汽车钢板弹簧悬架设计(doc41页).doc
微型汽车后钢板弹簧悬架设计

微型汽车后钢板弹簧悬架设计引言:随着城市化进程的不断加剧,城市交通拥堵问题越来越严重。
因此,市场对于小型和经济型微型汽车的需求也越来越大。
在微型汽车的设计中,悬架系统是一个非常重要的组成部分,它直接影响到汽车的行驶稳定性、舒适性和操控性。
本文将对微型汽车的后钢板弹簧悬架进行设计和优化。
1.简介后钢板弹簧悬架是一种常见的汽车悬架系统,它由钢板弹簧、减震器和连接件组成。
该悬架系统具有结构简单、制造成本低、可靠性高等优点,因此在微型汽车中广泛应用。
2.悬架系统设计参数在设计后钢板弹簧悬架系统时,需要考虑以下几个主要参数:a.轴距:轴距是指前后轮轴中心之间的距离。
较大的轴距可以提高汽车的稳定性,但同时会增加车身长度,影响车辆的机动性。
b.弹簧刚度:弹簧刚度是指弹簧对重力或外力施加的力与弹簧位移之间的关系。
合适的弹簧刚度可以保证汽车在行驶过程中的平稳性和舒适性。
c.减震器:减震器的作用是减少车辆行驶过程中的颠簸和震动,提高悬架系统的舒适性。
在选择减震器时,需要考虑减震器的压缩和回弹力、摩擦阻尼等因素。
d.响应频率:响应频率是指悬架系统在受到外力激励时产生的周期性振动的频率。
合适的响应频率可以提高悬架系统对不同路面的适应性,减少车辆在行驶过程中的颠簸和震动。
3.悬架系统优化为了优化后钢板弹簧悬架系统的设计,可以采取以下几个策略:a.优化弹簧刚度:通过调整弹簧的材料和参数,可以实现弹簧刚度的优化。
优化后的弹簧可以提供更好的悬架支撑能力和稳定性。
b.配置合适的减震器:根据车辆的重量和行驶需求,选择合适的减震器。
减震器的性能直接影响到悬架系统的舒适性和稳定性。
c.调整悬架系统的参数:通过调整悬架系统的参数,如轴距、悬架点位置等,可以实现悬架系统的优化。
优化后的悬架系统可以提高车辆的操控性和稳定性。
4.结论后钢板弹簧悬架是微型汽车中常用的悬架系统之一,它具有结构简单、制造成本低等优点。
在设计后钢板弹簧悬架系统时,需要考虑轴距、弹簧刚度、减震器等参数,并进行优化,以提高汽车的行驶稳定性、舒适性和操控性。
汽车后悬架系统钢板弹簧的设计毕业设计
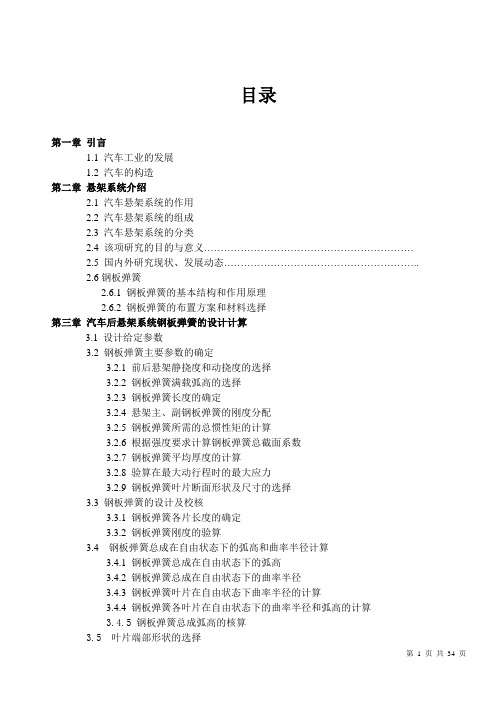
目录第一章引言1.1 汽车工业的发展1.2 汽车的构造第二章悬架系统介绍2.1 汽车悬架系统的作用2.2 汽车悬架系统的组成2.3 汽车悬架系统的分类2.4 该项研究的目的与意义………………………………………………………2.5 国内外研究现状、发展动态…………………………………………………..2.6钢板弹簧2.6.1 钢板弹簧的基本结构和作用原理2.6.2 钢板弹簧的布置方案和材料选择第三章汽车后悬架系统钢板弹簧的设计计算3.1 设计给定参数3.2 钢板弹簧主要参数的确定3.2.1 前后悬架静挠度和动挠度的选择3.2.2 钢板弹簧满载弧高的选择3.2.3 钢板弹簧长度的确定3.2.4 悬架主、副钢板弹簧的刚度分配3.2.5 钢板弹簧所需的总惯性矩的计算3.2.6 根据强度要求计算钢板弹簧总截面系数3.2.7 钢板弹簧平均厚度的计算3.2.8 验算在最大动行程时的最大应力3.2.9 钢板弹簧叶片断面形状及尺寸的选择3.3 钢板弹簧的设计及校核3.3.1 钢板弹簧各片长度的确定3.3.2 钢板弹簧刚度的验算3.4 钢板弹簧总成在自由状态下的弧高和曲率半径计算3.4.1 钢板弹簧总成在自由状态下的弧高3.4.2 钢板弹簧总成在自由状态下的曲率半径3.4.3 钢板弹簧叶片在自由状态下曲率半径的计算3.4.4 钢板弹簧各叶片在自由状态下的曲率半径和弧高的计算3.4.5 钢板弹簧总成弧高的核算3.5 叶片端部形状的选择3.6 钢板弹簧两端与车架的连接3.7 钢板弹簧弹簧销和卷耳的设计3.7.1 弹簧销的设计3.7.2 卷耳尺寸的确定第四章结论参考文献致谢第一章引言1.1 汽车工业的发展几千年来人们一直生活在马车时代。
