闭环伺服系统稳定性研究
全闭环伺服系统结构特点
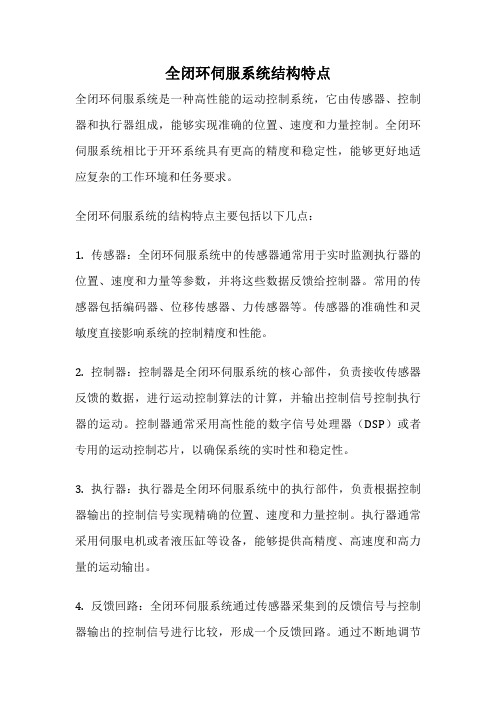
全闭环伺服系统结构特点全闭环伺服系统是一种高性能的运动控制系统,它由传感器、控制器和执行器组成,能够实现准确的位置、速度和力量控制。
全闭环伺服系统相比于开环系统具有更高的精度和稳定性,能够更好地适应复杂的工作环境和任务要求。
全闭环伺服系统的结构特点主要包括以下几点:1. 传感器:全闭环伺服系统中的传感器通常用于实时监测执行器的位置、速度和力量等参数,并将这些数据反馈给控制器。
常用的传感器包括编码器、位移传感器、力传感器等。
传感器的准确性和灵敏度直接影响系统的控制精度和性能。
2. 控制器:控制器是全闭环伺服系统的核心部件,负责接收传感器反馈的数据,进行运动控制算法的计算,并输出控制信号控制执行器的运动。
控制器通常采用高性能的数字信号处理器(DSP)或者专用的运动控制芯片,以确保系统的实时性和稳定性。
3. 执行器:执行器是全闭环伺服系统中的执行部件,负责根据控制器输出的控制信号实现精确的位置、速度和力量控制。
执行器通常采用伺服电机或者液压缸等设备,能够提供高精度、高速度和高力量的运动输出。
4. 反馈回路:全闭环伺服系统通过传感器采集到的反馈信号与控制器输出的控制信号进行比较,形成一个反馈回路。
通过不断地调节控制信号,使得实际输出与期望输出尽可能接近,从而实现准确的运动控制。
反馈回路能够有效地抑制系统的误差和干扰,提高系统的稳定性和精度。
5. 高性能控制算法:全闭环伺服系统通常采用先进的控制算法,如比例积分微分(PID)控制算法、模糊控制算法、模型预测控制算法等。
这些控制算法能够根据系统的数学模型和实时反馈信息,快速地调节控制参数,实现系统的高性能运动控制。
在全闭环伺服系统中,传感器、控制器、执行器和反馈回路相互作用,共同实现高精度、高稳定性的运动控制。
全闭环结构能够有效地抑制系统的误差和干扰,提高系统的响应速度和控制精度。
这种结构特点使得全闭环伺服系统在工业自动化、机器人技术、航空航天等领域得到广泛应用。
双闭环机床伺服系统的组成及各部分作用

一、概述机床作为制造业中常见的设备之一,对于产品加工具有至关重要的作用。
而机床的运动控制系统中的伺服系统更是其核心部分之一。
双闭环机床伺服系统作为目前应用较为广泛的一种机床伺服系统,其组成及各部分作用备受关注。
本文旨在对双闭环机床伺服系统的组成及各部分作用进行系统的介绍,以期对读者有所启发。
二、双闭环机床伺服系统的基本概念1.1 双闭环机床伺服系统的定义双闭环机床伺服系统是一种具有两个闭环控制的机床伺服系统,分别是速度环和位置环。
通过这两个闭环系统的协同作用,可以更加精准地控制机床的运动,提高加工精度和效率。
1.2 双闭环机床伺服系统的优势双闭环机床伺服系统相较于单闭环系统具有许多优势,如运动精度更高、动态性能更好、抗干扰能力更强等。
三、双闭环机床伺服系统的组成2.1 电机部分电机是双闭环机床伺服系统的核心部分,负责将电能转换为机械能,驱动机床的各种运动。
通常采用的是交流伺服电机或直流伺服电机。
2.2 传感器部分传感器是用来感知机床运动状态的装置,可以采集到机床位置、速度等信息,并反馈给控制系统,以实现闭环控制。
常见的传感器包括编码器、光栅尺等。
2.3 控制器部分控制器是双闭环机床伺服系统的大脑,负责接收传感器反馈的信号,计算控制算法得出控制指令,并驱动电机实现所需的运动。
