热处理工艺评定[2011]
08.0319热处理工艺评定管理规定

热处理工艺评定管理规定1主题内容和适用范围本标准规定了锅炉产品的热处理工艺评定的目标、职责、工作程序和资料的管理。
2 本文件适用于锅炉产品热处理工艺评定工作的管理。
3 术语3.1热处理工艺热处理过程中所采用的热处理方式和实施要求,包括热处理准备、热处理的材料、处理方式(正火、调质)、技术要求、操作要求等。
3.2热处理工艺评定热处理过程中是否达到产品设计要求性能和验证制定的热处理工艺指导书可行性。
4立项原则4.1须热处理的产品。
产品在投产前按相关标准的要求做相应的热处理工艺评定。
5职责5.1技术科会同检验定科热处理责任工程师负责评定项目立项及组织实施,收集试验、检验报告并完成热处理工艺评报告,并负责保管文件。
5.2生产科负责工艺评定生产任务的安排及协助。
5.3供应部门负责提供评定用原材料及辅料。
5.4检验科负责评定的主要检验工作,无损检测、试样的理化性能及金相检验并出具相应报告。
6工作程序评定工作程序可分为四个步骤:提出评定项目(立项);编制评定任务书及指导书;进行评定试验、编写评定报告。
热处理工艺评定管理规定6.1提出评定项目(立项)6.1.1当产品图样工艺性审查完成后,对照4.1-4.2立项原则,由热处理责任工程师提出新做的评定项目。
6.1.2热处理责任工程师负责编制热处理工艺评定任务书和热处理工艺指导书及热处理工艺评定流转卡。
6.2编制评定任务书及指导书评定任务书及指导书是实施热处理工艺评定试验工作的技术依据。
6.2.1评定任务书内容包括立项原因及热处理工艺评定编号;包括工艺评定物理性能、金相、试样形式和图样、材料牌号及规格、检验项目及数量、评定标准及完成日期等。
6.2.2评定指导书内容包括实施评定试验所必需的全部重要参数、附加重要参数和有关的非重要参数。
6.2.3评定流转卡内容包括评定试验原材料牌号及规格、试验工序及完成部门。
6.2.4评定任务书和指导书由热处理工艺人员编制、校对,由热处理责任工程师或工艺责任工程师审核。
解读47014-2011
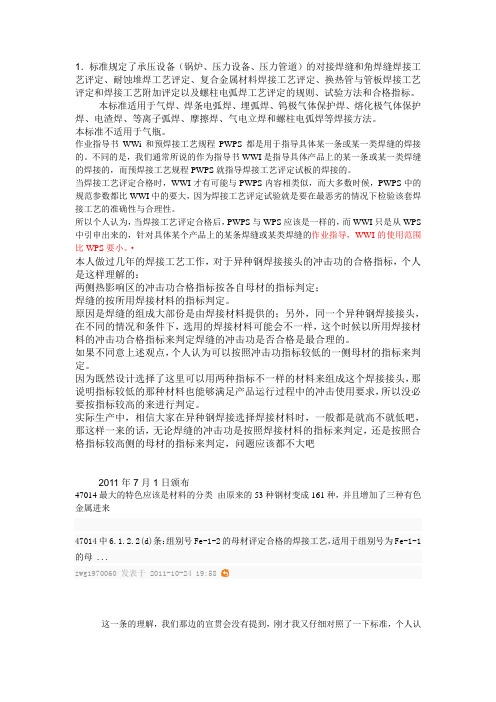
1.标准规定了承压设备(锅炉、压力设备、压力管道)的对接焊缝和角焊缝焊接工艺评定、耐蚀堆焊工艺评定、复合金属材料焊接工艺评定、换热管与管板焊接工艺评定和焊接工艺附加评定以及螺柱电弧焊工艺评定的规则、试验方法和合格指标。
本标准适用于气焊、焊条电弧焊、埋弧焊、钨极气体保护焊、熔化极气体保护焊、电渣焊、等离子弧焊、摩擦焊、气电立焊和螺柱电弧焊等焊接方法。
本标准不适用于气瓶。
作业指导书WWi和预焊接工艺规程PWPS都是用于指导具体某一条或某一类焊缝的焊接的。
不同的是,我们通常所说的作为指导书WWI是指导具体产品上的某一条或某一类焊缝的焊接的,而预焊接工艺规程PWPS就指导焊接工艺评定试板的焊接的。
当焊接工艺评定合格时,WWI才有可能与PWPS内容相类似,而大多数时候,PWPS中的规范参数都比WWI中的要大,因为焊接工艺评定试验就是要在最恶劣的情况下检验该套焊接工艺的准确性与合理性。
所以个人认为,当焊接工艺评定合格后,PWPS与WPS应该是一样的,而WWI只是从WPS 中引申出来的,针对具体某个产品上的某条焊缝或某类焊缝的作业指导,WWI的使用范围比WPS要小。
·本人做过几年的焊接工艺工作,对于异种钢焊接接头的冲击功的合格指标,个人是这样理解的:两侧热影响区的冲击功合格指标按各自母材的指标判定;焊缝的按所用焊接材料的指标判定。