马拖着车厢在乡村田埂上颠簸行驶,在城市的大街小巷中踢踏的慢跑。
人们的生活节奏缓慢,既沉重又舒展。
18世纪,瓦特打破了这种平静,蒸汽机的发明掀起了工业革命的浪潮。
随后,法国人尼克.卡歌楼特将蒸汽机装在马车上,第一辆“动力车”诞生了。
钢板弹簧悬架匹配设计
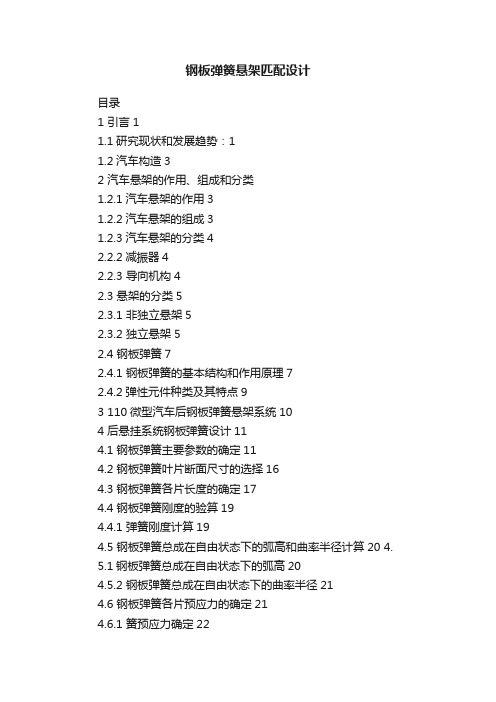
钢板弹簧悬架匹配设计目录1 引言11.1研究现状和发展趋势:11.2汽车构造32 汽车悬架的作用、组成和分类1.2.1汽车悬架的作用31.2.2汽车悬架的组成31.2.3汽车悬架的分类42.2.2减振器42.2.3 导向机构42.3 悬架的分类52.3.1 非独立悬架52.3.2 独立悬架52.4 钢板弹簧72.4.1 钢板弹簧的基本结构和作用原理72.4.2弹性元件种类及其特点93 110微型汽车后钢板弹簧悬架系统104 后悬挂系统钢板弹簧设计114.1 钢板弹簧主要参数的确定114.2 钢板弹簧叶片断面尺寸的选择164.3 钢板弹簧各片长度的确定174.4 钢板弹簧刚度的验算194.4.1 弹簧刚度计算194.5 钢板弹簧总成在自由状态下的弧高和曲率半径计算20 4.5.1钢板弹簧总成在自由状态下的弧高204.5.2 钢板弹簧总成在自由状态下的曲率半径214.6 钢板弹簧各片预应力的确定214.6.1 簧预应力确定224.7钢板弹簧各叶片在自由状态下的曲率半径和弧高的计算224.8 钢板弹簧总成弧高的核算244.8.1 簧总成弧高核算254.9钢板弹簧各片的应力验算265 结论28参考文献29致谢301引言1.1研究现状和发展趋势随着人类技术的不断发展,人们对交通出行的要求也越来越高,自从工业革命以来,瓦特在1766年制作发明出了第一台蒸汽机,使人类社会进入了“蒸汽时代”。
并且开始打响了工业革命的第一枪。
1769年,蒸汽机被瓦特和博尔顿开发研究并且使用。
由蒸汽机开始,机械工业得到愤俗的发展,并为汽轮机和内燃机的发展奠定了基础。
1895年,二冲程煤气内燃机在法国的勒努瓦的努力下发明了出来,它是利用煤气和空气混合气在电火花的点燃爆燃的方式产生燃烧制作出巨大的能量,这就是二冲程煤气内燃机。
1861年,四冲程工作循环方式由法国的德·罗夏提出,它的工作方式是进气、压缩、做功、排气。
并且被法国有关部门授予了专利。
钢板弹簧悬架设计
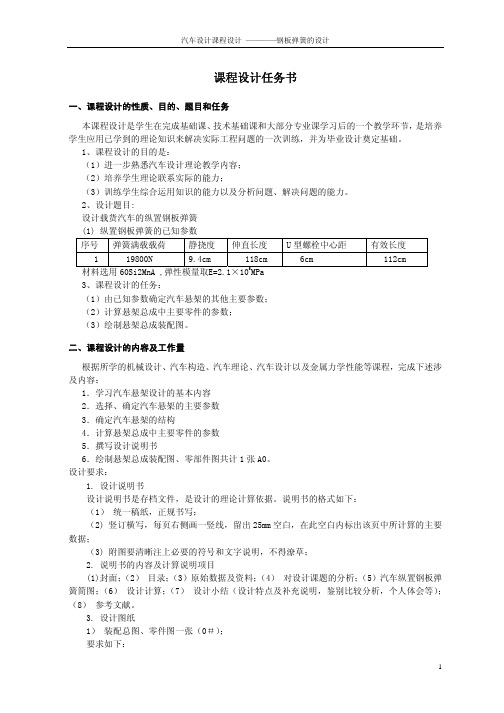
( ) Ri
=
R0
1+ (2σ 0i R0 ) / ( Ehi )i
H 02 = 123.5mm 、 H 03 = 99mm 、 H 04 = 77.3mm 、 H 05 = 58.2mm 、 H 06 = 41.8mm 、
H 07 = 28.1mm 、 H 08 = 17.2mm 、 H 09 = 8.9mm 、 H 010 = 3.3mm 。
6
汽车设计课程设计 ————钢板弹簧的设计
片 等 厚 , 其 长 度 成 等 差 数 列 , 即 li = l2 − (i − 2)a , i ∈[0,10] 。 其 中 l10 = s + a , 将
s
=
70mm, l 2
= 1180mm 代入得
a
=
1110 mm 9
=
370 3
mm
, l10
=
580 3
mm
,则各板长度为:
l1
=1180mm、
五、钢板弹簧各片自由状态下曲率半径的确定:
因钢板弹簧各片在自由状态下和装配后的曲率半径不同,装配后各片产生预应力,其值确定
了自由状态下的曲率半径 Ri 。各片自由状态下做成不同曲率半径的目的是:使各片厚度相同的钢
板弹簧装配后能很好地贴紧,减少主片工作应力,使各片寿命接近。 矩形断面钢板弹簧装配前各片曲率半径由下式确定
计算过程与步骤
一、 钢板弹簧片数取为 10,确定其宽度 b 的计算:
1.钢板断面宽度 b 的确定 有关钢板弹簧 的刚度、强度等,可按等截面简支梁的计算公式计算,但需引入挠度增大系数
