轴承座加工工艺设计过程和工序卡
毕业设计轴承座的加工工艺设计
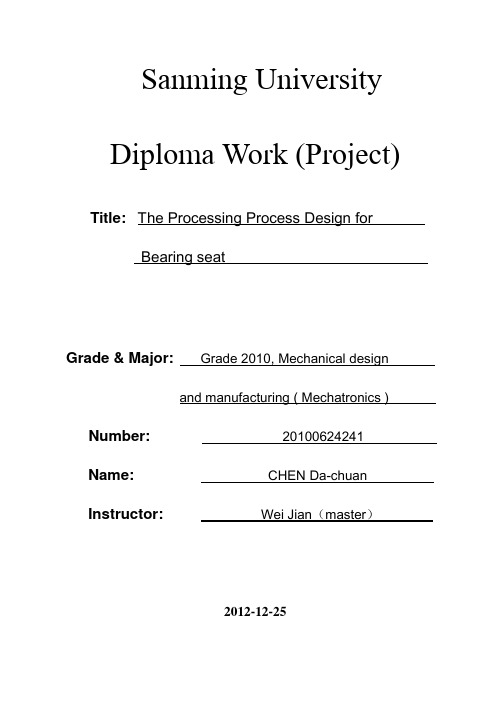
[Key words]Bearing seatFixtureProcess routeProcessing technology
1
1.1
随着机械制造业的发展和科学技术的进步,机械制造工艺的内涵和面貌下不断发生变化,近一二十年的技术进展主要表现在以下几方面:
(1)常规工艺的不断优化常规工艺的方向是实现高效化、精密化、强韧化、轻量化,以形成优质高效、低耗少污染的先进实用工艺为主要目标,同时实现工艺设备、辅助工艺、工艺材料、检测控制系统的成套工艺服务,使优化工艺易于为企业所采用。
在现今的发达国家中,毛坯生产的发展趋势表明,今后毛坯生产发展方向是力图在经济合理的范围内,使毛坯接近成品零件的尺寸形状。这可降低金属消耗量,减少加工余量和毛坯及铁屑的运输费用,这样就可提高生产率,降低零件的加工成本。对于毛坯生产,其特点主要是扩大新的先进的节约资源的工艺过程运用领域。采用电子技术管理切削加工过程,提高了对毛坯质量精度的要求。这将使其加工工艺得到必要的完善。
陶瓷结合剂的立方氮化硼砂轮、多孔砂轮和数控机床用的砂轮,具有寿命长、磨削性能稳定的特点。今后在磨削中将使用优质的加入合金成分的刚玉砂轮、用球形刚玉制造的砂轮、高纯度单晶刚砂轮、高强度耐热人造单晶刚石的复合材料砂轮。磨料的新型结合剂的开发将扩大高磨削的可能性。
轴承座加工工艺

1、轴承座的工艺分析及生产类型的确定1.1、轴承座的用途1零件的作用上紧定螺丝,以达到内圈周向、轴向固定的目的但因为内圈内孔是间隙配合,一般只用于轻载、无冲击的场合。
2零件的工艺分析该零件为轴承支架,安装轴承,形状一般,精度要求并不高,零件的主要技术要求分析如下:(参阅附图1)由零件图可知,零件的底座底面、端面、槽及轴承座的顶面有粗糙度要求,其余的表面精度要求并不高,也就是说其余的表面不需要加工,只需按照铸造时的精度即可。
底座底面的精度为Ra6.3,端面及内孔的精度要求为Ra12.5,槽的精度要求为Ra1.6,轴承座顶面精度要求为Ra3.2。
轴承座在工作时,静力平衡。
1.2、轴承座的技术要求:该轴承座的各项技术要求如下表所示:加工表面尺寸偏差(mm)公差及精度等级表面粗糙度(um) 形位公差(mm) 低端面400X160 IT10 6.3轴承座前后端面130 IT10 12.5Φ54上端面Φ54 IT10 12.5Φ120上端面φ250+0.03IT10 1.6Φ120上侧端面1700+0.16IT10 1.6 // 0.06 A 轴承座上端面50X160 IT10 3.2300x80的槽Φ140 IT10 12.5Φ120的半孔Φ1200+0.14 IT10 12.5Φ25的孔Φ25 IT10 12.5Φ26的孔Φ26 IT10 12.5Φ26孔上表面凸Φ54 IT10 12.5台40*40孔, 40*40 IT10 12.555*55孔55*55 IT10 12.51.3、审查轴承座的工艺性该轴承座结构简单,形状普通,属一般的底座类零件。
主要加工表面有Φ120上侧端面,要求其两个端面平行度满足0.06mm,其次就是;φ25和φ26孔通过专用的夹具和钻套能够保证其加工工艺要求。
