冷挤压模结构设计
铝合金冷挤压

铝合金冷挤压1. 引言铝合金冷挤压是一种常见的金属加工方法,通过将铝合金材料置于冷挤压机中,通过施加压力将材料挤压成所需的形状和尺寸。
这种加工方法广泛应用于航空航天、汽车制造、建筑和电子等领域,因其具有高效、节能、环保等优点而备受青睐。
本文将对铝合金冷挤压进行全面详细、完整且深入的介绍,包括其原理、工艺流程、设备和应用等方面。
2. 原理铝合金冷挤压的原理是利用挤压机施加的压力,使铝合金材料发生塑性变形,从而将其挤压成所需的形状和尺寸。
在冷挤压过程中,铝合金材料不会发生熔化,而是在室温下进行塑性变形,因此被称为冷挤压。
冷挤压的原理可以简单描述为以下几个步骤:1.材料装料:将铝合金材料放入冷挤压机的进料口。
2.施加压力:通过冷挤压机施加的压力,使材料开始发生塑性变形。
3.挤压成形:材料在压力的作用下,通过模具的缝隙挤压成所需的形状和尺寸。
4.产品取出:将挤压好的铝合金产品从冷挤压机中取出。
3. 工艺流程铝合金冷挤压的工艺流程通常包括以下几个步骤:1.材料准备:选择合适的铝合金材料,并进行切割和清洁处理,以确保材料的质量和表面光洁度。
2.模具设计:根据产品的形状和尺寸要求,设计合适的模具,包括模具的结构、尺寸和材料选择等。
3.模具制造:根据模具设计图纸,制造模具,并进行表面处理,以提高模具的耐磨性和使用寿命。
4.设备调试:将模具安装到冷挤压机上,并进行设备调试,包括调整挤压机的压力、速度和温度等参数。
5.材料预热:对铝合金材料进行预热处理,以提高材料的塑性和挤压性能。
6.冷挤压加工:将预热后的材料放入冷挤压机中,并施加适当的压力,使材料挤压成所需的形状和尺寸。
7.产品处理:对挤压好的铝合金产品进行去毛刺、去氧化和表面处理等工艺,以提高产品的质量和外观。
8.检验包装:对挤压好的产品进行质量检验,包括尺寸、外观和性能等方面,然后进行包装和出厂。
4. 设备铝合金冷挤压所需的主要设备包括:1.冷挤压机:用于施加压力,将铝合金材料挤压成所需的形状和尺寸。
6.1冷挤压模具设计
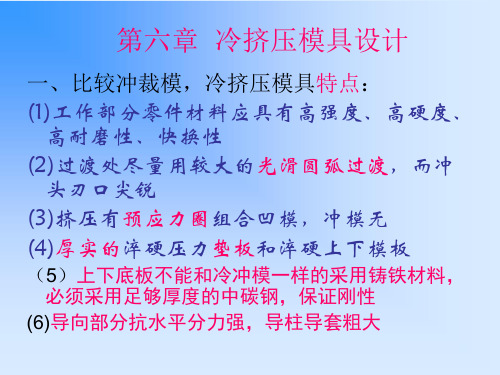
二、反挤压凸模高度确定
• 反挤纯铝时 l/d≤7-10 • 反挤紫铜时l/ d≤5—6; • 反挤黄铜时l/ d≤4—5; • 反挤低碳钢时l /d≤2.5—3 • 可用临界压杆 条件校核计算
三、反偏心方法、卸料方法
• 图12-26咬 住不变形区 减小失稳, 壁厚均匀; 图12-17工 作部分细长 过渡部分加 粗,加工卸 料槽;气孔 • 知识点:卸 料槽使用
六、反挤凸模与凹模制造尺寸与公差: 公差居中原则即入体原则
• 1.保证外径时图a
• 2.保证内径时图b
• Δ可选0.75、0.9系数 • 公差可选IT7-9级
例题1确定挤压凹模尺寸公差
• 原则:入体原则模具尺寸浮动 范围必须在挤压件尺寸公差允 许范围内 0.04 • 书本A100=(100-0.2) = 0 • 99.8 0.04 0 • 一般=(100-0.75*0.2) 1/ 4*0.2 0.05 0 • =99.85 0 • 简便=理想尺寸H7级公差 • =99.9 0.035 0 • 提问:如果挤压件是 φ100±0.2挤压凹模尺寸公差 如何? φ100±0.2= φ100.20-0.4表达不同而已 • 知识点:公差转化方法
0 +0.055
• 一般=(100-0.75*0.22)0+IT7=99.8350+0.035 • 简便=理想尺寸H7级公差=99.890+0.035 • 判断:三种算法的区别?哪个更合理?余量及胀 形影响
(三)反挤压顶杆设计 图6-18
• 设计要点: • 支承部分的直 径应放大, • 大R或斜锥过渡, 间隙0.1mm ,
0.3
0 解:书本T70=(70+0.18)0.036
例3如果是正挤压杆部直径φ100如何设 计正挤凹模工作带尺寸与公差?
