塑料模设计程序
塑料模具开发流程

分享塑胶模具设计思路与流程,建议收藏!
一套可靠的模具设计,主要体现在所成型的塑料制品的质量(外观质量和尺寸稳定性),加工制造时方便、迅速、简练,既又省资金、人力,留有更正、改良余地、使用时安全、稳定、便于维修、在注射成型时有较短的成型周期和较长使用寿命以及具有合理的模具制造工艺性等方面。
一、工厂模具设计主要流程
客户提供产品图→分析产品→确认塑料品种→确认模具材质→转工程图→乘缩水作镜相→完善组立图→订模胚→订模仁料→拔模→3D 分模→确定流道/浇口方式→参照排位图进行结构设计→拆镶件→更正3D→工程出图包括:(模仁/镶件/模胚/散件)→做BOM 表→校对审核。
在这里插入图片描述
二、在设计应注意的几个方面
我们在开始模具设计时,应多注意考虑几种方案,衡量每种方案优缺点,从中优选一种,对于T模,亦认真对待。
因为时间认识上的原因,当时认为合理的设计,经过生产使用实践也一定会有可能可以改进的地方。
在交出设计方案后,要与工厂多沟通,了解加工过程及制造使用中的情况。
每套模都应有一个固定分析经验,总结得失的过程,才能不断提高模具设计水平。
设计时多参考过去所设计的类似图纸,吸取其经验与教训。
塑料模具设计方案

塑料模具设计方案一、背景介绍在现代工业生产中,塑料制品的应用越来越广泛。
而塑料制品的生产离不开塑料模具的设计与制造。
本文将针对塑料模具的设计方案进行详细介绍。
二、需求分析在开始设计塑料模具之前,我们需要对项目需求进行详细的分析。
这包括产品形状、尺寸、材料以及生产要求等。
1. 产品形状根据产品的形状,我们可以确定模具的结构类型。
常见的模具结构包括单腔模具、多腔模具、嵌件模具等。
2. 产品尺寸对于产品尺寸的要求,我们需要考虑到产品的公差范围和精度要求。
根据尺寸要求,我们可以确定模具的材料及加工方式。
3. 材料选择根据生产批量和产品要求,我们可以选择合适的模具材料。
常见的模具材料包括模具钢、铝合金等。
不同的材料具有不同的强度和耐磨性能。
4. 生产要求根据客户的要求,我们需要考虑到生产效率、模具寿命以及产品表面质量等因素。
这将直接影响到模具的设计和制造过程。
三、塑料模具设计流程根据需求分析阶段的结果,我们可以进行具体的模具设计。
塑料模具设计一般包括以下几个步骤:1. 产品设计在模具设计之前,我们需要通过CAD等设计软件完成产品的三维模型设计。
这将作为模具设计的基础。
2. 模具结构设计根据产品的形状和尺寸要求,我们可以确定模具的结构。
这包括模具腔体、模具芯、模具副以及模具附件的设计和安装。
3. 模具零件设计根据模具结构设计,我们可以开始设计各个模具零件的具体形状和尺寸。
这包括模具腔体、模具芯、滑块、顶针等零部件。
4. 模具注塑系统设计模具注塑系统是模具设计的重要组成部分。
我们需要考虑到注塑机的规格、熔融物料的流动性以及产品的冷却周期等因素。
