有色金属的焊接
有色金属焊接方法

有色金属焊接方法有色金属焊接是指对铜、铝、镍、钛等非铁基金属的焊接过程。
由于这些金属的熔点低、导热性能好、导电性能好以及韧性强等特点,使得它们成为各种工业领域中广泛应用的材料。
下面将详细介绍一些常见的有色金属焊接方法。
1. 焊锡焊接:焊锡焊接主要适用于铜及铜合金的焊接。
该方法通过在焊缝上焊锡来完成焊接过程。
焊锡具有低的熔点,使得在加热的过程中只需受热区域达到焊锡的熔点即可保证焊接质量。
这种方法适用于很多领域,如电子器件、仪器仪表、管道等。
2. 氩弧焊接:氩弧焊接适用于铝及其合金的焊接。
氩气在该焊接方法中起到保护焊缝的作用,以防止氧化。
在焊接过程中,电弧通过铝焊丝,并在氩气的保护下使焊丝熔化,然后与基材达到焊接温度,形成焊缝。
这种方法适用于飞机、汽车、船舶等航空航天工业和交通工具制造业。
3. 电阻焊接:电阻焊接适用于铜、铝等金属的焊接。
该方法利用电流通过工件引起局部加热,使两个工件达到熔点而完成焊接过程。
这种方法能够在短时间内实现快速焊接,适用于各种金属材料的焊接,如汽车制造、管道安装等。
4. 慢速电弧焊接:慢速电弧焊接适用于钛及其合金的焊接。
由于钛的反应性较强,容易氧化,所以在焊接过程中需要使用惰性气体来保护焊缝。
电弧的温度可达到5000摄氏度,因此在焊接过程中需要较高的焊接能量。
这种方法适用于航空航天工业和化工工业中的钛材料焊接。
5. 气体焊接:气体焊接适用于铜、铝、镍等金属的焊接。
气体焊接主要包括氩气焊接、氢气焊接和二氧化碳焊接等。
其中,氩气焊接适用于非铁基金属及其合金的焊接,氢气焊接适用于高温合金的焊接,二氧化碳焊接适用于低碳钢等的焊接。
这种方法适用于船舶、汽车制造、建筑等各个领域。
总结起来,有色金属焊接方法有很多种,每种方法都有其适用的金属与焊接需求。
在选择合适的焊接方法时,需要根据具体的材料和焊接要求进行综合考虑。
同时,焊接操作和焊接设备的选择也是影响焊接质量的重要因素,需要严格遵循相关的操作规程和标准,确保焊接质量。
《金属材料焊接》课程标准
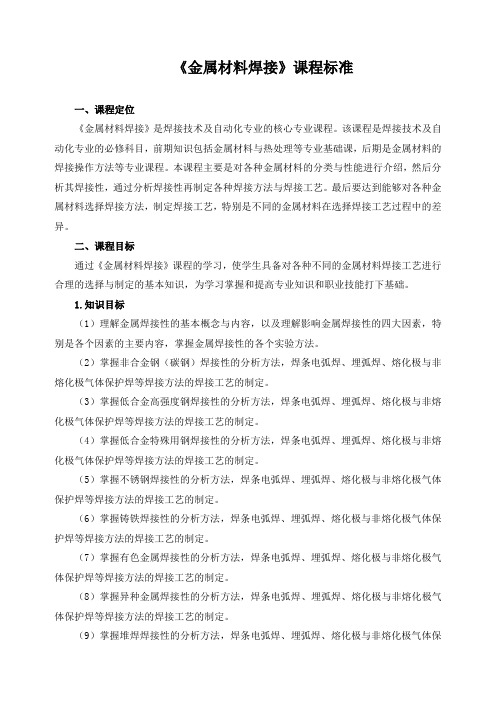
《金属材料焊接》课程标准一、课程定位《金属材料焊接》是焊接技术及自动化专业的核心专业课程。
该课程是焊接技术及自动化专业的必修科目,前期知识包括金属材料与热处理等专业基础课,后期是金属材料的焊接操作方法等专业课程。
本课程主要是对各种金属材料的分类与性能进行介绍,然后分析其焊接性,通过分析焊接性再制定各种焊接方法与焊接工艺。
最后要达到能够对各种金属材料选择焊接方法,制定焊接工艺,特别是不同的金属材料在选择焊接工艺过程中的差异。
二、课程目标通过《金属材料焊接》课程的学习,使学生具备对各种不同的金属材料焊接工艺进行合理的选择与制定的基本知识,为学习掌握和提高专业知识和职业技能打下基础。
1.知识目标(1)理解金属焊接性的基本概念与内容,以及理解影响金属焊接性的四大因素,特别是各个因素的主要内容,掌握金属焊接性的各个实验方法。
(2)掌握非合金钢(碳钢)焊接性的分析方法,焊条电弧焊、埋弧焊、熔化极与非熔化极气体保护焊等焊接方法的焊接工艺的制定。
(3)掌握低合金高强度钢焊接性的分析方法,焊条电弧焊、埋弧焊、熔化极与非熔化极气体保护焊等焊接方法的焊接工艺的制定。
(4)掌握低合金特殊用钢焊接性的分析方法,焊条电弧焊、埋弧焊、熔化极与非熔化极气体保护焊等焊接方法的焊接工艺的制定。
