机械加工工艺手册
机械加工工艺流程手册

机械加工工艺流程手册第一章概述 (2)1.1 加工工艺流程基本概念 (2)1.2 加工工艺流程的重要性 (2)第二章设计与工艺分析 (3)2.1 零件图样分析 (3)2.2 材料选择与处理 (3)2.3 加工工艺方案制定 (4)第三章铸造工艺 (4)3.1 铸造工艺流程 (4)3.2 铸件质量检验 (5)3.3 铸造缺陷分析与处理 (5)第四章锻造工艺 (6)4.1 锻造工艺流程 (6)4.2 锻件质量检验 (6)4.3 锻造缺陷分析与处理 (6)第五章焊接工艺 (7)5.1 焊接工艺流程 (7)5.2 焊缝质量检验 (7)5.3 焊接缺陷分析与处理 (7)第六章切削加工工艺 (8)6.1 切削加工工艺流程 (8)6.2 切削参数选择 (8)6.3 切削加工缺陷分析与处理 (9)第七章数控加工工艺 (9)7.1 数控加工工艺流程 (9)7.1.1 零件分析 (9)7.1.2 工艺路线规划 (9)7.1.3 编制工艺文件 (10)7.1.4 工装夹具设计 (10)7.1.5 零件加工 (10)7.2 数控编程与操作 (10)7.2.1 数控编程 (10)7.2.2 数控操作 (10)7.2.3 数控加工参数调整 (10)7.3 数控加工缺陷分析与处理 (10)7.3.1 缺陷分类 (10)7.3.2 缺陷分析 (10)7.3.3 缺陷处理 (11)7.3.4 预防措施 (11)第八章表面处理工艺 (11)8.1 表面处理工艺流程 (11)8.2 表面处理方法选择 (11)8.3 表面处理质量检验 (12)第九章装配工艺 (12)9.1 装配工艺流程 (12)9.2 装配方法与技巧 (12)9.3 装配缺陷分析与处理 (13)第十章质量管理与控制 (13)10.1 质量管理体系 (13)10.2 质量检验方法 (14)10.3 质量改进与持续改进 (14)第一章概述1.1 加工工艺流程基本概念加工工艺流程,指的是在机械制造过程中,按照一定的顺序和步骤,采用特定的加工方法,对原材料或半成品进行加工处理,使之成为符合设计要求的零件或组件的过程。
机械加工工艺手册第1卷

机械加工工艺手册第1卷
机械加工工艺手册第1卷是一本涵盖机械加工领域的教材或参考书籍。
它可能包含以下内容:
1. 机械加工基础知识:介绍机械加工的基本原理、工具和设备,包括不同类型的机床(如车床、铣床、钻床等)和切削工具(如车刀、铣刀、钻头等)。
2. 加工工艺流程:详细介绍不同材料(如金属、塑料、木材等)的加工工艺流程,包括材料选择、加工方法和工艺参数等。
3. 加工工艺参数:讲解加工过程中的关键参数,如切削速度、进给量、切削深度等,以及它们与加工质量和效率的关系。
4. 数控加工技术:介绍数控机床的原理和操作方法,包括程序编写、刀具路径规划和调整等。
5. 加工质量控制:讲解如何通过合理设置工艺参数和使用适当的检测工具(如千分尺、影像测量仪等)来控制加工质量。
6. 特殊加工工艺:介绍一些特殊的机械加工工艺,如线切割、电火花加工、激光加工等。
除了以上内容,机械加工工艺手册可能还包含实例和案例分析,以帮助读者更好地理解和应用所学知识。
由于各版权和出版社的差异,不同的机械加工工艺手册的内容和结构可能会有所不
同。
因此,在具体选择和购买之前,最好参考手册的目录和简介,以确定其是否满足自己的需求。
