博世流程设计-价值流图析
价值流程图概述(2021整理)

价值流程图(ValueStreamMapping,简称VSM)价值流程图概述价值流程图〔ValueStreamMapping〕是丰田精益制造〔LeanManufacturing〕生产系统框架下的一种用来描述物流和信息流的形象化工具。
它运用精益制造的工具和技术来关怀企业理解和精简生产流程。
价值流程图的目的是为了辨识和减少生产过程中的白费。
白费在那个地点被定义为不能够为终端产品提供增值的任何活动,并经常用于讲明生产过程中所减少的“白费〞总量。
VSM能够作为治理人员、工程师、生产制造人员、流程人员、需求商以及顾客发现白费、寻寻白费根源的起点。
从这点来讲,VSM依旧一项沟通工具。
然而,VSM往往被用作战略工具、变更治理工具。
VSM通过形象化地描述生产过程中的物流和信息流,来到达上述工具目的。
从原材料购进的那一刻起,VSM就开始工作了,它贯穿于生产制造的所有流程、步骤,直到终端产品离开仓储。
对生产制造过程中的周期时刻、当机时刻、在制品库存、原材料流淌、信息流淌等情况进行描摹和记录,有助于形象化当前流程的活动状态,并有利于对生产流程进行指导,朝向理想化方向开展。
VSM通常包括对“当前状态〞和“今后状态〞两个状态的描摹,从而作为精益制造战略的根底。
价值流程图〔VSM〕分析的是两个流程:第一个是信息〔情报〕流程,即从市场部接到客户订单或市场部推测客户的需求开始,到使之变成采购方案和生产方案的过程;第二个是实物流程,即从需求商需求原材料进库开始,随后出库制造、成品进库、产品出库,直至产品送达客户手中的过程。
此外,实物流程中还包括产品的检验、停放等环节。
企业在进行价值流程图〔VSM〕分析时,首先要选择出典型的产品作为深进调查分析的对象,从而绘制出信息〔情报〕流程和实物流程的现状图,然后将现状图与信息〔情报〕和实物流程的理想状况图相比立,发现当前组织生产过程中存在的咨询题点,进而针对咨询题点提出革新措施。
价值流程图的历史1980年代,丰田公司的首席工程师TaiichiOhno与senseiShigeoShingo领先运用往除生产白费的方法来猎取竞争优势,他们的要紧动身点是提高生产效率,而非提高产品质量。
价值流图分析法
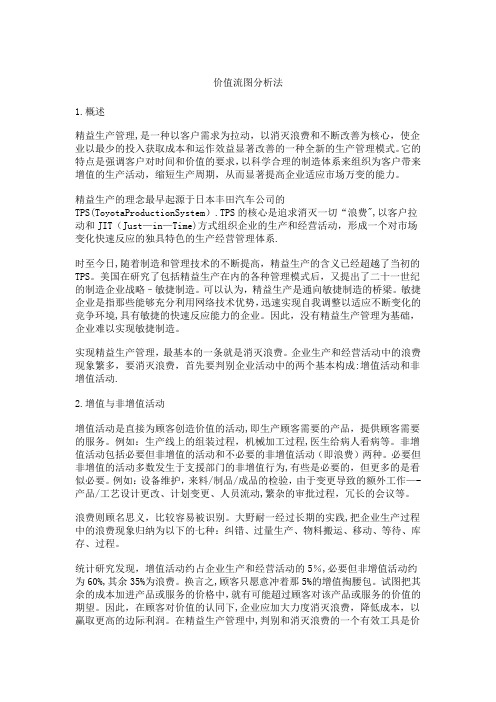
价值流图分析法1.概述精益生产管理,是一种以客户需求为拉动,以消灭浪费和不断改善为核心,使企业以最少的投入获取成本和运作效益显著改善的一种全新的生产管理模式。
它的特点是强调客户对时间和价值的要求,以科学合理的制造体系来组织为客户带来增值的生产活动,缩短生产周期,从而显著提高企业适应市场万变的能力。
精益生产的理念最早起源于日本丰田汽车公司的TPS(ToyotaProductionSystem).TPS的核心是追求消灭一切“浪费",以客户拉动和JIT(Just—in—Time)方式组织企业的生产和经营活动,形成一个对市场变化快速反应的独具特色的生产经营管理体系.时至今日,随着制造和管理技术的不断提高,精益生产的含义已经超越了当初的TPS。
美国在研究了包括精益生产在内的各种管理模式后,又提出了二十一世纪的制造企业战略–敏捷制造。
可以认为,精益生产是通向敏捷制造的桥梁。
敏捷企业是指那些能够充分利用网络技术优势,迅速实现自我调整以适应不断变化的竞争环境,具有敏捷的快速反应能力的企业。
因此,没有精益生产管理为基础,企业难以实现敏捷制造。
实现精益生产管理,最基本的一条就是消灭浪费。
企业生产和经营活动中的浪费现象繁多,要消灭浪费,首先要判别企业活动中的两个基本构成:增值活动和非增值活动.2.增值与非增值活动增值活动是直接为顾客创造价值的活动,即生产顾客需要的产品,提供顾客需要的服务。