(5)掌握不锈钢焊接性的分析方法,焊条电弧焊、埋弧焊、熔化极与非熔化极气体保护焊等焊接方法的焊接工艺的制定。
(6)掌握铸铁焊接性的分析方法,焊条电弧焊、埋弧焊、熔化极与非熔化极气体保护焊等焊接方法的焊接工艺的制定。
(7)掌握有色金属焊接性的分析方法,焊条电弧焊、埋弧焊、熔化极与非熔化极气体保护焊等焊接方法的焊接工艺的制定。
(8)掌握异种金属焊接性的分析方法,焊条电弧焊、埋弧焊、熔化极与非熔化极气体保护焊等焊接方法的焊接工艺的制定。
(9)掌握堆焊焊接性的分析方法,焊条电弧焊、埋弧焊、熔化极与非熔化极气体保护焊等焊接方法的焊接工艺的制定。
(10)掌握新型金属材料焊接性的分析方法,焊条电弧焊、埋弧焊、熔化极与非熔化极气体保护焊等焊接方法的焊接工艺的制定。
有色金属的焊接(Cu)
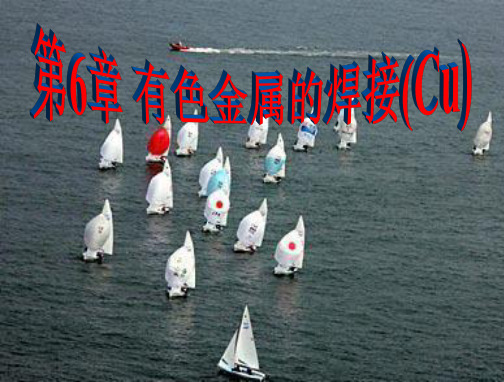
► 1、主要表现:熔化焊过程中,由于晶粒严重长大以及合金元 素蒸发,烧损与杂质的渗入使焊接接头的力学性能、导电性 能和耐蚀性能下降。
► 1)塑性显著降低
► 2)导电性下降
► 3)耐蚀性能下降
► 2、改善措施:主要是控制杂质的含量,减少合金烧损,通过 合金化对焊缝进行变质处理等;其次尽量减少热作用,焊后 进行消除应力处理等。
► 薄铜件焊后要立即对焊缝两侧的热影响区进行锤击。
► 5mm以上的中厚板,需要加热至500~600℃后进行锤 击。锤击后将焊件加热至500~600℃,然后在水中急冷, 可提高接头的塑性和韧性。
► 黄铜应在焊后尽快在500℃左右退火。
12
► 2.埋弧焊 ► 埋弧焊焊接铜及铜合金时,δ<20mm的焊件在不预热和不开坡口的条件
7
► 三、铜及铜合金的焊接工艺要点 ► (一)焊接方法的选择 ► 选用原则,应该根据被焊材料的成分、厚度、结
构特点及使用性能要求综合考虑。 ► 从铜是在常用的焊接金属中导热性最好这一点考
虑,焊接铜及其合金是需要大功率、高能量密度 的焊接方法,热效率越高、能量越集中越好。 ► 不同厚度的材料对各种焊接方法有其适应性。
► ①气焊薄板时应采用左焊法,这有利于抑制晶粒长大。当焊 件厚度大于6mm时,则采用右焊法;
► ②焊炬运动要尽可能的快,每条焊缝不要随意中断焊接过程, 最好单道焊,一次焊完。
► ③焊接长焊缝时,焊前必须留有合适的收缩余量,并要先点 固后焊接,焊接时应采用分段退焊法,以减少变形。
► ④对受力或较重要的铜焊件,必须采取焊后锤击接头和热处 理工艺措施。
热性强,焊缝易生成粗大晶粒。这也会加剧热裂纹的生成。 ► 2、铜及铜合金的焊接可采取哪些措施,防止热裂纹? ► 1)严格限制铜中杂质(氧、铋、铅、硫等)的含量。 ► 2)增强对焊缝的脱氧能力,通过焊丝加入硅、锰、磷等合金
电渣焊、铝热焊、高频焊

铝热化学反应是一个氧化还原反应。
它的化学反应的一般表示式是:
金属氧化物+铝 氧化铝+金属+热能
热剂由还原金属(铝)和氧化金属(氧化铁) 铁合金和铁屑等按一定比例组成。
化学反应产生的热量温度可达3000℃。在高温下铝作为还 原剂被氧化,形成氧化铝(Al2O3)为基的熔渣浮在上面。熔融 金属形成钢水。 铝能还原铁、钛、硅、锰、铬、钒、钨等。
优点:(1)焊接速度高。150~200M/min (2)热影响区小。工件自冷作用强。 (3)焊前可不清除工件待焊处表面氧化膜及污物。 (4)能焊的金属种类广。(碳钢、合金钢、不锈钢、 铝及铝合金、铜及铜合金、镍、钛、锆等金属)。
