芳烃转化、催化脱氢
化学工艺学学习总结
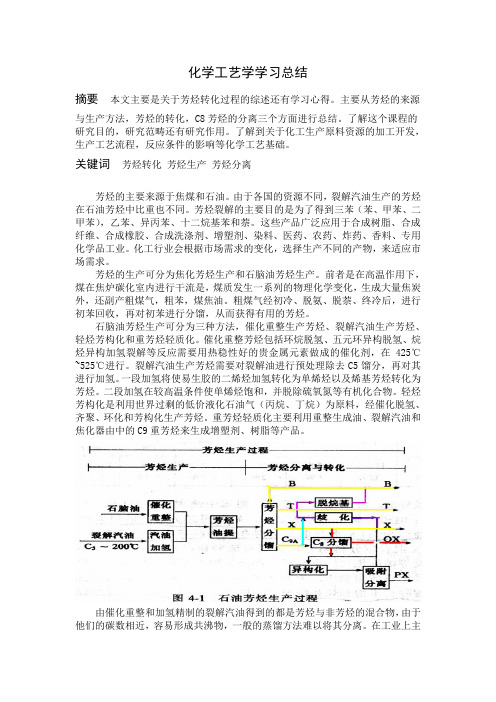
化学工艺学学习总结摘要本文主要是关于芳烃转化过程的综述还有学习心得。
主要从芳烃的来源与生产方法,芳烃的转化,C8芳烃的分离三个方面进行总结。
了解这个课程的研究目的,研究范畴还有研究作用。
了解到关于化工生产原料资源的加工开发,生产工艺流程,反应条件的影响等化学工艺基础。
关键词芳烃转化芳烃生产芳烃分离芳烃的主要来源于焦煤和石油。
由于各国的资源不同,裂解汽油生产的芳烃在石油芳烃中比重也不同。
芳烃裂解的主要目的是为了得到三苯(苯、甲苯、二甲苯),乙苯、异丙苯、十二烷基苯和萘。
这些产品广泛应用于合成树脂、合成纤维、合成橡胶、合成洗涤剂、增塑剂、染料、医药、农药、炸药、香料、专用化学品工业。
化工行业会根据市场需求的变化,选择生产不同的产物,来适应市场需求。
芳烃的生产可分为焦化芳烃生产和石脑油芳烃生产。
前者是在高温作用下,煤在焦炉碳化室内进行干流是,煤质发生一系列的物理化学变化,生成大量焦炭外,还副产粗煤气,粗苯,煤焦油。
粗煤气经初冷、脱氨、脱萘、终冷后,进行初苯回收,再对初苯进行分馏,从而获得有用的芳烃。
石脑油芳烃生产可分为三种方法,催化重整生产芳烃、裂解汽油生产芳烃、轻烃芳构化和重芳烃轻质化。
催化重整芳烃包括环烷脱氢、五元环异构脱氢、烷烃异构加氢裂解等反应需要用热稳性好的贵金属元素做成的催化剂,在425℃~525℃进行。
裂解汽油生产芳烃需要对裂解油进行预处理除去C5馏分,再对其进行加氢。
一段加氢将使易生胶的二烯烃加氢转化为单烯烃以及烯基芳烃转化为芳烃。
二段加氢在较高温条件使单烯烃饱和,并脱除硫氧氮等有机化合物。
轻烃芳构化是利用世界过剩的低价液化石油气(丙烷、丁烷)为原料,经催化脱氢、齐聚、环化和芳构化生产芳烃。
重芳烃轻质化主要利用重整生成油、裂解汽油和焦化器由中的C9重芳烃来生成增塑剂、树脂等产品。
由催化重整和加氢精制的裂解汽油得到的都是芳烃与非芳烃的混合物,由于他们的碳数相近,容易形成共沸物,一般的蒸馏方法难以将其分离。
4芳烃转化过程详解

萃取蒸馏法 从窄馏分中分离纯度高的单一芳
溶剂萃取 对溶剂性能的基本要求
对芳烃的溶解选择性好、溶解度高 与萃取原料密度差大 蒸发潜热与热容小、蒸汽压小 有良好的化学稳定性与热稳定性、腐
蚀性小
溶剂萃取
工业生产方法
Unex法
二甘醇
Sulfolane法 环丁砜 Arosolvan法 N-甲基吡络烷酮
裂解汽油中的C5馏分
异戊二烯 间戊二烯 环戊二烯
合成橡胶和精细化工原料
二烯烃加氢生成烯烃 汽油
加氢生成C5烷烃
烃裂解原料
一段加氢
二烯烃 烯基芳烃
单烯烃 芳烃
工艺条件:Pd/Al2O3 催化剂 (低温液相反应)
指标:二烯烃含量< 2%
二段加氢
单烯烃
饱和烃
脱除S 、O 、 N 等有机化合物
同部位加入由分离塔闪蒸出来的 氢,从而控制反应温度稳定,
副反应较少
重芳烃的产率较低
MHC法
原料:裂解汽油,非芳烃含量可达30% 特点:原料要预先进行两段加氢处理 可采用低纯度氢气
单程转化率、苯的收率、苯的纯度都高
4.2.2 芳烃的歧化与烷基转移
芳烃歧化
两个相同芳烃分子在酸性催化剂作用下, 一个芳烃分子上的侧链烷基转移到另一 个芳烃分子上去的反应
脱烷基产物在高压分离器中分离 原料裂解汽油需预处理
C6-C8馏分进行脱烷基
甲苯热脱烷基制苯 较适宜的反应条件
反应温度700~800℃ 液空速3~6h-1 氢/甲苯(摩尔比)3~5 压力3.98~5.0MPa 接触时间60秒左右
HAD法
原料:甲苯、混合芳烃、裂解汽油 特点:在柱塞流式反应器的六个不
第四章芳烃转化过程

第四章芳烃转化过程4.2芳烃的转化4.2.1概述一、芳烃转化反应的化学过程异构化、歧化与烷基转移、烷基化和脱烷基化等几类反应,都是按离子型反应机理进行,反应历程包括正烃离子的生成及正烃离子的进一步反应。
二、催化剂芳烃转化反应是酸碱型催化反应。
1. 酸性卤化物酸性卤化物与HX构成:A1Br3、A1Cl3、BF3等路易氏酸。
通式HX—MXn。
用于芳烃的烷基化和异构化等反应,较低温度和液相中进行。
