液化天然气储罐结构与建造
lng储罐施工方案
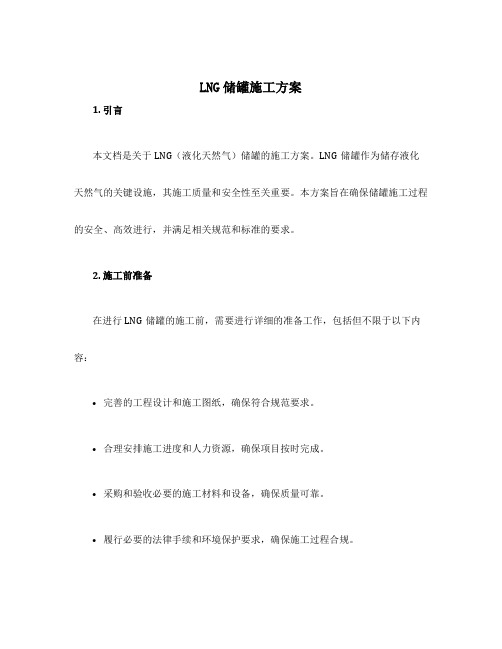
LNG储罐施工方案1. 引言本文档是关于LNG(液化天然气)储罐的施工方案。
LNG储罐作为储存液化天然气的关键设施,其施工质量和安全性至关重要。
本方案旨在确保储罐施工过程的安全、高效进行,并满足相关规范和标准的要求。
2. 施工前准备在进行LNG储罐的施工前,需要进行详细的准备工作,包括但不限于以下内容:•完善的工程设计和施工图纸,确保符合规范要求。
•合理安排施工进度和人力资源,确保项目按时完成。
•采购和验收必要的施工材料和设备,确保质量可靠。
•履行必要的法律手续和环境保护要求,确保施工过程合规。
3. 基础与地基处理LNG储罐的基础与地基处理是保证储罐稳定性和安全性的重要环节。
在进行基础与地基处理时,需参考相关设计标准,并采取以下措施:•清理施工区域,确保地表舒适。
•基坑开挖,按照设计要求进行挖掘和处理。
•填筑基础与地基,采用高强度混凝土,按层压实。
4. 储罐结构施工储罐结构施工是LNG储罐施工的核心环节。
在进行储罐结构施工时,需要严格遵循相关标准和规范,并采取以下步骤:4.1 薄层铺设•按照设计要求,进行初期薄层铺设。
•使用专用的防渗漏薄层材料,确保储罐内部液体的密封性。
•进行薄层的平整和固化,以提高储罐的结构稳定性。
4.2 壁板安装•使用预制的壁板进行安装,确保尺寸和质量的一致性。
•使用专业的安装设备进行壁板的悬挂和定位。
•进行壁板的焊接和密封处理,以确保储罐的密封性和强度。
4.3 屋盖安装•安装储罐的屋盖结构,使用预制的屋盖板进行安装。
•进行屋盖板的焊接和密封处理,以确保储罐的密封性和结构安全性。
4.4 罐底施工•进行储罐底板的铺设,使用预制的底板进行安装。
•进行底板的焊接和密封处理,以确保储罐的底部密封性和稳定性。
5. 现场安全与质量控制在整个LNG储罐施工过程中,安全和质量控制是至关重要的。
为确保施工的安全和质量,需要采取以下措施:•建立并执行严格的施工安全管理制度,包括安全培训和安全检查等。
LNG液化天然气储罐
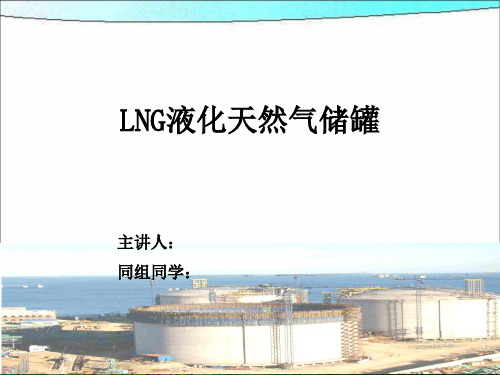
主讲人: 同组同学:
主要内容
• 一、LNG简介 • 二、LNG储罐分类及常见的结构 • 三、常见的事故及预防措施
一、LNG简介
• 1.LNG(liquefied natural gas)的定义:
• 《液化天然气的一般特性》(GB/T19204-2003):
•
LNG(液化天然气)是以甲烷为主要组分的烃类混
气化器组成的自动增压系统来完成的。当罐内压力低于自
动增压器的设定值时,调压器打开,罐内液体靠液位差缓 缓流入增压气化器,液体气化产生的气体流经调压器和气
相管补充到储罐内。气体的不断补充使得罐内压力回升, 当压力回升到调压器设定值以上时,调压器关闭。这时,
增压气化器内的压力会阻止液体的继续流入,增压过程结
束。
•减压:(超压保护)
•
LNG在储存过程中会由于储罐的环境漏热而缓慢
蒸发,导致储罐的压力逐步升高,最终危及储罐安全。
• 因此,必须采用释放罐内气体的方法控制压力上限。
