鼓风炉还原熔炼的基本原理
氧气底吹熔炼—鼓风炉还原炼铅新技术
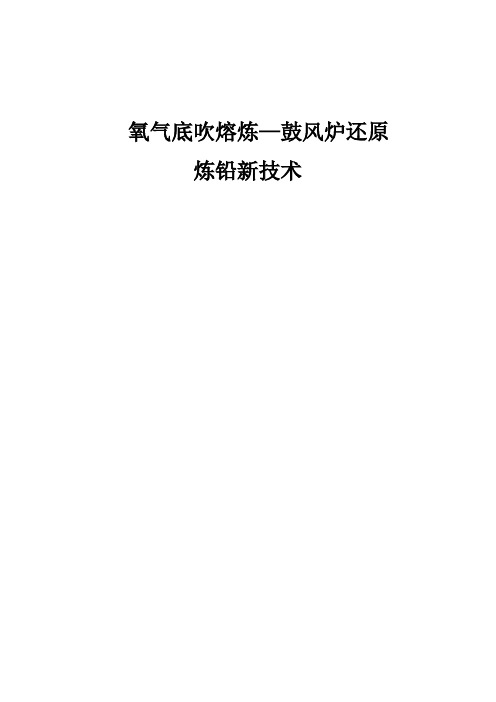
氧气底吹熔炼—鼓风炉还原炼铅新技术氧气底吹熔炼—鼓风炉还原炼铅法一、氧气底吹熔炼—鼓风炉法简介氧气底吹熔炼—鼓风炉还原炼铅法工艺流程为:熔剂、铅精矿或二次铅原料及铅烟尘经配料、制粒或混捏后进行氧气底吹熔炼,产出烟气、一次粗铅和铅氧化渣,烟气经余热锅炉回收余热和电收尘器收尘后采用二转二吸工艺制酸,尾气排放,铅烟尘返回配料。
铅氧化渣经铸块后与焦块、熔剂块混合后入鼓风炉进行还原熔炼,产出炉渣、烟气和粗铅,烟气经收尘后放空,铅烟尘返回配料。
工艺主要设备包括可旋转式氧气底吹熔炼炉,多元套管结构氧枪(多通道水冷高温喷镀耐磨底吹氧枪),特殊耐磨材质的氧枪口保护砖,浅层分格富铅渣速冷铸渣机(铅氧化渣铸渣机),带弧型密封罩和垂直模式壁中压防腐余热锅炉,全封闭铅烟尘输送配料等, 新型结构鼓风炉(双排风口大炉腹角高料柱)等。
工艺的核心设备是氧气底吹熔炼炉。
熔炼炉炉型结构为可回转的卧式圆筒形,在炉顶部设有2~3 个加料口,底侧部设有3~6 个氧气喷入口,炉子两端分别设一个虹吸放铅口和铅氧化渣放出口。
炉端上方设有烟气出口。
铅精矿的氧化熔炼是在一个水平回转式熔炼炉中进行的。
铅精矿、铅烟尘、熔剂及少量粉煤经计量、配料、圆盘制粒后, 由炉子上方的气封加料口加入炉内, 工业纯氧从炉底的氧枪喷入熔池。
氧气进入熔池后, 首先和铅液接触反应, 生成氧化铅(PbO ) , 其中一部分氧化铅在激烈的搅动状态下, 和位于熔池上部的硫化铅(PbS) 进行反应熔炼, 产出一次粗铅并放出SO 2。
反应生成的一次粗铅和铅氧化渣沉淀分离后, 粗铅虹吸或直接放出,铅氧化渣则由铸锭机铸块后, 送往鼓风炉工段还原熔炼, 产出二次粗铅。
出炉SO 2 烟气采用余热锅炉或汽化冷却器回收余热, 经电收尘器收尘, 送硫酸车间处理。
熔炼炉采用微负压操作, 整个烟气排放系统处于密封状态, 从而有效防止了烟气外逸。
同时, 由于混合物料是以润湿、粒状形式输送入炉的, 加上在出铅、出渣口采取有效的集烟通风措施, 从而避免了铅烟尘的飞扬。
3鼓风炉熔炼

炉料和焦炭由加料斗加入。 炉料和焦炭由加料斗加入。 炉子两侧的块料和焦炭多, 炉子两侧的块料和焦炭多,炉中心为夹有块料和 焦炭的中心精矿料柱, 焦炭的中心精矿料柱,从而形成炉料分布不均匀的状 态。 由于炉内炉料分布的不均匀,导致炉气沿炉子水 由于炉内炉料分布的不均匀, 平断面分布也不均匀。炉子两侧料柱中块料多, 平断面分布也不均匀。炉子两侧料柱中块料多,对炉 气阻力小,而炉子中心的混捏铜精矿多, 气阻力小,而炉子中心的混捏铜精矿多,再加上料斗 的密封料柱的压力,故对烟气的阻力较大。因而炉气 的密封料柱的压力,故对烟气的阻力较大。因而炉气 由炉子两侧流过的多,而流经炉子中心的则极少。 由炉子两侧流过的多,而流经炉子中心的则极少。
6