该零件除主要加工表面外,其余的表面加工精度均较低,不需要高精度机床加工,通过铣削、钻床的粗加工就可以达到加工要求。
由此可见,该零件的加工工艺性较好。
机械加工工艺过程卡片-后轮轴承座
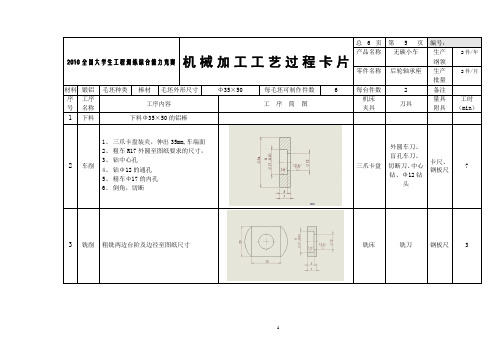
2010全国大学生工程训练综合能力竞赛机械加工工艺过程卡片总6页第5页编号:
产品名称无碳小车生产
纲领
2件/年零件名称后轮轴承座生产
批量
2件/月
材料锻铝毛坯种类棒材毛坯外形尺寸Φ35×50 每毛坯可制作件数 6 每台件数 2 备注
序号工序
名称
工序内容工序简图
机床
夹具
刀具
量具
附具
工时
(min)
1 下料下料Φ35×50的铝棒
2 车削1、三爪卡盘装夹,伸出35mm,车端面
2、粗车R17外圆至图纸要求的尺寸,
3、钻中心孔
4、钻Φ12的通孔
5、精车Φ17的内孔
6、倒角,切断
三爪卡盘
外圆车刀、
盲孔车刀、
切断刀、中心
钻、Φ12钻
头
卡尺、
钢板尺
7
3 铣削粗铣两边台阶及边径至图纸尺寸铣床铣刀钢板尺 3
4 钳工
1、 钻两个Φ3的孔
2、 去毛刺,终检
钳工台 电钻 钢板尺 1.5
编制(日期)
审核(日期)
标准化(日期) 会签(日期)
标记 处数 更改文件号
签字
日期
装 订 线
学校名称:。
轴承座加工工艺过程及工序卡

2
车床
车刀,镗刀,游标卡尺
200s
12
去毛刺
钳工台去毛刺
13
终检
尺寸公差的检测
设计(日期)
2011-12-17
审核(日期)
会签(日期)
标记
处数
更改文件
签字
日期
标记
处数
更改文件号
签字
日期
西安工业大学
机械加工工序卡片
生产类型
中批生产
工序号
01
零件名称
轴承座
零件号
零件重量
1.0kg
同时加工零件数
1
HB170~241
铸件
设备
夹具
辅助工具
名称
型号
专用
夹具
铣床
工
序
工
步
工步说明
刀
具
量
具
走刀
长度
(mm)
走刀
次数
切削
深度(mm)
进给量(mm/r)
主轴转速
(r/min)
切削
速度(mm/min)
基本工时min
07
1
夹轴承孔两侧面,以底面找正,铣底座的前后面及左右侧面,保证尺寸38mm和82mm
铣刀
游
标
卡
尺
8
机械设计制造极其自动化专业
机械加工工序卡片
生产类型
中批生产
工序号
06
零件名称
轴承座
零件号
零件重量
1.0kg
同时加工零件数
2
材料
毛坯
牌号
硬度
型式
重量
HT200
HB170~241
机械加工工艺过程卡片轴承座

钻床
丝锥,铰杆
10
镗
精镗Ø32+0.010
车间
卧式镗床
镗专用夹具,镗刀
11
最终检验
质管科
标记
处数
设计日期
审核日期
标准化日期
会签字日期
更改文件号
签字
日期
标记
处数
更改文件号
签字
检验
毛坯检验
质管科
4
铣
粗铣Ø60的端面
车间
卧式铣床
铣夹具,量具,铣刀
5
铣
精铣底座
车间
卧式铣床
铣夹具,量具,铣刀
6
铣
精铣上端面,精铣Ø60两端面
车间
卧式铣床
铣夹具,量具,铣刀
7
钻
钻Ø32孔,倒角1.5X45。
车间
钻床
钻夹具,立铣刀
8
钻
钻2XØ11孔和Ø11.9
车间
钻床