原因是焊缝的组成大部份是由焊接材料提供的;另外,同一个异种钢焊接接头,在不同的情况和条件下,选用的焊接材料可能会不一样,这个时候以所用焊接材料的冲击功合格指标来判定焊缝的冲击功是否合格是最合理的。
如果不同意上述观点,个人认为可以按照冲击功指标较低的一侧母材的指标来判定。
因为既然设计选择了这里可以用两种指标不一样的材料来组成这个焊接接头,那说明指标较低的那种材料也能够满足产品运行过程中的冲击使用要求,所以没必要按指标较高的来进行判定。
实际生产中,相信大家在异种钢焊接选择焊接材料时,一般都是就高不就低吧,那这样一来的话,无论焊缝的冲击功是按照焊接材料的指标来判定,还是按照合格指标较高侧的母材的指标来判定,问题应该都不大吧2011年7月1日颁布47014最大的特色应该是材料的分类由原来的53种钢材变成161种,并且增加了三种有色金属进来47014中6.1.2.2(d)条:组别号Fe-1-2的母材评定合格的焊接工艺,适用于组别号为Fe-1-1的母 ...zwg1970060 发表于 2011-10-24 19:58这一条的理解,我们那边的宣贯会没有提到,刚才我又仔细对照了一下标准,个人认为是这么理解的:NB/T47014 6.1.2.2条d)款组别号为Fe-1-2的木材评定合格的焊接工艺适用于组别号为Fe-1-1的母材。
Q-ZZ 30021锻件热处理验收规范-2011(下发 版)

Q/ZZ锻件热处理验收规范中国重型汽车集团有限公司发布前 言本标准代替QZZ 30021—1996《锻件热处理验收规范》。
本标准与QZZ 30021—1996相比,主要变化如下:——标准的编排格式按GB/T 1.1—2009《标准化工作导则 第1 部分:标准的结构和编写》的规定 进行了调整;——对原标准中3.2条、3.3条进行了修订,并取消了原标准中5.3.2条;——删除原标准3.4条对等温退火工艺晶粒度检测,增加调质工艺;——对原标准3.5条增加了“如没有规定,一般锻件按取样部位处总脱碳层深度,每边应小于或等于有效厚度的1%”——对原标准中3.6条进行了修订,增加了“但当锻件尺寸不够取拉伸试样时,则应按强度与硬度值进行换算后,对该锻件在取拉伸试样部位进行硬度检测。
”——对原标准中5.3.3条进行了修订,取消金相组织半级的规定;——在新标准中增加了3.8条和3.9条对过热和过烧的规定;——原标准中规定了拉伸性能,在新标准中修订为力学性能,并增加了对冲击韧性的检验规定; ——新标准中增加了非调质钢的有关规定;——取消了原标准5.3.2中所列出的各种具体钢号;——因GB/T 13320-2007较91版作了很大的改动,故金相组织评级图参照GB/T 13320-2007; ——原标准中取样位置已经不适用,对力学性能的取样位置按DIN EN 10083-1:2006-10重新作了规定;——增加了5.4.1和5.4.2条款,对热处理硬度的测定位置进行了明确规定;——对金相试样的取样位置重新作了规定,取消原标准中对边部和心部金相组织的判定依据; ——取消了原标准5.5.3中对金相试样的硬度检测;——因GB6397已取消,所以本标准中取消了GB6397标准;——本次修订删除了原标准中的“斯达—斯太尔汽车”、“等温退火”等词语;—— 增加了GB/T 229冲击试验标准和DIN EN 10083-1:2006-10 力学性能取样标准;——对原标准的附录A进行了修订。
热处理的标准