机械加工工艺手册
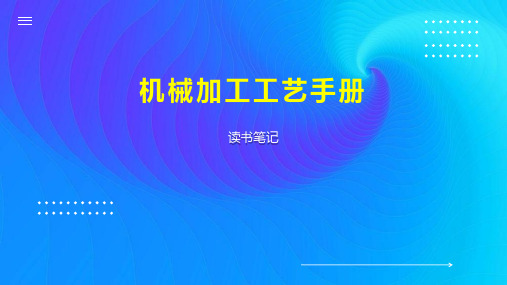
手册还针对不同工艺类型提供了丰富的实例和案例分析,帮助读者更好地理解实际生产中的问题, 提高解决实际问题的能力。这些案例分析涉及各种机械零件的加工过程,包括轴类零件、盘类零 件、箱体类零件和钣金件等,对于读者掌握机械加工工艺的实践应用非常有益。
“工欲善其事,必先利其器。”这句摘录深刻地阐述了工具在机械加工中的 重要性。机械加工离不开各种工具,而这些工具的性能和质量直接影响到加工的 精度和效率。因此,在机械加工过程中,选择合适的工具、保持工具的锋利和精 度至关重要。只有工具得心应手,才能事半功倍,提高加工效率。
另一句令人印象深刻的摘录是:“细节决定成败。”在机械加工中,细节的 把握至关重要。每一个微小的误差都可能影响到最终产品的质量和性能。因此, 机械加工者需要具备高度的责任心和严谨的态度,注重每一个细节,确保加工过 程中的精确控制。只有这样,才能生产出高质量的产品,赢得市场的认可。
作者简介
这是《机械加工工艺手册》的读书笔记,暂无该书作者的介绍。
谢谢观看
从整体结构上看,《机械加工工艺手册》的目录按照章节进行划分,每一章 都聚焦于机械加工过程中的一个特定领域或工艺。这种组织方式使得读者可以快 速找到他们需要的信息,提高了查询效率。
具体到每一章的内容,目录详细列出了该章所包含的各个小节。这些小节针 对具体的工艺流程、工具设备、材料特性、技术参数等进行了深入的阐述。这种 细致入微的分类方式使得读者可以对相关内容进行全面的了解。
机械加工工艺说明书

机械加工工艺说明书一、概述机械加工工艺是制造业中不可或缺的环节,其作用是将原材料经过一系列的加工工序,转变成最终的产品。
本说明书旨在详细介绍机械加工的各个环节及相应的操作要点,以便于操作人员能够准确地完成相关加工任务。
二、工艺流程1. 材料准备a) 根据产品要求,选用适当的原材料,并进行必要的检验和验收,确保其质量符合标准;b) 将材料切割成所需长度或尺寸,以便后续加工使用。
2. 设备准备a) 根据工艺要求,选择合适的机械设备,并对其进行调整和安装;b) 检查设备的各项功能,确保运行正常;c) 准备所需的刀具、夹具等辅助工具,并进行检查和清洁。
3. 工件装夹a) 根据产品图纸和工艺要求,选用合适的夹具,将工件固定在机床上;b) 确保工件夹紧牢固,防止在加工过程中产生位移或变形。
4. 切削加工a) 根据产品图纸,确定切削工艺参数,包括切削速度、进给量、切削深度等;b) 根据工艺要求,选择合适的刀具,并进行装配;c) 进行切削操作,注意操作规范和安全要求,确保加工质量。
5. 精加工a) 根据产品要求,进行相应的精加工工艺操作,如切割、车削、铣削等;b) 调整加工参数,保证精度和表面质量要求的满足。
6. 表面处理a) 根据产品要求,进行表面处理工艺操作,如研磨、抛光、喷涂等;b) 确保表面处理效果符合产品规范,并具备耐磨、耐腐蚀等特性。
7. 检验与评估a) 对加工完成的工件进行检验,包括尺寸、质量、外观等方面的评估;b) 将检验结果与产品要求进行对比,评估加工质量的合格性;c) 若发现不合格的情况,及时调整工艺参数或进行返工修正。
8. 包装与出货a) 根据产品要求,进行适当的包装,以确保产品安全运输;b) 准备相应的运输文件和证明文件,并按要求出具。
