快走丝线切割技术
快走丝线切割机床使用小窍门
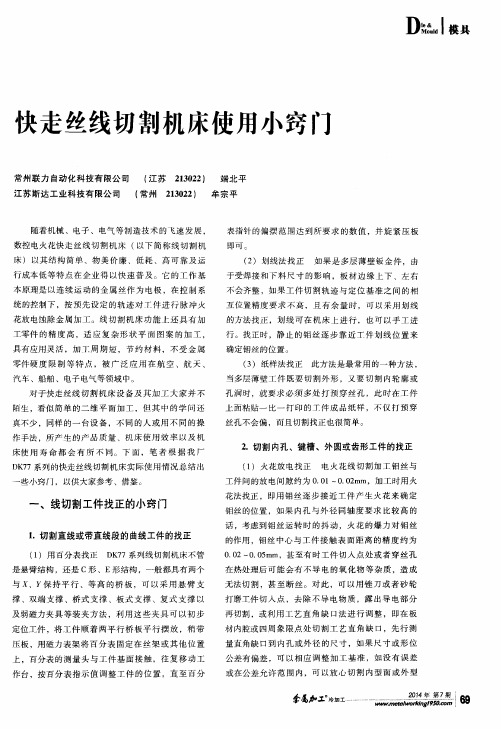
或在 公差 允 许 范 围 内 ,可 以放 心 切 割 内型 面 或 外 型
参磊
冷 加
的
一
2 .切割 内子 L 、键槽、外圆或齿形工件的找正
( 1 ) 火花 放 电找 正 电火 花 线 切 割加 工钼 丝 与 工 件 问的 放 电间 隙约 为 0 . 0 1~0 . 0 2 a r m,加 工 时用 火
些 小窍 门 ,以供 大家参 考 、借鉴 。
一
、
线切割工件找正的小窍 门
花 法找 正 ,即 用 钼丝 逐 步 接 近 工 件 产 生 火 花 来 确 定 钼 丝 的位 置 ,如果 内孔 与外 径 同轴 度 要 求 比较 高 的
话 ,考 虑到 钼 丝 运 转 时 的 抖 动 ,火 花 的爆 力 对 钼 丝
1 .切割直线或带直线段 的曲线 工件 的找正
( 1 )用 百分 表找 正 D K 7 7系列线 切 割机 床不 管
再 切割 ,或 利 用 工 艺 直 角 缺 口法 进 行 调 整 ,即在 板
及 弱 磁力 夹 具 等装 夹 方 法 ,利 用 这 些 夹 具 可 以 初 步 定位 工件 ,将 工 件 顺 着 两 平 行 桥 板 平 行 摆 放 ,稍 带
材 内腔 或 四周 象 限点 处 切 割 工 艺 直 角 缺 口 ,先 行 测
撑 、双端 支 撑 、桥式 支 撑 、板 式 支 撑 、复 式 支 撑 以
在 热处 理后 可 能会 有 不 导 电 的氧 化 物 等 杂 质 ,造 成 无 法切 割 ,甚 至 断 丝 。对 此 ,可 以用 锉 刀 或 者 砂 轮 打 磨工 件切 入 点 ,去 除 不 导 电物 质 ,露 出导 电部 分
i e & M
I 模 具
快走丝、慢走丝和中走丝
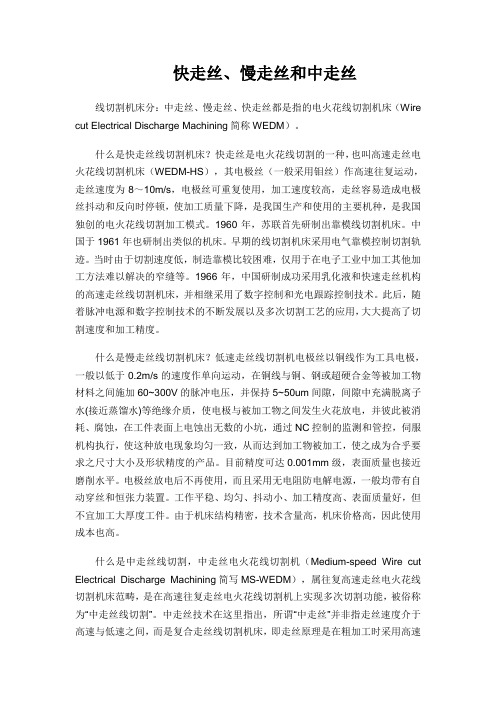
快走丝、慢走丝和中走丝线切割机床分:中走丝、慢走丝、快走丝都是指的电火花线切割机床(Wire cut Electrical Discharge Machining简称WEDM)。
什么是快走丝线切割机床?快走丝是电火花线切割的一种,也叫高速走丝电火花线切割机床(WEDM-HS),其电极丝(一般采用钼丝)作高速往复运动,走丝速度为8~10m/s,电极丝可重复使用,加工速度较高,走丝容易造成电极丝抖动和反向时停顿,使加工质量下降,是我国生产和使用的主要机种,是我国独创的电火花线切割加工模式。
1960年,苏联首先研制出靠模线切割机床。
中国于1961年也研制出类似的机床。
早期的线切割机床采用电气靠模控制切割轨迹。
当时由于切割速度低,制造靠模比较困难,仅用于在电子工业中加工其他加工方法难以解决的窄缝等。
1966年,中国研制成功采用乳化液和快速走丝机构的高速走丝线切割机床,并相继采用了数字控制和光电跟踪控制技术。
