LOB改善(生产线平衡)
LOB(线体平衡率)知识讲解2016628

课程要求
-- 封闭的环境:关闭手机,或改为震动状态。
-- 开放的心态:虚心学习,充分讨论与分享。 -- 参与的心态:积极参与,充分讨论与分享。
-- 空杯的心态:请带空杯来,装点水回去。
没有成功的企业,只有时代的企业。只有适应时代发展,才能成就百年名企!
没有成功的企业,只有时代的企业。只有适应时代发展,才能成就百年名企!
27
精益生产的最终目标,就是拧干毛巾里的最后一滴水!
例:流程程序图
1 电视机投入及外观检查 2 取出厂编号标签并贴上 3 取塑料袋,将电视机套入 4 取衬套,套入电视机 5 遥控器投入及外观检查 6 取塑料袋,将遥控器套入 7 附件投入及外观检查
准备﹔ 通过时间观测﹐分析作业价值﹐发现问题和改善空间﹔ 形成标准﹐比较实际差异﹐找出问题﹔ ……
没有成功的企业,只有时代的企业。只有适应时代发展,才能成就百年名企!
24
精益生产的最终目标,就是拧干毛巾里的最后一滴水!
4.2 山积表
山积表的使用: 山积表:将各分解动作时间,以迭加式直方图表现的一种
100.0%
4
10
0
每10秒做完成一个 部件,设备无人化
1
10
5
10
1
该工序平均每10秒 可出一个成品
1
10
正确的计算方法:线体平衡率=线体平衡率=(各工序节拍之和)/(各工序中人或主设备平均作业时间的瓶颈时间×人或主设备数之和) ×100%;照这个公式计算,=(10+20+10+10+10)/(10*6)*100%=(60/60)*100%=100%;
没有成功的企业,只有时代的企业。只有适应时代发展,才能成就百年名企!
生产线平衡分析LOB技术

13
二﹑生产线平衡的常见概念
5.生产力
生产力 = 每人每小时生产台数
假设生产同一产品,
A线用60人,每小时产出420台,
生产力
=420台/60人
=
7台/小时/人.
表面看B线的产 能高于A线
B线用65人,每小时产出480台,
生产力 = 480台/65人 = 6.77台/小时/人.
11
二﹑生产线平衡的常见概念
4.标准产能和实际产能
标准产能 标准产能(H) =3600(S)/瓶颈时间(S) 标准产能(班)=投入时间/瓶颈时间(S)
实际产能 实际产能是可供时间內所产出的良品数 1)人均产能=实际产能/投入时间/人数 2)单机台产能=实际产能/投入时间/机台数
12
二﹑生产线平衡的常见概念
C.T与T.T的关系?
6
二﹑生产线平衡的常见概念
[例]某制品流水线计划年销售量为20000件,另 需生产备件2000件,废品率2%,两班制工作, 每班8小时,时间有效利用系数95%,求流水线 的节拍。(年生产天数为:254天)
[解]
年生产天数
T效 = 254×8×2×60×95% = 231648 分钟 Q = (20000+2000) / (1-2%) = 22449 件
5
二﹑生产线平衡的常见概念
1.节拍.
指生产线上连续出产两件相同制品的时间间隔.它
决定了生产线的生产能力、生产速度和效率.它反映的
是客户的需求。
如何确定节拍?
节拍= 有效工作时间 1.依据产能需要.
产出数量
2.依据产线作业模式.
例:每小时产出400台,则节拍为:
精益生产系列(生产线平衡改善LOB,TT,CT解析)48页
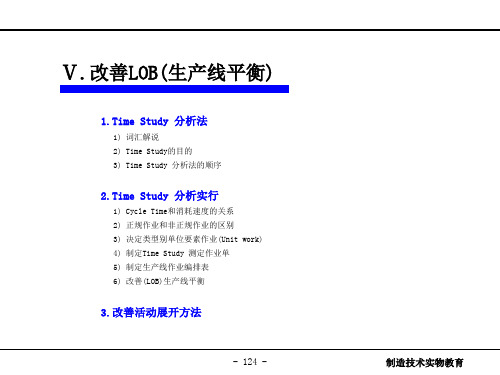
顺
① 实施Time Study.
