微通道反应器的高效精细化工时代
微通道反应开启化工高效精细化新时代

Information资讯集萃膜产业聚焦高质量发展突破点【本刊讯】(记者魏少平)5月11〜12日,由中国膜工业 协会主办的2019中国膜产业发展峰会在宁波召开。
与会人士 认为,膜产业已成为我国发展最为迅速的战略性新兴产业之 一,但还应在原始创新、产业化、应用拓展及增强国际竞争力 上下大力气,支撑化工行业高质量发展。
出席会议的十届全国人大常委会副委员长顾秀莲高度评 价了膜产业在促进国民经济发展和化工行业转型升级中的作 用。
她表示,经过多年的发展,我国多个膜专业领域都取得了 重大突破,开发出了一大批具有自主知识产权的科研成果。
膜 在海水淡化,工业废水处理,化工物质的分离、提纯、浓缩等 方面都得到了广泛应用,为我国化工行业高质量发展作出了 突出的贡献。
中国膜工业协会秘书长王继文表示,“十二五”以来,我国膜产业取得了快速的发展,每年都以20%左右的速度 增长。
据膜协会统计,2018年我国膜产业产值达2438亿元,比上年增长19.4%;目前涉膜企业数量达2038家,带动下游 万亿级产业。
膜已经渗透到国民经济的各个领域,在节能 减排、环保治理、传统产业升级等方面起到了重要的支撑 作用。
同时,与会专家也指出,膜产业在取得长足发展的同时,在原始创新、产业化、应用拓展和国际竞争能力上,与发达国 家还有较大差距。
中国工程院院士高从堦分析认为,目前分离膜的产业链,从基础研究到产业化仍有待强化。
不仅原创技术有待提升,关键装备水平有待进一步提高,而且由于高端膜仍依赖进口,膜技术产业链完整性有待完善,上下游企业连接的紧密度也 亟待加强。
中国石油和化学工业联合会副会长赵俊贵表示,在我 国石化行业转型升级任务十分繁重、行业安全环保压力日益 增大的形势下,加强膜产业的创新和高质量发展显得更加迫 切。
膜技术作为化工行业绿色发展的重要支撑技术,要牢牢 抓住行业转型升级的机遇,努力提升服务水平,促进行业实现 绿色、高质量发展。
顾秀莲对膜产业发展提出四点建议:一要将自主创新放 在产业发展的首位,瞄准国际前沿,加强膜产业链的原始创 新,着力发展高性能膜技术和膜产品。
化学反应工程的新技术应用案例分析
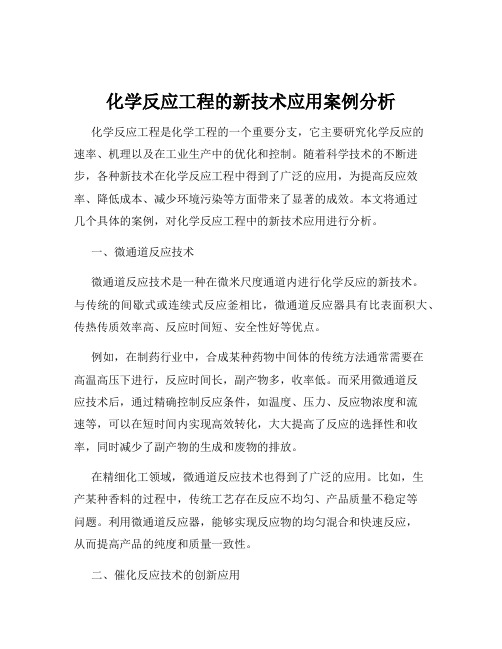
化学反应工程的新技术应用案例分析化学反应工程是化学工程的一个重要分支,它主要研究化学反应的速率、机理以及在工业生产中的优化和控制。
随着科学技术的不断进步,各种新技术在化学反应工程中得到了广泛的应用,为提高反应效率、降低成本、减少环境污染等方面带来了显著的成效。
本文将通过几个具体的案例,对化学反应工程中的新技术应用进行分析。
一、微通道反应技术微通道反应技术是一种在微米尺度通道内进行化学反应的新技术。
与传统的间歇式或连续式反应釜相比,微通道反应器具有比表面积大、传热传质效率高、反应时间短、安全性好等优点。
例如,在制药行业中,合成某种药物中间体的传统方法通常需要在高温高压下进行,反应时间长,副产物多,收率低。
而采用微通道反应技术后,通过精确控制反应条件,如温度、压力、反应物浓度和流速等,可以在短时间内实现高效转化,大大提高了反应的选择性和收率,同时减少了副产物的生成和废物的排放。
在精细化工领域,微通道反应技术也得到了广泛的应用。
比如,生产某种香料的过程中,传统工艺存在反应不均匀、产品质量不稳定等问题。
利用微通道反应器,能够实现反应物的均匀混合和快速反应,从而提高产品的纯度和质量一致性。
二、催化反应技术的创新应用催化剂在化学反应中起着至关重要的作用,能够降低反应的活化能,提高反应速率和选择性。
近年来,催化反应技术不断创新,出现了许多新型的催化剂和催化反应体系。
