第三代碳纤维技术经验
碳纤维材料成型方法

碳纤维材料成型方法
碳纤维材料的成型方法可以分为以下几种:
1.手工层叠法:即在模具内先放置一层预浸碳纤维布,再依次将预浸碳纤维布一层层放置于上面,并用滚轮或者压力板使碳纤维布充分挤压,使预浸树脂浸透整个碳纤维层数,最后将其压入到合适尺寸的模具中,通过烘干而完成成型。
手工层叠法适用于小批量、连续的生产方式。
2.预制件法:即将预制好的碳纤维制品放入模具中加以加热,将碳纤维制品软化后再压成形。
此种方法生产周期较长,但可以大幅度降低碳纤维材料的制造成本。
3.喷涂法:在模具中先涂抹一定的分离剂,然后利用机械设备将加热等温的碳纤维和树脂混合物喷涂在分离剂上形成预制件,最后经过热固定得到成品。
4.自动化成型法:面向高产量和工艺自动化的需求,采用自动化成型技术,如快速成型技术,机器缠绕技术,单轮轻微拉伸制品技术等。
碳纤维碳化工艺技术选择

碳纤维碳化工艺技术选择
碳纤维的碳化工艺技术选择主要有化学气相沉积(CVD)、高温石墨化、碳纤维预氧化炭化、电化学沉积等。
1.化学气相沉积(CVD):是一种通过在高温下将气体混合物中的原子或分子沉积在基底上形成薄膜的方法。
利用CVD技术可以在碳纤维表面均匀沉积碳化物,提高其强度和硬度。
2.高温石墨化:是将碳纤维在高温下经过石墨化处理,使其晶格结构变得更加有序,提高其热稳定性和力学性能。
3.碳纤维预氧化炭化:是先在氧化氮或氧气中进行预氧化处理,然后在高温下进行碳化处理。
这种方法可以改善碳纤维的微观结构,提高其热稳定性和力学性能。
4.电化学沉积:是通过在电解质溶液中施加电场,使碳纤维上的金属离子还原为金属沉积在其表面。
这种方法可以在碳纤维上形成金属涂层,提高其导电性和机械性能。
在选择碳化工艺技术时,需要考虑碳纤维的应用需求、成本、工艺复杂度等因素。
不同的工艺技术有着不同的特点和适用范围,需要根据具体情况进行选择。
碳纤维工艺简介

碳纤维工艺简介1 概要所谓碳纤维是指碳的重量含量占90%以上的纤维状碳材料。
由于碳在各种溶剂中不溶解,在隔绝空气的惰性气氛中(常压下),碳在高温时也不会熔融。
只有在10MPa、3000K以上高温条件下,才不经液相直接升华。
所以不能通过常规熔融纺丝和溶液纺丝的方法来制备碳纤维。
一般通过有机纤维有在惰性气体中高温碳化而制得。
有机化合物在惰性气体中加热到1000——3000℃时,所有非碳原子将逐步被驱除,碳含量逐步增加,固相间发生一系列脱氢、环化、交联和缩聚等化学反应,最终形成了碳纤维。
制造碳纤维所用的有机纤维应具有含碳量高、强度大、工艺性能好、在转化成碳纤维过程中不熔化等特点。
根据碳纤维的性能与用途,一般有三种分类方法:1)按照所采用的原料不同,可分为聚丙烯睛(PAN)基碳纤维、沥青基碳纤维、粘胶基碳纤维、酚醛树脂基碳纤维、聚酞亚胺基碳纤维、其他有机纤维基碳纤维等。
目前各国生产的高强度、高模量的碳纤维所用原丝主要以PAN纤维为主。
