异常工时管理办法
异常工时管理办法
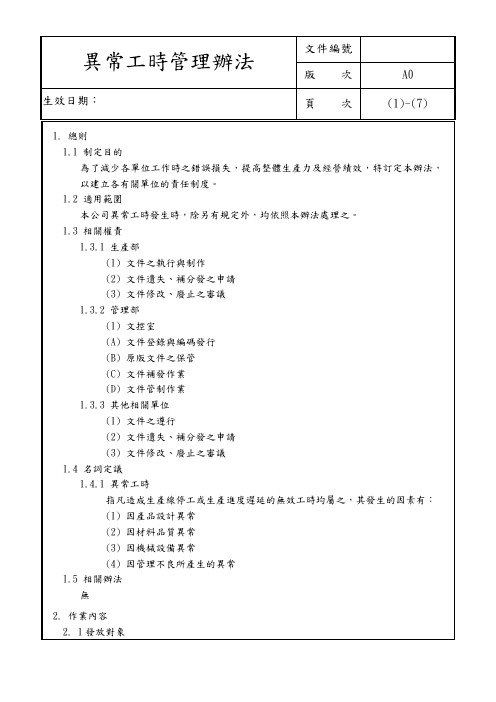
異常成本金額達到RMB30,000元才呈總經理(副董)行使核決。
2.3製造權限
2.3.1 生產線主管
(1) 填具項目
工令單號、型號、異常責任單位、異常原因、發生日期、起訖時間、異常工時、停工人數、每人停工時間、填表單位。
(2) 填具時間
發生異常狀況當天。
(3) 填具依據
依實際狀況填製。
(6) 工程單位責任
(A) 設備故障或故障後未及時修復。
(B) 試作遲延,造成生產遲延、停頓。
(7) 業務單位責任
顧客需求未事先知會主管,而造成臨時換線,生產單位人員停工時間。
(8) 協力廠商責任
(A) 交貨延遲。
(B) 進貨品質不良,生產線製造時產生損耗工時。
(C) 缺料。
(9) 其他責任
特殊案例處理後,列入慣例判斷。
(3) 如有特殊情況,則於隔月初召開異常損失檢討會,確定異常解決方法。
2.6.4 Leabharlann 失金額計算(1) 損失工時換算金額,為便於計算,以人民幣28元/H為原則,再依每小時平均工資率計算。
(2) 本辦法實施之初,損失金額以每小時人民幣28元為計算之標準,其後再依實際情況作適度調整訂正。
(3) 全線損失總工時(H)28(元)=損失金額。
2.5.2 責任單位判定
凡造成生產線停工、待料、生產進度遲延之工時損失,皆須追查其原因及責任單位以求改進。
(1) 管理單位責任
(A) 貨物稅單未購買。
(B) 進貨遲延,未事先通知生管單位,造成生產停工待料。
(C) 採購下單購備時間不足,進料遲延。
(D) 進料不全造成缺料。
(E) 未下單採購。
(F) 廠商未進貨。
1.3.2 管理部
异常工时管理制度

异常工时管理制度一、背景和意义在现代社会,工作生活节奏加快,人们的工作压力也越来越大。
许多企业为了追求利润最大化,会采取加班加点的方式来完成任务,导致员工的工作时间超出正常范围,严重影响员工身心健康和工作效率。
因此,建立健全的异常工时管理制度具有重要的意义,可以保障员工的合法权益,促进企业的可持续发展。
二、异常工时的定义异常工时指在法定工作时间范围内,员工因工作需要而超出正常工作时间的情况。
这包括延长工作时间、加班以及夜班等情况。
三、异常工时管理的原则1. 合法合规原则:异常工时管理须符合国家和地方相关法律法规,并遵循公平、公正的原则,保护员工的合法权益。
2. 稳健可持续原则:异常工时管理制度应当符合企业的可持续发展战略,平衡企业的生产运营和员工的工作生活。
3. 人性关怀原则:在安排员工异常工时时,须关注员工的身心健康,确保员工的工作时间合理合法。
四、异常工时管理的内容1. 建立健全的工时管理制度:企业应当制定明确的工时管理制度,规定员工的正常工作时间、加班和延时加班的申请流程、报酬标准以及工时记录和管理等内容。
2. 加班管理:企业应当严格控制员工的加班时间,加班应当由员工自愿选择,并在严格控制下进行,同时,应当给予相应的加班报酬。
3. 夜班管理:夜班工作的员工应当获得额外的健康保障和报酬,企业应当提供相应的安全保障措施。
4. 工时记录和管理:企业应当建立完善的工时记录系统,及时记录员工的正常工作时间和加班情况,确保员工的工时不超过法定范围。