序
-.经过现场负责人的同意后委托测定当天的工作时间 / 实际运转时间 /生产量 / 作业人员变动事项等正确数据.
-.测定者全员明确地测定开始点和终结点.
② 依单位作业填写Time Study测定用纸.
非运转 损失
能力运转 损失
时
间
运
能
转
力
率
运
转
率
运转损失
编排 损失 执行 损失
精密 作业 时间
成果Tact Time 能力Tact Time
Neck Time Cycle Time 精密时间
流失(消失) 能力
活
改善
动
范围
低效
工 作
纯粹的
- 129 -
制造技术实物教育
Ⅴ.改善LOB(生产线平衡)
3) Time Study 测定顺序
3.改善活动展开方法
- 124 -
制造技术实物教育
Ⅴ.改善LOB(生产线平衡)
1.Time Study 分析法
1)词汇解说
根据使用目的采用多种形式的使用Stop watch测定并分析作业者和设备作业量 处理时间方法.
种类
TACT TIME (T/T)
CYCLE TIME (C/T)
定义
制造一个单位数量的物品所需要的周期时间.
目的二.用做设定标准时间所需要资料.
通过作业者的观察, 用Stop Watch测定作业需要时间, 对所测定的作业时间评比顺序(Rating), 并用精密时间 算出结果值后, 考虑一定的盈余率, 用于设定标准时间.
LOB及现场工艺平衡培训

LOB及现场工艺平衡培训LOB(Line of Balance)及现场工艺平衡培训LOB(Line of Balance)是一种项目管理工具,旨在帮助团队在施工项目中实现工艺的平衡和优化。
同时,现场工艺平衡也是一项关键的能力,可以确保项目的顺利进行和高效完成。
为了提升团队的LOB和现场工艺平衡能力,进行有针对性的培训是必要的。
首先,在LOB的培训中,团队成员需要了解LOB的基本概念和原理。
LOB是通过绘制一条时间轴,将施工项目的关键工序和工作包进行分析和安排。
通过LOB图,团队可以一目了然地看到不同工序的时序关系,并进行优化方案的制定。
因此,在培训中,应该重点介绍LOB图的绘制方法和分析技巧,使团队成员能够准确把握工艺的平衡和优化。
其次,在现场工艺平衡的培训中,团队成员需要学习如何进行现场工序的调度和协调。
现场工艺平衡是指在施工现场,合理安排不同工艺的进行,以避免工序之间的瓶颈和资源浪费。
在培训中,应该介绍现场工艺平衡的原则和方法,如何通过调整工艺顺序、优化资源分配等,提高施工效率和质量。
同时,还应该加强团队成员的沟通和协作能力,以实现工艺的顺利进行和协调配合。
在培训的过程中,可以采取多种形式,如理论讲解、案例分析、实践演练等,以确保培训的效果。
此外,为了检验培训的成果和提高团队的实践能力,可以组织一些现场实训和模拟演练,让团队成员亲自操作和应用LOB和现场工艺平衡的技巧。
通过实际操作,团队成员可以更深入地理解和掌握这些方法,提高工作效率和协同配合能力。
总之,通过LOB及现场工艺平衡培训,可以提升团队的工艺管理能力和现场协调能力。
这对于提高项目施工效率、减少资源浪费和保证工程质量都具有重要意义。
因此,组织这样一场培训是非常必要的,可以为团队成员提供专业知识和实践技巧,以应对复杂的施工项目的挑战。
LOB(Line of Balance)及现场工艺平衡培训是现代项目管理的重要组成部分。
通过提供相关知识和实践技巧,这门培训有助于团队成员了解和应用工艺平衡的原则和方法,提高他们的项目管理能力和团队合作能力。
LOB效率改善实施步骤及要点

33.1 8.9
31.3
4 5 前盖 组件 6 7
邓华兰 颜访华
蒋兴元 付盼
11.9 16.3 13 10.1 9.5 5.5 6.4 3.9 24.8
14.7 15.7 11.8 6.5 7.9 3.9 10.1 4.3 23.9
17.3 15.8 11.7 6.1 5.4 4.3 8 5.2 20.8
20.0 10.0 0.0
8.9
16
