裂纹扩展的扩展有限元(xfem)模拟实例详解
ABAQUS平台的扩展有限元方法模拟裂纹实现
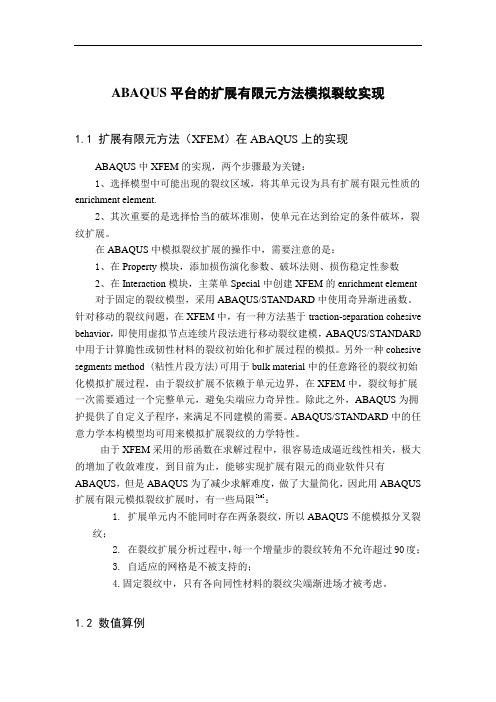
ABAQUS平台的扩展有限元方法模拟裂纹实现1.1 扩展有限元方法(XFEM)在ABAQUS上的实现ABAQUS中XFEM的实现,两个步骤最为关键:1、选择模型中可能出现的裂纹区域,将其单元设为具有扩展有限元性质的enrichment element.2、其次重要的是选择恰当的破坏准则,使单元在达到给定的条件破坏,裂纹扩展。
在ABAQUS中模拟裂纹扩展的操作中,需要注意的是:1、在Property模块,添加损伤演化参数、破坏法则、损伤稳定性参数2、在Interaction模块,主菜单Special中创建XFEM的enrichment element对于固定的裂纹模型,采用ABAQUS/STANDARD中使用奇异渐进函数。
针对移动的裂纹问题,在XFEM中,有一种方法基于traction-separation cohesive behavior,即使用虚拟节点连续片段法进行移动裂纹建模,ABAQUS/STANDAR D 中用于计算脆性或韧性材料的裂纹初始化和扩展过程的模拟。
另外一种cohesive segments method (粘性片段方法)可用于bulk material中的任意路径的裂纹初始化模拟扩展过程,由于裂纹扩展不依赖于单元边界,在XFEM中,裂纹每扩展一次需要通过一个完整单元,避免尖端应力奇异性。
除此之外,ABAQUS为拥护提供了自定义子程序,来满足不同建模的需要。
ABAQUS/STANDARD中的任意力学本构模型均可用来模拟扩展裂纹的力学特性。
由于XFEM采用的形函数在求解过程中,很容易造成逼近线性相关,极大的增加了收敛难度,到目前为止,能够实现扩展有限元的商业软件只有ABAQUS,但是ABAQUS为了减少求解难度,做了大量简化,因此用ABAQUS 扩展有限元模拟裂纹扩展时,有一些局限[16]:1.扩展单元内不能同时存在两条裂纹,所以ABAQUS不能模拟分叉裂纹;2.在裂纹扩展分析过程中,每一个增量步的裂纹转角不允许超过90度;3.自适应的网格是不被支持的;4.固定裂纹中,只有各向同性材料的裂纹尖端渐进场才被考虑。
基于xfem的垂直于双材料界面的裂纹扩展问题

文章主题:基于xfem的垂直于双材料界面的裂纹扩展问题在材料科学和工程领域,裂纹扩展问题一直是一个备受关注的研究课题。
特别是在双材料界面上的裂纹扩展问题,由于双材料特性的不均匀性和复杂性,增加了研究和分析的难度。
在本文中,我们将从基于xfem(扩展有限元法)的角度出发,探讨垂直于双材料界面的裂纹扩展问题,以期为这一领域的研究和实际应用提供新的思路和方法。
一、概述垂直于双材料界面的裂纹扩展问题是指在两种材料的交界面上,裂纹在垂直方向上的扩展行为。
这种情况下,裂纹扩展的受力和受约束条件都受到了双材料特性的影响,需要深入分析和研究。
传统的有限元法在模拟和分析这种问题时存在一定的局限性,而xfem则能够有效地刻画裂纹的扩展路径和受力情况,因此成为了研究这一问题的有力工具。