五、异常工时管理的实施1. 管理部门的责任:管理部门应当建立健全异常工时管理制度,保障不超规定工时,并提供必要的培训和指导。
2. 员工的责任:员工应当遵守企业的工时管理制度,合理安排自己的工作时间,不得擅自违背规定加班或延时加班。
3. 各部门的协作:企业各部门应当相互配合,共同做好异常工时管理工作,确保员工的工时不超标,并及时解决异常情况。
4. 员工权益的保障:企业应当建立健全的员工权益保障机制,对于违反工时管理制度的情况要依法处理并给予相应的惩罚。
【质量部】异常工时处理规范

1目的明确电器事业部异常工时责任归属,提升各部门协同处理异常的响应速度,特制订本制度。
2定义2.1生产异常:指造成生产停工或生产进度延迟的情形。
2.2异常工时:由生产异常造成的超过标准工时的无效工时,称为异常工时。
供应商方面,0.5小时以上的计入异常工时统计,内部0.5小时以上的计入异常工时的统计。
3职责3.1供应部生产处3.1.1产线班长:负责填写《异常工时费用承担表》,保证异常描述和工时数的准确性并通知相关人员到异常发生地现场确认。
3.1.2生产部异常工时统计员:负责异常数据初步审核及录入。
3.2质量部3.2.1巡检:第一时间对生产过程中出现的质量异常进行处理,不能给出处理结果的及时反馈相关工程师及上级,以及作为第三方对产线产生的异常工时数据进行核实。
3.2.2质量工程师:对质量问题引起的异常工时责任进行初判,推进质量异常问题改善闭环。
3.3电器部总经理:负责有争议的异常工时责任判定,促进异常工时制度正常运行。
3.4供应部采购处:负责跟踪各产品线供应商异常工时费用回馈情况,至账务费用抵冲发生产部门人力成本,处理进度及时反馈成本专员。
3.5财务部:负责月度异常工时费用抵冲工作;负责异常工时补偿款的到账确认。
3.6成本专员:负责公司内外部损失工时台账建立及费用执行情况跟踪。
4程序/规定/要求/4.1生产异常处理流程4.1.1异常发生时,生产部应立即通知相关部门前来确认处理,并报告直属上级。
a)因质量问题引起的异常由产线巡检第一时间确认处理,并通知质量工程师现场解决(如本人出差无法现场确认,须指定代理人处理)。
b)因待料引起的停线由生产班长第一时间通知计划专员,由计划处回复产线复产信息并判定责任部门。
4.1.2生产班长填写《异常工时费用承担表》,当日下班时将费用承担表交于车间主任处。
质量异常由巡检判定责任部门,待料异常由计划专员判定;4.1.3判定为外部供方问题,由采购部当日通知供应商确认信息,24H内无回复的默认同意判定;采购部依据接收到的处罚明细执行处罚并回复成本员。
生产异常管理规定
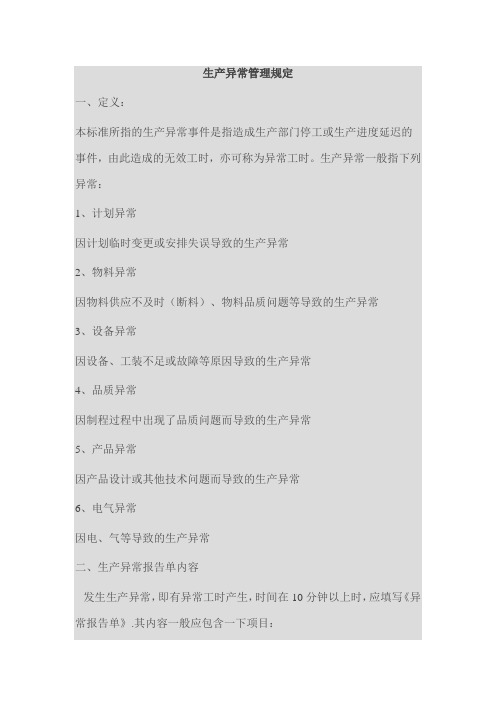
生产异常管理规定一、定义:本标准所指的生产异常事件是指造成生产部门停工或生产进度延迟的事件,由此造成的无效工时,亦可称为异常工时。
生产异常一般指下列异常:1、计划异常因计划临时变更或安排失误导致的生产异常2、物料异常因物料供应不及时(断料)、物料品质问题等导致的生产异常3、设备异常因设备、工装不足或故障等原因导致的生产异常4、品质异常因制程过程中出现了品质问题而导致的生产异常5、产品异常因产品设计或其他技术问题而导致的生产异常6、电气异常因电、气等导致的生产异常二、生产异常报告单内容发生生产异常,即有异常工时产生,时间在10分钟以上时,应填写《异常报告单》.其内容一般应包含一下项目:1、生产批号填具发生异常时正在生产的产品的生产批号或制令号.2、生产产品填具发生异常时正在生产的产品名称、规格、型号。