1 2 3 4 5 6 7 8 9 10 11 12 13 14 15 16 17 18 19 20
改善前: 改善前: 平衡率=561.8/(47.1*20)*100% 平衡率=561.8/(47.1*20)*100% =59.6%
改善后: 改善后: 平衡率=543.1/(33.0*20)*100% 平衡率=543.1/(33.0*20)*100% =82.3%
步骤六、改善效果展示—平衡率
PDVD 7320改善前平衡度 50.0 40.0 47.1
50.0 40.0
31.3 32.533.030.3 30.430.929.4 29.6 28.8 28.529.226.9 28.5 29.328.1 30.0 25.7 24.8 21
PDVD 7320改善后平衡度
步骤六、改善效果展示——单位产能
100 90 80 70 60 50 40 30 20 10 0 100 80
单位产能 人均产能
4.0 改善前
5.0 改善后
步骤四、动作浪费的改善
针对在动素时间测量的过程中对发现的动作浪费进行 改善,简化作业员的动作难度和疲劳度,并制作改善 案例集。
浪费改善案例1___不懂作业技巧的浪费 不懂作业技巧的浪费
LOB改善(生产线平衡)

A作业者 B作业者 C作业者
目的二.用做设定标准时间所需要资料.
通过作业者的观察, 用Stop Watch测定作业需要时间, 对所测定的作业时间评比顺序(Rating), 并用精密时间 算出结果值后, 考虑一定的盈余率, 用于设定标准时间.
• 分割作业内容. - 将作业内容以分析单位进行分割. • 定义要素作业. - 设定过小或过大的要素作业,报会导致测定困难或分析问题的困难. • 决定测定方法. - 连续测定反复作业. - 发生非正规作业时随时将其作业名及发生理由记录在备考栏上. • 决定测定次数. - 作业不稳定时测定次数定为十次测定, 稳定时以五次为定.
编排损失
执行损失 综合损失
- 128 -
制造技术实务教育
Ⅴ.改善LOB(生产线平衡)
• 制造能力分析表
成果Tact Time 非运转 损失
运转损失
能力运转 损失 工 作 时 间
能力Tact Time
流失(消失) 能力
Neck Time
时 间 运 转 率 编排 损失 能 力 运 转 率 执行 损失 精密 作业 时间 Cycle Time
定义 制造一个单位数量的物品所需要的周期时间.
计算方法 工作时间÷生产数
在单位工艺中以一个循环(CYCLE)(单位)作为作业标准执 行作业所需要的实际测定时间.
Time Study实测
在全体工艺中作业时间(CYCLE TIME)最多的工艺的时间.
Time Study实测 1. 最少作业需要时间 2. C/T × Rating(%)
3.改善活动展开方法
- 124 -
制造技术实务教育
IE学堂12-生产线平衡(LOB)-Michael

33
3.生产线平衡实战技法
“给我一根杠杆,一个支点,我就能翘动地球” --阿基米德在《论平面图形的平衡》一书中最 早提出了杠杆原理. 生产线平衡的核心,就是----克服瓶颈! 是撬动生产力的支点.
IE学堂系列课程
34
3.生产线平衡实战技法
瓶颈的认识 瓶颈的分类
正规作业的内容
瓶颈改善的方法 瓶颈改善的手法
有效工作时间 节拍= 产出数量
1小时×3600秒/小时÷400 = 9秒/台
IE学堂系列课程 10
例:计算节拍
[例]某制品流水线计划年(254天)销售量为20000 件,另需生产备件1000件,废品率2%,两班制工作, 每班8小时,时间有效利用系数95%,求流水线的节 拍(分钟)。
年生产天数
[解 ]
IE学堂系列课程
16
1.5时间损失率
S r ti S r
100%
S —工作地数目 r —节拍
ti —工序i的作业时间
IE学堂系列课程
17
1.6生产力的概念
生产力=每人每小时生产台数
假设生产同一产品,
A线用60人,每小时产出420台,
生产力= 7.
