生产线平衡改善教学案例
《案例-生产线平衡改善案例OK》
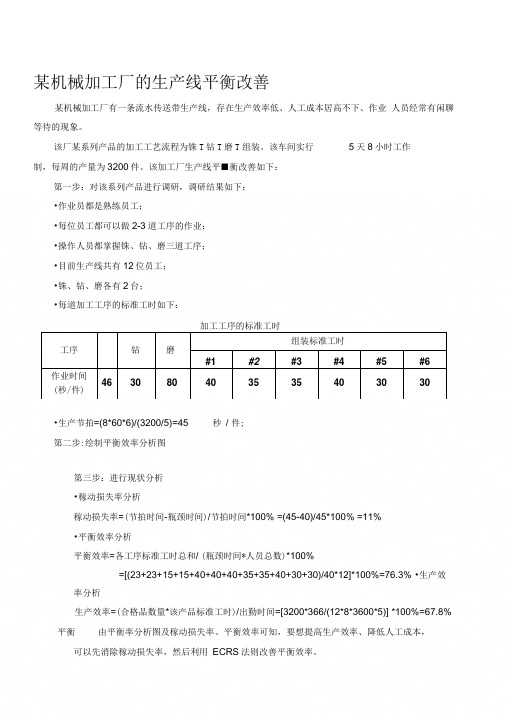
某机械加工厂的生产线平衡改善某机械加工厂有一条流水传送带生产线,存在生产效率低、人工成本居高不下、作业人员经常有闲聊等待的现象。
该厂某系列产品的加工工艺流程为铢T钻T磨T组装。
该车间实行5天8小时工作制,每周的产量为3200件。
该加工厂生产线平■衡改善如下:第一步:对该系列产品进行调研,调研结果如下:•作业员都是熟练员工;•每位员工都可以做2-3道工序的作业;•操作人员都掌握铢、钻、磨三道工序;•目前生产线共有12位员工;•铢、钻、磨各有2台;•每道加工工序的标准工时如下:加工工序的标准工时组装标准工时工序钻磨#1#2#3#4#5#6作业时间463080403535403030 (秒/件)•生产节拍=(8*60*6)/(3200/5)=45 秒/ 件;第二步:绘制平衡效率分析图第三步:进行现状分析•稼动损失率分析稼动损失率=(节拍时间-瓶颈时间)/节拍时间*100% =(45-40)/45*100% =11%•平衡效率分析平衡效率=各工序标准工时总和/ (瓶颈时间*人员总数)*100%=[(23+23+15+15+40+40+40+35+35+40+30+30)/40*12]*100%=76.3% •生产效率分析生产效率=(合格品数量*该产品标准工时)/出勤时间=[3200*366/(12*8*3600*5)] *100%=67.8% 平衡由平衡率分析图及稼动损失率、平衡效率可知,要想提高生产效率、降低人工成本,可以先消除稼动损失率,然后利用ECRS法则改善平衡效率。
第四步:消除稼动损失率消除稼动损失率的核心手段是提高生产量,使生产节拍时间与瓶颈时间相同或接近,即每周产量由3200件提高至3600件。
提高后的生产节拍=实际出勤时间/实际生产数量=8*60*60/(3600/5)=40秒/件这样可以直接减少人员等待时间,大大提高生产效率,改善后的生产效率为:生产效率=(3600*366) / (12*8*3600*5 ) *100%=76.3%第五步:通过ECRQt则进行改善由丁铁、钻的标准时间为23+23+15+15=76秒V 2个生产节拍,因为作业员熟知操作铁、钻、磨工序,所以可以减少一台钻,由4人变为2人操作。
生产线平衡案例分析培训

生产线平衡案例分析培训引言在现代制造业中,生产线平衡是一个至关重要的概念。
通过合理的生产线平衡,可以提高生产效率、降低成本、优化资源利用等。
本文将通过分析一个生产线平衡案例,介绍生产线平衡的原理和方法,并探讨如何进行生产线平衡培训。
案例分析假设一个玩具生产厂家拥有一个生产线,负责生产玩具汽车。
该生产线由多个工作站组成,每个工作站负责一道具体的工序。
现有数据如下:•工作站1:个体组装,每小时可完成200辆玩具汽车的组装。
•工作站2:上色,每小时可完成150辆玩具汽车的上色。
•工作站3:质检,每小时可完成180辆玩具汽车的质检。
根据以上数据,可以计算出每个工作站的产能利用率,如下:•工作站1:200/200 = 100%•工作站2:150/200 = 75%•工作站3:180/200 = 90%从上述数据可以看出,工作站2的产能利用率较低,成为生产线上的瓶颈工序。
如果不及时解决这个问题,将会影响整个生产线的效率和产能。
生产线平衡原理和方法生产线平衡是指合理地安排生产线上各个工作站的工作量,使得各个工作站之间的产能相对平衡,解决瓶颈问题,提高生产效率。
生产线平衡的原理和方法主要包括以下几个方面:1. 识别瓶颈工序首先,需要通过数据分析或实地观察,明确生产线上的瓶颈工序。
瓶颈工序指的是生产能力较低,成为整个生产线效率的制约因素的工序。
在上述案例中,工作站2就是瓶颈工序。