二、裂纹模型的建立在进行垂直于双材料界面的裂纹扩展问题建模时,需要考虑双材料界面的影响,分析裂纹在材料间传播的受力情况和速度。
利用xfem,可以方便地将裂纹扩展路径和扩展速度等参数纳入模型中,通过数值计算得到裂纹扩展的演化规律和裂纹尖端的受力情况。
这有助于更准确地理解和分析垂直双材料界面上的裂纹扩展问题。
三、影响因素分析垂直于双材料界面的裂纹扩展受到诸多因素的影响,其中包括材料性质、裂纹尺寸、应力状态等。
通过xfem的数值模拟,可以分析不同因素对裂纹扩展行为的影响程度,揭示裂纹扩展过程中的关键因素和规律。
这有助于为材料设计和工程应用提供更可靠的参考依据。
四、工程应用与展望垂直于双材料界面的裂纹扩展问题在工程应用中具有重要意义,例如在复合材料结构的设计和评估中。
通过对裂纹扩展行为的深入研究和分析,可以为工程实践提供更有效的裂纹控制和结构安全性评估方法。
未来,基于xfem的裂纹扩展问题研究还可以结合人工智能算法和大数据分析等方法,进一步提高模型精度和计算效率,拓展应用领域和深化理论研究。
个人观点与总结垂直于双材料界面的裂纹扩展问题是一个复杂而又具有挑战性的研究领域,需要运用先进的数值模拟方法和理论分析手段来探讨和解决。
ABAQUS XFEM 柱面与平面滑动接触中裂纹的扩展xfem(step by step)

ABAQUS XFEM 柱面与平面滑动接触中裂纹的扩展xfem(step by step)
1.part部分:
plate模型为2D 变形壳体尺寸为0.5x0.2M(因为后面采用的是MPa,所以这里采用的是M,为了单位统一) 。
用partition命令将plate切割成装配图上面一样(尺寸0.24x0.06)Rigid模型为2D解析刚体尺寸为R0.06圆的下面部分的2/3半圆(看装配模型就知道)。
注意要在上面设置一个参考点,在load部分加载位移边界用。
wire模型2D变形线尺寸为0.01位置坐标(0.25,0.2),(0.25,0.19)线两端点的坐标,大家懂的。
添加一个装配图对照模型。
2.property部分这一部分尽量多用图片
主要设置了一下几部分的材料属性,用的材料为Q345-steel(因为刚好找到了它的应力应变数据)1、密度2、弹性属性3、塑性属性4、损失准则
5.interaction部分
1.首先创建contact controls,创建步棸菜单栏interaction->contact controls->create,参数的设置见下图:
2.裂纹的设置,创建步棸菜单栏special->crack->create->xfem ,区域的选择见下图
3其他包括相互作用的一些属性见下图
6.load部分
位移边界条件的加载如下图
7.Mesh部分
种子布置见下图
网格控制主要采取的是structured
8.Job就ok了,祝大家好运。
也同时感谢论坛里面帮助过我的朋友。
ABAQUS精选本FEM扩展元例子的详细图解
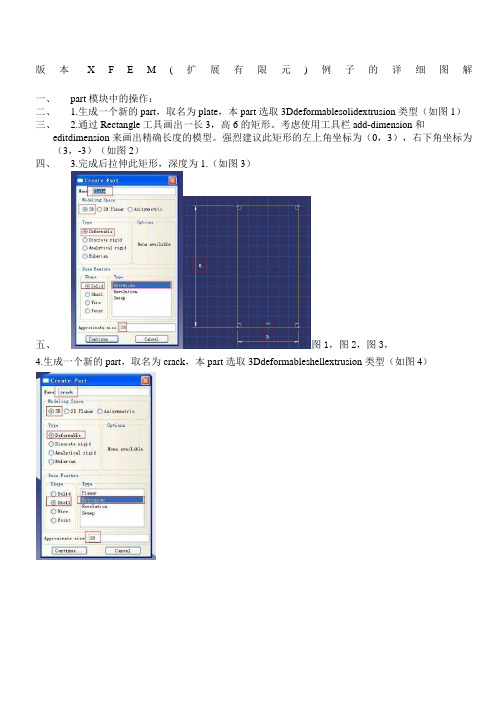
版本X F E M(扩展有限元)例子的详细图解一、part模块中的操作:二、 1.生成一个新的part,取名为plate,本part选取3Ddeformablesolidextrusion类型(如图1)三、 2.通过Rectangle工具画出一长3,高6的矩形。
