数控高速切削加工
高速切削加工的计算机数控技术

高速切削加工的计算机数控技术史毅(江西现代学院机械学院,江西南昌330029)应用科技脯要]棵器高速切哥唾加工计算机兹艘系统速度与精度的影响,分析了树嚎括补与直线插朴的优缺点。
介绍了高速教控系统的速度预控常J、误差补偿等其他动自匕目蝴】高速切削;插补;计算机数控对高速切削加工的主要要求是能够加工复杂曲面,加工质量和切削效率、速度要高。
计算机数控(C N C)系统的基本任务,是根据已编制的零件加工程序,计算出沿机床各坐标轴的进给指令,驱动各轴运动,从而获得所需的运动轨迹。
其中需要进行插补处理。
1计算初.姑蓝寸甭补1.1直线插补直线与圆弧是构成零件轮廓的最基本线条,通常计算机数控系统均具有圆弧与直线插补功能。
目前占主导地位的直线插补计算简单,但存在一些问题需要克服。
常规的计算机数控系统在直线插补时,必需采用高精度的表面描述来近似。
零件曲线曲率变化较大、表面轮廓复杂时,需要增加中间计算点的数量,这样就导致了数控程序执行时间延长。
C N C系统具有一定的插补周期,它与最大进给速度F,(m/m i n)的关系是F。
F60(L m。
选T定后,由于加工精度要求选取短的插补直线长度L,不仅会使计算数据扩大,还会直接限制最大进给速度,也就是插补周期问题。
这与高速切削加工所要求的轨迹进给速度发生矛盾。
降低了加工精度与速度。
此外,直线插补还会使工件表面产生棱面。
12样条插补相对于直线插补,样条插补更为精确,其中以圆弧插补最为常用。
直接处理样条程序段的N U RB S插补方法优点很多。
多边形的编程,将为直线从C A M系统传递样条轨迹描述的方式,或通过几何转换即压缩直线程序段代替。
建立在三次B样条函数基础上的N U R B S函数有可调参数∞,可以精确、灵活地控制逼近曲面或曲线的形状,可以精确地表示所有二次曲面与曲线。
样条曲线数据必须减少数据总量,同时为流畅的加工提供必需的曲率和切线连续的程序髓立渡。
要求计算机数控系统能够通过制定精修多边形程序段的途径,自动光滑处理运动轨迹从而获得较为光滑的零件表面。
数控技术第四章 高速切削与五轴联动加工编程基础

第一节 高速切削编程方法
(1)恒定的金属切除率 在高速切削的粗加工过程中,保持恒定的 金属切除率,可以获得以下的加工效果:①保持稳定的切削力; ②保持切屑尺寸的恒定;③没有必要去熟练操作进给量和主轴转 速;④较好的热转移,使刀具和工件均保持在较冷的温度状态; ⑤延长刀具的寿命;⑥较好的加工质量等。 (2)恒定的切削条件 为保持恒定的切削条件,一般主要采用层切 法、顺铣方式加工,或采用在实际加工点计算加工条件等方式进 行粗加工,如图4-7所示。
图4-4 尖角处刀具轨迹比较示意图 a)不好 b)好 c)很好 d)拐角处圆弧连接
第一节 高速切削编程方法
(2)保证工件的高精度 保证工件的高精度,重要的方法是尽量减 少刀具的切入次数,如图4-5所示。
图4-5 减少刀具切入次数示意图
第一节 高速切削编程方法
(3)保证工件的优质表面 1)在高速切削过程中,过小的进给量会影响实际的进给速率,造 成切削力的不稳定,产生切削振动,从而影响工件表面的质量, 故高速切削过程应采用合适的进给量平滑加工,如图4-6所示。
第四章 高速切削与五轴联动加工编程基础
第四章 高速切削与五轴联动加工编程基础
第一节 第二节 第三节 第四节
高速切削编程方法 多轴数控加工的工艺 五轴机床工件坐标系的建立 五轴数控加工刀具的补偿
第一节 高速切削编程方法
