数控机床操作入门
数控车床基本操作

数控车床基本操作数控车床是一种自动化程度较高的机床,它具有高精度、高效率、高灵活性等优点。
下面我将为你介绍数控车床的基本操作流程。
一、开机与关机1.开机:首先打开电源总开关,然后按下数控系统主电源开关,等待系统自检完成后,确认各轴电机及其他部件均正常运作,即可开始操作。
2.关机:在使用完毕后,首先关闭程序运行,然后按下系统的关机按钮,等待数控系统自动关机后,再关闭电源总开关。
二、工件装夹与刀具安装1.工件装夹:根据工件的形状和尺寸,选择合适的夹具进行装夹,并确保工件稳固可靠,不会出现偏移、晃动等情况。
2.刀具安装:根据加工工序和工件要求,选择合适的刀具,并按照图纸或工艺要求将刀具正确安装到刀柄上,并紧固好。
三、参数设置与程序输入1.参数设置:根据工件材料、刀具规格、加工工艺等因素,设置合适的加工参数,如切削速度、进给速度、切削深度等。
2.程序输入:使用国际通用的G代码编写加工程序,并将程序输入到数控系统中。
程序输入方式可以是手动方式输入,也可以通过CAD/CAM软件导入。
四、手动操作1.手动进给:在手动操作模式下,通过手动旋转手轮或按动控制按钮,控制轴向的移动速度和方向,实现工件的粗定位、精定位,以及切削进给等操作。
2.手动换刀:根据刀具的尺寸和使用顺序,手动将刀具进行更换,并通过手动输入刀具偏移量,更新系统中的刀具补偿数据。
五、自动操作1.自动运行:在程序输入完成后,通过数控系统的自动运行功能,启动程序运行,机床将自动按照程序指定的加工路径,进行自动操作。
2.自动换刀:当程序中需要更换刀具时,数控系统会自动暂停加工程序,同时发出换刀信号,操作人员可以进行刀具更换等操作。
六、实时监控与调整1.监控:在加工过程中,随时监控数控系统显示屏上的运行状态、报警信息等,以确保机床正常运行,并及时发现和解决问题。
2.调整:根据加工中的情况,及时调整切削参数、刀具补偿值等,以保证加工质量和效率。
七、加工结束与设备维护1.加工结束:当加工完成后,确认工件质量合格后,停止加工程序运行,并进行必要的测量、检查等工作,以确保工件符合要求。
数控加工中心新手操作需要学习的7个步骤

数控加工中心新手操作需要学习的7个步骤数控加工中心新手操作需要学习的7个步骤数控加工中心(numerically controlled production center)是一种功能较全的数控加工机床;是世界上产量最高、应用最广泛的数控机床之一。
今天店铺给大家讲讲数控加工中心新手操作需要学习的7个步骤,希望大家喜欢。
一、开机准备机床在每次开机或机床按急停复位后,首先回机床参考零位(即回零),使机床对其以后的操作有一个基准位置。
二、装夹工件工件装夹前要先清洁好各表面,不能粘有油污、铁屑和灰尘,并用锉刀(或油石)去掉工件表面的毛刺。
装夹用的等高铁一定要经磨床磨平各表面,使其光滑、平整。
码铁、螺母一定要坚固,能可靠地夹紧工件,对一些难装夹的小工件可直接夹紧在虎上;机床工作台应清洁干净,无铁屑、灰尘、油污;垫铁一般放在工件的四角,对跨度过大的工件须要在中间加放等高垫铁。
根据图纸的尺寸,使用拉尺检查工件的长宽高是否合格。
装夹工件时,根据编程作业指导书的装夹摆放方式,要考虑避开加工的部位和在加工中刀头可能碰到夹具的情况。
工件摆放在垫铁上以后,就要根据图纸要求对工件基准面进行拉表,对于已经六面都磨好的工件要校检其垂直度是否合格。
工件拉表完毕后一定要拧紧螺母,以防止装夹不牢固而使工件在加工中移位的现象;再拉表一次,确定夹紧好后误差不超差。
三、工件碰数对装夹好的工件可利用碰数头进行碰数定加工参考零位,碰数头可用光电式和机械式两种。