此后,随着脉冲电源和数字控制技术的不断发展以及多次切割工艺的应用,大大提高了切割速度和加工精度。
什么是慢走丝线切割机床?低速走丝线切割机电极丝以铜线作为工具电极,一般以低于0.2m/s的速度作单向运动,在铜线与铜、钢或超硬合金等被加工物材料之间施加60~300V的脉冲电压,并保持5~50um间隙,间隙中充满脱离子水(接近蒸馏水)等绝缘介质,使电极与被加工物之间发生火花放电,并彼此被消耗、腐蚀,在工件表面上电蚀出无数的小坑,通过NC控制的监测和管控,伺服机构执行,使这种放电现象均匀一致,从而达到加工物被加工,使之成为合乎要求之尺寸大小及形状精度的产品。
目前精度可达0.001mm级,表面质量也接近磨削水平。
电极丝放电后不再使用,而且采用无电阻防电解电源,一般均带有自动穿丝和恒张力装置。
工作平稳、均匀、抖动小、加工精度高、表面质量好,但不宜加工大厚度工件。
由于机床结构精密,技术含量高,机床价格高,因此使用成本也高。
数控快走丝线切割的编程
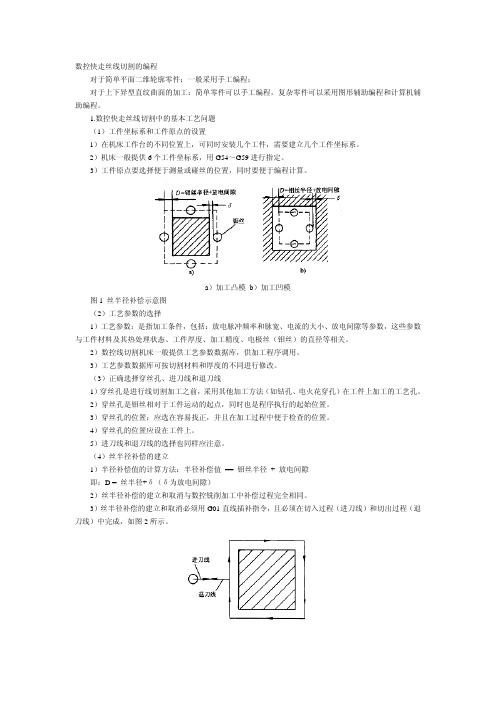
数控快走丝线切割的编程对于简单平面二维轮廓零件:一般采用手工编程;对于上下异型直纹曲面的加工:简单零件可以手工编程,复杂零件可以采用图形辅助编程和计算机辅助编程。
1.数控快走丝线切割中的基本工艺问题(1)工件坐标系和工件原点的设置1)在机床工作台的不同位置上,可同时安装几个工件,需要建立几个工件坐标系。
2)机床一般提供6个工件坐标系,用G54~G59进行指定。
3)工件原点要选择便于测量或碰丝的位置,同时要便于编程计算。
a)加工凸模b)加工凹模图1 丝半径补偿示意图(2)工艺参数的选择1)工艺参数:是指加工条件,包括:放电脉冲频率和脉宽、电流的大小、放电间隙等参数,这些参数与工件材料及其热处理状态、工件厚度、加工精度、电极丝(钼丝)的直径等相关。
2)数控线切割机床一般提供工艺参数数据库,供加工程序调用。
3)工艺参数数据库可按切割材料和厚度的不同进行修改。
(3)正确选择穿丝孔、进刀线和退刀线1)穿丝孔是进行线切割加工之前,采用其他加工方法(如钻孔、电火花穿孔)在工件上加工的工艺孔。
2)穿丝孔是钼丝相对于工件运动的起点,同时也是程序执行的起始位置。
3)穿丝孔的位置:应选在容易找正,并且在加工过程中便于检查的位置。
4)穿丝孔的位置应设在工件上。
5)进刀线和退刀线的选择也同样应注意。
(4)丝半径补偿的建立1)半径补偿值的计算方法:半径补偿值 == 钼丝半径 + 放电间隙即:D = 丝半径+δ(δ为放电间隙)2)丝半径补偿的建立和取消与数控铣削加工中补偿过程完全相同。
3)丝半径补偿的建立和取消必须用G01直线插补指令,且必须在切入过程(进刀线)和切出过程(退刀线)中完成,如图2所示。
图2 丝半径补偿(G41)的建立和取消(5)锥度加工条件1)首先必须输入下列参数:①上导轮中心到工作台面的距离S。
②工作台面到下导轮中心的距离W。
③工件厚度H。
如图3所示。