例如:生产线上的组装过程,机械加工过程,医生给病人看病等。
非增值活动包括必要但非增值的活动和不必要的非增值活动(即浪费)两种。
必要但非增值的活动多数发生于支援部门的非增值行为,有些是必要的,但更多的是看似必要。
例如:设备维护,来料/制品/成品的检验,由于变更导致的额外工作—-产品/工艺设计更改、计划变更、人员流动,繁杂的审批过程,冗长的会议等。
浪费则顾名思义,比较容易被识别。
大野耐一经过长期的实践,把企业生产过程中的浪费现象归纳为以下的七种:纠错、过量生产、物料搬运、移动、等待、库存、过程。
解释价值流图及价值流分析课件

•
每天都是美好的一天,新的一天开启 。20.11.820.11.807:4107:41:4707:41:47Nov- 20
•
人生不是自发的自我发展,而是一长 串机缘 。事件 和决定 ,这些 机缘、 事件和 决定在 它们实 现的当 时是取 决于我 们的意 志的。2020年11月8日 星期日 7时41分47秒 Sunday, November 08, 2020
如下图所示
建立精益化的物流的关键是理解信息是怎样流动的!
生产控 制中心
每周一次
每日一次
A
每日一次
生产主任
每日一次
B
C
1000
1000
880
目前状态图形中的这一部分表明,生产控制中心每周一
次将客户需求信息传递给生产主任,生产主任每日一次将需
求信息传递给价值流上的每一个部分。
6、几种常见价值流图形的图标
产品-路径分析揭示出了一些重要的实际情况:
• #4和#6产品具有相同的加工路径,而#8和#10 产品的加工路径略有不同。
• #4和#6产品的加工路径比#8和#10产品的加工 路径的复杂程度略低一些。
• #4和#6产品的总产量占考得联合公司产品总产量 的80%。
公司产品-路径分析(按加工过程分类)
产量 部件 机加工 去毛刺 弯曲 20160 #4 10080 #6
4360 #8 3200 #10
焊接
检查
打标记
第三步:
工作团队制定了一个培训计划,并在6个星期的 时间内学习了有关精益化生产所使用的工具和方法。
6月25日,团队全体成员参加了本公司的精益 化生产方式综述内容的学习,为期4天;6月30日, 5名队员走访一家精益化生产成功的标杆企业;7月 30日完成报告。
价值流图分析法解读

价值流图(Value Stream Mapping)
价值流图(Value Stream Mapping)
是:
• 让所有人看见整体情 况 • 根据真实数据 • • 根据工程标准或旧数据 • 一年一次的大计划
结构车间转台线目前工序流程图
优点: 1.反映出工序周期 2.工艺流程 3.车间或一条线在制品的 流转
• 前置期(Lead Time)
--物料流过整条价值流所需的时间
绘画价值流图- 基本图示
工序名称
加工时间:15S 转款时间:1hr
I
库存 手动资讯 电子资讯
Kaizen Burst
供应商/客户
生产过程
作业人员
FIFO
货车运送 推动物料 送产品到客户 先入先出
改善标志
提取物料
超市
缓存/备用 库存
生产看板
『精益管理』的常用工具
企业生产指标 (key Performance lndicators)
需求带动系统/看板 (Pull System/Kanban) 源头质管 (Qualiy Source) 标准化系统 (Standardization) 全面设备维护 (TPM) 防错系统 (Poka Yoke) 实验设计系统 (Design of Experiment) 厂房布局 (Layout) 单件流/单元式生产 (One-piece-flow/Cell Manufacturing) 快速换模系统 (SMED) 建议系统 (Suggestion System) 目视管理系统 (Visual Management)
为什么采用价值流图?