2.固体酸1)浸附在适当载体上的质子酸:H2SO4、H3PO3、HF等。
常用的是磷酸/藻土,磷酸/硅胶烷基化反应。
2)浸渍在适当载休上的酸件卤化物:BF3/γ-A12O3催化剂3)混合氧化物催化剂:SiO2-A12O3催化剂4)贵金属-氧化硅-氧化铝:Pt/SiO2-A12O3,具有酸、加氢脱氢功能。
主要用于异构化反应。
5)分子筛:ZSM-5,具有酸功能,还具有热稳定性高和择形性等功能,用于芳烃歧化与烷基转移、异构化和烷基化。
4.2.2芳烃歧化——二甲苯生产一、概述三种异构体的混合物,呈无色透明易挥发有芳香气味的液体,有毒,不溶于水,溶于乙醇和乙醚。
二甲苯性质二甲苯分子式为C6H4(CH3)2,有三种异构体,其各自物理性状分别为:(1)邻二甲苯,熔点-25℃,沸点144℃。
(2)间二甲苯,熔点-47.4C,沸点139.3℃。
(3)对二甲苯,熔点13.2C,沸点138.5℃。
用途:a混合二甲苯主要用作油漆涂料工业的溶剂和航空汽油添加剂。
b对二甲苯可以氧化制得对苯二甲酸,进而可以生产聚酯纤维和聚酯薄膜,c邻二甲苯氧化可制得邻苯二甲酸酐,是制造醇酸树脂和聚酯树脂,以及用作塑料增塑剂的重要中间体,d间二甲苯可氧化成间苯二甲酸,是制造醇酸树脂、饱和及不饱和聚酯塑料的原料。
二、甲苯歧化反应定义:芳烃歧化是指两个相同芳烃分子在酸性催化剂作用下,一个芳烃分子的侧链烷基转移到另一个芳烃分子上去的反应。
芳烃歧化反应的逆反应为烷基转移反应,即两个不同芳烃分子之间发生烷基转移的过程,目的:芳烃联合装置中的芳烃歧化装置就是将分馏装置中的甲苯和C9芳烃歧化,在—定的温度和临氢条件下,在催化剂作用下,转化为苯和C8芳烃,以增产二甲苯。
第8章 芳烃转化过程

8.2 芳烃转化
各种芳烃组分中用途最广、需求量最大的是苯与对二甲苯,其 次是邻二甲苯。
8.2.1 芳烃的脱烷基化
芳烃的脱烷基化:烷基芳烃分子中与苯环直接相连的烷基,在一定的条件下 可以被脱去。 工业上主要应用于甲苯脱甲基制苯、甲基萘脱甲基制萘。
但其共同点是必须经蒸馏除去裂解汽油中C4馏分、部分C9芳烃与C9+馏分,
(2)裂解汽油加氢 裂解汽油加氢是目前普遍采用的精制方法。由于从裂解汽油中除去双烯烃、 单烯烃和氧、氮、硫等有机化合物的工艺条同,—般采用二段加氢精制工 艺。 第一段加氢的目的,将使易生胶的二烯烃加氢转化为单烯烃以及烯基芳烃转 化为芳烃。 这一段加氢在比较缓和的工艺条件下进行,以避免二烯烃聚合。 因此一段加氢多采用它(Pd/Al203)为催化剂,在低温(低于l00℃)液相下进行 选择性加氢。 一段加氢也有少数采用非贵金属镍钻、铂钨等催化剂,此类催化剂,其反 应温度一般要高于100℃,在这样温度下双烯烃难免在催化剂表面聚合,从 而降低催化剂活性,导致催化剂再生频繁。 裂解汽油经一段加氢后,其中二烯烃含量小于2%(以质量计); 第二段加氢目的,主要使单烯烃饱和并脱除硫、氧、氮等有机化合物。 这一段加氢精制,普遍采用非贵金属Co-Mo- Al203系列的催化剂,工艺技 术比较成熟。二段加氢在较高温度气相条件下进行。 二段加氢后,裂解汽油的溴值小于1,含硫质量分数小于2×10-6。
(2)重芳烃轻质化的Dctol工艺
8.1.2 芳烃馏分的分离
由催化重整相加氢精制裂解汽油得到的含芳烃馏分都是由芳烃 与非芳烃组成的混合物。 由于碳数相同的芳烃与非芳烃的沸点非常接近,有时还会形成 共沸物,用一般的蒸馏方法是难以将它们分离的。 为了满足对芳烃纯度的要求,目前工业上实际应用的主要是溶 剂萃取法和萃取蒸馏法。
第三章 芳烃转化过程
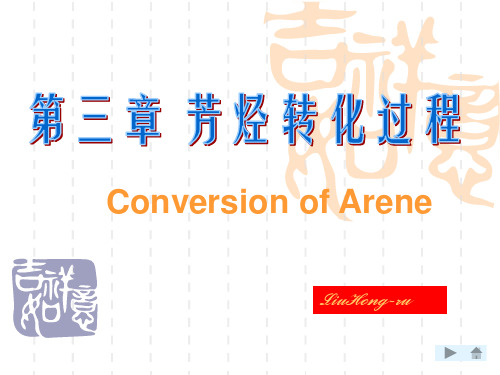
表 3-6 温度对二甲苯异构化反应平衡组成的影响 温度/℃ 371 427 482 二甲苯异构体的平衡组成(摩尔分数) 间二甲苯 0.527 0.521 0.517 对二甲苯 0.237 0.235 0.233 邻二甲苯 0.236 0.244 0.250
至燃料系统
甲苯
反 应 器
分 离 器
一、C8芳烃的的组成与性质