考虑使用工具栏add-dimension和editdimension来画出精确长度的模型。
强烈建议此矩形的左上角坐标为(0,3),右下角坐标为(3,-3)(如图2)四、 3.完成后拉伸此矩形,深度为1.(如图3)五、图1,图2,图3,4.生成一个新的part,取名为crack,本part选取3Ddeformableshellextrusion类型(如图4)5.生成一条线,此线的左端点坐标为(0,),右端点坐标为(,)6.完成后拉伸此线,深度为1.(如图6)7.保存此模型为XFEMtutor(如图7),以后经常保存模型,不再累述。
8.在partPlate中分别创建4个集合,分别为:all,bottom,top和fixZ,各部分的内容如图8~11所示。
二、Material模块中的操作:1.创建材料elsa,其弹性参数为E=210GPa,泊松比为(如图12)最大主应力失效准则作为损伤起始的判据,最大主应力为(如图13)损伤演化选取基于能量的、线性软化的、混合模式的指数损伤演化规律,有关参数为G1C=G2C=G3C=42200N/m,=1.(如图14)2.创建一个SolidHomogeneous的section,名为solid(如图15),此section与材料elsa相联(如图16),并将此section赋给platepart(也就是集合all)(如图17)3.赋予材料取向,分别如图18~21所示。
三、划分网格:网格控制为:Hex型structured(如图22),单元类型为C3D8R(如图23)设置plate各边的网格种子为8,26,36(如图24),各边种子的个数不能改变(如图25)四、装配模块:选中plate和crack两个part,分别生成2个实体(如图26),生成一个参考点,参考点的坐标为(,-3,0)(如图27,28)。
基于XFEM的膜盘联轴器裂纹扩展模拟
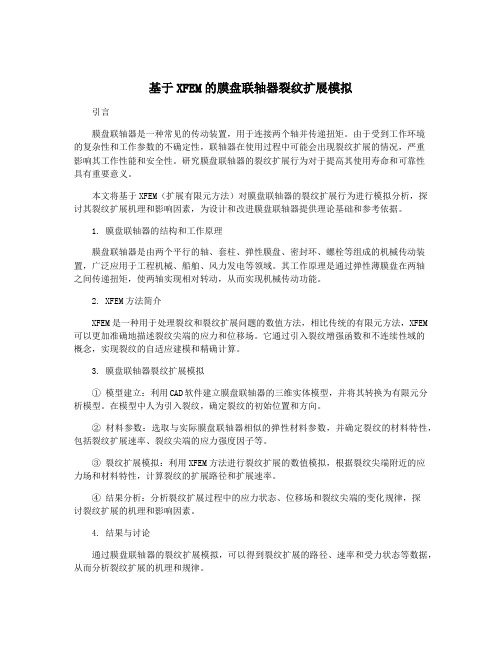
基于XFEM的膜盘联轴器裂纹扩展模拟引言膜盘联轴器是一种常见的传动装置,用于连接两个轴并传递扭矩。
由于受到工作环境的复杂性和工作参数的不确定性,联轴器在使用过程中可能会出现裂纹扩展的情况,严重影响其工作性能和安全性。
研究膜盘联轴器的裂纹扩展行为对于提高其使用寿命和可靠性具有重要意义。
本文将基于XFEM(扩展有限元方法)对膜盘联轴器的裂纹扩展行为进行模拟分析,探讨其裂纹扩展机理和影响因素,为设计和改进膜盘联轴器提供理论基础和参考依据。
1. 膜盘联轴器的结构和工作原理膜盘联轴器是由两个平行的轴、套柱、弹性膜盘、密封环、螺栓等组成的机械传动装置,广泛应用于工程机械、船舶、风力发电等领域。
其工作原理是通过弹性薄膜盘在两轴之间传递扭矩,使两轴实现相对转动,从而实现机械传动功能。
2. XFEM方法简介XFEM是一种用于处理裂纹和裂纹扩展问题的数值方法,相比传统的有限元方法,XFEM 可以更加准确地描述裂纹尖端的应力和位移场。
它通过引入裂纹增强函数和不连续性域的概念,实现裂纹的自适应建模和精确计算。