3、异常的发生单位填具发生异常的制造单位名称4、发生日期填具发生异常的日期5、起止时间填具发生异常的起始时间、结束时间6、异常描述填具异常发生的详细状况,尽量用量化的数据或具体的事实来陈述7、停工人数、影响度、异常工时分别填具受异常影响而停工的人数、因异常而导致时间损失的影响度8、临时对策有异常发生的部门填具应对异常的临时应急措施9、填表单位由异常发生的部门经办人员或主管填写10、责任单位对策(根本对策)由责任单位填异常的处理对策三、使用流程1、异常发生时,发现异常的部门主管应立即通知技术部门或相关责任单位,前来研究对策,加以处理,并报告直属上级.2、生产部门会同技术部门、责任单位采取异常的临时应急对策并加以执行,以降低异常带来的影响.3、异常排除后,由生产部门填写《异常报告单》并转给责任单位。
4、责任单位填具异常处理的根本对策,以防止异常的重复发生,并将《异常单》反馈生产部.5、生产部接单后,将一联复印给财务部6、财务部保存异常报告单,作为向厂商索赔的依据及制造费用的会计凭证7、主管部门保存异常报告单,作为生产进度控制点,并为生产计划提供参考依据8、生产部应对责任单位的根本对策的执行结果进行跟踪。
异常工时管理方法

异常工时管理办法
一、定义
1.工时损失是直接人员投入工时中的非正常工时;
2.工时损失分为额外工时和异常工时;
3.额外工时包含:打样、试产、计划性换线、盘点、设备机台保养、培训等非异常造成的有价值工时损失;
4.异常工时包含:非计划换线、工程变更、返工、特采、待料、来料不良、制程异常、设备/工具异常等异常造成的无价值工时
损失。
二、目的
为明确各类工时损失责任归属,有效管制人工成本,体现完整的损失项目及时间,以降低损失,提高工时的有效利用率以及规范工时损失填写,签核,转嫁依序进行,特制定本规定。
三、范围
适用于公司所有异常工时损失管理。
四、职责
1.工程部负责异常工时损失管理制度的制定、修改及执行过程中的监督;
2.生产部及相关部门负责过程实施和申报;
3.工程部部负责异常工时损失的标准工时审核确认;
4.工程部负责本制度的核准,及异常工时损失争议的判定。
五、工时损失类别及责任界定
七、执行
以上规定自本文件发行之日时立即实施。
制定:会签:审核:。
电子厂异常工时管理制度

一、总则为了规范电子厂生产过程中的异常工时管理,提高生产效率,确保产品质量,保障员工权益,特制定本制度。
二、适用范围本制度适用于电子厂所有员工,包括生产一线员工、技术人员、管理人员等。
三、异常工时定义异常工时是指因设备故障、原材料问题、工艺流程调整、人员操作失误等原因导致的非正常工时。
四、异常工时分类1. 设备故障:指生产设备出现故障,导致生产线停机或减产。
2. 原材料问题:指原材料质量问题或供应不足,导致生产线停机或减产。
3. 工艺流程调整:指因工艺流程调整导致生产线停机或减产。
4. 人员操作失误:指员工在操作过程中出现失误,导致生产线停机或减产。