表 3-11 C8 芳烃各异构体的某些性质 性质 组分 邻二甲苯 间二甲苯 对二甲苯 乙苯 沸点/℃ 144.411 139.104 138.351 136.861 熔点/℃ -25.173 -47.872 13.263 -94.971 相对碱度 2 3-100 1 0.1 与 BF3-HF 生成配 合物相对稳定性 2 20 1 -
+
三、工业生产方法
脱烷基制苯主要工艺方法
催 化 工艺方法 原料 剂 组 成 Hydeal (UOP 公司) Pyrotol ( Airproducts 裂解汽油 and Chemi -cals公司) HAD(ARCO /HRI 公司) 甲苯、混合 芳烃 入 MHC 裂解汽油 (日本三菱公司) 出口 <700 口 2.45 98%-99% 98%-99% 677-704 3.9-4.9 96%-100% 96%-100% Al2 O3 Cr2 O3 / 600-650 5.9-6.9 98.5% 98.5% 4-5 芳烃萃取 物 Cr2 O3 / 600-650 Al2 O3 3.4-3.9 0.5 >98% 99.98% 1.5 工艺条件 理论产率 温度 /℃ 压力 /MPa 空速 的收率 /h-1 命/a 苯纯度 剂 寿 催 化
④ 贵金属-氧化硅-氧化铝催化剂(异构化)
⑤ 分子筛催化剂
催化脱氢和氧化脱氢

根据上述机理可推知这类催化剂活性衰退的
原因可能是催化剂表面或近表面这一层在反 应过程中形成的阴离子缺位,在反应条件下不 能被气相中氧再充满,因而使Fe2+不能再被氧 化成Fe3+,导致催化剂活性和选择性下降。
13
2.主要副反应
丁烯氧化脱氢过程,可能发生的副反应,主要有下列几种类 型:
第四章
催化脱氢和氧化脱氢
第一节 烃类催化脱氢反应的化学 第二节 乙苯脱氢合成苯乙烯
第三节 烃类的氧化脱氢
1
第三节 烃类的氧化脱氢
一、氧化脱氢反应简介
如上节课所学,催化脱氢受化学平衡转化率不会太高(转化率太高了 选择性又低了),尤其是低级烷烃和低级烯烃的催化脱氢反应(20-50% ),芳烃还好些(可以达到85%的转化率)。要使平衡向有利于脱氢方 向移动,可以采取移走生产物-----氢的方法。如果在脱氢系统中加入能 够和氢相结合的所谓氢“接受体”,随时去掉反应生成的氢,这样就可以 使平衡向脱氢方向移动,转化率就可以大幅度提高。同时由于这些氢的 “接受体”与氢结合放出大量的热量,又可以大大降低热量的消耗。可 以作为氢接受体的物质很多,如氧、卤素和含硫化合物等。它们能夺取 烃类分子中的氢,使其转变为相应的不饱和烃,而烃被氧化,这种类型 的反应称为氧化脱氢反应。
8
2.铁酸盐尖晶石催化剂
这类催化剂有: ZnFe2O4、MnFe2O4、MgFe2O4、ZnCrFeO4 和 Mg0.1Zn0.9Fe2O4 等铁酸盐,具有尖晶石型结构的氧化物催化剂。 (Mg--镁) 这类催化剂,是60年代后期开发的一类丁烯氧化脱氢催化剂。 据研究,在该类催化剂中,a-Fe2O3的存在是必要的,不然催化剂的 活性就会很快下降。 铁酸盐尖晶石催化剂,对丁烯氧化脱氢具有较高的活性和选择性,含 氧副产物少,三废污染少。正丁烯在这类催化剂上氧化脱氢,转化率可 达到70%左右,而选择性可达到90%或者更高。
芳烃转化过程综述
芳烃转化过程综述摘要本文献系统介绍了芳烃的基本定义及其主要产品苯、甲苯、二甲苯的主要特点以及其在工业上的主要应用,综述了近些年来对芳烃生产、转化、分离技术在科学研究与生产发展的概况及国内外芳烃产品生产技术的发展形势与生产格局,并展望了未来芳烃生产新技术的发展趋势。
关键词芳烃,转化,苯,发展1.概述[1]芳烃是芳香族碳氢化合物的简称,亦称芳香烃,也是含苯结构的碳氢化合物的总称。
这类化合物从其碳氢比来看,具有高度不饱和性,但实际确实比较稳定的。
与脂肪烃和脂环烃不同,其化学行为是:比较容易进行取代反应,不易进行加成反应和氧化反应,这种特性曾作为芳香性的标志。
我们常说的芳烃,一般指分子中含有苯环结构的芳烃,而不含苯环结构的芳烃,称为非苯芳烃。
芳烃中的“三苯”(苯、甲苯、二甲苯,简称BTX)和烯烃中的“三烯”(乙烯、丙烯、丁二烯)是化学工业的基础原料,具有重要地位。
