基于精益生产的“一个流”和生产线平衡的研究
基于精益思想的生产线改造仿真与研究

ted method with eM—Plant software.The simulation output analysis was made based on the throughput,W IP and the f lexibility to market.The effect of traditional method and that of the method based on lean thought were compared,which provides a basis for the practical improvement of production lines. Key words:lean thought;production line;eM -Plant;simulation
和外部供应链 、生产资源 、商业运作过程 ,用户 可以 通过 仿 真模 型 分析不 同变 型产 品 的影 响 。
Research on Reconstruction and Sim ulation of Production Line Based on Lean Thought
Liu Guang—fu ,Li M iao (1.School of Economics& Management;2.School of Mechanical Engineering,Ton ̄i University,Shanghai,20180 4 ,China)
A bstract:Lean thought was applied in the reconstruction of production line and lean thought criteria:line bMancing,continuous—flow,MIX production and standard management,were followed.By analyzing the as—
基于精益生产的汽车玻璃生产线平衡优化研究毕业论文 精品
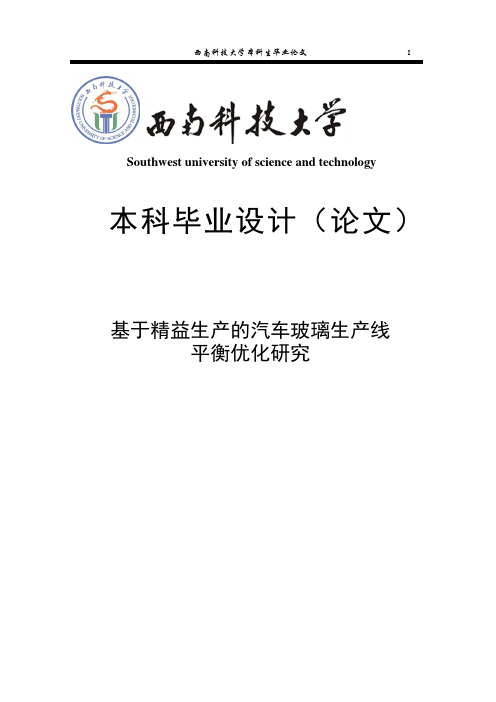
Southwest university of science and technology本科毕业设计(论文)基于精益生产的汽车玻璃生产线平衡优化研究毕业设计(论文)原创性声明和使用授权说明原创性声明本人郑重承诺:所呈交的毕业设计(论文),是我个人在指导教师的指导下进行的研究工作及取得的成果。
尽我所知,除文中特别加以标注和致谢的地方外,不包含其他人或组织已经发表或公布过的研究成果,也不包含我为获得及其它教育机构的学位或学历而使用过的材料。
对本研究提供过帮助和做出过贡献的个人或集体,均已在文中作了明确的说明并表示了谢意。
作者签名:日期:指导教师签名:日期:使用授权说明本人完全了解大学关于收集、保存、使用毕业设计(论文)的规定,即:按照学校要求提交毕业设计(论文)的印刷本和电子版本;学校有权保存毕业设计(论文)的印刷本和电子版,并提供目录检索与阅览服务;学校可以采用影印、缩印、数字化或其它复制手段保存论文;在不以赢利为目的前提下,学校可以公布论文的部分或全部内容。
作者签名:日期:基于精益生产的汽车玻璃生产线平衡优化研究摘要:如今的制造行业竞争日趋激烈,在企业推行精益生产方式成为企业管理者非常关注的问题。
