现场IE改善案例分析--生产线平衡分析改善案例
IE工业工程改善案例

IE工业工程改善案例标题:利用IE工业工程改善案例提高生产效率和质量摘要:本文将介绍一个利用IE工业工程改善案例的实际应用,旨在提高生产效率和质量。
通过分析当前生产线上的问题,确定改进的目标和方向,并采取合适的IE工业工程工具和方法进行改进。
该案例将展示如何通过IE工业工程的技术手段,从而全面提高生产线的效率和质量。
引言:1.案例背景:制造企业生产线在生产过程中出现了一系列问题,导致生产效率低下、产品质量不稳定。
为了改善这一现状,企业决定运用IE工业工程进行系统的分析和改进。
2.目标分析:通过对生产线的观察和数据收集,确定改进的目标和方向。
例如,提高产品的生产效率、减少生产过程中的浪费、增加产品质量稳定性等。
3.分析工具的运用:根据目标分析的结果,应用IE工业工程中的各种分析工具,例如流程分析、时间研究、生产线平衡、人力资源规划等,识别瓶颈、浪费和改善机会。
4.改进方案的设计:基于分析工具的结果,制定改进方案。
例如,优化工作流程、改善生产线布局、优化人员配备等。
同时,结合人员培训和技术投入,提高员工的技能水平,以支持新工艺的实施。
5.实施和验证:将改进方案进行实施,并进行效果验证。
通过比较改进前后的数据和指标,评估改进方案的有效性。
同时,对员工的反馈进行收集和分析,以便继续改进和完善。
6.结果与总结:通过IE工业工程的改进,生产线的效率得到显著提升,产品质量也得到了稳定的提高。
通过系统的改进和优化,企业实现了生产成本的降低和利润的增加。
结论:本案例展示了通过IE工业工程改善的过程和效果。
通过对生产线进行系统的分析和优化,可以全面提升生产效率和质量。
因此,利用IE工业工程改善案例是企业实现可持续发展和竞争优势的有效途径之一。
生产线平衡分析与改善(最全面的IE分析-生产线平衡)

2023/12/24
8
二、流水生产线概述
1、 流水生产的基本概念 ● 流水线生产的分类
➢单人单产品式 ➢单产品固定式 ➢多产品固定式 ➢自由流水式 ➢连续传动流水式 ➢ 间歇传动流水式 ➢分组式
设某一产品从原料到成品,需经过A、B、C、D四个工序,其基本标 准工时(秒/个)及相关生产效率、良率、投入机台/人员数分别见表11: 可以求各工序每小时产量为: A工序每小时产量=(3600秒÷6.90)×90%×95%×1=470.87个 B工序每小时产量=(3600秒÷5.1)×80%×99.5%×1=470.87个 C工序每小时产量=(3600秒÷34.40)×100%×99.9%×2=209.09个 D工序每小时产量=(3600秒÷30.40)×100%×99.5%×2=238.8个 。
IE工业工程
-----生产线平衡
主讲:
课 程 内容
生产线平衡 一、生产线平衡的概述 二、流水生产线概述 三、生产线平衡的设计 四、生产线平衡的方法及改善原则 5、案例分析
2023/12/24
2
1.概念
一、生产线平衡的概述
生产线平衡即对生产的全部工序进行平均化,调整作业 负荷,以使各作业的时间尽可能相近的技术手段与方法,它 是生产流程设计及作业标准化中最重要的方法,是通过平衡 生产线使现场真正实施生产同步化,从而达到“一个流”的 理想。
2023/12/24
。
28
四、生产线平衡的改善方法与原则
2、平衡率改善的图示。
2023/12/24
29