以酶催化反应为例,酶作为一种生物催化剂,具有高效、专一、温和的催化特性。
在食品工业中,利用酶催化技术可以将淀粉转化为葡萄糖、果糖等甜味剂,不仅反应条件温和,而且产品质量高、安全性好。
在环保领域,光催化技术也展现出了巨大的潜力。
例如,利用二氧化钛等光催化剂,可以在光照条件下将有机污染物分解为无害物质,为废水处理和空气净化提供了新的途径。
此外,纳米催化剂的出现也为化学反应工程带来了新的机遇。
纳米级的催化剂颗粒具有更高的比表面积和活性位点,能够显著提高催化效率。
常州大学环境与安全工程学院院长张跃微反应开启化工高效精细化新时代

l\\<>\ATI\(-TAU'.N'I'I倉:1新达人常州大学环境与安全工程学院院长张跃:微反应开启化工高效精细化新时代■文/杜浩钧李伟宁微通道反应器是新型的反应器,其高效的传热传质接近理论值。
近年来,微通道反应器已经在多家化工行业应用,打破了国外公司的技术垄断,标志着化工界技术上取得了重大突破。
在该项目国产化研究的过程中,常州大学环境与安全工程学院院长张跃功不可没。
他带领团队勇于向新事物发起挑战,并以自主研发的技术为企业带来了丰厚的经济效益,获得了业内专业人士的肯定和认可。
张跃主持的项目《新型微通道反应器系统关键技术开发及产业化应用》获得了2019年中国化工学会技术奖二等奖。
敢闯天下先的技术团队微反应技术起源于20世纪90年代初的欧洲,美国康宁公司在2008年将微反应器技术推广到工业化应用阶段。
对传统化工装备而言,微通道反应器是一项革命性的创新技术,为化工产业开启了崭新的高效精细化时代,为行业转型升级、提升创新能力、实现绿色发展提供了有效的技术手段。
但在当时,无论是理论研究还是实际应用,国内还是一片空白。
张跃在采访中说,不可否认,近年来,微通道反应器在国内快速推广,美国康宁公司起到了一定的促进作用。
10年前,常州大学与该公司成立了联合实验室,但后来康宁公司因故撤走。
是继续做?还是放弃?摆在张跃及其同事面前的是一个前途未卜的选择。
但后来的事实证明,张跃答对了这道题,但解题的过程却是异常艰辛。
张跃向记者介绍说,微通道(连续流)反应器是一种依靠微加工技术,在特定的固体基质上蚀刻出固定形态的通道,并具有一定化学反应适用性的化工设备。
与常规釜式反应器相比,其内部通道直径非常细小,通常为10-500Pm,却拥有极大的比表面积,比釜式反应器的比表面积要大上几百倍张跃发表获奖感言甚至上千倍,因而有效地提升了换热效率和传质效率,并且能够精确控制反应温度,确保反应物料瞬间混合,有助于提高化学反应收率、选择性、安全性和产品质量。
微通道反应器中精细化学品合成危险工艺研究进展

课题组自2016年开始,开展基于微通道反应器的连续化生产工艺开发等方面的研究工作。
对氯化、溴化、氟化、氧化、重氮化、硝化、加氢及胺化等反应过程进行了深入系统的研究。
本文是在课题组前期研究基础上,对相关领域最新研究成果进行了归纳、总结,并结合作者多年研究心得所撰写,以期为科研工作者了解相关领域的研究现状、发展趋势提供帮助。
摘要:卤化、氧化、重氮化、硝化以及催化加氢是精细化工生产中的重要反应,通常以间歇方式在釜式反应器中进行,存在安全隐患,并且反应效率低。
微通道反应器技术的发展为解决上述问题提供了有效途径,因此,发展基于微通道反应器的安全高效合成工艺成为当前精细化工领域的研究热点之一。
该文综述了近年来微通道反应器中涉及精细化工产品合成危险工艺的研究进展,并指出了微通道反应器存在的不足和今后研究的方向。
结束语与展望本文总结了新型微通道反应器的设计、构建和相关产品在微通道反应器中合成工艺的研究进展,涵盖了放热剧烈、反应物或产物不稳定、物料配比严格、高温高压等危险反应工艺,与国家石化化工行业鼓励推广应用的技术和产品目录的第一条“新型微通道反应器装备及连续流工艺技术”的范畴相契合[92]。