芳烃中以苯、甲苯、二甲苯、乙苯、异丙苯、十二烷基苯和萘最为重要,这些产品广泛应用于合成树脂、合成纤维、合成橡胶、合成洗涤剂、增塑剂、染料、医药、农药、炸药、香料、专业化学品等工业。
对发展国民经济、改善人民生活起着极其重要的作用。
化学工业所需要的芳烃主要是苯、甲苯、二甲苯。
苯可以用来合成苯乙烯、环己烷、苯酚、苯胺及烷基苯等;甲苯不仅是有机合成的优良溶剂,而且可以很撑异氰酸酯、甲芳烃,二甲苯异构体分酚,或通过歧化和脱烷基制备苯;二甲苯和乙苯同属C8别为对二甲苯、邻二甲苯和间二甲苯。
工业上常用术语的“混合二甲苯”实际上是乙苯和三个二甲苯异构体组成的混合物。
对二甲苯主要用于生产对苯二甲酸或对苯二甲酸二甲酯,与乙二醇反应生成的聚酯用于生产纤维、胶片和树脂,是最重要的合成纤维和塑料之一;邻二甲苯主要用途是生产邻苯二甲酸酐,进而生产增塑剂,如邻苯二甲酸二辛酯(DOP)、邻苯二甲酸二丁酯(DBP)等;间二甲苯的主要用途是生产间苯二甲酸及少量的间苯二腈,后者是生产杀菌剂的单体,间苯二甲酸则是生产不饱和聚酯树脂的基础原料;乙苯的主要用途是制取苯乙烯,芳烃组分中,异丙苯用于生产苯酚/丙酮进而生产丁苯橡胶和苯乙烯塑料等。
2013化工工艺学(1)试题参考答案
3、有一种精细化工中间体为3-硝基4-氨基苯甲醚,请以苯为原料,设计出一种合成工艺路线,并对工艺路线和工艺条件进行简要说明。
步骤1:苯与氯气氯化反应,分离得氯苯,氯化条件与分离条件的选择
2)
3)
10、PX项目的主要原料是,复旦大学学生中毒死亡的药物中文名为N-二甲基亚硝胺,其化学结构式为。
对二甲苯,(CH3)2=N-NO
得
分
三、简答题(本大题共3小题,每小题10分,共30分)
1、简要说明CO+H2合成甲醇的工艺条件及其选择原则,并绘制出低压法合成甲醇的工艺流程简图。
CO+H2合成甲醇的工艺条件:包括反应温度,反应压力,空速,反应用催化剂,原料CO与H2的配比,反应原料中CO2的浓度等。(3分)
湘潭大学2013年上学期2010级《化工工艺学》课程考试试卷参考答案
得
分
一、名词解释(本大题共8小题,每小题2分,共16分)
1.Aromax(芳构化)工艺
经过溶剂萃取重整汽油的芳烃所剩的抽余油,主要含C6-C8烷烃和环烷烃,在Pt/BaK-L分子筛催化剂的作用下,使烷烃和环烷烃转化为芳烃的工艺。
2.一碳化学
工艺条件的选择原则:主要考虑反应速度(快),反应选择性(高),催化剂的性能(在允许使用的温度和压力范围内)及催化剂的生产能力(大),反应条件尽可能不苛刻(易于操作和控制)。
流程图主要考虑原料气与循环气的压缩,加氢反应反应气的分段进料,反应出口气的部分放空(维持惰性气体浓度的平衡),反应产物的分离。流程由压缩机,合成反应器,分离器,闪蒸罐,脱轻组份塔和精馏塔六部分组成。(3分)
芳烃转化催化剂
芳烃转化催化剂一、芳烃的概念和应用芳烃是一类分子中含有苯环结构的化合物,具有广泛的应用价值。
它们可以作为化学品、材料和能源等方面的原料,例如:制药、染料、塑料、合成橡胶、润滑油和燃料等。
二、芳烃转化反应1. 芳香族烴的催化裂解芳香族烴在高温下经过催化裂解反应,产生轻质烷基化合物和苯等芳香族烴,这种反应被称为催化裂解。
这种转化反应是工业上最重要的方法之一。
2. 芳香族烴的氢气加氢在加氢过程中,氢气与芳香族烴发生加成反应,生成饱和脂肪族环状碳氢化合物。
这种转化反应可以使得分子量增加,同时还可以改善产品的抗爆性能。
3. 芳香族烴的脱氢脱氢是指在高温下将芳香族烴中部分或全部氢原子去除形成不饱和双键。
这种反应可以用于制备芳烃衍生物。
三、芳烃转化催化剂1. 催化裂解催化剂常见的催化裂解催化剂有氧化铝、硅酸铝、硅酸钙等,其中以氧化铝为主。
这种催化剂具有高比表面积和强的酸性,能够加速反应速率,同时也可以防止产物之间的重聚。
2. 氢气加氢催化剂常见的氢气加氢催化剂有镍、铜、钯等金属及其合金。
这些金属具有良好的选择性和活性,能够促进反应的进行。
3. 脱氢催化剂常见的脱氢催化剂有铬、钼等过渡金属及其氧化物。
这些催化剂具有良好的稳定性和高效率,能够使得反应速率提高数倍以上。