方法有分中碰数和单边碰数两种,分中碰数步骤如下:光电式静止,机械式转速450~600rpm。
分中碰数手动移动工作台X轴,使碰数头碰工件一侧面,当碰数头刚碰到工件使红灯亮时,就设定这点的相对坐标值为零;再手动移动工作台X轴使碰数头碰工件的另一侧面,当碰数头刚碰上工件时记下这时的相对坐标。
根据其相对值减去碰数头的直径(即工件的长度),检查工件的长度是否合符图纸要求。
把这个相对坐标数除以2,所得数值就是工件X轴的中间数值,再移动工作台到X轴上的中间数值,把这点的X轴的相对坐标值设定为零,这点就是工件X轴上的零位。
数控机床操作面板图文详解
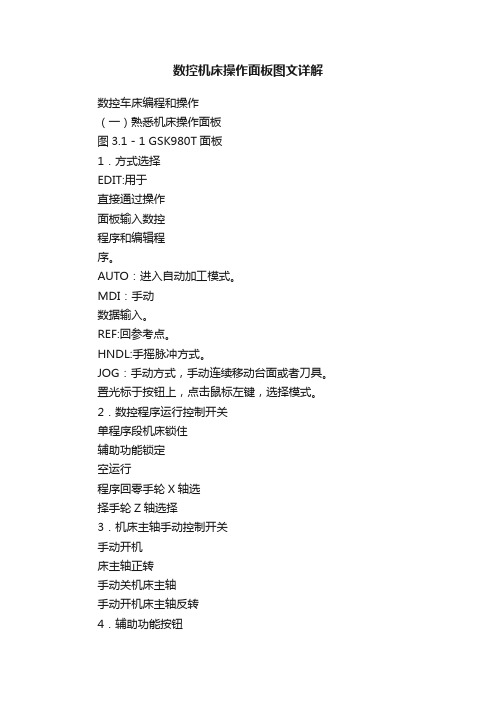
数控机床操作面板图文详解
数控车床编程和操作
(一)熟悉机床操作面板
图3.1-1 GSK980T面板
1.方式选择
EDIT:用于
直接通过操作
面板输入数控
程序和编辑程
序。
AUTO:进入自动加工模式。
MDI:手动
数据输入。
REF:回参考点。
HNDL:手摇脉冲方式。
JOG:手动方式,手动连续移动台面或者刀具。
置光标于按钮上,点击鼠标左键,选择模式。
2.数控程序运行控制开关
单程序段机床锁住
辅助功能锁定
空运行
程序回零手轮X轴选
择手轮Z轴选择
3.机床主轴手动控制开关
手动开机
床主轴正转
手动关机床主轴
手动开机床主轴反转
4.辅助功能按钮
冷却液润滑液
换刀具5.手轮进给量控制按钮
选择手动台
面时每一步的距离:0.001毫米、0.01毫米、0.1毫米、1毫米。
置光标于旋钮上,点击鼠标左键选择。
6.程序运行控制开关
循环停止
循环启动 MST选择停
止
7.系统控制开关
NC启动
NC停止8.手动移动机床台面按钮
选择移动轴,正方向移动按钮,负方向移动按钮。
快速进给9.升降速按钮
主轴升降速/快速进给
升降速/进给升降速
10紧急停止按钮(12)手轮
(二)熟悉GSK980T数控系统的输入面板
图3.2-1 GSK980T输入面板1.按键介绍
(1)数字键(2)字母键
数字/字母键用于输入数据到输入区域(如下图所示),系统自动判别取字母还是取数字。
图3.2-2。
最简单数控操作方法

最简单数控操作方法数控机床(Numerical Control Machine Tool,简称CNC)是在计算机的控制下运行的机床,它是在传统机床基础上发展起来的高效、精确的自动化设备。
数控操作方法是指如何使用数控机床进行加工,下面我将详细介绍最简单的数控操作方法。
首先,数控操作方法的第一步是开机操作。
在开机前,我们需要确保电源线连接稳定,控制系统电源开关处于关闭状态。
然后,按下主控开关,启动电源,这时控制系统开始自检程序,如果没有报警信号,便可以进行下一步。
第二步是打开机床电源。
按下机床电源开关,启动所有部分的电源,包括电机、泵站等。
等待机床回零,即各轴回到机床坐标系的原点位置。
在此过程中,操作人员要注意观察数控系统的显示屏,确认回零是否完成。
第三步是加载工艺程序。
在数控加工之前,需要通过数据传输介质(如U盘、电脑等)将加工程序转移到数控机床的控制系统上。
完成程序下载后,需要进行程序编辑,即对程序进行查看和检查,确保程序的正确性和合理性。
同时,还需要设置加工参数,如加工速度、切削深度等。
第四步是夹持工件。
将待加工的工件放置在机床工作台上,并用夹具夹紧。
夹紧时要确保工件牢固不松动,以免影响加工精度和安全性。
第五步是进行工件坐标系的设定。
在进行数控加工之前,需要确定工件的坐标系,以便数控系统能够正确地定位和加工。