图3 锥度加工条件参数2)锥度加工的建立和退出图4 锥度切割加工范围和加工误差分析例题①锥度加工的建立和退出过程如图4所示:建立锥度加工(G51或G52),退出锥度加工(G50)②程序段必须是G01直线插补程序段,分别在进刀线和退刀线中完成。
快走丝线切割加工工艺

提高快走丝线切割加工工艺指标快走丝线切割机床是目前我国电加工行业的主导产品之一,是模具加工的重要设备,也是电加工机床出口创汇的主要品种。
快走丝线切割机床与慢走丝线切割机床相比由于其在性能价格比上的优势,以及它固有的技术特点,近年来被越来越多的国外用户所接受,并已引起外国制造商的注意。
这种情况对我们发展快走丝线切割机床既提供了机遇,也提出了挑战。
如果我们对快走丝线切割加工工艺的研究与开发不给以足够的重视,就有可能使我们在这一领域中失去优势,而处于被动的状态。
我国的快走丝线切割机床发展至今,其加工工艺指标没有重大的突破。
而面对模具工业整体要求的提高以及加工方法的竞争,其加工工艺指标必须要有较大的提高,方能适应市场竞争的要求。
早在“八五”期间,电加工行业就提出作为提供用户的商品快走丝线切割机床应具备下列指标:1.表面粗糙度Ra为1.25~0.63μm时,切割速度为20mm2/min.2.表面粗糙度Ra为2.5~1.25μm时,切割速度为40mm2/min.3.按国标GB7926-87中有关条目的加工与检验方法,切割八角工件时,其纵剖面的尺寸差为0.006mm,横剖面的尺寸差为0.009mm。
加工四个孔的位置误差为0.008mm,四个孔的尺寸误差为0.012mm。
4.应有高效切割机床提供用户,最高速度达到250mm2/min。
以上的指标目前对于成为商品化的快走丝线切割机床(或按目前的加工工艺方法)来讲,几乎都难以达到和实现。
二.提高快走丝加工工艺指标的重要手段是多次切割多次切割犹如常规金加工中通过粗加工、半精加工和精加工等多道工序去除加工余量,其加工工艺效果是不言而喻的。
所以不论高精度机床还是普通机床都采用多次切割工艺,包括慢走丝线切割机床,也是通过多次切割来达到其高精度、高光洁度的效果。
但对于我国的快走丝线切割机床能否采用多次切割技术,本人认为,我们要分析快走丝线切割机床上实现多次切割的关键是在具有高重复定位精度的机床上,使电极丝具有确定的动态平衡位置以及较窄的的动态变化范围。
有关线切割
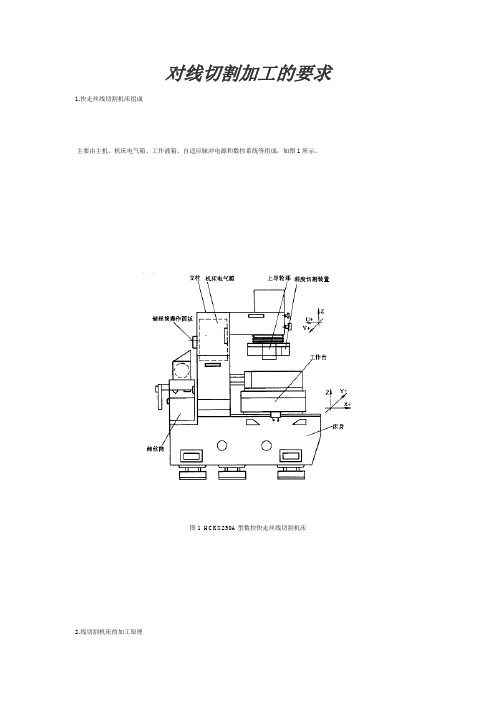
对线切割加工的要求1.快走丝线切割机床组成主要由主机、机床电气箱、工作液箱、自适应脉冲电源和数控系统等组成,如图1所示。
图1 HCKX250A型数控快走丝线切割机床2.线切割机床的加工原理(1)线切割——数控电火花线切割加工的简称。
(2)工作原理:利用移动的金属丝作工具电极,并在金属丝和工件间通以脉冲电流,利用脉冲放电的腐蚀作用对工件进行切割加工的。
(3)由于它利用的是丝电极,因此,只能作轮廓切割加工。
