件审查审查MRS、PPS、ES、SCHEMATIC、产品结构爆炸图、RD TEST REPORT等文件是否齐全。
审查市场需求规格(MRS)是否合理、内容是否齐全,若有发现文件或资料不齐全者,可经部门主管核可后,以书面通知拒绝执行DVT Test。
5.1.2 测试计划订定内容包括 TEST ITEM & TEST SCHEDULE & TEST LOCATION。
测试条件及判定标准,依测试办法及工程规格书判定之。
5.2 DVT Test PLAN与PVT Test PLAN 之订定原则:5.2.1 依据试产机种之工程文件,由DQM订定DVT Test与PVT Test测试项目。
军品可靠性鉴定试验通用程序

军品可靠性鉴定试验通用程序1概述可靠性鉴定试验(Reliability Qualification Test ,RQT)是为验证产品的设计是否达到了规定的可靠性要求,由认购方认可的单位按选定的抽样方案,抽取有代表性的产品在规定条件下所进行的试验。
可靠性鉴定试验是产品可靠性的确认试验,也是研发产品进入量产前的一种验证试验。
可靠性鉴定试验是一种抽样检验。
由于抽样检验是通过检查样本的质量来判断整批产品质量状况的,所以可能会犯以下两类错误:①将合格产品批误判为不合格产品批,称为第1类错误;②将不合格产品批误判为合格产品批,称为第2类错误。
犯第1类错误时会使生产方受损失,所以称犯这类错误的概率为生产方风险,一般用a表示;犯第2类错误时会使使用方受损失,所以称犯这类错误的概率为使用方风险,一般用0表示。
理想的抽样检验方案要求a = B =0,但这样的试验方案不存在。
因为要使a =0即绝不可把合格批误判为不合格批,这只要把任一批产品都判为合格即可,但这样B增大;反之,要使B =0,就会导致a增大。
此外试验还受时间、经费、试验资源等条件约束,因此在实际工作中常常是生产方和使用方共同协商和权衡来制定试验方案。
2编制产品可靠性鉴定试验大纲针对产品的具体特点及可靠性鉴定工作的需求,由承试单位负责,承制单位参加制订《产品可靠性鉴定试验大纲》。
该大纲作为该产品可靠性鉴定试验的总体规划技术文件,至少应包括下列各项内容:(a)试验目的;(b)适用范围:应明确本试验大纲适用于什么产品、哪种可靠性指标的验证;(c)引用标准和文件:应列出编写本试验大纲及本次试验应遵循和执行的所有标准和文件;(d)受试产品说明和要求:应说明受试产品的功能与用途、受试产品的组成、受试产品的技术状态和受试产品的数量;(e)统计试验方案:应说明本次试验所采用的统计试验方案及相关参数量值的确定;(f)试验条件:应说明试验时的标准大气条件要求、试验的环境条件和工作条件要求(试验剖面),包括电应力、温度应力、湿度应力、振动应力或其它工作应力的要求;(g)试验设备和测试仪表要求:应明确对用于此次试验的试验设备的能力及测试仪表的种类及精度要求及检定情况;(h)受试产品检测项目:应明确试验过程中的检测要求,包括检测内容、检测方式和检测时机、次数等;(i)故障判据、故障分类及统计原则:应明确该产品的关联责任故障判据,及故障的种类、分类原则和故障的统计原则;(k)试验前有关工作要求:应明确进行此次试验前,承试方和承制方及订购方应完成的工作项目,包括在此之前应完成的试验项目、应成立的组织机构、应编写的试验文件、试验设备能力调查、受试