热处理的标准热处理是一种通过加热和冷却金属材料来改变其物理和机械性能的工艺。
在工业生产中,热处理被广泛应用于各种金属制品的生产过程中。
热处理的标准对于保证产品质量和性能至关重要。
本文将介绍热处理的标准以及其在工业生产中的重要性。
首先,热处理的标准包括了对于加热温度、保温时间、冷却速率等工艺参数的规定。
这些参数的选择对于最终产品的性能具有决定性的影响。
例如,对于碳钢材料的热处理,通常需要将材料加热至临界温度以上,然后进行保温一定时间,最后以适当的速率冷却至室温。
这些参数的选择需要根据具体材料的成分和要求来确定,因此热处理的标准需要根据不同材料的特性进行具体规定。
其次,热处理的标准还包括了对于产品性能的要求。
不同的产品对于硬度、韧性、强度等性能有着不同的要求,因此热处理的标准需要明确规定产品在经过热处理后应具备的性能指标。
这些性能指标不仅需要符合国家标准,还需要满足具体行业的要求,例如航空航天、汽车制造、机械加工等行业对于产品性能有着严格的要求,因此热处理的标准需要根据不同行业的需求进行具体规定。
最后,热处理的标准对于产品质量和性能的保证至关重要。
通过严格执行热处理的标准,可以保证产品具有一致的性能和质量。
同时,热处理的标准也可以帮助企业降低生产成本,提高生产效率。
通过科学合理的热处理工艺,可以减少产品的废品率,提高产品的利用率,从而降低生产成本,提高企业的竞争力。
总之,热处理的标准对于保证产品质量和性能具有重要意义。
通过严格执行热处理的标准,可以确保产品具有一致的性能和质量,满足不同行业的需求。
因此,企业在生产过程中应严格遵守热处理的标准,确保产品质量,提高生产效率,降低生产成本,从而获得更好的经济效益。
滑轮热处理评定报告

西安力航电力石化设备有限公司叶轮热八、、处理报告报告编号:QA1007002编制日期:2011年3月20日叶轮热处理工艺评定报告:评定要求叶轮材料按照我公司标准WJ-QI-QA-003《材料规范》规定执行:化学成分:316LC:0.32 〜0.40 ; Si:0.17 〜0.37;Mn:0.5 〜0.8;P < 0.035;S < 0.035;Ni < 0.25;Cr < 0.25;Cu < 0.25。
机械性能:316L (T b>490Mpa (T s((T 0.2)>255Mpa S 5> 18% 40%硬度:316L HB 149 〜187热处理类型:正火+回火热处理设备:校准合格的设备名称规格型号编号校准报告井式电阻炉JB-1800 91-031 201000090439自动平衡记录仪XWG-101【K(0 〜1100)0】8J11230 201000090437-1数子温度指示调节仪XMG-101【K (0〜1300)0]0510 201000090438-1二:热处理曲线5G0D C±25回火四:评定记录机械性能316L其它试验:超声波检测:合格硬度:316L:195HB 197HB 198HB热处理工姓名:将达亮试验执行人:邹成贵试验编号:1007001 试验日期:2011-3-14五:评定结论试验根据热处理标准进行试件的准备和试验,对热处理工艺文件:《叶轮热处理工艺》WJ- QI-QA-012的内容进行评审,并经过实际验证。
认为其满足现场使用要求。