常见的控制器包括PLC、DSP等。
2.4 励磁部分励磁部分是用来控制电机的磁场强度的部分,可以根据运动需要调节电机的磁场,以实现精确的运动控制。
通常采用的是三相功率放大器。
四、双闭环机床伺服系统各部分的作用3.1 电机的作用电机是双闭环机床伺服系统的动力来源,可以根据控制器输出的控制指令实现精确的运动控制。
其性能的好坏直接影响着机床的加工精度和效率。
3.2 传感器的作用传感器负责采集机床的运动状态信息,并将其反馈给控制器,以实现闭环控制。
传感器的准确性和稳定性对机床的运动控制起着至关重要的作用。
3.3 控制器的作用控制器是整个双闭环机床伺服系统的大脑,负责接收传感器反馈的信号,计算控制算法,并输出控制指令驱动电机运动。
闭环伺服系统设计

主控界面设计
设计简洁明了的主控界面,方便用户进行系统监控和控制。
自定义报表和图形显示
根据用户需求,设计各类报表和图形显示,提供直观的数 据分析和可视化功能。
05 闭环伺服系统调试与优化
系统调试流程
硬件检查
检查伺服系统的硬件连接是否 正确,确保电机、编码器、驱
数据分析
对记录的数据进行统计分析,找出最优的控制参数组合。
参数应用
将最优的控制参数应用到伺服系统中,并进行验证和确认。
06 闭环伺服系统发展趋势与 展望
新技术与新材料的应用
01
数字孪生技术
利用数字孪生技术建立系统的虚拟模型,实现物理系统与数字模型的实
时交互,提高系统的预测和优化能力。
02
新型传感器技术
模糊控制算法
基于模糊逻辑和专家经验, 处理不确定性和非线性问 题,提高系统鲁棒性。
神经网络控制算法
模拟人脑神经元网络,通 过学习自适应调整系统参 数,实现复杂系统的智能 控制。
通信协议设计
串行通信协议
如RS-232、RS-485等,实现设备间的数据传输和命令控制。
网络通信协议
如TCP/IP、UDP等,实现远程数据交换和控制,提高系统扩展性。
驱动器选型与设计
01
02
03Байду номын сангаас
驱动器类型选择
根据电机类型和控制需求, 选择合适的驱动器类型, 如直流电机驱动器、交流 电机驱动器等。
驱动器参数匹配
根据电机参数和控制要求, 选择合适的驱动器参数, 如电压、电流、功率等。
驱动器控制算法
根据电机控制策略,设计 驱动器的控制算法,如 PID控制、模糊控制等。
伺服系统的开环控制与闭环控制
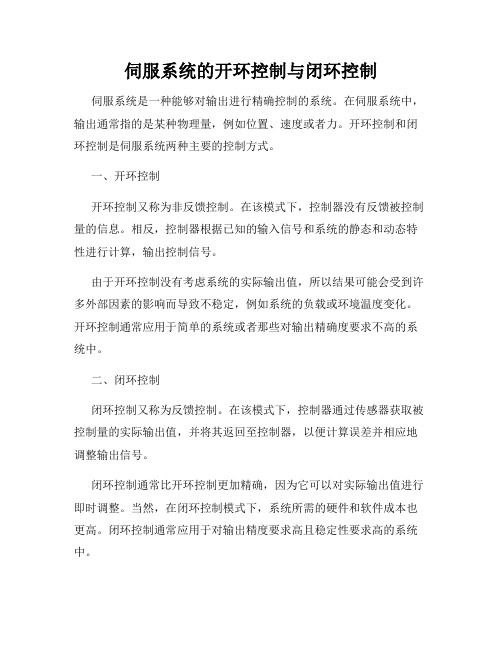
伺服系统的开环控制与闭环控制伺服系统是一种能够对输出进行精确控制的系统。
在伺服系统中,输出通常指的是某种物理量,例如位置、速度或者力。
开环控制和闭环控制是伺服系统两种主要的控制方式。
一、开环控制开环控制又称为非反馈控制。
在该模式下,控制器没有反馈被控制量的信息。
相反,控制器根据已知的输入信号和系统的静态和动态特性进行计算,输出控制信号。
由于开环控制没有考虑系统的实际输出值,所以结果可能会受到许多外部因素的影响而导致不稳定,例如系统的负载或环境温度变化。
开环控制通常应用于简单的系统或者那些对输出精确度要求不高的系统中。
二、闭环控制闭环控制又称为反馈控制。
在该模式下,控制器通过传感器获取被控制量的实际输出值,并将其返回至控制器,以便计算误差并相应地调整输出信号。
闭环控制通常比开环控制更加精确,因为它可以对实际输出值进行即时调整。
当然,在闭环控制模式下,系统所需的硬件和软件成本也更高。