钻夹具
钳工
攻螺纹M14X1.5-6H
机械加工工艺过程卡片
产品型号
零(部)件图号
产品名称
轴承座
零(部)件名称
共()页
第()页
材料牌号
HT150
毛坯种类
普通灰铸铁
毛坯外形尺寸
130X45X65
每个毛坯可制件数
1
每台件数
备注
工序号
工序名称
工序内容
车间
工段
设备
工艺装备
工时定额/min
准终
单件
1
铸造
砂型铸造
外协
2
清砂
除去浇冒口、锋边及型砂
外协
3
机械加工工艺过程卡片轴承座.(DOC)

产品型号
零(部)件图号
产品名称
轴承座
零(部)件名称
共()页
第()页
材料牌号
HT150
毛坯种类
普通灰铸铁
毛坯外形尺寸
130X45X65
每个毛坯可制件数
1
每台件数
备注
工序号
工序名称
工序内容
车间
工段
设备
工艺装备
工时定额/min
准终
单件
1
铸造
砂型铸造
外协
2
清砂
除去浇冒口、锋边及型砂
外协
3
车间
钻床
丝锥,铰杆
10
镗
精镗Ø32+0.010
车间
卧式镗床
镗专用夹具,镗刀
11
最终检验
质管科
标记
处数
设计日期
审核日期
标准化日期
会签字日期
更改文件号
签字
日期
标记
处数
更改文件号
签字
(注:素材和资料部分来自网络,供参考。请预览后才下载,期待你的好评与关注!)
检验
毛坯检验
质管科
4
铣
粗铣Ø60的端面
车间
卧式铣床
铣夹具,量具,铣刀
5
铣
精铣底座
车间
卧式铣床
铣夹具,量具,铣刀
6
铣
精铣上端面,精铣Ø60两端面
车间
卧式铣床
铣夹具,量具,铣刀
7
钻
钻Ø32孔,倒角1.5X45。
车间
钻床
钻夹具,立铣刀
8
钻
钻2XØ11孔和Ø11.9
车间
轴承座加工工艺
精心整理1、轴承座的工艺分析及生产类型的确定1.1、轴承座的用途1零件的作用上紧定螺丝,以达到内圈周向、轴向固定的目的但因为内圈内孔是间隙配合,一般只用于轻载、无冲击的场合。
2零件的工艺分析该零件为轴承支架,安装轴承,形状一般,精度要求并不高,零件的主要技术要求分析如下:(参阅附图1)由零件图可知,零件的底座底面、端面、槽及轴承座的顶面有粗糙度要求,其余的表面精度要求并不高,也就是说其余的表面不需要加工,只需按照铸造时的精度即可。
底座底面的精度为Ra6.3,端面及内孔的精度要求为Ra12.5,槽的精度要求为Ra1.6,轴承座顶面精度要求为Ra3.2。
轴承座在工作时,静力平衡。
1.2、轴承座的技术要求:该轴承座的各项技术要求如下表所示:加工表面尺寸偏差(mm)公差及精度等级表面粗糙度(um)形位公差(mm)低端面400X160 IT10 6.3轴承座前后端面130 IT10 12.5 Φ54上端面Φ54 IT10 12.5 Φ120上端面φ250+0.03IT10 1.6Φ120上侧端面170+0.16IT10 1.6// 0.06 A轴承座上端面50X160 IT10 3.2 300x80的槽Φ140 IT10 12.5 Φ120的半孔Φ1200+0.14 IT10 12.5 Φ25的孔Φ25 IT10 12.5 Φ26的孔Φ26 IT10 12.5 Φ26孔上表Φ54 IT10 12.5面凸台40*40孔, 40*40 IT10 12.555*55孔55*55 IT10 12.51.3、审查轴承座的工艺性该轴承座结构简单,形状普通,属一般的底座类零件。