(4)工作原理如图2所示。
图2 线切割机床的加工原理1--数控装置2--储丝简3--导轮4--电极丝5--工件6--喷嘴7--绝缘板8--脉冲发生器9--液压泵10--水箱11--控制步进电动机(5)当工件与线电极间的间隙足以被脉冲电压击穿时,两者之间即产生火花放电而切割工件。
(6)通过数控装置l发出的指令,控制步进电动机11,驱动X、Y两托板移动,可加工出任意曲线轮廓的工件。
3.线切割机床的分类(1)根据控制方式的不同,电火花线切割机床分为:电气靠模线切割机床;光电跟踪线切割机床;数字控制线切割机床。
(2)根据电极丝走丝方式的不同,数控线切割机床分为:快走丝线切割机床;慢走丝线切割机床。
1)快走丝线切割机床①线电极运行速度较快(300—700m/min)。
②可双向往复运行,即丝电极可重复使用,直到丝电极损耗到一定程度或断丝为止。
③常用线电极为:钼丝(Φ0.1~Φ0.2mm)。
④工作液通常为:乳化液或皂化液。
⑤由于电极丝的损耗和电极丝运动过程中换向的影响,其加工精度要比慢走丝差,表面粗糙度要高;⑥尺寸精度:0.015~0.02mm;⑦表面粗糙度Rɑ:1.25~2.5μm。
⑧一般尺寸精度最高可达到:0.01mm,表面粗糙度Rɑ为:0.63~1.25μm。
2)慢走丝线切割机床①线电极运行速度较低(0.5~15m/min)。
②线电极只能单向运动,不能重复使用,这样可避免电极损耗对加工精度的影响。
③丝电极有:紫铜、黄铜、钨、钼和各种合金,直径一般为0.1~0.35mm。
快走丝线切割原理

快走丝线切割原理
丝线切割原理是通过高速旋转的切割盘将丝线切割成所需的长度或形状。
切割盘通常由硬质材料制成,如金属或陶瓷,并具有细小的切割刃。
当切割盘旋转时,丝线被置于切割刃的路径上。
在切割过程中,切割盘的切割刃快速穿过丝线,并施加足够的力量使丝线断裂。
这种切割方式可用于各种类型和强度的丝线,如塑料丝、金属丝、玻璃丝等。
丝线切割的准确性和效率取决于切割盘的旋转速度、切割刃的数量和尺寸、切割盘与丝线的接触力等因素。
根据不同的应用需求,切割盘可以根据需要进行调整和更换。
丝线切割机通常由电机驱动,控制面板上的按钮或旋钮可用于调整切割盘的速度和切割参数。
一些高级型号的丝线切割机还配备了传感器和自动控制系统,可以实现精确的切割操作并确保切割质量。
总之,丝线切割原理通过旋转的切割盘切割丝线,以实现所需的切割长度或形状。
这种切割方式具有准确性高、环保、高效等特点,并可适用于各种丝线材料。
线切割快走丝个人经验

操作方法:旋转“间隔微调”旋钮,调节脉冲间隔宽度的大小,顺时针旋转间隔宽度变大,逆时针旋转间隔宽度变小。
选择原则说明:加工工件高度较高时,适当加大脉冲间隔,以利排屑,减少切割处的电蚀污物的生成,使加工较稳定,防止断丝。因为在脉宽档位确定的情况下,间隔在“间隔微调”旋钮确定下,间隔宽度是一定的,所以要调节间隔大小就是旋转“间隔微调”旋钮。在有稳定高频电流指示的情况下,旋转“间隔微调”旋钮时,电流变小表示间隔变大,电流变大表示间隔变小。