五、异常工时报告流程1. 异常发生时,当班员工应立即向班组长报告。
2. 班组长接到报告后,应立即向生产部经理报告。
3. 生产部经理接到报告后,应立即组织相关人员进行分析,确定异常原因,并采取措施进行处理。
4. 处理完成后,生产部经理应向人力资源部报告异常工时情况。
六、异常工时处理措施1. 设备故障:(1)设备维修人员应立即进行设备维修,确保设备恢复正常运行。
(2)维修过程中,如需更换备品备件,应及时向采购部门提出申请。
(3)维修完成后,设备维修人员应向生产部经理报告维修情况。
2. 原材料问题:(1)采购部门应立即与供应商联系,核实原材料问题,并采取措施解决问题。
(2)在原材料问题得到解决前,生产部经理应协调生产计划,确保生产线正常运转。
3. 工艺流程调整:(1)工艺部门应制定详细的工艺调整方案,并组织相关人员实施。
(2)工艺调整过程中,生产部经理应密切关注生产线运行情况,确保调整顺利进行。
4. 人员操作失误:(1)班组长应组织员工进行操作培训,提高员工操作技能。
(2)对操作失误导致的生产异常,班组长应进行现场指导,帮助员工纠正错误。
七、异常工时统计与分析1. 人力资源部负责对异常工时进行统计,每月向生产部经理报告。
2. 生产部经理根据统计结果,分析异常原因,提出改进措施。
质量异常返工工时管理规定
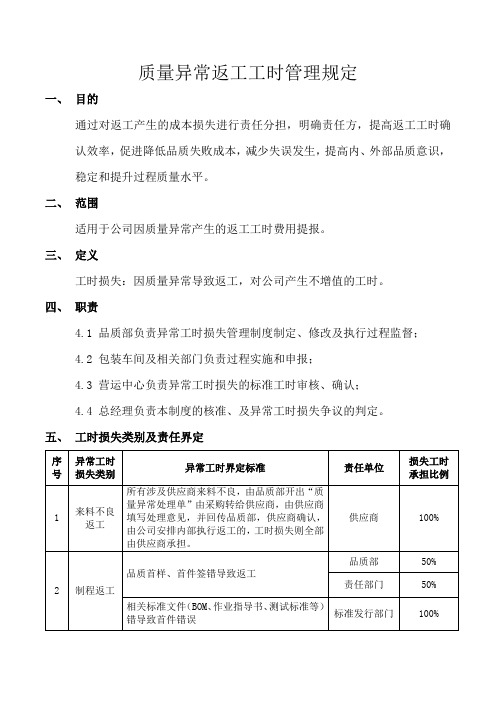
质量异常返工工时管理规定
一、目的
通过对返工产生的成本损失进行责任分担,明确责任方,提高返工工时确认效率,促进降低品质失败成本,减少失误发生,提高内、外部品质意识,稳定和提升过程质量水平。
二、范围
适用于公司因质量异常产生的返工工时费用提报。
三、定义
工时损失:因质量异常导致返工,对公司产生不增值的工时。
四、职责
4.1 品质部负责异常工时损失管理制度制定、修改及执行过程监督;
4.2 包装车间及相关部门负责过程实施和申报;
4.3 营运中心负责异常工时损失的标准工时审核、确认;
4.4 总经理负责本制度的核准、及异常工时损失争议的判定。
五、工时损失类别及责任界定
六、作业流程
6.1返工作业规定
6.1.1 返工作业报表由组长负责填写,由车间主管审核,生产统计员
建档统计,工时损失统计表,需在返工完成后3天内完成。
6.1.2返工完成后,工时统计表需连同品质部开出的“质量异常处理单”
一同交给营运中心经理进行核对签名确认,总经理审批。
6.2 返工作业工时管理制度
工时损失必须如实记录填写返工工时,如发现隐瞒、乱报、虚报工时者,
经核实后对虚报部门申请人进行严重惩罚,同时追究部门负责人管理
责任。
6.3 异常工时追责(按13元/H核算),以品质处罚单的形式进行通报处理。
以上规定从2020年8月21日起实施。
会签:审批:。
异常工时管理办法

异常工时管理办法1.目的: 通过对异常工时的原因分析,并制订有效纠正措施,使异常工时得以管控, 以不断提升生产 效率,特制定本办法。
2. 范围 :适用于因各类异常产生的异常工时均属之3、定义:3.1 异常工时: 是指因各种原因造成生 产停工或生产进度延迟所导致的无效工时,称之为异常 工时。