缺点: (1)电源回路的高压部分对人身与设备的安全有威胁。 (2)维修费用高。(振荡管等元件的工作寿命短)
举 例
钢筋热剂焊的套管接头
钢筋热剂焊接
高 频 焊
一、高频焊原理
1) 高频焊是利用流经工件连接面的高频电流所 产生的电阻热加热工件,并施加顶锻力的情 况下,使工件金属间实现相互连接的一种焊 接方法。 2)高频焊时,焊接电流仅在工件上平行于接头 连接表面流动,而不是垂直于接头界面流动。 3)高频电流穿透工件的深度,取决于电流频率, 工件的电阻率及磁导率。通常采用的频率范 围为300~450KHz。 4)高频焊主要利用集肤效应和邻近效应。
2.铝热焊设备
铝热焊设备主要是造型设备、坩埚、预热工具、装卡工具、 支架和整修工具等。
二、铝热焊的特点及应用
1.特点
1)铝热焊设备简单,投资少,焊接操作简单,不需电源。 2)适合于野外作业。 3)接头质量是通过填加物来控制。 4)缺点是焊缝金属为相当大的铸造组织,性能较差。
2.应用
简单介绍铅的焊接方法及安全防护事项?
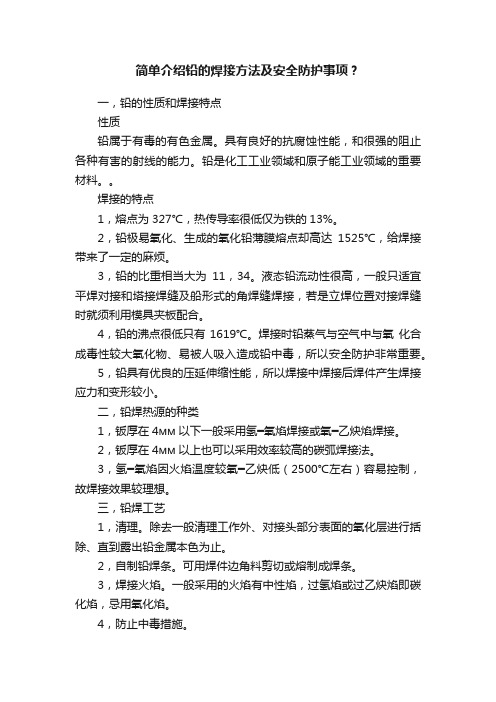
简单介绍铅的焊接方法及安全防护事项?一,铅的性质和焊接特点性质铅属于有毒的有色金属。
具有良好的抗腐蚀性能,和很强的阻止各种有害的射线的能力。
铅是化工工业领域和原子能工业领域的重要材料。
焊接的特点1,熔点为327℃,热传导率很低仅为铁的13%。
2,铅极易氧化、生成的氧化铅薄膜熔点却高达1525℃,给焊接带来了一定的麻烦。
3,铅的比重相当大为11,34。
液态铅流动性很高,一般只适宜平焊对接和塔接焊缝及船形式的角焊缝焊接,若是立焊位置对接焊缝时就须利用模具夹板配合。
4,铅的沸点很低只有1619℃。
焊接时铅蒸气与空气中与氧化合成毒性较大氧化物、易被人吸入造成铅中毒,所以安全防护非常重要。
5,铅具有优良的压延伸缩性能,所以焊接中焊接后焊件产生焊接应力和变形较小。
二,铅焊热源的种类1,钣厚在4мм以下一般采用氢━氧焰焊接或氧━乙炔焰焊接。
2,钣厚在4мм以上也可以采用效率较高的碳弧焊接法。
3,氢━氧焰因火焰温度较氧━乙炔低(2500℃左右)容易控制,故焊接效果较理想。
三,铅焊工艺1,清理。
除去一般清理工作外、对接头部分表面的氧化层进行括除、直到露出铅金属本色为止。
2,自制铅焊条。
可用焊件边角料剪切或熔制成焊条。
3,焊接火焰。
一般采用的火焰有中性焰,过氢焰或过乙炔焰即碳化焰,忌用氧化焰。
4,防止中毒措施。
(1,保持作业场所良好的通风,减低空气中铅的含量。
(2,及时冲洗作业场地减少含铅尘土。
(3,作业场地应远离生话场所、如休息室、宿舍、食堂等。
(4,焊工要做到严格穿戴好工作服、手套、工作帽、口罩等。
工作下班前不吃东西不吸烟。
(5,工作结束后及时淋浴,工作服一天一换,未洗工作服禁忌穿回家。
(6,饭前脱去工作服、洗手、洗睑、漱口刷牙后方可进食。
(7,定期健康检查。
如果发现口中含甜味时应及时求医。
镁合金TIG焊焊接工艺

l O・
科 技 论 坛
镁合金 T I G 焊 焊 接 工 艺
尚 振 一
( 南通航 运职 业技术 学院, 江苏 南通 2 2 6 0 1 0 )
摘
要: 介绍 了焊接镁合金 的几种工 艺方法 , 包括 T I G焊、 电子束焊 、 激光 焊以及搅拌摩擦焊。针对镁合金的焊接 特点 , 着重论述具有