一、高速加工编程与普通加工编程的区别 高速切削中的数控编程代码并不仅仅在切削速度、切削深度和进 给量上不同于普通加工,而且还必须是全新的加工策略,以创建 有效、精确、安全的刀具路径,从而达到预期的加工要求。 1.高速加工中数控编程的特点 1)由于高速切削的特殊性和控制的复杂性,编程要注意加工方法 的安全性和有效 2)要尽一切可能保证刀具轨迹光滑平稳,这会直接影响加工质量 和机床主轴等零件的寿命。 3)要尽量使刀具所受载荷均匀,这会直接影响刀具的寿命。 2.对CAM编程软件的功能要求
高速切削刀具在数控加工应用论文
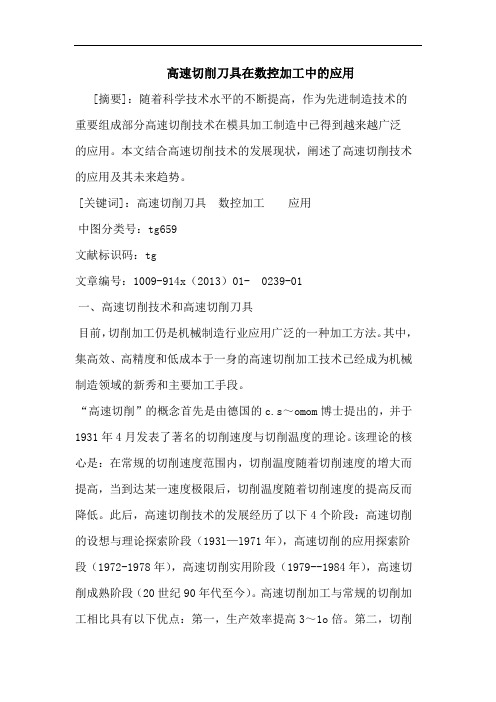
高速切削刀具在数控加工中的应用[摘要]:随着科学技术水平的不断提高,作为先进制造技术的重要组成部分高速切削技术在模具加工制造中已得到越来越广泛的应用。
本文结合高速切削技术的发展现状,阐述了高速切削技术的应用及其未来趋势。
[关键词]:高速切削刀具数控加工应用中图分类号:tg659文献标识码:tg文章编号:1009-914x(2013)01- 0239-01一、高速切削技术和高速切削刀具目前,切削加工仍是机械制造行业应用广泛的一种加工方法。
其中,集高效、高精度和低成本于一身的高速切削加工技术已经成为机械制造领域的新秀和主要加工手段。
“高速切削”的概念首先是由德国的c.s~omom博士提出的,并于1931年4月发表了著名的切削速度与切削温度的理论。
该理论的核心是:在常规的切削速度范围内,切削温度随着切削速度的增大而提高,当到达某一速度极限后,切削温度随着切削速度的提高反而降低。
此后,高速切削技术的发展经历了以下4个阶段:高速切削的设想与理论探索阶段(193l—l971年),高速切削的应用探索阶段(1972-1978年),高速切削实用阶段(1979--1984年),高速切削成熟阶段(20世纪90年代至今)。
高速切削加工与常规的切削加工相比具有以下优点:第一,生产效率提高3~1o倍。
第二,切削力降低30%以上,尤其是径向切削分力大幅度减少,特别有利于提高薄壁件、细长件等刚性差的零件的加工精度。
第三,切削热95%被切屑带走,特别适合加工容易热变形的零件。
第四,高速切削时,机床的激振频率远离工艺系统的固有频率,工作平稳,振动较小,适合加工精密零件。
高速切削刀具是实现高速加工技术的关键。
刀具技术是实现高速切削加工的关键技术之一,不合适的刀具会使复杂、昂贵的机床或加工系统形同虚设,完全不起作用。
由于高速切削的切削速度快,而高速加工线速度主要受刀具限制,因为在目前机床所能达到的高速范围内,速度越高,刀具的磨损越快。
探析数控高速加工技术综述
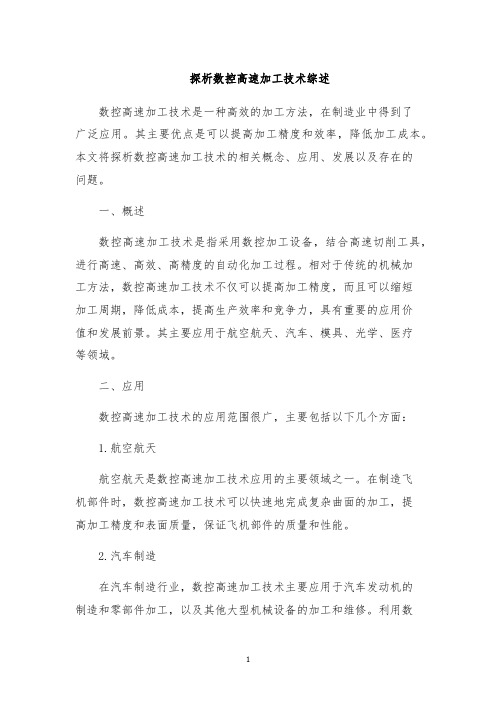
探析数控高速加工技术综述数控高速加工技术是一种高效的加工方法,在制造业中得到了广泛应用。
其主要优点是可以提高加工精度和效率,降低加工成本。
本文将探析数控高速加工技术的相关概念、应用、发展以及存在的问题。
一、概述数控高速加工技术是指采用数控加工设备,结合高速切削工具,进行高速、高效、高精度的自动化加工过程。
相对于传统的机械加工方法,数控高速加工技术不仅可以提高加工精度,而且可以缩短加工周期,降低成本,提高生产效率和竞争力,具有重要的应用价值和发展前景。
其主要应用于航空航天、汽车、模具、光学、医疗等领域。
二、应用数控高速加工技术的应用范围很广,主要包括以下几个方面:1.航空航天航空航天是数控高速加工技术应用的主要领域之一。
在制造飞机部件时,数控高速加工技术可以快速地完成复杂曲面的加工,提高加工精度和表面质量,保证飞机部件的质量和性能。