方法是在储罐的气相管道上设置调压器,当储罐内压力升 高到设定值时,减压阀便缓慢打开,将罐内气体放出,当
压力降回到设定值以下时,自动调压器自动关闭。需要指 出的是,这里所说的调压器并不是我们常用的气体调压器。
• 一定条件下,下层强烈的热对流循环促使分层界面被 打破,上下层发生掺混,密度趋于相等。原处于过饱和状态 的下层LNG及时大量蒸发,储罐内将出现翻滚现象,引发超 压事故。
•原因分析:
• (1)液化天然气存在不同组分。由于罐内LNG为混 合物,主要为Cl,少量的C2,极少量的C3一C6。不同物质 在液化后密度不同,因而储存时可能在储罐内出现分层, 重组份在储罐下部,轻组份在储罐上部。
液化天然气储罐区设计

液化天然气储罐区设计
首先,储罐大小和数量是储罐区设计的首要考虑因素。
液化天然气储罐的大小和数量要根据实际需求和预期储存量来确定。
通常来说,储罐的容量应该足够满足所需天然气的储存,同时要考虑到生产需求和储罐的维护周期,以便在必要时进行储罐的清洗、维修和更换。
储罐的数量也需要考虑到天然气的供应压力和储罐的使用寿命等因素。
其次,储罐区的排列和布局也是一个重要的设计考虑因素。
液化天然气储罐应该采用合适的排列方式,以便提供足够的安全间距和适当的操作空间。
储罐之间的间距应该满足法定要求,并考虑到紧急情况下的疏散和救援活动。
储罐区的布局应该便于日常操作和维护,并提供充足的通风和防火措施,以减少事故的发生和蔓延。
第三,安全防护措施是液化天然气储罐区设计中不可忽视的一部分。
储罐区应该配备适当的安全设备,如气体泄漏和火灾报警系统、灭火器、应急照明等。
此外,储罐区还应该有足够的消防水源,并设有消防车辆、灭火器和灭火剂等设备。
储罐区的工作人员应该接受足够的安全培训,并严格遵守相关操作规程和安全操作程序。
最后,液化天然气储罐区设计还应考虑到对环境的影响。
储罐区的选址应避免对周围环境和居民造成不利影响,如空气污染、噪音污染和地下水污染等。
在储罐区建设和运营过程中,应采取合适的措施,以减少对土壤、水源和生态环境的不良影响。
如果必要,还应制定应急预案,以应对可能发生的环境事故。
综上所述,液化天然气储罐区设计需要综合考虑储罐大小和数量、储罐的排列和布局、安全防护措施以及环境影响等因素。
只有在全面考虑这些因素的基础上,才能设计出安全可靠、环保合规的液化天然气储罐区。
大型LNG储罐设计及建造技术

设计技术
1、罐体结构设计
大型LNG储罐通常采用多层壁结构,由内向外依次为耐腐蚀层、绝热层、抗拉 层和外防护层。其中,耐腐蚀层用于保护储罐内壁不受腐蚀,绝热层用于减少 LNG的蒸发损失,抗拉层用于增强储罐的抗拉伸性能,外防护层则用于防止外 界因素对储罐的影响。
2、强度设计
大型LNG储罐的强度设计是确保其安全性能的关键因素。在设计过程中,需对 储罐进行全面的应力分析,包括储罐在充装、排放、根部受力和热胀冷缩等情 况下的应力变化。根据分析结果,对储罐的结构进行优化,以使其在各种工况 下都能满足强度要求。
4、抗压性能强:能够承受储罐内的高压,保证储罐的稳定性。
5、使用寿命长:要求绝热材料具有较长的使用寿命,能够保证储罐的长期使 用。
二、大型LNG储罐绝热材料的应 用范围