2)按照制造条件和方法的不同,可分为碳纤维、石墨纤维、氧化纤维、活性碳纤维、气相生长碳纤维等。
3)按力学性能分类,可分为通用级碳纤维和高性能碳纤维,其中高性能碳纤维又细分为中强型、高强型、中模型、高模型、超高模型。
2 聚丙烯腈基碳纤维的原料丝PAN原丝BASF的新的PAN原丝生产工艺是在52℃,一个大气压下用氧化还原性催化剂,在无离子水中进行连续悬浮聚合制得丙烯腈,甲基丙烯酸甲酯和甲基丙烯酸的共聚体。
产物从反应器中连续排出,未反应单体和部分水被从产物中分离,经冷凝后回反应器。
脱气后的产物浆液经真空过滤后水洗,生成含水50WT%的料块。
湿料块先与少量的表面活性剂和润滑剂混合,然后挤压成1/8英寸的粒子,再干燥到含水2wt%。
之后再喷洒乙腈水溶液增塑成可熔融挤出的塑料粒子。
最终的复合粒子含聚合物72.7wt%,丙酮腈13.9wt%和水13.4wt%。
含有增塑剂、表面活性剂和润滑剂的复合聚合物粒子在174℃的电加热挤压机中均匀熔融,熔体经过组件的过滤,从孔径为55m的6000孔喷丝板挤出,再牵伸至单丝纤度为9旦的共6K丝束,再经上油以抗凝结和抗静电,干燥以去除丙烯腈和水。
碳纤维的发展及应用
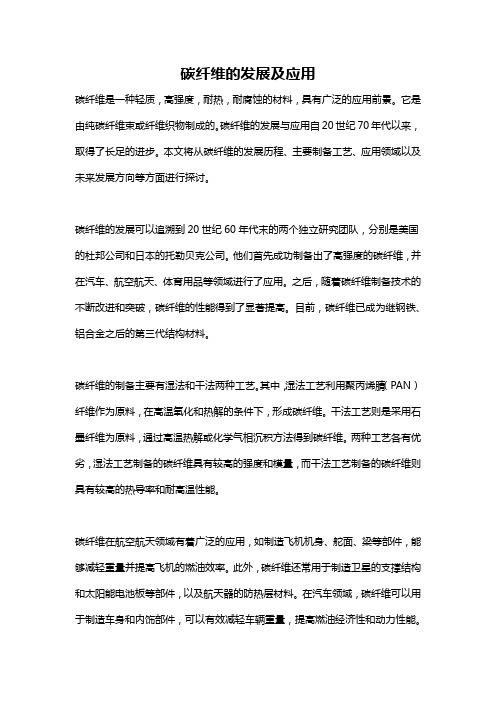
碳纤维的发展及应用碳纤维是一种轻质,高强度,耐热,耐腐蚀的材料,具有广泛的应用前景。
它是由纯碳纤维束或纤维织物制成的。
碳纤维的发展与应用自20世纪70年代以来,取得了长足的进步。
本文将从碳纤维的发展历程、主要制备工艺、应用领域以及未来发展方向等方面进行探讨。
碳纤维的发展可以追溯到20世纪60年代末的两个独立研究团队,分别是美国的杜邦公司和日本的托勒贝克公司。
他们首先成功制备出了高强度的碳纤维,并在汽车、航空航天、体育用品等领域进行了应用。
之后,随着碳纤维制备技术的不断改进和突破,碳纤维的性能得到了显著提高。
目前,碳纤维已成为继钢铁、铝合金之后的第三代结构材料。
碳纤维的制备主要有湿法和干法两种工艺。
其中,湿法工艺利用聚丙烯腈(PAN)纤维作为原料,在高温氧化和热解的条件下,形成碳纤维。
干法工艺则是采用石墨纤维为原料,通过高温热解或化学气相沉积方法得到碳纤维。
两种工艺各有优劣,湿法工艺制备的碳纤维具有较高的强度和模量,而干法工艺制备的碳纤维则具有较高的热导率和耐高温性能。
碳纤维在航空航天领域有着广泛的应用,如制造飞机机身、舵面、梁等部件,能够减轻重量并提高飞机的燃油效率。
此外,碳纤维还常用于制造卫星的支撑结构和太阳能电池板等部件,以及航天器的防热层材料。
在汽车领域,碳纤维可以用于制造车身和内饰部件,可以有效减轻车辆重量,提高燃油经济性和动力性能。
碳纤维还广泛应用于体育用品制造,如高尔夫球杆、自行车框架、滑雪板等。
除了上述应用领域,碳纤维还具有广阔的发展前景。
随着全球环保意识的增强,碳纤维被认为是一种绿色材料,并且在可再生能源、新能源汽车等领域有着重要的应用潜力。