δ加以修正。因此,可根据修正后的简支梁公式计算钢板弹簧所需要的总惯性矩 J0 。对于对称钢
(完整word版)钢板弹簧悬架设计(2)(word文档良心出品).docx
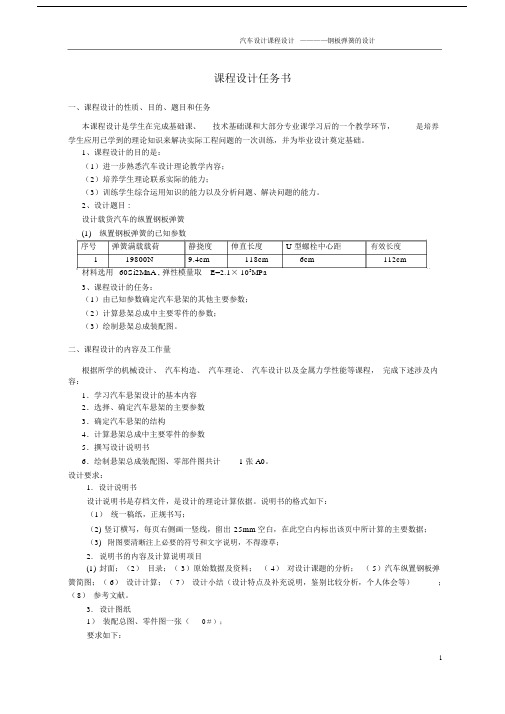
汽车设计课程设计————钢板弹簧的设计课程设计任务书一、课程设计的性质、目的、题目和任务本课程设计是学生在完成基础课、技术基础课和大部分专业课学习后的一个教学环节,是培养学生应用已学到的理论知识来解决实际工程问题的一次训练,并为毕业设计奠定基础。
1、课程设计的目的是:(1)进一步熟悉汽车设计理论教学内容;(2)培养学生理论联系实际的能力;(3)训练学生综合运用知识的能力以及分析问题、解决问题的能力。
2、设计题目 :设计载货汽车的纵置钢板弹簧(1)纵置钢板弹簧的已知参数序号弹簧满载载荷静挠度伸直长度U 型螺栓中心距有效长度119800N9.4cm118cm6cm112cm 材料选用60Si2MnA , 弹性模量取E=2.1× 105MPa3、课程设计的任务:(1)由已知参数确定汽车悬架的其他主要参数;(2)计算悬架总成中主要零件的参数;(3)绘制悬架总成装配图。
二、课程设计的内容及工作量根据所学的机械设计、汽车构造、汽车理论、汽车设计以及金属力学性能等课程,完成下述涉及内容:1.学习汽车悬架设计的基本内容2.选择、确定汽车悬架的主要参数3.确定汽车悬架的结构4.计算悬架总成中主要零件的参数5.撰写设计说明书6.绘制悬架总成装配图、零部件图共计 1 张 A0。
设计要求:1.设计说明书设计说明书是存档文件,是设计的理论计算依据。
说明书的格式如下:(1)统一稿纸,正规书写;(2) 竖订横写,每页右侧画一竖线,留出 25mm空白,在此空白内标出该页中所计算的主要数据;(3)附图要清晰注上必要的符号和文字说明,不得潦草;2.说明书的内容及计算说明项目(1)封面;(2)目录;( 3)原始数据及资料;( 4)对设计课题的分析;( 5)汽车纵置钢板弹簧简图;( 6)设计计算;( 7)设计小结(设计特点及补充说明,鉴别比较分析,个人体会等);(8)参考文献。
3.设计图纸1)装配总图、零件图一张(0#);要求如下:a.图面清晰,比例正确;b.尺寸及其标注方法正确;c.视图、剖视图完整正确;d.注出必要的技术条件。
钢板弹簧悬架设计
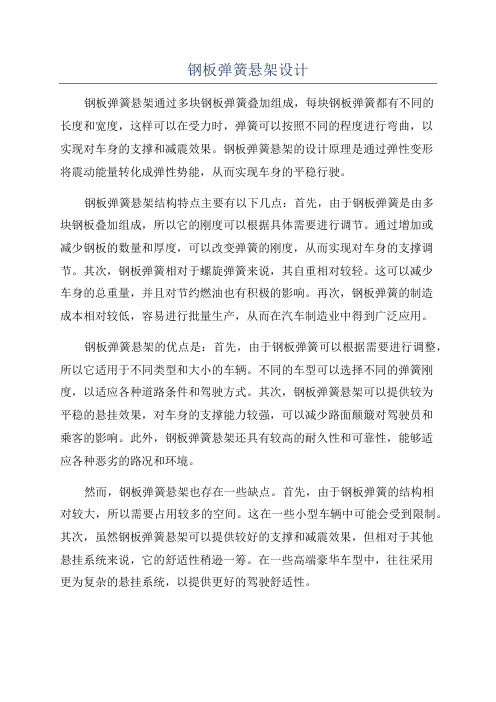
钢板弹簧悬架设计钢板弹簧悬架通过多块钢板弹簧叠加组成,每块钢板弹簧都有不同的长度和宽度,这样可以在受力时,弹簧可以按照不同的程度进行弯曲,以实现对车身的支撑和减震效果。
钢板弹簧悬架的设计原理是通过弹性变形将震动能量转化成弹性势能,从而实现车身的平稳行驶。
钢板弹簧悬架结构特点主要有以下几点:首先,由于钢板弹簧是由多块钢板叠加组成,所以它的刚度可以根据具体需要进行调节。
通过增加或减少钢板的数量和厚度,可以改变弹簧的刚度,从而实现对车身的支撑调节。
其次,钢板弹簧相对于螺旋弹簧来说,其自重相对较轻。
这可以减少车身的总重量,并且对节约燃油也有积极的影响。
再次,钢板弹簧的制造成本相对较低,容易进行批量生产,从而在汽车制造业中得到广泛应用。
钢板弹簧悬架的优点是:首先,由于钢板弹簧可以根据需要进行调整,所以它适用于不同类型和大小的车辆。
不同的车型可以选择不同的弹簧刚度,以适应各种道路条件和驾驶方式。
其次,钢板弹簧悬架可以提供较为平稳的悬挂效果,对车身的支撑能力较强,可以减少路面颠簸对驾驶员和乘客的影响。
此外,钢板弹簧悬架还具有较高的耐久性和可靠性,能够适应各种恶劣的路况和环境。
然而,钢板弹簧悬架也存在一些缺点。
首先,由于钢板弹簧的结构相对较大,所以需要占用较多的空间。
这在一些小型车辆中可能会受到限制。
其次,虽然钢板弹簧悬架可以提供较好的支撑和减震效果,但相对于其他悬挂系统来说,它的舒适性稍逊一筹。