从中发现:(1)微反应器的材质与反应物在反应器内表面的均匀分布以及耐腐蚀性密切相关,从而影响反应能否顺利进行;(2)均相或气-液两相反应可以在经典的毛细管线圈反应器内进行,通过工艺参数的优化可以达到理想的结果,其中停留时间是主要因素;(3)对于光催化反应,微反应器的构型设计应满足尽可能大的受光面积;(4)对于气-液-液三相反应,微反应器的设计首先考虑的是反应物相的充分混合问题,混合器和反应器芯片的构造与构型是优先考虑的因素;(5)采用催化活性组分修饰的毛细管微反应器可以解决经典毛细管反应器不能进行固-液或气-固-液多相催化反应的问题,而且无需催化剂的分离,其中负载催化活性组分的活性和稳定性是优先考虑的问题;(6)填充床反应器上也可进行固-液或气-固-液多相催化反应,催化剂的填充需避免大的压降问题;(7)除了反应温度、反应压力以外,气体流速、液体流速以及停留时间也是获得微通道反应器中相关反应优化工艺的重要参数。
微反应器在精细化工领域氧化反应中的应用进展

微反应器在精细化工领域氧化反应中的应用进展摘要:精细化工在化工行业的地位十分重要,精细化学品种类多、专用性强、附加值高,广泛应用于各领域。
随着绿色环保节能理念的提出,精细化工行业越来越注重可持续发展,绿色化工技术已成为精细化工行业实现节能减排、绿色安全生产的新趋势。
关键词:微反应器;精细化工;氧化反应;应用进展引言微化工技术是当今化工领域的研究热点,微化工技术的核心部件就是微反应器。
与传统反应器相比,微反应器具有换热效率和混合效率高、高度集成化、可精准控制反应时间、安全性高等优点,在精细化工、制药工业、生物化工等领域具有广阔的应用前景。
目前微反应器的主要应用领域包括有机合成过程、微米及纳米材料的制备、日用化学品的生产等。
BRANUE等人利用微反应器生产选择性氟化的药物产品,在9个月内实现了从实验室规模到生产500kg高质量产品的生产过程。
郑亚峰在毛细管微反应器中进行乙烯环氧化反应,在不添加任何催化剂和抑制剂的情况下,乙烯的转化率为57%。
1.微反应器概述微反应器从上世纪90年代发展至今连续流加氢反应器可分为:填充式微反应器;壁载式微反应器;浆料式微反应器三类。
与传统反应器相比微反应器具有:(1)安全高效;微反应加氢装置具有体积小,用料少等优势,过程安全可控;(2)传热传质充分:微反应器内各种物料间接触更充分,热量吸收时间更短;(3)连续可放大:微反应器内可实现连续反应,提高产物选择性和转化率,从实验室小试到实际生产存在放大效应,微反应器通过增加反应次数省去中试环节。
微反应器的应用:(1)多相化学合成;(2)纳米材料制备;(3)药物连续结晶;(4)光化学反应等。
2.烷烃氧化烷烃被氧化后可得到醇、醛、酮和酸。
烷烃氧化是生产有机化工产品和精细化学品的重要工业过程。
但是传统烷烃氧化过程存在传质及传热效果差、转化率低、产率低、反应条件较苛刻等缺点,微反应器的出现为烷烃氧化提供了一条新途径。
开发一种微反应器模块化设备,使用长度可变且可替换的毛细管(长100m、内径1mm)作为单个反应器,在一定流速、温度(75~165℃)和压力(25~100bar)下,以液体异丁烷和氧气为原料制备过氧化氢叔丁醇(TBHP)。模块化结构微反应器解决了传统间歇式反应器无法连续生产、不适用反应条件苛刻且存在爆炸隐患工艺的问题,使得TBHP的制备过程可以在毛细管反应器中完成;在停留时间为4h时,异丁烷转化率达到5%,TBHP选择性为60%。将工业磷酸氧钒(VPO)催化剂填充至微反应器中,应用于正丁烷氧化制备马来酸酐。结果表明,当微反应器狭缝宽度为1.5mm、反应温度为410℃、反应时间为48h时,正丁烷转化率为88%,马来酸酐选择性为63%,而且在正丁烷入口体积分数高达4.5%时,微反应器仍可以实现几乎等温的操作;当微反应器狭缝宽度增至3.0mm时,反应热显著增加,热点温差(热点值与盐浴温度420℃的差值)未超过298℃,较工业多管式反应器减小了约80%。证明了微反应器对于这种典型的高放热、非均相催化气相氧化反应具有较大的应用潜力。