针对福耀玻璃汽车配件有限公司平弯钢化厂生产线不平衡及产量不能满足订单需求的情况,本文运用精益生产和工业工程方法和理论,对该厂区生产现状进行数据收集,对生产系统进行现场分析,发现其生产过程中存在的问题并提出改进方案,并对改善后的生产系统进行效果评估。
本文的主要设计内容如下:(1)生产现状的分析和原始数据的采集,运用IE基础手法对生产线进行系统的分析。
(2)根据收集数据找出生产系统瓶颈工序,计算目前的生产线平衡率。
(3)对生产线进行优化改善。
运用基础IE手法(如MOD法、联合作业分析等)提出改进方案,改善瓶颈工序,建立新的生产线平衡。
(4)评估改善后的生产系统。
通过平衡率和瓶颈工序对改善的方案进行评价。
精益论文范文

学习与实施精益生产的关键——深入理解、掌握精益生产的理念和三条基本原理川仪金属功能材料分公司黄德钧从2008年5月17日开始,至今已参加了9次(9天)由重庆川仪总厂有限公司组织的精益生产管理培训。
通过这次精益生产管理培训,较系统的对精益生产进行了学习,使精益生产的精髓得以理解。
在培训即将结束之际,将一点学习心得整理如下供大家商榷。
接触“精益生产”一词,已是较早的事了。
那是上世纪的八十年代末九十年代初,由菲利普·科特勒等人合着的一本叫《新的竞争——日本打进欧美市场的成功经验》小册子中有这样一段描述:由于日本汽车制造业都将其零部件供应厂安排在自己同一工业区之内,如同在自己的经营活动中所运用的方法一样,所以能采用著名的“看板”(Kanban)即“及时供应”(“Just-in-time”inventory system)。
合理的生产流水线的安排减少了运输费用,使运输中造成的损坏减少到最低程度,并大幅度降低了必要的库存储备。
在“看板”制度下,很多部件一直要等到下一道工序需要前几小时才生产出来。
当时,想这是一种什么样的生产管理系统,令老美大加赞赏。
于是对这方面的资料与书籍进行了查阅,接触到“精益生产”一词,慢慢的知道其演变过程。
然而,这个期间大多数国内资料都将“精益生产”的具体操作都用“看板”管理来演绎。
逐渐的就有种感觉,似乎“精益生产”=“准时化生产”=“看板”管理。
同时,大量的成功案例都在机械加工、电子器件组装、仪器仪表装配类加工装配型企业上,而在流程型企业中宣有成功案例。
当时,流程型企业的成功生产管理案例主要为推行MRP获得。
认为像我所在的流程型企业应当从推行MRP来获得生产效率的提高(现在应是ERP管理系统)。
正是这种对精益生产的认识不足,造成了今天的后果——我们不得不重新学习、了解、认识和利用JIT哲理与精益生产。
上世纪中叶,当美国的汽车工业处于发展的顶峰时,以大野耐一为代表的丰田人对美国的大批量生产方式进行了彻底的分析,得出了两条结论:1.大批量生产方式在削减成本方面的潜力要远远超过其规模效应所带来的好处2.大批量生产方式的纵向泰勒制组织体制不利于企业对市场的适应和职工积极性、智慧和创造力的发挥基于这两点认识,丰田公司根据自身面临需求不足、技术落后、资金短缺等严重困难的特点,同时结合日本独特的文化背景,逐步创立了一种全新的多品种、小批量、高效益和低消耗的生产方式。
精益生产之生产线平衡的定义
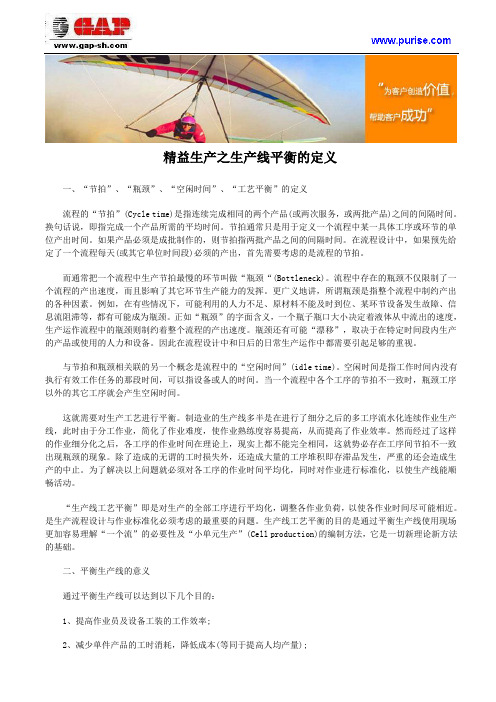