5. 模具闭合系统设计模具闭合系统包括模具的开合、顶出及脱模等功能。
我们需要确保模具的闭合性能和稳定性,以及产品的顶出和脱模效果。
四、模具制造与试模在完成设计方案后,我们可以进行模具的制造和试模。
这包括以下几个步骤:1. 材料采购与加工根据设计方案,我们需要采购合适的模具材料,并进行相应的加工和热处理。
注塑模具设计流程
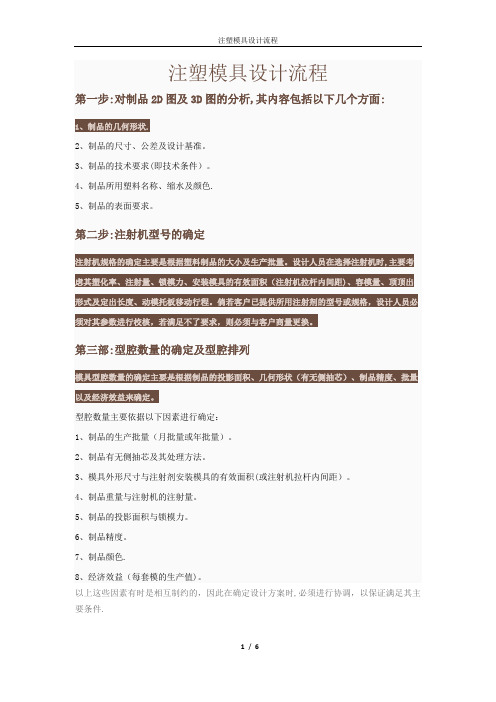
注塑模具设计流程第一步:对制品2D图及3D图的分析,其内容包括以下几个方面:1、制品的几何形状.2、制品的尺寸、公差及设计基准。
3、制品的技术要求(即技术条件)。
4、制品所用塑料名称、缩水及颜色.5、制品的表面要求。
第二步:注射机型号的确定注射机规格的确定主要是根据塑料制品的大小及生产批量。
设计人员在选择注射机时,主要考虑其塑化率、注射量、锁模力、安装模具的有效面积(注射机拉杆内间距)、容模量、顶顶出形式及定出长度、动模托板移动行程。
倘若客户已提供所用注射剂的型号或规格,设计人员必须对其参数进行校核,若满足不了要求,则必须与客户商量更换。
第三部:型腔数量的确定及型腔排列模具型腔数量的确定主要是根据制品的投影面积、几何形状(有无侧抽芯)、制品精度、批量以及经济效益来确定。
型腔数量主要依据以下因素进行确定:1、制品的生产批量(月批量或年批量)。
2、制品有无侧抽芯及其处理方法。
3、模具外形尺寸与注射剂安装模具的有效面积(或注射机拉杆内间距)。
4、制品重量与注射机的注射量。
5、制品的投影面积与锁模力。
6、制品精度。
7、制品颜色.8、经济效益(每套模的生产值)。
以上这些因素有时是相互制约的,因此在确定设计方案时,必须进行协调,以保证满足其主要条件.型腔数量确定之后,便进行型腔的排列,以及型腔位置的布局。
型腔的排列涉及模具尺寸、浇注系统的设计、浇注系统的平衡、抽芯(滑块)机构的设计、镶件型芯的设计以及热流道系统的设计。
以上这些问题由于分型面及浇口位置的选择有关,所以在具体设计过程中,要进行必要的调整,以达到最完美的设计。
第四步:分型面的确定分型面,在一些国外的制品图中已作具体规定,但在很多的模具设计中要由模具人员来确定,一般来讲,在平面上的分型面比较容易处理,有时碰到立体形式的分型面就应当特别注意.其分型面的选择应遵照以下原则:1、不影响制品的外观,尤其是对外观有明确要求的制品,更应注意分型面对外观的影响.2、利于保证制品的精度。
使用UG进行塑料模具设计
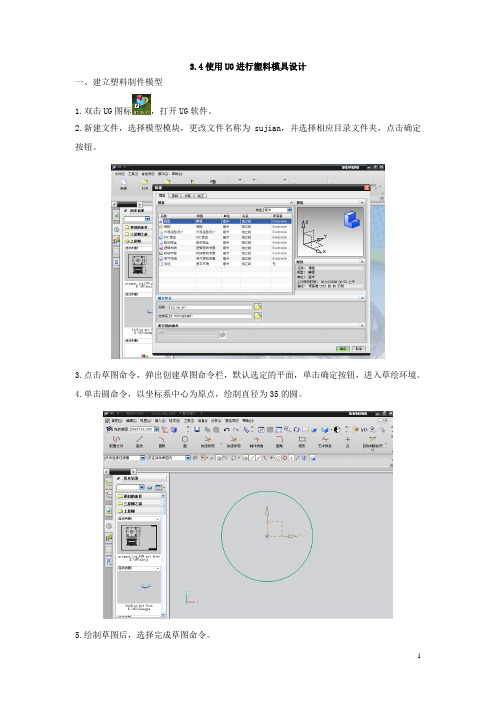
3.4使用UG进行塑料模具设计一、建立塑料制件模型1.双击UG图标,打开UG软件。
2.新建文件,选择模型模块,更改文件名称为sujian,并选择相应目录文件夹,点击确定按钮。
3.点击草图命令,弹出创建草图命令栏,默认选定的平面,单击确定按钮,进入草绘环境。