2.汽车制造在汽车制造行业,数控高速加工技术主要应用于汽车发动机的制造和零部件加工,以及其他大型机械设备的加工和维修。
利用数控高速加工技术,可以提高汽车发动机的工作效率和稳定性,降低噪音和污染,保证汽车的安全性和质量。
3.光学制造在光学行业,数控高速加工技术主要应用于光学元件的制造和加工。
利用数控高速加工技术,可以制造出高精度、高稳定性的光学元件,提高光学设备的精度和性能,满足不同领域的应用需求。
4.医疗制造在医疗行业,数控高速加工技术主要应用于人工骨、植入物等医疗设备的制造和加工。
利用数控高速加工技术,可以使医疗设备更加精确地适应不同的人体部位和病情,提高医疗治疗的效率和安全性。
三、发展趋势随着科技的不断发展和制造业的升级换代,数控高速加工技术也在不断地发展和完善。
未来数控高速加工技术的发展可能会朝着以下几个方向发展:1.高速切削目前数控高速加工技术的切削速度一般在500 m/min以上,但是随着材料的不断进步和加工工具的不断改进,未来数控高速加工技术的切削速度可能会更快,达到1 000 m/min以上。
模具数控高速切削加工的工艺分析与工艺处理

2 半精加工工艺分析
半 精 加 工强 调 加 工效 率 与 质量 要 求 的统 一性 , 半 精加 工 后的零 件应 表面 光 洁 、余量 均 匀 ,模具 半
何轮 廓 。一般 可 采用 大直径 刀具 ,以大切 削 间距 与 较大 的公 差值 进行 切削 加工 。例 如 :使 用端 面铣 刀 和平头 铣 刀及配 合 21 主 轴 的加工 方 式 , 分发 挥 / 2 充 机 床主 轴 的额定 功 率。 分 析粗 加工 的切 削特 征 , 入 时刀具 载 荷显著 切 增 大 ,切 出时 突 然变小 ,趋于 零 。切削过 程 中,切
弧式 )切 入与切 出方式 ,避 免 垂直切 入 与切 出 。如
加工模 具 型腔 时 ,应避 免 刀具 垂直切 入 零件 ,而 应 采用倾 斜 式下 刀方 式 ( 斜 角一般 为 2 。 ~3 。) 倾 0 0 。 有条件 的 话可 采用 螺旋 式下 刀 方式 ,以减小 刀具 载
清角 加工— — 精加 工等 工序 。对于 精度 要求 高
削内侧 拐角 时刀 具载 荷显 著增 大 ,切 削外 侧拐 角时
刀具 载荷 显著 减小 , 致 刀具承 受 的载荷 发生变 化 , 导 造 成切 削过程 不 稳定 ,刀具磨 损快 ,加工 表面 质量 下降 。因 此 ,为 保持切 削 条件 相对 稳定 ,可采用 相 应 措施 改善 切 削状 况 。 1 ( )恒 定 的 切 削 载荷 。通 过 C AM 软件 计 算获 得 恒定 的切 削层 面积 和 材料 切 除 率 ,使切 削载 荷 与刀具 磨损 率保 持均 衡 ,有利 于 提 高加工质量 和延长 刀具寿命 。 ) 斜式切 入与切 出。 ( 倾 2
数控技术第七章 高速切削加工实例

图7-8 粗加工刀具路径
第一节 螺旋薄壁零件加工实例
6)单击“接受”按钮。
图7-9 粗加工仿真
第一节 螺旋薄壁零件加工实例
3.精加工 1)在窗口左侧PowerMILL资源管理器中,右击“刀具”→“产生 刀具”→“端铣刀”,设置铣刀直径为4mm,长度为20mm。 2)在主工具栏中单击刀具路径策略按钮,打开“新的”对话框, 选择“精加工”选项卡,如图7-10所示,然后选择“等高精加 工”,在“等高精加工”对话框中作如图7-11所示的设置。
图7-10 “精加工”选项卡
第一节 螺旋薄壁零件加工实例
图7-11 “等高精加工”对话框
3)在主工具栏中单击进给和转速按钮,
第一节 螺旋薄壁零件加工实例