实践 应 用 性 强 、 生 产 成 本较 陷 防 治 。 关键词 : 镁合金 ; 1 r I G焊 ; 焊接 工 艺 ; 焊接 缺 陷
镁合金的密度小 , 约为 1 . 7 8 g / c m s , 是铝的 2 , 3 , 钢的 1 , 4 。同时, 3 - 4焊前表面处理 。镁合金表 面一般 采用机械 以及化学 处理方 镁合金还具 有高的比强度 、 比刚度 、 减震性和导热性 , 较 好的可切削 法 ,清理 坡 口两侧 1 5 m m一 2 0 m m的范围内的氧化物 以及污染物 , 清 性和可回收性 , 因而被称为 2 1 世纪的“ 绿色” 工程材料 。 因此它在汽 理后裸露在空气 中的镁 由于化学性质活泼会再次被空气氧化 , 所 以 车、 通信 、 航 空航天等领域具有巨大的应用前景 。 清理后需要快速进行焊接避免镁的氧化又带来 的一系列的问题 。 如 1 焊 接 性 分 析 果使用化学材料清理 , 那么焊接时间可以适当的延长一点 。 由于镁 合金的熔 点低, 线膨胀系数 和导 热率高 , 与氧 、 氮 的亲 和 3 . 5 T I G焊的电流及极性选择 。用 T I G焊焊接镁 合金时 , 为 了有 力 强, 焊后 易形成夹杂和脆性相 , 易产生焊接 变形 和热裂纹 , 使焊 接 利 于气体的逸 出以及利 用“ 阴极 破碎效应 ” 一般都使 用交流 电源并 接 头的力学性能下降。针对镁合金焊接的特点 和难 点, 应采用能 量 采 用 低 电弧 。 密度大 、 焊接热输入小 、 焊接速度快 的高效焊接方法。 近些年来 出现 3 . 6焊丝的选择与使用 。焊丝 中所使 用的材料对焊接后 接头的 的新工艺 , 如 T I G焊、 真空 电子束焊 、 激光焊 以及搅拌摩擦焊等。 组织性能影响很大,通常情况下都会使用 的焊丝 中 M g的 比例都会 2 焊 接 方 法 分析 比母材低 。因为二次相 的量 以及接头 刚度在高温镁蒸 发严重且 Mg 2 . 1 T I G焊。用 T I G焊焊接镁合金时 , 由于 T I G焊加热范围小 , 比例较大 的情况下都会变得很 大, 相反的接头强度就会变低 。 热源集 中性好 , 焊接后 , 热影响区的范围和变形的尺寸都较小 , 并且 3 . 7 钨极 的选择与使用 。钨极选择综合性能好 的铈钨极 , 钨极直 焊缝抗腐蚀 的性能也得到了提 高 , 接头的整体性能变得更加优 良。 径与 电流密度根据试件情况进行合理选择 。 2 . 2电子束焊 。电子束焊是一种高能密度的焊接工艺 , 穿 透性能 4 焊接 接 头 缺 陷 及 其 产 生 原 因分 析 好, 可 以对镁合金厚板进行焊接 , 接头质量好。但是电子束焊要求在 4 . 1 焊接气孔缺陷分析 真空环境下进行 , 而且, 电子束焊枪结构 复杂 , 设备投 资和运行成本 4 . 1 . 1 气孔形成原因。 气 孔问题在所有 的焊接过程 中都是十分常 比电弧 焊要 高许多倍 , 对焊接接 头装 配要求严格 , 焊接时容 易激发 见的 , 几乎所有 的钢材 、 有 色金 属焊接的时候都会产生气孔 , 而镁 合 X 射线, 对 环境产生危害 。以上弱点限制了电子束焊接 的广泛应用。 金 的一些有 色金属特殊 的 自身性能导致 了产生气孔 的概率往往 比 2 . 3 激光 接 。激光焊接高度集 中的能量会将热影响 区的面积 其他的金属材料 还要 大一些 。 