四、芳烃转化催化机理1. 催化裂解机理在高温下,芳香族烴分子中苯环上部分键断裂形成自由基,然后与其他芳香族烴分子或自身重组形成轻质烷基化合物和苯等芳香族烴。
催化剂作为催化反应的中介,能够加速反应速率,同时也可以防止产物之间的重聚。
2. 氢气加氢机理在氢气加氢过程中,芳香族烴分子中部分或全部的双键被还原成单键,形成饱和脂肪族环状碳氢化合物。
这种反应是一个典型的加成反应,金属催化剂能够促进反应的进行。
3. 脱氢机理在高温下,过渡金属催化剂能够将芳香族烴分子中部分或全部的氢原子去除形成不饱和双键。
这种反应是一个典型的脱除反应,通过控制反应条件和催化剂选择可以实现不同类型芳烃转换。
C+9_重芳烃催化加氢脱烷基技术研究进展
化工进展Chemical Industry and Engineering Progress2024 年第 43 卷第 3 期C +9重芳烃催化加氢脱烷基技术研究进展张鹏飞,严张艳,任亮,张奎,梁家林,赵广乐,张璠玢,胡志海(中石化石油化工科学研究院有限公司,北京 100083)摘要:随着我国芳烃联合装置、乙烯裂解装置的扩能或新建,国内C +9重芳烃产量也大幅增加;利用催化加氢脱烷基技术将C +9重芳烃转化为BTX 等轻质芳烃,对炼化企业具有良好的经济效益。
本文以C +9重芳烃生产BTX 为出发点,阐述了催化加氢脱烷基反应体系中的碳正离子机理和自由基机理,概述了国内外催化加氢脱烷基反应工艺和催化剂的研究进展,并分析了各工艺、催化剂的优缺点,最后对反应机理、工艺及催化剂的发展方向进行了展望。
增产BTX 的同时联产三甲苯、四甲苯等高附加值单体芳烃是未来催化加氢脱烷基工艺的发展方向。
新型催化剂的研发方向则应结合具体的生产目标和反应机理,定向制备出高活性、高选择性、高稳定性的催化加氢脱烷基催化剂。
关键词:C +9重芳烃;催化加氢脱烷基;反应机理;工艺;催化剂中图分类号:TQ241.1;TE624.4+5 文献标志码:A 文章编号:1000-6613(2024)03-1266-09Research progress in the catalytic hydrodealkylation of C +9 heavyaromaticsZHANG Pengfei ,YAN Zhangyan ,REN Liang ,ZHAGN Kui ,LIANG Jialin ,ZHAO Guangle ,ZHANG Fanbin ,HU Zhihai(Sinopec Research Institute of Petroleum Processing Co., Ltd., Beijing 100083, China)Abstract: The capacity expansion or new construction of aromatic complex and ethylene cracking plantin China led to a drastic increase in the yield of C +9 heavy aromatics. The conversion of C +9 heavy aromatics to BTX by catalytic hydrodealkylation technology would be conducive to improving economic benefits for refinery. Based on the production of BTX from C +9 heavy aromatics, firstly, the mechanism of carbenium-ion and free radical in the reaction system of catalytic hydrodealkylation was emphasized. Secondly, the progress of the research on the hydrodealkylation process and catalysts in the domestic and foreign was summarized. Thirdly, the advantages and