冷挤压工艺流程

冷挤压工艺流程冷挤压工艺是指将金属或其他材料通过模具的力学加工,把原材料变形成各种形状的加工工艺。
冷挤压使金属材料获得一定形状,主要用于生产钣金件,机械件,光伏电池框架等零件,广泛应用于汽车,电子,家具,农机和船舶等行业。
冷挤压工艺流程主要包括:材料称重、材料拉伸、材料加热、模具加热、模具安装、金属加工、工件测量、正模配合、模具开合、冷挤压成空、工件表面处理、模具清理等几个主要环节。
1.料称重:材料称重是指将冷挤压所需的不同形状的原材料备好,根据模具的设计尺寸和车间工艺要求做一定数量称重,通过专用称重仪器对材料进行称量,确保材料称量到位,保证冷挤压成型质量。
2.料拉伸:通过拉伸原料,能使其内部的晶粒发生改变,使材料的组织变得更加紧密,也可以除去材料中的内应力。
冷挤压中,材料拉伸约占材料损失的4%,因此需要精确的拉伸技术,以确保冷挤压的均匀性。
3.料加热:热处理技术是冷挤压工艺中重要的环节,可以改善材料的组织结构,以提高冷挤压成形品质和模具使用寿命。
材料加热可以使金属材料更容易变形,同时可以减少模具温度,提高材料模具分离程度,从而节省冷挤压过程中材料的损失。
4.具加热:模具加热是为了满足冷挤压时,模具间隙能充满材料,缩短成型时间,保证工件的完整性,提高工件性能和表面质量,以及模具的使用寿命。
模具的加热温度取决于材料的热弹性,而模具的加热热量应根据工艺要求控制在合理范围内。
5.模具安装:将模具安装在冷挤压机上,并经过严格的检查,确认模具的准确性和完整性,以确保冷挤压工件的精度和完整性,并按照冷挤压机设计要求和生产要求,调整模具的间距和尺寸,使其能够满足成型件的要求。
6.金属加工:金属加工是指通过冷挤压或开口冷挤压,将金属材料进行变形,以获得所需的形状和尺寸。
冷挤压的金属加工要求高压下的均匀加载,以确保工件的精度和模具的使用寿命,并避免材料破裂和冲击力过大。
7.工件测量:挤压工艺中,测量件是非常重要的,需要根据工件的要求,使用测量仪器检测出偏差,并用于精确调整模具,确保成型件的精度和质量。
底座冷挤镦工艺及模具设计

随 着机 械工 业 中 固定 装置 用 的底 座产量 不 断增
产 率 。 为此 , 国外 工 业 发达 国家 逐 渐 研 制 和 推 广 应 用 一项 新 型 的金属 塑性 成形 技术 —— 冷挤 镦 工艺 。 冷挤 镦是 一种 少 或无 切屑压 力 加工新 工 艺 。它
是 根据 金 属塑 性成 形 原 理 , 将 冷 态 的金 属 毛 坯 放人
件。
1 零 件
用 于 连接 装 置 的 底座 零 件 如 图 I所 示 . 材 料 为
优质的 1 0号碳 素 结构 钢 。过去 采用 方料切 削 加工 , 其 生产 工 艺 较 复 杂 , 机 械 加 工 工 时长 , 材 料 利 用 率 低, 成本 高 , 生产 效 率 较 低 , 质 量 也 不 易保 证 。当采 用 冷挤 镦成 形工 艺后 , 该件 制造 工艺 简单 , 生 产率 提
DOI : 1 0 . 3 9 6 9 / j . i s s n . 1 6 7 4 - 6 4 5 7 . 2 0 1 3 . 0 3 . 0 1 6
中图分 类号 : T G 3 7 6 . 5
文献 标识 码 : A
文章 编 号 :1 6 7 4 6 4 5 7 ( 2 0 1 3 ) 0 3 - 0 0 6 9 - 0 4
第 5卷
第 3期
精
密 成 形 工 程
2 0 1 3年 5月
J OURNAL O F N E TS HAP E F O RMI NG E NGI N EE RI NG
传动轴冷挤压工艺及模具设计
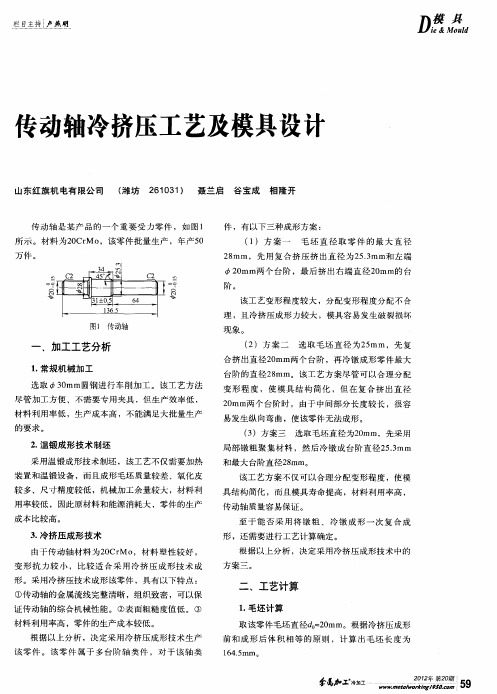
(3)配 合精 度 下 模 座 与下 模 板 之 间 的 配 合 精 度采 用 H7/g6的 配 合 。
(4)模 架 装 配 为 了保 证 上 下 模 架 之 间的 同 轴 度 ,设 计 了专用 的装 配 心轴 。
拦旦主持i 燕盟
D篡 。d
传动轴冷挤压工艺及模具设计
山东红旗 机 电有 限公司 (潍坊 261031) 聂兰启 谷 宝成 相 隆开