四、生产线平衡的改善方法与原则
生产线平衡分析改善案例

生产线平衡分析改善案例引言生产线平衡是指在生产过程中,通过合理分配各个工序的工作量,使得各个工序的产能能够实现平衡,从而提高生产效率、降低成本,并确保产品质量。
本文将以一个实际案例为例,介绍生产线平衡分析和改善的具体过程。
案例背景某电子产品制造公司拥有一条生产线,生产一种电子产品,该产品的组装工序分为A、B、C、D四个子工序。
在目前的生产线上,工序A的生产能力远超其他三个工序,导致A工序成为瓶颈工序,无法满足后续工序的需求,从而影响了整个生产线的效率和产量。
因此,公司决定进行生产线平衡分析,并制定改善方案,以提高生产线的平衡度。
生产线平衡分析1. 数据收集首先,需要收集工序A、B、C、D的工作时间数据,包括每个工序的加工时间、准备时间和等待时间。
这些数据将作为分析的基础。
2. 流程图绘制根据数据收集到的各个工序的时间,并结合实际生产情况,可以绘制出生产线的流程图。
流程图可以清晰地展示每个工序的工作时间和流程顺序,有助于进一步分析。
3. 生产线平衡计算根据流程图,可以计算出每个工序的工作时间总和。
然后,根据目标产量,计算出每个工序的标准工作时间,即每个工序应该占用的时间比例。
通过比较实际工作时间和标准工作时间,可以评估生产线的平衡度。
4. 分析结果根据生产线平衡计算的结果,可以看出工序A的工作时间远超其他工序,导致生产线的不平衡。
这也解释了为什么A工序成为瓶颈工序。
改善方案1. 调整工序A的产能由于工序A是瓶颈工序,可以考虑通过增加设备或优化工艺,提高工序A的产能,以满足后续工序的需求。
这可以通过增加工序A的设备数量、提高工段效率或优化工艺流程等手段实现。
2. 优化其他工序除了调整工序A的产能外,还可以进一步优化其他工序的流程,减少每个工序的工作时间。
例如,可以通过流程改进、工艺优化、培训员工等方式,提高其他工序的效率,从而平衡整个生产线。
3. 调整生产计划根据生产线平衡分析的结果,可以对生产计划进行合理调整。
IE改善案例展示及学习
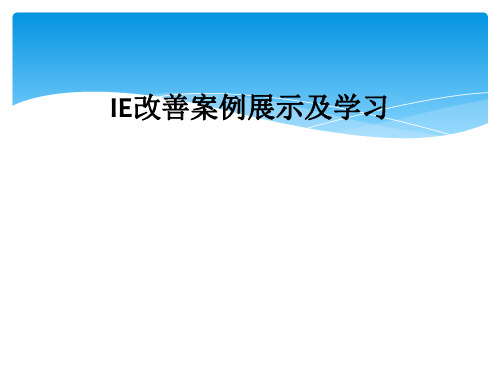
改善对象 改善日期
问题描述
商用公司370型号安装底脚工位员工没有工装,只能用手将底脚安装上,影响员工工作效率
商用公司 2012.07.28
改善措施
根据370底脚样式制作打底脚工装(如图所示),将此工装安在气枪上,把底脚安装好,即省了人力又减少操作时间10s
类别
改善前
改善后
对比照片
差异
员工打底脚时没有工装,用手操作,费时费力
--实验装置之间,而且,试验装 置在另一个房间,从而造成在这 两个房间之间频繁移动现象。
消除一点一滴的浪费是我们追求的目标
1.器皿的配置
作业量减少,操作更简单。简化
2.储水瓶
橡胶软管,橡胶栓种类减少,烧杯减少
3.过滤台(装置的配置台)
作业台减少,有效利用空间
消除一点一滴的浪费是我们追求的目标
改善方案
消除一点一滴的浪费是我们追求的目标
消除一点一滴的浪费是我们追求的目标
消除一点一滴的浪费是我们追求的目标
2.现场改善项目汇总
改善名称 改善部门 问题描述
刷漆工位接漆工装设计 IE办公室
改善类型 改善人
IE改善档案卡
质量改善 管伟琴
生产现场刷漆工位在刷漆过程中油漆经常滴落在压机底板上,影响产品质量
消除一点一滴的浪费是我们追求的目标
1)推进项目汇总表
3.物料模块化进度
项目