三、安全注意事项在进行机械加工过程中,为确保人身安全和设备正常运行,操作人员需要注意以下事项:1. 严格遵守相关安全操作规程,戴好防护设备;2. 使用机械设备前,确保设备正常运行,并对其进行检查和维护;3. 在加工过程中,避免发生意外,如刀具掉落、工件飞溅等;4. 操作中如遇异常情况,应立即停机检查,排除故障后方可继续操作;5. 加工或更换刀具时,注意切削部分的锋利度,避免误伤。
机械加工工艺手册
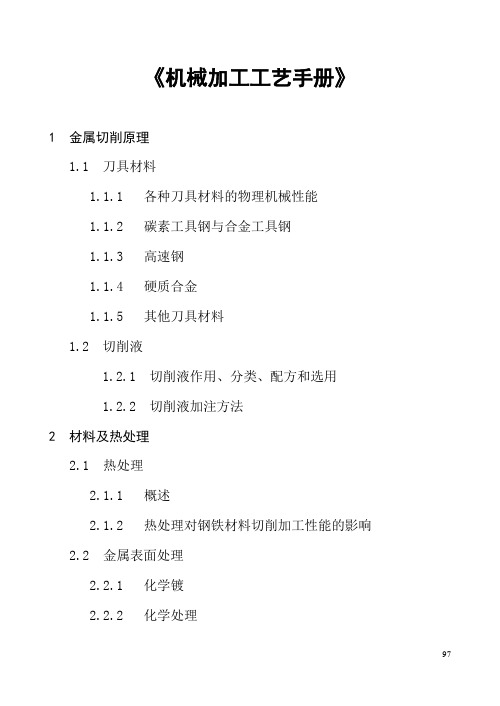
《机械加工工艺手册》1 金属切削原理1.1 刀具材料1.1.1各种刀具材料的物理机械性能1.1.2碳素工具钢与合金工具钢1.1.3高速钢1.1.4硬质合金1.1.5其他刀具材料1.2 切削液1.2.1 切削液作用、分类、配方和选用1.2.2 切削液加注方法2 材料及热处理2.1热处理2.1.1概述2.1.2热处理对钢铁材料切削加工性能的影响2.2金属表面处理2.2.1化学镀2.2.2化学处理972.2.3阳极氧化处理2.2.4喷镀2.2.5油漆涂装3 毛坯及余量3.1 毛坯种类和毛坯余量3.1.1轧制件3.1.2铸铁3.1.3锻件3.1.4冲压件3.1.5焊接件3.2 工序间加工余量3.2.1外圆柱表面加工余量及偏差3.2.2内孔加工余量及偏差3.2.3轴端面加工余量及偏差3.2.4平面加工余量及偏差3.2.5有色金属及其合金的加工余量3.2.6切除渗碳层的加工余量3.2.7齿轮和花键精加工余量4 机械加工质量984.1 机械加工精度4.2 机械加工表面质量4.2.1已加工表面粗糙度4.2.2加工硬化5 机械加工工艺规程制定5.1 工艺规程的编制5.2 零件结构的切削加工工艺性5.2.1工件便于装夹和减少装夹次数5.2.2减少刀具的调整与走刀次数5.2.3采用标准刀具,减少刀具种类5.2.4减少刀具切削空行程5.2.5避免内凹表面及内表面的加工5.2.6加工时便于进刀、退刀和测量5.2.7减少加工表面数和缩小加工表面面积5.2.8增加刀具的刚度与耐用度5.2.9保证零件加工时必要的刚度5.2.10 合理地采用组合件和组合表6 车削6.1 车削用量与车削参数计算996.1.1车床切削用量、车削力与车削功率6.1.2自动车床的车削用量6.2 卧式车床与立式车床加工7 铣削7.1 铣床7.1.1铣床主轴联系尺寸与工作台T形槽尺寸7.1.2铣床附件7.1.3铣床附加装置7.2 铣刀及其辅具7.2.1铣刀类型、几何参数与规格7.2.2硬质合金可转位铣刀与刀片7.2.3其他铣刀7.2.4铣刀直径和角度的选择7.2.5铣刀的安装与铣刀辅具7.3铣削用量及铣削钢的参数计算7.3.1铣削进给量的选择7.3.2确定铣削用量及功率常用表格7.3.3铣削切削时间的计算7.4铣削加工工艺1007.4.1分度头的分度计算与分度头应用7.4.2平面的精铣7.4.3型面精铣8 钻削8.1 钻床8.1.1钻床类型、技术参数与联系尺寸8.1.2立式钻床型号、技术参数与联系尺寸8.1.3摇臂钻床型号、技术参数与联系尺寸8.1.4排式钻床型号与技术参数8.1.5铣端面、打中心孔机床型号与技术参数8.1.6数控钻床与十字工作台钻床型号与技术参数8.2 