所示 。材料为20CrMo,该零件批量生产 ,年产50
重 l 蘼— ——_-]
一 加工工艺分析 .
1.常规机 械加工 选取 30mm圆钢进行车 削加 工。该工艺方法 尽 管加 工方 便 、不需 要 专 用 夹具 ,但 生 产效 率 低 , 材料 利 用 率 低 ,生 产 成 本 高 ,不 能 满 足大 批 量 生产
2.温锻成形 技术制坯 采 用 温 锻 成形 技术 制 坯 ,该 工艺 不 仅 需 要加 热 装 置和 温 锻 设 备 ,而 且 成 形毛 坯 质 量较 差 、氧 化皮 较 多 、尺 寸 精 度较 低 ,机 械 加 工 余量 较 大 ,材料 利 用率较低 ,因此原材料和能源消耗大 ,零件的生产 成 本 比 较 高 。 3.冷挤压成形技 术
处 理 ,才 能达 到 降低 坯料 与模 具 之 间的摩 擦 和 降 低 冷 挤 压 时 的变 形 力的 目的 。所 以 ,毛坯 磷 化 处 理 后 必须 进 行 皂化 处 理 。
四、模具结构及设计
剪 切 下料 模 按 照常 规 设 计 ,这 里 主 要 介 绍 局部 镦 粗 模 和 冷镦 成 形 模 的设 计 。
球头销冷挤压工艺及模具设计

球头销冷挤压工艺及模具设计万亚飞;吴淑芳【摘要】球头销是汽车中的重要零件之一,在工作过程中受力情况非常复杂,对其成形过程进行研究,寻求更加合理的成形方案,对提高球头销的质量有重要的意义.针对某载重汽车球头销的结构特点,结合球头销冷挤压成形工艺,为了进一步减小变形抗力、提高挤压件质量,在传统的两工步成形的基础上,提出了三工步冷挤压成形的工艺方案.设计了球头销尾部、锥体、球头的冷挤压模具,并运用大型有限元模拟软件DEFORM对球头销成形过程进行数值模拟,得到了模具填充情况、等效应力应变、载荷—行程曲线.模拟结果表明,该工艺方案的变形抗力大大减小,成形质量显著提高.【期刊名称】《模具制造》【年(卷),期】2014(014)002【总页数】5页(P52-56)【关键词】球头销;冷挤压;模具设计;数值模拟【作者】万亚飞;吴淑芳【作者单位】长春理工大学机电工程学院吉林长春 130022;长春理工大学机电工程学院吉林长春 130022【正文语种】中文【中图分类】TG3721 引言球头销是汽车转向拉杆联结部分的一个重要零件,在工作过程中,受力情况比较复杂,受拉、压、剪、扭、弯曲和冲击等多种载荷的作用,因此,要求其具有较高的疲劳强度和冲击韧性。
根据球头销种类、尺寸、形状等的不同,生产中常用的加工方法有车削加工、楔横轧、冷挤压等。
在车削加工球头销的过程中浪费了大量金属材料和机加工工时,增加了成本,而且机械性能也不理想。
楔横轧加工球头销对加工设备和模具设计要求较高。
而冷挤压作为一种近净成形的塑性成形技术在球头销的生产中得到了广泛的应用[1]。
冷挤压工艺是根据金属的塑性变形原理,利用装在压力机上的模具,在相当大的压力及一定的速度下,使金属在模腔内产生塑性变形,从而使毛坯变成所需形状、尺寸及一定性能的制件[2]。
冷挤压过程中,金属基本处于三向压应力状态,大大提高了金属的塑性变形能力,使金属在模具型腔内产生稳定的塑性流动,形成所需要的形状和尺寸,达到少无切削的目的。
汽车活塞销挤压模的设计与改进

产 品 , 时 还 能 获 得 较 高 的 尺 寸 精 度 和 较 低 的 同
表 面 粗 糙 度 。本 文 通 过 改 进 和 优 化 原 汽 车 活 塞
等 的压 应 力 作 用 下 , 压 后 金 属 材 料 的 晶 粒 组 挤
织 更 加 细 小 而 密 实 [ 。 同 时 , 于 冷 挤 压 利 用 1 ] 由
De i n a d i p o e e fe tu i n d e f r a t m o ie p so o t sg n m r v m nto x r so i o u o b l it n b l
LIH a - i n we ,YAN G n Pi g,YAN a H o
2 4
Di nd M ou d T e hn o y N o 1 20 ea l c ol g 2 1
.