第一期 (商用公司)
已完成 7
推进中 0
第二期 (冷柜业务链)
3
4
第二期
(冰箱业务链)
2
5
澳洋
0
8
消除一点一滴的浪费是我们追求的目标
暂不实施 4 0 0 0
生产线平衡分析改善案例

齿条生产线平衡改善一、项目名称齿条生产线平衡改善二、项目目标1、粗校至滚铆达成一件流,无心磨至高频小批量流动2、生产线在制减少70%,周转车下线,采用传送带传输3、生产周期缩短80%4、生产线平衡率提升至80%,人员效率提升10%5、生产过程PPM下降50%三、项目组织一、项目名称、目的及内容:目的:1、生产线平衡分析改善。
通过成组分线后,选取代表型号进行生产线平衡分析,运用丰田生产方式结合瓶颈限制理论管理2、生产线换型分析改善。
通过对每天的产量确定固定的生产时间,确定换型可利用时间,以此设置标准工序超市以及流转批量。
3、标准化作业改善:通过对现场时间以及动作分析,并进行工位改善,编制标准化作业指导书。
将现场作业标准化,包括标准作业时间,标准在制,标准作业顺序。
4、传送方式改善:确定工序超市、流转批量后,进行流转方式改善。
二、项目组成员及分工:职姓名工作要求位组长负责进行分工,指导并监控整个过程按节点实施。
协调资源。
副组长负责整个项目的对策评价、实施监控。
组员负责进行齿条标准时间以及动作研究,以及动作、流转改善组员负责整个项目的对策拟定评价、实施。
组员负责进行齿条标准时间与动作分析,生产线平衡方案的制定。
编制标准化作业指导书。
组员布局图绘制,标准作业下发组员负责项目整个进行过程中的质量监控。
组员负责流转设施的自制,布局调整。
三、项目实施具体计划:序号阶段项目内容责任人起始完成时间时间1现状分析时间研究、动作分析、生产线平衡分析培训TOC简介改善专员2月4日2月16日2 生产线布局分析改善专员3 代表型号的测时、动作分解改善专员4 换型时间的调查改善专员5对策拟定根据时间分析,确定工序超市及工序间流转方式,及工序流转数量各分项小组(齿条线、齿轮轴线)2月8日3月15日6根据设备放置及工序节拍确定线体长度、速度、分段形式各分项小组(齿条线、齿轮轴线)7 标准化作业的编制改善专员8 改善过程中的质量监控9 对策评价改善对策的评价项目组成员3月16日3月23日10 对策实施流转线体制作2月8日3月15日现场试运行,质量部、技术部评价,项目成员、质管、技术3月25日2月25日11 项目验收现场项目验收质管部、技术部3月26日3月30日四、现状分析1、问题描述在2011年底整个机加车间分线分级,建立初步“流水线”作业方式后,加工过程中的各种浪费被显现出来,包括(1)节拍不平衡的效率损失(2)人员等待设备的浪费(3)在制品的浪费(4) 批量的不合格品及返工浪费(5) 搬运的浪费(6) 动作的浪费为此,生产部的带领下,机加车间开展了生产线平衡改善以及流转方式改善项目,运用丰田最基本最重要的IE时间测定与动作分析改善手法实施方法改善,通过流水线架的制作,实现按节拍的“单件流”生产。
现场改善及ie手法

THANK YOU
感谢聆听
时间研究
通过观察和测量作业人员完成某项任务所需的时间,制定合理的时 间标准。
作业标准化
将最优的作业方法和流程标准化,确保所有作业人员都能按照统一 的标准进行操作,提高生产效率和产品质量。
标准作业程序(SOP)制定
编写详细的标准作业程序,明确每一步骤的操作规范和要求,为作 业人员提供明确的指导。