2. 改善瓶颈工序针对瓶颈工序,可以考虑以下几种改善方法:•提高工作站的产能:通过增加设备数量、改进工艺或技术等方式,提高工作站的生产能力。
•减少工作站的工作量:通过优化生产流程,简化工序或调整工作站之间的任务划分,减少瓶颈工序的工作量。
在上述案例中,可以考虑增加上色工作站的设备数量或改善工艺,以提高生产效率。
3. 平衡工作站的工作量在解决瓶颈工序的同时,还需要平衡其他工作站的工作量,使得各个工作站的产能相对平衡。
平衡工作站工作量的方法包括:•调整任务划分:根据不同工作站的产能和工作特点,合理划分任务,避免工作站之间的工作量差距过大。
生产线平衡案例分析过程

生产线平衡案例分析过程1. 引言生产线平衡是一种优化生产过程的方法,旨在确保生产线上的工作站之间的工作负载均衡,以提高生产效率和产品质量。
本文将以一个实际案例为例,分析生产线平衡的过程。
2. 案例背景假设某公司生产手机,并且生产线上有三个关键工作站:组装、测试和包装。
每个工作站的工人数量不同,导致工作负载不均衡,组装工作站负责最多的工作量,而测试和包装工作站的工作负载较少。
3. 数据收集为了分析生产线平衡的问题,首先需要收集一些关键数据。
包括每个工作站的工作时间、工人数量以及每个工作站的工作量。
工作站工作时间(分钟)工人数量工作量(数量)组装工作站30 3 200测试工作站25 2 150包装工作站20 2 100通过收集这些数据,可以计算出每个工作站的单位时间工作量,即每分钟能完成的工作量。
根据上表数据,可以得出以下结果:•组装工作站的单位时间工作量为6.67件/分钟(200件/30分钟)•测试工作站的单位时间工作量为6件/分钟(150件/25分钟)•包装工作站的单位时间工作量为5件/分钟(100件/20分钟)4. 分析和优化通过计算每个工作站的单位时间工作量,可以判断哪个工作站是生产线上的瓶颈工作站。
在这个案例中,组装工作站的工作量最大,成为瓶颈,会导致生产线的工作负载不平衡。
为了平衡工作负载,可以采取以下优化措施:•调整工人数量:增加组装工作站的工人数量,以减轻其工作负荷。
•优化工作时间:分析工作时间,寻找减少生产时间的方法,例如改进工艺或引入自动化设备。
•转移工作量:将部分组装工作转移到其他工作站,以平衡各工作站的负载。
5. 优化结果评估经过优化措施的实施后,重新计算每个工作站的单位时间工作量,以评估结果。
工作站工作时间(分钟)工人数量工作量(数量)单位时间工作量(件/分钟)组装工作站30 4 200 5测试工作站25 2 150 6包装工作站20 2 100 5通过调整组装工作站的工人数量,将其增加到4人,重新计算单位时间工作量之后,可以看到组装和包装工作站的工作量现在已经达到了平衡,测试工作站的工作量仍然保持不变。
生产线平衡分析改善案例

生产线平衡分析改善案例引言生产线平衡是指在生产过程中,通过合理分配各个工序的工作量,使得各个工序的产能能够实现平衡,从而提高生产效率、降低成本,并确保产品质量。
本文将以一个实际案例为例,介绍生产线平衡分析和改善的具体过程。
案例背景某电子产品制造公司拥有一条生产线,生产一种电子产品,该产品的组装工序分为A、B、C、D四个子工序。
在目前的生产线上,工序A的生产能力远超其他三个工序,导致A工序成为瓶颈工序,无法满足后续工序的需求,从而影响了整个生产线的效率和产量。
因此,公司决定进行生产线平衡分析,并制定改善方案,以提高生产线的平衡度。
生产线平衡分析1. 数据收集首先,需要收集工序A、B、C、D的工作时间数据,包括每个工序的加工时间、准备时间和等待时间。
这些数据将作为分析的基础。
2. 流程图绘制根据数据收集到的各个工序的时间,并结合实际生产情况,可以绘制出生产线的流程图。
流程图可以清晰地展示每个工序的工作时间和流程顺序,有助于进一步分析。
3. 生产线平衡计算根据流程图,可以计算出每个工序的工作时间总和。