主要加工表面有Φ120上侧端面,要求其两个端面平行度满足0.06mm,其次就是;φ25和φ26孔通过专用的夹具和钻套能够保证其加工工艺要求。
该零件除主要加工表面外,其余的表面加工精度均较低,不需要高精度机床加工,通过铣削、钻床的粗加工就可以达到加工要求。
滚动轴承的机械加工工艺过程卡
滚动轴承的机械加工工艺过程卡
滚动轴承的机械加工工艺过程卡如下:
1. 材料准备:
- 选择合适的轴承材料,如钢材。
- 对材料进行切割,获得适当尺寸的坯料。
2. 热处理:
- 将坯料进行加热处理,以提高其硬度和强度。
- 进行淬火、回火等热处理工艺,以达到所需的材料性能。
3. 粗加工:
- 将坯料进行车削、铣削等粗加工工艺,将其加工成近似形状的轴承零件。
- 进行车削、铣削等工艺,以获得轴承内外圈的准确尺寸和形状。
4. 精加工:
- 对粗加工后的零件进行研磨、磨削等精加工工艺,以提高其表面质量和尺寸精度。
- 进行研磨、磨削等工艺,以获得轴承内外圈的光滑表
面和准确尺寸。
5. 组装:
- 将精加工后的轴承内外圈与滚动体、保持架等零件进
行组装。
- 使用适当的装配工艺和工具,将各个零件组装在一起,形成完整的轴承。
6. 检测:
- 对组装好的轴承进行检测,以确保其质量和性能符合
要求。
- 进行外观检查、尺寸检测、轴向游隙检测等工艺,以
验证轴承的质量和性能。
7. 表面处理:
- 对检测合格的轴承进行表面处理,如防锈处理、涂层
处理等。
- 进行防锈、涂层等工艺,以提高轴承的耐腐蚀性和使
用寿命。
8. 包装:
- 将经过表面处理的轴承进行包装,以保护其不受损坏。
- 使用适当的包装材料和方法,将轴承包装好,以便运输和存储。
以上是滚动轴承的机械加工工艺过程卡的详细描述,每个步骤都是为了确保轴承的质量和性能,以满足使用要求。
轴承座机械加工工艺过程卡
机械加工工艺过程卡产品型号及名称零件生产批量第 1 页零件名称轴承座零件图号共 1 页毛坯种类型材材料名称及型号棒料45#钢每件毛坯制坯数1 成品外形尺寸毛坯外形尺寸Φ44x43零件重量毛坯重量每台产品件数 1车间名称工序号工序名称工序内容单件工时机床名称夹具名称刀具名称及编号辅具名称及编号量具名称及编号1 下料下Φ44x43的棒料2 车端面车右端端面,切削深度3 CA6140 三爪卡盘硬质合金车刀游标卡尺3 车外圆粗通车外圆到Φ41,再精通车外圆到Φ40CA6140 三爪卡盘硬质合金车刀游标卡尺4 车端面车左端端面,切削深度3 CA6140 三爪卡盘硬质合金车刀游标卡尺5 车外圆粗车左端外圆到Φ32长22,再半精车外圆到Φ28长22CA6140 三爪卡盘硬质合金车刀游标卡尺6 车外圆以左端面为基准车右端外圆到Φ32长10,半精车外圆到Φ29长10,最后精车外圆到Φ28长10CA6140 三爪卡盘硬质合金车刀游标卡尺7 钻孔以中心轴为基准钻通孔Φ20CA6140 三爪卡盘高速钢钻头游标卡尺8 镗孔粗镗孔到Φ21.8,再精镗孔到Φ22CA6140 三爪卡盘高速钢镗刀游标卡尺9 车槽车通孔内两卡圈槽CA6140 三爪卡盘硬质合金车刀10 攻丝钻螺纹孔,攻丝高速钢螺母丝锥床丝锥刀游标卡尺11 铣铣端面,利用分度头120°铣三斜面万能立式铣床分度头高速钢立铣刀12 送检倒角,去毛刺,送检。