产品的安装和测试要求及准备工作评审要求等;(1)试验过程中的监测及记录要求:应明确试验过程中受试产品和试验设备的监测要求,同时应给出相应的记录表格;(m)故障的报告和处理:应明确在试验过程中发生故障后应按何种方式进行报告,应填写哪些记录以及故障的处理程序;(n)试验结束:应规定试验的结束方式、试验提前结束的条件以及试验结束后应完成的工作项目;(o)试验报告要求:应明确由谁编写试验报告、试验报告的主要内容和应提交的单位部门;(p)有关问题的说明:应对试验大纲中其它章节中尚不明确的事项进行规定,以保证试验大纲的完整性和严密性。
可靠性试验程序
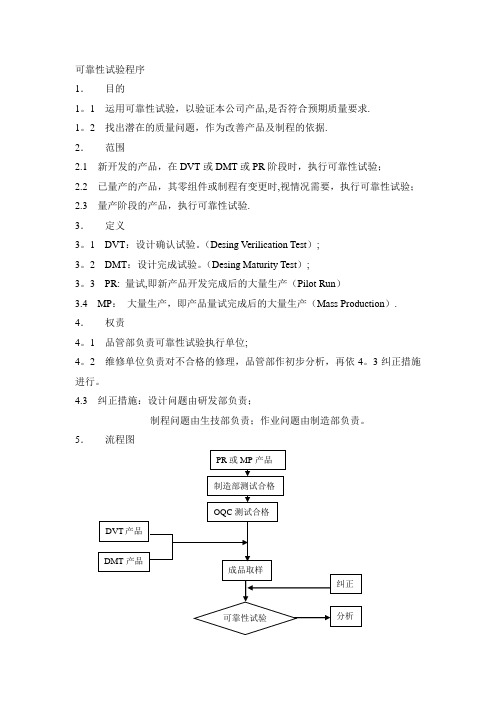
可靠性试验程序1.目的1。
1 运用可靠性试验,以验证本公司产品,是否符合预期质量要求.1。
2 找出潜在的质量问题,作为改善产品及制程的依据.2.范围2.1 新开发的产品,在DVT或DMT或PR阶段时,执行可靠性试验;2.2 已量产的产品,其零组件或制程有变更时,视情况需要,执行可靠性试验;2.3 量产阶段的产品,执行可靠性试验.3.定义3。
1 DVT:设计确认试验。
(Desing Verilication Test);3。
2 DMT:设计完成试验。
(Desing Maturity Test);3。
3 PR: 量试,即新产品开发完成后的大量生产(Pilot Run)3.4 MP:大量生产,即产品量试完成后的大量生产(Mass Production). 4.权责4。
1 品管部负责可靠性试验执行单位;4。
2 维修单位负责对不合格的修理,品管部作初步分析,再依4。
3纠正措施进行。
4.3 纠正措施:设计问题由研发部负责;制程问题由生技部负责;作业问题由制造部负责。
5.流程图6.内容及要求6.1成品取样:6.1.1 全新产品,于DVT或DMT或PR阶段时,依DVT/DMT测试规范执行可靠性试验。
6。
1.2 已量产的产品,其零组件或制程有变更时,依“产品可靠性试验项目”,由品管部决定应执行的可靠性试验项目;6.1.3 量产阶段的产品(OQC检验的合格品),质量工程课应于每年年初拟定“年度量产产品可靠度测试计划”,按产品分类取样。
每六个月随机抽验执行环境试验,每九个月执行寿命试验。
6.2可靠性试验内容:6.2。
1 可靠性试验一般在公司内执行,若公司能力不足时,则送外试验,必须说明试验名称、负责人员,试验起始时间及异常状况联络人。
6。
2。
2 可靠性试验执行项目:参照“产品可靠性试验项目”6.2.3 试验完后,质量工程课人员对所得的相关资料和产品本身进行查验,判断是否符合公司规格或客户要求,并由主管审核后发出可靠性试验结果报告。
TS16949程序文件FMEA控制程序
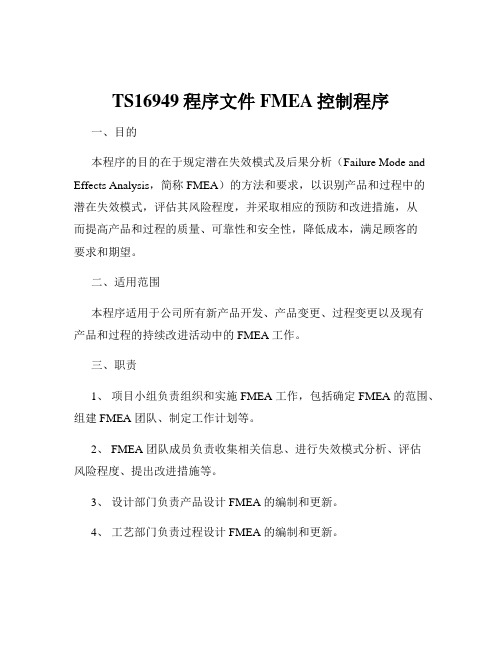
TS16949程序文件FMEA控制程序一、目的本程序的目的在于规定潜在失效模式及后果分析(Failure Mode and Effects Analysis,简称 FMEA)的方法和要求,以识别产品和过程中的潜在失效模式,评估其风险程度,并采取相应的预防和改进措施,从而提高产品和过程的质量、可靠性和安全性,降低成本,满足顾客的要求和期望。
二、适用范围本程序适用于公司所有新产品开发、产品变更、过程变更以及现有产品和过程的持续改进活动中的 FMEA 工作。