打开“进给和转速”对话框,设置如图7-12所示参数后,单击 “接受”按钮,退出该对话框。
图7-12 精加工“进给和转速”对话框
第一节 螺旋薄壁零件加工实例
第一节 螺旋薄壁零件加工实例
2)在主工具栏中单击毛坯按钮,打开“毛坯”对话框,在“限界” 选项中输入其长、宽、高3个方向的极限坐标,如图7-2所示。
图7-2 “毛坯”对话框
第一节 螺旋薄壁零件加工实例
2.粗加工
图7-3 “端铣刀”对话框
第一节 螺旋薄壁零件加工实例
1)在刀具工具栏中单击按钮,显示出所有刀具图标,单击按钮, 打开“端铣刀”㊀对话框,选择“刀尖”选项卡,设置参数如图73所示,单击“关闭”退出。 2)在主工具栏中单击刀具路径策略按钮,打开“新的”对话框, 选择“三维区域清除”选项卡,选择“偏置区域清除”,如图7-4 所示,“偏置区域清除”对话框中的设置如图7-5所示。 3)在主工具栏中单击“进给和转速”按钮,打开“进给和转速” 对话框,设置参数如图7-6所示,单击“接受”按钮,退出该对话 框。 4)在主工具栏中单击按钮,打开“快进高度”对话框,按图7-7所 示设置参数后,单击“接受”按钮,退出对话框。
数控机床中高速切削加工技术的应用分析
文 献标识 码 : h
文章编 号 : 1 6 7 1 - 7 5 9 7( 2 0 1 3 )2 0 - 0 0 1 6 - 0 1
位, 对 高速 主轴 的 负载 容 量 和寿 命产 生 直接 影 响 。 因此 , 增 强 机床 主 轴 结构 性能 可 有效 优 化机 床 整体 性 能 , 提 高生 产率 。 所 以在 高速切 削系 统 中 , 须配 备 能移动迅 速 、 定位精 确 的进给 系统 。 面对 高性 能进给 系统 , 机床 导轨 及工作 台结 构面 临更 大 的挑 战 。 2 . 4 数控 高速切 削工 艺
产 生 的热及 切 削产 生 的力 度 的变 化 , 导 致 刀具 受到 磨 损 , 进 而
影 响工 具加 工表 面 。对 高速 切 削 运行 原 理进 行深 入 研 究 , 有 助 于 切削用量 选 择趋于 科学 合理性 , 是 工件 加工 的理论 基础 。
4 高速切 削加 工技术对 数控 机床 提 出的新要 求
过 程 中的稳 定性 , 无法 满足 高 速切 削中零 件 N c程序 的要求 。 因
此 , 在 高 速切 削过 程 中 需 人工 编程 来优 化 或补 充 自动编 程 , 使
得 高 速切 削价值 下 降 。只有 开 发新 的数 据 编程 , 让 主轴 功 率 与
切 削数 据相 吻合 , 扩展 高速 切 削的利用 空 间。
1 数 控高 速切削 加工 的应 用意义
数控 高 速 切 削加 工 , 可 明显 提 高切 削加工 的 生产 效 率 , 提
术, 在 技 术使 用 中 , 相应 加 工 参数 及参 考 实例 相 对 匮乏 。高 速 切 削 工艺 参数 优化 是 目前 高 速 切 削工艺 应 用 的最 大制 约 因素 之
高速数控切削加工中的刀具研究
第一 , 输入漏电流及处理 。 当使用 双线式 传感 器 , 如光 电 传感器 、接近开关或带氖灯的限位开关等作为输入装置 与 P C连接时 , L 由于这些元件在关断时有较大的漏 电流 , 会 引起输入信号错误接通 。 电流小于 1 A时一般没 漏 .m 3 有 问题 ; 如果大 于 1 A, . m 为防止信号错误接通 的发生 , 3 可在 P C的相应输入端并联一个泻放 电阻 ,以降低输人 L 阻抗 , 减少漏 电流的影 响。 第二 , 输出漏电流及处理 : 对晶 体管或可控硅输 出型 P C 其输出接上负载后 , L, 由于输 出 漏 电流会造成设 备的误动作 。 了防止这种情况 , 为 可在输 出负载两端并联旁路 电阻。