disadvantages of those process and catalysts was analyzed. Finally, the development direction of reaction mechanism, process and catalyst were forecasted. The future development direction of catalytic hydrodealkylation was to increase the production of BTX and simultaneously produce high value-added monomers such as tritoluene and tetratoluene. The research and development of novel catalysts should be combined with specific production objectives and reaction mechanisms, and the catalytic hydrodealkylation catalysts with high reaction activity, high selectivity and high stability should be prepared directionally.Keywords: C +9 aromatics; catalytic hydrodealkylation; reaction mechanism; process; catalyst综述与专论DOI :10.16085/j.issn.1000-6613.2023-0410收稿日期:2023-03-17;修改稿日期:2023-10-23。
- 1、下载文档前请自行甄别文档内容的完整性,平台不提供额外的编辑、内容补充、找答案等附加服务。
- 2、"仅部分预览"的文档,不可在线预览部分如存在完整性等问题,可反馈申请退款(可完整预览的文档不适用该条件!)。
- 3、如文档侵犯您的权益,请联系客服反馈,我们会尽快为您处理(人工客服工作时间:9:00-18:30)。
二、工艺条件
1.反应温度 由反应原理可知,苯烷基化是放热反应。 (1)热力学分析,在较低的温度下有较好的平衡收率,随着温度的升 高,乙苯的收率反而下降。同时,在非均相烷基化过程中,温度过高,不利 于乙烯的吸收,催化配合物容易树脂化而遭破坏,若温度超过120℃时,配 合物明显树脂化而失去催化作用; (2)化学动力学方面,反应温度低,反应速度慢,对反应进行不利;
1.第一种方案 首先把粗乙苯中的苯、乙苯及二乙苯(ABC)从第一塔的 塔顶蒸出,塔顶馏分进入第二塔、第三塔,按沸点的高低依次 蒸出苯(A)、乙苯(B),第三塔塔釜得到二乙苯(C)。第 一塔釜液中含有少量二乙苯,送入第四塔,用减压精馏将二乙 苯从塔顶蒸出。方案示意图如图6-4。 2. 第二种方案 按挥发度高低,逐一分出各组分,即顺序分离方案。在第 一塔中把粗乙苯中的苯从塔顶蒸出,其余组分进入第二塔;在 第二塔中,将乙苯自塔顶蒸出,其余组分进入第三塔;在第三 塔中,将二乙苯自塔顶蒸出,釜液送至蒸发器脱去焦油得到多 乙苯。如图6-5。
二是加入一定量的氯乙烷,使它与苯反应而产生:
C2H5Cl + C6H6 → C6H5C2H5 + HCl
3.反应机理 采用三氯化铝为催化剂时,必须有助催化剂存在。真正对 烷基化反应起催化作用的是由苯、乙烯、三氯化铝和氯化 氢组成的三元配合物,俗称“红油”。它是红棕色的油状 液体,密度1.05 kg/L,且不溶于烃。 所有反应都处于动态平衡,即乙基不断地由一种配合物转 变为另一种配合物。 影响平衡的因素较多,如原料的配比、三氯化铝的纯度与 用量、氯化氢的用量等。
④反应易达平衡,受反混影响不大
⑤乙烯溶解及反应具有热量放出,约为3400 kJ/h
鼓泡式反应器:见图6-3
1-催化剂配臵槽;2-烷基化反应器;3,5,17,18,19-冷凝器; 4-二乙苯吸收塔;6-沉降器;7,11-混合器;8,12-泵;9-水洗塔; 10,13-分离器;14-蒸苯塔;16-二乙苯精馏塔;20,21,22-加热器