精益生产之生产线平衡的定义一、“节拍”、“瓶颈”、“空闲时间”、“工艺平衡”的定义流程的“节拍”(Cycle time)是指连续完成相同的两个产品(或两次服务,或两批产品)之间的间隔时间。
换句话说,即指完成一个产品所需的平均时间。
节拍通常只是用于定义一个流程中某一具体工序或环节的单位产出时间。
如果产品必须是成批制作的,则节拍指两批产品之间的间隔时间。
在流程设计中,如果预先给定了一个流程每天(或其它单位时间段)必须的产出,首先需要考虑的是流程的节拍。
而通常把一个流程中生产节拍最慢的环节叫做“瓶颈“(Bottleneck)。
流程中存在的瓶颈不仅限制了一个流程的产出速度,而且影响了其它环节生产能力的发挥。
更广义地讲,所谓瓶颈是指整个流程中制约产出的各种因素。
例如,在有些情况下,可能利用的人力不足、原材料不能及时到位、某环节设备发生故障、信息流阻滞等,都有可能成为瓶颈。
正如“瓶颈”的字面含义,一个瓶子瓶口大小决定着液体从中流出的速度,生产运作流程中的瓶颈则制约着整个流程的产出速度。
瓶颈还有可能“漂移”,取决于在特定时间段内生产的产品或使用的人力和设备。
因此在流程设计中和日后的日常生产运作中都需要引起足够的重视。
与节拍和瓶颈相关联的另一个概念是流程中的“空闲时间”(idle time)。
空闲时间是指工作时间内没有执行有效工作任务的那段时间,可以指设备或人的时间。
当一个流程中各个工序的节拍不一致时,瓶颈工序以外的其它工序就会产生空闲时间。
这就需要对生产工艺进行平衡。
制造业的生产线多半是在进行了细分之后的多工序流水化连续作业生产线,此时由于分工作业,简化了作业难度,使作业熟练度容易提高,从而提高了作业效率。
然而经过了这样的作业细分化之后,各工序的作业时间在理论上,现实上都不能完全相同,这就势必存在工序间节拍不一致出现瓶颈的现象。
除了造成的无谓的工时损失外,还造成大量的工序堆积即存滞品发生,严重的还会造成生产的中止。
生产线平衡分析与改善(最全面的IE分析-生产线平衡)

2023/12/24
8
二、流水生产线概述
1、 流水生产的基本概念 ● 流水线生产的分类
➢单人单产品式 ➢单产品固定式 ➢多产品固定式 ➢自由流水式 ➢连续传动流水式 ➢ 间歇传动流水式 ➢分组式
设某一产品从原料到成品,需经过A、B、C、D四个工序,其基本标 准工时(秒/个)及相关生产效率、良率、投入机台/人员数分别见表11: 可以求各工序每小时产量为: A工序每小时产量=(3600秒÷6.90)×90%×95%×1=470.87个 B工序每小时产量=(3600秒÷5.1)×80%×99.5%×1=470.87个 C工序每小时产量=(3600秒÷34.40)×100%×99.9%×2=209.09个 D工序每小时产量=(3600秒÷30.40)×100%×99.5%×2=238.8个 。
IE工业工程
-----生产线平衡
主讲:
课 程 内容
生产线平衡 一、生产线平衡的概述 二、流水生产线概述 三、生产线平衡的设计 四、生产线平衡的方法及改善原则 5、案例分析
2023/12/24
2
1.概念
一、生产线平衡的概述
生产线平衡即对生产的全部工序进行平均化,调整作业 负荷,以使各作业的时间尽可能相近的技术手段与方法,它 是生产流程设计及作业标准化中最重要的方法,是通过平衡 生产线使现场真正实施生产同步化,从而达到“一个流”的 理想。
2023/12/24
。
28
四、生产线平衡的改善方法与原则