序编制 中增加软件容错技术 ,提高 P C控制系统的可靠 L 性设计水平 。 具体方法如下 : 其一 , 加程序复执技术 。 增 该 技术 的主要功能就是如果程序在执行的进程 中出现了错 误或者故障 ,将会对被干扰 的先行指令进行若干次的重 新执行。 假如复执成功 , 则表示干扰 ; 假如复执失败 , 则表
切 削相 适 应 的 刀具 材 料 、 具 结构 及 刀 具 监控 技 术 。 刀
关键词: 高速 切 削 ; 刀具 ; 数控 加 工 中图 分 类 号 : G 5 T 69 文 献标 识 码 : A 文 章 编 号 :0 6 83 (0 12 — 06 0 10 — 97 2l) 2 09 — 1
示软件失败 ( 通常显示为“ al )其二 , Fu ” 。 t 处理死循 环。 由 程序确定导致死循 环的原因是主要故障还是次要故障 , 如果是主要故障则要进行停机处理 ;如果是次要故 障则
要进行相应的子程序处理 。 其三 , 设置软件延时。 对于控
数控高速切削加工技术的发展与应用研究
摘 要 : 文系统 介绍 了数 控高速切 削加工的基 础理论及 发 展 过程 , 本 分析 了高速 k - 的优 点和应峒 领域 , Y - - 总结了发 展 数控 高速切 削加 工需要 的关键
技 术和研 究方向。
关 键词 : 高速切 削 关键 技 术 应 用研 究 中图分 类号: TG5 6 文献 标i.5 A 0 P : 文章编 号: 0 7 9 1 ( 0 1 0 —0 0 —0  ̄ 10— 44 21) 6 07 2 ,
数 控 高 速 切 削 技 术 ( i pe a h ig S Hg S edM c i n , M,或 Hg pe 切 削 加 工 的 生产 率 ,和 常 规 切 削 相 比还 具 有 一 些 明 显 的 优 越 性 : h n H i S ed h C tn, C ,是提 高加工效 率和加工质量 的先进制造技术之 , ut g i HS ) 第 一 、切 削 力 小 : 在 高 速铣 削 加 工 中, 用 小 切 削 量 、高 切 削 速 采 相 关 技 术 的 研 究 已成 为 国 内外 先 进 制 造 技 术 领 域 重 要 的研 究 方 度 的切削形 式, 使切削力 比常规 切削 降t 3 % 以 E,尤 其是 主轴  ̄0 向 。我 国是 制 造 大 国 ,在 世 界 产 业 转 移 中 要尽 量 接 受 前 端 而 是 轴 承 、刀具 、工件受到的径 向切 削力大幅度减少。既减轻刀具磨 后 端 的转 移 , 即要 掌 握先 进 制 造 核 心 技 术 ,否 则 在 新 一 轮 国 际 产 损 ,又有 效控 制 了加: 【系统 的振动 ,有 利于提 高加工 精度 。第 业 结 构 调 整 中 ,我 国 制造 业 将 进 一 步 落后 。研 究先 进 技 术 的理 论 二 、材料切除率高: 采用 高速切 削 ,切 削速度和进给速度都大幅度 和应用迫在眉睫 。 提 高 ,相 同 时 间 内的 材 料 切 除率 也 相 应 大 大 提 高 。 从 而 大 大 提 高
高速切削加工技术
高速切削的适用性
高速切削的适用性
高速加工作为一种新的技术,其优点是显而易见的,它给传统的金属切削理论带来了一种革命性的变化。那 么,它是不是放之四海而皆准呢?显然不行。即便是在金属切削机床水平先进的瑞士、德国、日本、美国,对于这 一崭新技术的研究也还处在不断的摸索研究当中。实际上,人们对高速切削的经验还很少,还有许多问题有待于 解决:比如高速机床的动态、热态特性;刀具材料、几何角度和耐用度问题,机床与刀具间的接口技术(刀具的 动平衡、扭矩传输)、冷却润滑液的选择、CAD/CAM 的程序后置处理问题、高速加工时刀具轨迹的优化问题等等。