文章编 号 :0 14 3 ( 0 1 0 —0 40 1 0 — 9 4 2 1 ) 60 2 — 3
汽 车活 塞 销 挤压 模 的设 计 与 改 进
李 汉卫 ,杨 萍 ,闫 浩
Ab t a t s r c :Th e hn c l u s i n n t e s r c u e d sg n o m i g p o e so x r so i e t c i a e to si h t u t r e i n a d f r n r c s fe t u i n d e q
活 塞 销 的各 项 力 学 性 能 指 标 均 高 于 切 削 加 工 的
无 切 屑 加 工 工 艺 , 汽 车 、 械 、 舶 、 天 航 在 机 船 航 空 、 工 和 电 器 仪 表 等 制 造 领 域 得 到 越 来 越 广 军
泛 的应 用 。 在 冷 挤 压 中 , 属 材 料 处 于 三 向 不 金
冷挤压模具的结构分类与设计(

冷挤压模具的结构分类与设计(冷挤压模具是用于制造金属材料中凸台、凹槽、型材等形状的模具。
冷挤压是一种用压力将金属材料挤压成希望得到的形状的加工方法,其工艺和设备相对简单,成本低,可以制造出高强度和高精度的零部件,因此被广泛应用于汽车、航空航天、电子、军工等行业。
冷挤压模具的结构主要包括模具座、模具坯料导向器、模具上下模、模具磨床、模具中心销等几个部分。
模具座是支撑和固定模具的基础,其通常由底板和护板组成。
模具座上部设有导向器,用于引导坯料进入模具。
模具上下模是冷挤压模具的主要部分,通过在模具中心销的作用下上下开合,实现模具内坯料的挤压成型。
模具磨床主要用于修磨模具的工作面,并确保模具上下模的平行度。
模具中心销则是用于固定模具上下模的位置,以确保模具挤压工艺的精度。
1.封闭型模具:模具上下模的结构封闭,适用于对形状和尺寸要求较高的零部件的生产。
封闭型模具具有较高的工艺要求,但可以制造出更高精度的零部件。
2.开放型模具:模具上下模的结构相对开放,适用于要求不太高的形状的零部件的生产。
开放型模具结构相对简单,制造成本低,但精度相对较低。
3.多工位模具:模具上设有多个工作位置,可同时进行多个零件的挤压成型,提高生产效率。
多工位模具通常应用于批量生产的场合。
1.材料选择:模具材料应具有良好的耐磨性、强度和韧性,常见的模具材料有工具钢、硬质合金等。
根据具体的工艺要求,还可以进行表面硬化处理。
2.结构设计:结构设计应根据零件的形状和尺寸来确定。
模具的结构应尽量简单,以便于制造和维护,同时还需要考虑模具的强度和刚度。
3.工作面设计:工作面需要考虑零件的形状和尺寸,工作面的形状应尽量与零件的形状相匹配,以确保成型质量。
4.导向装置:导向装置用于引导坯料进入模具,并确保上下模的相对位置的准确性。
导向装置应结构简单,操作方便。
5.挤压力的确定:挤压力的大小直接影响到成型质量和模具的寿命。
挤压力的确定需要考虑零件的形状和尺寸,以及材料的性能。
- 1、下载文档前请自行甄别文档内容的完整性,平台不提供额外的编辑、内容补充、找答案等附加服务。
- 2、"仅部分预览"的文档,不可在线预览部分如存在完整性等问题,可反馈申请退款(可完整预览的文档不适用该条件!)。
- 3、如文档侵犯您的权益,请联系客服反馈,我们会尽快为您处理(人工客服工作时间:9:00-18:30)。
冷挤压模结构设计
上下模板是冷挤压压力的主要支承部分,由于冷挤压的单位压力较高,上下模板不能采用铸铁材料。