2、平衡率改善的图示。
2023/12/24
29
四、生产线平衡的改善方法与原则
精益生产--生产线平衡(pdf 20页)
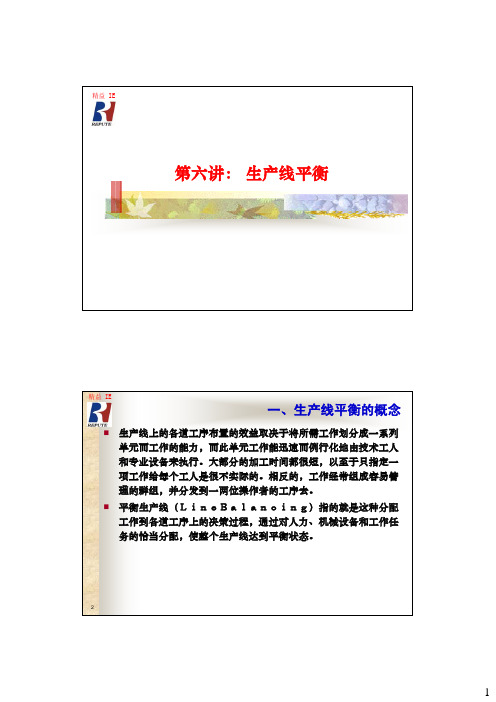
精益 IE
第六讲: 的概念
生产线上的各道工序布置的效益取决于将所需工作划分成一系列 单元而工作的能力,而此单元工作能迅速而例行化地由技术工人 和专业设备来执行。大部分的加工时间都很短,以至于只指定一 项工作给每个工人是很不实际的。相反的,工作经常组成容易管 理的群组,并分发到一两位操作者的工序去。
8
4
精益 IE
5.重排的方法
9
精益 IE
6.作业改善后合并的方法
10
5
精益 IE
案例
11
精益 IE
改善
分析这条生产线可以发现,瓶颈工序就是钻孔的工序。针对这八道工序的特 点,分解工序3(钻孔)的作业动作,提出以下的平衡改善措施:
改善瓶颈作业(即工序3钻孔),将工序3的定位动作(8秒)分担给工序2完 成。
Cell Line (目前Cell Line作业站并无一个统一的称呼,如NPS作 业站、流线化生产、一个流作业、摊贩式作业等)是指生产上的 一个组织单位。一个作业站配备有生产一类产品的全套设备,同 时还配有一名或若干名掌握多种技能、能熟练使用这些设备的全 能作业者。每个作业站独立完成整个产品的全部生产作业。整个 车间或工厂则由多个作业站组成。
因此希望朝多制程操作的作业方式安排
16
8
精益 IE
5、作业员的多能工化
具有能操作多制程作业能力的作业员,称为多能工。
精益生产如何实现生产线平衡

精益生产如何实现生产线平衡在当今竞争激烈的制造业环境中,精益生产已经成为众多企业追求卓越运营和提高竞争力的重要手段。
而实现生产线平衡是精益生产中的一个关键环节,它对于提高生产效率、降低成本、提升产品质量以及增强员工满意度都具有重要意义。
那什么是生产线平衡呢?简单来说,生产线平衡就是将生产线上各个工序的作业时间进行合理分配,使得每个工序的作业负荷尽可能相等,从而减少生产线中的闲置时间和等待时间,提高整体生产效率。
要实现生产线平衡,首先需要对生产线进行详细的分析和评估。
这包括对每个工序的作业内容、作业时间、操作方法以及所需的设备和工具等进行深入了解。
通过现场观察、数据收集和时间测量等方法,获取准确的生产信息。
在收集到相关数据后,我们可以使用一些工具和方法来分析生产线的平衡状况。
例如,绘制工艺流程图可以直观地展示生产线上各个工序的先后顺序和相互关系;制作作业时间柱状图可以清晰地看出每个工序作业时间的长短差异。
接下来,我们可以根据分析结果,找出影响生产线平衡的关键因素。
常见的影响因素包括:工序作业内容不合理、作业顺序安排不当、设备故障或性能不佳、员工技能水平参差不齐以及物料供应不及时等。
针对这些问题,我们可以采取一系列措施来实现生产线平衡。
首先,对工序进行重新设计和优化。
去除不必要的作业步骤,简化复杂的操作,将一些可以合并的工序进行合并,从而减少工序数量,降低作业时间。
其次,合理安排作业顺序。
根据工序之间的先后关系和作业时间,采用启发式算法或仿真软件等工具,确定最优的作业顺序,以减少工序之间的等待时间和运输时间。
再者,提升设备的稳定性和性能。
定期对设备进行维护保养,及时排除故障,确保设备能够正常运行。
对于性能不足的设备,可以考虑进行升级改造或更换。
同时,加强员工培训,提高员工的技能水平和工作效率。