生产异常一般包括计划异常、物料异常、设备异常、品质异常、产品 异 常、水电异常及人员异常等 。
(未包括正常工单转线工时) 4.1 生产部: 实施制程异常改善对策 , 负责对异常工时及因延误导致的失败成本的统计,对于产线的异常有产生异常工时的,生产开出《生产线异常损耗时间确认表》,并统计因延误导致的失败工时给到责任单位确认 4.2 品质部:制程数据统计 ,品质异常反馈与提报 ,异常状态的核实,物料品质 的保证以及外观不 良异常的主导, 并负责改善效果的追踪。
4.3 制工部:负责制程功能性品质异常 、工艺引起的异常、设备异常、新产品出 现流程异常的 主导分 析及改善方案的提出,相关重工流程的制订及异常工时的审核。
5.4 开发部: 试产品质异常改善与异常工时吸收 ;产品重大设计品质缺陷 改善与异常工时吸收 .5.5 PMC 部:负责物料的及时供应,生产计划的制订与调配,出现异常时生产的及时调度及物 料上的及时配合,保证生产顺畅。
5.6 行政部:保证水电的正常及人员的招聘。
5.7 财务部:对异常的协调及损耗工时稽核,尽量将损耗 工时控制在公司合理的范围内。
5. 作业 内容:5.1 因换线、调机及设备异常 (产线上设备 )处理等引起的异常 工时在 15 分钟以内可由公司吸收,超过 15 分钟由生产提报异常工时 和 异常状况,产线以外设备(如加工机器)应看是 否影响生产,影响生产由工程吸收,不影响生产维修工时(经上级批准同意 )应由公司吸 收, IE核定异常工时。
5.2 异常工时的判定:外观不良引起的异常工时由品质部 IPQC 判定责任单位,包括超声外观不良及超声后跌落 问题3.2 计划异常:因生产计划临时变更或 3.3 物料异常:因物料供应不及(断料 3.4 设备异常:因设备、工装夹具不足 3.5 品质异常:因制程中出现了品质问 3.6 产品异常:因产品设计或其他技术 3.7 水电异常:因水、气、电等导致的 3.8 人员异常:因招聘问题导致人力不4.权责:安排失误等导致的异常。
- 1、下载文档前请自行甄别文档内容的完整性,平台不提供额外的编辑、内容补充、找答案等附加服务。
- 2、"仅部分预览"的文档,不可在线预览部分如存在完整性等问题,可反馈申请退款(可完整预览的文档不适用该条件!)。
- 3、如文档侵犯您的权益,请联系客服反馈,我们会尽快为您处理(人工客服工作时间:9:00-18:30)。
异常工时管理办法1.目的:通过对异常工时的原因分析,并制订有效纠正措施,使异常工时得以管控,以不断提升生产效率,特制定本办法。
2. 范围:适用于因各类异常产生的异常工时均属之。
3、定义:异常工时:是指因各种原因造成生产停工或生产进度延迟所导致的无效工时,称之为异常工时。
生产异常一般包括计划异常、物料异常、设备异常、品质异常、产品异常、水电异常及人员异常等。
(未包括正常工单转线工时)计划异常:因生产计划临时变更或安排失误等导致的异常。
物料异常:因物料供应不及(断料)、物料品质问题等导致的异常。
设备异常:因设备、工装夹具不足或故障等原因而导致的异常。
品质异常:因制程中出现了品质问题而导致的异常,也称为制程异常。
产品异常:因产品设计或其他技术问题而导致的异常,也称机种异常。
水电异常:因水、气、电等导致的异常。
人员异常:因招聘问题导致人力不足及公司管理问题导致人员的怠工异常。