4.单击圆命令,以坐标系中心为原点,绘制直径为35的圆。
5.绘制草图后,选择完成草图命令。
6.在工具栏中点击拉伸命令,之后弹出拉伸命令工具栏,选择草绘的圆,设置拉伸高度为18,拔模角度为5,点击确定。
7.移动坐标系位置。
点击WCS命令,在弹出命令栏中将ZC改为1.5,其余默认,点击确定。
此时坐标系原点向上移动1.5mm。
8.选则平移后的XC-YC作为草绘平面,绘制直径为32的圆,点击完成草图。
9.点击拉伸按钮,原则上步草绘曲线作为拉伸曲线,在限制中将结束改为直至选定对象,选择实体上表面作为终止面,将布尔运算改为求差,拔模角度为5。
10.单击倒圆角命令,选择零件底面外圆,倒角大小为3,单击应用;选择零件底面内圆,倒角大小为1.5,单击确定。
完成零件体建立。
二、创建模块(型芯和型腔)1.点击开始—所有应用模块—注塑模向导,进入模具设计。
此时弹出注塑模工具条。
2.点击项目初始化项目,进行初始设计,将材料改为ABS,其余默认,点击确定。
3.由于注塑时候型腔保持不变,型芯运动,因此需要改变分型方向。
点击WCS动态,将Z轴改为向下,点击鼠标中键确定。
4.建立模具工作坐标。
点击模具CSYS,弹出对话框,选择选定面的中心命令,选择口的圆环表面,单击确定,此时模具坐标就移到分模面了。
5.点击工件按钮,将开始设为15,结束设为25,单击确定。
6.点击分型工具按钮,弹出分型管理器,对工件进行分型,建立模具型芯和型腔。
7.选择编辑分型线按钮,创建分型线。
弹出分型线对话框,选择自动搜索分型线,点击确定。
弹出对话框,点击选择体,选择零件,点击确定。
完成分型线的建立。
8.建立分型面。
塑料模具流程图
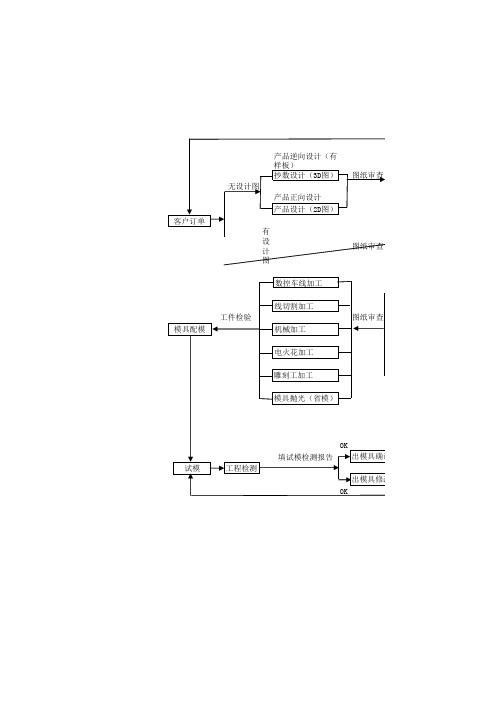
出产品工程图纸(2D)
模具方案确定
出模具总装图及BOM 物料明细表(BOM)
PRO/E分模(3D图) 出模具加工散件图纸(2DD图)
模具制造工艺方案确定
填模具加工计划
出模具确认书 出模具修改通知单
入仓或产品加工(备货)
修模
产品逆向设计(有样板) 抄数设计(3D图) 图纸审查 无设计图 产品正向设计 产品设计(2D图)
客户订单
有设计图
数控车线加工 线切割加工
图纸审查
工件检验 模具配模
机械加工 电火花加工
图纸审查
雕刻工加工
模具抛光(省模)
OK 填试模检测报告 试模
工程检测 出模具修改通知单 出模具确认书
OK
塑料模具制造流程图
塑料模设计计算过程(例题)
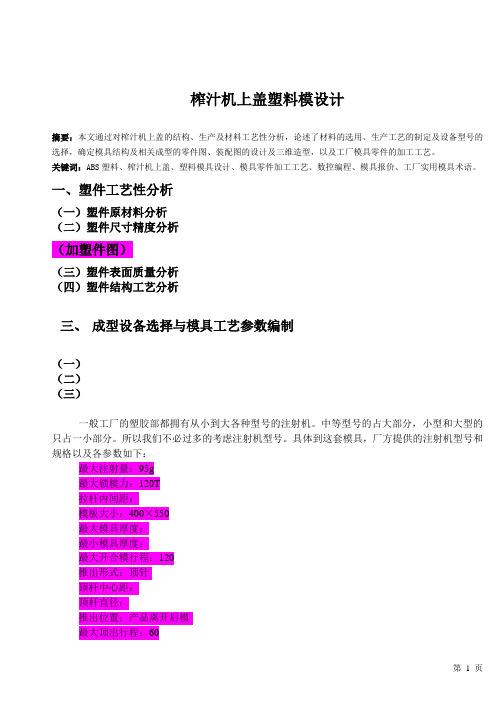
榨汁机上盖塑料模设计摘要:本文通过对榨汁机上盖的结构、生产及材料工艺性分析,论述了材料的选用、生产工艺的制定及设备型号的选择,确定模具结构及相关成型的零件图、装配图的设计及三维造型,以及工厂模具零件的加工工艺。
关键词:ABS塑料、榨汁机上盖、塑料模具设计、模具零件加工工艺、数控编程、模具报价、工厂实用模具术语。