通过培训,使员工能够熟练掌握操作技能,减少因操作不当而导致的时间浪费。
此外,优化物料供应流程也是非常重要的。
生产线平衡分析计划书范文
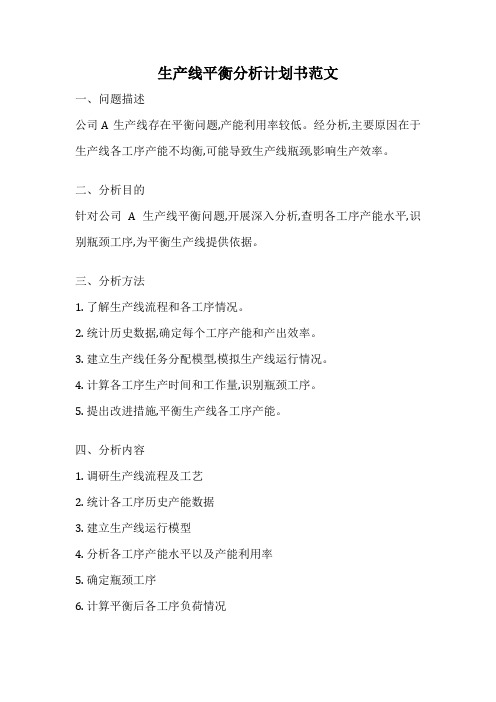
生产线平衡分析计划书范文
一、问题描述
公司A生产线存在平衡问题,产能利用率较低。
经分析,主要原因在于生产线各工序产能不均衡,可能导致生产线瓶颈,影响生产效率。
二、分析目的
针对公司A生产线平衡问题,开展深入分析,查明各工序产能水平,识别瓶颈工序,为平衡生产线提供依据。
三、分析方法
1. 了解生产线流程和各工序情况。
2. 统计历史数据,确定每个工序产能和产出效率。
3. 建立生产线任务分配模型,模拟生产线运行情况。
4. 计算各工序生产时间和工作量,识别瓶颈工序。
5. 提出改进措施,平衡生产线各工序产能。
四、分析内容
1. 调研生产线流程及工艺
2. 统计各工序历史产能数据
3. 建立生产线运行模型
4. 分析各工序产能水平以及产能利用率
5. 确定瓶颈工序
6. 计算平衡后各工序负荷情况
五、预期效果
通过对生产线进行深入分析,识别瓶颈工序,平衡各工序产能,使生产线达到均衡状态,提高整体产能利用率,为公司增加产值提供依据。
六、时间安排
1月:数据收集及分析模型建立
2月:分析报告初稿完成
3月:报告定稿及改进方案呈报
以上就是生产线平衡分析计划书的内容大纲,希望能为您的分析提供参考。
如果需要,还可根据实际情况进行 detail 调整完善。
- 1、下载文档前请自行甄别文档内容的完整性,平台不提供额外的编辑、内容补充、找答案等附加服务。
- 2、"仅部分预览"的文档,不可在线预览部分如存在完整性等问题,可反馈申请退款(可完整预览的文档不适用该条件!)。
- 3、如文档侵犯您的权益,请联系客服反馈,我们会尽快为您处理(人工客服工作时间:9:00-18:30)。
天津大学
硕士学位论文
基于精益生产的“一个流”和生产线平衡的研究
姓名:汪凯
申请学位级别:硕士
专业:工业工程
指导教师:沈江;张玉海
20071201
基于精益生产的“一个流”和生产线平衡的研究
作者:汪凯
学位授予单位:天津大学
1.学位论文彭阳自动转换开关精益生产与生产线平衡研究2008
精益生产的核心内容就是在企业内部减少资源浪费,以最小的投入获得最大的产出。
其最终目标就是要以具有最优质量和最低成本的产品,对市场的需求做出最迅速的响应。
而通过生产线的平衡可以实现单元生产、提高生产应变能力、对应市场变化、实现柔性生产系统。
本文通过对精益生产、生产线平衡及相关知识的研究,将理论运用到实际中,完成了分析自动转换开关产品的市场需求、研究产品的结构和装配工时、规划物料和生产线的布置、设计工作台和生产线线体、分析产品的价值流等工作。
其间利用MTM软件分析工时、用正交试验设计方法寻求使生产线效率较高的最适水平、用价值流图分析研究产品的整个价值流、用仿真软件模拟设计出来的U型生产线并分析模拟结果,最终设计出产量能满足客户需求的、投资成本比较低的、生产线各项指标也比较优化合理的自动转换开关的生产线。
该生产线主线与单组线独立开,主线为一条U型线,三个工位两人操作,装配工位平衡率达到96%以上。
单组线则为一条假U型线,仅为了缩短作业员的移动距离和线体占地面积而将各单组工位排成U型。