3、 在线切割加工时,各个状态的切换尽量在丝筒换向或关断高频时进行,且不要单次大幅度调整状态,以免断丝。
4、 新换钼丝刚开始切割时,加工电流选择正常切割电流的三分之一至三分之二,经十来分钟切割后,调至正常值,以延长钼丝使用时间。
(二)、短路电流测试
置“电压调整”旋钮2档,“脉冲幅度”开关接通1+2+2,“脉宽选择”旋钮3档,“间隔微调”旋钮中间位置,用较粗导线短路高频输出端(上线臂前端靠上导轮的一块钨钢是高频输出负极,工作台上沿是高频输出正极),开高频电源,开丝筒电机,开控制器高频控制开关,此时高频电源电流表指示约为2.8A
理论上就是这样的。
在理论基础的指导下,还应结合实际情况来调节,力求稳定加工!!!不管你怎么调,只要调稳定了,就一定不会断丝!而稳定加工的一个很重要很重要的依据就是电流表的指针一定要定在一个位置!!!!!!就是摆动也是很微小的摆动!!!!!!如果电流表的指针忽上忽下的来回摆动,幅度要是很大的话,突然电流表指针指向4A以上,就会有马上断丝的危险!这代表当前的参数设置的很不合理,应重新调节。调节时,应从小的加工电流比如1A开始,慢慢调高,并要注意加工当中切勿调节!!!这样会引起突然断丝。可以在换向时或暂停加工时调节,调好再割割看,如果稳定了,那就OK了。
线切割快走丝个人经验总结
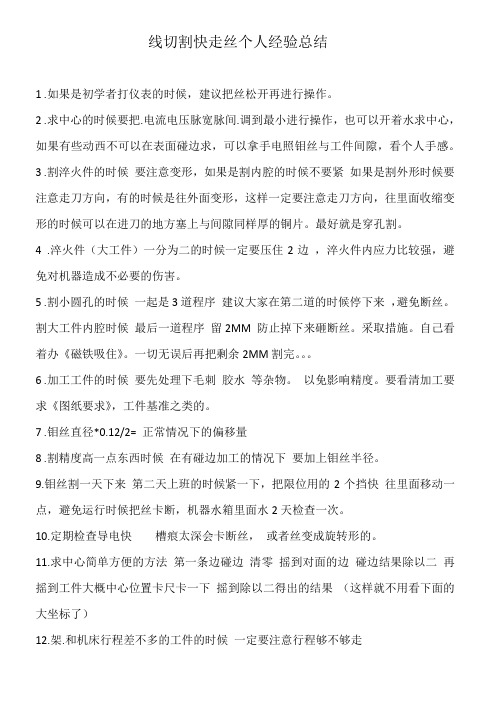
线切割快走丝个人经验总结1 .如果是初学者打仪表的时候,建议把丝松开再进行操作。
2 .求中心的时候要把.电流电压脉宽脉间.调到最小进行操作,也可以开着水求中心,如果有些动西不可以在表面碰边求,可以拿手电照钼丝与工件间隙,看个人手感。
3 .割淬火件的时候要注意变形,如果是割内腔的时候不要紧如果是割外形时候要注意走刀方向,有的时候是往外面变形,这样一定要注意走刀方向,往里面收缩变形的时候可以在进刀的地方塞上与间隙同样厚的铜片。
最好就是穿孔割。
4 .淬火件(大工件)一分为二的时候一定要压住2边,淬火件内应力比较强,避免对机器造成不必要的伤害。
5 .割小圆孔的时候一起是3道程序建议大家在第二道的时候停下来,避免断丝。
割大工件内腔时候最后一道程序留2MM 防止掉下来砸断丝。
采取措施。
自己看着办《磁铁吸住》。
一切无误后再把剩余2MM割完。
6 .加工工件的时候要先处理下毛刺胶水等杂物。
以免影响精度。
要看清加工要求《图纸要求》,工件基准之类的。
7 .钼丝直径*0.12/2= 正常情况下的偏移量8 .割精度高一点东西时候在有碰边加工的情况下要加上钼丝半径。
9.钼丝割一天下来第二天上班的时候紧一下,把限位用的2个挡快往里面移动一点,避免运行时候把丝卡断,机器水箱里面水2天检查一次。
10.定期检查导电快槽痕太深会卡断丝,或者丝变成旋转形的。