微通道的行业未来

近年来精细化工行业安全事故频发,而且都涉及到了一些剧烈的爆炸事故,这样就给这个行业戴上了高危的帽子。
而正因为如此,连续流微反应器是精细化工行业看好的提升生产操作安全的技术之一,微反应器的技术的普及已经成为业内的趋势。
那么这样一个小小的装置是如何提升化学实验中的生产实验安全的呢?和传统反应釜进行大量吨位的实时反应相比,微反应器内部有着成百万上千万的微通道,每个通道内都可以同时进行实验反应,而所使用的化学反应物质可能只有几毫升,所以即使发生危险也是在可控范围之内的。
同时,微通道反应器的一个特点就具有很好换热效率,可以有效避免反应中热力的堆积。
不同于传统夹套搅拌釜动辄上百平方米的占地面积,微通道反应器小而紧凑,占地面积只有几平方米,可谓是“迷你化工厂”。
化学反应在微通道中连续流动发生,反应快速完成,且过程精确可控,可实现无人化连续操作,极大减少了精细化工在研发和生产中的安全隐患。
正因为以上的诸多优点,所以微反应器也适用于很多类型反应。
举个很好的例子,像一些危险性比较高的反应,使用常规反应器会采用逐渐滴加的方式进行实验,即使如此还是会产生热和大量的副产物;但是如果在微通道进行反应,那么实验产生的副产物就能减少几十倍上百倍,并且因为比表面积大,,流动行为以层流为主,停留时间可精确控制。
除了体积小,多位专家还特别强调了微反应器在换热方面的优势,这使得微反应器可以适用于多个领域。
微反应器在氯化反应、氟化反应、烷基化反应、过氧化反应、磺化反应的等多种反应类型。
所以在医药化工领域都有着广泛的前景。
现阶段我国连续流设备多种多样,但精细化工反应工况复杂,单独从设备改造和工艺改进,很难实现化工生产的本质安全,需要设备和工艺的紧密结合。
尽管连续流设备已得到学术界和企业界的初步认可,但由于人员认可度差异、配套资源缺乏等因素,连续流设备在整个行业尚属于初级推广阶段,其优势和意义尚未完全展现出来,还需要各领域的共同推动。
上海惠和化德生物科技有限公司,是一家专注于微反应器连续工艺开发及工业化的创新性高科技公司。
微反应器在化学化工领域中的应用
微反应器在化学化工领域中的应用作者:李尚锐来源:《科教导刊·电子版》2018年第26期摘要微反应器是微型化学反应的发生装置,可以具有隔热和进行快速传输的作用,能够严格控制化学反应的方式和反应的时间,可以快速的对化学反应进行放大,因此具备很强的安全性特征,微反应器具有安全性能高的特点,与传统的化学反应装置相比,可以大大缩短化学反应的处理时间,提高化学反应的效率,提升产品的生产效率。
但是微反应器也容易出现堵塞的问题,在催化剂的装载和化学反应通道的设计方面具备较高难度。
关键词微反应器反应通道化学化工微反应器又被称作为微通道反应器,是集合了微反应器、换热器、微萃取器等化学分析容器的微型化学设备,微反应器产生于微流控致技术,由于微尺度的衡量标准不同,微反应器与传统的化学反应器具相比具有较大优势,提高了化学反应的技术含量,提升了化学反应的持续时间,受到了相关研究领域的关注。
1微反应器的技术优点1.1可以精确的控制反应的时间微反应器可以对反应的时间进行精确的控制,通过改变反应器的反应通道控制化学反应的流速,控制化学反应可能产生的中间物质,在化学反应产生之前将物质转换到另一个反应区间,因此该技术的产生不会对化学反应的稳定性产生影响,如果遇到多相体系,也能通过控制流速而改变物质产生反应的时间,通过改变流体的类型,可以对整体反映效果达到控制的目的。