通过这样的研究过程,能更早地建立起优化的生产线体进行生产,使得自动转换开关在工厂正式生产的进程加快,大大缩短了从产品研发到进入工厂正式生产的时间,减少了时间、人力及投资的浪费。
2.期刊论文王巍.李洋.闻金珠.Wang Wei.Li Yang.Wen Jinzhu基于精益生产的美的微波炉生产现场改善分析-森
林工程2007,23(5)
基于精益生产的理论.对现场改善理论进行了研究,重点分析了现场改善的方法,对现有的现场改善方法进行总结和扩充,详细研究各方法的功能、特点、实施步骤.并针对目前现场改善方法相互孤立,不成体系的状况,结合美的企业具体情况,对现有方法进行整合,建立了基于精益生产的现场改善方法体系,包括方法研究、作业测定、5S管理、定王管理、以及生产线平衡等,并提出体系中各部分的功能及其相互之间的联系,在美的微波炉公司总装厂现场得以应用,对其应用效果进行对比分析.
3.期刊论文叶晓素.蔡勇.YE Xiao-su.CAI Yong精益生产方式下生产线平衡的研究-机电工程技术2009,38(11)
生产线平衡是影响企业发展的重要因素,精益生产方式的理论为解决生产线平衡问题提供了一个新的且切实可行的方法.运用精益生产理论对生产线五要素进行分析,找出产生瓶颈工位的原因,提出解决方案,调整整条生产线,将企业的各种浪费降到最低,从而达到使各工位负荷尽量相等、提高生产线平衡率的目的.
4.学位论文杜永杰精益生产在S企业中的应用研究2008
精益生产是一种先进的生产经营管理理论。
它的核心思想是消除浪费,消除生产全过程中一切不产生附加价值的劳动和资源,追求“尽善尽美
”,达到增强企业适应市场多元化的应变能力,获得更高的经济效益。
本文结合大型手机制造厂S公司的实际情况,运用精益生产的理论对企业的生产经营进行了分析和改进。
本文是按照3个改进方案进行的。
第一,根据分析物料流动的路线研究,改善了公司的物流路线,消除了物料路线交叉造成的等待。
同时改进了原材料的包装形式,在没有增加仓库配料区域的情况下,增加了配料区的日生产能力。
第二,基于对公司生产效率现状的分析。
提高生产线平衡在没有增加生产面积和投入人数的情况下增加了日产出数。
应用MOPATS理论重新制定标准时间,消除了各个项目之间的差异,并且建立了动素库为新项目的前期导入作为参考资料。
培养多技能工(可以完成多个操作站,多个项目的操作),达到提高生产效率的目的。
第三,分析公司设备使用效率的现状,引入多产品共线的概念,提高了公司的总设备使用效率。
在没有增加新的生产线体的情况下,增加手机的生产品种。
5.学位论文窦永昌精益生产研究2005
本文主要阐述了本人在工作中对精益生产的研究。
结合本企业的精益生产实际,分析了精益生产过程中的产生的一些问题,这些问题在其他企业中也可能发生,因此分析这些问题是有代表性的。
本文分析了影响生产线效率的一些因素,首先对生产时间和非生产时间进行了整体分析,然后就非生产时间进行了细分,找出了影响生产线效率的瓶颈,然后通过流程优化和生产线平衡的方法来进行改善。
6.期刊论文汪凯.WANG Kai基于精益生产的"一个流"和生产线平衡的研究-企业技术开发(学术版)2009,28(8)
根据市场预测创建产品、业务运作由销售预测来推动、保持大量(他们认为市场需要的)库存的做法已经过时.顾客的个性化需求年代已经来因此,生产只能够被真正的顾客需求所拉动,而不是你希望销售的东西来推动.这就是精益生产与传统方式的主要区别.