目视
• 整体流程目视化,而不仅仅是单件单 件流 • 从顾客角度看待流程(外部顾客) • 上游对下游工序的影响(内部顾客) • 便于识别流程中浪费 • 显示物料和信息流之间的联系 • 将不同部门或智能的问题联系在一起
价值和价值流程图

— 31 —
如何理解价值流图:
是:
让所有人看见整体情况 根据真实数据 改善的蓝图 持续改善的依据
不是:
流程图 根据工程标准或旧数
据 一年一次的大计划
— 32 —
什么是价值流图分析:
— 33 —
价值流图分析:先对运作过程中的现状进行分析,即对“当前状态图”进行分 析,从顾客一端开始,首先了解顾客的需求情况和节拍,然后研究运作流程中的每 一道工序,从下游追溯到上游,直至供应商。分析每个工序的增值和非增值活动, 包括准备、加工、库存、物料的转移方法等,记录对应的时间,了解分析物流信息 传递的路径和方法,然后根据分析情况来判别和确定出浪费所在及其原因,为消灭 浪费和持续改善提供目标。最后根据企业的实际情况,设计出新的价值流程,为未 来的运作指明方向。
奥通门封供应商
■ 流程信息 ■ 客户/供应商
OXOX
■ 均衡生产
■ 生产计划
单件工时(S):1680 设备数量:1 设备故障率(%):2 换模时间(min): 一次合格率:88% 搬运距离(m):1 转运批量(件):1 在制品(待加工):80 在制品(已加工):1 其它有用信息:
■ 数据表 ■ 操作工
价值简介:
下面的情况那些是增值的?
— 18 —
价值简介:
统计研究发现,企业生产活动中增值和非增值活动的比重如下:
浪不费增值
增值
必要非增值
— 19 —
增值 5%
不增值 35%
必要非增值 60%
目录
— 20 —
1、价值简介 2、价值流及价值流图简介 3、价值流图的绘制 4、价值流图分析
企业如何获取利润:
— 38 —
价值流图符号及意义:物流
价值流图析(佟)
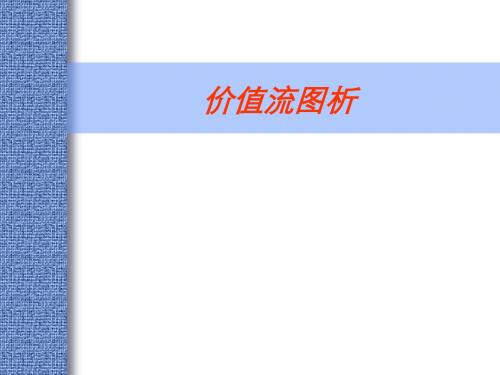
价值流图析
产品系列
现状图 通过划出材料和信息流搞清 生产现状
现状图
未来状态图
工作计划
价值流图析 – 绘制现状图
用图标来表示过程和流动,符号在公司内保持一致,使 每个人都绘画并理解你将要实施精益生产的图表
过程水平 单个车间 多个车间 包含整个公司
价值流图析 -- 材料流图标
总装
XYZ
生产时间=45s 换模时间=30min 3 班 2%废品率
价值流图析价值流图析 Nhomakorabea起步价值流图析-- 起步
何为价值流图析 材料流和信息流 价值流经理 使用图析工具 选择一个产品系列
价值流图析-- 起步
价值流是当前产品通过其基本生产过程所要求的全部活 动(包括增值和不增值活动) 从原材料到产品到顾客手中的生产流 从概念到投产的设计流 本手册照眼于为精益生产相关联的从顾客要求追溯到原 材料的生产流
公司
工
每天300件
生产过程
周一 周三
外部供应商
数据箱
库存
最大20件
FIFO 货车运送 推动箭头
提供顾客合格品 先进先出顺序流动
换模具