大型LNG储罐绝热材料主要应用于以下场景:
1、城市燃气储备:城市燃气储备基地需要大量的LNG储罐来存储燃气,为了保 证燃气的恒温和安全存储,需要使用高性能的绝热材料。
建造技术
பைடு நூலகம்
1、施工组织
大型LNG储罐的建造过程需要严谨的施工组织。在施工前,应制定详细的施工 方案,明确各阶段的任务和目标,确保施工顺利进行。同时,建立完善的质量 管理体系,确保每个环节的质量都符合要求。
2、施工工艺
大型LNG储罐的建造涉及到多种工艺,包括钢板焊接、耐腐蚀涂料涂装、绝热 材料填充等。在施工过程中,要严格遵守工艺规程,确保每个环节的施工质量 都达到要求。
四、大型LNG储罐绝热材料的探 讨与建议
针对上述实际应用案例中出现的问题,提出以下几点建议:
1、加强技术研发:继续研究和开发新型的绝热材料,提高其保温性能、耐低 温性能和环保性能,降低生产成本,提高使用寿命。
万立方米LNG储罐设计
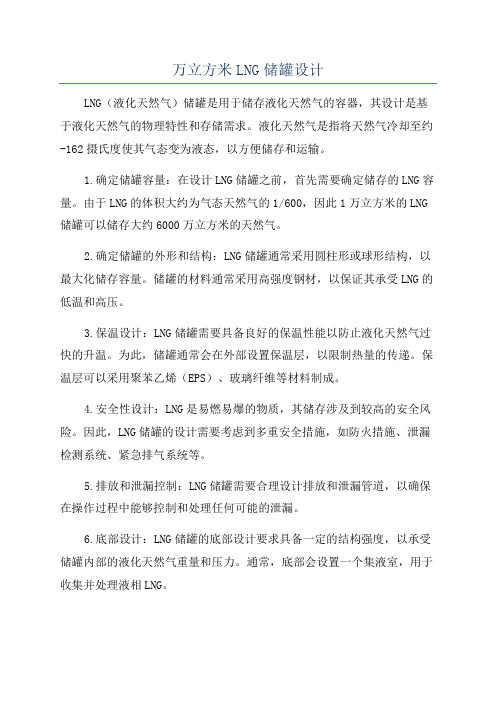
万立方米LNG储罐设计LNG(液化天然气)储罐是用于储存液化天然气的容器,其设计是基于液化天然气的物理特性和存储需求。
液化天然气是指将天然气冷却至约-162摄氏度使其气态变为液态,以方便储存和运输。
1.确定储罐容量:在设计LNG储罐之前,首先需要确定储存的LNG容量。
由于LNG的体积大约为气态天然气的1/600,因此1万立方米的LNG 储罐可以储存大约6000万立方米的天然气。
2.确定储罐的外形和结构:LNG储罐通常采用圆柱形或球形结构,以最大化储存容量。
储罐的材料通常采用高强度钢材,以保证其承受LNG的低温和高压。
3.保温设计:LNG储罐需要具备良好的保温性能以防止液化天然气过快的升温。
为此,储罐通常会在外部设置保温层,以限制热量的传递。
保温层可以采用聚苯乙烯(EPS)、玻璃纤维等材料制成。
4.安全性设计:LNG是易燃易爆的物质,其储存涉及到较高的安全风险。
因此,LNG储罐的设计需要考虑到多重安全措施,如防火措施、泄漏检测系统、紧急排气系统等。
5.排放和泄漏控制:LNG储罐需要合理设计排放和泄漏管道,以确保在操作过程中能够控制和处理任何可能的泄漏。
6.底部设计:LNG储罐的底部设计要求具备一定的结构强度,以承受储罐内部的液化天然气重量和压力。
通常,底部会设置一个集液室,用于收集并处理液相LNG。
7.对外界环境的适应能力:LNG储罐需要适应不同的气候条件和环境影响,以确保其安全运行。
这可能需要考虑到地震、风力、雪负荷等外界影响因素。
以上是万立方米LNG储罐设计的基本要点,每个设计工程可能会根据具体要求有所不同。
LNG储罐的设计不仅需要考虑到储存需求和功能要求,还需要充分满足安全性和环境要求,以确保设备的长期稳定运行。
lng储罐结构及原理

lng储罐结构及原理
LNG(液化天然气)储罐是其中一种常见的储存液化天然气
的结构。
LNG储罐主要由外壳、保温层、内壁、支撑系统、
压力释放系统等组成。
1. 外壳:LNG储罐外部通常由钢材制成,它起到保护内部液
化天然气免受外部环境因素的影响,如温度变化和物理冲击等。
2. 保温层:为了保持LNG的低温状态,储罐表面会添加保温层。