11.求中心简单方便的方法第一条边碰边清零摇到对面的边碰边结果除以二再摇到工件大概中心位置卡尺卡一下摇到除以二得出的结果(这样就不用看下面的大坐标了)12.架.和机床行程差不多的工件的时候一定要注意行程够不够走13.还有就是最头疼割铝,如果是割的少的同志,准备一个矮一点的导电快。
在加工的时候,过半个小时往钼丝上刷点煤油,刷煤油是为了清洁钼丝上的氧化铝。
(煤油有分解作用)你也可以用布之类的东西去搞(在丝运行的情况下拿着手上的布裹住钼丝)其实原理很简单只要保持钼丝上清洁就好了《或者用紫铜做导电块》。
- 1、下载文档前请自行甄别文档内容的完整性,平台不提供额外的编辑、内容补充、找答案等附加服务。
- 2、"仅部分预览"的文档,不可在线预览部分如存在完整性等问题,可反馈申请退款(可完整预览的文档不适用该条件!)。
- 3、如文档侵犯您的权益,请联系客服反馈,我们会尽快为您处理(人工客服工作时间:9:00-18:30)。
3.1上下导轮的距离(Z轴高度),产生锥度偏差Δβ。3.2下导轮中心到工件底源自的距离,如:ΔX=ΔHb·tanβ。
3.3工件厚度,
3.4导轮半径R及半径补偿,高速走丝是以导轮支撑高速运行的电极丝,当进行锥度加工时,其支撑点将随着锥度的形成产生较小的变化,产生位移误差,Δl=R/cosβ-R,针对这一误差,可在锥度控制系统中加入导轮半径误差补偿功能(即随着锥度角的变化,对,导轮半径造成的电极丝偏移进行实时补偿)。
4、各因素对加工工艺指标影响相互关系图
六、工件的装夹
1 桥式装夹:两点式、三点式、四点式,装夹稳定,调整容易,但不适用太小的工件;三点定平面,调整容易,四点式,夹持更稳固,但调整麻烦;
2 悬臂式装夹:用于较小型工件,工件受一点支撑,装夹简洁,成本小,但易造成受力不均匀,且调整不方便;
3 钳式装夹:操作简单,两点支撑,稳定性优于悬臂式;
三、应用范围
模具加工、特殊形状、难加工零件、贵重材料加工、多件叠加加工(获得一致尺寸)、制造电火花成型用电极等。
四、工艺指标
1、切割速度Vs:单位时间内电极丝中心线在工件上切过的面积总和称为切割速度,单位为mm2/min。
2、表面粗糙度Ra:用微观轮廓平面度的平均算术偏差值Ra来表示。
3、加工精度:尺寸精度、形状精度、(如:直线度、平面度、椭圆度)和位置精度(如:平行度、垂直度、倾斜度),其影响因素有:切割轨迹的控制精度、机械传动精度、工件装夹定位精度及脉冲电源参数的波动、电极丝的直径误差以及损耗和抖动、工作液脏污程度的变化、加工者的熟练程度等。
1.4、短路峰值电流is的影响,增加短路峰值电流,切割速度提高,表面粗糙度会变差,(短路峰值电流大,相应的加工电流大,脉冲能量大,放电痕变大,且电极丝损耗大,从而使加工精度降低。一般情况下,is<40A,平均加工电流I<5A)
1.5放电波形的影响,电压波形前沿上升较缓,电极丝损耗较小,但不利于脉冲宽度变窄,波形不易形成,降低切割速度。
电火花线切割技术
一、原理