刀具及其辅具8.2.1钻头8.2.2深孔钻8.2.3扩孔钻、锪钻(平底、锥面)8.2.4铰刀8.2.5孔加工复合刀具8.2.6辅具8.3钻、扩、铰孔切削用量及钻削参数计算1018.4钻、扩、铰加工工艺8.4.1加工方法选择8.4.2钻、扩、铰加工工艺举例8.5孔的挤光和滚压9 镗削9.1镗床9.1.1镗床类型与技术参数9.1.2镗床附件9.2镗刀及其辅具9.2.1镗刀分类、装夹和调节方式9.2.2单刃镗刀9.2.3双刃镗刀9.2.4刀杆与镗杆9.2.5系列刀具9.3镗床的切削用量9.3.1卧式镗床的镗削用量与加工精度9.3.2金刚镗床的精密镗削用量9.3.3坐标镗床的切削用量9.4镗削加工工艺1029.4.1金刚镗床加工9.4.2坐标镗床加工10 拉削10.1 拉刀10.1.1常用拉刀设计10.1.2拉刀技术条件10.1.3圆拉刀设计10.1.4常用拉刀结构特点10.1.5挤压推刀10.2 拉削工艺10.2.1拉削切削液及其浇注方法10.2.2拉刀的刃磨工艺和方法11 磨削11.1 磨料与磨具11.1.1各种磨料的主要物理性能11.1.2磨具大致分类11.1.3普通磨料及其选择11.1.4超硬磨料磨具11.1.5涂覆磨具10311.2 磨床与磨床夹具11.3 普通磨削11.3.1外圆磨削11.3.2内圆磨削11.3.3平面磨削11.3.4无心磨削11.3.5砂轮平衡与修整11.3.6磨削液11.4 高效与精密磨削11.4.1高速磨削11.4.2高速重负荷磨削11.4.3低粗糙度磨削11.5 超硬磨料磨具磨削11.5.1金刚石砂轮磨削11.5.2立方氮化硼(CBN)砂轮磨削11.5.3超硬磨料砂轮修整11.6 砂带磨削11.6.1砂带磨削11.6.2砂带磨削工艺参数选择10411.6.3砂带磨削实例11.7 珩磨11.7.1珩磨油石的选择11.7.2珩磨工艺参数与珩磨液11.7.3特种珩磨工艺11.8 游离磨粒加工11.8.1研磨11.8.2抛光12 精密加工及超精密加工12.1 精密加工和超精密加工的范畴12.2 金刚石刀具的超精密切削12.3 超精密磨料加工12.3.1精密磨削和超精密磨削12.3.2精密和超精密砂带磨削12.3.3精密和超精密研磨12.3.4精密和超精密抛光13 特种加工13.1 概述13.2 电火花穿孔、成形加工10513.2.1电火花穿孔、成形加工机床13.2.2电火花加工的工具电极和工作液系统13.3 电火花切割加工13.3.1电火花线切割机床13.3.2常用电火花线切割电源13.3.3若干因素对线切割工艺效果的影响13.4 电化学加工13.4.1电化学加工原理及设备组成13.4.2电解加工13.4.3电化学抛光13.4.4刷镀13.5 超声加工13.6 高能束加工13.6.1激光加工13.6.2电子束加工13.6.3离子束加工13.7 复合加工13.7.1电解-电火花复合加工13.7.2电解磨削与电解研磨10613.7.3超声电解复合加工13.8 其他特种加工13.8.1水喷射切割13.8.2磨料喷射加工13.8.3挤压珩磨加工14 螺纹加工14.1 车螺纹14.1.1专用螺纹车床14.1.2螺纹车刀14.1.3工艺参数的选择与计算14.1.4旋风铣削螺纹14.2 丝锥攻螺纹14.2.1普通螺纹丝锥攻螺纹14.2.2螺母丝锥攻螺母螺纹14.2.3锥形丝锥攻锥螺纹14.2.4挤压丝锥挤压螺纹14.3 板牙套螺纹14.3.1板牙及辅具14.3.2圆板牙机动套螺纹的切削速度10714.4 