(1)CAM系统应具有很高的计算编程速度
高速加工中采用非常小的切给量与切深,故高速加工的NC程序比对传统数控加工程序要大得多,因而要求计 算速度要快,要方便节约刀具轨迹编辑,优化编程的时间。
(2)全程自动防过切处理能力及自动刀柄干涉检查能力
高速加工以传统加工近10倍的切削速度进行加工,一旦发生过切对机床、产品和刀具将产生灾难性的后果, 所以要求其CAM系统必须具有全程自动防过切处理的能力。高速加工的重要特征之一就是能够使用较小直径的刀 具,加工模具的细节结构。系统能够自动提示最短夹持刀具长度,并自动进行刀具干涉检查。
如此看来,主轴转速为10~r/min这样的高速切削在实际应用时仍受到一些限制: (1)主轴转速10~r/min时,刀具必须采用 HSK 的刀柄,外加动平衡,刀具的长度不能超过120mm,直径不 能超过16mm,且必须采用进口刀具。这样,在进行深的型腔加工时便受到限制。 (2)机床装备转速为10~r/min的电主轴时,其扭矩极小,通常只有十几个N·m,最高转速时只有5~6N·m。 这样的高速切削,一般可用来进行石墨、铝合金、淬火材料的精加工等。 (3)MIKRON公司针对这些情况开发了一些主轴最高转速为r/min、r/min、r/min和r/min的机床,尽力提高 进给量(~mm/min),以保证机床既能进行粗加工,又能进行精加工,既省时效率又高。
- 1、下载文档前请自行甄别文档内容的完整性,平台不提供额外的编辑、内容补充、找答案等附加服务。
- 2、"仅部分预览"的文档,不可在线预览部分如存在完整性等问题,可反馈申请退款(可完整预览的文档不适用该条件!)。
- 3、如文档侵犯您的权益,请联系客服反馈,我们会尽快为您处理(人工客服工作时间:9:00-18:30)。
浅析数控高速切削加工
【摘要】数控高速切削加工以高效率和高精度为基本特征,它在切削机理上是对传统切削的重大突破,是近20多年来迅速崛起的先进制造技术之一。
文章介绍了“数控高速切削加工”的内涵、优势、应用现状和发展趋向,提出了在实现高速切削加工中应关注的主要问题。
【关键词】高速;加工机理;优势;推广价值
1.前言
高速切削加工是集高效、优质、低耗于一身的先进制造技术,在常规切削加工中备受困扰的一系列问题,通过高速切削加工的应用能够得到解决。
“高速切削”的概念是由德国物理学家
carl.j.salomon提出,于1931年4月提出了著名的切削速度与切削温度理论。
该理论的核心是:在常规的切削速度范围内,切削温度随着切削速度的增大而提高,当到达某一速度极限后,切削温度随着切削速度的提高反而降低。
随后,高速切削技术的发展经历了4个阶段:高速切削的设想与理论探索阶段(193l—l971年),高速切削的应用探索阶段(1972-1978年),高速切削实用阶段(1979--1984年),高速切削推广阶段(20世纪90年代至今)。
对高速切削加工的界定有以下几种划分思路:一是以主轴转速作为界定高速切削加工的尺度,认为主轴转速在10000-20000r/min 以上即为高速切削加工;二是以主轴直径d和主轴转速n的乘积dn 来界定,当dn值达到(5~2000)×105mm.r/min,则认为是高速
切削加工,新近开发的加工中心主轴dn值大都已超过100万;三是以切削速度高低来区分,认为切削速度跨越常规切削速度5至10倍即为高速切削加工。