3. 膜盘联轴器裂纹扩展模拟① 模型建立:利用CAD软件建立膜盘联轴器的三维实体模型,并将其转换为有限元分析模型。
在模型中人为引入裂纹,确定裂纹的初始位置和方向。
② 材料参数:选取与实际膜盘联轴器相似的弹性材料参数,并确定裂纹的材料特性,包括裂纹扩展速率、裂纹尖端的应力强度因子等。
③ 裂纹扩展模拟:利用XFEM方法进行裂纹扩展的数值模拟,根据裂纹尖端附近的应力场和材料特性,计算裂纹的扩展路径和扩展速率。
④ 结果分析:分析裂纹扩展过程中的应力状态、位移场和裂纹尖端的变化规律,探讨裂纹扩展的机理和影响因素。
4. 结果与讨论通过膜盘联轴器的裂纹扩展模拟,可以得到裂纹扩展的路径、速率和受力状态等数据,从而分析裂纹扩展的机理和规律。
裂纹扩展路径:根据模拟结果可以得到裂纹扩展的路径和形态,研究裂纹扩展与联轴器结构的关系,探讨载荷大小和方向对裂纹扩展的影响。
裂纹扩展的扩展有限元(xfem)模拟实例详解
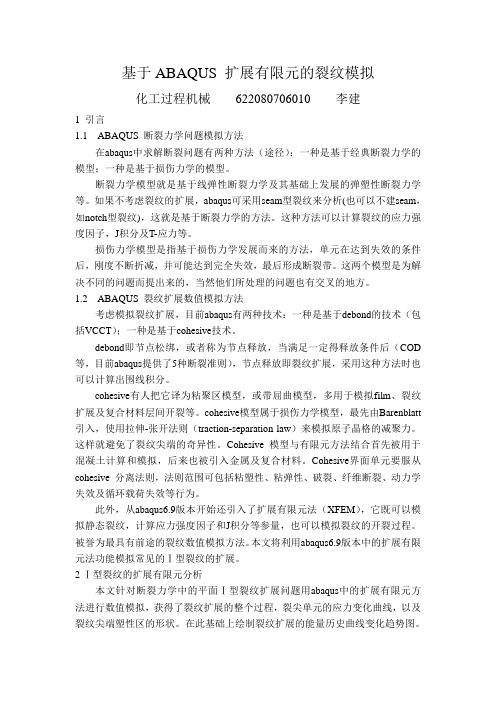
基于ABAQUS 扩展有限元的裂纹模拟化工过程机械622080706010 李建1 引言1.1 ABAQUS 断裂力学问题模拟方法在abaqus中求解断裂问题有两种方法(途径):一种是基于经典断裂力学的模型;一种是基于损伤力学的模型。
断裂力学模型就是基于线弹性断裂力学及其基础上发展的弹塑性断裂力学等。
如果不考虑裂纹的扩展,abaqus可采用seam型裂纹来分析(也可以不建seam,如notch型裂纹),这就是基于断裂力学的方法。
这种方法可以计算裂纹的应力强度因子,J积分及T-应力等。
损伤力学模型是指基于损伤力学发展而来的方法,单元在达到失效的条件后,刚度不断折减,并可能达到完全失效,最后形成断裂带。
这两个模型是为解决不同的问题而提出来的,当然他们所处理的问题也有交叉的地方。
1.2 ABAQUS 裂纹扩展数值模拟方法考虑模拟裂纹扩展,目前abaqus有两种技术:一种是基于debond的技术(包括VCCT);一种是基于cohesive技术。
debond即节点松绑,或者称为节点释放,当满足一定得释放条件后(COD 等,目前abaqus提供了5种断裂准则),节点释放即裂纹扩展,采用这种方法时也可以计算出围线积分。
cohesive有人把它译为粘聚区模型,或带屈曲模型,多用于模拟film、裂纹扩展及复合材料层间开裂等。
cohesive模型属于损伤力学模型,最先由Barenblatt 引入,使用拉伸-张开法则(traction-separation law)来模拟原子晶格的减聚力。
这样就避免了裂纹尖端的奇异性。
Cohesive 模型与有限元方法结合首先被用于混凝土计算和模拟,后来也被引入金属及复合材料。
Cohesive界面单元要服从cohesive 分离法则,法则范围可包括粘塑性、粘弹性、破裂、纤维断裂、动力学失效及循环载荷失效等行为。
此外,从abaqus6.9版本开始还引入了扩展有限元法(XFEM),它既可以模拟静态裂纹,计算应力强度因子和J积分等参量,也可以模拟裂纹的开裂过程。
XFEM实现裂纹扩展
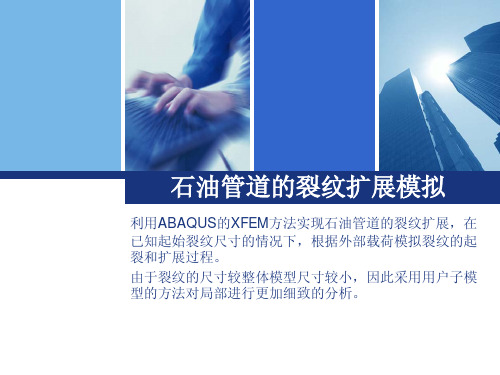
---因为专注,所以卓越!