强调改进标志 缓存或备用储存 操作工
物理拉动
价值流图析 -- 信息流图标
每周 计划
手动信息流 电子信息流 计划 负荷平衡盒
OXOX
20
去掉看板
生产看板
看板符号
看板位置
价值流图析-- 起步
进行价值流分析意味着对全过程进行研究,而不是单个 过程 改进全过程,而不是仅仅优化局部
本书阐述 供应商
你的工厂或公司
整个价值流
顾客及最终使用者
价值流图析 -- 何为价值流图析
价值流图分析
总之,永远站在客户立场上看待我们的工作价 值。谁对我们的工作进行最终评判和衡量,谁就是 我们的客户。
客户—我们从事一切生产经营活动并进行改善的最根本的出发点和落脚点
路漫漫其悠远
价值流图基本概述
价值流:是为满足客户要求,当前产品(不论是一个商品、一项服务,或两者 的 结合)通过其基本生产过程所必须的全部活动。包括从供应商处 购买的原材料到达企业,企业对其进行加工后转变为成品再交付客户 的全过程。企业内以及企业与供应商、客户之间的信息沟通形成的信 息流也是价值流的一部分。
价值流图的基本构成有四大部分: • 顾客部分。顾客发出信息,可能是订单,新产品,等等; • 公司系统部分。可能是ERP, SAP任何系统,顾客信息进入公司系统; • 供应商部分。 • 内部物料流。主要指产线部分,至少需要人机料(Man, Machine, Material)
价值流图关注的重点部分: • 原材料到成品整个制程、工艺上的信息; • 成品到顾客; • 关注信息流部分。顾客—〉公司系统〈--供应商 • 计算L/Time, 同时包含VA(有价值),NVA(无价值)部分及有价值比例。
一个产品以下两条流程至关重要:(价值流图析的主要过程) • 从原材料到产品交到客户手中的生产流程。(物流) • 从概念到投产的设计流程。(信息流)
一个产品通过这些主要流程所需要的全部活动:增值和非增值活动 • 增值活动:真正能创造出顾客可以接受的价值的行动。 • 非增值活动:
– 必要但不创造价值(减少)。 如目前产品开发、补充订货、生产系统还需要,因而不能马上取消的活动。为了消
通常我们首先按照80—20原则,对影响企业最大的产品进行图析。 3. When——确定何时做(正确选择确定物流)
价值流程图分析
.
18
制造循环
换模时间? 每个流程机器数量? WIP 质量 流程浪费 两个流程之间的距离 生产柔性
.
19
信息流
生产和采购指令的下达? 给谁 频率 产生流程
购买指令的产生和修正,MRP管理那部分生产循环?
.
20
VSM现状-前导期时间数据柱状图
前导期时间数据
• 获得生产前导时间 • 获得生产加工时间 (标准时间) • 将关键路径上的生产前导时间相加 • 增值比率为总生产加工时间除以总前导时间
CT = 60 min
CT = 1.2 min
CT = 40.3 min
45
1
2
2
1
5
1
1.6
0.9
0.9
60ห้องสมุดไป่ตู้
1.2
40.3
Total = 57 Days Total = 1 Hr. 44.9 Min.