生产线平衡与布局优化
运用各种计划和控制手段,确 保生产系统按照预定目标高效 运行。
IE手法在现场改善中的应用
流程优化
通过分析和改进工作流程,消除浪费、提高效率 。例如,减少不必要的操作步骤、简化工作流程 等。
设备改善
对生产设备进行改进和优化,提高设备效率和可 靠性。例如,采用自动化设备、改进设备维护计 划等。
物料管理
意义
现场改善是企业提高竞争力、实现可持续发展的重要手段之一。 通过现场改善,企业可以不断提高产品质量、降低生产成本、提 高生产效率、增强员工士气,从而赢得更多的市场份额和客户信 任。
现场改善的目标与原则
目标
现场改善的主要目标是提高生产效率、降低生 产成本、提高产品质量、增强员工士气等,以
实现企业的整体经营目标。
现场改善及IE手法
目
CONTENCT
录Hale Waihona Puke • 现场改善概述 • IE手法简介 • 现场改善的步骤与方法 • IE手法在现场改善中的具体应用 • 现场改善的实践案例 • 现场改善的挑战与对策
01
现场改善概述
现场改善的定义与意义
定义
现场改善是一种通过优化工作流程、提高工作效率和质量、降低 成本等方法,对生产现场进行持续改进的管理方法。
IE工业工程改善案例

生产实习目的1.通过实习了解工业工程领域的知识的应用背景。
2.深入了解企业中工业工程各种基本知识和原理的实际应用情况,巩固和加深对知识的理解,并加以整合,提高综合分析问题和解决问题的能力。
3.了解实习企业的生产管理的基本情况,发现存在的问题并提出解决方案。
4.掌握提案改善的一般流程及具体做法,在团队中(或个人)如何完成一个提案从提出到发表的全流程,为毕业后的实操奠定坚实基础。
5.学习企业管理人员,工程技术人员对企业的高度责任感,对工作尽职尽责,勇于改革,不断进取创新的奉献精神。
实习任务从数据统计得出的各类产品装配各工件装配 SPT ,及拉平衡状况分析表,及原因分析与改善建议。
装配部部门简介装配部,作为车模生产的最后一道工序,肩负着车模成品的组装和包装的全部生产过程。
装配部现有六条生产线和一条样办组装线。
常用的设备有:钻床,电批,手啤机,风批,烙铁,高周波,封口机等。
为了更好的完成各种的生产任务,装配部引入了精益生产工艺流程。
精益生产是目前工业界公认最佳的一种生产组织体系和方式。
通过合理的排拉,达到合理生产,提高效率和质量的目的。
例子一:DCP1/25 货车,按流程标准可分成:车身半品( 10人),车身组合(16人),内座组合(4人),车底组合(11人),成品组装(7人)和包装(9人)共六个小组(57人)来完成。
每个小组会有一次或以上的自检。
例子二:YTB002 1/42莱茵之星单层客车按流程标准可分成:内座组装(12人),车底组装(9人),车身组装(20人),成品包装(6人)共四个小组(47人)来完成,在其中也加入了多少的自检。
装配车间平面分布图装配生产线平衡改善过程 了解产品组装工艺 对U 型拉进行工时测定,得到统计数据 从统计数据分析U 型拉平衡状况 识别瓶颈工位,找出不平衡的原因 运用平衡改善法则(ECRS 法则)、动作经济原则等方法制定改善方案 将改善方案告知组长或装配主任,实施现场改善 改善效果分析总结平衡改善法则-ECRS 法则简介 符号 名称说明E 取消Eliminate 对于不合理、多余的动作或工位给予取消 C 合并Comebine 