然后,根据目标产量,计算出每个工序的标准工作时间,即每个工序应该占用的时间比例。
通过比较实际工作时间和标准工作时间,可以评估生产线的平衡度。
4. 分析结果根据生产线平衡计算的结果,可以看出工序A的工作时间远超其他工序,导致生产线的不平衡。
这也解释了为什么A工序成为瓶颈工序。
改善方案1. 调整工序A的产能由于工序A是瓶颈工序,可以考虑通过增加设备或优化工艺,提高工序A的产能,以满足后续工序的需求。
这可以通过增加工序A的设备数量、提高工段效率或优化工艺流程等手段实现。
2. 优化其他工序除了调整工序A的产能外,还可以进一步优化其他工序的流程,减少每个工序的工作时间。
例如,可以通过流程改进、工艺优化、培训员工等方式,提高其他工序的效率,从而平衡整个生产线。
3. 调整生产计划根据生产线平衡分析的结果,可以对生产计划进行合理调整。
生产线平衡分析改善案例

齿条生产线平衡改善一、项目名称齿条生产线平衡改善二、项目目标1、粗校至滚铆达成一件流,无心磨至高频小批量流动2、生产线在制减少70%,周转车下线,采用传送带传输3、生产周期缩短80%4、生产线平衡率提升至80%,人员效率提升10%5、生产过程PPM下降50%三、项目组织一、项目名称、目的及内容:目的:1、生产线平衡分析改善。
通过成组分线后,选取代表型号进行生产线平衡分析,运用丰田生产方式结合瓶颈限制理论管理2、生产线换型分析改善。
通过对每天的产量确定固定的生产时间,确定换型可利用时间,以此设置标准工序超市以及流转批量。
3、标准化作业改善:通过对现场时间以及动作分析,并进行工位改善,编制标准化作业指导书。
将现场作业标准化,包括标准作业时间,标准在制,标准作业顺序。
4、传送方式改善:确定工序超市、流转批量后,进行流转方式改善。
二、项目组成员及分工:职姓名工作要求位组长负责进行分工,指导并监控整个过程按节点实施。
协调资源。
副组长负责整个项目的对策评价、实施监控。
组员负责进行齿条标准时间以及动作研究,以及动作、流转改善组员负责整个项目的对策拟定评价、实施。
组员负责进行齿条标准时间与动作分析,生产线平衡方案的制定。
编制标准化作业指导书。
组员布局图绘制,标准作业下发组员负责项目整个进行过程中的质量监控。
组员负责流转设施的自制,布局调整。
三、项目实施具体计划:序号阶段项目内容责任人起始完成时间时间1现状分析时间研究、动作分析、生产线平衡分析培训TOC简介改善专员2月4日2月16日2 生产线布局分析改善专员3 代表型号的测时、动作分解改善专员4 换型时间的调查改善专员5对策拟定根据时间分析,确定工序超市及工序间流转方式,及工序流转数量各分项小组(齿条线、齿轮轴线)2月8日3月15日6根据设备放置及工序节拍确定线体长度、速度、分段形式各分项小组(齿条线、齿轮轴线)7 标准化作业的编制改善专员8 改善过程中的质量监控9 对策评价改善对策的评价项目组成员3月16日3月23日10 对策实施流转线体制作2月8日3月15日现场试运行,质量部、技术部评价,项目成员、质管、技术3月25日2月25日11 项目验收现场项目验收质管部、技术部3月26日3月30日四、现状分析1、问题描述在2011年底整个机加车间分线分级,建立初步“流水线”作业方式后,加工过程中的各种浪费被显现出来,包括(1)节拍不平衡的效率损失(2)人员等待设备的浪费(3)在制品的浪费(4) 批量的不合格品及返工浪费(5) 搬运的浪费(6) 动作的浪费为此,生产部的带领下,机加车间开展了生产线平衡改善以及流转方式改善项目,运用丰田最基本最重要的IE时间测定与动作分析改善手法实施方法改善,通过流水线架的制作,实现按节拍的“单件流”生产。
生产线平衡分析改善案例(PPT53张)

工位间和工位内的多余的WIP为零。
B值=1
一 物 流
物流
顺畅流动 没有停滞
物留
中间停滞 隐藏问题
“一个流”的益处