在实际生产中,配制催化剂时,必须注意催化剂AlCl3用量 和助催化剂氯化氢的来源。 (1)AlCl3用量对烷基化反应的影响见表
(2)生产上助催化剂氯化氢的来源一般采用两种方法获得: 一是加入一定量水或靠原料苯中所带的微量水分使 AlCl3水解而放出: AlCl3 + 3H2O → 3HCl + Al(OH)3
四、粗乙苯精制方案 烷基化液经沉降、水洗、中和处理后,通称为粗乙苯(其中含苯50%、 乙苯35%、二乙苯12%、多乙苯3%)。 由于这些组分沸点相差都比较大,采用普通精馏方法即可将其分开。根 据各组分沸点不同,可将粗乙苯分成如表所示的A、B、C、D四个部分。 苯及烷基苯在常压下的沸点
A 组分 苯 沸点/K 353.24 乙苯 409.35 间二乙苯 邻二乙苯 对二乙苯 454.40 456.45 456.75 B C 1,3,5 -三乙苯 488.15 D 1,2,4 -三乙苯 490.15
2.气相烷基化(Mobll/Badger)生产技术 尽管近年来传统的液相烷基化法生产乙苯的技术有很大改进,比如 在减轻腐蚀、减少污水排放量、实行最优化操作以及降低原材料和公用 工程消耗上都取得明显经济效益,但是AlCl3的腐蚀和排放问题只能是减 轻而不可能根除。
20世纪70年代Mobll公司开发的ZSM系列新型沸石催化剂,在石油炼制、 石油化工和C1化学发展中得到广泛应用。由于SZM-5的强酸性、良好的热 稳定性和抗结炭能力,Mobll公司和Badger工程公司联合开发了用ZSM-5为 催化剂在气相使乙烯和苯进行烷基化的新工艺,无疑在乙苯生产技术发展 中是一重大变革。Mobll公司使用ZSM-5正是在催化剂高活性、高选择性和 比较好的抗结炭能力相结合上获得了技术突破。许多公司争相采用这一新 工艺建厂,到1985年世界采用Mobll/Badger气相烷基化工艺生产乙苯的总 生产能力已达300万t/a以上。到1995年底,取得Mobll/Badger专利许可, 共建成35套乙苯生产装臵,总生产能力达1000万t/a。由于该工艺在气相 反应,故既可采用聚合级乙烯作原料,亦能用炼厂催化裂化(FCC- Fluld Catalytlc Cracklng 流化床催化裂化)尾气分离得到的稀乙烯作原料。
第一节 苯烷基化制乙苯生产技术
一、反应原理(尽管乙苯生产工艺各异,但其原理基本一致) 1.主反应——放热反应。
副反应——苯的烷基化过程,同时发生各种芳烃转化反应, 所以产物是乙苯、二乙苯和多乙苯等各种异构体的复杂混 合物;烯烃发生聚合反应生成高沸点的焦油和焦炭。 2.催化剂——催化剂是AlCl3,活性高,可在373K以下反应, 且具有使多烷基苯与苯发生烷基转移的催化作用,在氯乙 烷存在下使烷基化反应更有效进行,所以又称氯乙烷为活 化剂。也可加入少量水使生成少量HCl作助催化剂。 使用AlCl3催化剂的主要缺点是对设备的腐蚀性很大,但由 于AlCl3价廉易得,催化活性高,所以工业上仍广泛采用。
芳烃来源构成
分 布 美国 西欧 石 油
日本
催化重整油 79.6% 49.4% 37.8%
裂解汽油 19.1% 44.8% 52.2%
煤焦化 4.0% 5.9%
10.0%
芳烃含量与组成
组成 芳烃含量 苯 甲苯 催化重整油 50%~72% 6%~8% 20%~25% 裂解汽油 54%~73% 19.6%~36% 10%~15.0% 焦化芳烃 >85% 65% 15%
3.两种方案各有优缺点。 ①第二方案按沸点高低逐步分离,也正好满足了按组分 从多到少的分离顺序,因此塔负荷相对较小。相应塔的直径 较小,动力消耗也较少。但是其中较重要组分需经三个塔的 高温加热,停留时间较长,容易产生树脂状焦ቤተ መጻሕፍቲ ባይዱ物,造成损 失。为了克服这一缺点,第三塔往往采用减压精馏,但如果 较重组分的侧链中含有不饱和键时,则不宜采用此分离方案。 ②为了避免较重组分在塔釜内高温加热和停留时间过长, 以减少焦化损失,常采用第一方案进行分离。但此方案第一 塔塔顶负荷较大,因为粗乙苯中90%以上组分从塔顶蒸出,所 以能量消耗要高一些。 目前国外两种方案均有采用,我国多采用第二种分离方案。