螺纹切头切螺纹14.4.1圆梳刀外螺纹切头切螺纹14.4.2径向平梳刀外螺纹切头切螺纹14.4.3切向平梳刀外螺纹切头切螺纹14.4.4径向平梳刀内螺纹切头切螺纹14.5 铣螺纹14.5.1螺纹铣刀14.5.2铣螺纹工艺参数的选择与计算14.6 滚压螺纹14.6.1滚压螺纹对坯件的要求14.6.2滚压工具耐用度14.6.3螺纹滚压头滚压螺纹14.6.4滚丝轮滚压螺纹14.6.5搓丝板滚压螺纹14.7 磨螺纹14.7.1砂轮14.7.2工艺参数的选择与计算14.7.3切削液的选择15 齿轮加工10815.1 概述15.2 成形法铣圆柱齿轮15.3 滚齿15.3.1滚刀15.3.2滚齿工艺15.3.3硬齿面滚齿15.4 插齿15.4.1插齿原理15.4.2插齿机15.4.3插齿刀15.4.4插齿工艺15.5 剃齿15.5.1剃齿原理和方法15.5.2剃齿机15.5.3剃齿刀15.5.4剃齿夹具15.5.5剃齿工艺15.5.6小啮合角剃齿15.6 磨齿10915.6.1磨齿夹具15.6.2砂轮的选择和修形15.6.3磨齿工艺15.7 珩齿15.7.1珩齿机15.7.2珩齿轮15.7.3珩齿工艺15.8 蜗轮和蜗杆加工15.8.1蜗杆加工15.8.2蜗轮加工15.8.3新型蜗杆副加工15.9 直齿锥齿轮加工15.9.1 成型齿轮铣刀铣齿法15.9.2 刨齿15.9.3 双刀盘滚切法铣齿15.10 弧齿锥齿轮加工15.10.1常用弧齿锥齿轮切齿机、检验机、研齿机、磨齿机15.10.2弧齿锥齿轮铣刀15.10.3机床调整计算11015.10.4弧齿锥齿轮EPG检验及推荐值15.10.5研齿15.10.6 锥齿轮切齿机床常用数表15.11 长幅外摆线锥齿轮加工15.11.1 切齿机床、滚动检验机和研齿机型号与主要技术参数15.11.2 切齿刀具15.11.3 长幅外摆线锥齿轮有关参数计算16 花键加工16.1概述16.1.1花键的加工方法16.1.2花键各种加工方法的技术经济性比较16.2花键轴的成形铣削加工16.2.1刀具及其刃磨16.2.2工艺参数的选择和计算16.2.3高效成形铣削和精铣16.3花键轴的展成加工16.3.1展成加工机床及其附件16.3.2花键滚刀16.3.3工艺参数的选择及计算11116.3.4滚削加工举例16.3.5花键轴的插削加工16.4花键轴的磨削加工16.4.1花键轴磨床16.4.2砂轮16.4.3工艺参数的选择和计算16.5花键轴的无屑加工16.6花键孔的加工16.6.1用插齿刀加工渐开线花键孔16.6.2用插齿刀加工矩形花键孔17 难加工材料的切削加工17.1难切削金属材料的切削加工17.1.1概述17.1.2高锰钢的切削加工17.1.3高强度钢的切削加工特点17.1.4不锈钢的切削加工17.1.5高温合金的切削加工17.1.6钛合金的切削加工17.1.7难熔金属及其合金的切削加工11217.1.8喷涂(焊)材料的切削加工17.2难加工非金属硬脆材料的加工17.2.1难加工非金属硬脆材料的性能及其加工特点17.2.2硬脆非金属材料的主要加工方法18 柔性自动化加工18.1柔性自动化加工方法及其系统18.2柔性自动化加工设备18.2.1数控机床技术参数18.2.2加工中心技术性能参数18.2.3柔性制造单元技术性能参数18.2.4数控机床附件18.2.5托板18.3柔性自动化加工系统的工夹具系统18.3.1T SG82工具系统18.3.2各类数控刀柄的柄部18.3.3夹具系统113。