7.学位论文饶中生产线过程重组案例研究2004
通过研究分析,提出了底层制造系统的重组应综合业务流程再造(Business Process Reengineering, BPR)和精益生产(Lean Production)的思想和基本原理,从流程分析开始,应用精益生产的五原则(价值、价值流、流动、拉动和尽善尽美)以及工作研究中的ECRS(取消、合并、重排、简化)四大原则,消除流程中的各种浪费,使所有增值作业流动起来。
在流程中使用看板拉动技术,保证流程中的库存最小,同时使系统的瓶颈显现出来。
应用方法研究优化工序的操作消除操作中的浪费。
通过将工序操作分解为工作单元并应用预定时间标准法测算出各工作单元中的标准时间。
最后应用生产线平衡的技术,重组作业,使流程的平衡延迟最小化,从而完成生产线过程的重组工作。
论文是以一家外资电子公司的装配线重组为背景,对底层制造系统重组的理论、原则、方法进行了探讨,对实践中的关键技术进行了总结,对底层制造系统重组进行了综合的阐述。
8.学位论文凌永昶基于生产线平衡优化的价值流图析应用研究2009
产品的生产过程由若干生产活动组成,生产活动又分为增值活动,不增值活动和浪费三种,消除浪费、尽量减少非增值活动、提高增值活动的效率,这是企业缩短产品生产周期,占领市场先机,降低库存成本,增加利润的关键,而价值流图析技术则是实现这一目标的有效方法。
本课题以某电视机生产企业的PT5生产装配线为研究对象,通过对电视机生产线的现场调查、收集整理了相关数据;绘制了生产线的工艺程序图;分析了现行生产线存在的问题;在此基础上对生产线进行了工位合并与简化,运用Proplanner软件建立了山积表,实现生产线初次平衡;建立了生产线的优化模型,借助于Xpess-mosel运筹学软件运行了优化模型,得到了优化结果,即优化后的生产节拍时间46秒,优化后生产线的平衡率由76.55%提高到84.16%;据此进行了产品的价值流分析,绘出了产品的价值流现状图与未来图,通过比较与分析,产品的订货提前期由原来的21.57天缩短为7.46天,其中生产装配线上的生产周期时间由原来的9.56天缩短为1.72天:生产装配线上的在制品数量由原来的4846件减少到860件;生产装配线上的增值率由原来的0.42%提高到2.33%。
由此看出,将山积表的平衡方法与生产线优化模型的结合,为产品的价值流分析提供了科学依据。
9.学位论文李加忠硬盘装配车间精益设施规划2009
论文以设计高效、合理的硬盘车间布置,高负荷精益的硬盘返工线,以及精益的物流系统为目的。
阐述和介绍了设施布置方法,精益生产的思想和特点,以及精益物流搬运的概念及特点。
然后以精益概念为指导,运用设施系统布置规划方法,通过对产品及其工艺的分析,确定硬盘返工线所需要的面积。
结合厂房和车间的实际条件,并通过对硬盘的产量的分析,计算各单位间的物料量,以及各个生产单位之间的关系,进行了车间布局。
从生产线
10.会议论文马继强.王强.张梅精益生产工作法——三元整合法2007
焊装车间装配线班长马继强在300c系列白车身的生产中,灵活运用精益生产培训中所学到的理论知识,利用SwI标准作业指导书和PPSR“实际问题解决报告”等方法,自己创新“三元整合法”来平衡装配线的生产平衡,在保证产品质量的前提下,最大化增值性工作内容和标准化工作的使用,装配线的生产节拍由投产初期的12-15分钟/辆份提高到目前的2.5-3.5分钟,辆份,生产效率比试装投产初期提高了近80%,为满足增产需求奠定了坚实的基础。
同时,在达到生产线平衡后,还应用PDCA持续改进的方法,不断进行生产加工操作的优化和改进,此方法正在逐步推广应用于其它车间。
本文链接:/Thesis_Y1518440.aspx
下载时间:2010年5月12日。