一般情况下,可以使用机床的机械坐标系或工件坐标系,根据实际情况选择。
第六步是进行刀具的装夹和刀具长度的设定。
根据工艺程序的要求,选择相应的刀具,并将其安装在机床的刀柄上。
完成刀具装夹后,还需要设定刀具的长度,使其正确与工件接触。
第七步是进行刀具补偿和刀具半径设定。
在数控切削加工中,由于刀具的磨损和刃口的尺寸误差等因素,往往需要进行刀具补偿。
通过数控系统的相关操作,确定需要进行刀具补偿的参数,并将其设置为合适的数值。
同时,还需要进行刀具半径的设定,以纠正刀尖偏差对加工精度的影响。
第八步是进行加工参数的设定。
cnc数控机床新手入门教程书本

CNC数控机床新手入门教程书本
第一章:认识数控机床
在当前制造业中,数控机床的地位日益重要。
数控机床是一种通过计算机程序
控制工作过程的机床,可以高效、精准地加工各种零件。
本章将介绍数控机床的基本概念、分类和优势。
第二章:数控编程基础
数控编程是使用计算机程序来控制数控机床的基础。
本章将介绍数控编程的基
本原理、常用代码和语法规则,帮助新手掌握编程技能。
第三章:数控机床操作
操作数控机床需要掌握操作面板、参数设置、工件装夹等技能。
本章将介绍数
控机床的操作流程和注意事项,帮助新手熟练操作机床。
第四章:数控加工工艺
数控加工是数控机床的核心应用领域,包括铣削、车削、钻削等加工工艺。
本
章将介绍各种加工工艺的原理、应用和优缺点,帮助新手理解加工过程。
第五章:数控机床维护与保养
数控机床是昂贵的设备,需要定期维护和保养才能保持良好状态。
本章将介绍
数控机床的常见故障及排除方法、维护保养技巧,帮助新手延长机床的使用寿命。
结语
通过本教程,希望新手能够快速入门数控机床领域,掌握基本的操作、编程和
维护技能,为未来的发展打下坚实基础。
学习数控机床不仅可以提高技能,还可以拓宽职业发展的可能性,希望读者在实践中不断成长,探索更多机床应用的可能性。
数控机床基础操作方法

数控机床基础操作方法
数控机床基础操作方法包括以下几个步骤:
1. 打开电源:先找到机床的电源开关,将其打开。
2. 初始化机床:按照机床的操作说明书,按下初始化按钮或输入特定的命令进行机床的初始化操作。
3. 选择工艺程序:根据加工零件的要求,选择相应的工艺程序。
通常可以通过键盘输入程序号或者选择菜单中的程序。
4. 装夹工件:将要加工的工件安装到机床的工作台上,并用夹具进行夹紧。
5. 设置工件坐标系:通过机床的坐标轴控制系统,设置工件坐标系的原点和参考坐标。
6. 设置加工参数:根据加工零件的要求,设置加工参数,包括加工速度、进给速度、切削速度等。
7. 运行程序:输入指令,启动加工程序。
程序将自动控制机床进行加工操作。
8. 监控加工过程:通过机床的显示屏或监控系统,实时监控加工过程,检查加
工状态是否正常。
9. 完成加工:当加工程序执行完毕后,机床会停止运动。
将工件从机床上取下,并进行必要的检查和测量。
10. 关闭机床:关闭电源开关,结束机床的操作。
需要注意的是,数控机床的操作方法可能因不同的机床品牌和型号而有所不同,操作前最好阅读相应的操作手册或咨询专业人员。
此外,在操作过程中应注意安全,避免发生意外事故。
数控机床操作入门
数控机床操作入门一、基本原理数控机床通过计算机控制系统,将加工工艺参数输入到机床中,并由机床自动执行加工操作。
其主要原理包括:输入加工程序—调整机床工作参数—启动机床执行加工操作。
二、数控机床的组成数控机床主要包括机床本体、数控装置和操作台。
其中,机床本体是进行实际加工的部分,数控装置是控制机床运行的核心,操作台用于操作机床和设置加工参数。