此外,碳纤维在建筑领域也有一定的应用空间,可以制造轻型建筑结构和防震设备,提高建筑物的抗震性能。
在医疗器械领域,碳纤维也常用于制造人工关节、各类手术器械等。
此外,碳纤维在船舶、铁路等交通运输领域,以及电子、电信、能源等行业也有着广泛的应用。
然而,碳纤维的制造成本较高,限制了其在一些领域的推广应用。
碳素纤维简介
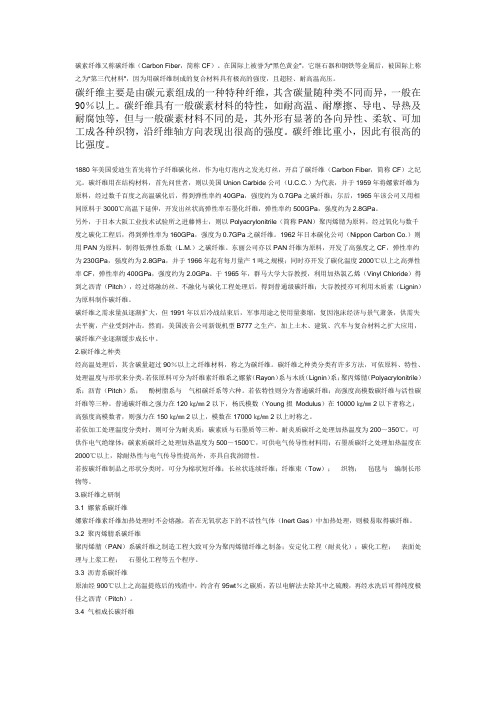
碳素纤维又称碳纤维(Carbon Fiber,简称CF)。
在国际上被誉为“黑色黄金”,它继石器和钢铁等金属后,被国际上称之为“第三代材料”,因为用碳纤维制成的复合材料具有极高的强度,且超轻、耐高温高压。
碳纤维主要是由碳元素组成的一种特种纤维,其含碳量随种类不同而异,一般在90%以上。
碳纤维具有一般碳素材料的特性,如耐高温、耐摩擦、导电、导热及耐腐蚀等,但与一般碳素材料不同的是,其外形有显著的各向异性、柔软、可加工成各种织物,沿纤维轴方向表现出很高的强度。
碳纤维比重小,因此有很高的比强度。
1880年美国爱迪生首先将竹子纤维碳化丝,作为电灯泡内之发光灯丝,开启了碳纤维(Carbon Fiber,简称CF)之纪元。
碳纤维用在结构材料,首先问世者,则以美国Union Carbide公司(U.C.C.)为代表,并于1959年将嫘萦纤维为原料,经过数千百度之高温碳化后,得到弹性率约40GPa,强度约为0.7GPa之碳纤维;尔后,1965年该公司又用相同原料于3000℃高温下延伸,开发出丝状高弹性率石墨化纤维,弹性率约500GPa,强度约为2.8GPa。
另外,于日本大阪工业技术试验所之进藤博士,则以Polyacrylonitrile(简称PAN)聚丙烯腈为原料,经过氧化与数千度之碳化工程后,得到弹性率为160GPa,强度为0.7GPa之碳纤维。
1962年日本碳化公司(Nippon Carbon Co.)则用PAN为原料,制得低弹性系数(L.M.)之碳纤维。
东丽公司亦以PAN纤维为原料,开发了高强度之CF,弹性率约为230GPa,强度约为2.8GPa,并于1966年起有每月量产1吨之规模;同时亦开发了碳化温度2000℃以上之高弹性率CF,弹性率约400GPa,强度约为2.0GPa。
于1965年,群马大学大谷教授,利用加热氯乙烯(Vinyl Chloride)得到之沥青(Pitch),经过熔融纺丝、不融化与碳化工程处理后,得到普通级碳纤维;大谷教授亦可利用木质素(Lignin)为原料制作碳纤维。
碳纤维生产核心技术
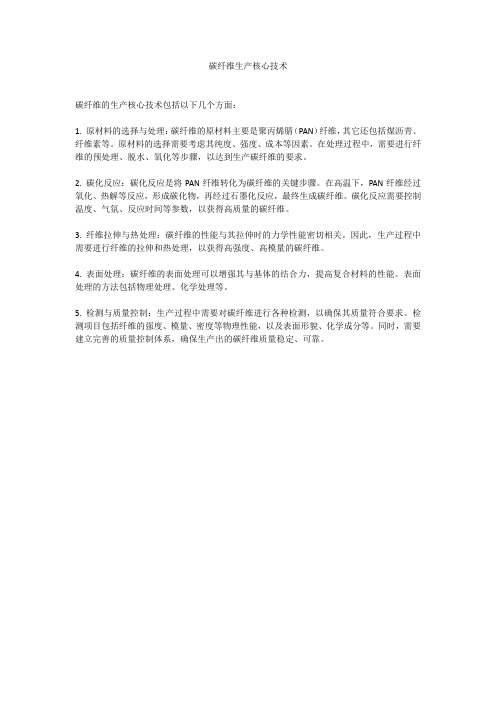
碳纤维生产核心技术
碳纤维的生产核心技术包括以下几个方面:
1. 原材料的选择与处理:碳纤维的原材料主要是聚丙烯腈(PAN)纤维,其它还包括煤沥青、纤维素等。
原材料的选择需要考虑其纯度、强度、成本等因素。
在处理过程中,需要进行纤维的预处理、脱水、氧化等步骤,以达到生产碳纤维的要求。