在一些高端豪华车型中,往往采用更为复杂的悬挂系统,以提供更好的驾驶舒适性。
总结起来,钢板弹簧悬架是一种常见的汽车悬挂系统设计。
它通过多块钢板叠加组成,可以提供较为坚硬的支撑,并且具有调整刚度、轻量化和低成本的优点。
然而,它的空间占用较大和相对较低的舒适性是其缺点。
在实际应用中,钢板弹簧悬架可以根据具体需求进行选择和调整,以满足不同车型的悬挂需求。
汽车钢板弹簧悬架设计
汽车钢板弹簧悬架设计汽车钢板弹簧悬架设计引言钢板弹簧悬架是汽车悬架系统中通用的一种。
它具有结构简单、可靠耐用、维护方便等优点,已经成为了汽车悬架系统中不可少的一个组成部分。
本文将探讨汽车钢板弹簧悬架设计的相关知识,包括设计原理、结构材料、设计参数等内容。
一、设计原理汽车钢板弹簧悬架的设计原理是基于弹性和变形实现对汽车震动的吸收和减少。
其基本原理就是利用钢板的弹性变形来吸收汽车在行驶过程中的震动。
弹簧最基本的原理就是哈客定理,即移动的钢板弯曲,因而有了张力和弯曲的复合作用。
钢板弹簧的弹力与材料尺寸、形状和弯曲角度等有关,形状越大、角度越大、宽度越宽,就越能产生弹射力,抗弯曲能力就越好。
二、结构材料汽车钢板弹簧悬架的结构材料是弹簧钢板,它是一种高强度的钢板。
弹簧钢板的化学成分比较复杂,其中含有较多的铬、钼、锰等合金元素,从而保证了钢板的强度和韧性。
弹簧钢板的强度分为两种,一种是静载强度,即弹簧钢板未经过加载状态,所能承受的最大应力;另一种是动载强度,即弹簧钢板在载荷加速状态下,所能承受的应力。
在制造钢板弹簧悬架时,应根据车重、行驶条件、路面状况等因素进行设计选择材料。
三、设计参数汽车钢板弹簧悬架的设计参数有弹簧高度、弹簧宽度、弹簧板厚等。
弹簧高度是弹簧的有效长度,弹簧宽度是弹簧的有效宽度,应根据汽车底盘结构与弹簧安装方式选定。
弹簧板厚直接影响钢板弹簧的强度和韧性,通常采用1.5mm到4mm的钢板材料加工制造。
如果太薄,就不能在车载荷下承受高的撞击力;如果太厚,则不能很好地吸收地面颠簸,影响行驶舒适性。
此外,还需要考虑弹簧孔距、总圈数、自由高度等因素,以达到最优的悬架系统设计效果。
四、结论本文综述了汽车钢板弹簧悬架的设计原理、结构材料和设计参数等知识点,这里强调一下设计数据的选择是钢板弹簧悬架设计中非常关键的一环。
必须根据所要使用的车辆的行驶条件、驾驶员驾驶习惯和所装载的重量等,对钢板弹簧的各项基本参数进行科学合理的结构设计,使得汽车钢板弹簧悬架的设计能满足汽车行驶舒适和悬架稳定等各种要求。
汽车钢板弹簧悬架设计
汽车钢板弹簧悬架设计1.弹簧选用汽车钢板弹簧主要由弹簧片组成,弹簧片之间通过铆钉连接。
在选用弹簧片时,需要根据车辆的重量和使用环境来确定合适的弹簧片数量和材料。
弹簧片的数量越多,弹簧刚度就越高,对于重负荷的车辆,需要选择刚度较高的弹簧片。
弹簧片的材料可以选择高强度钢板,以提高弹簧的寿命和可靠性。
2.弹簧布局汽车钢板弹簧的布局主要包括前后轴的弹簧组织和布置。
为了保证车辆的稳定性和悬挂的平衡性,前后轴的弹簧刚度需要相对均衡,可以根据车辆设计的重心位置和工况来确定各个轴的刚度比例。
同时,在弹簧的布置上,需要考虑到弹簧的有效作用长度,以及与减震器和车架的配合情况,确保弹簧在工作时能够正常运动。
3.减震器选用汽车钢板弹簧悬架中的减震器起到控制弹簧振动和提高行驶平稳性的作用。
减震器的选用需要根据车辆的重量和行驶条件来确定。
一般而言,重负荷的车辆需要选择刚度较高的减震器,而轻负荷的车辆可以选择较为柔软的减震器。
常见的减震器有液压减震器、气压减震器和双作用减震器等。
在实际应用中,需要根据车辆的需求和预算来选择合适的减震器。
4.悬挂系统调校在汽车钢板弹簧悬架的设计中,调校是一个关键的环节。
通过调整弹簧刚度、减震器阻尼、弹簧预紧力等参数,可以实现悬挂系统的理想性能。
悬挂系统的调校需要根据车辆的用途和乘客的需求来进行,例如,运载车辆和越野车辆需要更硬的悬挂系统来增加稳定性和通过性,而乘用车和豪华车则需要更柔软的悬挂系统来提高乘坐舒适性。