三、数控机床的操作流程1.开机准备首先,按下机床的开关按钮,待机床自检完成后,将键盘锁解除,启动数控装置。
2.加工程序输入将预先编好的加工程序输入到数控装置中。
一般来说,加工程序由若干行指令组成,每行指令包括几组代码,用于控制机床的运动、速度、方向等参数。
注意加工程序的输入要准确无误。
3.机床坐标系设置机床坐标系是指数控机床中与零点、参考点相关的坐标系。
根据加工要求,需要在机床上设置坐标系。
可以通过机床上的数显装置,将刀具移动到指定位置,然后设置坐标系。
4.加工参数设置加工参数包括切削速度、进给速度、刀具半径补偿等。
根据加工要求,在数控装置中设置相应的参数。
5.刀具更换将原有的刀具拆卸下来,并将新刀具安装好。
注意刀具的安装要牢固,以免引起事故。
6.手动操作调试在自动运行前,可以选择手动操作调试功能进行调试。
通过手动按钮可以分别控制各个轴的运动,确保机床的运动轨迹正确。
7.运行加工程序调试无误后,可以启动机床运行加工程序。
注意观察加工过程中是否出现异常情况,如异常声音、振动等,及时停机检修。
8.加工结果检验加工完成后,进行加工结果的检验。
可以使用量具、测量仪器等进行测量,与预定尺寸进行对比,判断加工结果是否合格。
四、数控机床操作的注意事项1.提前准备好加工程序、加工参数等相关数据,确保准确无误。
2.加工前必须确认机床状态良好,各项功能正常。
3.在操作过程中,要时刻观察机床运行情况,确保安全操作。
4.加工结束后,及时清理机床,保证机器的使用寿命。
总结:数控机床操作入门需要熟悉机床的基本原理和组成部分,掌握数控机床的操作流程并注意相应的注意事项。
数控车床操作步骤
数控车床操作步骤一、开机准备1.检查数控车床的电源线是否接地良好,各联接线是否连接紧密。
2.检查各轴的润滑情况,润滑油是否足够。
3.打开数控系统主机电源,同时打开数控机床电源开关并确认所有系统各轴运行状态指示灯正常。
二、上工件1.将要加工的工件放在数控车床工作台上,固定好。
2.检查工件是否安装正确,是否固定牢固。
三、安装刀具1.打开刀塔盖板,清理刀塔槽内的杂物。
2.选择合适的刀具,并检查其磨损状况。
将刀具安装在刀塔上,并确保刀具固定牢固。
3.调整刀具的位置,使其与工件表面夹角适当。
四、调整工件坐标系1.打开数控系统主界面,进入坐标系调整界面。
2.按照要求输入工件的坐标数据,调整工件的坐标系。
3.利用手动操作功能,将工件移动至数控车床零点位置,并保存零点坐标。
五、编写加工程序1.在数控系统中选择合适的编程方式,如G代码或M代码。
2.编写加工程序,包括切削数据、进给数据、刀具路径、起始点等。
3.检查程序的正确性,并保存程序。
六、加载加工程序1.将已编写好的加工程序通过U盘或其他存储设备导入数控系统中。
2.进入程序管理界面,选择需要加载的加工程序,并执行加载操作。
七、开机自检1.执行数控系统开机自检程序,包括各轴回零、刀具长度补偿、刀具半径补偿等。
2.检查数控系统是否正常运行,并观察各轴的运动是否准确。
八、开始加工1.调整加工速度和进给速度,确保加工过程的稳定性。
2.执行加工程序,观察加工过程中刀具和工件的状态,并进行必要的调整。
3.完成加工后,关闭数控车床电源开关并清理加工现场。
总结:。
数控机床操作入门
数控机床操作入门
数控机床是一种以数字化控制系统为基础,通过控制系统程序自动控制机床进行加工操作的一种先进设备。
它在现代制造领域中扮演着至关重要的角色。
想要操作好数控机床,需要掌握一定的基础知识和技能。