实验表 明其表面一层很难彻底 去除的 减 到最小 , 而且激 光束 比较容易控制 , 焊接镁合 金可 以有效 防止传 Mg O更容易与空气 中的水相结合 , 所 以在镁合金焊接 时对气 孔的敏 统焊接工艺产生的缺 陷 , 焊接接头质量好 。但激光器功率一般都 比 感度更大。 较小 , 镁合金表 面对激光束 的吸 收率很低 , 而且 深熔 焊时存在 阈值 4 . 1 . 2气 孔 产 生 的 预 防措 施 。 焊 前 对 材 料 进 行 清 理 在 整个 焊 接 过 问题,技术还不够成熟成本非常高 , 如今只是在航空航 天等高端科 程中是非常重要 的一个步骤 , 保护气 的成分 同样会影 响焊缝 中气 孑 L 技技术 中应用 , 在一般工业 中还没有得 到广泛应用 。 的形成。实验发 现 , 使用了双重保护且使用高气压 的保护气 的试 件 2 . 4搅拌摩擦焊。 搅拌摩擦焊是一种新 型的固相塑 『 生连接工艺 , 相对于没有使用双重保护和保护器 的气压 比较低 的试 件 , 气孔 的量 在焊接 过程 中, 金属不 熔化 , 焊接 时温度相对较低 ,因而可 以避免 会减少 8 0 %以上。 必要 时可 以加入一些不影响材料本身机械性能的 其他焊接方法所产生 的焊接缺 陷 , 焊接镁合金时不会出现熔化焊的 合金材料来 降低液 态金属 的粘度 ,这样气泡 就会从焊缝 中快速 析 各种缺陷, 接头性能 良好 , 对镁合金 的焊接具有独 特的优势 。但是 , 出。 镁合金搅拌摩擦 焊的工艺 限制较 多, 搅拌头适应性差 , 且磨 损较快 , 4 . 2焊 接 裂 纹 分 析 工艺还不成熟, 目前 限于用在结构简单的构件。 4 . 2 . 1 裂纹形成原 因。从镁合金焊接 时裂纹 的分 布情况 知道 , 焊 因此 , 我们将 T I G焊焊接镁合金的焊接工艺作为代表来探讨镁 缝 晶粒 结 晶过 程 中是 一 个 薄 弱 的环 节 , 首先结晶的部分金属纯度会 合金的焊接工艺 以及缺陷防治 。 比较 高 , 后 结 晶 的 金 属 相 对 杂 质 就 比较 多 , 而 这 些 杂 质 形 成 的 低 熔 3 T I G焊工艺参数对焊缝 的影响 共 晶物的熔点较低 , 在 焊 缝 金 属 凝 固的 后 期 位 于 晶 界 部 位 , 会 形 成 3 . 1 焊接线能量 的影 响。焊接 电流大小 以及 焊接速度 快慢 对焊 层膜 ,此时 由于镁合金冷却收缩量较大会产生较大 的拉应力 , 焊 接 的线 能量都起着至关重要的作用 。 在焊接镁合金时 电流以及焊接 缝 晶界在拉伸应力的作用下就非常容易被撕裂而导致裂纹的形成 。 速度在允许 的范 围内, 都要尽量 的取上 限值 。焊接速 度过慢则 必然 4 . 2 . 2 裂 纹 产 生 的预 防 措 施 。 试 验 分 析研 究 发 现 可 以从 工 艺 以及 会导致热影 响区过大并伴随热裂纹 的出现 。 冶金两个方面降低镁合金焊接 过程 中热裂纹 的产生。 工艺 因素则主 3 . 2氩气流量的选择 。T I G焊焊接镁合金时, 保护气 可以有效地 要是通过规范操作 , 选择正确焊接顺序及接头并 预热来 减少焊件 的 预 防有害气体进入焊接区 , 气体流量在一定 范围内 , 随着流量上升 , 膨胀量 , 从 而达到 降低裂纹 的产 生。