一、塑件工艺性分析(一)塑件原材料分析(二)塑件尺寸精度分析(加塑件图)(三)塑件表面质量分析(四)塑件结构工艺分析三、成型设备选择与模具工艺参数编制(一)(二)(三)一般工厂的塑胶部都拥有从小到大各种型号的注射机。
中等型号的占大部分,小型和大型的只占一小部分。
所以我们不必过多的考虑注射机型号。
具体到这套模具,厂方提供的注射机型号和规格以及各参数如下:最大注射量:95g最大锁模力:120T拉杆内间距:模板大小:400×550最大模具厚度:最小模具厚度:最大开合模行程:120推出形式:顶针顶杆中心距:顶杆直径:推出位置:产品离开后模最大顶出行程:60定位圈直径:喷嘴球面半径:sr20四、拟定模具结构形式(一)确定型腔数量及排列方式型腔的数量是由厂方给定,为“一出二”即一模二腔,他们已考虑了本产品的生产批量(小批量生产)和自己的注射机型号。
因此我们设计的模具为多型腔的模具。
考虑到模具成型零件和抽芯结构以及出模方式的设计,模具的型腔排列方式如下图所示:图 (2)(二)模具结构形式的确定由于塑件外观质量要求高,尺寸精度要求一般,且装配精度要求高,因此我们设计的模具采用多型腔单分型面。
根据本塑件榨汁机上盖的结构,模具将会采用单个分模面,二个行位的结构。
(三)分型面位置的确定如下图所示,采用A-A平直的分型面,前模(即定模)做成平的就行了,胶位全部做在后模(即动模),大简化了前模的加工。
A-A分型面也是整个模具的主分模面。
下图中虚线所示的B -B和C-C分型面是行位(即滑块)的分型面。
这样选择行位分型面,有利于线切割行位以及后模仁和后模镶件这些成型零件。
塑料模具课程设计实例
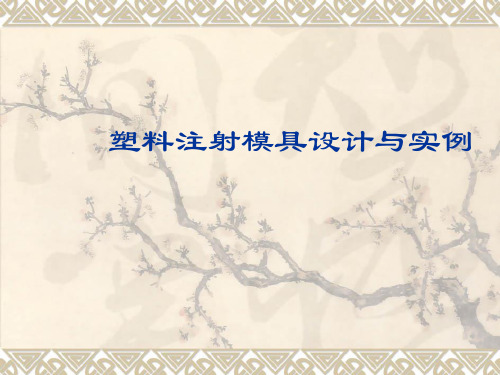
塑料注射模具设计与实例
本章基本内容
(2)模具钢
3Cr2Mo(P20)钢:可预硬化的塑料模具钢,预硬化后
硬度为36~38 HRC,适用于制作塑料注射模具型腔,其 加工性能和表面抛光性较好。 10Ni3CuAIVS(PMS)钢:析出硬化钢。预硬化后时效 硬化,硬度可达40~45 HRC。热变形极小,可做镜面抛 光,特别适合于腐蚀精细花纹。可用于制作尺寸精度高, 生产批量大的塑料注射模具。 6Ni7Ti2Cr钢:马氏体时效钢。在未加工前为固熔体 状态,易于加工。精加工后以480℃~520℃进行时效, 硬度可达50-57 HRC。适用于制造要求尺寸精度高的小 型塑料注射模具,可做镜面抛光。 8CrMnWMoVS(8CrMn)钢:为易切预硬化钢,可做镜面 抛光。其抗拉强度高,常用于大型注射模具。调质后硬 度为33-35 HRC,淬火时可空冷,硬度可达42-60 HRC。 25CrNi3MoAI钢:适用于型腔腐蚀花纹,属于时效硬 化钢。调质后硬度23 25 HRC,可用普通高速钢刀具加 工。时效后硬度38~42 HRC。可以做氮化处理,氮化处 理后表层硬度可达1100 HV。 Crl6Ni4Cu3Nb(PCR)钢:耐腐蚀钢。可以空冷淬火,