1. 内建品质管理; 2. 创造真正的灵活弹性; 3. 创造更高的生产力; 4. 腾出更多厂房空间; 5. 改善安全性; 6. 改善员工士气; 7. 降低存货成本。
生产线平衡定义
对生产的全部工序进行均衡,调整作业 负荷和工作方式,消除工序不平衡和工 时浪费,实现“一个流”。
入料
出料
平衡生产线的意义
通过平衡生产线可以综合应用到程序分析、动作分析 、layout分析,搬动分析、时间分析等全部IE手法,提 高全员综合素质 在平衡的生产线基础上实现单元生产,提高生产应变 能力,对应市场变化实现柔性生产系统 减少单件产品的工时消耗,降低成本(等同于提高人 均产量) 减少工序的在制品,真正实现“一个流” 提高作业及设备工装的工作效率
5、生产线平衡的计算
各工程净时间总计 生产线平衡率(%)= 时间最长工程*人员数 *100% 如上图表中,生产线平衡率= 1505 90*19 不平衡率(%)= 100% —平衡率(%) *100% = 88%
对生产线来说,不平衡率越小越好,一般控 制5%-13%之间,至少要控制在15%以下。
案例:工时测定和线平衡计算
降低线体速度,减少生产产量
减少人手(2) 工 作 時 間
因生产需求量降低而 可降低线体速度
将工序3﹑4的工作时 间分配至工序 1﹑2﹑5里﹐从而工 序3﹑4工作岗位的人 手可调配至其它生产 线去。
工序 1
生产线平衡案例

实施平衡措施后,生产线平衡率得到显著提高, 在制品数量减少,设备故障率降低,整体生产效 率提升。
案例二:电子产品生产线平衡
生产线现状分析
针对电子产品生产线,发现其存在工序繁多、作业时间不稳定、 物料供应不及时等问题。
平衡措施实施
通过作业测定对工序进行重新组合与排序,实现作业时间的均衡化; 加强物料计划与调度管理,确保物料供应的稳定性。
稳定性。
降低生产成本和浪费
减少因生产线不平衡而产生的在制品库存和成品 库存,降低库存成本。
通过优化生产计划和调度,减少生产过程中的停 机、换模等浪费,降低生产成本。
提高设备利用率和员工工作效率,减少人力和物 力的浪费。
增强企业竞争力和可持续发展能力
• 生产线平衡有利于企业实现精益生产和敏捷制造,快速响应市场需求变 化。
优化资源配置
通过生产线平衡,合理配置人力、 物力和财力资源,使生产过程更加 顺畅,提高企业的整体运营水平。
生产线平衡的定义和意义
定义
提升生产效率
降低成本
提高产品质量
增强企业竞争力
生产线平衡是对生产线 上各个工序进行作业时 间分析和调整,使各工 序的作业时间尽可能相 等或接近,以达到提高 生产效率、降低成本的 目的。
编制方法
根据工艺流程图提供的基础数据,计算各工序的生产能力、负荷率等 指标,并按照一定的格式编制成表格。
瓶颈分析和改善
定义
瓶颈分析是指通过分析生产线上各工序的生产能力和负荷 情况,找出制约生产线整体效率的瓶颈工序,并制定相应 的改善措施。
作用
通过瓶颈分析,可以针对生产线上的瓶颈工序进行改善, 提高生产线的整体效率,降低成本,提高产品质量。
即每个产品需要在多长时间内完成生产。
生产线平衡分析与改善PPT课件
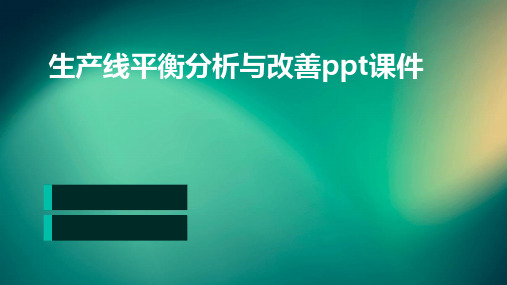
某汽车企业在生产过程中面临工艺复杂、生产流程长等问题,通过改进生产工 艺和引入智能制造技术,实现了生产线平衡的持续改进,提高了生产效率和产 品质量。
06 结论与展望
生产线平衡对企业的影响
提高生产效率
生产线平衡能够优化资源配置,减少生 产过程中的空闲时间,提高设备利用率,
从而提高生产效率。
持续改进与优化
定期检查
定期对生产线进行检查,发现潜在问题并及时解 决。
员工培训
加强员工培训,提高操作技能和生产意识,促进 持续改进。
ABCD
数据跟踪
建立数据跟踪机制,对生产线相关数据进行实时 监测和分析,以便及时调整和优化。
创新与改进
鼓励员工提出创新和改进意见,激发团队活力和 创造力,实现持续改进与优化。