在进行悬挂系统的调校时,需要进行一系列的试验和数据分析,以确定最佳的参数组合。
物理试验和计算机仿真是常用的手段。
通过调整参数和验证,最终确定悬挂系统的设计。
总之,汽车钢板弹簧悬架设计需要考虑弹簧选用、弹簧布局、减震器选用和悬挂系统调校等方面。
通过合理的设计和调校,可以实现符合车辆需求和乘客舒适性要求的悬挂系统。
汽车钢板弹簧的设计
汽车钢板弹簧的设计一、汽车钢板弹簧的基本特性钢板弹簧的主要功能是作为汽车悬架系统的弹性元件,此外多片弹簧的片间摩擦又起作系统的阻尼作用,多数钢板弹簧通过卷耳和支座兼有导向作用。
但就其基本的受力情况及结构特点,钢板弹簧具有以下两个基本特征:1、无论钢板弹簧以什么形式装在汽车上,它都是以梁的方式在工作,也就是说它的主要受力方向垂直于钢板弹簧长度。
同时,由于受变形相对其长度很小,因此可以利用材料力学中有关小挠度梁的理论,即线性原理来进行分析计算。
2、钢板弹簧装在汽车上所承受的弯矩,基本上是单向载荷,因而其弯曲应力也是单向应力。
二、等应力梁的概念椭圆形半椭圆形四分之一椭圆形除早期的汽车采用过椭圆形钢板弹簧,近代汽车绝大多数采用半椭圆形钢板弹簧,只有极少数采用四分之一椭圆形钢板弹簧。
无论何种形式的钢板弹簧,就其总成而言,都是根部支承,端部承爱集中载荷,它都是以梁的方式在工作。
众所周知,理想的梁应该是一根等应力梁,这样才能获得材料的最佳利用。
对于钢板弹簧而言,无论单片或多片,设计者应该努力将它设计成等应力梁或近似于等应力梁。
就单片梁而言,当只有单片承爱集中载荷时,有两种轮廓可以满足等应力梁的要求。
对于等厚度者,宽度应成三角形,对于等宽度者,厚度为抛物线形状。
当然,从理论上讲,只要截面系数沿片长方向与弯矩成比例变化,都可以成为等应力梁。
然而汽车上几乎没有采用同时变厚又变宽的弹簧。
上述轮廓线只是对弯曲应力而言,实际上钢板弹簧端部受剪切强度的要求以及卷耳的存在,第一种轮廓只能是在三角形端部加上等宽的矩形或整个宽度成为梯形,而第二种轮廓只能是抛物线端部接上一段等厚度的矩形或厚度按梯形变化的梁。
为了简化轧制工艺,对于等宽度者,可用梯形代替抛物线。
此外,根部也设计成为平直的,便于与支承座贴合,也就是说,或者由梯形和根部、端部为矩形的三段直线构成。
所以,在实际应用上,只能把弹簧设计成为近似的等应力梁。
由于结构上的原因,没有人在汽车上采用等厚度变宽度的单片钢板弹簧,但等宽度变厚度的单片钢板弹簧早就得到实际的应用。
毕业设计(论文)-汽车悬架钢板弹簧的设计
目录第1章绪论 (2)第2章悬架系统的结构与分析 (4)2.1悬架的功能和组成 (4)2.2汽车悬架的分类 (4)2.3悬架的设计要求 (4)2.4悬架主要参数 (5)2.4.1悬架的静挠度cf及刚度c (5)2.4.2悬架的动挠度df (6)2.4.3悬架侧倾角刚度及其在前、后轴的分配 (6)2.4.4钢板弹簧结构............................................................................. . (7)第3章前后悬架系统的设计 (8)3.1前悬架系统设计 (8)3.1.1钢板弹簧的设计 (8)3.1.2.钢板弹簧的验算 (10)3.2后悬架系统设计 (13)3.2.1钢板弹簧的设计 (13)3.2.2钢板弹簧的验算 (15)第4章减振器设计 (19)4.1减振器分类 (19)4.2前后悬架减振器计算 (19)4.2.1相对阻尼系数和阻尼系数 (19)4.2.2最大卸荷力 (20)4.2.3工作缸直径 (21)第5章结论 (23)5.1钢板弹簧参数 (23)5.1.1前悬架参数 (23)5.1.2后悬架参数 (23)5.2双筒式减振器参数 (24)5.2.1前减震器参数 (24)5.2.2后减震器参数 (24)参考文献 (25)第1章绪论悬架是汽车的车架与车桥之间的一切传力连接装置的总称。