网格划分
焊缝在管道的上下起始位置,造成几何模型的急剧变化, 导致网格不容易划分,因此,使用专业的的前处理软件 ANSA进行网格划分,使得焊缝的网格密度大于其他位置 的网格密度。
初始裂纹在焊缝中的位置
---因为专注,所以卓越!
分析过程
---因为专注,所以卓越!
I型裂纹扩展过程的动画演示
---因为专注,所以卓越!
II型裂纹扩展过程的动画演示
---因为专注,所以卓越!
ABAQUS采用XFEM模 案例2 块实现压力容器的裂纹 过程的模拟,如果图所 示,压力容器与外部连 接的接口处存在初始微 裂纹,当容器内压力达 到一定程度,裂纹开始 启裂并扩展。 模型的建模与应用针对 工程实例,很好的展现 了XFEM强大的裂纹扩 展功能。
石油管道的裂纹扩展模拟
利用ABAQUS的XFEM方法实现石油管道的裂纹扩展,在 已知起始裂纹尺寸的情况下,根据外部载荷模拟裂纹的起 裂和扩展过程。 由于裂纹的尺寸较整体模型尺寸较小,因此采用用户子模 型的方法对局部进行更加细致的分析。
一、XFEM模块功能简述
ABAQUS V6.9及其以后的版本将拓展有限元方法引入到 其分析中,并增加了新的模块XFEM,该方法可以认为是 有限元方法处理不连续问题的革命性变革。这是第一个将 XFEM商用化的软件。 固体力学中存在两类典型的不连续问题,一类是因材料特 性突变引起的弱不连续问题,这类问题以双材料问题和夹 杂问题为代表,其复杂性由物理界面处的应变不连续性引 起;另一类是因物体内部几何突变引起的强不连续问题, 这类问题以裂纹问题为代表,其复杂性由几何界面处的位 移不连续性和端部的奇异性引起。物体内部物理界面的脱 粘或起裂,是上述两类问题的混合。
裂纹扩展的扩展有限元xfem模拟实例详解
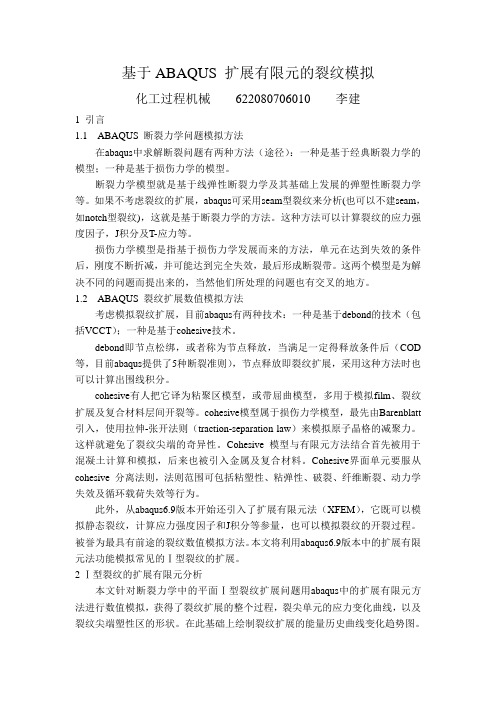
基于ABAQUS 扩展有限元的裂纹模拟化工过程机械622080706010 李建1 引言1.1 ABAQUS 断裂力学问题模拟方法在abaqus中求解断裂问题有两种方法(途径):一种是基于经典断裂力学的模型;一种是基于损伤力学的模型。
断裂力学模型就是基于线弹性断裂力学及其基础上发展的弹塑性断裂力学等。
如果不考虑裂纹的扩展,abaqus可采用seam型裂纹来分析(也可以不建seam,如notch型裂纹),这就是基于断裂力学的方法。
这种方法可以计算裂纹的应力强度因子,J积分及T-应力等。
损伤力学模型是指基于损伤力学发展而来的方法,单元在达到失效的条件后,刚度不断折减,并可能达到完全失效,最后形成断裂带。
这两个模型是为解决不同的问题而提出来的,当然他们所处理的问题也有交叉的地方。
1.2 ABAQUS 裂纹扩展数值模拟方法考虑模拟裂纹扩展,目前abaqus有两种技术:一种是基于debond的技术(包括VCCT);一种是基于cohesive技术。
debond即节点松绑,或者称为节点释放,当满足一定得释放条件后(COD 等,目前abaqus提供了5种断裂准则),节点释放即裂纹扩展,采用这种方法时也可以计算出围线积分。
cohesive有人把它译为粘聚区模型,或带屈曲模型,多用于模拟film、裂纹扩展及复合材料层间开裂等。
cohesive模型属于损伤力学模型,最先由Barenblatt 引入,使用拉伸-张开法则(traction-separation law)来模拟原子晶格的减聚力。
这样就避免了裂纹尖端的奇异性。
Cohesive 模型与有限元方法结合首先被用于混凝土计算和模拟,后来也被引入金属及复合材料。