轴承工艺卡
设计轴承座零件的机械加工工艺规程邱凯云126040359工学122轴承座零件图其余25技术要求1 铸后时效处理2 未注倒角C13 材料:HT200零件的分析零件的作用轴承座是用于支撑轴类零件的,镗孔的目的是为了满足滚动轴承的外圈和轴承孔的配合要求,或者是滑动轴承外圆与轴承孔的配合,两个孔是用于固定轴承座的,单边固定是出于满足结构和安装位置的要求。
零件的工艺分析⑴φ30及φ8两孔都具有较高的精度要求,表面粗糙度Ra的值为1.6um,是加工的关键表面。
⑵轴承座上、下表面及前、后两端面的表面粗糙度Ra为3.2 um,是加工的重要表面。
轴承座的上表面有位置精度要求0.008,而且与轴承孔中心线有平行度要求0.003。
轴承座的前、后端面与轴承孔中心线垂直度要求为0.003,是重要的加工表面。
⑶φ13沉孔加工表面粗糙度要求较低。
⑷其余表面要求不高。
零件的生产类型生产类型及工艺特征轴承座为支承件,查附表2确定,轴承座属于轻型小批量生产零件毛坯的确定确定毛坯类型及其制造方法有附表5《常见毛坯类型》可知,材料为HT200,可确定毛坯类型为铸件。
估算毛坯的机械加工余量根据毛坯的最大轮廓尺寸(82)和加工表面的基本尺寸(42),查附表6《》可得出,轴承座上下表面机械加工余量为3.5,其余为3。
绘制毛坯简图,如图1定位基准选择 选择精基准经分析零件图可知,轴承座底面为高度方向基准,轴承座前端面为宽度方向基准。
考虑选择以加工的轴承座底面为精基准,保证底面与φ30孔中心线的距离为30。
该基准面积较大,工件的装夹稳定可靠,容易操作,夹具结构也比较简单。
选择粗基准图1 毛坯简图绘制步骤选择不加工的φ30孔外轮廓面为基准,能方便的加工出φ30孔(精基准),保证孔中心线与轴承座上端面平行度。
φ30孔外轮廓面的面积较大,无浇口、冒口飞边等缺陷,符合粗基准的要求。
拟定机械加工工艺路线选择加工方法根据加工表面的精度和表面粗糙要求,查附表可得内孔、平面的加工方案,见表2如下:表2 轴承座各面的加工方案拟定机械加工工艺路线,如表3表3 轴承座的机加工工艺方案加工余量及工序尺寸的确定确定轴承座底平面的加工余量及工序尺寸(1)轴承座底平面的加工过程如图2所示;粗铣底面精铣底面图2 轴承座底面加工过程图(2)根据工序尺寸和公差等级,查附表14《平面加工方案》得出粗铣、精铣底面的工序偏差,按入体原则标注,考虑到高度方向上以下底面为尺寸基准,并要保证中心线到地面的高度为30mm。
- 1、下载文档前请自行甄别文档内容的完整性,平台不提供额外的编辑、内容补充、找答案等附加服务。
- 2、"仅部分预览"的文档,不可在线预览部分如存在完整性等问题,可反馈申请退款(可完整预览的文档不适用该条件!)。
- 3、如文档侵犯您的权益,请联系客服反馈,我们会尽快为您处理(人工客服工作时间:9:00-18:30)。