对于无法取消又是必要的,看是否可以合并以达到省时、简化的目的 R重排Rearrange 经过取消、合并后,可再根据“何人”“何时”“何处”三个提问后进行重排S简化Simplify 经过取消、合并、重排后的必要工位,应考虑能否采用最简单的方法或设备替代,以节省人力和时间以上ECRS法则,具体可通过下列图片来说明生产中如何运用改善:装配线平衡典型案例数据统计时间:2012/8/2-2012/8/3 U拉序号:U24、U25产品编号:53072(太空车)组装部分:成品和包装改善方案提出时间:2012/8/2改善方案实施时间:2012/8/3改善前各工位组装工艺工位序号 组装工艺SPT(秒)人数设备1 双花轴装进轮子*2,再用啤机压紧 9.5 1 手啤机2 再装入太同车下壳,再用压紧轮子*2 11 1 手啤机3 太空车上壳+太空车下壳组件 6 14 太空车身打螺丝13 1 电动批5 太空车上壳表面粘贴蓝色标签1 8 16 太空车上壳表面粘贴蓝色标签2 8 17 太空车上壳表面粘贴蓝色标签3 8 18 太空车半品装太空车雷达 6 1 抹布9 清洁位,车身抹洗面水 9 1 抹布10 检查位,擦拭车身 10 111 太空车成品装进胶袋 6 112 胶袋粘透明胶纸,并最终装进外箱8 1此款产品的装配线由U25、U24两个U型拉组成,工位分布如下图所示:平衡率=各工序的作业时间/(瓶颈工位时间*人数)=(9.5+11+6+13+8+8+8+6+9+10+6+8)/(13*12)=65.71%平衡损失率=1-平衡率=34.29%改善前装配线工位平衡图改善措施从统计数据分析这条装配线,可以发现瓶颈工位是工位4。
生产线平衡分析与改善最全面的IE分析生产线平衡
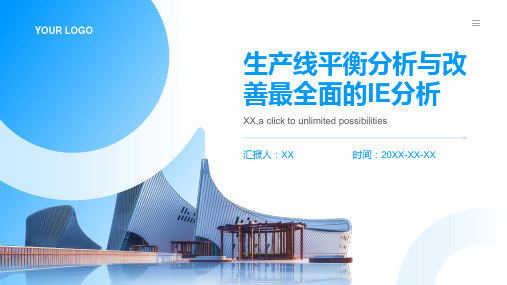
最全面的IE分 析生产线平衡 案例分析
PART 1
单击添加章节标题
P生A产R线T平2衡分析的概念和重要
性
生产线平衡分析的定义
定义:生产线平衡分析是指对生产线上的各个工 序进行平衡,使各工序的工作时间尽可能相近, 从而提高生产效率的过程。
目的:通过对生产线平衡进行分析,可以找出生 产过程中的瓶颈工序,优化生产流程,提高生产 效率,降低生产成本。
跨部门协作:加强各部门之间的沟通与协作,共同推进生产线平衡改善的实施和监控工作。
PIEA分R析T在5生产线平衡改善中的
Hale Waihona Puke 应用IE分析的基本概念和原则
IE分析的定义:工业工程分析, 旨在提高生产效率和降低生产成 本。
IE分析在生产线平衡改善中的应 用:通过分析生产线上的瓶颈、 浪费和不合理之处,提出改善方 案。
注意事项3:考虑人机配合 和作业节拍
注意事项1:分析前要明确 目标和范围
注意事项4:注意设备维护 和保养
PART 4
生产线平衡改善的策略和措施
生产线平衡改善的目标和原则
提高生产效率:通过优化生产线布局和作业分配,降低生产成本,提高产出效率。 降低不良品率:通过平衡生产线上的作业,减少生产过程中的波动和异常,降低不良品率。 提高员工满意度:通过合理分配工作量和减轻员工负担,提高员工的工作积极性和满意度。
生产线平衡分析的工具和技术
作业分析:确定每个作业步骤的时间和顺序,识别瓶颈和浪费。 工艺流程图:可视化生产线流程,找出潜在的改进点。 动作分析:研究工人操作,优化动作,提高效率。 生产计划与调度:合理安排生产计划,确保生产线的平衡。