机械加工工艺师手册.d

机械加工工艺师手册2篇机械加工工艺师手册(一)第一章:机械加工概述机械加工是指利用机械设备对零件进行切削、磨削和其他加工方法,使其达到特定的尺寸、形状和表面质量要求的工艺过程。
在制造业中,机械加工是非常重要的一环,它直接影响着产品的质量和性能。
1.1 机械加工分类机械加工可以根据工艺过程的不同进行分类,常见的机械加工包括车削、铣削、钻削、磨削、镗削、拉削等等。
这些加工方法各有特点,适用于不同类型的工件和加工要求。
1.2 机械加工设备机械加工设备是进行机械加工的工具,常见的设备有数控机床、立式加工中心、龙门加工中心、磨床、车床等等。
这些设备通过控制系统精确控制刀具或工件的运动,实现对工件的加工。
1.3 机械加工工艺流程机械加工过程需要按照特定的工艺流程进行,一般包括六个步骤:加工准备、装夹定位、工艺参数确定、切削加工、设备参数调整和工件检验。
每个步骤的操作都需要严格控制,以确保产品的质量和精度。
第二章:机械加工工艺2.1 切削速度和进给量切削速度和进给量是机械加工中的重要参数,它们直接影响加工表面质量、加工效率和刀具的寿命。
选择适当的切削速度和进给量是提高加工效果的关键。
2.2 刀具选择和刃磨刀具是机械加工中必不可少的工具,不同的切削工艺需要选择不同的刀具。
刀具的选择要考虑加工材料的硬度、刀具材料的耐磨性和刃磨工艺等因素。
刃磨是保证刀具切削性能的重要工艺。
2.3 加工参数的确定在机械加工过程中,加工参数的确定非常重要。
加工参数包括切削速度、进给量、切削液的使用和切削力的控制等。
通过合理的参数选择和调整,可以提高加工效率和产品质量。
机械加工工艺师手册(二)第三章:机械加工工艺常见问题与解决方法3.1 表面加工粗糙度不达标表面加工粗糙度是评价加工质量的重要指标之一。
若表面加工粗糙度不达标,可能是切削速度过快或进给量过大,也可能是刀具磨损导致切削效果不佳。
解决方法包括降低切削速度、减小进给量和更换刀具等。
机械工程师的机械加工工艺技术手册
机械工程师的机械加工工艺技术手册简介机械加工工艺技术,是机械工程领域中一个既基础又重要的领域。
作为机械工程师必备技能之一,掌握机械加工工艺技术将决定产品质量和生产效率的高低。
本手册将针对机械加工工艺技术进行详细的介绍和说明。
第一章:加工工艺方案的设计1.1 设计产品的加工方案机械工程师需要在设计产品的同时,考虑到加工方案的设计。
这就需要针对产品提出合理的加工方案,包括机床的选择、切削刀具、夹具和加工工艺路线等。
1.2 工艺流程的设计完整的加工工艺流程是确保产品生产质量的必要条件。
因此,机械工程师需要根据产品特点和工艺要求,设计出完整且高效的工艺流程,并通过实际操作和数据分析进行不断优化。
第二章:机床的选择和使用2.1 机床类型及其特点机床是机械加工工艺的核心设备,机械工程师需要掌握不同类型机床的特点以及适用范围。
常见类型包括车床、铣床、钻床、磨床、刨床等。
2.2 机床参数的选择和调整机床参数的选择和调整对于机械加工的成败至关重要。
机械工程师需要根据具体产品加工要求,合理选择和调整机床参数,如进给速度、切削速度、主轴转速等。