3.乙苯工业生产方法 世界上90%以上的乙苯是由苯和乙烯烷基化生产制得,其 余是由炼油过程生产的C8芳烃分离得到。苯和乙烯烷基化是在 酸性催化剂存在下进行,其生产工艺多种多样。 (1)以所用催化剂不同可分为: 三氯化铝(AlCl3)法、BF3-Al2O3法和固体酸法; (2)若以反应状态不同可分为: 液相法和气相法两种。(液相三氯化铝法又可分为传统 的两相烷基化工艺和单相高温烷基化工艺,前者的典型代表 是道化学公司法、老孟山都法、 UCC 法、 CdF 法;后者的典型 代表是新孟山都法。气相分子筛固体催化剂烷基化法的典型 代表是Mobil/Badger工艺,Lummus/Unocal/UOP工艺。) (3)催化蒸馏技术(CDT-catalytic distillation technology)是近来新发展的生产乙苯新工艺。
用AlCl3作催化剂,在95℃时,乙苯的生成量随乙烯/苯摩尔比的增加而
增加,多乙苯的生成量也相应随之提高。当原料配比超过0.6时,乙苯生成 量的增加不显著,而多乙苯生成量却显著加大。
所以乙烯对苯的摩尔比以 0.5 ~0.6 为宜(当有多乙苯循环使用时,这
个比例数应当是原料混合物中烷基和苯核的比值)。
(3)适宜的反应温度随所用催化剂不同而不同,如传统的用AlCl3作催
化剂,乙烯对于苯液相烷基化温度一般控制在90~100℃。 (4)原料烃类的转化率随温度的降低和气体在反应区停留时间的缩短
而降低。在一定的反应容积中,气体通入量增加,则其停留时间就相对缩短。
因此,气体通入量应严格控制在使原料在反应区有较适宜的停留时间,有利 于提高反应效果。
乙苯侧链容易氧化,其氧化产物随氧化剂的强弱及反应 条件的不同而不同。例如,用强氧化剂(高锰酸钾等)氧化 或在催化剂作用下用空气或氧气进行氧化,生产苯甲酸;若 用缓和的氧化剂或在缓和的反应条件下进行氧化,则生成苯 乙酮。 乙苯的侧链在一定条件下,可从相邻的两个碳原子上脱 去1mol氢而形成C=C双键,生成苯乙烯。 2.主要用途 ( 1 )主要用于脱氢制造苯乙烯(是三大合成材料的重要单 体); ( 2 )其次是用作溶剂、稀释剂以及用于生产二乙基苯、苯 乙酮、乙基蒽醌等; (3)还是医药工业的重要原料。
随着烯烃和苯比 例的增加,一烷 基苯收率开始是 增加,到一定程 度多烷基苯收率 增加。
3.原料纯度——是指原料乙烯和原料苯的纯度
用AlCl3催化剂进行液相烷
基化反应时, (1)原料乙烯可以采用不同浓度,但其中所含的硫化氢、乙炔、一氧化 碳及含氧化物(如乙醚、乙醛)等必须清除。(因为它们能破坏催化剂络 合物或使催化剂钝化,引起催化剂中毒或失活);另外,乙烯中所含丙烯、 丁烯等高级烯烃也应除去。(因为它们比乙烯更易进行烷基化反应,使烷 基化产物复杂化,造成分离困难,且增加原料的消耗量)。 (2)原料苯中的硫化物同样是烷基化反应催化剂的毒物,因此要求苯中 硫的总质量含量应小于0.1%;苯中若含有甲苯应严格控制其含量,因为在 三氯化铝作用下容易生成甲乙苯,给乙苯的分离带来了困难,且增加原料 乙烯的消耗。苯中若含有过量水,可将三氯化铝水解产生的氯化氢,对设 备有腐蚀作用;产生的氢氧化铝沉淀会造成管道和设备堵塞。如果起助催 化作用的氯化氢是由苯中所带水分使AlCl3进行适量水解产生,则苯中含水 量一定要精确计算,不可过量太多,一般含水量应小于500~700mg/kg。
乙烯转化率与温度及气体通入量的关系 温度/K 333 353 353 373 373 气体通入量 /m3 12 12 36 12 36 每摩尔苯吸收乙烯 的量* 0.44 0.47 0.54 0.70 0.80 排出气体乙烯含 量/(%) 32~62 10~14 31~54 6~8 7~8
2.原料配比——乙烯对苯的摩尔比 由于在反应体系中所有生成催化剂配合物的反应都处于动态平衡状态, 配合物周围介质中乙烯浓度越大,三氯化铝配合物中所含烷基越多,生成 的烷基苯也越多。因此,随着所吸收乙烯/苯的比率的增加,反应将向生成 多烷基苯的方向进行。所以,乙烯/苯的比例对烷基化产品的组成有很大影 响。