热处理设备评定报告有效加热区热电偶测试点位置如图示说明:红色代号①、②、③、④为上面蓝色代号⑤、⑥、⑦、⑧为下面黑色代号⑨为中间、井式电阻炉校准记录:热处理炉有效加热区检测记录900C热处理炉有效加热区检测记录600C测量结果的不确定度:U=18C, K=2测量结果的不确定度:U=0.8C, K=2 评定依据:确认部门质量管理部技术工艺部质检部确认人员2010-3-14 评审日期。
热处理工艺
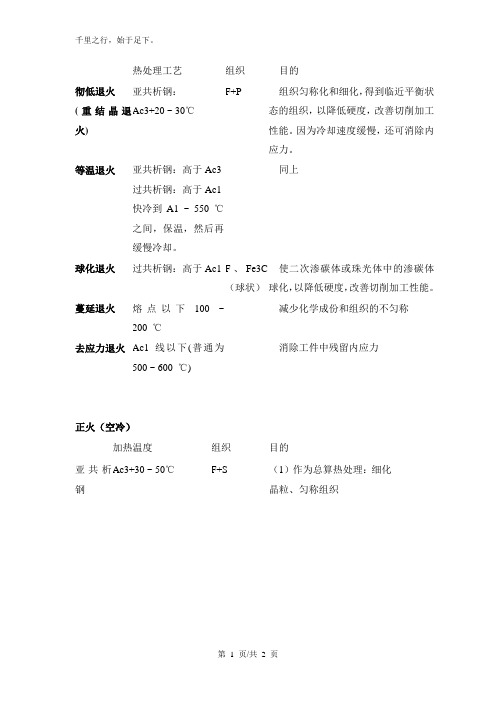
使二次渗碳体或珠光体中的渗碳体球化,以降低硬度,改善切削加工性能。
蔓延退火
熔点以下100~200℃
减少化学成份和组织的不匀称
去应力退火
Ac1线以下(普通为500~600℃)
消除工件中残留内应力
正火(空冷)
加热温度
组织
目的
亚共析钢
Ac3+30~50℃
F+S
(1)作为总算热处理:细化晶粒、匀称组织
(2)作为预先热处理:对结构较大的合金结构钢前,淬火或调质前常举行正火,消除魏氏组织和带状组织,并获得细小而匀称的组织。
(3)改善切削加工性能:调节硬度
过共析钢
Accm+30~50℃
S+ Fe3CⅡ
热处理工艺
组织
目的
彻低退火
(重结晶退火)
亚共析钢:Ac3+20 Nhomakorabea30℃F+P
组织匀称化和细化,得到临近平衡状态的组织,以降低硬度,改善切削加工性能。因为冷却速度缓慢,还可消除内应力。
等温退火
亚共析钢:高于Ac3
过共析钢:高于Ac1
快冷到A1~550℃之间,保温,然后再缓慢冷却。
同上
球化退火
过共析钢:高于Ac1
2a11热处理工艺

2A11热处理工艺主要包括淬火、回火和时效处理。
1. 淬火:将2A11铝合金加热至480-520℃,保温一定时间,然后迅速冷却至室温,使合金中的固溶体转变为过饱和固溶体。
淬火的目的是提高合金的硬度和强度,同时为后续的回火和时效处理做准备。
2. 回火:将淬火后的2A11铝合金加热至180-260℃,保温一定时间,然后冷却至室温。
回火的目的是消除淬火过程中产生的应力,提高合金的韧性和塑性。
回火温度的选择需要根据合金的性能要求和实际应用环境来确定。
3. 时效处理:将回火后的2A11铝合金在一定温度下保持一段时间,使其组织结构发生时效硬化。
时效处理的目的是进一步提高合金的硬度和强度,同时保持良好的韧性和塑性。
时效处理的温度和时间需要根据合金的性能要求和实际应用环境来确定。
在实际操作中,2A11热处理工艺还需要考虑以下几个因素:
1. 加热速度:加热速度对合金的组织和性能有很大影响。
一般来说,加热速度越快,淬火效果越好,但过高的加热速度可能导致合金内部产生过大的热应力,从而影响其性能。
2. 保温时间:保温时间对合金的淬火效果和回火效果有很大影响。
保温时间过短,淬火效果不佳;保温时间过长,可能导致合金过热,影响其性能。
3. 冷却速度:冷却速度对合金的淬火效果和组织有很大影响。
一般来说,冷却速度越快,淬火效果越好,但过高的冷却速度可能导致合金内部产生过大的热应力,从而影响其性能。
综上所述,2a11热处理工艺主要包括淬火、回火和时效处理。
热处理工艺评定记录表

热处理工艺评定记录热处理工艺评定记录(PQR)/QR13-02 序号:09002 公司名称工艺评定记录编号PQR-02 日期2009-2-23冲击试验其他试验试验类型硬度试验见硬度检查报告其他兹证明本报告所述均属正确,并且试验是根据热处理工艺要求进行试件的准备和试验的。
签字人日期2009-2-23石油机械设备制造有限公司硬度检查报告热处理工艺评定记录(PQR)QR13-02 序号:09005公司名称工艺评定记录编号PQR-05 日期2009-2-23冲击试验其他试验试验类型硬度试验见硬度检查报告其他兹证明本报告所述均属正确,并且试验是根据热处理工艺要求进行试件的准备和试验的。