预备区下部温度较高,中心料柱的铜精矿又受到上 预备区下部温度较高, 部较柱的压力作用,且与侧料柱交界的界面上温度很高, 部较柱的压力作用,且与侧料柱交界的界面上温度很高, 从而发生固结和烧结,产出具有一定强度的精矿块。 从而发生固结和烧结,产出具有一定强度的精矿块。 固结和烧结 在预备区石灰石受热发生分解: 在预备区石灰石受热发生分解: CaCO3→CaO + CO2
1
鼓风炉是一种具有垂直作业空间的冶金设备。 鼓风炉是一种具有垂直作业空间的冶金设备。炉料 和燃料从炉子上部加料口分批加入, 和燃料从炉子上部加料口分批加入,空气或富氧空气从 炉子下部两侧的风口鼓入, 炉子下部两侧的风口鼓入,产出的高温烟气通过炉料与 燃料的空隙而上升,并经炉子上部的烟气出口排出炉外。 燃料的空隙而上升,并经炉子上部的烟气出口排出炉外。
7
(2)焦点区 ) 焦点区是进行激烈化学反应和熔化过程的区段, 焦点区是进行激烈化学反应和熔化过程的区段,一 般位于风口上方一米左右的地方,最高温度达 般位于风口上方一米左右的地方,最高温度达1250 ~ 1350 ℃。 在焦点区内,被氧化的主要是FeS,产出的 在焦点区内,被氧化的主要是 ,产出的FeO与 与 炉料中的SiO2造渣。此外,转炉渣中的 3O4也直接与 造渣。此外,转炉渣中的Fe 炉料中的 SiO2和FeS作用造渣。 作用造渣。 作用造渣 焦炭几乎全部在焦点区被鼓入的空气燃烧: 焦炭几乎全部在焦点区被鼓入的空气燃烧: C + O2 = CO2
鼓风炉富氧熔炼炼铜

铜氧化矿的鼓风炉还原熔炼

銅氧化礦的鼓風爐還原熔煉Smelting Reduction of Copper Oxide Ore Blast Furnace文/邊瑞民 申殿邦 劉俊江東營方圓有色金屬有限公司摘要:本文系統介紹了銅氧化礦採用鼓風爐還原熔煉的基本原理、生產過程、常見故障及其處理方法、合理渣型的探討與建議等。
銅氧化礦還原熔煉工藝原是一項老技術,而現代銅冶煉工藝幾乎都將處理硫化礦生產技術作為研究重點。
因而銅氧化礦的鼓風爐還原熔煉有數十年無人研究與應用,很少有相關資料。
近年來,由於非洲礦產的開發,處理銅氧化礦問題又提上新的議事日程。
為此,東營方圓有色金屬有限公司(以下簡稱方圓公司)於2006年建設了依台處理銅氧化礦的舉行全水套鼓風爐(見圖1),爐體分別有上下水套組成,底部設有固定式本床。
爐料經計量後有加料小車通過提升機運送到加料平台人工上料,打鋼釬或燒氧間斷放渣放銅,爐渣經水碎後出售。
冷卻水循環使用,採用羅茨鼓風機供風。
煙氣依次經沉降冷卻室、漩渦收塵器、U型管冷卻器,使煙氣溫度降低到100℃以下,並使用其中的粗塵分離,再通過離心式引風機進入布袋室收塵後達標排空,其工藝流程(見圖2)。
爐子系負壓操作,車兼內外基本無煙塵,清潔環保,勞動環境優越。
圖1 銅氧化礦還原熔煉鼓風爐圖2 銅氧化礦還原熔煉流程圖方圓公司當時尚未建設銅的粗煉系統,而陽極爐產生的精煉渣無適當的設備進行處理,只能廉價出售。
銅氧化礦還原熔煉鼓風爐建成投產後,將精煉渣以適當的比例配入氧化礦中處理,效果很好。