塑料注射模具制造特点 塑料注射模具零件常用加工方法和材料 塑料注射模具装配 塑料注射模具设计与制造实例
重点、难点
塑料注射模具制造特点 塑料注射模具零件常用加工方法和材料 塑料注射模具设计
塑料模具的工艺流程

塑料模具的工艺流程
塑料模具的工艺流程主要包括以下几个步骤:
1. 设计阶段:
- 需求分析:根据产品需求确定模具设计方案,包括产品的尺寸、形状、精度要求等。
- 模具设计:使用CAD软件进行详细的设计,包括模具结构设计(型腔、浇注系统、冷却系统、顶出系统等)。
2. 模具制造阶段:
- 材料准备:选择适合的模具钢材或其他材料,按照设计图纸切割成大致形状。
- 加工粗胚:通过铣床、刨床、车床等对模具粗胚进行粗加工,形成初步轮廓。
- 精密加工:运用CNC数控机床进行精加工,包括电火花线切割、电火花成型、精密磨床研磨等,确保模具精度。
- 组装调试:将各个部件装配在一起,安装标准件和热流道系统等,进行试模试验,对模具进行微调优化。
3. 试模与验收阶段:
- 注塑试模:将完成组装的模具安装在注塑机上,进行试模并生产样品,检验产品尺寸、外观及性能是否符合要求。
- 整改与确认:根据试模结果对模具进行必要的修正和改进,直至产品达到设计要求并通过客户或内部验收。
4. 生产阶段:
- 正式生产:模具经过验收合格后,投入批量生产,定期进行维护保养,保证产品质量稳定。
5. 后期维护与报废处理:
- 在模具使用过程中,会定期进行清理、润滑以及磨损部位的修复或更换。
- 当模具因磨损严重、技术更新或其他原因不能满足生产需求时,进行评估决定是否需要翻新或报废处理。
以上就是塑料模具从设计到生产再到后期维护的基本工艺流程,具体细节可能根据不同产品和模具复杂程度有所差异。
- 1、下载文档前请自行甄别文档内容的完整性,平台不提供额外的编辑、内容补充、找答案等附加服务。
- 2、"仅部分预览"的文档,不可在线预览部分如存在完整性等问题,可反馈申请退款(可完整预览的文档不适用该条件!)。
- 3、如文档侵犯您的权益,请联系客服反馈,我们会尽快为您处理(人工客服工作时间:9:00-18:30)。
第一节 注射模设计程序
二、注射模结构设计
14.绘制模具工作图 (1)装配图: 4)装配图的右上角绘制塑件图,复杂的塑件则绘制 在另外一张图纸上(标明尺寸、公差、名称、材料、 收缩率、特殊要求等) 5)模具的技术要求和必要的使用说明; 6)模具零件明细表。
第一节 注射模设计程序
二、注射模结构设计
14.绘制模具工作图 7)总装图中的技术要求一般包括以下一些内容:
6.确定侧向分型与抽芯机构的结构形式 方法:根据塑件特点及型腔布局等,可选择斜导柱、斜 滑块等结构,并确定侧抽芯机构的布置方式。
第一节 注射模设计程序
二、注射模结构设计
推出机构???