三、职责1、项目小组负责组织和实施 FMEA 工作,包括确定 FMEA 的范围、组建 FMEA 团队、制定工作计划等。
2、 FMEA 团队成员负责收集相关信息、进行失效模式分析、评估风险程度、提出改进措施等。
3、设计部门负责产品设计 FMEA 的编制和更新。
4、工艺部门负责过程设计 FMEA 的编制和更新。
5、质量部门负责 FMEA 工作的监督和审核,确保其符合相关要求和标准。
6、其他相关部门负责提供必要的支持和配合。
四、工作程序1、 FMEA 策划项目小组根据产品和过程的特点,确定需要进行 FMEA 的项目和范围。
组建 FMEA 团队,团队成员应包括设计、工艺、质量、生产、采购等相关部门的代表。
制定 FMEA 工作计划,明确工作进度和责任分工。
2、收集相关信息FMEA 团队成员收集与产品和过程有关的技术文件、标准、规范、以往的经验教训、顾客的要求和期望等信息。
对收集到的信息进行整理和分析,为后续的失效模式分析提供依据。
3、失效模式分析针对产品或过程的每个功能或工序,分析可能出现的失效模式。
失效模式应描述为可观察到的现象或故障表现。
4、后果分析评估每个失效模式可能产生的后果,包括对产品性能、安全性、可靠性、顾客满意度等方面的影响。
后果的严重程度应根据其对产品和顾客的影响程度进行评估,并采用适当的评分标准进行量化。
5、原因分析分析导致每个失效模式产生的潜在原因。
产品可靠性、维修性、保障性、测试性、安全性和环境适应性质量控制程序
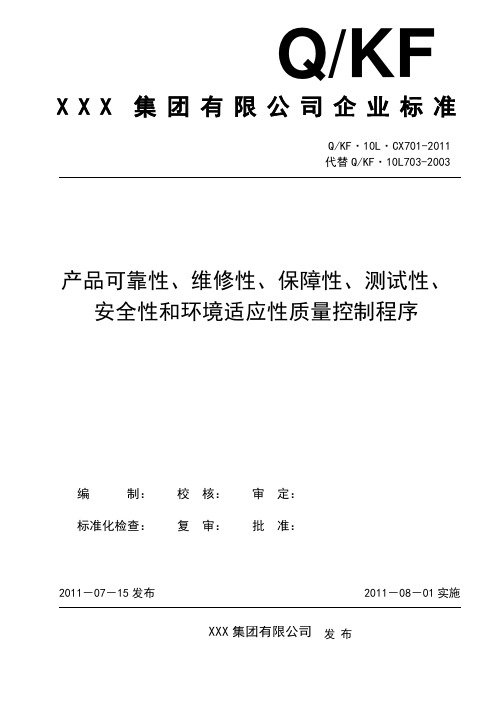
Q/KFKF X X X集团有限公司企业标准Q/KF·10L·CX701-2011代替Q/KF·10L703-2003产品可靠性、维修性、保障性、测试性、安全性和环境适应性质量控制程序编制:校核:审定:标准化检查:复审:批准:2011-07-15发布2011-08-01实施XXX集团有限公司发布更改记录Q/KF·10L·CX701-2011 产品可靠性、维修性、保障性、测试性、安全性和环境适应性质量控制程序1 范围本程序规定了产品的可靠性、维修性、保障性、测试性、安全性和环境适应性(以下简称“六性”)的设计要求和实施方法。
本程序适用于产品“六性”的设计和管理。
2 规范性引用文件下列文件对于本文件的应用是必不可少的。
凡是注日期的引用文件,仅注日期的版本适用于本文件。
凡是不注日期的引用文件,其最新版本适用于本文件。
GJB/Z 23-1991 可靠性和维修性工程报告编写一般要求GJB/Z 57-1994 维修性分配与预计手册GJB/Z 91-1997 维修性设计技术手册GJB/Z 768A-1998 故障树分析指南GJB 150A-2009 环境适应性GJB 190-1986 特性分类GJB 368B-2009 装备维修性通用规范GJB 450A-2004 装备可靠性工作通用要求GJB 451A-2005 可靠性维修性术语GJB 813-1990 可靠性模型的建立和可靠性预计GJB 841-1990 故障报告、分析和纠正措施系统GJB 899A-2009 可靠性鉴定和验收试验GJB 900-1991 系统安全性通用大纲GJB 1032-1990 电子产品环境应力筛选方法GJB 1371-1992 