2.数控高速切削加工的优势
随着切削速度的提高,单位时间毛坯材料的去除率增加,加工效率提高,从而缩短了产品的制造周期,提高了产品的市场竞争力。
同时,高速切削加工的“量小速快”使切削力减少,切屑的高速排除,减少了工件的切削力和热应力变形,十分有利于刚性差和薄壁零件的加工。
高速切削加工中,主轴转速的提高使切削系统的工作频率远离了机床的低阶固有频率,提高了切削系统的刚性,进而使产品表面质量获得提高。
数控高速切削加工和常规切削相比的主要优势可归纳为:第一,生产效率可提高3~10倍。
第二,切削力可降低30%以上。
第三,切削热95%被切屑及时带走,特别适合加工容易热变形的零件。
第四,机床的激振频率远离工艺系统的固有频率,工作平稳,适合加工精密零件。
第五,经济效益明显。
3.数控高速切削加工的应用
数控高速切削工艺的应用,能使制造成本降低20%左右,产生新的经济增长点。
以某锻造厂加工曲轴和连杆锻模为例,传统的加工工序为:外形粗加工→仿形铣粗加工型槽→热处理→外形精加工→数控电火花粗、精加工型槽→钳工打磨抛光型槽→表面强化处理。
而采用高速切削加工后的工序为:外形粗加工→热处理→外形精加
工→高速铣加工型槽→表面强化处理。
通过高速铣削加工直接完成淬硬钢模具,使生产成本从传统工艺的27000多元降到22000元。
高速切削加工具备过程平稳、振动小的特点,与常规切削相比,可提高加工精度1~2级,并能取消后续的光整加工。
同时,采用数控高速切削加工工艺,可以在一台机床上实现对复杂整体结构件的粗、精加工,减少了转工序中多次装夹带来的定位误差,也有利于提高工件的加工精度。
如某企业加工的铝质模具,模具型腔长达1500mm,要求尺寸精度误差±0.05mm,表面粗糙度ra0.8μm。
原先的制造工艺为:粗刨→半精刨→精刨→铲刮→抛光,制造周期为60小时。
采用高速切削加工工艺后,改为半精加工和精加工,加工周期仅需6小时,加工效率提高近10倍。
可见,高速切削加工在制造业中有着广阔的应用前景。
4.数控高速切削加工的关键环节
高速切削加工不仅包含着切削过程的高速,还包含了工艺过程的集成和优化,可谓是加工工艺的统一。
高速切削加工是在数控装置、机床结构及材料、机床设计、制造工艺、高速主轴系统、快速进给系统、高性能cnc系统、高性能刀夹系统、高性能刀具材料及刀具设计制造工艺、高效高精度测量测试工艺、高速切削工艺等诸多技术均获得充分成熟之后综合而形成,可谓是一个复杂的系统工程。
高速切削加工应用中还存在着一些有待解决的问题,如对高硬度材料的切削机理、刀具在载荷变化过程中的破损内因的研究,高
速切削数据库的建立,适用于高速切削加工状态的监控技术和绿色制造技术的开发等。
数控高速切削加工所用的cnc机床、刀具和cad/cam软件等,价格昂贵,初期投资较大,在一定程度上也制约着高速切削技术的推广应用。
实现数控高速切削加工的关键环节如下:
4.1高速切削机理的研究
高速切削加工过程是导致工件表面层产生高应变速率的高速切削变形和刀具与工件之间的高速切削摩擦行为形成的为热、力耦合不均匀强应力场的制造工艺。
与传统的切削加工相比,加工中工件材料的力学性能、切屑形成、切削力学、切削温度和已加工表面形成等都有其不同的特征和规律。
各类材料在高速加工前提下,切屑的形成机理,切削力、切削热的转变规律,刀具磨损规律及对加工概况质量的影响规律,都有了极大的变化。
通过对以上理论的研究,有利于促进高速切削工艺规范的确定和切削用量的选择,为具体零件和材料的加工工艺拟定能够提供理论依据。
4.2高速切削机床的配备
高速切削机床是实现高速切削加工的必备条件,高速主轴系统、快速进给系统和高速cnc控制系统是关键。