7.确定温度调节系统结构
方法:根据模具的结构、塑料的成型性能、塑件的尺寸
精度和质量要求等。
8.排气系统设计 方法:利用模具分型面和推杆与成型零件的间隙排气, 必要时专门进行排气系统设计。
第一节 注射模设计程序
三、注射模设计的审核
3.注射模设计质量 2)是否考虑了塑件对导向精度的要求,导向机构设计 是否合理; 3)成型零件工作尺寸计算是否正确,能否保证塑件精 度,结构是否合理且具有足够的强度和刚度; 4)支承零件能否保证模具具有足够的整体强度和刚度; 5)注射模设计时,是否考虑了试模及修模要求。
第一节 注射模设计程序
三、注射模设计的审核
4.装拆及搬运条件方面 有无便于装拆时用的撬槽、装拆孔、牵引螺钉和起吊 装置(如供搬运用的吊环或起重螺栓孔等),是否对 其做出了标记。
思考与练习: 进行注射模课程设计。
第一节 注射模设计程序
二、注射模结构设计
12.校核模具与注射机的有关尺寸 方法:最大注射量校核、最大锁模力校核、安装尺寸 校核、开合模行程校核等。
13.注射模结构设计的审查 方法:对设计的注射模进行初步审查并征得用户的同 意,同时对用户提出的要求加以确认和修改。
第一节 注射模设计程序
二、注射模结构设计
第一节 注射模设计程序
三、注射模设计的审核
2.设计图样方面 1)装配图:零部件装配关系是否明确,配合代号是否 恰当合理,零件的标注是否齐全,与明细表中的序号 是否对应,有关的必要说明是否具有明确的标记,整 个注射模的标准化程度; 2)零件图:零件号、名称、加工数量是否标注确切, 尺寸公差和形位公差是否合理齐全,成型零件是否预 留了修磨量,超高精度是否合理,零件材料选择是否 恰当,热处理要求和表面粗糙度要求是否合理;
①对于模具某些系统的性能要求。例如对推出系统、 滑块抽芯结构的装配要求,脱模斜度等。 ②对模具装配工艺的要求。例如模具装配后分型面间 的贴合间隙应不大于0.05mm;模具上、下面的平行度 要求;并指出由装配决定的尺寸和对该尺寸的要求。
③模具使用,装拆方法。 ④防氧化处理、模具编号、刻字、标记、油封、保管 等要求。
第一节 注射模设计程序
二、注射模结构设计
14.绘制模具工作图 (2)零件图:
4)结构形体尺寸应按机械制图国家标准标注,对于 型腔型芯的设计基准、尺寸基准、形位尺寸及公差、 脱模斜度、圆角半径、镶块尺寸、表面粗糙度等要 合理齐全,并充分考虑加工工艺要求与实际可能性; 5)合理确定零件材料,正确确定热处理要求及表面 粗糙度要求; 6)绘制标题栏,拟定必要的技术要求及其它说明。
第一节 注射模设计程序
三、注射模设计的审核
1.基本结构方面 6)推出机构及侧抽芯机构是否合理、安全、可靠,与 其他零件是否干涉或碰撞; 7)是否有排气系统,形式是否合理; 8)是否需要温度调节系统,结构形式是否合理; 9)支承零部件结构是否合理; 10)外形尺寸能否保证安装,固定方式是否合理可靠; 11)模具工作过程各运动部件动作是否协调性与稳定。
模具设计任务书的内容:塑件图样(塑料品种、牌 号、颜色、透明度等)、塑件使用说明或技术要求、 生产批量、仿制塑件样品、模具图样等。
第一节 注射模设计程序
一、设计前的准备工作
2.收集并分析必要的设计原始资料与数据 (1)符合标准的塑件图样或塑件样品; (2)塑件产量; (3)塑料品种牌号; (4)塑件生产车间设备型号及参数; (5)模具制造设备及制造技术水平; (6)其他要求。 认真分析消化这些原始资料和数据及其与成型工艺、 模具设计的关系。
9.成型零件工作尺寸计算 方法:计算成型零件工作尺寸及侧抽芯机构尺寸,确定 模具型腔侧壁厚度、模板厚度及模具闭合高度。