装备保障性分析GJB 1391-1992 故障模式、影响及危害性分析程序GJB 1407-1992 可靠性增长试验GJB 2072-1994 维修性试验与评定GJB 2547-1995 装备测试性大纲13Q/KF·10L·CX701-201112 GJB 3837-1999 装备保障性分析记录GJB 3872-1999 装备综合保障通用要求GJB 4239-2001 装备环境工程通用要求3 术语和定义3.1 可靠性产品在规定的条件下和规定的时间内完成规定功能的能力。
可靠性试验管理程序
深圳市恒宝通光电子有限公司作业类指导书可靠性试验规定作业指导书(试行版)HPT3-W-I-531.目的:验证产品的光电性能和机械性能的可靠性,验证产品的设计是否满足顾客的需求。
2.适用范围:本程序适用于恒宝通无铅化(符合ROHS标准)产品为SM 1x9光模块、SFF、GBIC、SFP和BiDi光模块,以及新开发的光模块等产品的可靠性测试。
3.参考文件: Bellcore TA-NWT 000983Bellcore TR-NWT 000468MIL-STD-8834.可靠性试验监控程序如有批量生产(每月1000个以上),则下述产品要提供规定的样品数量做可靠性试验作为监控产品的可靠性质量。
4.11.25Gb/s、2.5Gb/s SM 1x9光模块;1.25Gb/s、2.5Gb/s SFF;1.25Gb/s、2.5Gb/s SFPDDM光模块等4.1.2 每半年的可靠性试验在样品进行长期的可靠性试验前,要求对样品进行预处理试验。
关于长期4.2GBIC、SFP和各类BIDI等4.2.2 每年的可靠性试验在样品进行长期的可靠性试验前,除了进行机械震动和振动试验外,要求对样品进行预处理试验。
关于长期的可靠性试验监视计划工艺流程,请参4.3.工艺流程4.3.1每季度的可靠性试验 4.3.2每半年/年的可靠性试验4.3.3每季度/半年可靠性试验在光、电测试后不合格品处理流程NO4.3.4每年可靠性试验在光、电测试后不合格品处理流程NONO 只是参数值的问题4.4不合格定义不合格就是不符合监控测试部分的规范说明书。
不合格类型被更进一步分解为两组,即灾难性和参数失败。
4.4.1 灾难性就是(1)一个模块不工作。
(2)一个模块测量出来的参数在测试软件所规定的范围以外。
(3)EEPROM测试失败。
(4)外壳或者屏蔽罩破裂、漏电、表面破损。
(5)一个模块所测量出的参数变化范围超出标准范围(包括测试仪器所允许最大0.8dB的偏差)LOP 3dB CSEN 3dB4.4.2参数失败就是:(1)上升沿时间,下降沿时间,占空比,PWD,Threshold,消光比,老化前后偏差;(2)功率和灵敏度变化在1.5dB与3dB之间,包括测试仪器的R&R所允许的最大偏差0.8dB。
产品质量检验程序
产品质量检验程序在生产过程中,产品质量检验是确保产品符合质量标准的重要环节。
本文将介绍产品质量检验的程序,包括质量检验的目的、流程、方法和结果评估等方面。
一、质量检验的目的质量检验的主要目的是确保产品的合格率和可靠性。
通过检验,我们可以及时发现并纠正产品制造过程中的问题,提高产品质量,满足客户的需求和期望。
同时,质量检验也可以帮助企业降低成本、增强竞争力。
二、质量检验的流程质量检验的流程一般包括取样、测试、评估和记录等步骤。