它的作用是弹性地连接车桥和车架,缓和行驶中车辆受到的冲击力。
保证货物完好和人员舒适,使汽车在行驶中保持稳定的姿势,改善操纵稳定性;同时悬架系统承担着传递垂直反力,纵向反力和侧向反力以及这些力所造成的力矩,以保证汽车行驶平顺;并且当车轮相对车架跳动时,特别在转向时,车轮运动轨迹要符合一定的要求,因此悬架还起使车轮按一定轨迹相对车身跳动的导向作用。
悬架是汽车中的一个重要组成部分,它把车架与车轮弹性地连接起来,关系到汽车的多种使用性能。
悬架是一个较难达到完美要求的汽车总成,这是因为悬架既要满足汽车的舒适性要求,又要满足其操纵稳定性的要求,而这两方面又是互相对立的。
- 1、下载文档前请自行甄别文档内容的完整性,平台不提供额外的编辑、内容补充、找答案等附加服务。
- 2、"仅部分预览"的文档,不可在线预览部分如存在完整性等问题,可反馈申请退款(可完整预览的文档不适用该条件!)。
- 3、如文档侵犯您的权益,请联系客服反馈,我们会尽快为您处理(人工客服工作时间:9:00-18:30)。
汽车钢板弹簧悬架设计(1)、钢板弹簧种类汽车钢板弹簧除了起弹性元件作用之外,还兼起导向作用,而多片弹簧片间磨擦 还起系统阻尼作用。
由于钢板弹簧结构简单,使用维修、保养方便,长期以来钢板弹 簧在汽车上得到广泛应用。
目前汽车使用的钢板弹簧常见的有以下几种。
① 通多片钢板弹簧,如图1-a 所示,这种弹簧主要用在载货汽车和大型客车上, 弹簧弹性特性如图2-a 所不,呈线性特性。
图1 图2② 少片变截面钢板弹簧,如图1-b 所不,为减少弹簧质量,弹簧厚度沿长度方向 制成等厚,其弹性特性如一般多片钢板弹簧一样呈线性特性图2-a 。
这种弹簧主要用于 轻型货车及大、中型载货汽车前悬架。
③ 两级变刚度复式钢板弹簧,如图1-c 所示,这种弹簧主要用于大、中型载货汽 车后悬架。
弹性特性如图2-b 所示,为两级变刚度特性,开始时仅主簧起作用,当载 荷增加到某值时副簧与主簧共同起作用,弹性特性由两条直线组成。
④ 渐变刚度钢板弹簧,如图1-d 所示,这种弹簧多用于轻型载货汽车与厢式客车 后悬架。
副簧放在主簧之下,副簧随汽车载荷变化逐渐起作用,弹簧特性呈非线性特 性,如图2-c 所示。
多片钢板弹簧钢板弹簧计算实质上是在已知弹簧负荷情况下,根据汽车对悬架性能(频率)要 求,确定弹簧刚度,求出弹簧长度、片宽、片厚、片数。
并要求弹簧尺寸规格满足弹 簧的强度要求。
荷 载V :3.1钢板弹簧设计的已知参数1)弹簧负荷通常新车设计时,根据整车布置给定的空、满载轴载质量减去估算的非簧载质量, 得到在每副弹簧上的承载质量。
一般将前、后轴,车轮,制动鼓及转向节、传动轴、转向纵拉杆等总成视为非簧载质量。
如果钢板弹簧布置在车桥上方,弹簧3/4的质量为非簧载质量,下置弹簧,1/4弹簧质量为非簧载质量。
2)弹簧伸直长度根据不同车型要求,由总布置给出弹簧伸直长度的控制尺寸。
在布置可能的情况下,尽量增加弹簧长度,这主要是考虑以下几个方面原因。
①由于弹簧刚度与弹簧长度的三次方成反比,因此从改善汽车平顺性角度看,希望弹簧长度长些好。
②在弹簧刚度相同情况下,长的弹簧在车轮上下跳动时,弹簧两卷耳孔距离变化相对较小,对前悬架来说,主销后倾角变化小,有利于汽车行驶稳定性。
③增加弹簧长度可以降低弹簧工作应力和应力幅,从而提高弹簧使用寿命。
④增加弹簧长度可以选用簧片厚的弹簧,从而减少弹簧片数,并且簧片厚的弹簧对提高主片卷耳强度有利。
3)悬架静挠度汽车簧载质量与其质量组成的振动系统固有频率是评价汽车行驶平顺性的重要参数。
悬架设计时根据汽车平顺性要求,应给出汽车空、满载时前、后悬架频率范围。
如果知道频率,就可以求出悬架静挠度值c。
选取悬架静挠度值时,希望后悬架静挠度值c2小于前悬架静挠度值ci,并且两值最好接近,一般推荐:c2 (0.7 ~ 0.9) ci (3.1)为防止汽车在不平路面行驶时经常撞击缓冲块,悬架设计时必须给出足够的动挠度值d。