該鼓風爐的原料主要有兩種,從南非等地進口的銅氧化礦以及自產的銅陽極爐精煉渣,屬連續作業,年開爐時間330天,處理料量50,000噸,其中銅氧化礦40,000噸,銅精煉渣10,000噸,生產粗銅10,000噸。
經多年的反覆生產實踐,技術條件不斷優化,工藝操作日趨成熟。
目前,爐子生產運行穩定,並實現了連續生產,大幅提升了爐子的作業率及處理能力,有效降低了生產成本。
熔炼炉原理

熔炼炉原理熔炼炉是一种用来将金属或其他物质加热至高温并使其熔化的设备。
在工业生产和制造过程中,熔炼炉被广泛应用于金属冶炼、玻璃制造、陶瓷生产等领域。
熔炼炉的原理是通过加热将固体物质转化为液态,从而实现材料的加工和制造。
本文将介绍熔炼炉的原理及其工作过程。
熔炼炉的原理主要包括加热和熔化两个过程。
首先,熔炼炉通过加热装置对物质进行加热,使其温度逐渐升高。
当物质的温度达到其熔点时,固体物质开始逐渐转化为液态。
在这个过程中,熔炼炉需要提供足够的热量以确保物质能够完全熔化。
同时,熔炼炉还需要具备良好的保温性能,以保持物质在液态状态下的稳定温度。
熔炼炉的工作过程通常包括装料、加热、熔化和倾铸等步骤。
首先,需要将待加工的物质装入熔炼炉的容器中。
然后,启动加热装置对物质进行加热,直至其达到熔化温度。
在熔化过程中,熔炼炉需要保持合适的温度和保温时间,以确保物质能够完全熔化。
最后,当物质完全熔化后,可以进行倾铸或其他加工操作,从而得到所需的成品。
熔炼炉的原理是基于物质的热力学性质和相变规律。
当物质受热时,其分子内部的运动将加速,从而使其温度升高。
当温度达到一定数值时,物质的结构将发生改变,固体逐渐转化为液态。
这一过程是一个热力学平衡过程,需要在一定温度范围内进行,并受到热量传递和热损失的影响。
因此,熔炼炉的设计和操作需要考虑到物质的热力学特性,以确保熔化过程的顺利进行。
熔炼炉的原理是工业生产中不可或缺的重要设备。
通过熔炼炉,可以对金属、玻璃、陶瓷等物质进行加工和制造,从而满足各种工业生产的需求。
熔炼炉的原理和工作过程对于材料加工和制造具有重要意义,对于提高生产效率和产品质量具有重要作用。
总之,熔炼炉的原理是通过加热将固体物质转化为液态,从而实现材料的加工和制造。
熔炼炉的工作过程包括加热、熔化和倾铸等步骤,需要充分考虑物质的热力学性质和相变规律。
熔炼炉在工业生产中具有重要作用,对于提高生产效率和产品质量具有重要意义。
还原熔炼的原理及方法

还原熔炼的原理及方法熔炼是指将金属或合金加热至其熔点,使其化为液态,以便进行加工或再次制成新的金属制品的过程。
熔炼是金属加工的重要方法,可以通过熔点降低的方式来进行熔炼。
熔炼的原理是利用金属或合金的熔点进行加热使其进入液态,然后通过一系列的加工工艺来得到指定形状和性能的金属制品。
熔炼的方法可以根据金属或合金的特性和加工要求来选择合适的熔炼工艺,保证所得的金属制品的质量和性能满足要求。
熔炼的方法主要有火法熔炼和电炉熔炼两种,下面我将对这两种方法进行详细介绍。
火法熔炼是通过燃料的燃烧来加热金属或合金至其熔点,将其熔化成液态。