本文将介绍数控机床的基本原理、操作流程和常见问题解决方法,帮助初学者快速入门数控机床操作。
数控机床基本原理
数控机床的核心是数控系统,它由硬件和软件两部分组成。
硬件部分包括机床本体、数控装置、执行机构等,而软件部分则负责编写控制程序和参数设置。
数控机床通过数控系统的指令控制各轴运动和加工过程,实现高精度的零件加工。
数控机床操作流程
步骤一:开机准备
1.打开主电源
2.启动数控系统
3.进行刀具和夹具的安装
步骤二:编写加工程序
1.使用专业软件编写加工程序
2.设置加工参数和路径
步骤三:检查程序和零件定位
1.检查加工程序是否正确
2.将工件正确装夹定位
步骤四:调试和加工
1.手动试运转各轴
2.开始自动加工操作
步骤五:加工完成和关机
1.检查加工零件质量
2.关闭数控系统和机床
常见问题解决方法
加工误差过大
1.检查机床各轴的运动是否顺畅
2.调整刀具和工件的安装角度
程序错误
1.检查编写的加工程序有无错误
2.重新编写加工程序并调试
总结
数控机床操作是一门复杂而重要的技能,需要系统地学习和实践。
通过掌握数
控机床的基本原理、操作流程和常见问题解决方法,可以提高工作效率和加工质量。
希望本文能对初学者有所帮助,让大家更好地理解和掌握数控机床操作技能。
数控机床新手入门教程
数控机床新手入门教程第一章:数控机床基础知识在工业领域,数控机床被广泛应用于各种加工过程中,它的出现极大地提高了生产效率和产品质量。
但是对于新手来说,数控机床可能显得复杂和难以理解。
在本章中,我们将介绍数控机床的基础知识,帮助新手快速入门。
1.1 什么是数控机床?数控机床是一种能够依靠程序控制工件加工过程的机床。
通过预先设定的程序,数控机床可以自动地执行各种加工操作,如铣削、钻孔、切割等。
相比传统机床,数控机床具有更高的精度和生产效率。
1.2 数控机床的组成数控机床通常由控制系统、执行系统和机械系统三部分组成。
控制系统负责接收和解释加工程序,执行系统负责实际执行加工操作,机械系统则是实现工件的定位和固定。
这三个系统密切配合,共同完成加工任务。
1.3 数控编程数控编程是数控机床的核心技术之一。
编写良好的数控程序可以确保加工过程顺利进行。
数控编程语言通常包括G代码和M代码,新手需要掌握这些代码的基本规则和语法。
第二章:数控机床操作指南在掌握了数控机床的基础知识后,接下来是学习如何正确操作数控机床。
本章将介绍数控机床的操作流程和注意事项,帮助新手顺利上手。
2.1 数控机床的启动和停止在操作数控机床之前,首先需要进行机床的启动操作。
启动过程包括打开电源、检查机床状态等步骤。
而停止操作则是在加工结束后的必要步骤,确保机床安全关闭。
2.2 参考坐标系和工件坐标系的设置在进行加工操作之前,需要确立参考坐标系和工件坐标系。
参考坐标系是机床的基准点,工件坐标系则是工件上各点相对于基准点的坐标。
正确设置坐标系可以保证加工的准确性。
2.3 加工参数的调整根据加工要求,需要对数控机床的加工参数进行调整。
这包括刀具速度、进给速度、切削深度等参数的设置。
合理的加工参数可以提高加工效率和产品质量。
结语数控机床作为现代工业的重要设备,对于新手来说可能有一定的学习曲线。
但是只要掌握了基础知识和操作技巧,就能够轻松应对各种加工任务。
- 1、下载文档前请自行甄别文档内容的完整性,平台不提供额外的编辑、内容补充、找答案等附加服务。
- 2、"仅部分预览"的文档,不可在线预览部分如存在完整性等问题,可反馈申请退款(可完整预览的文档不适用该条件!)。
- 3、如文档侵犯您的权益,请联系客服反馈,我们会尽快为您处理(人工客服工作时间:9:00-18:30)。