工业大学机械加工工序卡片生产类型中批生产工序号01零件名称轴承座零件号零件重量 1.0kg 同时加工零件数 1材料毛坯牌号硬度型式重量HT200 HB170~241 铸件设备夹具和辅助工具名称型号工序工步工步说明刀具量具走刀长度(mm)走刀次数切削深度(mm)进给量(mm/n)主轴转速(r/min)切削速度(mm/min)基本工时011 铸造毛坯游标卡尺工业大学机械加工工序卡片生产类型中批生产工序号02零件名称轴承座零件号零件重量 1.0kg 同时加工零件数 1材料毛坯牌号硬度型式重量HT200 HB170~241 铸件设备夹具辅助工具名称型号工序工步工步说明刀具量具走刀长度(mm)走刀次数切削深度(mm)进给量(mm/r)主轴转速(r/min)切削速度(m/min)基本工时min02 121.铸件外非加工表面彻底清洗干净2.涂耐油漆工业大学机械加工工序卡片生产类型中批生产工序号03零件名称轴承座零件号零件重量 1.0kg 同时加工零件数 1材料毛坯牌号硬度型式重量HT200 HB170~241 铸件设备夹具和辅助工具名称型号专用夹具立式钻床Z535工序工步工步说明刀具量具走刀长度(mm)走刀次数切削深度(mm)进给量(mm/r)主轴转速(r/min)切削速度(m/min)基本工时min03 1 1.夹轴承孔两侧毛坯,2.铣轴承座底面,照顾尺寸30mm和表面粗糙度。
铣刀游标卡尺42 粗铣1精铣2粗铣2精铣10.14 235 92.3 0.15工业大学机械加工工序卡片生产类型中批生产工序号04零件名称轴承座零件号零件重量 1.0kg 同时加工零件数 1材料毛坯牌号硬度型式重量HT200 HB170~241 铸件设备夹具和辅助工具名称型号专用夹具钻床Z535工序工步工步说明刀具量具走刀长度(mm)走刀次数齿升量(mm)进给量(mm/z)主轴转速(r/min)切削速度(m/min)基本工时min04 121.钻Ø9的孔2.锪Ø13的沉头孔。
保证孔深8mm。
麻花钻锪钻游标卡尺22 2 1 630 16.5 0.09工学院机械设计制造极其自动化专业机械加工工序卡片生产类型中批生产工序号05零件名称轴承座零件号零件重量 1.0kg 同时加工零件数 1材料毛坯牌号硬度型式重量HT200 HB170~241 铸件设备夹具辅助工具名称型号专用夹具立式铣床X51工序工步工步说明刀具量具走刀长度(mm)走刀次数切削深度(mm)进给量(mm/z)主轴转速(r/min)切削速度(mm/min)基本工时min05 1 以已加工底面和沉头孔定位基准,在轴孔处压紧,铣主视图底座上平面及轴承孔左、右侧面44mm。
铣刀游标卡尺4 上平面2左右侧面2粗铣2精铣10.14 235 92.3 0.3 工学院机械设计制造极其自动化专业机械加工工序卡片生产类型中批生产工序号06零件名称轴承座零件号零件重量 1.0kg 同时加工零件数 2材料毛坯牌号硬度型式重量HT200 HB170~241 铸件设备夹具辅助工具名称型号专用夹具刨床B635工序工步工步说明刀具量具走刀长度(mm)走刀次数切削深度(mm)进给量(mm/z)主轴转速(r/min)切削速度(mm/min)基本工时min06 1刨1mm*1mm槽照顾底面厚度15mm。