4 .权责:生产部:实施制程异常改善对策, 负责对异常工时及因延误导致的失败成本的统计,对于产线的异常有产生异常工时的,生产开出《生产线异常损耗时间确认表》,并统计因延误导致的失败工时给到责任单位确认.品质部:制程数据统计,品质异常反馈与提报,异常状态的核实,物料品质的保证以及外观不良异常的主导,并负责改善效果的追踪。
制工部:负责制程功能性品质异常、工艺引起的异常、设备异常、新产品出现流程异常的主导分析及改善方案的提出,相关重工流程的制订及异常工时的审核。
开发部:试产品质异常改善与异常工时吸收;产品重大设计品质缺陷改善与异常工时吸收.PMC部:负责物料的及时供应,生产计划的制订与调配,出现异常时生产的及时调度及物料上的及时配合,保证生产顺畅。
行政部:保证水电的正常及人员的招聘。
财务部:对异常的协调及损耗工时稽核,尽量将损耗工时控制在公司合理的范围内。
5. 作业内容:因换线、调机及设备异常(产线上设备)处理等引起的异常工时在15分钟以内可由公司吸收,超过15分钟由生产提报异常工时和异常状况,产线以外设备(如加工机器)应看是否影响生产,影响生产由工程吸收,不影响生产维修工时(经上级批准同意)应由公司吸收,IE核定异常工时。
异常工时的判定:外观不良引起的异常工时由品质部IPQC判定责任单位,包括超声外观不良及超声后跌落问题在内。
产品性能不良引起的异常工时由工程PE判定责任单位,判定结果须及时知会给责任单位,如有异议及时申请裁决。
因工艺引起的异常、设备异常、新产品出现流程异常由工程部主导,具体可参照《制程品质异常处理管理办法》,异常工时的裁决依《标准工时管理办法》执行。
异常工时的责任承担部门5.3.1 因新产品试产所产生的异常工时由公司承担,工时必须要经过IE实际确认为准。
5.3.2 生产线已按生产排程安排生产,因欠料造成生产停线所产生的延误工时由物控承担(如因供应商交货不及时导致欠料由物控承担,如因物料品质问题导致欠料由品质及资源转供应商承担)。
由供应商承担全部工时。
5.3.3 如因临时插单或客户紧急要求出货,由此产生的换线延误工时由公司承担。
5.3.4 超声波异常引起的额外工时的处理:5.3.4. 1 如因产线未能按流程提前30分钟发单通知调模员调模,则所产生的延误由产线承担。
5.3.4.2 如因调模不及时,或者按照正常的情况下可以调好(调模员的操作技能影响),由此产生的延误工时由制工部承担。
调模员承担20%,制工副主任承担10%、制工主任承担10%、制工经理承担10%、公司承担50%。
5.3.4.3 如因超声模具及超声波设备性能上的问题影响到生产,由此产生的延误工时由公司承担。
5.3.4.4调模员无法调好时,调模人员应及时通知ME工程师或以上人员及品质部对可否生产作出判断,产生的延误再根据具体原因状况来由ME来定相应异常工时承担的责任部门。
5.3.4.5调模员负责调模,品质部负责确认,确认合格下拉生产后再出现因品质异常需再来调整超声工艺而导致生产的延误,由品质部承担(超声波参数未发生变异者),若超声波发生变异引发的异常工时由工程部承担。