2. 碳化反应:碳化反应是将PAN纤维转化为碳纤维的关键步骤。
在高温下,PAN纤维经过氧化、热解等反应,形成碳化物,再经过石墨化反应,最终生成碳纤维。
碳化反应需要控制温度、气氛、反应时间等参数,以获得高质量的碳纤维。
3. 纤维拉伸与热处理:碳纤维的性能与其拉伸时的力学性能密切相关。
因此,生产过程中需要进行纤维的拉伸和热处理,以获得高强度、高模量的碳纤维。
4. 表面处理:碳纤维的表面处理可以增强其与基体的结合力,提高复合材料的性能。
表面处理的方法包括物理处理、化学处理等。
5. 检测与质量控制:生产过程中需要对碳纤维进行各种检测,以确保其质量符合要求。
检测项目包括纤维的强度、模量、密度等物理性能,以及表面形貌、化学成分等。
同时,需要建立完善的质量控制体系,确保生产出的碳纤维质量稳定、可靠。
类似老太太打毛衣,碳纤维3D一体成型机织技术

类似⽼太太打⽑⾐,碳纤维3D⼀体成型机织技术南极熊导读:碳纤维的应⽤⼴泛,但传统的采⽤铺层技术。
如果采⽤来⾃军⼯的技术——碳纤维3D⼀体成型机织,不需要进热压罐,那么将可能带来全新的应⽤市场机会。
虽然有专家提到“我每⼀次做3D打印报告,有⽼太太打⽑⾐也是增材制造,我们⼩姑娘⼏⼗年前就打了,怎么第三次⾰命,增材制造跟3D打印不是⼀回事”。
但南极熊收到不少⽤户对碳纤维打印技术的需求咨询,此技术不失为⼀种可能的⽅案。
△南极熊配图:市场上已有的碳纤维制品2018年11⽉27-28⽇,2018增材制造全球创新⼤赛上,南极熊现场看到了⼀些3D打印好项⽬的路演。
△碳纤维3D⼀体成型机织技术项⽬联合创始⼈何彬先⽣下⾯是现场速记,南极熊希望可以很好还原其项⽬路演过程。
碳纤维3D⼀体成型机织技术——何彬军⼯级别的碳纤维3D⼀体成型机织技术我们团队带来“碳纤维3D⼀体成型机织技术”。
这个技术是我们国家的战略预研技术,之前是应⽤在航空航天⽅⾯,技术成型后,在国家海军上先做的应⽤,因此我们技术发明⼈获得了国家当年的科技成果奖。
现在⽣产流⽔线是位于北京重点军⽅的科研机构内。
现有3D碳纤维机织技术和市场上铺层技术做了⼀个对⽐,优势在于整体⼈⼯成本和效率都要⽐现有铺层技术改进很多,⽬标是最终可以做到⼤批量⽣产和低成本化。
这个技术可以应⽤的⾏业有风⼒发电叶⽚、汽车整车车⾝制造⾥⾯减重的模块,包括部分零件,像⽆⼈机、⼤型客机、3C产品、⽂体⽤品,在碳纤维复材领域上需求量⾮常⼤,同时包括像轨道交通领域,也是应⽤了很多。
我们所针对⾏业⽬标是车⾝轻量化,尤其是针对新能源汽车领域,在国家⼗三五规划要求⾥⾯,增材复材和新能源汽车是我们未来⼤的发展⽅向,也是明确有⼤量需求。
市场前景及优势从2020年新能源汽车市场预测来看,全球新能源汽车年均有2000万辆,我们国家市场达到500万辆以上。
从新能源汽车⾏业车⾝减重零部件市场需求来看,这个市场将达到万亿级市场。
碳纤维的生产工艺与原理
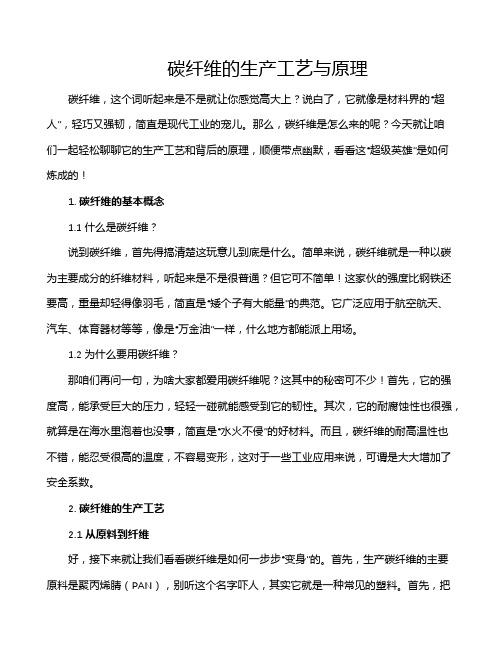