保温层通常由保温材料制成,如聚氨酯泡沫或玻璃纤维。
3. 内壁:LNG储罐的内壁主要由不锈钢或铝合金制成,以保
证储存LNG的完整性和密封性。
4. 支撑系统:支撑系统用于支持储罐的外壳和保温层。
通常,储罐底部有一个支撑结构,可以承受液体的重量。
5. 压力释放系统:由于LNG在很低的温度下会产生气体,储
罐内的压力会增加。
为了防止储罐爆炸或损坏,储罐内部设有压力释放系统,用于释放过多的气体。
LNG储罐的工作原理是通过液化天然气的特性实现的。
液化
天然气需要在极低的温度下(-162°C)和适当的压力下才能变成液态。
LNG储罐提供了一个密封和绝热的环境,在这个环
境下,液化天然气可以保持稳定的低温状态。
当需要使用
LNG时,通过控制储罐内部的压力和温度,可以使液态天然
气重新转化为气体,供应给需要的设备或系统使用。
20万立方米LNG储罐设计

20万立方米LNG储罐设计LNG(液化天然气)储罐是用于储存液态天然气的设施,通常是由钢制或混凝土制成。
它们被广泛应用于天然气供应链的各个环节,包括天然气开采、运输、储存和分销。
本篇文章将讨论一个20万立方米LNG储罐的设计。
首先,设计一个20万立方米LNG储罐需要考虑以下几个关键因素:1.储罐结构:LNG储罐可以采用钢制或混凝土结构。
钢制储罐通常采用钢板组成圆筒形储罐,具有较高的强度和耐腐蚀性。
混凝土储罐通常具有较低的成本和更长的使用寿命,但施工周期相对较长。
2.安全性:LNG是高压低温液体,需要采取多种措施来确保储罐的安全性。
例如,储罐应具有良好的绝热性能,以保持低温状态并减少液化气体的蒸发。
此外,储罐还应配备安全阀和泄漏探测系统,以应对潜在的危险情况。
3.储罐容量:20万立方米的LNG储罐可以满足相对大规模的天然气需求。
储罐的容量应根据供需情况和储存周期进行评估,并确保足够的储存量供应天然气。
4.环境影响:LNG储罐的设计应考虑其对周围环境的潜在影响。
例如,储罐应位于安全距离内,以减少爆炸风险。
此外,储罐的绝热材料和排放控制系统应设计为减少温室气体和其他污染物的排放。
5.维护和运营:LNG储罐的设计应兼顾维护和运营的需求。
例如,储罐应具备易于检查和维修的结构,并配备必要的设备,如泵和阀门等。
针对以上要求,一个20万立方米的LNG储罐设计可以遵循以下步骤:2.安全性分析:进行安全性分析,评估潜在的风险和威胁,并设计相应的安全措施。
例如,采用多层绝热材料和防雷设备来降低储罐的温度和爆炸风险。
3.结构设计:选择合适的储罐结构,并进行结构设计。
对于钢制储罐,需要进行材料选择、焊接和腐蚀保护等方面的设计。
对于混凝土储罐,需要进行形状设计、混凝土配比和防渗处理等方面的设计。
4.绝热设计:设计合理的绝热系统,以保持LNG的低温状态。
这可以通过选择合适的绝热材料、设计合理的层次和厚度以及采用外保温措施等方式实现。
大型LNG储罐施工技术

大型LNG储罐施工技术流程液化天然气(LNG)是通过将常压下气态的天然气冷却至-162℃凝结成液体,天然气液化后可大大节约储运空间和成本,是一种清洁、高效的能源。
储罐D80m,H50m,δ55mm,常压,容量约20万m3。