1. 取样:根据检验标准和要求,从生产线上随机选取代表性样品。
2. 测试:对取样的产品进行相关的物理、化学、机械等测试,以评估其质量和性能。
3. 评估:根据测试结果和预设的质量标准,判断产品的合格性,并记录合格或不合格的结论。
4. 记录:将检验过程中的相关数据和结果进行记录,包括样品信息、检验结果、检验员等。
三、质量检验的方法产品质量检验可以采用各种方法和工具,下面介绍两种常用的方法:1. 外观检验:通过肉眼观察产品的外观,检查是否有瑕疵、变色、变形等表面缺陷。
2. 功能性检验:根据产品的设计要求,进行相应的功能测试,如电器产品的电流、电压测试,机械产品的运转试验等。
除了以上方法,还可以根据产品的特点和要求,采用其他专业的检验方法,如X射线检测、声波检测、拉力测试等。
四、质量检验结果评估在质量检验中,根据检验结果的合格与否,可以分为合格品和不合格品。
1. 合格品:符合质量标准和要求,可以正常出货或投入市场。
2. 不合格品:不符合质量标准和要求,需要进行相应的处理,如修复、重新制造或报废等。
对于不合格品,企业需要追溯其原因,采取相应的纠正措施,确保类似问题不再发生,并承担相应的责任。
五、质量检验的重要性质量检验在产品生产中具有重要的作用:1. 保证产品质量:通过检验,可以发现和排除产品生产过程中的缺陷和问题,确保产品的质量稳定和一致性。
2. 提高客户满意度:优质的产品可以满足客户的需求和期望,提高客户对企业的信任和满意度。
可靠性测试规范
可靠性测试规范.公司名称:XXX文件编号:ZGG-xxx-1-2016发行日期:2016-xx-xx发行部门:质量管理部修订履历表修订次数修订内容修订日期备注1 可靠性测试规范批准 2016-xx-xx可靠性试验规范1 目的根据客户要求及产业界标准,根据产品特性,特制定本检验标准,作为物料及成品可靠性检验依据和质量基准,以保证本公司产品质量,满足客户要求。
2 适用范围本公司使用的所有物料(塑胶件、五金件、螺丝、电池、适配器、数据线、LCD、触摸屏、接口、连接器、按钮等)及成品均适用。
3 权责3.1 质量部:负责进行到料材料、试产及量产阶段成品的可靠性实验,实验结果的判定,问题点的反馈及追踪。
3.2 研发部DQA:负责零件承认时可靠性测试验证可靠性测试;可靠性测试失败的原因分析及改善。
3.3 工程部:协助RD之问题点分析改善。
3.4 生产部:试验机的制作。
4 可靠性检验实施原则4.1 根据量产实验需求,以随机抽样形式从生产线抽取相应的机台作实验,实验数量为每月/每机种/2台。
4.2 新机种、机构变更(包装材料或方式变更等)按实际需求抽取相应试投机器至少2台以上进行试验。
4.3 在新产品量产初始,关键元器件变更,重大制程变更或发现不符合项时,应增加抽样数量和抽样频率。
这些变更应由质量工程师通知。
4.4 所有产品需要进行100%老化测试合格方可转入下一工序。
4.5 到料材料的可靠性试验IQC根据抽样计划依按照GB2828.1-2012正常检查一次抽样方案特殊检查水平S-2进行;成品可靠性试验数量为每月/每机种/2台。
4.6 所有试产机器可靠性测试项目通过后才可转入量产阶段。
可靠性测试fail需由研发或工程分析整改重新测试合格后方可转入下一阶段。