但是 为了从 根本上解决热裂纹 保护效果变好 , 但不是无 限制 的上升 , 一旦到了一定流量限值 , 再加 的产生 , 就必须从控制源头冶炼来提 升接头的机械性能降低裂纹产 大流量 , 不仅不会提升保护效果 , 反而质量下降 ; 因为过大 的氩气流 生 的产 生 来 实 现 对 裂 纹 的 掌控 。 反 而会 产生紊流将空气卷 入受保护 区; 因此 , 气 体流量要 根据具体 结 束 语 焊接位置以及坡 口形式等综合考虑 。 镁合金 在采用 T I G焊焊接工 艺相 比于其他焊 接方法 其优势 在 3 . 3 焊接接头设计 。 镁合金的焊接接头有很多种形式 , 可以采用 于热影响区的范 围和变形 的尺 寸较小 , 并且焊缝抗腐蚀 的性 能会得 对接 、 外角接 、 搭接 、 V形对接 、 x形对接等 , 坡 口的选择在 镁合金 的 到极大的提高 , 接头的整体性能变得更加优 良且成本相对合 理。操 焊 接 选 择 上 是 一 项 重 要 的 问题 , 焊 接 时选 择 的 坡 i S l 不正 确 , 在 焊 接 作方法简单 , 对试件装 配以及操作条件要 求较低 , 合理制 定焊接工 时容易导致产生夹渣与未焊透等缺陷 , 如何 选择坡 E l 的形式需要根 艺以及 缺陷防治 , 保 证经济性 与实用性 的完美结合。 据实际的工件情况来分析 。
镍及镍合金焊接操作工艺规范.2011.11.28.F

一. 制定镍及镍合金焊接规范的目的:氯碱化工制碱成套设备的开发、制造是我公司确定的重要增长极,也是我公司发展壮大的战略部署。
镍及镍合金焊接是氯碱化工制碱工艺流程主要耐蚀设备制作的关键工序之一,镍及镍合金焊接质量的好坏直接影响到该设备的使用寿命,因此它也是我公司成功进入制碱设备制造的核心技术之一。
为严格把握镍及镍合金的焊接质量特制订本规范。
二. 镍材焊接的特点及注意事项:因为镍具有单相组织,焊接时存在焊接热裂纹倾向、焊缝气孔、焊接接头的晶间腐蚀倾向等等。
1. 镍在高温中易于生成高度致密的保护膜,在多层焊接的结合面易产生裂纹缺陷,严重影响到材料焊接处的强度及耐蚀性,因此焊接时必须采用氩气保护焊。
在焊接面上应采用专门的保护罩防止氩气的扩散,提高氩气保护层的浓度;镍材间焊接时焊缝背后面也应有氩气保护,防止镍金属在高温时的氧化。
2.镍材的焊接最容易出现的缺陷为裂纹。
产生裂纹的主要元素为氧(O)、硫(S)、铅(Pb)等,它们易与镍形成低熔点的共晶体分布于晶界上。
在焊接时必须选用含氧、硫、铅低,且与母材耐蚀性相同的焊丝,同时注意坡口及中间焊缝表面的氧化层的清除工作。
3.镍材的焊接最容易出现的焊缝缺陷还有气孔。
焊丝、焊件表面上的水分、锈蚀、油污则是焊缝中形成氢气孔的主要来源。
因此镍的焊接必须注意焊缝表面的清洁以及焊丝、焊件的加热、保温和烘干。
4. 高温含硫气体能使镍材腐蚀和变脆。
焊接或热处理前,应彻底清除工件上的油污、油漆及润滑剂等一切含硫或含铅的污染物。
加热炉的气氛中应严格控制含硫量。
加热用煤气或天然气的含硫量应小于0.57g/m3(重庆气矿对天然气脱硫规定为小于0.29g/m3),燃料油的含硫量应小于0.5%,不得用焦炭或煤加热。
5. 焊接热循环的影响:在焊接的热作用下,焊缝和基本金属容易过热,造成晶粒粗大,使接头力学性能和耐腐蚀性能下降。
6.焊接热裂纹的产生:镍基合金具有高的焊接热裂敏感性,在弧坑易产生大口裂纹,焊缝可能产生宏观裂纹、微观裂纹或二者同时存在的裂纹。
有色金属焊接方法

有色金属焊接方法
有色金属焊接方法主要包括以下几种:
1. 熔化焊:根据有色金属的特性,选择适当的焊接材料,通过熔化使焊材与工件接触表面结合,常用的熔化焊方法包括电弧焊、气焊、激光焊等。
2. 压力焊:通过施加压力使焊件接触表面产生塑性流动,并将焊件压接在一起,常用的压力焊方法包括冷压焊、热压焊、摩擦焊等。
3. 铺层焊:将焊材铺在基材表面,通过加热或压力使焊材与基材融合,常用的铺层焊方法包括溶射、蒸镀等。
4. 点焊:通过电流传递产生瞬时高温,使焊接部位融化并形成焊点,常用于薄板金属焊接。
5. 预焊:先将焊件预热至一定温度,再施加外力使焊件结合,常用于高温金属焊接。
需要根据具体的有色金属材料和焊接要求来选择适当的焊接方法。
- 1、下载文档前请自行甄别文档内容的完整性,平台不提供额外的编辑、内容补充、找答案等附加服务。
- 2、"仅部分预览"的文档,不可在线预览部分如存在完整性等问题,可反馈申请退款(可完整预览的文档不适用该条件!)。
- 3、如文档侵犯您的权益,请联系客服反馈,我们会尽快为您处理(人工客服工作时间:9:00-18:30)。
上一页 下一页 返回
8.1 铝及铝合金的焊接
• 8.1.2铝及铝合金的焊接性
• 铝及其合金具有与其他金属不同的物理特性,见表8-2,因此铝及其 合金的焊接工艺特点也与其他金属有很大的差别。
上一页 下一页 返回
8.1 铝及铝合金的焊接
• 按热处理方式,铝合金分为非热处理强化铝合金和热处理强化铝合金。 前者只能变形强化,后者既能变形强化,也可热处理强化
• 按成形方法不同,分为变形铝及铝合金、铸造铝合金。 • 铝合金的分类见表8-1。
上一页 下一页 返回
8.1 铝及铝合金的焊接
• 非热处理强化铝合金又称防锈铝,主要是Al-Mn和Al-Mg系合金,防 锈铝可通过加工硬化、固溶强化来提高力学性能,特点是强度中等、 塑性及耐蚀性好,焊接性良好。热处理强化铝合金是通过固溶、淬火、 时效等工艺措施提高力学性能,经热处理后可显著提高抗拉强度,但 焊接性较差,熔焊时易产生焊接裂纹,焊接接头力学性能下降。
• 2.铝及其合金的牌号及性能 • 纯铝牌号以国际四位数字体系表达,如1A(B)x x,其中第一位为1,
第二位为英文大写字母A, B或其他字母(有时也用数字),第三、四位 为阿拉伯数字,表示铝的最低质量分数中小数点后面的两位数字。
上一页 下一页 返回
8.1 铝及铝合金的焊接
• 如果第二位为A,则表示原始纯铝,如果第二位为B,则表示原始纯 铝的改型情况,即与原始纯铝相比,元素含量略有改变;如果第二位 是数字,则表示杂质极限含量的控制情况,0表示无特殊控制,1~9 表示对一种或几种杂质有特殊控制。例如1 A99表示铝的质量分数为 99. 99%的原始纯铝,1 B99表示铝的质量分数为99. 99%的改型纯 铝;1070表示杂质极限含量无特殊控制、铝的质量分数为99. 70%的 纯铝;1235表示对两种杂质极限含量有特殊控制、铝的质量分数为99. 35%的纯铝。可以看出,纯铝牌号中最后两位数字越大,纯度越高。
第8章 有色金属的焊接
• 8.1 铝及铝合金的焊接 • 8.2 铜及铜合金的焊接 • 8.3 钛及钛合金的焊接
返回
8.1 铝及铝合金的焊接
• 8.1.1铝及铝合金的类型及性能特点
• 1.铝及铝合金的分类 • 工业纯铝:铝的质量分数为99. 0%~99. 7 %,还含有少量的Fe和Si及
其他杂质。 • 铝合金:工业纯铝的强度较低,不能用来制造承受载荷很大的结构,
上一ቤተ መጻሕፍቲ ባይዱ 下一页 返回