碳纤维的生产工艺与原理碳纤维,这个词听起来是不是就让你感觉高大上?说白了,它就像是材料界的“超人”,轻巧又强韧,简直是现代工业的宠儿。
那么,碳纤维是怎么来的呢?今天就让咱们一起轻松聊聊它的生产工艺和背后的原理,顺便带点幽默,看看这“超级英雄”是如何炼成的!1. 碳纤维的基本概念1.1 什么是碳纤维?说到碳纤维,首先得搞清楚这玩意儿到底是什么。
简单来说,碳纤维就是一种以碳为主要成分的纤维材料,听起来是不是很普通?但它可不简单!这家伙的强度比钢铁还要高,重量却轻得像羽毛,简直是“矮个子有大能量”的典范。
它广泛应用于航空航天、汽车、体育器材等等,像是“万金油”一样,什么地方都能派上用场。
1.2 为什么要用碳纤维?那咱们再问一句,为啥大家都爱用碳纤维呢?这其中的秘密可不少!首先,它的强度高,能承受巨大的压力,轻轻一碰就能感受到它的韧性。
其次,它的耐腐蚀性也很强,就算是在海水里泡着也没事,简直是“水火不侵”的好材料。
而且,碳纤维的耐高温性也不错,能忍受很高的温度,不容易变形,这对于一些工业应用来说,可谓是大大增加了安全系数。
2. 碳纤维的生产工艺2.1 从原料到纤维好,接下来就让我们看看碳纤维是如何一步步“变身”的。
首先,生产碳纤维的主要原料是聚丙烯腈(PAN),别听这个名字吓人,其实它就是一种常见的塑料。
首先,把PAN纤维拉伸,变得更加紧密,这一步就像是“紧箍咒”,让分子间的距离变得更小。
然后,经过氧化、碳化等多个步骤,分子结构就开始发生变化,变得越来越“碳化”。
2.2 高温烘烤接下来就是重头戏了,纤维要经过高温烘烤。
你能想象吗?这些纤维被放进温度高达2000摄氏度的炉子里,简直是火焰山的感觉。
这个过程就像是给纤维来个“桑拿”,把多余的杂质挥发掉,留下的就是纯粹的碳。
最后,经过冷却和整理,这些看似普通的纤维,瞬间就摇身一变,成了我们熟知的碳纤维,简直是神奇得不得了!3. 碳纤维的应用3.1 航天领域的“无敌战舰”说到碳纤维的应用,咱们不得不提航天领域。
- 1、下载文档前请自行甄别文档内容的完整性,平台不提供额外的编辑、内容补充、找答案等附加服务。
- 2、"仅部分预览"的文档,不可在线预览部分如存在完整性等问题,可反馈申请退款(可完整预览的文档不适用该条件!)。
- 3、如文档侵犯您的权益,请联系客服反馈,我们会尽快为您处理(人工客服工作时间:9:00-18:30)。
第三代碳纤维技术经验集团企业公司编码:(LL3698-KKI1269-TM2483-LUI12689-ITT289-
相比传统的金属材料和其他纤维制成的复合材料,碳纤维复合材料具备质量轻、强度高、弹性模量高的特点,可比传统铝合金结构减重30%,对武器装备性能提升贡献巨大,被广泛用于制造航空器机体及发动机、导弹外壳等。
美国F-22、F-35战斗机的碳纤维复合材料用量比例分别达到24%和36%,以A350、波音787为代表的新型大型民机的碳纤维复合