签字人日期硬度检查报告热处理工艺评定记录(PQR)QR13-02 序号:0912公司名称工艺评定记录编号PQR-12 日期2009-2-23冲击试验其他试验试验类型硬度试验见硬度检查报告其他兹证明本报告所述均属正确,并且试验是根据热处理工艺要求进行试件的准备和试验的。
签字人日期2009-2-23硬度检查报告热处理工艺评定记录(PQR)QR13-02 序号:0913公司名称工艺评定记录编号PQR-13 日期2009-2-23冲击试验其他试验试验类型硬度试验见硬度检查报告其他兹证明本报告所述均属正确,并且试验是根据热处理工艺要求进行试件的准备和试验的。
签字人日期2009-2-23硬度检查报告热处理工艺评定记录(PQR)QR13-02 序号:0913公司名称工艺评定记录编号PQR-13 日期2009-2-23冲击试验其他试验试验类型硬度试验见硬度检查报告其他兹证明本报告所述均属正确,并且试验是根据热处理工艺要求进行试件的准备和试验的。
签字人日期2009-2-23硬度检查报告热处理工艺评定记录(PQR)/QR13-02 序号:0913公司名称工艺评定记录编号PQR-13 日期2009-2-23冲击试验其他试验试验类型硬度试验见硬度检查报告其他兹证明本报告所述均属正确,并且试验是根据热处理工艺要求进行试件的准备和试验的。
- 1、下载文档前请自行甄别文档内容的完整性,平台不提供额外的编辑、内容补充、找答案等附加服务。
- 2、"仅部分预览"的文档,不可在线预览部分如存在完整性等问题,可反馈申请退款(可完整预览的文档不适用该条件!)。
- 3、如文档侵犯您的权益,请联系客服反馈,我们会尽快为您处理(人工客服工作时间:9:00-18:30)。
文件编号:GL-WI-7.5.2-2011典型产品0Cr18Ni9和00Cr17Ni14Mo2钢管和022Cr22Ni5Mo3N
(S32205)双相钢不锈钢无缝管
热处理工艺评定方案
一.目的
验证热处理能力及过程的可靠性是否满足标准及客户要求。
二.依据
JB/T9197:2008《不锈钢和耐热钢热处理》
GL-WI-P09 《钢管热处理操作规程》
GB/T9452-2003《热处理炉有效加热区测定方法》
GB5310-2008 《高压锅炉用无缝钢管》
GB13296-2007 《锅炉热交换器用不锈钢无缝钢管》
GB9948-2006 《石油裂化用无缝钢管》
GB/T21833-2008《铁素体-奥氏体双相不锈钢无缝钢管》
三.热处理评价准则
1.热处理工艺评定要求
1.1评定的提出
A.新材料投入生产时,由热处理责任工程师根据工艺路线提出评价方案;
B.新工艺应用于生产时,由热处理责任工程师提出评定方案;
C.以前未涉及材料首次生产时,由热处理责任工程师提出评定方案;
D.产品质量理化性能出现较大波动时,由热处理工艺员提出评定方案;
E.其它原因(如炉子大修后)认为应该进行热处理工艺评定时,由相关人员提出评定方案;F.客户对工艺要求进行确认或评审时,由市场部门提出要求,技术部组织进行工艺评审。
2、评定准备
A.在接到评定通知后,热处理责任工程师准备评定的具体实施,并提出具体方案交工艺负责人及技术副总会签。
B.评定方案由公司生产技术副总(总工)审批。
评定的实施由热处理工序负责实施,相关单位配合。
C.在评定前,必须进行热处理过程确认,确保过程质量。