目录第一章绪论近来来,数控技术的发展十分迅速,数控机床的普及率越来越高,在机械制造业中得到了广泛的应用。
制造业的工程技术人员和数控机床的操作与编程技术人员对数控机床及其操作与编程技术的需求越来越大。
数控机床是一种完全新型的自动化机床,是典型的机电一体化产品。
数控技术集计算机技术、成组技术、自动控制技术、传感检测技术、液压气动技术以及精密机械等高新技术于一体,是现代化制造技术的基础技术和共性技术。
随着数控机床的广泛应用,急需培养大批能熟练掌握现代数控机床编程、操作、维修的工程技术人员。
为普及与提高数控加工新技术,本教程针对目前广泛运用的FANUC和SIEMENS两种系统进行操作介绍。
第二章数控车床结构第一节数控车床简介数控车床分为立式数控车床和卧式数控车床两种类型。
立式数控车床用于回转直径较大的盘类零件的车削加工。
卧式数控车床用于轴向尺寸较长或小型盘类零件的车削加工。
相对于立式数控车床来说,卧式数控车床的结构形式较多、加工功能丰富、使用面广。
本教程主要针对卧式数控车床进行介绍。
卧式数控车床按功能可进一步分为经济型数控车床、普通数控车床和车削加工中心。
1.经济型数控车床采用步进电动机和单片机对普通车床的车削进给系统进行改造后形成的简易型数控车床,成本较低,但自动化程度和功能都比较差,车削加工精度也不高,适用于要求不高的回转类零件的车削加工。
2.普通数控车床根据车削加工要求在结构上进行专门设计并配备通用数控系统而形成的数控车床,数控系统功能强,自动化程度和加工精度也比较高,适用于一般回转类零件的车削加工。
这种数控车床可同时控制两个坐标轴,即X轴和Z轴。
3.车削加工中心在普通数控车床的基础上,增加了C轴和动力头,更高级的机床还带有刀库,可控制 X、Z和 C三个坐标轴,联动控制轴可以是(X、Z)、(、C)或(Z、C)。
由于增加了C轴和铣削动力头,这种数控车床的加工功能大大增强,除可以进行一般车削外,还可以进行径向和轴向铣削、曲面铣削、中心线不在零件回转中心的孔和径向孔的钻削等加工。
在卧式数控车床上可车削加工的零件如图2-l所示。
数控车床由数控系统、床身、主轴、进给系统、回转刀架、操作面板和辅助系统等部分组成。
图2-2、图2-3所示分别为韩国大宇重工生产的立式数控车床PUMA-VIS和卧式车削加工中心PUMA.SHC.3A。
图2-1 车削加工的零件种类图2-2 立式数控车床图2-3 卧式车削加工中心第二节数控车床的卡盘和尾架液压卡盘是数控车削加工时夹紧工件的重要附件,对一般回转类零件可采用普通液压卡盘;对零件被夹持部位不是圆柱形的零件,则需要采用专用卡盘;用棒料直接加工零件时需要采用弹簧卡盘。
对轴向尺寸和径向尺寸的比值较大的零件,需要采用安装在液压尾架上的活顶尖对零件尾端进行支撑,才能保证对零件进行正确的加工。
尾架有普通液压尾架和可编程液压尾架。
图2-4所示分别为普通液压卡盘和液压尾架,图2-5所示为利用液压尾架进行车削加工。
图2-4 液压卡盘和液压尾架a)普通液压卡盘 b)液压尾架图2-5 车削加工状态第三节数控车床的刀架刀架是数控车床非常重要的部件。
数控车床根据其功能,刀架上可安装的刀具数量一般为8把、10把、12把或16把,有些数控车床可以安装更多的刀具。
刀架的结构形式一般为回转式,刀具沿圆周方向安装在刀架上,可以安装径向车刀、轴向车刀、钻头、镜刀。
车削加工中心还可安装轴向铣刀、径向铣刀。
少数数控车床的刀架为直排式,刀具沿一条直线安装。
数控车床可以配备两种刀架:1.专用刀架由车床生产厂商自己开发,所使用的刀柄也是专用的。
这种刀架的优点是制造成本低,但缺乏通用性。