火法熔炼通常使用高温燃料来提供热能,如焦炭、煤炭、天然气等。
火法熔炼可以分为炼铁炉、转炉、电炉和电弧炉等几种形式。
其中炼铁炉是通过焦炭和铁矿石的还原反应将铁矿石还原成铁水,并利用高温将铁水熔化成铁水并分离出不溶于铁水的渣滓,从而得到纯净的铁水;转炉是通过氧气吹炼法将废钢、再生铁或生铁进行冶炼;电炉是通过电能将金属或合金加热至其熔点,然后制成相应的金属制品。
火法熔炼的优点是生产成本较低,但是操作复杂,环境污染严重,而且设备需要耗费大量的能源。
电炉熔炼是利用电能将金属或合金加热至其熔点,然后熔化成液态。
电炉熔炼通常使用感应电炉、电弧炉、电阻炉、电渣炉等几种形式。
感应电炉是利用电磁感应原理将感应盘的内金属对感应盘外的金属产生感应电流,并使之加热。
电弧炉是通过电弧将金属或合金加热至其熔点,制成相应的金属制品,其优点是温度控制精准、操作简单、熔炼质量好等,但缺点是设备成本高,能耗大。
电阻炉是利用电阻加热将金属或合金加热至其熔点,然后制成相应的金属制品,其优点是加热速度快、设备布局灵活等,但缺点是成本高、能耗大。
电渣炉是利用电阻加热,将金属或合金加热至其熔点,然后制成相应的金属制品,其优点是操作方便、能耗低、熔炼质量好等,但设备成本高。
总结来说,熔炼是一种将金属或合金加热至其熔点,使其熔化成液态的加工方法,能够通过一系列的加工工艺来得到指定形状和性能的金属制品。
还原炉工作原理 -回复
还原炉工作原理-回复【还原炉工作原理】还原炉是一个重要的工业设备,用于将金属氧化物还原成金属。
它广泛应用于冶金、化工、建材等领域。
本文将从还原炉的基本原理、燃料选择、还原反应过程以及影响还原效果的因素等方面,一步一步地回答还原炉的工作原理。
第一步,基本原理还原炉的基本原理是利用高温环境下气体与金属氧化物发生反应,从而使金属氧化物还原成金属。
在还原炉中,通常使用的还原气体有氢气、一氧化碳和甲烷等。
这些还原气体能够与氧化物中的氧原子结合,形成水蒸气或二氧化碳等,同时还释放出大量的热能,提供反应所需的能量。
第二步,燃料选择还原炉的燃料选择对反应过程和效果有重要影响。
燃料需要具备足够的热值,以提供反应所需的热能。
同时,还需要考虑燃料与金属氧化物之间的化学反应性。
一般来说,氢气是最常用的还原炉燃料,因为它具有高效的还原能力,并且在反应过程中产生的副产品少。
但是,在某些情况下,一氧化碳和甲烷也可以作为燃料使用。
第三步,还原反应过程还原反应是整个还原炉工作的核心。
反应过程可以分为几个不同的阶段。
首先,金属氧化物在高温下被燃料中的还原剂气体还原成金属和水蒸气或二氧化碳。
其次,金属与还原剂气体之间可能发生一系列反应,例如金属与氧化剂反应生成金属氧化物等。
最后,通过合适的物理操作,可以将金属分离出来,获得纯净的金属产品。
第四步,影响还原效果的因素还原炉的效果受多种因素影响,包括温度、压力、还原剂浓度、反应时间等。
温度是影响还原效果最主要的因素之一。
较高的温度有助于提高反应速率和还原程度。
同时,气氛中的气压也对还原效果有重要影响。