调模员5.3.6.1因生产紧急针对定制品首次来料不良申请特采使用部分(需要加工、挑选使用),在生产使用时造成延误工时建议挂公司,5.3.6.2不良比率在目前AQL允收水准范围内造成生产挑选、加工造成延误工时部分建议由公司吸收,但若属于供应商明显工艺不符、偷工减料原因造成,由生产确认后转品质部与厂商直接沟通确定转嫁供应商,IPQC及时开出《品质异常处理单》并附不良样品转品质部IQC。
承担30%,制工副主任承担10%、制工主任承担10%、制工经理承担10%、公司承担40%。
5.3.5测试仪器及夹具异常的处理:5.3.5.1如因产线未能按流程提前30分钟发单通知制工设备员,则所产生的延误由产线承担。
5.3.5.2生产制程中发生测试仪器及测试夹具异常且严重影响到生产时,生产组长立即通知到制工测试技术人员,制工技术人员必须在接到通知5分钟内赶到现场处理,15分钟内无法处理时必须给出临时解决方案,因制工未及时处理造成的延误工时全部由制工承担。
技术人员承担30%,制工副主任承担10%、制工主任承担10%、制工经理承担10%、公司承担40%。
5.3.5.3制工分析因仪器设备损坏无法短时间修复,并且已经及时告知生产,从仪器损坏至制工告知生产期间造成的工时超过15分钟外的损耗由制工承担,当制工已及时告知生产后,而产线未做及时处理的,由此所产生的工时损耗由生产承担,否则,包括因异常而临时转线的工时由责任单位承担。
5.3.5.4 当自动测试系统硬件故障时, 30分钟内由公司吸收。
5.3.6材料品质异常:5.3.6.3不良比率超出AQL允收水准,IQC可以抽检到而实际未有检验到部分挂IQC(目前检验标准可以发现问题),同时对应损失转嫁供应商;若属于双方均未进行管制,且属于目前不可控部分,异常工时暂挂公司,但最终实际损失由生产确认后转品质部与厂商直接沟通确定转嫁供应商,IPQC 及时开出《品质异常处理单》并附不良样品转品质部IQC。
5.3.6.5偶发性现象,如QA抽检高压不良1个,电性不良1个,属电子物料不明原因损坏,非人为焊锡品质问题等之INT不良,产生的异常工时由公司承担,工时必须要经过IE实际确认为准。
5.3.6.6属设计隐含性问题且IQC在静态检测无法检测所造成制程异常,其异常工时挂开发部。
开发部承担60%,公司承担40%。
5.3.6.7经我司认可的供应商提供之承认书,与我司相关资料之间存在差异,如尺寸、无公差等,而造成制程过程装配之匹配不良,该异常工时由开发部或制工部承担。
开发承担30%、制工承担30%、公司承担40%。
5.3.7功能性品质异常5.3.7.1生产制程发生重大的产品功能性不良而产生的延误工时由制工判定的责任单位承担。
5.3.7.2如制工提供的解决方案对改善无效果导致产品的二次及多次返工,由此产生的延误工时及报废由制工承担。
技术人员承担30%,制工副主任承担10%、制工主任承担10%、制工经理承担10%、公司承担40%。
5.3.7.3若解决方案经过相关会议决定后实施并有较好的改善效果但仍有一定的损失时此损失由责任单位承担。
5.3.7.4制工在处理完产线电性能异常后,牵涉到消耗库存原材料所产生的无效工时由公司承担,工时必须要经过IE实际确认为准。
5.3.7.5元件参数差异与产品设计存在匹配性问题所造成的无效工时由公司承担,工时必须要经过IE实际确认为准。
5.3.7.6因客退品重工所造成的无效工时:5.3.7.产品退货原因明确部分由责任单位承担。