VSM第一步 – 走完全部流程
.
25
收集数据
.
26
贴到墙上
.
27
完成现状图
.
28
计算 OEE
流程名 标准时间 (C/T) 换模时间 (C/O) 设备综合效率(OEE)
其他可能用到的数据信息
包装容量
工作时间 (休息除外)
废品率
产品型号数量
缓冲量
.
13
价值流程图分析构成
30 Days
Supplier
Supplier Loop
Bi-Monthly
MRP
Monthly Orders 880
= OEE
Availability × Performance × Quality
价值流图技术PPT课件
I
I
I
I
3500
1500
1850
2300
I
200t
仓库
3.2.4识别价值流中的增值与非增值时间
增值活动(VA)
无效活动(NVA)
定义:任何符合客户需求的动作、服务、材料变化
定义:任何不符合客户需求的工作、服务、材料变化。所有可以被取消、简化、降低、合并的动作。
先进先出料道
Max 80 pcs.
5.2规划将来状况应考虑的要点
5.2.5 在所有工序中,瓶颈在什么地方?选定何处作为生产控制节拍?
1.2价值流图分析的作用
分析系统整体存在的问题,具有看到宏观生产流程的能力 帮助发现浪费源 展示了信息流与物流之间的联系 广泛沟通的工具 确定优先次序 结合精益的概念与技术…避免“只挑容易的” 来改进难 形成实施计划的基础 建立起确定改善目标的数据基础
组装1
C/T:35S C/O:0min Oper:1 Uptime:100% Shifts:25,600s 2%Scrap
发货
I
I
I
I
3500
1500
1850
2300
I
200t
天
35S
25.8天
天
天
2.0
8.3
148S
48S
60S
天
3.5
5S
天
4.5
7.5
仓库
3.2.7当前状况图示
XX钢铁厂
每种产品都应有价值流图---全面了解浪费情况
小批多品种绘减值流图较难---运用产品分族矩阵分类
3.1.1产品分族矩阵
工艺顺序、关键设备或工序
工序1
价值流程图(VSM)案例分析详解
主要内容
一、价值流概念 二、价值流程图 三、价值流程图案例分析
一、价值流的概念
价值流是制造产品所需一切活动的总和,包含了增 值活动和不增值活动。 使用价值流分析意味着对全过程进行研究,而不 只是研究单个过程;改进全过程,而不是仅仅优化局 部。 据统计,增值活动约占企业生产和经营活动的5%, 不增值活动约占95%。因此,应在价值流中识别不增 值活动,通过持续不断地开展价值流改进,消除各种 浪费,降低成本。 价值流改进重点在于物流和信息流。
设备布置也应作相应调整,具体布置如图所示
未来价值流程图
需要注意的是,由于钻孔、精车抛光、检验三道工序是2个 人在U形生产线中完成的,如采用逐兔式完成,因此每人115s完 成三道工序的生产即115s共完成两个工件的加工,同时粗车工 人120s完成两个毛坯加工,因此相当于U形生产线中57.5s完成 一个零件的加工。因此,图3-2中后面三道工序的加工周期标注 57.5s。 同时,我可以看出,依照新的方案安排生产,生产提前期可 减小到0.5天,比原来减少了66.67%((1.5-0.5)/1.5x100%) 。同时可实现流水线下的拉式生产,在制品库存也可明显减少 ,对装配车间的需求响应将更加的迅速准确。此外生产线平衡 率大大提高
价值流程图分析特征
价值流程图分析以客户的观点分析现有价值流程图 每一个活动的必要性,画出期待的价值流的未来状态 图,并制定实施计划。 (1)绘制出并简单显示出物流和信息流 (2)揭示产生浪费的原因 (3)创建一个改善的价值流 (4)创建和协调一个跨部门团队方法
价值流程图分析的好处
(1)目视化工具 (2)信息沟通方式 (3)有利于发现存在的问题 (4)创建一个改善的价值流
二、价值流程图
- 1、下载文档前请自行甄别文档内容的完整性,平台不提供额外的编辑、内容补充、找答案等附加服务。
- 2、"仅部分预览"的文档,不可在线预览部分如存在完整性等问题,可反馈申请退款(可完整预览的文档不适用该条件!)。
- 3、如文档侵犯您的权益,请联系客服反馈,我们会尽快为您处理(人工客服工作时间:9:00-18:30)。
2,2 d
4
8.309 23.972 KAIZEN and GEMBAKAIZEN
are the trademarks of KAIZEN Institute