气压越高,反应速率越快,但是需要考虑安全因素。
此外,还原剂浓度和反应时间也会对还原效果产生影响,需要根据具体情况进行调控。
第五步,工业应用还原炉广泛应用于冶金、化工、建材等领域。
在冶金行业,还原炉常用于金属的冶炼过程,例如将铁矿石还原为纯铁。
在化工行业,还原炉可用于催化剂的再生与回收,实现资源的循环利用。
氧气底吹熔炼——鼓风炉还原炼铅新技术及应用
氧气底吹熔炼——鼓风炉还原炼铅新技术及
应用
随着社会工业化进程的加速,各种生产工艺也在不断推陈出新,为了满足人们对高品质产品的需求,各种新技术应运而生。
其中就包括了氧气底吹熔炼——鼓风炉还原炼铅新技术。
这种技术的出现,不仅改善了铅熔炼中的环境问题,还提高了铅产量,使得铅冶炼业得到了更好的发展。
传统的铅熔炼工艺在煤气炉中进行,由于煤气本身所含有的硫化氢等有毒物质对环境的污染,以及因高温燃烧产生的大量废气对空气的污染,除了对环境造成了严重的影响,同时也使得铅熔炼的能源利用率很低,
为了解决这些问题,氧气底吹熔炼——鼓风炉还原炼铅新技术应运而生。
这种技术采用氧气作为燃料,通过底吹方式将氧气吹入铅熔炼炉中,使得铅在高温高浓氧气氛下迅速氧化还原,加快了铅的熔化
和反应速率,同时废气、废渣产生率也得到了大幅度降低,不仅对环
境影响减小,而且对于铅产出质量的提高也有明显作用。
在现如今的铅冶炼业,氧气底吹熔炼——鼓风炉还原炼铅新技术
得到了广泛应用。
采用这种技术可以使得铅炉的能耗比传统炉子降低
约25%~35%不等,同样的情况下也能产生更多的铅产出,同时在生产过程中无污染的废气排放,使得工作环境更加安全,这给企业的生产过
程增加了很多收益和竞争力。
综上所述,氧气底吹熔炼——鼓风炉还原炼铅新技术的广泛应用,不仅对于环保和节能的发展产生了积极的推动作用,而且在提高生产
成本的同时也促进了铅冶炼业的发展。
因此,这种技术的应用前景非
常广阔,也值得我们在实际生产中予以重视。
铅烧结矿的鼓风炉还原熔炼
第 三 节 铅烧结矿的鼓风炉还原熔炼
概述 烧结焙烧得到的铅烧结块中的铅主要以PbO(包括结合态的硅酸铅)和少量的PbS、金属Pb及PbSO4等形态存在,此外还含有伴存的Cu、Zn、Bi等有价金属和贵金属Ag、Au以及一些脉石氧化物。 鼓风炉熔炼的主要过程有:碳质燃料的燃烧过程、金属氧化物的还原过程、脉石氧化物(含氧化锌)的造渣过程,有的还发生造锍、造黄渣过程,最后是上述熔体产物的沉淀分离过程。
从上面计算可以看出,当采用强还原气氛时,有利于降低渣含铅。但是,强还原气氛除在热的利用上不经济以外,还受到铁的还原反应的制约: FeO(液) + CO = Fe (液) + CO2 在铅冶炼中,铅铁是完全不互溶的,所以金属铅几乎不含铁。为使有足够的还原气氛以降低渣含铅,局部的很少量的铁还原是很难避免的,对熔炼过程无多大妨碍。但当还原气氛强时,则固体铁作为独立相析出,从而影响熔炼的顺利进行。
此反应式为吸热反应,故此带温度降至1200-1300度。
炉缸区