如果应用微反应器,通过控制反应停留的时间,会取得更加明显的效果,控制恒定的流速是保证化学反应的关键。
1.2集成化程度较高我国目前的微加工技术已经比较进步,可以实现微反应以及微分离等操作步骤,一些微反应单元的操作可以集成到固定的反应芯片之中,从而实现对微反应进行实时监控的目标,这样的反应效果可以提升反应的效率,节省产品生产的成本,如果材料混合之后反应还有停留时间,则需要及时更换反应的速度,将反应安排在同一个区域。
通过多种形式的反应控制模式,可以实现化学反应的重复性,对平行试验方式的实现较为有利。
微通道化学反应器的设计及优化
微通道化学反应器的设计及优化随着科技的不断进步,化学反应器的设计与制造已经进入了微观尺度的领域。
微通道化学反应器是一种基于微流体技术的新型反应器,它具有高效、快速、低能耗等优点,因此在实验室和研究中得到了广泛的应用。
本文将从微通道化学反应器的定义、优点和应用中探讨其设计和优化的方法。
一、微通道化学反应器的定义微通道化学反应器是指在毫升级别以下的微型反应器中,通过改变微型通道的特性,控制反应物和溶液的流动状态,实现化学反应的过程。
它是一种基于微流体技术的新型反应器,适用于各种化学反应和制备,如有机合成、催化反应、聚合反应等。
微通道化学反应器的主要结构包括微通道反应器本体、上下游对接组件、进料口、出料口等。
二、微通道化学反应器的优点相对于传统的大型化学反应器,微通道化学反应器具有以下优点:1.快速:由于微通道反应器的尺寸极小且在微级范围内,反应物和溶液的物质传输效率更高,反应速度更快,反应时间更短。
2.高效:微通道反应器中,反应物与催化剂的接触面积变大,对反应的物料进行混合和分散作用更加显著,因此反应效果更佳。
3.低能耗:由于微通道反应器中反应溶液的体积远小于传统化学反应器,因此在制备和反应过程中所需的能耗较低,省去了大量装置、热交换器和冷却器等反应器自带的设备。
4.实时监测:微通道反应器中,反应过程实时可控,可在线实时监测反应过程,实现安全操作和反应过程的最佳控制。
5.绿色环保:由于采用微通道反应器,可实现溶剂和催化剂的高效利用,从而大大降低潜在的污染物的排放。
三、微通道化学反应器的应用微通道化学反应器在各种化学反应和制备中均有应用,如有机合成、催化反应、聚合反应等。
具体应用领域如下:1.有机合成:微通道化学反应器可应用于各种有机合成反应,如酯化反应、脱水反应、烷基化反应等,针对化学反应过程中难控、难扩展的问题,微通道化学反应器可以很好地解决,从而大大提高化学反应的效率和品质。
2.催化反应:微通道化学反应器可应用于各种催化反应,如均相氧化反应、氢化反应、酸碱催化反应等。
流动化学微通道反应器的应用现状及展望
流动化学微通道反应器的应用现状及展望一、引言随着科学技术的发展,微通道反应器在流动化学领域的应用越来越广泛。
微通道反应器具有高传热、高传质、高反应效率等优点,适用于多种化学反应过程。
本文将介绍微通道反应器的技术特点、应用现状及未来发展趋势,旨在为相关领域的研究和应用提供参考。
二、微通道反应器的技术特点1.高传热、高传质:微通道反应器具有较小的通道尺寸,能够显著提高传热和传质效率。
这使得化学反应可以在更高的反应速率下进行,同时减少了能源消耗。
2.高反应效率:由于微通道反应器的特殊结构,化学反应可以在短时间内完成,减少了副反应和废物生成,提高了产品的质量和产量。
3.易于控制:微通道反应器可以通过改变通道尺寸、反应条件等参数来控制化学反应过程,从而实现反应过程的精确控制。
4.安全性高:微通道反应器具有较低的操作压力和温度,减少了化学反应的风险和安全隐患。