4.7 试验前,依据对应的《成品检验规范》、《进料检验规范》文件进行100%的电气性能和机构性能及内外观检验。
5 参考数据文件编号:DZ-049-1-2015发行日期:2016-1-15发行部门:质量管理部5.1 《不合格品控制程序》RUIYI-PD8.3-20165.2 《来料检验规程》ZGG-003-1-20165.3 《进料检验规范》ZGG-004-1-20165.3《GB2828.1-2012抽样计划》5.4 客户规格和各供货商的产品型录、图面、规格6定义6.1 抽样计划(Sample Plan):到料材料抽样计划按照GB2828.1-2012正常检查一次抽样方案特殊检查水平S-2进行。
可靠性试验控制程序
小件产品,报告和样品放在一起,以便查阅。大件产品用封口胶袋装好后,标识好相关编号存在样 品存放区内。 5.5.6 受测样品于试验前,须先依据各产品之检验标准执行基本外观检验及功能测试,确认受测样品均符合规 格无影响后续之各项试验,方可进行; 5.5.7 试验之执行须确实依据各项测试作业指导书执行测试工作; 5.5.8 试验后亦须依据各产品之检验标准执行检验; 5.5.9 若有失效发生,在 24 小时内完成结果判定,立即通知委托单位及确认失效状态并发出【可靠性测试不 合格通知单】,【失效分析报告】。 5.6 报告 5.6.1 试验结束后,应填写【可靠度测试报告】,报告应有品保单位之制作者及审核者签名; 5.6.2 电子报告仅供参考,正式报告以书面报告为准; 5.6.3 若发现已发行之报告有误,应立即通知相关单位,同时重新制作正确之报告重新发行,并尽可能将原发 行有误之报告收回。 5.7 不符合测试的控制 当发现任何不符合预期的测试条件、测试程序或要求时,实验室应采取下述措施: 5.7.1 应对不符合的工作设定管理的职责和权限, 当不符合的工作确定后, 应制定和采取措施(如暂停工作、 停发报告等); 5.7.2 应评估不符合工作所造成的影响; 5.7.3 立即采取纠正措施,并对不符合工作的可接受性作决定; 5.7.4 必要时,通知客户并撤消报告; 5.7.5 是否恢复工作由实验室最高主管决定。 5.8 信赖性测试失效处理 5.8.1 原物料验证:填写【可靠性测试不合格通知单】、【可靠度测试报告】签核至部门经理会签至委托部门 经理; 5.8.2 新产品验证:填写【可靠度测试报告】签核至部门经理会签至委托部门经理;
- 1、下载文档前请自行甄别文档内容的完整性,平台不提供额外的编辑、内容补充、找答案等附加服务。
- 2、"仅部分预览"的文档,不可在线预览部分如存在完整性等问题,可反馈申请退款(可完整预览的文档不适用该条件!)。
- 3、如文档侵犯您的权益,请联系客服反馈,我们会尽快为您处理(人工客服工作时间:9:00-18:30)。
目的:
为了确保产品之质量能自开发设计至量产出货能符合本公司标准及满足客户需求,制订本办法以验证产品的可靠度及性能。
1.法规或标准:
1.1.ISO9001:2000标准
1.2.IECQ QC080000标准
2.内容:
2.1.组织权责、人员权责、人员资格规定参见《职位说明书》
2.2.名词定义:
2.2.1.System Integration Build (SI) :系统整合阶段。
2.2.2.Product Validation Build (PV) :产品验证阶段。
2.2.