LNG全容罐的典型结构:储罐为双层构造,其外罐为混凝土罐底及预应力混凝土罐壁(或低合金高强钢Q345),混凝土外罐内壁设置有16Mn钢板焊制的防潮屏蔽层,外罐顶为钢顶及钢筋混凝土灌注复盖的复合拱顶。
内罐为9Ni钢制的自承式开顶罐,内罐上方设置铝合金吊顶和绝热材料。
在内外罐之间设置一定高度的由9Ni钢焊制的壁角保护装置及次级底板,在内罐泄漏时可由此中间罐起保护作用。
内外罐之间用弹性玻璃毡毯及膨胀珍珠岩填充绝热,在内罐底板、次级底板和防潮屏蔽底板之间均分别用泡沫玻璃砖及干砂绝热。
施工流程:预制→外罐→外罐拱顶→内罐底板→内罐壁板→附件→充水试验1.外罐施工工艺LNG低温储罐外罐通常为预应力混凝土结构(或低合金高强钢Q345)。
预应力混凝土结构重点关注:(1)外罐墙体控制混凝土水化热,防止出现温度裂缝。
主要从外墙混凝土配合比设计、分层分段浇筑施工、混凝土洒水覆盖等方面进行控制管理。
(2)外罐的垂直度和表面平整度等,直接影响拱顶气压顶升实施。
外罐墙体模板拼接容易出现模板面弧度、尺寸、垂直度等超标,要求按照图纸制作造型木弧度样板,精确测放出模板位置,用水准仪检查标高。
(3)预应力管道的施工,需要做好成品保护和接头处的密封工作,防止混凝土进入管道内部。
通常采用通球试验保障内部通畅。
2.拱顶施工工艺拱顶施工工艺主要为模块化施工工艺,将拱顶分块预制后组装焊接成整体,采用整体气压顶升工艺将拱顶顶升到安装位置焊接固定。
气压顶升技术是利用拱顶结构与储罐外壁之间形成密闭空间的特点,使用多台鼓风机向密闭空间不断地输送低压空气,从而拱顶钢结构按照预定路径上升至设计高度,并与拱顶承压环连接。
该技术的难点在于控制好整个拱顶的平衡、密封及提升速度,保持穹顶的平稳上升,重点是平衡系统和密封系统,以及风机系统、测量系统、通讯系统。
- 1、下载文档前请自行甄别文档内容的完整性,平台不提供额外的编辑、内容补充、找答案等附加服务。
- 2、"仅部分预览"的文档,不可在线预览部分如存在完整性等问题,可反馈申请退款(可完整预览的文档不适用该条件!)。
- 3、如文档侵犯您的权益,请联系客服反馈,我们会尽快为您处理(人工客服工作时间:9:00-18:30)。
液化天然气储罐结构与建造由于全容罐具有更高的安全性,在LNG储存越来越大型化并且对储存安全性要求越来越高的今天,全容罐得到更多的采用也是必然的。
下面就大型全容罐,特别是近几年来我国沿海新建LNG接收站广泛采用的16×104m3的全容式储罐的结构与建造作一介绍。
一、全容罐的结构及发展(一) 全容罐的结构地上式全容罐一般为平底双壁圆柱形。
与LNG直接接触的内罐为9%镍钢,外罐为预应力钢筋混凝土,罐顶有悬挂式绝热支撑平台,内外罐之间用膨胀珍珠岩、弹性玻璃纤维或泡沫玻璃砖等材料绝热保温。
1. 设计条件(1) 内罐设计温度:-170~+60℃;设计压力:29kPa(真空1.5kPa)。
(2) 外罐安全经受6h的外部火灾;承受地震加速度0.219;承受风力170m/s;抗渗性:当发生内罐LNG溢出时,外罐混凝土墙至少要保持10cm厚不开裂并保持2MPa以上的平均压应力。
日最大蒸发率≤0.05%(质量)。
(3) 设计标准储罐的基本设计规范为BS7777。