三、微通道反应器的应用现状1.制药行业:在制药行业中,微通道反应器被广泛应用于药物合成、生物催化反应等领域。
其高传热、高传质性能使得药物合成过程更加高效、安全。
2.化工行业:微通道反应器在化工行业中得到了广泛应用,如烯烃聚合、燃料生产等。
其高反应效率和易于控制的优点使得化工生产过程更加优化和可控。
3.环境治理:微通道反应器可用于处理环境污染问题,如废水处理、有害气体净化等。
其高效率和安全性使得环境治理更加有效和环保。
4.能源领域:微通道反应器在能源领域也有广泛的应用,如燃料电池、太阳能电池等。
其高效率和精确控制性能使得能源转换和利用更加高效和可持续。
四、微通道反应器的未来发展趋势1.微型化:随着微制造技术的发展,未来微通道反应器可能会更加微型化,从而进一步提高传热、传质效率,并使得设备更加紧凑和便携。
2.多功能化:未来的微通道反应器可能会具备更多的功能,如混合、分离、检测等,从而能够实现更加复杂的化学反应过程。
3.智能化:随着物联网、人工智能等技术的发展,未来的微通道反应器可能会更加智能化,能够实现自我感知、自我控制和故障诊断等功能,从而提高设备的安全性和效率。
微反应器在化学化工领域中的应用
CHEMICAL INDUSTRY AND ENGINEERING PROGRESS 2016年第35卷第1期·10·化 工 进 展微反应器在化学化工领域中的应用刘兆利,张鹏飞(天津大学化工学院,天津 300072)摘要:微反应器是微型化学反应系统,具有换热和传质效率高、严格控制反应时间、易于放大、安全性能好等特点。
和传统搅拌反应器相比,这些特点使得微反应器在缩短反应时间、大幅度提高化学反应的转化率和产品收率等方面展现出一定的优势。
但微反应器也存在易堵塞,催化剂负载、微通道的设计与制造难度大等问题。
本文介绍了近年来快速发展的微反应器技术,回顾了微反应器的特点,重点探讨微反应器在化学化工领域的应用以及微反应器在精细化工和制药工业、生物化工领域的应用实例,讨论了微反应器目前存在的诸多挑战。
微反应器目前是化学和化工学科的前沿和热点方向,分析表明微反应器仍然有很大的发展空间,有潜力改变化学化工前景。
提出应进一步深入系统地认识微反应器内化学反应以及微通道设计的基本规律和机理,将微反应器技术引入更广泛的反应体系中,加强微反应器的集成化水平。
关键词:微反应器;微通道;微尺度;层流;安全中图分类号:TQ 052 文献标志码:A 文章编号:1000–6613(2016)01–0010–08 DOI :10.16085/j.issn.1000-6613.2016.01.002Applications of microreactor in chemistry and chemical engineeringLIU Zhaoli ,ZHANG Pengfei(School of Chemical Engineering ,Tianjin University ,Tianjin 300072,China )Abstract :Microreactor belongs to the miniature chemical reaction system ,which has some characteristics of high heat- and mass- transfer rates ,strictly-controlled reaction time ,easy scale-up ,excellent safety performance ,and so on. Comparing with the common batch reactors ,advantages of microreactors are reducing reaction time ,greatly promoting conversion and yields. On the other hand ,there are some existing challenges ,such as the clogging problem ,catalyst loading ,design and fabrication of microchannels ,and so on. This paper aims to introduce the microreactor technology ,which has been growing rapidly in recent years. Some of the basic characteristics of microreactor are summarized focusing on applications of microreactor in chemistry and chemical engineering as well as some of typical examples of existing in fine chemical and pharmaceutical industry. A variety of challenges are also discussed. Microreactor is a frontier and hot topic in the research of chemistry and chemical engineering and analysis shows that microreactor still has very big development space and has the potential to change the chemistry and chemical engineering landscape. In the future ,further in-depth and systematic understanding of the regularities and mechanisms of chemical reaction in microreactor and design of microchannels should be emphasized. Introducing the microreactor technology into more reaction systems and further improving the integration level still need to be perfected.Key words :microreactor ;microchannels ;microscale ;laminar flow ;safety 收稿日期:2015-07-08;修改稿日期:2015-07-29。
- 1、下载文档前请自行甄别文档内容的完整性,平台不提供额外的编辑、内容补充、找答案等附加服务。
- 2、"仅部分预览"的文档,不可在线预览部分如存在完整性等问题,可反馈申请退款(可完整预览的文档不适用该条件!)。
- 3、如文档侵犯您的权益,请联系客服反馈,我们会尽快为您处理(人工客服工作时间:9:00-18:30)。
微通道反应器的高效精细化工时代
微通道连续流反应器技术基于独特的非金属耐腐材质和卓越的传热-传质性能设计,可有效强化合成反应条件,是对传统化工小试和中试生产装备的重大革新,它打开了新时代高效化学研发和生产的窗口。
让化学反应时间从几小时或几十小时缩短到几十秒到几分钟,同时解决强腐蚀、易爆、高能耗、高溶剂消耗和高污染排放等诸多难题,这正是微通道反应器独有的魅力。