上下模板加导柱、导套就组成有导向的冷挤压模架,无导柱、导套者则为无导向模架
图1为在导柱、导套导向通用反挤压模具。
卸年亦有导向,其导向的基准仍为模架的导柱。
反挤压时挤压件的端面往往是不平的,缺件时使凸模受力不均匀,可能造成凸模偏移而折断。
缺件有强有力的导向时,提高了凸模的稳定性,这是因为卸件板与凸划亦有导向的缘故。
反挤压适用模架兼作为下挤压及复合挤压使用。
图2为有导柱导套导向正挤压通用模具。
图3为镦挤复合模具。
通用反挤、正挤和镦挤复合模架中的组合凹模在相同吨位的压力机上都设计成可以互换的,提高了模具的使用范围。
模架精度可分为三级,其技术指标见表1,用于不同挤压件选用,常用的为Ⅱ级。
卸件板与顶件杆:挤压有时粘在凸模上,有时粘在凹模中,有此部件,能将打主挤压件取出。
卸件板与顶件杆都是用于制件脱模的零件。
凸模与凹模垫板:通用冷挤压模具中,采用了多层垫板。
为了防止高的挤压单位压力直接传递给模板而造成局部凹陷或变形,必须在凹模底端加上垫板,以便把加工压力均匀分散传递,起到缓冲作用。
凸模固定器及定位环:凸模固定器是将凸模安装在上模上,而定位环则可考虑挤压件的不同直径快速交换,提高了模具的通用性能。
凸模与凹模:冷挤压模具的工作部件,在设计时必须认真对待。
应选用具一定韧性的高强度钢材制造。
凸模与凹模承受了最大的冷挤压单位压力。
为了加强凹模的强度,通常采用预应力组合凹模,可以用二层或三层组合而成。
表1
图1
图2
图3
接,不允许有加工刀痕存在。
对于正挤压纯铝空心件的凸模,可采用型式b设计,凸模与芯轴制作成整体。
挤压黑色金属空心件,整体式凸模就不宜采用,在凸模本体与芯轴的直径急剧过渡区就很易断裂。
应当采用型式c与型式d的组合式,使凸模本体与芯轴组合而成。
组合芯轴分固定式c与活动式d。
固定用于芯轴直径较大,而活动式用于芯轴直径较小的环形件。
活动芯轴可随变形金属同时向下滑动一锻距离,从而改善了芯轴的受拉情况,防止芯轴被拉断。
图5为下挤压凸模顶端形状的又一种型式。
此型式有下列特点:
(1)端面有0.5°~1°斜角,其作用是保证凸模的稳定性。
特别是毛坯二端不平时尤为重要。
(2)同凹模配合的有效长度为3~5mm,而不是全直筒式的。
凸模在高的单位挤压力作用下,有时会使凸模直径胀大,增加了凸模下移的阻力。
仅有3~5mm有效长度,就能确保凸模的使用精度。
(3)后角3°的存在,采用小圆弧相联,具有较低的应力集中系数,保证凸模具有较高的寿命。
为此,这种型式的凸模亦广为采用。
公式1
图1
图2
图3
图4
图5
g=1.0~3.0mm,有色金属。
g=2.0~4.0mm,黑色金属。
后隙:b=0.05~0.1mm
凹模模膛深度:见公式2。
凹模工作带以下高度:0.7倍的模膛直径。
带矫正的正挤压凹模结构见图4。
多台阶的正挤压凹模结构见图5。
公式1
公式2
图1
图2
图3
图4
图5
圈压合后,凹模内腔直径有所缩小,收缩量约为0.3%。
当挤压件精度要求高时,压合后应对凹模内腔的尺寸进行修正。
中外圈的材料选择:
中层预应力圈:40Cr、35CrMoA热处理硬度HRC40~42;
外层预应力圈:45、40Cr热处理硬度;
中层预应力圈:HRC36~38
中圈与外圈在反复使用的条件下,应进行200度的低温回火,以去除内应力。
各圈压合时,在压力机外必须装设有机玻璃挡板,以保证安全。
公式1
公式2
公式3
公式4
公式5
公式6
图1
图2
图3
图4
图5
图6
图7。