悬架动挠度值与汽车使用情况和静挠度值c有关,一般推荐:(3.2)城市公用车辆2~2.5,公路用车辆 2.5 ~ 3.5,越野车辆 >3.5。
4)弹簧满载弧高由于车身高度、悬架动行程及钢板弹簧导向特性等都与汽车满载弧高有关,因此弹簧满载弧高值°应根据整车和悬架性能要求给出适当值,一般取°10 ~ 30mm有的车辆为得到良好的操纵稳定性,满载弧高取负值3.2钢板弹簧刚度和应力关于钢板弹簧刚度和应力计算,基于不同的假设计算方法而异。
在弹簧计算中有两种典型的而又截然相反的假设,即共同曲率法和集中载荷法。
实际钢板弹簧往往不完全符合这两种假设中的任一种,因此有些学者提出折衷方法,同时兼用上述的两种假设,这种计算分析方法有一定的实用性。
这里仅对多年来一直采用的上述两种假设计算方法进行讨论。
3.1.1共同曲率法共同曲率法是假设钢板弹簧在任何负荷下,弹簧各片彼此沿整个长度无间隙接触, 在同一截面上各簧片具有共同的曲率半径。
如果将多片弹簧各片展开,将展成一个平面,组成一个新的单片弹簧(图3.1、图3.2)。
这个变宽度的单片弹簧力学特性和用共同曲率法假定的多片钢板弹簧是一样的,这样就可以用单片弹簧计算方法来计算多片钢板弹簧。
单片弹簧计算按其几何形状不同可以有两种计算方法。
一种是梯形单片弹簧(图 3.1),另一种是按多片弹簧各片长度展开成的阶梯形单片弹簧(图3.5)。
3.2.1.1梯形单片弹簧计算梯形单片弹簧变形和应力,可以利用材料力学求小挠度梁方法计算。
1)梯形单片弹簧变形3a -------------------------Bp图3.1所示的梯形单片弹簧可以看成是一个由几个相同的片宽b和厚度h的簧片组成,如果弹簧伸直长度为21 ,弹簧中部作用的负荷为2p,计算弹簧变形时,可以近似的认为用整个长度21计算出的值与长度是1端部作用负荷是p的板簧变形是相同的,这样,整个的梯形单片弹簧的计算可以用一端固定,另一端受力的梯形悬臂梁来代替。
F面用单位载荷法(莫尔定理)计算板簧在负荷作用点的变形:1 M P M1 o^|—d xx式中:M p :距端点x处的力矩,M p P xb x:梯形单片弹簧距端点x处的宽度10 :梯形单片弹簧在根部的惯性矩nbh3I o12:钢板弹簧形状系数i n'nb :梯形单片弹簧各片宽度(3.3)M1:单位力距端点x处的力矩,M i xl x :梯形单片弹簧距端点x处的惯性矩l x b x h3xP l0[(1 )卩(3.4)I图h :梯形单片弹簧各片厚度l :梯形单片弹簧主片伸直长度之半,I L/2n :总片数n':等长的主片数E :材料拉伸弹性模数,取E 2.1 104 kgf / mm 2 (3.3)式积分后,经整理:式中:k 1 :挠度增大系数。
梯形单片簧的变形可以看成厚度是h ,宽度是nb 的矩形板簧变形乘以挠度增大系 数k 1。
需要说明一点的是,上面计算公式只适用于等厚多片弹簧,对于各片厚度或惯性 矩不等的多片弹簧,应按等效惯性矩方法来确定各片的展开宽度,再按上式计算。
图3.2是钢板弹簧形状系数 与挠度增大系数k 1关系曲线。
如果钢板弹簧形状系数 1时,由(3.6)式,挠度增大系数k 1 1.5,此时弹簧变形由(3.5)式得:PI 3 2EI o该式为三角形等截面梁在力P 作用下的变形表达式(图3.3)。
PI k i1 2(1)2 ln(1 )](3.5)(3.6)mm(3.7)3EI ok i1梯形单片板簧的形状系数0V V 1为计算方便,有的文献推荐用下式计算挠度增大系数。
1.4423(1 2")2n表3.1是用(3.6)式和(3.9)式计算出的板簧挠度增大系数k 1,首先把 0时,挠度增大系数k i 值为:(3.6)式中ln (1 ) 一项展开成的幕级数,求0时的极限。
(丄 1)2(2 3rT )]10 时,k i 1,由(3.5)式,弹簧变形Pl 3EImm (3.8)该式是矩形板簧在力P 作用下的变形表达式(图3.4)。