B线用66人,每小时产出450台,
12
IE学堂系列课程
1.2瓶颈时间
瓶颈(Bottleneck)﹕ 产线作业工时最长的工位的标准工时称之为瓶 颈。更广义地讲,所谓瓶颈是指整个流程中制约产 出的各种因素。 瓶颈还有可能“漂移”,取决 于在特定时间段内生产的产品或 使用的人力和设备。
IE学堂系列课程
13
1.3单件标准时间
单件标准时间(Standard Time) : 一个作业员独自完成一个产品所有加工 作业所需的时间.(单位:分钟人)
LOB概念及公式

分解 No
/
标 准 作 业 表(改善后1 )
作业内容
12S-LS01 产品组装 LOB 提升
2.5人
原材料区 外检 组装CORE
打胶带
工程名 品名
平邑组装4线 12S-LS01
综合测试 终检
0.5人 打印
外检
组装
HT
2.28
5.2
N
1
2.5
C.T
2.28
2.08
TT
3
3
∑HT=15.96s
N=8人
T.T:在现有时间下 单个产品用时
解释:时间是固定的一天8个小时(加班时间越长 对公司越有利) ,客户需求是一定的 也就是我们所说 的计划产能。 n:用时人均(同等时间的情况下用人最小)
样板生产线概要-改善前1 (组装4线 12S-LS01)
1. 生产线名称 2. 生产线形态 3. 生产方式
平邑组装4线
生产实 绩
9000EA
8. 生产线效率现状
开动率 不良率
0%
0% √
√
9. 生产LEAD TIME 10. 作业方式
外协
采购
出货
合计
√ 立式作业
单技能工
加工
组装
√
坐式作业
√ 多技能工
客观检查
自主检查
11. 实际开动时间
460分
12. 工程概要 对4号线 12S-LS01 产能不变,人员计划减少2人。
2
◇
综合测试
1.45
综合测试仪
1
◇
终检
2.15
-
1
○
打印
0.47
印章
0.5
- 1、下载文档前请自行甄别文档内容的完整性,平台不提供额外的编辑、内容补充、找答案等附加服务。
- 2、"仅部分预览"的文档,不可在线预览部分如存在完整性等问题,可反馈申请退款(可完整预览的文档不适用该条件!)。
- 3、如文档侵犯您的权益,请联系客服反馈,我们会尽快为您处理(人工客服工作时间:9:00-18:30)。
终结(End point)
装订作业后把装订器放在原位,以后作业者的手分离于 装订器的瞬间是 “装订作业”要素动作的终结点.
- 138 -
制造技术实务教育
Ⅴ.改善LOB(生产线平衡)
• 两个人做一个工艺
开始(Start point)
两个人一组时第①个单位要素作业的开始点是 以两个人中先开工的人的开始点为基准.
开始(Start point)
一个人同时制造两个以上的制品时, 不管哪个制品以第一个
动作为做开始点的基准.
终结(End point)
一个人同时制造两个以上的制品时,不管哪个制品以最后一个 动作为做终结点的基准.
※ 一个人同时制造两个以上的作业时, 只看制品的变换过程而测定要素作业的话, 会测定错误 及耽误时间, 这个时候以作业者动作为基准测定的话, 容易分析出来.
• 分割作业内容. - 将作业内容以分析单位进行分割. • 定义要素作业. - 设定过小或过大的要素作业,报会导致测定困难或分析问题的困难. • 决定测定方法. - 连续测定反复作业. - 发生非正规作业时随时将其作业名及发生理由记录在备考栏上. • 决定测定次数. - 作业不稳定时测定次数定为十次测定, 稳定时以五次为定.