Cohesive界面单元要服从cohesive 分离法则,法则范围可包括粘塑性、粘弹性、破裂、纤维断裂、动力学失效及循环载荷失效等行为。
此外,从abaqus6.9版本开始还引入了扩展有限元法(XFEM),它既可以模拟静态裂纹,计算应力强度因子和J积分等参量,也可以模拟裂纹的开裂过程。
- 1、下载文档前请自行甄别文档内容的完整性,平台不提供额外的编辑、内容补充、找答案等附加服务。
- 2、"仅部分预览"的文档,不可在线预览部分如存在完整性等问题,可反馈申请退款(可完整预览的文档不适用该条件!)。
- 3、如文档侵犯您的权益,请联系客服反馈,我们会尽快为您处理(人工客服工作时间:9:00-18:30)。
基于ABAQUS 扩展有限元的裂纹模拟化工过程机械622080706010 李建1 引言1.1 ABAQUS 断裂力学问题模拟方法在abaqus中求解断裂问题有两种方法(途径):一种是基于经典断裂力学的模型;一种是基于损伤力学的模型。
断裂力学模型就是基于线弹性断裂力学及其基础上发展的弹塑性断裂力学等。
如果不考虑裂纹的扩展,abaqus可采用seam型裂纹来分析(也可以不建seam,如notch型裂纹),这就是基于断裂力学的方法。
这种方法可以计算裂纹的应力强度因子,J积分及T-应力等。
损伤力学模型是指基于损伤力学发展而来的方法,单元在达到失效的条件后,刚度不断折减,并可能达到完全失效,最后形成断裂带。
这两个模型是为解决不同的问题而提出来的,当然他们所处理的问题也有交叉的地方。
1.2 ABAQUS 裂纹扩展数值模拟方法考虑模拟裂纹扩展,目前abaqus有两种技术:一种是基于debond的技术(包括VCCT);一种是基于cohesive技术。
debond即节点松绑,或者称为节点释放,当满足一定得释放条件后(COD 等,目前abaqus提供了5种断裂准则),节点释放即裂纹扩展,采用这种方法时也可以计算出围线积分。
cohesive有人把它译为粘聚区模型,或带屈曲模型,多用于模拟film、裂纹扩展及复合材料层间开裂等。
cohesive模型属于损伤力学模型,最先由Barenblatt 引入,使用拉伸-张开法则(traction-separation law)来模拟原子晶格的减聚力。
这样就避免了裂纹尖端的奇异性。
Cohesive 模型与有限元方法结合首先被用于混凝土计算和模拟,后来也被引入金属及复合材料。
Cohesive界面单元要服从cohesive 分离法则,法则范围可包括粘塑性、粘弹性、破裂、纤维断裂、动力学失效及循环载荷失效等行为。
此外,从abaqus6.9版本开始还引入了扩展有限元法(XFEM),它既可以模拟静态裂纹,计算应力强度因子和J积分等参量,也可以模拟裂纹的开裂过程。
被誉为最具有前途的裂纹数值模拟方法。
本文将利用abaqus6.9版本中的扩展有限元法功能模拟常见的Ⅰ型裂纹的扩展。
2 Ⅰ型裂纹的扩展有限元分析本文针对断裂力学中的平面Ⅰ型裂纹扩展问题用abaqus中的扩展有限元方法进行数值模拟,获得了裂纹扩展的整个过程,裂尖单元的应力变化曲线,以及裂纹尖端塑性区的形状。
在此基础上绘制裂纹扩展的能量历史曲线变化趋势图。
2.1 平面裂纹的几何模型几何模型的尺寸参数如图1所示,其中a=1.5m,b=3m,L=10m,厚度为1m。
上下两端分别承受25.32MPa的拉力。
图1 裂纹的几何示意图2.2 有限元模型有限元程序采用大型通用ABAQUS6.9软件,选用8节点六面体减缩单元(C3D8R)。