3、评定程序
A.评定应达到的要求
⑴新材料应用,应达到相应材料标准检测项目的最低要求;
⑵新工艺应用,要达到相应工艺方案的最低要求;
⑶要达到图纸或技术规范提最低要求,产品质量出现较大波动,要达到质量稳定可靠;
B.热处理工序按批准的工艺评定方案进行产品的热处理。
C.热处理工艺员对整个工艺评定过程进行详细质量跟踪。
D.试验检测
⑴过程无误后,进行理化等相关试验与检测。
⑵理化检测项目按热处理工艺评定方案进行,一般情况下至少要进行抗拉、屈服强度和延伸的性能测试。
⑶理化检测按技术要求的位置取样,并对取样位置的正确性负责,无取样位置规定时,按相应性能试验取样规定进行取样。
⑷在试样加工或制取过程中要注意不能改变试样的性能。
⑸按相应专业规定进行试验并出据试验报告。
4、评定要求
A.热处理责任工程师组织相关专业人员对评定数据进行综合判定。
评定结果达到要求后,经过半年以上生产后至少重复进行一次再评定,检测评定的重现性。
⑴当重复评定能够达到要求时,可视为评定有效。
⑵当评定结果与首次评定结果有差异时,要识别是正常的波动还是异常波动。
必要时可以进行第三次评定,以重复验证评定结果。
B.评定结果不满足评定要求时,应查找原因,重新制定评定方案并实施。
C.评定结果符合要求后,由热处理工艺员负责收集整理评定资料并保存;
D.相应的热处理工艺方案由生产技术副总(总工)批准后纳入热处理质量管理体系文件。
5.评审输出要求
A.确认连续式辊底炉设备的能力、设备的可靠性,主在控制参数有保温段的温度及温度波动(炉温均匀性和)范围以便指导生产;
B.确认工艺参数的可靠性,主要控制参数包括,热处理不同规格产品时保温段温度、热处理速度(产品在保温段经过的时间)以确保热处理的有效性。
C.确认人员是否符合热处理工段的要求,能否满足上岗要求。
D.确认热处理工艺作业指导书的可靠性,以保证该作业指导书能正常指导生产,确保产品符合标准和客户要求的各项工艺及物理性能的要求。
四.评价验证方法:
A.试样选择:公司产品φ21.3×1.24~φ273.0×6.0选用大中小规格规格常用材质TP304、TP316L、S31803和S32205作为评价参考对象,可选用1.5米的小样块随炉固溶热处理采用工艺设备的辊速(上限、下限)不同的辊速,对试块进行试验判定其理化性能进而确定工艺的可靠性,试验样选择应采取,低温高速一组,高温低速线组,其性能合格就能代表整个参数范围内。
设计试件选择:选择从大TP304Hφ273×6规格到
TP316L φ19×1的奥氏体钢和S31803双相不锈钢φ21.3×1.24 φ60.3×3.91 两规格的代表性产品进行热处理工艺可靠性确认,共涉及六个材质八个规格来确定热处理工艺。
B.评价前准备:
1.确认项目
(1)炉温均匀性及控制稳定性
炉温控制区分为预热区、加热区、保温区(3米),对保温段的炉温均匀性和稳定性进行确认,确保钢管产品在保温段符合要求;
(2)辊速控制:确认热处理辊底炉各项工艺参数,包括设备的烧嘴分布、炉温情况、测
温度点位置及相关数据,通调频电机调整炉辊转速对应的线速度;
(3)产品特性(性能)确认:
按GB13296和GB/T21833标准要求的检测项目及验收准则对以下项目:拉伸、压扁、扩口、晶间腐蚀、晶粒度进行验收。
2.对已编制的热处理(固溶)的工艺技术参数进行工艺有效验证,处理参数依据见附表1。
表1:钢管热处理的温度及加热速度
对热处理执行技术参数进行记录:热处理(固溶)的工艺参数原始记录和曲线。