3.Manufacturing Verification Build (MV) :制造验证阶段。
2.2.4.Mass Production (MP) :量产。
2.2.5.Engineering Change Request (ECR) :工程变更要求。
2.2.6.ORT: Ongoing Reliability Test
2.2.7.RoHS:
全名为「电机电子产品中有害物质禁限用指令(The Restriction of
Hazardous Substances in Electrical and Electronic Equipment (ROHS)
Directive (2002/95/EC)」。
为欧盟在2003年所公布的环保指令,RoHS管
制产品在生产阶段中含有害物质的最大量。
2.2.8.WEEE:
为「废电机电子产品指令 (Waste Electrical and Electronic Equipment
(WEEE) Directive (2002/96/EC)」为欧盟在2003年所公布的环保指令,
WEEE则管制产品在废弃阶段必须回收的比率及方式。
2.2.9.IECQ QC 080000 HSPM:
「国际电工技术委员会 (International Electrotechnical Commission , IEC)」
下「国际电子零件认证制度(IEC Quality Assessment System for
Electronic Components, IECQ)」所核可的有害物质管理(Hazardous
Substance Process Management, HSPM) 标准。
2.2.10.有害物质流程管理(Hazardous Substance Process Management, HSPM):
建立在ISO 9001:2000的质量管理系统之上,以「流程导向」的方法,管理
有害物质在产品的使用,并逐步达成全产品无有害物质的目标。
2.2.11.绿色产品(Green product GP):
在产品生命周期过程中,指符合EU RoHS或客户的环保要求,或是不同地
区、国家所订定的相关规定之产品。
2.2.12.绿色零组件(Green component):
指符合 EU RoHS或客户的环保要求,或是不同地区、国家所订定的相关规
定之零组件产品。
2.2.1
3.有害物质(Hazardous Substance, HS):
任何表列于RoHS 与WEEE 指令及客户的要求中被禁止使用之材料与规范
的物质,称为有害物质。
包括铅、镉、汞、六价铬、PBB以及PBDE。
2.2.14.限制物质(Restricted Substance, RS):
指任何表列于RoHS 与WEEE 指令及客户的要求中被禁止使用之材料与规
范的物质,在此标准内与有害物质是互通的用字。
2.2.15.无有害物质(Hazardous Substances Free,HSF):
指减量或排除如表列于EU RoHS及WEEE指令、客户要求或其它适当标准
及规定之物质。
Lead free process无铅制程:
以无铅焊料做为组装印刷线路板焊接材料 , 藉由回焊方式将所有电子零件
着装于印刷线路板之生产制造流程 .所使用的印刷线路板及所有电子零件以
及焊接材料内之有毒害物质含量都需符合 RoHS之法令, 并且印刷线路板及所有电子零件在SMT制程中能满足无铅焊料高温作业之耐热性及预防锡须
的电镀等制程需求条件.组装完成之电子产品亦完全符合可信赖性测试之验
证。
2.2.16.物质安全数据表(Material Safety Data Sheet,MSDS):
供货商需对产品中含有之化学物质制造供货商数据、物质理化特性、火灾
爆炸反应特性、健康危害、急救暴露预防、泄漏处理等有利于安全处理之
化学物质数据表。
2.3.流程控制点
2.4.流程图 :
2.4.1.可靠度实验项目及方法:
2.4.2. SI Build TEST:
2.4.
3. PV Build Test:
2.4.4. MV Build Test
2.5.1.可靠度实验工作说明
完整之可靠度实验,以机种为单位,量产前须进行 Reliability Test,量产
后须进行 OFT 或 ECR 验证,除 ECR 验证外,Reliability Test 及 OFT均
须订定实验计划,包括样品需求,实验项目及方法均应明确记载,本办法
所订为标准之实验计划,若因应客户的需求,则修改之。
2.5.2. SI Build TEST工作说明:
产品在研发单位 (RD) 开发至一般功能均正常后,为保证将来量产出货时使用不会发生故障,须模拟使用者之环境加以测试,以期找出问题点加以修
改,方可保证量产后之质量。
执行单位按流程取得SI Build TEST测试样品,并依照测试计划和测试程序
执行实施测试内容,发布测试报告。
测试结束,在执行单位释出RELEASE
NOTICE后,项目方可进入下一阶段。
2.5.
3. PV Build TEST工作说明:
产品已通过可靠性实验,但在正式量产前,须进行可靠验证实验,以估算
产品之使用寿命,了解是否符合质量要求。
执行单位按流程取得PV Build TEST测试样品,并依照测试计划和测试程序
执行实施测试内容,发布测试报告。
测试结束,在执行单位释出RELEASE
NOTICE后,项目方可进入下一阶段。
2.5.4. MV Build TEST工作说明:
执行单位按流程取得MV Build TEST测试样品,并依照测试计划和测试程
序执行实施测试内容,发布测试报告。
测试结束,在执行单位释出RELEASE
NOTICE后,项目方可进入下一阶段。
2.6.不合格品管制方法:
测试后产品不合格,将贴上不合格品标签加以追踪,并对此样品进行分析,提出改善对策。
此样品在测试结束后保留在测试单位。