网格划分的模型如图2所示。
图2 网格图2.3 材料性能在有限元分析中假定材料为理想线弹性的,弹性模量E为2.1×105MPa,泊松比为0.3。
本文采用的是基于损伤力学演化的失效准则。
具体的参数设置如下。
损伤判据为最大主应力失效准则作为损伤起始的判据,最大主应力为84.4MPa。
损伤演化选取基于能量的、线性软化的、混合模式的指数损伤演化规律,有关参数为G1C= G2C= G3C=42200N/m,α=1。
2.4 边界条件和初始条件对于含有裂纹的平板,我们仅仅需要约束住它的刚体位移,保证在在平板两个断面施加应力载荷时,平板不会出现意外的刚体运动。
设置裂纹类型为扩展有限元裂纹,扩展区域是整个平板,扩展路径为任意路径。
由于计算裂纹扩展实际上是一个大变形问题,所以分析步骤的几何非线性一定要打开。
由于裂纹扩展本身是一个强烈的非连续问题,它将导致求解过程的迭代有可能出现不收敛的情况,另外,求解的增量步也会要求很小,这会导致求解时间很长。
因此非常有必要对求解过程做一些参数控制,以避免迭代不收敛导致的求解失败的情况的出现。
图3 裂纹体及其扩展区域图4 载荷及边界条件3 结果分析3.1 静态裂纹的应力强度因子及J积分的验证计算应力强度因子及J积分时,需要设置裂纹不能扩展,从而计算静态裂纹的应力强度因子,同时还要在历史变量输出中做相关的设置。
另外分析步也需要将几何非线性去除,因为裂纹没有扩展。
由此计算得到了裂尖在25.32MPa载荷下的Ⅰ型应力强度因子。
同时,我们根据断裂力学理论中关于此模型的理论解如公式(1),计算理论的应力强度因子。
最后得到的结果列于表1。
⎪⎭⎫⎝⎛=I b a F a K πσ (1)上式中a ,b 分别是裂纹体的几何尺寸,F 为关于a 和b 比值的函数,可以查表得到,本文中a 与b 的比值为0.5,查表得到F 的函数值为1.50。
表1 应力强度因子的对比表本文计算值 理论计算值 )(2/1m MPa K ⋅I58.6958.28由此可以计算相对误差为:1.06%,此误差显然属于5%的允许误差范围之内。
所以本文计算得到的应力强度因子是可信的。
此外,本文还利用此模型计算了静态裂纹的J 积分值,由于材料是理想线弹性的,所以J 积分与应力强度因子之间存在这样关系,如公式(2)。
EK J 2I = (2)本文在这里列出J 积分的变化趋势图,图中对比了公式(2)的理论解以及有限元结果。
从图中可以看出,两者是吻合的,说明了有限元模拟是正确的。
J 积分随加载的变化趋势图如图5所示。
红色实线表示的是理论结果,黑色点表示有限元结果。
0.02.0x1034.0x1036.0x1038.0x1031.0x1041.2x1041.4x1041.6x1041.8x104J 积分/N m -1Step time图5 J 积分历史曲线图3.2 裂纹扩展过程展示Step time=0.1143 Step time=0.3943 Step time=0.6743 Step time=0.7976 Step time=0.8708 Step time=0.9551Step time=0.9994 Step time=0.9998 Step time=1图6 裂纹扩展过程从上述的裂纹扩展过程的应力分布图,我们可以得到如下几点结论,证明我们的数值模拟具有一定的正确性。
首先,在裂纹尖端出现了应力集中,这是和断裂力学理论符合的。