Ⅴ.改善LOB(生产线平衡)
1.Time Study 分析法
1) 词汇解说 2) Time Study的目的 3) Time Study 分析法的顺序
2.Time Study 分析实行
1) Cycle Time和消耗速度的关系 2) 正规作业和非正规作业的区别 3) 决定类型别单位要素作业(Unit work) 4) 制定Time Study 测定作业单 5) 制定生产线作业编排表 6) 改善(LOB)生产线平衡
非正规作业
正规作业
正规作业
• 现场实习 : 看生产线找一下正规作业和非正规作业.
- 137 -
制造技术实务教育
Ⅴ.改善LOB(生产线平衡)
3) 类型别单位要素作业(Unit work)的决定
• 区分单位要素作业时, 明确地区分开始点和终结点.
开始(Start point)
为了去拿装订器 , 作业者的视线看装订器的 瞬间是 “装订作业”要素动作的开始点.
※ VTR 摄像法(在现场难测定时能采用的测定法)
- 为了了解摄像对象的整个流程而进行摄像. - 摄像时间观测, 作业状况, 技巧性, 非常规作业, 单纯动作, 附属动作等. - 生产线的状况不佳时不要摄像.(对正常的状况下测定)
- 133 -
制造技术实务教育
Ⅴ.改善LOB(生产线平衡)
2.Time Study 分析事实
⑦ Door 投入
③ 门上贴 标签
⑥ 设定 叉车 ⑤ 取下门 保护纸
④ 空箱处理
- 134 -
制造技术实务教育
Ⅴ.改善LOB(生产线平衡)
□ 正规作业 (Regular work)
周期性地发生的有规则的作业, 即标准时间(S/T)的规定作业内容需要包括由作业条件, 环境, 方法等诱发的事项. • Spring插入部位太狭窄而不能一次插入, 要经过两三次才能插入. • Screw固定时, 固定物的洞和固定部位的洞不一致而犯错误.
② 依单位作业填写Time Study测定用纸.
-.填写对象名 / 型号名 / 分析日期 / 分析者. -.填写工艺号 / 工艺名 / 单位(要素)作业名 /线作业编排表.
-.填写工艺号 / 型号名 / 分析日期 / 分析者. -.工作时间 / 实际运转时间 / 生产成果数据. -.按工艺制造循环时间(最多,平均) / 精密时间的图象. -.计算生产线平衡效率.
□ 非正规作业 (Irregular work)
非周期性地发生的作业内容, 即没有标准时间(S/T)的规定作业内容. • 取出不良. • 取出空箱
• 替换或材料叉车(Trolley)
• 解开绑着材料的绳子 • 作业者不小心掉下材料
- 135 -
制造技术实务教育
Ⅴ.改善LOB(生产线平衡)
2) 正规作业和非正规作业的区分
定义 制造一个单位数量的物品所需要的周期时间.
计算方法 工作时间÷生产数
在单位工艺中以一个循环(CYCLE)(单位)作为作业标准执 行作业所需要的实际测定时间.
Time Study实测
在全体工艺中作业时间(CYCLE TIME)最多的工艺的时间.
Time Study实测 1. 最少作业需要时间 2. C/T × Rating(%)
精密时间
以标准作业方法完成给定的作业量所需要的最少时间.
- 125 -
制造技术实务教育
Ⅴ.改善LOB(生产线平衡)
• Cycle Time
作业 内容 A B 合计 测定次数 1 13.7 9.4 23.1 2 13.5 12.6 26.1 3 11.2 7.8 19.0 4 15.6 14.6 30.2 5 14.1 12.4 26.5 平均 13.6 11.4 26.0 Tact Time: 40秒
终结(End point)
两个人一组时单位要素作业的终结点是
以两个人中最后结束作业的人的终结点为基准.
※ 把同时作业的两个人各个测定的话, 犯循环时间变小的错误, 因此会出与实际能制造产品的能力不同的分析结果. - 139 -
制造技术实务教育
Ⅴ.改善LOB(生产线平衡)
• 一个人做两个以上的制品
2台 1台
活 动
改善 范围
(460分)
低效
精密时间
工 作
纯粹的
- 129 -
制造技术实务教育
Ⅴ.改善LOB(生产线平衡)
3) Time Study 测定顺序
• 实施Time Study. • 填写单位作业的Time Study测定用纸.