碳纤维复合材料的运用已成为衡量武器装备先进性的标志之一。
碳纤维是构成复合材料的关键原材料,承担着复合材料约90%的载荷,其拉伸强度和弹性模量是实现复合材料结构性能目标的关键。
碳纤维复合材料生产和应用技术已经是航空工业制造水平的重要标志之一。
市场发展
高端碳纤维市场一直为日美两国所垄断。
高端碳纤维绝大部分是小丝束的聚丙烯腈(PAN)基碳纤维。
目前全球最主要的6家小丝束碳纤维供应商的市场占比情况是:日本东丽公司占35%~40%、东邦公司占23%、三菱丽阳公司占14%;美国赫氏公司占12%、氰特工业公司占8%;台湾塑料工业和英国SGL公司占3%~5%。
日本3家企业的碳纤维约占全球70%~80%的市场份额,其中东丽公司产能最大,产品性能最好,是全球最大的碳纤维供应商,代表了日本最高的技术水平和研发实力。
美国的两家企业市场占有率约为20%,其中赫氏公司拥有40多年为美国军机开发应用碳纤维的经验,能够自主生产供应碳纤维,是美国厂家中高模量碳纤维技术的领导者;氰特工业公司以碳纤维的后续产品预浸料为主,碳纤维产品性能和研发能力低于赫氏。
台湾塑料工业公司及SGL的产品性能略低于日本和美国的水平。
碳纤维以拉伸强度和弹性模量为主要指标,目前商业化产品已经发展到第二代,日美两国在广泛应用的第二代碳纤维产品上性能相当。
第一代以20世纪60年代东丽公司的T300和赫氏公司的AS4低强低模碳纤维为代表,T300主要用于波音737等型号的次承力构件,AS4应用在早期F-14战斗机的平尾等部位。
第二代高强度、中等模量碳纤维以20世纪80年代东丽公司的T800和赫氏公司IM7系列为代表,同代产品还有东丽的T700、T1000,赫氏的IM8、IM9等。
T800强度比T300强度提高了68%,模量提高了28%,大量用于A350、波音787等飞机机翼机身的主承力结构。
IM7比AS4强度提高了37%,模量提高了21%,大量用于美国的“三叉戟”Ⅱ潜射导弹及F-22、F-35战斗机等。
第二代碳纤维模量偏低
现阶段,航空航天等领域应用最广泛的是第二代高强度中等模量碳纤维。
由于模量偏低,且碳纤维材料脆性大,易导致复合材料结构部件的疲劳损伤,甚至发生灾难性破坏,限制了航空武器装备性能的提升,更难以满足新一代航空武器装备的性能要求。
随着美国启动第六代战斗机、新一代远程轰炸机、第一代无人舰载作战飞机的研制,航空武器装备对巡航速度、航程、机动性、隐身性能、防护能力和维修性等指标都提出了更高要求,这就需要拉伸强度、断裂韧性、冲击性能等综合性能更高的碳纤维。
要获得综合性能高的碳纤维,就必须在强度和模量这两个基本属性上取得突破,而第三代碳纤维的主要技术特征就是同时实现高拉伸强度和高弹性模量。
同时实现高的拉伸强度和弹性模量是碳纤维研制过程中的技术难点。
原丝制备和碳化是碳纤维制备的两个核心工艺:高质量的PAN原丝是实现碳纤维高性能和批量生产的关键;碳化过程的控制与碳纤维的拉伸强度和弹性模量直接相关。