LICB 产品族 当前状态图 – 关键业绩指标
6 Month weekly Rolling Forecasts Suppliers UK: 9 Others: 80 Fixed Orders (1 time/week) CLP2 (MRP System) CLP1 Long Term Planning SAP 6 Month Daily Rolling Forecasts Customers Fixed Orders • 没有足够的产 出来满足需求 CLP1 Despatch Order Volumes: LICB 2007: 10.864/d; LICB 2008: 5.221/d; LIX 2007: 8.398/d; LIX 2008: 10.040/d; 3d
Rotor Intermediate
WIP Rotor Rotor Winding
Break Times 12 37Ext Other Parts 90 11 Total Breakdown 137 32 103 308 3 Type Change Loss 90 21 34 73 TPM 40 26 27 11 Ext Small Parts 9 PPM 31 47 415 3 14 10 In Line Rework 30 d 12 3 9 Low Volume Line 11,3 182 In Line Scrap 12 0 0 2 Output/h: A Batch size: 1 Productivity: 8,3 (parts/manhour) Material Shortage (CLP)Regulator 6 6 Regulator 0 1 Daily Lost Time: 33% Unplanned Work (Parts processed 5 but 0 no O/P recorded 0 47 2,8 Material Shortage (Subassembly) 5d 0 0 0 A Service Failure (Air, Electricity, 1 etc) 0 0 0 Rectifier Process Set Ups (Not Type 1Change) 0 Rectifier 0 0 3 Material Defect 0 0 0 0 6 2,8 d Training 0 0 0 3 A 4 Meetings 0 0 110 5 16 45 Stator Stator High Volume Line Kan Ban Full 0 0 0 0 Output/h: 480 EOL Scrap 0d 0 2 3Batch Size: 500 2,8 Productivity: 15,5 (parts/manhour) A EOL Rework 0 0 13 12 Lost Time: 33% Daily
Finishing
成品库存管理+批量和 包装数据
Units sec min Internal parts Suppliers parts Storage min/day % %
11,3min/day d
Regulator
CLP1 • 时间计划表完 Despatch Order 成低 (不合格 ). 线边超市
LICB 产品族 当前状态图
6个月的每周滚动预测 供应商 英国: 9 其它: 80 固定订单(1 次/周) 早期报警列表
日依据
CLP2 (物料需求计划系统)
CLP1 长期计划SAP Bosch EVA 订单进入
6个月日滚动预测 客户 固定订单
容量: LICB 2007: 10.864/d; LICB 2008: 5.221/d; LIX 2007: 8.398/d; LIX 2008: 10.040/d;
风扇(再包装) 铜线轴 爪极... 重的 30 分钟 子装配 整流器 A 整流器 整流器
3 6
2 码头
成品 15 min 成品仓库: 11层分极零部件 频率: 丰田: 3天 宝马/DC: 1 天 大众: 2周
2,8 d 铸件: PVB: 6,7 d, CONS: 3,6 d GE + SP Daily, IT + TU Wkly Del. 帽子: PVB: 4 d, UK bi-Daily Del. 滑轮: PVB: 7 d (4 Obs) , CONS: 4 d GE + SP Daily, CA + UK Wkly Del.