(3.9)k 2。
图3.4矩形钢板弹簧M KQLI K4I okgf mm(3.13)表3.12)梯形单片弹簧刚度 弹簧刚度K :由于弹簧变形 和负荷P 之间是线性关系(图5.1直线1),故弹簧刚度是一常数 3)钢板弹簧应力梯形单片弹簧在根部(或中心螺栓处)应力:QL 4W o弹簧比应力(单位变形应力):式中:W o :梯形单片弹簧在根部的断面系数按(3.11),(3.12)式,计算出应力和比应力是平均应力和平均比应力,它不能反 映各片的确实受力情况。
对于片厚不等的弹簧,用下面方法计算各片弹簧应力。
根据共同曲率假设,任意负荷时同一截面上各片曲率半径相等条件,弹簧各片所 承受的弯矩应正比于其惯性矩。
由力矩平衡可求出作用在各片弹簧上的力矩。
2P48EI 。
L 3k 248EI o L 3k ikgf / mm (3.10)kgf / mm 2(3.11)12EI o 2k 1L W o12EI o 2k 2L W o2kgf / mm / mm(3.12)W obh 23mm式中 M K —作用在第K 簧片上的力矩,kgf mmI K —第K 片弹簧惯性矩,mm 4I 。
一弹簧各片惯性矩之和,mm 4nI o IK 1h K —第K 片弹簧片厚,mm第K 片弹簧在根部的应力K 和比应力K 为:2kgf /mm /mm式中 W K —第K 片弹簧断面系数,mm 3 3.2.1.2阶梯形单片弹簧1)阶梯形单片弹簧变形£1匸阶梯形单片弹簧变形计算和梯形单片弹簧一样,不同之处是这种弹簧的断面惯性 矩沿长度变化不能用一个连续函数表示,因此为了求得梁的变形,只能采用分段积分 求出。
用单位载荷法求负荷P 作用点处弹簧变形 (图3.6))bh <3 12M K W KQLI K 4I O W Kkgf / mm 2(3.14)(3.15)图3.5l iPx 2dxEl x上式经整理后得:式中:a K 111I K 1 :阶梯形单片弹簧第K 1片长度之半;I x :阶梯形单片弹簧距端点x 处的惯性矩;Y K :第1片至第K 片弹簧惯性矩之和的倒数1/mm 4l ii 1I i :阶梯形单片弹簧第i 片惯性矩3, bh i4I imm12h i :阶梯形单片弹簧第i 片厚度,mmb :阶梯形单片弹簧各片宽度,mmY K 1 :第1片至第K 1片弹簧惯性矩之和的倒数图3.6(l i l 2 0(| (i i也dxI 2) El iPx 2(I 1 l n ) Edx P3E Ka 3K (Y K1mm(3.16l i :阶梯形单片弹簧主片长度之半,l iL/2;0 (总片数n ),故a n 1 I 1,而Y n 1 02)阶梯形单片弹簧刚度 弹簧刚度K :—弹簧刚度修正系数,取 0.9 ~ 0.95利用(3.17)式计算出的弹簧刚度值,要比实际测得的刚度要大,这主要是由于 计算中认为弹簧片端部承受了弯矩,这一假设与实际情况不符。
由于实际弹簧的侧边 轧制成圆角,弹簧断面惯性矩比理论值小,因此用(3.17)式计算弹簧刚度时,弓I 用 了一个刚度修正系数。
一般弹簧片数多时取值下限,片数少时取上限3)阶梯形单片弹簧应力阶梯形单片弹簧应力与比应力计算可按(3.11, (3.12)或(3.14), (3.15)式计3.2.2集中载荷法与共同曲率法假设相反,集中载荷法是假设各弹簧片在片端接触,因此弹簧片间 力的传递仅在弹簧片端进行,这对于弹簧片之间有镶块或衬片的钢板弹簧是比较合适 的。
图(3.7)是按这一假设建立的钢板弹簧示意图,弹簧片一端固定,另一片通过滚 柱与上一片弹簧接触。
Y K 1 K 1I ii 11/ mm 42P6En §a K(Y KY K 1)K 1kgf / mm(3.17)式中:用上式计算时,由于l n 11)弹簧片端负荷假设主片卷耳处负荷为P ,其它各片在端点处产生的力为X K ,根据两相邻簧片 在接触点处变形相等原理,可求出作用在各片端部负荷。