微通道反应器技术已应用于医药、农药和染料中间体合成。
常见的应用领域包括选择性硝化、浆态加氢、重氮偶合、磺化、卤化和氧化等反应,以及在材料和催化剂制备中用于纳米材料合成、特种试剂制备如格氏试剂和过氧化试剂等。
微反应器技术,特别是液相微反应器技术最早于上世纪90年代后期在德国出现。
当时根据原子能技术民用化项目的要求,微型机械加工技术以及微通道结构热交换器被用于处理强放热和高危险化学品。
德国在1997年开发成功微米级高硼硅玻璃微通道反应器用于偶氮偶合反应。
微反应器技术很多年来一直徘徊在研发和科研应用阶段,停留在“微小”的流体通量水平上,主要用于实验室小剂量化学合成路线的研究和筛选。
将微反应器优良的传质和传热效能体现在大规模的产业化装置中,一直是该领域的瓶颈。
但现在已经成为具有生产成本优势的工业化利器。
据统计,在精细化工反应中,大约有20%的反应可以通过采用微流体化工技术,在收率、选择性或安全性等方面得到提高。
微化工技术可用于高效换热、高效混合、强放热反应过程,高附加值精细化学品、剧毒物质、超细/纳米颗粒以及高能炸药的生产过程。
微流体化工技术涉及物理、化学、化工、生物、材料、微电子以及微机械加工等诸多领域,学科交叉性强,其基本原理是通过特殊设计的微结构单元对流经的反应流体进行切割,实现反应流体见以微米时空尺寸,甚至更小进行混合和换热。
与传统化工技术相同,微化工技术也使用反应器、混合器、换热器等单元组件。
但同传统化工工艺相比,微化工工艺微反应工艺实现了对传质传热的真正强化,使化学过程更快的传质传热、更好的时空收率、更安全环保、更经济节能、占地面积小,大大降低投资成本及能耗。
技术优势明显。
根据Lonza对化学反应的动力学分类(A-C三类,反应时间从100ms到10 min),微反应器的常规应用准则如下:
A类化学反应(瞬间反应),只单独使用微结构反应元件即可:如微混合器(通常内部设计有微热换器),不需要连接管线;
B类化学反应(快速反应),可将微反应器和常规的流动式反应器组合使用:如微混合器加延时管线;
C类化学反应(慢反应),使用常规的流动式反应器:如管式反应器,反应器的管径最好是阶梯式增加,以减少压降;
目前世界范围资源日趋减少,环境问题越来越严重的情况下,微流体化工技术为一些危险、苛刻、环境影响严重的化工产品提供了一条先进安全的绿色化学工程路线,为未来化工行业的发展提供了一条先进安全的绿色化学工程路线,为未来化工行业的发展提供了一条有潜在意义的发展方向。
在制药、精细化学品和中间体的合成反应中,适于微反应器内进行的反应过程应包含下面的三类。
第一类:瞬间反应
反应半衰期小于1s,这类反应主要受微观混合效果控制,即受传质过程控制,如氯化、硝化、溴化、磺化、氟化、金属有机反应和生成微-纳米颗粒的反应]等;由于传质效果较差,故在传统尺度反应器内进行时,过程难以控制,且产品质量较差。
第二类:快反应
反应半衰期介于1 s~10 min之间,处于传质过程和本征动力学共同控制区域,混合效果对这类反应的影响较小、甚至可忽略不计;但当这类反应的生成焓较大
时,采用常规尺度反应器一般不能及时把热量移出,易造成局部温度过高,最终导致反应过程失控和副反应的发生,使反应选择性和产率降低;而利用微反应器的高效传热性能则可以使反应在较低温度梯度下平稳进行,反应过程易控,可提高目的产物的选择性和产率。
第三类:慢反应
反应半衰期大于10 min,处于本征动力学控制区域,此类反应理应更适合于间歇或半间歇釜式反应器;但对于仅在苛刻反应条件下才能发生的反应,如:反应在高温、高压条件下,反应物、产物均为剧毒物质或反应放热剧烈的反应等,若从生产过程安全角度考虑,则适于在微反应器内进行,可极大地提高过程安全性能。