包括风口以下至炉缸底部,其温度上部为1200 ~ 1300℃,下部为1000~1100℃,深度为0.8 ~ 1.3米。过热后的各种熔融液体,流入炉缸按比重分层。由于铅的比重(约10.5)最大,故沉于缸底;其上层为砷冰铜(比重6 ~ 7);再上层为铅冰铜(比重4.1 ~ 5.5),最上层为炉渣(比重3.3 ~ 3.6)。
SiO2-FeO-CaO三元系炉渣
在有色金属硫化精矿原料中,杂质金属含量较多的是铁。精矿中的硫化铁经氧化脱硫和高价氧化铁还原形成相对稳定的低价铁氧化物—氧化亚铁(FeO)进入炉渣,成为炉渣的主要组成之一。 FeO是一种碱性氧化物,熔点1370℃,它与酸性氧化物—二氧化硅(SiO2,熔点1713 ℃ )结合形成稳定的的铁硅酸盐,如铁橄榄石(2FeO· SiO2),熔点1205 ℃,因此火法炼铅一般都添加石英石作熔剂,以补充铅精矿原料中SiO2成分的不足。
重金属冶金学--铅冶金--铅烧结矿的鼓风炉还原熔炼
10
3、还原反应反应热力学
1)金属氧化物CO还原(间接还原)
在铅的还原熔炼过程中,炉料所 含的各种物质都参与如下反应。 MeO=Me+1/2O2 CO+1/2O2=CO2 MeO+CO=Me+CO2 (3-1) (3-2) (3-3)
由式(1)与式(2)得式(3): 不同温度下各种金属氧化物还原反 应平衡的pCO/pCO2比较见图3-2。 由图可见,在1000℃时金属氧化 物还原的先后顺序是: Cu2O、PbO、NiO、CdO、SnO2、 Fe3O4、FeO、ZnO、Cr2O3、MnO。
18
在有碱性氧化物FeO和 CaO参与下,铅的氧化物 被还原的顺序为PbO·SiO2、 PbO、2PbO·SiO2,其中 PbO·SiO2最易被还原。 由于CaO与SiO2形成多 种硅酸盐,所以在配料时 CaO:SiO2的比值对还原反 应进行的程度有很大关系。 (生成 3CaO·SiO2 的△G 最负)
第 三 节
铅烧结矿的鼓风炉还原熔炼
一、概述 1、鼓风炉还原熔炼目的
使铅的氧化物还原,并与贵金属和铋等聚集进入粗铅,而 使各种造渣成分(包括SiO2、CaO、FeO、Fe3O4等)及锌等进 入炉渣,以达到相互分离。
1
1、鼓风炉还原熔炼目的
目的:使铅的氧化物还原,并与贵金属和铋等聚集进入粗 铅,而使各种造渣成分(包括SiO2、CaO、FeO、Fe3O4等)及 锌等进入炉渣,以达到相互分离。 当原料含铜较高时,可产出铅冰铜将铜富集;若原料含铜 不太高,可将铜富集于粗铅中,此时铜在炉渣中的损失将稍大。
21
22
5、铅烧结块中其他组分在还原熔炼中的行为
• 铅烧结块中除含主金属铅和主要杂质金属铁的化合物之外,还含 有锌、铜、砷、锑、铋、镉等氧化物,它们在熔炼中的行为分别 叙述如下:
- 1、下载文档前请自行甄别文档内容的完整性,平台不提供额外的编辑、内容补充、找答案等附加服务。
- 2、"仅部分预览"的文档,不可在线预览部分如存在完整性等问题,可反馈申请退款(可完整预览的文档不适用该条件!)。