8.1 铝及铝合金的焊接
• 因而,铝及铝合金焊前应严格清理焊件及焊丝表面的氧化膜,并对熔 池及高温区金属进行保护,防止在焊接过程中熔池及高温区金属的氧 化。
• 二、能耗大 • 由于铝合金的导热率很大,焊接过程中散热很快,大量的热能被传到
基体金属内部,熔化铝及铝合金要消耗更多的能量。因而焊接时,为 了保证接头处熔合良好,应采用能量集中、功率大的焊接热源,必要 时采取预热等措施。
上一页 下一页 返回
8.1 铝及铝合金的焊接
• 三、容易产生气孔 • 1.产生气孔的原因 • 铝及铝合金本身不含碳,液态铝又不溶解氮,焊接时不会产生一氧化
碳气孔和氮气孔。因此,铝及铝合金焊接时的气孔主要是氢气孔,氢 的来源有两方面:一是弧柱气氛中的水分;二是焊丝及母材表面氧化膜 吸附的水分,而后者对焊缝气孔的影响更为重要。 • 在焊接高温条件下,铝及铝合金的液态熔池很容易吸收气体,焊后冷 却凝固过程中来不及析出,而积聚在焊缝中形成气孔。由图8-1可以 看出,在平衡条件下,氢在液相中的溶解度为0. 69mL/100g,而在 固相下的溶解度仅为0. 036mL/100g,结晶前后其溶解度相差约20倍。
所以使用受到限制。在纯铝中加入少量合金元素,能大大改善铝的各 项性能,例如Cu,Si和Mn能提高强度,Ti能细化晶粒、Mg能防止海 水腐蚀、Ni能提高耐热性等,因此在工业上大量使用的是铝合金。
下一页 返回
8.1 铝及铝合金的焊接
• 按合金化系列,铝及其合金分为工业纯铝(1 x x x系)、铝铜合金(2x xx系)、铝锰合金(3 x x x系)、铝硅合金(4x x x系)、铝镁合金(5 x x x 系)、铝镁硅合金(6x x x系)、铝锌镁铜合金(7x x x系)。
上一页 下一页 返回
8.1 铝及铝合金的焊接
• 四、焊接热裂纹 • 焊接热裂纹是热处理强化铝合金焊接时常出现的问题,非热处理强化
的铝镁合金热裂倾向较小,在接头拘束较大、焊缝成形控制不当时也 会产生。常见的裂纹主要是焊缝结晶裂纹,有时在近缝区可以见到液 化裂纹。 • 1.铝合金产生焊接热裂纹的原因 • 铝合金属于典型的共晶型合金。低熔点共晶组织的存在是铝合金产生 结晶裂纹的重要原因之一,它对结晶裂纹的影响除了与其本身熔点较 低有关以外,还与其存在的形态有关。低熔点共晶组织若是呈连续薄 膜状或网状分布于晶界,使晶粒分离,结晶裂纹倾向就大;若是呈球 状或颗粒状分布于晶界,则结晶裂纹倾向就小。
• 一、易氧化 • 铝与氧的亲和力很强,在空气中与氧极易结合生成一层致密的Al2O3
氧化膜,厚度为0. 1~0. 2μm,熔点为2 050℃,熔点远远超过铝的熔 点,密度是铝的1. 4倍,对水分的吸附能力很强,在焊接过程中易产 生气孔和夹杂,存在于熔池表面时会影响电弧的稳定性,阻碍焊接过 程的正常进行。
上一页 下一页 返回
8.1 铝及铝合金的焊接
• 2.防止焊缝产生气孔的措施 • 铝及铝合金焊缝气孔均是氢气孔,防止气孔的主要措施一是减少氢的
来源,减少氢与液态金属作用的时间;二是尽量促使氢自熔池中逸出。 • (1)减少氢来源焊接时使用的焊接材料要严格控制含水量,使用前需
进行干燥处理。焊丝和母材表面的氧化膜和油污必须彻底清理干净。 氢弧焊时,氢气中的含水量应小于0. 08% ,氢气管路也要保持干燥。 • (2)控制焊接参数焊接参数(焊接电流、电弧电压、焊接速度等)主要是 影响熔池的存在时间,进而影响氢向熔池的溶入和析出时间。