第三章:切削刀具选择和使用3.1 切削刀具的种类和特点切削刀具是机械加工重要的加工工具之一,包括铣刀、车刀、钻头等。
机械工程师需要掌握不同切削刀具的特点,如材质、刀具形状、齿数等。
3.2 切削参数的选择和调整切削参数的选择和调整直接影响物料加工的结果和精度,因此机械工程师需要根据物料的性质和刀具的特点,合理选择和调整切削参数,如切削深度、切削速度、进给量等。
第四章:夹具和装夹4.1 夹具的种类和作用夹具是机械加工中常用的固定工件的装置,具有固定、定位、支撑和保护作用。
机械工程师需要了解不同类型夹具的作用和适用范围。
4.2 夹具的选择和使用夹具的选择和使用对机械加工的质量和效率都有很大的影响。
机械工程师需要根据具体产品的要求选择合适的夹具,确保加工精度和效率。
第五章:加工过程中的质量控制5.1 动态质量控制加工过程中的动态质量控制是确保产品质量的关键环节,它可以及时发现和纠正加工中的偏差,避免加工过程中的影响产品质量的缺陷。
机械加工工艺手册
• 机械加工质量问题的解决途径主要包括工艺改进、设备更新、材料优化等。 • 工艺改进:通过调整切削参数、选用合适的刀具和材料等方式提高加工质量 • 设备更新:通过更换精度高、性能好的设备,提高加工质量 • 材料优化:通过选用合适的材料、控制材料杂质等方式提高材料性能
性能、化学性能等。
机械加工材料的选择应 根据加工对象、加工要 求和加工条件进行。
• 金属材料:包括钢、铸铁、铝、 铜等及其合金 • 非金属材料:包括塑料、橡胶、 木材、陶瓷等 • 复合材料:包括碳纤维、玻璃纤 维、陶瓷纤维等增强复合材料
• 力学性能:包括强度、硬度、韧 性等方面的要求 • 物理性能:包括密度、导热性、 导电性等方面的要求 • 化学性能:包括耐腐蚀性、抗氧 化性等方面的要求
• 机械加工质量问题的分析与解决需要实践经验和理论知识的支持。 • 实践经验:通过实际操作、案例分析等方式积累的经验 • 理论知识:通过学习、培训等方式掌握的理论知识
05
机械加工安全与环保
机械加工过程中的安全注意事项
• 机械加工过程中的安全注意事项主要包括个人防护、设备安全、工作环境等方面的内容。 • 个人防护:包括佩戴安全帽、防护眼镜、耳塞等个人防护用品 • 设备安全:包括设备操作、设备检修、设备维护等方面的安全要求 • 工作环境:包括防火、防爆、防毒等方面的安全要求
机械加工质量的检测方法
• 机械加工质量的检测方法主要包括尺寸检测、形状检测、位置检测等。 • 尺寸检测:通过测量仪器、量具等设备检测工件的尺寸精度 • 形状检测:通过光学仪器、触针式仪器等设备检测工件的形状精度 • 位置检测:通过激光测距仪、光学显微镜等设备检测工件的位置精度
机械加工工艺手册
机械加工工艺手册机械加工工艺手册是一本应用书籍,是机械加工生产厂家必备的工具书之一,也是学生学习机械加工知识的重要资料。
它包括机械加工的各种工艺、加工设备和工具、加工方法及加工过程中的各种技巧和经验。
下面就内容进行详细介绍。
一、机械加工的基础知识机械加工的基础知识是机械加工工艺手册的重要部分。
它包括机械加工的概念、机械加工的发展历程、机械加工的基本原理、机床的分类和构造、加工工具的分类和使用方法等方面。
掌握这些基础知识对于从事机械加工工作的人员来说至关重要。
二、常见的机床和刀具机床和刀具是机械加工的核心设备,它们的质量和使用方法直接影响着机械加工的效率和质量。