Continous Loop F. Assys
K
Small 60 min Subs+F.Assys
Daily/ Weekly
External Components
P
Fans (repack) Cooper Wire Shafts Claw poles ...
Heavy 30 min Subs
Average of Average of Average of Average of Average of Average of Average of Average of Regulator Average of Average of Average of Average Rectifierof Average of Average of Average of Stator Average of Average of Average of
• 拉式流愿景 – 生产线概念的演变;
• 拉式流愿景 – 图; • 拉式流愿景 – 建议; • 拉式流愿景 – 改善分项目; • 推进计划; • 目标和收益; • 投资;
• 成本收益概要;
• 附录 – 超市规模.
2
KAIZEN and GEMBAKAIZEN are the trademarks of KAIZEN Institute
min/day min/day 2,8 min/day d A min/day Rectifier min/day min/day 2,8 d min/day A min/day Stator min/day
2,8 d
A
调节器
低容量生产线 产出/小时: 182 批量: 1 生产力: 7,2 (件/人小时) 日损失时间: 47%
21 天
3
LICB 产品族 当前状态图 – 关键业绩指标
6个月每周滚动预测 供应商 英国: 9 其它: 80 固定订单 (1 次/周) 早期报警列表
日依据
CLP2 (物料需求计划系统)
CLP1 长期计划SAP Bosch EVA 订单进入
6个月日滚动预测
• LICB 2007 节拍: 4,6 秒 (OT: 14 小时); • LICB 2008 节拍: 9,6 Customers 秒 (OT: 14 小时 ); 固定订单
Jan to Sep 2007 Data
LICB LVL 12 480 1.264 158 253 53% 47% 49 55 34 Regulator 7 26 15 Rectifier 0 16 1 Stator 15 7,2 22 Rotor
Intermediate
LIX HVL 10,6 1.216 4.495 222 794 65% 35% 63 154 53 35 52 26 3 12 48 17 7,9 28 LVL 19,8 854 1.743 122 575 67% 33% 87 68 20 31 34 1 0 18 9 11 7,7 16 Rotor
5 3 14
3
每天/每周
外部零件
9
11,3 d
P
调整器 调整器
A 调整器
低容量生产线 产出/小时: 182 批量: 1 生产力: 7,2 (件/人小时) 日损失时间: 47%
10.121/d
服务水平(OTIF准时完全): 2005: 94%; 2006: 93%; 2007: 90%.
2,2 d
3
2,8 d
卡迪夫,起动机和发电机
起动机和发电机
拉式流系统项目
计划阶段-价值流图析
卡迪夫,2007年10月 8-12 日
1
KAIZEN and GEMBAKAIZEN are the trademarks of KAIZEN Institute
拉式系统项目,计划阶段 检索
• 当前状态图 • 当前状态图 – 关键业绩指标; • 当前状态图 – 浪费,不均衡,超负荷;
10.121/d
服务水平(OTIF准时完全): 2005: 94%; 2006: 93%; 2007: 90%.
2,2 天
3
2 码头
FG 15 min 成品仓库: 11层分极零部件 Freq:
整流器
3 6
定子
10
5
16
4
A parts/manhour Rotor 转子
WIP Rotor
大容量生产线 产出/小时: 480 批量: 500 生产力: 15,5 (件/人小时) 日损失时间: 33%
Daily/ Weekly Break Times
Components
738 K 67% Small 60 min 33%
Subs+F.Assys
1.019.900 磅 (6月 – 8月).
外部小零件
5 3 14
9
127 P Total Breakdown 47 Type Change Loss 40 Material Shortage (Subassembly) 38 Heavy 3035 min In Line Rework Fans (repack) Subs Cooper Wire TPM 25 Shafts PPM 19 Claw poles ... Material Shortage (CLP) 16 Material Defect 10 Others 10 Productivity # Operators 15,5 31WIP Rotor