闭环控制通常应用于对输出精度要求高且稳定性要求高的系统中。
三、开环控制和闭环控制的比较总的来说,开环控制和闭环控制各有优缺点。
开环控制通常比较简单,并且可以为系统提供基本的控制。
但是,由于其不考虑实际输出值的变化,所以其控制精度较低,对于环境变化比较敏感。
闭环控制虽然成本高,但其控制精度相对较高,可以从控制误差中学习并自我调节。
此外,由于它可以实施实时调整,所以闭环控制通常比开环控制更稳定。
四、结论在伺服系统中,开环控制和闭环控制是两种常见的控制模式。
适合哪种控制模式应该根据具体情况而定,包括对所需控制的输出精度要求、系统成本、环境条件等各种因素的影响。
闭环伺服系统结构特点

闭环伺服系统结构特点
一、引言
闭环伺服系统是一种常见的控制系统,其结构特点决定了其在工业自动化领域的广泛应用。
本文将从以下几个方面对闭环伺服系统的结构特点进行详细介绍。
二、闭环伺服系统的基本组成
1. 传感器:用于检测被控对象的状态或位置,将信号转换为电信号送入控制器;
2. 控制器:处理传感器反馈信号,并根据设定值和反馈信号计算出控制指令;
3. 执行机构:根据控制指令执行动作,如电机、液压缸等。
三、闭环伺服系统的工作原理
1. 传感器检测被控对象状态或位置,并将信号送入控制器;
2. 控制器处理传感器反馈信号,并根据设定值和反馈信号计算出控制指令;
3. 控制指令送入执行机构,执行机构按照指令执行动作;
4. 执行机构动作产生反馈信号,传回给控制器;
5. 控制器根据反馈信号调整控制指令,使得被控对象达到设定值。
四、闭环伺服系统的优点
1. 精度高:闭环伺服系统通过反馈控制,可以实现对被控对象的精确控制;
2. 稳定性好:闭环伺服系统可以根据反馈信号实时调整控制指令,保证被控对象的稳定性;
3. 响应速度快:闭环伺服系统可以根据反馈信号实时调整控制指令,响应速度快。
五、闭环伺服系统的应用领域
1. 机器人:闭环伺服系统可以用于机器人的运动控制;
2. 飞行器:闭环伺服系统可以用于飞行器的姿态控制;
3. 机床:闭环伺服系统可以用于机床的位置和速度控制。
六、结论
闭环伺服系统是一种精确、稳定、响应速度快的控制系统,其基本组成包括传感器、控制器和执行机构。
在机器人、飞行器、机床等领域得到了广泛应用。
伺服控制系统特点及应用
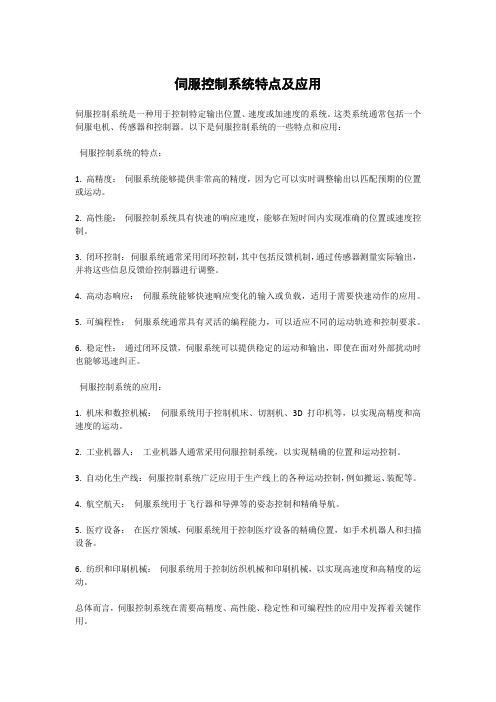
伺服控制系统特点及应用
伺服控制系统是一种用于控制特定输出位置、速度或加速度的系统。
这类系统通常包括一个伺服电机、传感器和控制器。
以下是伺服控制系统的一些特点和应用:
伺服控制系统的特点:
1. 高精度:伺服系统能够提供非常高的精度,因为它可以实时调整输出以匹配预期的位置或运动。
2. 高性能:伺服控制系统具有快速的响应速度,能够在短时间内实现准确的位置或速度控制。
3. 闭环控制:伺服系统通常采用闭环控制,其中包括反馈机制,通过传感器测量实际输出,并将这些信息反馈给控制器进行调整。
4. 高动态响应:伺服系统能够快速响应变化的输入或负载,适用于需要快速动作的应用。
5. 可编程性:伺服系统通常具有灵活的编程能力,可以适应不同的运动轨迹和控制要求。
6. 稳定性:通过闭环反馈,伺服系统可以提供稳定的运动和输出,即使在面对外部扰动时也能够迅速纠正。
伺服控制系统的应用:
1. 机床和数控机械:伺服系统用于控制机床、切割机、3D打印机等,以实现高精度和高速度的运动。