设备利用率是指生产线设备在一段时间内 的有效工作时间与总工作时间的比值,反 映了设备的利用情况。
生产效率
在制品库存
生产效率是指生产线在一定时间内完成的 产品数量与总工作时间的比值,反映了生 产线的生产能力。
在制品库存是指生产线在制品的数量和存 储时间,反映了生产线的库存状况。
生产线平衡的优化目标
01
随着工业4.0和智能制造的兴起,未来生产 线平衡将更加注重智能化技术的应用,如
物联网、大数据、人工智能等。
绿色生产线的推广
随着环保意识的提高,未来生产线平衡将 更加注重环保和可持续发展,推广绿色生
产技术和设备。
柔性生产线的构建
为了更好地适应市场需求的变化,未来生 产线平衡将更加注重生产线的柔性和可重 构性。
绘制工艺流程图,直观展示工艺流程, 便于发现瓶颈环节。
引入自动化和智能化设备,减少人工 干预,提高生产效率。
- 1、下载文档前请自行甄别文档内容的完整性,平台不提供额外的编辑、内容补充、找答案等附加服务。
- 2、"仅部分预览"的文档,不可在线预览部分如存在完整性等问题,可反馈申请退款(可完整预览的文档不适用该条件!)。
- 3、如文档侵犯您的权益,请联系客服反馈,我们会尽快为您处理(人工客服工作时间:9:00-18:30)。
每日計劃
I
I
I
I
I
3.改善过程--D-M-A-I-C
因果分析
机 Analyze
人
WIP多 LT长 UPPH低
良率低
推式生产
质量意识弱
产能不匹配
管理效率低下
路线迂回 洁净度不达标
环
作业分配不合理
品种多
工站不连续
法
重工不規范
料
排配不合理
3.改善过程--D-M-A-I-C
价值流未来图
每日计划仅向检包发出
液底
6.1 6
改善後
流程優化 布局頁 改碼 : 善1 /1
工作說明
距 離
時 間
人 力
(m )
3.改善过程--D-M-A-I-C
顾客需求:約1.4K/10H 理想出货节拍为25秒
CT(秒)
節拍設定 人力重排
18
16
14
12
10
8
6
11.5
4
2
0 遮蔽
13.9 粉底
12.596
13.822
16.492
与前工站距离3米!完全可以合并!
3.改善过程--D-M-A-I-C
WIP, Lead Time, UPPH
Define
精益生产
WIP 降低
LT 缩短
UPPH
提升
3.改善过程--D-M-A-I-C
以Q系列机种为例进行测量
Measure
LT=39H
WIP=2,625pcs UPPH=1.21pcs
价值流图
VSM分析案例—2.VMS图
原料、半成品 仓库
每月预测 每周计划
车间调度部门 MRP
每日计划
700 件/日 料盘 = 25 件
2 班制
手推车 1次/班
粗车
每周计划
钻孔
精车、抛光
每月预测
裝配工位
700 件日 料盘 = 25 件
2 班制 手推车 2次/班
检验
350件 1
175件
1
175件
1
175件 1
两班制
两班制
5
VSM分析案例—3.需求分析
每天的平均产量 = 700 件 生产节拍 = 每每 天天 有生 效产 (s工 )产 7作 37量 6时 00 020间 72 s 等待及运输时间1= 在有 制效 品 生 工 库 产 作 存 2 3 节 5 5 时 7 2 0 拍 22 0 间 00 .5天 等待及运输时间2= 在有 制效 品 生 工 库 产 作 2 1 存 节 5 7 时 7 2 5 拍 22 0间 0.2 0天 5
Improve
8
1.背景介紹
镁合金涂装主要产品
S
Q
1.背景介紹
镁合金涂装生产流程
暂存 贴纸 一底
补土
重工
捡包
一底研磨 二底 二底研磨
重工
移印 首捡
面2
面1
入库
1.背景介紹
镁合金涂装主要工艺
贴纸 一底 二底 面漆 移印 检包
2.现状描述
镁合金涂装工段
多处、大量WIP堆放 物流路线迂回交叉 不必要的生产间断
设计一个精益价值流 建立想要达到的理想状态