其他相关规范有API620、ACI318、NFPA 59A等。
2. 内罐(1) 板材内罐壁板材料为含镍9%的合金钢板,如广东大鹏LNG接收站采用ASTM A 553M Type 1,其化学成分和机械性能见表4-5和表4-6[2]。
表4-5 9%镍钢板(ASTM A553M Type 1)化学成分 %表4-6 9%镍钢板(ASTM A553M Type 1)机械性能(2) 罐底罐底铺设两层9%Ni钢板,厚度为6mm和5mm。
底板外圈为环板,两层底板中间为保温层、混凝土层、垫毡(zhan)层和干沙层。
(3) 罐壁罐壁分层安装,分层数按板材宽度而定。
对于容积16×104m。
以上的全容罐一般有10层。
最底层壁板厚度24.9mm,最上层壁板厚度12mm。
内罐外壁用保温钉固定绝热保温材料。
(4) 罐顶内罐顶部为悬挂式铝合金吊顶,以支撑罐顶膨胀珍珠岩保温层。
3. 外罐(1) 罐基础全容罐的基础应按储罐建造场地的土壤条件,通过工程地质调查研究后确定。
一般可以采用坐基式基础或架空形基础。
坐基式基础内罐底板直接坐落在基础上,为防止罐内液体的低温使土壤冻胀,坐基式基础需要配置加热系统。
架空形基础可以不设加热系统。
(2) 罐墙壁全容罐的外罐墙用预应力钢筋混凝土制成。
容积为16×104m3左右的全容罐外罐内径约80m、墙高约50m。
混凝土墙体竖向采用VSL预应力后张束,两端锚固于混凝土墙底和顶部。
墙体环向采用同样规格的钢绞线组成的VSL预应力后张束,环向束每束围绕混凝土墙体半圈,分别锚固于布置成90度的四根竖向扶壁柱上。
墙体内置入预埋件以固定防潮衬板及罐顶承压环。
(3) 罐顶罐顶盖为钢筋混凝土球面穹顶,支承于预应力钢筋混凝土圆形墙体上。
球面穹顶混凝土由H钢梁、顶板及钢筋构成加强结构,顶面上设有工作平台,放置运行控制设备及仪表、阀等。
混凝土穹顶内设有碳钢钢板内衬,施工时作为模板,使用时可用以防止气体渗漏。
(二) 全容式储罐的发展典型的全容式储罐由预应力钢筋混凝土外层罐和9%Ni钢内层罐组成,罐顶为钢筋混凝土制成。
随着全容罐需求的不断增加,储罐结构设计和材料应用的不断改进,一方面储罐的容量越来越大,容积达20×104m3的地上全容罐已在建造;另一方面设计和建造技术的发展,储罐建设费用下降,建造周期缩短。
(1) 储罐内罐材料9%Ni钢板的制造、焊接、检验技术进步迅速:日本已可制造50mm厚度的钢板;焊缝NDE检验采用可记录数据的AUT方法,比现用的RT检验在安全性、质量可靠性、缩短检验时间等方面优点明显。
(2) 预应力外罐材料采用60MPa高强度混凝土,是通常混凝土强度的1.5倍,减少壁厚30%左右,从而减少了施工工作量。
(3) 增加9%Ni钢内罐壁板的宽度达到4.3m,减少圈数,既减少了焊接和检验工作量,也提高了板材整体性能及尺寸度的一致性。
(4) 混凝土外罐壁应用液压提升装置,滑模施工,提高劳动生产率,缩短工期。
(5) 采用多参数控制混凝土质量。
对原料质量、含水率、搅拌器载荷值等参数实时检测,及时调配。
(6) 提高预制化程度,对钢结构部分尽可能分块预制,现场拼装以减少现场安装、焊接工作量。