2. 工业机器人:工业机器人通常采用伺服控制系统,以实现精确的位置和运动控制。
3. 自动化生产线:伺服控制系统广泛应用于生产线上的各种运动控制,例如搬运、装配等。
4. 航空航天:伺服系统用于飞行器和导弹等的姿态控制和精确导航。
5. 医疗设备:在医疗领域,伺服系统用于控制医疗设备的精确位置,如手术机器人和扫描设备。
6. 纺织和印刷机械:伺服系统用于控制纺织机械和印刷机械,以实现高速度和高精度的运动。
总体而言,伺服控制系统在需要高精度、高性能、稳定性和可编程性的应用中发挥着关键作用。
PMAC控制下的高精度转台双闭环伺服系统设计与调试.

PMAC控制下的高精度转台双闭环伺服系统设计与调试PMAC 是一个开放式的运动控制器,它有多种型号,系统使用的是TURBO PMACⅡ型卡,该卡在国内的使用不多。
用PMAC控制转台闭环伺服系统,从理论上来讲,伺服环内各元件误差以及运动中造成的误差都可以得到补偿,因而可以达到很高的跟随精度和定位精度,但由于受机械变形、温度变化、振动及其它因素的影响,要实现高精度、良好的稳定性和快速的动态响应特性,闭环系统的调试有一定的难度。
就PMAC 控制的转台闭环系统进行调试过程中遇到的几个问题进行分析,并提出解决办法,以供大家借鉴。
1 伺服系统的设计1.1 PMAC 概述美国DeltaTau 公司的可编程多轴运动器(PMAC)是世界上功能强大的运动控制器之一,它借助于Motorola 的DSP56001/56002 数字信号处理器,可以同时操纵1~8 个轴。
而且它还可以自动对任务进行优先等级判别,从而进行实时的多任务处理,这使得它在处理时间和任务切换这方面大大减轻主机和编程器的负担,提高了整个控制系统的运行速度和控制精度。
PMAC 具有开放平台,不仅可以用G 代码,而且可以用C 或BASIC 语言编程,它能够对存储在它内部的程序进行单独的运算,执行运动程序、PLC 程序,并可进行伺服环更新,并以串口、总线两种方式与主计算机进行通讯。
1.2 转台控制系统设计该控制系统由PC(上位机)、PMAC 控制器(下位机)、Dynaserv驱动器、PARK 的高精度旋转工作台、测量与反馈系统组成。
其控制原理,如图1 所示。
PARK 的高精度旋转工作台与一般工作台不同,它的电机是无刷直接驱动电机,回转工作台的台面是电机的转子,没有了传动机构,这样就减少了传动误差。
该系统是一个双闭环系统,由于该系统中执行机构采用的是直接驱动电机,其双闭环系统不同于通常的双闭环,其速度环和位置环共用圆光栅位置反馈信号,内环是速度环,外环是位置环。
闭环伺服系统结构特点

闭环伺服系统结构特点引言闭环伺服系统是一种常见的控制系统,被广泛应用于工业自动化、机械控制以及电子设备等领域。
本文将对闭环伺服系统的结构特点进行全面、详细、完整且深入地探讨。
一. 闭环伺服系统概述闭环伺服系统由传感器、控制器和执行器组成。
其中,传感器用于监测被控变量的状态,控制器根据传感器反馈的信息进行计算并产生相应的控制信号,最终由执行器完成动作。
闭环伺服系统的特点在于其具有反馈控制机制,通过不断对被控变量进行测量并与设定值进行比较,系统可以自动调整控制信号以实现精确控制。
二. 闭环伺服系统的结构特点闭环伺服系统具有以下结构特点:1. 传感器传感器是闭环伺服系统的重要组成部分,用于实时监测被控变量的状态。
传感器可以是物理量传感器,如温度传感器、压力传感器等,也可以是位置传感器、速度传感器等。