多年的碳纤维研制经历表明:大幅度地提高碳纤维弹性模量时,拉伸强度会明显降低;而当保持碳纤维的高拉伸强度时,又很难大幅度提高纤维的弹性模量。
究其原因,碳纤维是由大量
石墨微晶组成的各向异性材料。
高强度碳纤维通常要求微晶尺寸较小,而高模碳纤维通常要求微晶尺寸较大,如何解决这一矛盾是碳纤维研制中的最大难题。
日美各辟蹊径突破技术瓶颈
日本东丽公司通过突破碳化工艺,使碳纤维强度和模量同时提升10%以上,率先达到了第三代碳纤维的技术要求。
东丽公司认为,碳纤维同时获得高拉伸强度和高弹性模量的关键在于碳化过程中的热处理技术及高温设备。
在热处理技术方面,温度、牵伸、催化、磁场等许多因素都会影响纤维碳化后的性能。
2014年3月,东丽宣布研制成功T1100G碳纤维。
东丽利用传统的PAN溶液纺丝技术,精细控制碳化过程,在纳米尺度上改善碳纤维的微结构,对碳化后纤维中石墨微晶取向、微晶尺寸、缺陷等进行控制,从而使强度和弹性模量都得到大幅提升。
T1100G的拉伸强度6.6GPa,比T800提高12%;弹性模量324GPa,提高10%,正进入产业化阶段。
美国佐治亚理工学院研究小组通过突破原丝制备工艺,在保持碳纤维高强度同时,弹性模量提升28%以上。
赫氏公司的碳纤维产品30年来一直停留在中等弹性模量水平,性能难以突破。
美国国防预研局(DARPA)在2006年启动先进结构纤维项目,目的是召集全国优势科研力量,开发以碳纤维为主的下一代结构纤维。
佐治亚理工学院作为参研机构之一,从原丝制备工艺入手,提高碳纤维弹性模量。
2015年7月,该研究小组利用创新的PAN基碳纤维凝胶纺丝技术,将碳纤维拉伸强度提升至5.5~5.8GPa,拉伸弹性模量达354~
375GPa。
虽然拉伸强度和IM7相当,但弹性模量实现了28%~36%的大幅提升。
这是目前报道的碳纤维高强度和最高模量组合。
其机理是凝胶把聚合物链联结在一起,产生强劲的链内力和微晶取向的定向性,保证在高弹性模量所需的较大微晶尺寸情况下,仍具备高强度。
这表明美国已经具备了第三代碳纤维产品的自主研发实力。
日美从两条不同的技术途径都获得了高强度、高模量碳纤维。
从目前的研究成果来看,东丽的第三代碳纤维产品强度更高,更适用于抗拉强度设计值高的结构件;美国的产品弹性模量更高,更适用抗弯、抗冲击、抗疲劳强度设计值高的部件。
日美相关企业和机构都明确表示第三代碳纤维的应用目标是航空航天高端市场,替代目前的T800和IM7第二代碳纤维产品,提高军机结构部件强度、刚度等综合性能。
东丽是传统PAN溶液纺丝技术的先驱,原丝技术高度成熟,产业化能力强,从第一、第二代产品来看,其第三代产品有望在未来5~10年实现工业化生产并全面投放市场。
美国放弃传统溶液原丝制备工艺,采用凝胶纺丝技术,有更大余地对工艺优化,碳纤维性能也有更大提升空间。
美国计划于2030年前后面世的第六代战斗机、新一代远程轰炸机、第一代无人舰载作战飞机极有可能通过应用第三代碳纤维技术而大幅提高作战性能。