二、全容罐的建造(一) 外罐建造1. 墙体浇筑外罐墙体浇筑是混凝土工作量最大的部分。
按照通常钢筋混凝土施工程序,在布置钢筋,安装预应力护套、预埋件和模板后,进行混凝土浇筑、养护。
对于近40m高的墙体,需要分层从下至上逐层浇筑。
2. 安装承压环在浇筑最上层墙体前,安装承压环。
在按照承压环结构分段预制,预埋螺栓焊接完成后,吊装于罐壁顶部组装焊接,检验合格后进行混凝土浇筑。
3. 气升罐顶储罐顶部是钢结构的半球形拱顶,采用大型圆柱形储罐惯用的压缩空气吹升法施工,可以减少高空作业工作量,所需施工机具和设备少,对施工进度和安全有利。
罐顶结构在罐底预制完成后与罐壁密封,为防止气升过程的倾斜、偏移,罐顶上均布平衡钢索,一端固定在罐底中心,另一端固定于承压环上。
使用鼓风机鼓风,在空气压力下,罐顶匀速、平稳升起。
罐顶到位后,与预埋于墙体的顶部承压环固定、焊接。
4. 罐顶建造罐顶为球面结构,H型钢作为钢梁,顶部铺碳钢板,顶板上焊接预埋螺栓,升顶后固定于浇筑在混凝土罐壁顶部的承压环上。
同时在罐底预制铝合金吊顶,吊顶杆用螺栓连接于罐顶钢梁上,然后将预制好的铝合金吊顶提升与吊顶杆连接。
气升前,将罐顶上的人孔、接管、电缆托架等附件一块安装上去,以减少高空作业工作量。
布钢筋完成后,分两次浇筑混凝土。
5. 罐壁预应力张拉混凝土墙体浇筑、养护完成后,将钢绞线穿进预埋于墙体的护套中,竖向钢绞线两端锚于混凝土墙底部及顶部;墙体环向的钢绞线每束围绕混凝土墙体半圈,分别锚固于布置成90度的四根竖向扶壁柱上。
用液压设备拉伸到设计应力后,固定两端,进行水泥灌浆。
(二) 内罐建造1. 罐底内罐底部有两层底板,均为9%镍钢。
按照从下而上、由内而外、由四周到中间的顺序施工。
先进行第二层罐底环板安装、焊接完成后,进行底板铺设。
焊缝搭接采用手工焊,为防止变形,应注意焊接顺序:环板→横向焊缝→纵向焊缝→环板与边缘板焊缝→边缘板之间焊缝→边缘板与中心板焊缝。
2. 罐壁内罐罐壁的施工由下而上,逐层安装和焊接。
每层板的卷制、坡口准备应预先加工完成。
现场吊装采用吊车和罐顶电动绞车。
第一层壁板安装时,要确定在环板的准确位置,可以用专用卡具及辅助工具以调整位置保证组装质量。
底板与壁板角焊缝的焊接,至少应安装完第三层壁板及第1~2层壁板焊缝全部焊完后方可进行。
3. 保温液化天然气的低温特性要求储罐必须具有完善的保温隔热性能,以防止外界热量的漏入,确保储罐的日蒸发率控制在0.05%以内。
通常在内罐和外罐之间的环形空间填充膨胀珍珠岩。
内层罐壁的外侧安装弹性玻璃纤维保温毯,保温毯为珍珠岩提供弹性,克服储罐因温度变化而产生的收缩,防止珍珠岩的沉降。
保温毯还对储罐惰化处理过程中,吹扫气体的流动有利。
为了防止储罐罐顶的热泄漏,在吊顶上安装保温材料,铺设厚度1.2m的膨胀珍珠岩。
气密性试验合格后,进行内顶保温层的安装及夹层珍珠岩的填充。
首先在内罐壁外包一层纤维玻璃棉,包扎好后用专用加热设备加热到900%,然后从顶部往下装填珍珠岩,分层装填,分层夯实,直至到顶。
最后进行顶部甲板珍珠岩的铺设。
在进行珍珠岩灌注时要注意防潮。
储罐底部保温层采用泡沫玻璃砖。
这是因为罐底保温材料除了保温性能外,还要求有足够的机械强度以承受上部的液体载荷。