传感器将被控变量的状态转换为电信号,传递给控制器进行处理和分析。
2. 控制器控制器是闭环伺服系统的核心部分,负责计算控制信号以实现对被控变量的精确控制。
控制器通常采用微处理器、DSP芯片等计算设备,利用反馈控制算法对传感器反馈的信息进行分析和处理。
控制器根据测量值与设定值之间的差异计算出控制信号,并通过输出接口将信号传递给执行器。
执行器是闭环伺服系统的输出端,用于实现控制信号的动作。
执行器可以是电动机、伺服阀、液压缸等,根据被控变量的不同而选择不同的执行器。
执行器将控制信号转换为相应的动作或力,并作用于被控对象,从而实现对被控变量的控制。
4. 反馈回路闭环伺服系统的关键特点在于其具有反馈回路。
反馈回路是指从执行器输出到传感器输入之间的连接路径,它将被控对象输出的实际值反馈给控制器,用于控制器对控制信号的修正。
通过不断测量和比较实际值与设定值之间的差异,系统可以自动调整控制信号,达到对被控变量的精密控制。
三. 闭环伺服系统的工作原理闭环伺服系统按照以下步骤工作:1. 传感器测量传感器实时测量被控变量的状态,并将其转换为电信号。
- 1、下载文档前请自行甄别文档内容的完整性,平台不提供额外的编辑、内容补充、找答案等附加服务。
- 2、"仅部分预览"的文档,不可在线预览部分如存在完整性等问题,可反馈申请退款(可完整预览的文档不适用该条件!)。
- 3、如文档侵犯您的权益,请联系客服反馈,我们会尽快为您处理(人工客服工作时间:9:00-18:30)。
闭环伺服系统稳定性研究
摘要:在数控机床中,伺服系统是数控装置和机床的中间联接环节,是数控系统的重要组成部分、伺服系统接受来自伺服控制器的进给脉冲,经变换和放大后转化为机床工作台的位移,使工作台跟随指令脉冲移动、本文讨论了伺服数控系统的数学模型,对闭环伺服系统的稳态性能进行了详细分析、同时给出了实验结果,设计了实物样机,该研究结果为伺服系统的稳定性能分析提供理论基础、
关键词:伺服;数控机床;伺服电机;稳定性能
0 引言
从控制论观点出发,对数控系统的技术要求可归纳为:①滚珠丝杠机械平台的精度要求具有摩擦阻力小、传动效率高、运动灵敏、无爬行现象,可进行预紧使其具备无间隙运动,传动刚度高,反向时无空程死区等特点、②由于数控机床的速度和精度等技术指标,在很大程度上由伺服系统的性能所决定、因此,研究伺服系统的稳态性能十分重要、
从控制论可知,高阶系统过渡过程的数学表达式是由一些指数项和衰减正弦项组成、如果在这些表达式中,有一些项的影响很小,可以将其忽略,则这个系统就可以用一个低阶系统来近似、在工程上,通常把高阶系统近似于一阶系统或二阶系统,我们把数控机床位置伺服系统简化为典型的二阶系统、本文将应用控制系统的分析方法来讨论数控机床位置伺服系统的稳态性能指标、
1 伺服数控系统的数学描述
对伺服系统的数学描述,实际上就是首先建立系统中各个环节的传递函数,然后求出整个系统的传递函数、这里以伺服控制数控机床为例,推导出其机械结构传递函数、
图1为数控机床的结构简图,输入为电机的转角θ,输出为工作台的位移L X 、图中1J 、2J 和1K 、2K 分别为电机轴及丝杠轴上的转动
惯量和扭转刚度;m 为工作台质量、f 为导轨运动的粘性阻尼系数、0K 为丝杠螺母副的综合拉压刚度;i 是齿轮减速比,1>i 、
图1 数控机床的结构简图
在综合考虑传递链的刚性和阻尼后,可得到如下输入、输出的微分方程式:
θπL K i
s X K dt dX f dt X d J L L L L L L ⋅=++22 (1) 式中:L J ——折算到丝杠轴上的总惯量;
L f ——折算到丝杠轴上的导轨粘性阻尼系数;
L K ——折算到丝杠轴上的机械传递装置总刚度;
S ——丝杠导程、
设机械传动装置的传递函数为)(s G L ,
可见数控机床的机械进给传动装置可以简化为一个二阶环节、2 稳定性能分析
位置伺服系统的稳态性能指标主要是定位精度,指的是系统过渡过程终了时实际状态与期望状态之间的偏差程度、一般数控机床的定位精度应不低于0.01mm,而高性能数控机床的定位精度将达到0.001mm以上、影响伺服系统稳态精度的原因可以有两类,一类是位置测量装置的误差和测量误差;另一类是系统误差,系统误差与系统输入信号的性质和形式有关,也与系统本身的结构和参数有关、本文主要讨论系统误差对稳态精度的影响,伺服系统的任务也可以说是要尽可能使系统的输出准确地跟踪给定输入,同时,各种扰动输入对系统跟踪精度的影响应当减少到最小、
下面将讨论几种典型信号输入或扰动干扰输入情况下的误差分析、
2.1 单位阶跃给定输入时的稳态误差
经简化整理后二阶典型伺服系统结构框图见图2所示,其中)(s
G
k
是系统的开环传递函数,K为开环放大倍数,T为时间常数、由于开环传递函数中只包含一个积分环节,习惯上亦称为I型系统、
在单位阶跃给定输入下,即输入信号s
( 、
)
s
R1
由于
经整理得:
利用拉氏变换的终值定理,求得系统的稳态误差、
上式表明,在单位阶跃的给定输入下,I型系统的稳态误差为零,这个结论是在忽略电机轴上负载的条件下才成立的、由于伺服系统电机的转速到位移之间是一个积分环节,只要输出)(t
C与输入)(t
R不相等,它们之间的偏差电压经放大后就使电机旋转,当负载为零时,电机将一直转到偏差电压等于零为止,因此稳态误差为零、如果考虑负载的话,则当电机输出转矩与负载转矩平衡时工作停止、为了维持这个转矩,放大器输入端就得有一定的偏差电压,因而稳态误差不等于零、
2.2 单位速度给定输入时的稳态误差
单位速度输入信号2
R ,稳态误差:
t
1
)(s
(5)式表明在单位速度给定输入时,I型系统的稳态误差等于开环放大倍数的倒数,这说明在速度输入下,要实现准确跟踪,电机的输出轴必须随着作同步变化,因此电机的电枢上应保持有一定数值的电压、由于I型系统中,只有一个积分环节,放大器只能是比例环节,要维持一定的电枢电压,放大器输入端必须有一个偏差电压,所以系统的稳态误差不会等于零、当然开环放大倍数W越大,稳态误差的值愈小、
2.3 单位恒值负载扰动输入的影响
如前所述,伺服系统所承受的各种扰动作用也是要影响系统的跟
随精度、扰动可来自负载X 检测装置及其它各种原因、最常见的扰动是负载扰动和从测量装置引入的噪声干扰、为了简便,仅讨论单位恒值负载扰动的影响、
图3 所示是给定输入为零,只考虑负载扰动输入时的系统结构图、
图3中)(1s G 表示M 作用点之前的传递函数,)(2s G 是M 作用点之后的传递函数、对于I 型系统)(1s G 中没有积分环节,)(2s G 中包含一个积分环节、对于单位恒值负载扰动s s M 1)( 、
设由M 引起的稳态误差为f e ,其拉氏变换式为)(s E f 、
由于
图3 负载扰动输入时的系统结构图
图3所示,可以更清楚地表达负载扰动输入下的系统结构、