• 填写生产线作业编排表.
顺 序
① 实施Time Study.
-.经过现场负责人的同意后委托测定当天的工作时间 / 实际运转时间 /生产量 / 作业人员变动事项等正确数据. -.测定者全员明确地测定开始点和终结点.
目的三.包含于制造活动的各种损失分析.
分析作业量的执行(完成)能力与实际生产成果的差, 以用于掌握制造能力.
- 127 -
制造技术实务教育
Ⅴ.改善LOB(生产线平衡)
□ 制造活动的损失分析
• 词汇解说
区分 成果Tact Time 定义 在工作时间中制造一个单位数量的 物件所需要的总周期时间. 在实际运转中制造一个单位数量的 物件所需要的周期时间. 在工作时间中没有被用于运转而流失(消失)的时间的比率(生 产线停止 : 设备故障,交换模式 , 缺材料等) 在实际运转时间(作业时间)中未用于作业而流失(消失) 的时间比率(战时停止, 等待作业等) 非运转损失 + 能力运转损失 在工艺间由于工作量的不平衡而流失的时间比率 (发生等待或停滞等) 从作业者的努力程度, 熟练程度, 作业环境等方面的流失时间比率. 损失(流失时间比率)总和 合计 计算方法 工作时间÷生产数量
36秒 32秒 28秒 26秒 24秒 C/T 26秒 C/T 32秒 C/T 29秒
A作业者 B作业者 C作业者
目的二.用做设定标准时间所需要资料.
通过作业者的观察, 用Stop Watch测定作业需要时间, 对所测定的作业时间评比顺序(Rating), 并用精密时间 算出结果值后, 考虑一定的盈余率, 用于设定标准时间.
• Tact Time
- 工作时间: 460分
- 生产数量: 690台
- (460分×60秒)÷ 690台 = 40秒
24秒 20秒 20秒 18秒 16秒 16秒 14秒
26秒 22秒 20秒 21秒 19秒 18秒
Neck Time: 26秒 平均 C/T: 21秒 精密时间: 18秒
18秒
[工艺1] [工艺2] [工艺3] [工艺4] [工艺5] [工艺6]
③ 明确测定者全员的测定开始点和终结点.
• 明确测定开始点和终结点. • 明确测定时间的标示单位(一般以北/100秒为单位四舍五入).
④ 树立测定计划.
• 划分测定对象的工艺. • 掌握作业内容. - 详细地观测作业内容, 事先正确地掌握正规作业和异常发生事项.
- 131 -
制造技术实务教育
Ⅴ.改善LOB(生产线平衡)
„„„„„
[平均]
- 126 -
制造技术实务教育
Ⅴ.改善LOB(生产线平衡)
2)Time Study的目的 目的一. 作业者与设备的实际作业需要.
在制造物件的过程中, 制造物件实际能力受制造能力最低的 Neck工艺的左右, 因此为了找到这一Neck工艺与作业量 的不平衡程度, 需要用Stop Watch测定作业需要时间, 以用于分析不平衡程度对制造能力的影响.
能力Tact Time
非运转 损失 运转 损失 能力运转 损失 合计
实际运转时间÷生产数量
{(成果T/T-能力T/T) ÷成果T/T}×100(%) {(能力T/T-N/T) ÷成果T/T}×100(%) {(成果T/T-N/T) ÷成果T/T}×100(%) {(N/T - C/T) ÷成果T/T}×100(%) {(C/T-精密时间) ÷成果T/T}×100(%) 运转损失 + 编排损失 + 执行损失
3.改善活动展开方法
- 124 -
制造技术实务教育
Ⅴ.改善LOB(生产线平衡)
1.Time Study 分析法
1)词汇解说
根据使用目的采用多种形式的使用Stop watch测定并分析作业者和设备作业量 处理时间方法.
种类 TACT TIME (T/T) CYCLE TIME (C/T) NECK TIME
START
正规作业 非正规作业