其次,观察裂纹附近的应力分布,我们可以看到应力分布的趋势是与理论计算的塑性区的形状大致相同的,理论计算的塑性区形状如图7所示。
图7 理论上的塑形区形状图3.3 裂尖单元应力变化其次,考察裂尖单元的应力随载荷增加的变化。
实际上裂尖单元应力值的具体大小并没有意义,因为表征断裂韧强度的是应力强度因子和J 积分。
而单元应力随载荷增加导致的变化可以帮助我们理解裂尖单元在起裂到完全断裂的整个过程。
观察图8,我们可以大致得到这个裂尖单元参与断裂过程的整个历史。
首先,在应力加载的早些时候,裂尖单元的应力随着载荷的增加而增加,此时裂尖单元的应力并没有达到损伤判据的临界应力,所以单元没有起裂。
随着载荷的继续增加,应力值继续增加,当到大概0.7976左右时,裂尖的最大主应力达到了最大主应力损伤判据的临界值,于是裂纹起裂,直至完全裂开,单元的应力奇异性消失,裂尖单元转变为一个普通的非裂尖单元。
这个过程对应于图8中的右边应力增大后有急剧减小的曲线。
之后,由于载荷还没有完全加载完毕,所以裂尖单元在转变为普通单元之后随着载荷的继续增加,其单元应力又会随之在增加。
以上就是一个裂尖单元在整个加载过程中的单元应力历史变化的三个阶段。
最大主应力/M P aStep time图8 裂纹尖端单元应力历史曲线3.4 裂纹扩展分析如图9所示,载荷从零开始不断加载。
随着载荷的增加,裂尖处的单元应力也不断增加。
当裂尖处的最大主应力值达到临界值时,裂尖处的单元开始失效,裂纹开始穿过单元扩展,时间步大概是0.7976左右,此时裂尖处开始形成粘结裂纹(cohesive crack)。
从0-0.7976这个过程可以认为是裂纹孕育期。
之后随着裂尖处的能量释放率达到裂纹扩展阻力率G C 时,裂尖处的粘结裂纹开始扩展成真实裂纹,裂尖单元的XFEM值达到1。
裂尖处的单元损伤值达到临界值,时间步大概是0.9996左右。
此时认为这一结构开始失效,裂纹失去平衡,开始失稳扩展,真实裂纹开始形成并不断扩展。
从0.7976-0.9996这个过程可以认为是裂纹的萌生过程。
0.9996以后裂纹失稳扩展,结构失效。
从图中可以看出初始裂纹长度为12个单元距离,到最终加载结束时,真实裂纹长度为15个单元长度,粘结裂纹长度为7个单元长度。
图9 随加载历史扩展的动态裂纹图3.5 裂纹扩展的能量历史曲线绘出整个模型的总能量,动能,内能和外力功随计算过程的历史曲线如图10所示。
由图可以看出,总能量和动能在整个过程中并没有发生显著的增加,可以表明整个计算过程基本是稳定的。
而伪应变能在计算过程中有稍微的增长。
-1x101x102x103x104x105x106x107x108x109x10能量/N m -1Step time图10 裂纹扩展的能量历史曲线4 结论本文的工作是基于abaqus6.9版本的扩展有限元功能计算了Ⅰ型裂纹的扩展。
得到如下几点结论。
首先,本文计算了Ⅰ型裂纹的应力强度因子,结构表明计算值与理论值的误差在5%以内,结果可靠有效。
同时计算了裂纹的J 积分值,获得了J 积分的历史曲线,有限元结果与理论结果吻合。
裂纹的扩展过程与理论是吻合的,整个裂纹扩展的计算没有出现不稳定的情况。
裂尖出现了应力的奇异性,裂纹扩展平稳。
并通过研究裂尖单元的应力历史曲线,直观的获得了裂纹在一个单元上扩展的三个典型阶段。
其次,对裂纹扩展的过程进行了分析,指出了裂纹扩展的大概几个阶段以及具体的裂纹扩展过程。
最后,对裂纹扩展过程中的能量变化作了简单描述,说明了计算过程的稳定性,并验证了系统的能量守恒关系。