(三) 9%镍钢的焊接对于9%镍钢的焊接是内罐建造的主要工作量,由于9%镍钢对磁性很敏感,为避免现场焊接时产生电弧偏吹,要求出厂钢材残余磁含量不超过50高斯,同时现场施工时远离强磁场,并准备消磁设备。
(1) 对于焊缝的焊接:对接焊缝,厚度大于14.7mm的壁板采用双面坡口,厚度小于14.7mm的壁板采用单面坡口;环向焊缝采用背面焊剂保护埋弧自动焊;其他焊缝采用手工电弧焊工艺。
(2) 焊材的选用除满足机械性能要求外,更重要的是焊缝金属线膨胀系数要与9%镍钢接近,以避免焊缝受热循环在低温服役时产生应力集中而疲劳破坏。
资料表明,手工焊工艺的AWS A5.11M/ENiCrMo-6;伊萨OK92.55焊条及埋弧焊工艺的AWS A5.14/A5.14M ERNiCrMo-4,法国Btihler Thyssen Thema nit Nimo C276焊丝,匹配EN760/SA FB255AC H5/Marathon 104焊剂,线膨胀系数最接近母材,并按照设计要求及BS EN ISO 15614标准进行焊接工艺评定。
所要求的焊材化学成分见表4-7[2]。
表4-7 焊材合金成分及机械性能(3) 9%镍钢的焊接性能良好,对冷裂纹的敏感性很低。
为保证焊缝的高强度及低温韧性,焊接时要严格控制焊接参数,特别是预热、层间温度和热输入。
通常厚度小于50mm的板材无需预热,焊前温度高于10℃即可。
层间温度控制在150℃以下,以避免焊缝热影响区韧性的下降,同时焊缝金属属于奥氏体材料可避免热裂纹的产生。
热输入的控制是保证焊缝机械性能的关键,在1~3k J/mm范围,采用直焊道技术,特别是立焊不能摆动过宽。
焊缝返修对焊缝性能产生不利影响,因此返修操作应按照返修程序的要求进行,并且相同位置的返修仅限一次。
(四) 后续工作1. 检验储罐的检验工作主要是围绕焊缝进行的。
按照相关标准,储罐需要进行包括卵、RT、PMI和真空试验等项必要的检验。
(1) 订检验按照EN571-1的标准,对罐底环板焊缝、壁板与环板焊缝的根部焊道和盖面焊道、罐壁板焊缝进行检验。
(2) RT检验按照BS7777标准,对内罐所有9%镍钢壁板与环板的对接焊缝进行射线探伤(RT)。
要求焊缝100%检验。
(3) 真空试验按照BS7777标准,为了确保焊缝的气密性,对储罐的所有焊道进行100%的真空试验。
环板对接焊缝需要在水压试验前、后检验两次。
(4) PMI检验对每条焊缝抽检一点,进行焊缝合金成分鉴定(PMI),确认焊缝金属的Ni、Cr、Mo含量在规定的范围内。
2. 试验(1) 水压试验内罐充水,进行盛水试验,在空罐、1/4、1/2、3/4液位高度和盛满水时分别进行基础沉降、环向位移、径向位移和倾斜的测量。
水压试验完成后,对罐底板搭接焊缝、环板的对接焊缝及罐壁板与环板的T型焊缝进行第二次真空检验。
(2) 气压试验内罐盛水试漏合格后,将外罐开口大门复位合格后,进行外罐气密试验,气压试验压力36.25kPa,保持1h以上,用肥皂水检查外罐壁、罐顶。
负压500Pa检测真空阀(VSV)、安全阀(PSV)的性能。
3. 干燥与冷却采用液氮循环的方式,进行储罐的干燥和惰化,降低罐内湿度和含氧量到规定的要求。