刨刀游标卡尺38 2 1.5 0.35 工学院机械设计制造极其自动化专业机械加工工序卡片生产类型中批生产工序号07零件名称轴承座零件号零件重量 1.0kg 同时加工零件数 1材料毛坯牌号硬度型式重量HT200 HB170~241 铸件设备夹具辅助工具名称型号专用夹具铣床工序工步工步说明刀具量具走刀长度(mm)走刀次数切削深度(mm)进给量(mm/r)主轴转速(r/min)切削速度(mm/min)基本工时min07 1 夹轴承孔两侧面,以底面找正,铣底座的前后面及左右侧面,保证尺寸38mm和82mm铣刀游标卡尺8 前2后2左2右2粗铣2精铣10.14 235 92.3 0.3 工学院机械设计制造极其自动化专业机械加工工序卡片生产类型中批生产工序号08零件名称轴承座零件号零件名称轴承座零件号零件重量 1.0kg 同时加工零件数 1 材料毛坯牌号硬度型式重量HT200 HB170~241 铸件设备夹具辅助工具名称型号专用夹具钻床Z535工序工步工步说明刀具量具走刀长度(mm)走刀次数切削深度(mm)进给量(mm/r)主轴转速(r/min)切削速度(mm/min)基本工时min09 1 钻Ø6的油孔麻花钻游标卡尺15 1 0.25 630 16.5 0.2工学院机械设计制造极其自动化专业机械加工工序卡片生产类型中批生产工序号10零件名称轴承座零件号零件重量 1.0kg 同时加工零件数 1材料毛坯牌号硬度型式重量HT200 HB170~241 铸件设备夹具辅助工具名称型号专用夹具钻床Z535工序工步工步说明刀具量具走刀长度(mm)走刀次数切削深度(mm)进给量(mm/r)主轴转速(r/min)切削速度(mm/min)基本工时min10 1 钻Ø4的油孔,保证与Ø6的油孔相通。
麻花钻游标卡尺8 1 0.25 500 4工学院机械设计制造极其自动化专业机械加工工序卡片生产类型中批生产工序号11零件名称轴承座零件号零件重量 1.0kg 同时加工零件数 1材料毛坯牌号硬度型式重量HT200 HB170~241 铸件设备夹具辅助工具名称型号专用夹具车床CA64140工序工步工步说明刀具量具走刀长度(mm)走刀次数切削深度(mm)进给量(mm/r)主轴转速(r/min)切削速度(mm/min)基本工时min11 1 以底面及沉头孔定位,在未加工的圆柱表面夹紧。
采用弯板式专用夹具装夹工件,车Ø30mm、镗Ø35mm孔、倒角1×45°,保证Ø30mm中心至上平车刀,镗刀游标卡尺车:3镗:3粗2精0.5粗:0.3精:0.0.042500 87.9 1.2面距离15及Ø30mm的表面粗糙度0.8。
工学院机械设计制造极其自动化专业机械加工工序卡片生产类型中批生产工序号12零件名称轴承座零件号零件重量 1.0kg 同时加工零件数 1材料毛坯牌号硬度型式重量HT200 HB170~241 铸件设备夹具辅助工具名称型号专用夹具钳工台工序工步工步说明刀具量具走刀长度(mm)走刀次数切削深度(mm)进给量(mm/r)主轴转速(r/min)切削速度(mm/min)基本工时min12 1 去毛刺游标卡尺3工学院机械设计制造极其自动化专业机械加工工序卡片生产类型中批生产工序号13零件名称轴承座零件号零件重量 1.0kg 同时加工零件数 1材料毛坯牌号硬度型式重量HT200 HB170~241 铸件设备夹具辅助工具名称型号专用夹具钳工台工序工步工步说明刀具量具走刀长度(mm)走刀次数切削深度(mm)进给量(mm/r)主轴转速(r/min)切削速度(mm/min)基本工时min。