生产线平衡分析的注意事项
注意事项2:充分了解生产 流程和工艺要求
- 1、下载文档前请自行甄别文档内容的完整性,平台不提供额外的编辑、内容补充、找答案等附加服务。
- 2、"仅部分预览"的文档,不可在线预览部分如存在完整性等问题,可反馈申请退款(可完整预览的文档不适用该条件!)。
- 3、如文档侵犯您的权益,请联系客服反馈,我们会尽快为您处理(人工客服工作时间:9:00-18:30)。
生产线平衡定义
对生产的全部工序进行均衡,调整作业 负荷和工作方式,消除工序不平衡和工 时浪费,实现“一个流”。
出料
入料
平衡生产线的意义
通过平衡生产线可以综合应用到程序分析、动作分析 、layout分析,搬动分析、时间分析等全部IE手法,提 高全员综合素质
在平衡的生产线基础上实现单元生产,提高生产应变 能力,对应市场变化实现柔性生产系统
(4) 4种增值的工作
站在客户的立场上,有四种增值的工作
1、使物料变形 2、组装 3、改变性能 4、部分包装
物料从进厂到出厂,只有不到 10% 的时间是增值的!
工序
符 号
内容
作业内容
分类
加工 作业
○
加工 作业
■产生附加价值的工序及作 业
卖得掉
检查
□
数量检查 ■虽然有必要,但需要进行 品质检查 改善的工序及作业
现场IE改善案例分析--生 产线平衡分析改善案例
2020年7月14日星期二
内容安排
一、线平衡定义 二、生产线平衡分析方法 三、B值、F值的定义与计算 四、线平衡案例分析
一、线平衡定义
生产线平衡定义
什么是生产线平衡
生产线平衡是指构成生产线各道工序所需的 时间处于平衡状态,作业人员的作业时间尽 可能的保持一致,从而消除各道工序间的时 间浪费,进而取得生产线平衡。
减少人手(1)
將工序3里的工作时 间分配至工序2﹑4 及5之內﹐从而工序 3里的人手可调配其 它生产线去
可行性﹕須工序 2﹐4及5內均有足夠 时间接受额外工作。
ቤተ መጻሕፍቲ ባይዱ
生产线平衡-例3﹕减少人手(2人)
降低线体速度,减少生产产量
工作時間
工序 1 2 3 4 5
减少人手(2)
因生产需求量降低而 可降低线体速度
减少单件产品的工时消耗,降低成本(等同于提高人 均产量)
减少工序的在制品,真正实现“一个流”
提高作业及设备工装的工作效率
生产线平衡计算
• 节拍 – 生产周期
最长工序时间(瓶颈岗位时间)决定了整个生产线的 作业时间,即等于节拍
平衡率
平衡率=
∑(各工序的作业时间) 瓶颈岗位时间*人数
* 100%
• 产品标准工时= 每个工位所用时间的总和
生产线平衡-例2﹕减少人手(1人)
减少人员,维持生产数度不变
工作時間
工序 1 2 3 4 5
减少人手(1)
將工序3里的工作时 间分配至工序2﹑4及 5之內﹐从而工序3里 的人手可调配其它生 产线去
可行性﹕須工序2﹐4 及5內均有足夠时间 接受额外工作。
减少人员,维持生产数度不变
工作時間
工序 1 2 3 4 5
作 业 时 间
工序 1 2 3 4 5
作业改善压缩
作 业 时 间
工序 1 2 3 4 5
分担转移
作 业 时 间
工序 1 2 3 4 5 6
加 人(作业分解)
作 业 时 间
工序 1 2 3 4 5
合并重排
作 业 时 间
工序 1 2 3 4 5
减人(分解消除)
作 业 时 间
工序 1 2 3 4 5
减人(作业改善压缩 )
1505
如上图表中,生产线平衡率=
*100% = 88%