- 3、如文档侵犯您的权益,请联系客服反馈,我们会尽快为您处理(人工客服工作时间:9:00-18:30)。
lgKp=3250/T+0.417×10-3T+0.3
表4-6
由表可知:还原所需CO浓度不大,低于1000℃,为万分之几至千分之几,高 于1000℃为3%~5%。不管固体氧化铅还是液体氧化铅都易还原。T高,所需
➢ 被还原金属以MO或硅酸盐、铁酸盐等形态存在;还原过程既有气固反应,又 有液固反应。
➢ 产出液态金属。对沸点低的金属(如锌)则以气态产出,再冷凝为液态;
➢ 鼓风炉中,焦炭为燃料和还原剂。在强还原气氛与提供过程所需热量间,存
在矛盾。密闭鼓风炉炼铅锌,通过预热鼓风使这一问题得到解决。
A
1
表4-1
A
2
表4-8 复杂铅氧化物用CO还原时平衡气相中CO含量
ቤተ መጻሕፍቲ ባይዱ
组成见表4-2、表4-3.
烧结块化学成分:含铅40%~50%,含硫率视块中铜、锌含量而定。含锌高
时,应进行死烧,彻底脱硫;含铜高于1.5%,则应留少量的硫;若含铜、锌 都
高时,先进行死烧,在鼓风炉熔炼时,则加入少量黄铁矿使铜硫化而造锍。
FeO、SiO2、CaO、MgO、Al2O3等成分应符合选定的渣型。烧结块物相分 析实例
PCO2/PbO.XPbO.PCO = K =425 (1473K, aPb=1) XPbO = PCO2/ PCO .PbO.425
其中PbO 作为碱性较强的氧化物,在铁硅酸盐炉渣中的活度系数被认为是0.3,
计算PCO2/PCO与 XPbO和wpb(炉渣中铅的百分含量)的关系如表4-8
A
11
表4-7 还原气氛对炼铅渣渣含铅的影响
3
4.4 鼓风炉炼铅
4.4.1 铅烧结块鼓风炉还原熔炼的目的
烧结焙烧得到的铅烧结块中的铅主要以PbO(包括结合态的硅酸铅和铁酸铅) 和少量的PbS、金属Pb及PbSO4形态存在,此外还含有伴存的Cu、Zn、Bi等
有价金属和贵金属Ag、Au以及一些脉石氧化物。
➢ 最大限度地将烧结块中的铅还原出来获得金属铅,同时将Au、Ag、 Bi等贵 金属富集其中;
4.2 还原熔炼的原理与反应
图4-1
A
➢ 位于CO-CO2线上方的氧化 物易还原,贵金属、铜等进 入粗铅;
➢ SiO2,CaO,Al2O3等不会被还 原,进入炉渣;
➢ ZnO在1500K以内,比FeO 难还原,进入炉渣;
➢ 应控制还原条件,使FeO进 入炉渣,而不被还原为金属 铁;
➢ As, Sb, Bi部分以低价氧化物 挥发,部分被还原进入粗铅。
➢ 将铜还原进入粗铅;若烧结块中含Cu、S 都高时,则使铜呈Cu2S形态进入 铅锍(俗称铅冰铜)中,以便下一步回收;
➢ 如果炉料中含有Ni、Co时,使其还原进入黄渣(俗称砷冰铜);
➢ 将烧结块中一些易挥发的有价金属化合物(CdO)富集于烟尘中,便于进一 步综合回收;
➢ 使脉石成分(SiO2、FeO、CaO、MgO、Al2O3)造渣,锌也以ZnO形态入渣,
便于回收。
A
4
4.4.2 铅鼓风炉炉料组成与熔炼过程发生的主要过程
物料:炉料和燃料。炉料的主要组成是自熔烧结块(占90%~100%);熔