2.通用刀架根据一定的通用标准内 VDI,德国工程师协会)而生产的刀架,数控车床生产厂商可以根据数控车床的功能要求进行选择配置。
图2-6和图2-7所示分别为一种专用刀架和VDI通用刀架。
图2-6 专用刀架图2-7 VDI刀架第四节数控车床的刀具在数控车床或车削加工中心上车削零件时,应根据车床的刀架结构和可以安装刀具的数量,合理、科学地安排刀具在刀架上的位置,并注意避免刀具在静止和工作时,刀具与机床、刀具与工件以及刀具相互之间的干涉现象。
数控车床上常用的刀具如图2-8所示。
图2-8 数控车床常用刀具第三章 FANUC系统数控车床操作第一节 FANUC O-TD数控系统简介FANUCO-D系列是具有与O-C系列同等的高可靠性的CNC系统是世界上是最成功的CNC,精确的测试和完整质量控制确保其故障率很低,O-D系列配置高可靠性的FANU C αC系列和β系列AC伺服电机,机床主轴可配置高速,大功率的FANUC AC 主轴电机系列。
O-D系列以功能包的方式提供给用户,它包括CNC单元、控制电机、主轴电机和控制电机放大器。
O-TD有O-TD和O-TD Ⅱ两种配置,OMD有O-MD Ⅱ-种配置。
用户可根据具体应用选择最佳的系统配置。
FANUC O-TD车床仿真系统是一个基于WINDOWS操作系统的应用软件,可根据各种电脑排版软件生成的G代码进行加工,如MASTCAM,还可以根据手写G代码数控程序进行加工。
该系统是基于WINDOWS应用软件,并对BEIJING-FANUC Series O-TD数控系统进行高度仿真,具有良好的人机界面和简便的操作性能;具有同FANUC O-Series CNC控制器相同的屏幕、面板组成和功能,加载NC文件时,自动对程序进行语法检查;具有自动、编辑、MDI、MPG、JOG 等模式和Dry、M01等开关;编辑模式中,实时提供G代码功能与格式提示信息系统实时处理NC 代码,生成机床移动指令。
第二节控制面板与操作FANUC O-TD主界面如下图所示:界面上的部件可以分为四个区域:1.数控机床电源2.屏幕显示3.屏幕字符输入键区4.控制按钮和旋钮区下面详细介绍界面的各个部分:1.数控机床电源为电源开关和电源指示灯,“ON”按钮表示开电源,“OFF”按钮表示关电源。
右边边的是一个指示灯,当启动电源时,指示灯变成红色,当关闭电源,指示灯恢复原来的颜色。
2.屏幕显示屏幕显示如下图所示:屏幕主显示区:主要显示当前的加工状态,如当前机床系和工件系的X,Z坐标值,主轴转速,进给速度,以及输入各种参数的值,当系统读入加工文件后,此区域还可以显示加工的G代码。
屏幕下方显示菜单,菜单的选择依靠下方的菜单软键,菜单有嵌套,一个菜单下可能有若干个子菜单,通过菜单,我们能访问到系统所有的功能和设置。
操作菜单依靠下面介绍的菜单功能键。
屏幕的最下面是菜单功能区,即软键,各软键的具体名称随按下的功能键而改变。
菜单功能键区:中间的五个按钮对应着屏幕中的五个菜单,按下菜单软键即选择了相对应的菜单命令。
左边第一个按钮的功能是向左滚动菜单。
按钮的功能是向右滚动菜单。
3.屏幕字符输入键区屏幕字符键区如下图所示:屏幕字符键主要在撰写和修改程序时用到:键为上档键,当按下此键后,在屏幕中将有显示,表示现在处于上档2状态。
再按下此键后,在屏幕中将有显示,表示现在处于上档3状态。
对于按钮来说,当上档键没有按下时,输入屏幕的将是“K”字符,而当上档键按下一次时,输入则为“J”,而当上档键按下两次时,输入则为“I”。
键为退格键,用于删除前一字符,相当于键盘上的BackSpace键。