第一节 注射模设计程序
二、注射模结构设计
10.选用标准模架 方法:根据设计、计算的模具主要尺寸,合理选用标准 模架及标准模具零件。
11.绘制模具结构草图 方法:根据模具类型及结构,选择标准模架,确定模具 零件主要结构尺寸和功能尺寸(如抽芯距、斜导柱或斜 滑块倾斜角度、定距分型距离、推出距离等)熟练运用塑料模具设计程序
重点和难点: 理论运用于实践
第一节 注射模设计程序
一、设计前的准备工作
1.接受设计任务 模具设计任务的三种类型:
(1)提供经审定的塑件图样及其技术要求,要求设计 成型工艺及模具;
(2)提供塑件样品,要求测绘塑件图样并设计成型 工艺及模具;
(3)提供塑件图样和模具图,要求按实际生产条件, 审定模具图。
第一节 注射模设计程序
三、注射模设计的审核
2.设计图样方面 3)制图方法:制图方法是否正确,是否符合有关国家 标准,图面表达的几何图形与技术要求是否容易理解。 3.注射模设计质量 1)设计注射模时,是否正确考虑了塑料原料的工艺特 性、成型性能及注射机类型可能对成型质量的影响,对 成型过程中可能产生的缺陷是否在设计时采取了相应的 预防措施;
第一节 注射模设计程序
三、注射模设计的审核
1.基本结构方面 1)注射模的结构与基本参数与注射机是否匹配; 2)注射模是否具有合模导向机构,机构是否合理; 3)分型面选择是否合理,塑件是否留在设有推出机构 的动模(或定模)一侧; 4)型腔布局与浇注系统设计是否合理,浇口是否与塑 料原料相适应,位置是否恰当,形状及尺寸是否合适; 5)成型零件设计是否合理;
第一节 注射模设计程序
一、设计前的准备工作
3.分析成型工艺性能 (1)分析塑料的成型工艺性; (2)分析塑件的成型工艺性。
4.明确设计要求 (1)明确塑件的使用要求:用途、作用、尺寸公差、 技术要求; (2)明确塑件的生产纲领:塑件产量与模具价格,生 产效率与模具寿命,模具自动化程度与模具复杂程度。
2.确定分型面 方法:根据分型面的选择原则,力求模具结构简单。
3.确定型腔的排列形式 平衡式或非平衡式,与推杆、冷却水道协调。
第一节 注射模设计程序
二、注射模结构设计
4.浇注系统设计 方法:根据模具类型、型腔数目及布局、塑件原料及 塑件尺寸等。
5.确定型芯和型腔的结构和固定方式 方法:根据塑件特点及型腔布局等,可选择整体式、 整体嵌入式、组合式等结构,并确定固定方式。
⑤有关试模及检验方面的要求。
第一节 注射模设计程序
二、注射模结构设计
14.绘制模具工作图 (2)零件图:非标准的模具零件,特别是成型零件, 应符合机械制图国家标准,还应注意: 1)绘图顺序:先成型零件后结构零件; 2)绘制比例:1:1,必要时放大或缩小; 3)图形方位尽可能与装配图一致,应符合加工习惯; 视图选择与表达应合理、正确、布置得当;
14.绘制模具工作图 (1)装配图:正确表达以上设计计算,对各零部件装 配关系、联接紧固、定位表达清楚,应符合机械制图 国家标准,还应注意:
1)绘制比例:1:1; 2)正确选择足够视图:主视表达模具整体结构,俯视 表达型腔布局、分流道设置及冷却回路等; 3)应标注出必要的尺寸,如轮廓尺寸、配合尺寸、 与注射机的装配关系尺寸、模具功能尺寸等;
第一节 注射模设计程序
一、设计前的准备工作
5.注射成型工艺卡的制定 注射成型工艺卡包含以下内容: (1)塑件概况; (2)塑料概况; (3)注射机参数; (4)注射成型条件。
第一节 注射模设计程序
二、注射模结构设计
1.确定型腔数目 方法:最大塑化量、额定注射量、最大锁模力、 产品的精度要求、生产的经济性等。