这表明恒值负载扰动会使I型系统产生稳态误差,误差值的大小与负载扰动作用点之前的传递函数的放大倍数成反比、
3 实验结果与结论
经过以上理论分析,我们在日本安川公司SGDL-0:AP交流伺服系统上进行了动态实验,实验结果如图4、图5所示,图4为系统突加负载1P.U.时的伺服电机电流响应,实验结果看出,电机负载发生扰动变化时,其电流将有所变化,但最终趋于稳定、图5为伺服系统的过渡过程响应曲线,从图5中可以看出,该伺服电机在负载扰动时,系统将有一定的震荡现象,但系统能有效抑制脉动转矩,成功牵入同步稳定状态、
由此得出结论,如果一个伺服系统在给定输入作用下输出响应的超调量较大、过程时间越短,则它的抗干扰性能就好;而超调量较小,过渡过程时间较长的系统,恢复时间就长(除非调节对象的时间常数很小)、这就是二阶典型系统的跟随性能与抗干扰性能之间存在一定的内在制约和矛盾的地方,也是这类闭环伺服控制系统固有的局限性、
图4 系统突加负载时的电流响应
图5 伺服系统的过渡过程响应曲线
4 伺服数控系统线路设计及其实物样机
南京工业大学研制开发了高性能交流伺服(数控机床)控制系统。
该系统性能稳定,质量可靠,可广泛应用于数码雕刻、包装机械、模具生产等工业生产应用场合,更适用于高等学校机电一体化,电子电器,电气自动化专业学生(研究生)生产实习,课程设计等课程的实验研究。
该系统的实物样机如图6所示。
图6 现代交流伺服系统的实物设计构成
主要性能指标:
电源:50Hz,(%
5.0交流变频;
2,主轴:Kw
220 )V,功率Kw
10
X,Y,Z轴伺服驱动:日本W
400、W
400;
750、W
数控加工功能:X,Y,Z三轴联动/主轴切割转速可达m in
15000r无
级调速;
加工最大尺寸:mm mm mm 200500600⨯⨯,定位精度:0.001mm ; 编程格式:国际ISO 标准DIN66025国际标准代码格式编程,可接收CAD 、CAM (DXF 格式)文件,有高级语言接口,二次开发能力强,加工程序图形模拟和动态跟踪显示。
伺服控制:采用全日本进口交流伺服电机,最高转速in m r 5000,编码器脉冲输出R P 16384振动等级:V15力矩输出:(max)16.7~39.2m N ⋅冷却方式:IP55自冷。
参考文献:
[1] 任仲贵主编.现代制造工程[M].上海:中国纺织大学出版社,1999.
[2] 张根保著.先进制造技术[M].重庆:重庆大学出版社,1996.
[3] 刘跃南主编.机床计算机数控及其应用[M].北京:机械工业出版社,1997
[4] 唐荣锡主编.柔性制造系统[M].北京:北京航空航天大学出版社,1994.
[5] W.莱昂哈特.电气传动控制[M].北京:科学出版社,1986.9.
[6] 舒志兵,李俊.PWM 电压型逆变器的数学模型分析[J].南京化工大学学报,2001,23(5):61-63.
[7] 国家自然科学基金委员会工程与材料科学部.机械工程科学技术前沿[M].北京:机械工业出版社,1996.
[8] Juang,Jyh ching.On adaptive special design in optical disco-servo system[J].IEEE Transactions on control system technology,2000,8(6):971-978.
[9] 杨先逵主编.计算机辅助机械制造[M].北京:清华大学出版社,1998.。