5.3.7.产品退货原因不明确或有争议部分暂时由公司承担。
5.3.7.7因环境因素(温、湿度)变化造成产品HI-POT不良:5.3.7.温、湿度不可控部分,为了保证产品品质,PE要求需增加人力控制或重工所造成的无效工时由公司承担。
5.3.7.温、湿度可控部分,为了保证产品品质,PE要求需增加人力控制或重工所造成的无效工时由责任部门承担。
5.3.8外观不良异常:5.3.8.1生产制程中发生外观不良并严重超标时,IPQC主管如无法决定时必须立即上报处理,由此产生的异常工时由责任单位承担,如因未及时处理造成的工时及报废由生产部承担。
5.3.8.2如生产未按工程与品质部制定的方案执行所造成的损失由生产承担。
5.3.9产品异常的处理:5.3.9.1在生产制程中发生因产品本身设计问题所造成品质异常所产生的延误工时及材料报废由开发承担,生产统计好工时、报废成本。
开发部承担60%、公司承担40%。
5.3.10水电异常的处理:5.3.10.1当生产车间的用电线路发生故障并严重影响到生产,生产立即通知电工,若不能在30分钟内解决需告知产线以便产线作重新调整安排。
若在30分钟内不得到解决且未及时告知产线所产生的延误工时由总务部承担。
5.3.10.2制工部每天早上定时将空压机打开,保证生产设备正常用气,如因设备不能正常运转而产生的延误工时由制工部承担。
技术人员承担30%,制工副主任承担10%、制工主任承担10%、制工经理承担10%、公司承担40%。
5.3.11资料(或资料错误)与实物不符影响到的异常:5.3.11.1当物料与最新BOM不符,又未有代用单,导致停线,则所有的异常工时全部由责任单位承担;5.3.11.2当实物与资料不符,或与各种标准资料不符的,铭牌、DC线图纸与实物不一致导致停线的,所有异常工时及报废物料由开发承担,如BOM、作业指导书错误导致产线产生异常工时及报废的则由制工承担。
技术人员承担30%,制工副主任承担10%、制工主任承担10%、制工经理承担10%、公司承担40%。
5.3.11.3制工出的重工流程错误,导致重复性重工的,则产生的异常工时及报废物料由制工承担。
技术人员承担30%,制工副主任承担10%、制工主任承担10%、制工经理承担10%、公司承担40%。
5.3.11.4物料与供应商承认书一致,到产线使用时因原材料匹配问题而产生的品质异常,其异常工时将由开发或制工承担。
开发承担40%、制工承担40%、公司承担20%。
5.3.12未按流程或标准作业产生的异常5.3.12.1PMC未按流程直接量产,出现品质隐患而导致返工产生的异常工时及报废物料由PMC部承担;(如果影响交期,经公司同意直接量产,出现品质隐患由公司承担。
)。
PMC部承担60%、公司承担40%。
5.3.12.2生产未按SOP、操作流程作业,IPQC、PE及IE发现后要求重工,产生的异常工时及报废物料全部由生产承担。
5.3.12.3品质异常发生时,生产未按工程给的品质异常处理临时对策执行者,IPQC或制工要求返工而产生的异常工时和报废物料全部由生产承担。
5.3.12.4品管及制工人员在正常下拉的合格品内抽检发现有工艺不良品,如短路、空焊等不良要求返工时,产生的异常工时及报废物料由生产承担。