90*19
不平衡率(%)= 100% —平衡率(%)
对生产线来说,不平衡率越小越好,一般控 制5%-13%之间,至少要控制在15%以下。
案例:工时测定和线平衡计算
请大家观看电子分厂电装3人柔性线视频
1、一边看一边测试,最后计算平衡率 2、计算一下线小时理论产量 3、提出提升线平衡的思路方法
• 生产线平衡损失 = 1 - 平衡率 一般要求生产线平衡率达到85%以上
何谓标准工时
标准时间是指,“一个熟练工用规定的 作业方法以标准速度进行作业时所需的作业 时间”。
在熟练度、合理性、工作热情及其他所 有方面都相同的“标准作业员”以标准的作 业方法及一般的努力程度进行作业,次日不 会感到疲劳的“作业时间”。
7、改善瓶颈岗位
(1)改善的4大原則
1)减少动作次数 2)同时使用双手 3)缩短移动距离 4)使动作变得轻松
(2) IE动作改善的4原则:
ECRS原则 1、Eliminate ——取消 2、Combine ——合并 3、Rearrange ——重排 4、Simplify ——简化
(3)ECRS法运用图示简介
二、生产线平衡分析方法
1、识别瓶颈岗位
2、作业岗位工时测定
B
①
A
A通过①,B前端到达①所需时间
3、建立山积表
将各分解动作时间,以叠加式直方图表現的一种 研究作业时间结果的手法。
4、工时测定分析(蓝色为作业的时间红色为失去平衡的时间)
5、生产线平衡的计算
各工程净时间总计 生产线平衡率(%)= 时间最长工程*人员数 *100%
评分标准 1、2、3、4名分别 100、80、60、40分 计算公式错不得分 计算公式对,结果错,扣10分
3人线视频
实例计算
计算公式
(32+37+40)
平衡率=
(40*3)
*100% = 90.8%
电装7人线标准工时
请 计 算 平 衡 率
6、生产线平衡分析的方法
1、确定对象与范围 2、用作业分析把握现状 3、测定各工程的净时间 4、制作速度图表 5、计算平衡 6、分析结果,制定改善方案
搬运 ○
移动
搬运·移 ■虽然现状无可奈何,但需 卖不掉 动 要进行大幅度改善的工序及 操作 作业
停滞 待待
▽
储藏·滞 留
等待
■不产生附加价值的工序及 作业
损失
现在大家思考一下……
我们的生产线上 有多少岗位是不增值的
扑克牌游戏规则
1、每个分厂安排4个人(厂长、工艺、作业长、班长) 2、小组内部自己安排4个人的工作 3、要求是将52张扑克牌按同一花色、从大到小的排成一排 4、时间最少的小组获胜 5、开始和结束计时以固定的人员手敲击桌子为准 6、游戏开始由工作人员将牌洗好
生产线平衡-例1﹕缩短生产节拍
提升生产速度﹐维持人手不变
工作时间
工序 1 2 3 4 5
缩短生产节拍
将工序2里一部 分可抽调的时间 转至工序3里﹐ 以缩减整体的生 产节拍
提升生产速度﹐维持人手不变
改善前 改善后
工作时间
工序 1 2 3 4 5
缩短生产节拍
将工序2里一 部分可抽调的 时间转至工序 3里﹐以缩减 整体的生产节 拍
将工序3﹑4的工作时 间分配至工序 1﹑2﹑5里﹐从而工 序3﹑4工作岗位的人 手可调配至其它生产 线去。
降低线体速度,减少生产产量
增加节拍时间
工作時間
工序 1 2 3 4 5
减少人手(2)
因生产需求量降低而 可降低线体速度
将工序3﹑4的工作时 间分配至工序 1﹑2﹑5里﹐从而工 序3﹑4工作岗位的人 手可调配至其它生产 线去。