键用于输入在“插入”和“替换”间切换。
键用于删除当前文本。
用于光标向前和光标向后定位。
则是向上翻页和向下翻页。
用于输入空格。
是回车键,相当于键盘上的Enter键。
键在程序编辑状态下用于输出当前编辑的文件。
键用于显示当前绝对坐标和相对坐标屏幕。
显示程序编辑屏幕。
显示坐标偏置设置屏幕。
显示刀具参数的设置屏幕。
显示选项菜单。
各功能键的作用如下:1.位置功能键POS按功能键后,按对应的软键可以显示以下内容。
(1)全部坐标按软键“全部”后会显示如上图所示的全部坐标显示画面。
该画面中的X、Z是刀具在工件坐标系中当前位置的相对坐标和绝对坐标。
这些坐标值随刀具的移动而改变。
在该画面中还显示下列的内容:当前位置指示;当前程序名称;各个软键名称;当前运行方式;当前运行时间。
(2)绝对坐标当按软键“绝对”后会显示绝对坐标显示画面,如下图所示:(3)当按下软键“相对”后,所显示的内容除坐标为相对坐标值外,其余与绝对位置显示画面相同。
如下所示:2.程序功能键PRGRM按功能键后,出现如下所示的当前执行程序画面:按对应的软键:(1)软键菜单左滚键“<”显示左边还有的菜单按钮。
上面的显示已经包括最左的菜单软键了。
(2)软键【保存】保存目前的程序。
(3)软键【复制】复制选中的程序指令。
(4)软键【剪切】剪切选中的程序指令。
(5)软键【粘贴】粘贴选中的程序指令。
(6)软键【返回】返回到主菜单屏幕。
(7)软键菜单右滚键“>”显示右边还有的菜单按钮。
按下以后显示如下:(8)软键【删除】删除选中的程序指令。
(9)软键【程序】显示当前执行程序文件的属性。
再按就又回到前面的程序显示状态。
(10)软键【当前】显示当前的加工代码,并把当前的加工代码行高度变亮显示。
3.零点设置OFSET按该功能键以后可以进行工件坐标系设置和显示。
如下所示:如下图所示:当把刀具地刀位点移动到工件的最外圆一点时,输入刀位点的坐标数值,按下软键【确定】就确定了工件坐标系。
4.刀具参数设置键 TOOL PARAM按下该功能键后可以进行刀具补偿值的设置和显示,即进行对刀操作。
显示如下:按对应的软键:(1)软键【对刀】当刀具的刀位点移动到对刀参考点以后,按下这个软键就会自动的屏幕上显示出刀具的长度补偿值。
(2)软键【向前】显示前一把刀具的参数设置屏幕。
(3)软键【向后】显示后一把刀具的参数设置屏幕。
(4)软键【确认】确认输入的刀具的参数设置。
(4)软键【返回】返回到主菜单屏幕。
所谓对刀,就是要获知车刀与一把设定的基准刀在X轴和Z轴方向上的距离,也就是求刀补。
刀具正确安装后,接着要进行对刀。
下面介绍的对刀法,优点是无需特殊对刀工具,简便快速,有时1-2min就能对出一把刀,而且较为正确有效。
通常设定第1把进行车削的刀具为基推刀。
一般情况下,钻头、中心钻及复杂刀具不作基准刀,在安排工步时应予考虑。
例中认定外圆刀(1号刀)为基准刀。
将一根直径20-30mm的棒料夹在三爪自定心卡盘上,手动进给,先试切毛坯,把端面和外圆光一刀。
把刀具的刀尖移到工件的最外一点O(如下图所示),这样子就建立了如图所示的直角坐标系。
此时按软键【对刀】就设置了刀具补偿,完成了对刀。
如果2号刀是外螺纹刀,通过慢速点动,小心翼翼地将外螺纹刀刀尖刚刚接触上棒料地外圆最外一点,并最终使刀具处于图2所示位置。
这样子第二把刀就对好了,其他的刀具以此类推。
5.设置键MENU按下按钮,将出现选项菜单设置屏幕,如下图所示:默认显示的是【参数】子菜单屏幕,此时可以修改的系统参数有:1.进给率默认为400mm/min,进给速度最低为零,最大值由具体的机床决定。