它要求具备高性能的主轴单元和冷却系统、高刚性的机床结构、安全装置和监控系统以及优良的静动力特性,具有技术含量高、机床制造难度大等特点。
通常,选用高速数控车床、加工中心,也有釆用专用的高速铣、钻床,
它们都具有高速主轴系统和高速进给系统。
一般主轴转速在10000r/min以上,有的甚至高达60000-100000r/min,且要保证动态和热态机能。
也可釆用高速丝杆或直线电机,提高机床进给系统的快速响应。
目前,直线电机最高加速度可达2-10g(g为重力加速度),最大进给速度可达60-200m/min或更高。
4.3高速切削工艺的刀具
随着切削速度的大幅度提高,刀具材料和刀具制造工艺都要能适应新的环境。
刀具系统必需具有较高的几何精度和装夹再定位精度,以及较高的装夹刚度。
高速切削刀具除了满足静平衡外还必需满足动平衡要求,尽可能减轻刀体质量,以减轻高速扭转时所受到的离心力。
高速切削中常用的刀具材料有单涂层或多涂层硬质合金、陶瓷、立方氮化硼(cbn)、聚晶金刚石等,高速切削刀具刀刃的外形正向着高刚性、复合化、多刃化和超精加工方向发展。
4.4数控编程系统要求
高速切削有着比传统切削更特殊的工艺要求,除了要具备高速切削机床和高速切削刀具外,还要有合适的cam编程软件。
高速加工的cam编程系统应具有很高的计算速度、较强的插补功能、全程自动过切检查及处理能力、自动刀柄与夹具干涉检查、进给率优化处理功能、待加工轨迹监控功能、刀具轨迹编辑优化功能和加工残余分析功能等特点。
高速切削应用程序首先要注意加工的安全性和有效性;其次,要保证刀具轨迹光滑平稳,这会直接影响加工质量和机床主轴等零件的寿命;第三,要尽量使刀具载荷均匀,这会直
接影响刀具的寿命。
通常,使用的cnc软件中的编程功能都不能满足在整个切削过程中保证切削载荷不变的要求,需要由人工加以填补和优化,这在一定程序上降低了高速切削的价值。
因此,必需研究一种全新的编程方式,使切削数据适合高速主轴的功率特征,充分发挥数控高速切削加工的优势。
目前,引进的cam软件,如cimatron、mastercam、ug、pro/e等,都在逐步增添适合于高速切削的编程模块,为高速切削加工的应用提供了良好的条件。
5.结束语
由于数控高速切削加工在提高生产效益、降低制造成本中潜力巨大,美国、日本等国早在上世纪60年代初,就起动了超高速切削机理的研究。
1978年美国完成了对高速加工数控铣床的改造,完成主轴转数30000r/min与100000r/min的重要参数指标。
现在,欧美等发达国家生产的各类超高速机床已经实现商业化,在飞机、汽车及模具制造行业中获得了大量的应用。
我国在研究和开发高速切削工艺方面,与国外工业发达国家相比,仍存在着较大的差距。
为适应社会经济发展需要,满足航空航天、汽车、模具等各行业的制造需求,必需加强对高速加工工艺基本理论的研究,加快高速主轴单元和高速进给单元的开发,努力实现高速机床的国产化,开发适应高速加工的cad/cam自主软件系统和后置系统,建立新型检测工艺监控系统。
发展数控高速切削加工是提高加工效率和质量、降低成本的主要途径,把当前的高速切削水平实用化,使我国机械加工业整体切削效率提高1~2倍,缩小
与工业发达国家的差距,是我国从事制造行业专业人员在新世纪的奋斗目标。
参考文献:
[1] 孙文诚高速切削加工模具的关键工艺研究 [j].机械制造与自动化2008(5).
[2] 韩福庆高速切削刀具材料的开发与选择[j] 化学工程与装备 2008.
[3] 周纯江叶红朝高速切削刀具相关关键技术的研究[j] 机械制造2008.。