剂在烧结就配好了。其它炉料有返料、铁屑、萤石、石英块(烧结块残硫高、
熔炼炉渣渣型改变以及炉况不正常时可添加)等。燃料为焦炭,为炉料的
9%~14%。焦炭既是燃料也是还原剂。国内外各炼铅厂烧结块成分及鼓风炉炉 料
A
8
4.4.2 熔炼过程发生的主要过程
➢ 碳质燃料燃烧; ➢ 金属氧化物还原; ➢ 脉石及氧化锌成分造渣等过程; ➢ 可能还发生硫化物形成锍、砷化物形成黄渣过程; ➢ 上述熔体产物的沉淀分离过程
A
9
4.4.3 铅鼓风炉还原熔炼的理论基础
➢ 氧化铅还原热力学 (根据炉内上下区域温度)
327℃ :PbO(s)+CO=Pb(s)+CO2+63625J 327~883℃:PbO(s)+CO=Pb(l)+CO2+58183J
CO 浓度也越大。PbO被C直接还原反应为:
为Pb吸O热+反C应=,Pb在+4C0O0~-590005℃81时.8已4J较为A显著,在700℃时,则强烈进行。10
4.4.3 铅鼓风炉还原熔炼的理论基础
➢ 复杂铅氧化物(PbO•SiO2)还原的热力学
PbO.SiO2(晶体)+CO=Pb(液)+SiO2(无定形)+CO2 2PbO.SiO2(晶体)+2CO=2Pb(液)+SiO2(无定形)+2CO2
A
7
表45
对焦炭的质量要求: ①高热值, 保证化学反应过程和熔炼过程进行; ②高着火温度, 避免在炉子上部发生过早的燃烧; ③适当孔隙率,提高透气性,促进空气与炉气在料柱中均匀分布; ④足够的机械强度, 防止在炉子下部被压碎或磨碎; ⑤少量灰分和水分。
某厂具体要求:固定碳75%~80%,灰分小于16%;发热值25~ 29MJ/kg;着火温度600~800℃,孔隙率40%~50%;抗压强度大于 7.0MPa;块度50~100mm。
如表4-4。
块度:50~120mm,小于50mm和大于120mm的不大于25%;空隙度:
不小于
A
5
50%~60%;强度:烧结块的转鼓率为28%~40%,或从1.5m高处三次自
4-2
A
6
4-3
鼓风炉中一般不加返渣(占用炉子生产能力,增加焦炭的消耗)。铁、硅、钙熔剂 和萤石应严格拒绝入炉,只作炉况不好,渣型变化时临时措施之用。
第4章 还原熔炼的基本原理
4.1 概述 铅锌锡锑铋等重金属的还原熔炼是以氧化矿或硫化矿的焙烧产物为原料,以碳
质还原剂兼作燃料,在高温炉内进行熔融和还原冶炼,呈液态(气态冷凝后)产 出金属,同时使脉石和杂质形成炉渣被分离出去。还原熔炼(MO(包括金属硅 酸盐、铁酸盐等)还原为M)的主要特征为:
➢ 还原剂均为固体碳质还原剂。高温下,实际为CO。碳的气化反应(布多尔反 应,波—贝反应)。
硅酸铅( (XPbO•ySiO2) )是烧结块中最多的一种结合态氧化铅,熔化温度
为720-800℃, 熔融后的硅酸铅还原反应进行的程度是降低鼓风炉渣含铅的关键。 还原反应进行的极限以氧化物形态残留在炉渣中的金属铅量,按如下反应进行:
PbO(熔渣) + CO = Pb(l) + CO2
Gθ = -87320 + 8.95T(J)