机械加工工艺手册详细介绍了各种机床和刀具的类型、特点和应用范围,包括铣床、车床、钻床、切割机、磨削机、加工中心等。
此外,还介绍了各种刀具的分类和使用方法,如车刀、铣刀、钻头、刨头、锯片、磨石等,使读者对机床和刀具有更全面的了解。
机械加工的工艺流程是指将原材料加工成半成品或成品时所需的工序和加工顺序。
机械加工工艺手册详细介绍了各种加工流程的特点和应用范围,如铣削、车削、钻孔、切割、磨削、冷加工和热加工等,使读者了解机械加工的完整流程和工艺技巧,更好地掌握机械加工技术。
四、机械加工的操作技巧和注意事项机械加工过程中,操作技巧和注意事项极为重要。
一般来说,操作技巧的熟练程度越高,工作效率和加工质量越高。
机械加工工艺手册重点介绍了各种机床和刀具的操作技巧和注意事项,如正确测量、切削参数调整、工件装夹、进给速度控制、危险环境识别和处理等,使读者更好地应对机械加工中的各种问题和挑战。
五、机械加工的质量控制和故障处理机械加工的质量控制和故障处理是机械加工工艺手册的重点内容。
它包括了各种质量控制和故障处理的方法和技巧,如检验工具和设备的精度、检验工艺流程中的每个环节、识别加工质量问题,以及纠正加工过程中的各种故障等。
这些章节的内容可以帮助读者更好地掌握机械加工质量控制和故障处理的方法和技巧,提高工作效率和生产质量。
机械加工工艺与装配技术手册
机械加工工艺与装配技术手册一、简介机械加工工艺与装配技术手册是为了帮助工程师、技术人员以及制造商理解和应用机械加工和装配过程而编写的专业指南。
本手册将介绍机械加工的基本原理、工艺流程以及常见的装配技术,旨在提供实用的指导和技术支持。
二、机械加工工艺1. 切削工艺切削工艺是机械加工中最常用的一种方法。
它通过将切削工具与工件接触,通过旋转或线性运动,将工件上的材料逐渐剥离,从而达到所需的形状和尺寸。
在切削工艺中,常用的设备包括车床、铣床、磨床等。
这些设备通过控制切削刃具的移动、速度和切削参数来加工工件。
2. 成形工艺成形工艺是通过对金属材料进行塑性变形来加工工件。
通常使用冷加工或热加工方法进行成形。
在冷加工中,通常使用压力将材料通过模具成型。
热加工则涉及到加热材料以降低其硬度,然后进行塑性变形。
常见的成形工艺包括锻造、压铸和冲压等。
3. 焊接工艺焊接是将两个或多个工件通过加热或施加压力连接在一起的方法。
焊接工艺可以分为熔化焊接和压力焊接两类。
熔化焊接通过将工件加热到熔化温度并添加填充材料,使其融合在一起。
压力焊接则是通过施加压力将工件紧密连接在一起,而不需要添加填充材料。
焊接工艺广泛应用于制造业中,常见的方法包括电弧焊、气体保护焊、激光焊等。
三、装配技术1. 机械装配机械装配是将多个零部件组装成为一个完整的机械产品的过程。
在机械装配中,需要根据设计要求选择适当的工具和方法。
装配过程中要注意保持零部件的准确位置和合适的间隙,以确保机械产品的性能和稳定性。
机械装配可以使用手工装配、自动化装配和半自动化装配等方法。
2. 电气装配电气装配是将电子元件组装成为电路板或设备的过程。
在电气装配中,需要按照电路图和工艺要求进行布线、焊接和连接等操作。
为了确保电气装配的质量和可靠性,需要进行测试和调试。
电气装配工艺也在不断发展,如表面贴装技术(SMT)和无铅焊接等。
3. 精密装配精密装配是指对高精度、高要求的产品进行组装。