在这个过程中要求保存以下数据作为热处理工艺评价的依据:在工艺评价记录中应有设备数据附页,热处理工艺记录及原始记录符合工艺要求。
五.样块的跟踪检测试验:
判定热处理结果是根据处理后产品的特性来实现的,我们需要对以下检测项目进行检验,确定性能是否满足.检测项目包括:抗拉强度Rm、屈服强度Rp0.2、延伸率A、扩口工艺性能、压扁工艺性能试验的要求。
检测热处理后金相的晶粒度恢复情况及晶间腐蚀是否满足要求。
在这个过程中要求保存以下数据作为热处理工艺评价的依据:试块的各检测项目的检测报告数据。
如拉伸、扩口、压扁和晶腐等。
编制:胡纯潮技术部审批:冯元2010年12月30日
文件编号:GL -WI-7.5.2-2011
典型产品1Cr19Ni9,0Cr18Ni9和00Cr17Ni14Mo2钢管和
022Cr22Ni5Mo3N (S32205)双相钢不锈钢无缝管热处理工艺评价记录 一. 热处理设备确认记录
主要设备:连续式辊底炉
设备名称:连续式辊底炉 17500*1120*400 设备状态:完好 相关设备:煤气发生炉(热源人工煤气)2m 3 设备状态:完好 二. 热处理工艺参数确认记录 A . 辊底炉参数:
生产设备: 炉膛:17500*1120*400 炉子温控系统采用5点控温,整台炉子共有3个热电偶测温,其中主要的3个测温点,其中炉膛中3#测温点测得的温度预热段1#为保温区的温度,保温段长为距离炉膛出口3.5米的距离,保温时间为钢管进入保温段到炉膛出口所经历的时间。
热源:采用清洁管道天燃气。
辊速:主电动机辊速表,调节辊速相应线速度的变化来实现热处理保温时间调整之目的。
连续式辊底炉如图2
B . 炉温均匀性确认
*按GB/T 9452-2003进行保温段炉温均匀性测定
图中符号:
L :保温段长 4.5 m ; H :保温段高0.45 m ; B :炉膛内宽度1.16 m ;
数字:1、2、3、4、5为测试热电偶位置。
当保温段为1052℃时测得各截面温度测试结果: 温度在标准温度1052℃度最低为1041℃最高为1061℃,偏差在规定的±15℃范围,保温段炉内温均匀性符合要求。
C.辊速确认:见线速度测量记录附页1。
结论:热处理设备经过确认符合工艺要求。
三.样块进行热处理的相关记录:
按公司设定的热处理(固溶)的工艺技术参数进行控制情况下,对以上8个规格产品理化性能指标准均达到要求。
热处理原始记录.
四. 人员确认:
热处理操作工和热处理负责人,均培训合格上岗,样件操作过程符合工艺作业指导书的要求,所以
人员确认符合要求。
结论:人员经过确认符合上岗要求。
五.设定参与评价的产品检验合格情况(按GB13296和GB/T21833标准检验):
α-相
α-相500倍
以上八个规格经检验全部合格。
六:物理性能试验报告、晶间腐蚀和晶粒度评级报告、冲击试验报告、热处理曲线。
热处理工艺评价结论:公司作业指导书各项工艺参数经试验确认均符合产品标准要求,技术部进行确
认后符合实际情况。
根据以上数据分析结果我们可以看出,我们之前设定的热处理工艺方案下生产出
来的钢管样块各项理化性能均达到较理想的要求,从而我们认为我们制定的热处理工艺符合生产实际
要求。
确认的热处理工艺参数对照表如下:
七.热处理的工艺再确认:随着生产的进行所涉及的钢种会更多规格也会更多,公司在应2012年2月底前进行热处理再确认,确保工艺更大满足要求。
技术部审批:冯元2011年2月28日
附表:转速与线速度对照表。