计划和实施
实施计划,达到的理想状态
VSM分析数据收集
生产过程数据 生产可利用时间 生产周期时间 换模时间 正常运行时间 生产班次 生产批量/数量 操作工时 关键工序/瓶颈工序
库存数据 生产过程之间 门到门 返工、维修区域 零件库 在制品库 未运输成品
有效时间25200s
有效时间25200s
两班制
两班制
35s
生0产.2车5d间
55s
175件 I
0.25d
1
加工时间=25s 换模时间=0 使用率=100%
有效时间25200s 两班制
25s 7
175件 I
0.25d
生产线平衡案例3---物流分析法
DMAIC
Measure
Analyze
Define Control
175件
I
加工时间=60s 换模时间=0
I
使用率=100%
有效时间25200s
两班制
加工时间=35s 换模时间=0
I
加工时间=55s 换模时间=0
I
加工时间=25s 换模时间=0
I
使用率=100%
使用率=100%
使用率=100%
有效时间25200s
有效时间25200s
有效时间25200s
两班制
生产车间
标准的VSM布局
信息流
生产控制
客户
供应商
每周计划
浪费
浪费
无价值
粗车
1 有价值
1.将不连续的流重点标记出来;
钻孔
精车、抛光
2.找出1 物料流和信息1 流交互的地方;
3.浪费和需要改进处重点标记出来。 物料流
VSM分析关键步骤
选择一个 产品
从头到位聚焦一个产品、过 程或服务,搜集相关数据
分析当前问题: 信息、物料、交互
研究者:林燕梅 日 期 : 09年 8月
時間單位 :
m in
s
人流型
物流型
現行
步 驟
加 工 ○
搬檢等 運驗待 →□ D
工作說明
距 離
時 間
(m )
ECRS
改善情況
人 力
取 消
合 併
重 排
簡 化
步 驟
加 工 ○
搬 運 →
檢 驗 □
等 待 D
儲 存 ▽
1●
遮蔽
11.5 12
2
D
暂时放置
90
3→
搬运下一个工站 1 2
6
VSM分析案例—2.VMS图
原料、半成品 仓库
每月预测
车间调度部门
每月预测
每周计一划 个产品的生产M过RP 程中,产每日品计划生产时间
裝配工位
700 件/日
料盘 = 25 件 2 班制
(产生价值时间)=175s,生产过程时间(包
每周计划
括物流等时间)=1.5d,生产时间占了2‰。
手推车 1次/班
4●
除尘
6.4 1
5●
粉底
0 8.5 3
6●
烤炉
1200 1
7→
搬往下一工站 4 8
8●
补土
14 3
9
D
暂时放置
210
10 →
搬 运 下 一 个 工 站 25 50 1
11 ●
一底机磨
11 3
12
D
暫時放置
330 1
13 →
搬 运 下 一 个 工 站 18 36 1
14 ●
一底手磨
7.7 6
15 ●
工站不连续
作业分配不合理
推式生产观念
路线迂回
流程优化 布局改善
重工不規范
节拍设定 人力重排
拉动设置
拉动生产
3.改善过程--D-M-A-I-C
实现价值流未来图三步走
Improve
节拍设定 人力重排
流程优化 布局改善
拉动设置
3.改善过程--D-M-A-I-C
流程分析圖
工作名稱: 涂装一底二底 開 始 :遮 蔽 結束: 二底研磨
液底
面漆
移印检檢包包
遮蔽
粉底
液底
面漆
檢包
移印检包
3.改善过程--D-M-A-I-C
節拍設定 人力重排
貼紙
...
貼紙工艺:
非重工 + 重工量 = 產出
捡包
700 件/日
料盘 = 25 件 2 班制
手推车 2次/班
粗车
钻孔
精车、抛光
检验
350件 I
0.5d
1
加工时间=60s 换模时间=0 使用率=100%
有效时间25200s 两班制
60s
175件 I
0.25d
1
175件
1
加工时间=35s
加工时间=55s
换模时间=0
I
换模时间=0
使用率=100%
使用率=100%