电火花加工又称放电加工,加工时工件与加工用电极为极性不同的电极对,电极对之间充满工作液,起到恢复电极间的绝缘状态及带走放电时产生的热量的作用。在正常电火花加工过程中,电极与工件不接触,而是保持一定的距离(称为间隙),在工件与电极间施加一定的电压,当电极向工件进给至某一距离时,两极间的工作液介质被击穿,局部产生火花放电,放电产生的瞬时高温(8000到12000℃左右)将电极对的表面材料融化(钕铁硼主相熔点1185℃)甚至汽化,逐步蚀除工件,通过控制连续不断地脉冲式的火花放电,就可将工件材料按人们预想的要求予以蚀除,达到加工的目的。
1.6加工极性的影响,线切割加工因脉冲宽度较窄,所以用正极加工,即工件接正极,电极丝接负极,(选用正脉冲波),反接会降低切割速度甚至不能进行切割,并且电极丝损耗大。
1.7进给速度的影响,进给速度应紧密跟踪工件蚀除速度,以保持加工间隙恒定在最佳之处。(最好的进给速度应使有效放电状态的比例尽量大,开路和短路状态比例尽量小,才能使加工速度、加工精度和表面质量都达到最好状态。)进给速度超过工件蚀除速度,容易造成频繁短路,切割速度降低,表面粗糙度差,上下端面切成焦黄色,断丝概率变大;反之,电极间隙偏大,偏于开路,直接影响切割速度,且间隙中电极丝的振动造成时而开路时而短路,直接影响加工表面粗糙度。
2.3工件厚度的影响,工件的切割厚度薄,有利于排屑和消电离,加工稳定性好,但工件太薄,放电脉冲利用率低,效率低,且电极丝易产生抖动,影响精度;工件厚,工作液,难于进入和充满放电间隙,排屑差,易发生短路,影响精度,加工稳定性差,降低切割速度;但电极丝抖动小,又有利于提高加工速度和精度。因此注意根据工件厚度选择脉冲间隔和脉冲宽度。
4 机外装夹:上一工件在加工中,可装夹另一工件,节约装夹和找正时间,多用于悬臂式装夹。
七、工件找正
按划线找正、按基准孔或已成型孔找正、按外形找正。
八、调整变频进给速度
数控线切割的好坏,在很大程度上取决于操作者调整进给速度是否适宜,长期实践表明,用矩形波脉冲进行加工时,不管工件材料、尺寸大小,一般调节加工电流为短路电流的70~80%,严格从理论上说,加工电流与短路电流比值β=1-uc/ui,uc是火花放电维持电压,ui是脉冲空载电压。
4、电极丝损耗θ:可用电极丝在切割10000mm2后电极丝减少量表示,一般长100m的钼丝,切割10000mm2电极丝直径减少0.01mm。
五、各工艺参数对加工的影响
1、电参数
1.1、脉冲宽度ti的影响,增加脉冲宽度,切割速度提高,表面粗糙度变差。(增加脉冲宽度,则单脉冲放电能量增加,当ti>40μs,加工速度增加不多,而电极丝损耗却增大)。[通常ti为1~60μs,脉冲频率为10~100KHz]
其基本物理原理是自由正离子和电子在场中积累,很快形成一个被电离的导电通道。在这个阶段,两板间形成电流。导致粒子间发生无数次碰撞,形成一个等离子区,并很快升高到8000到12000度的高温,在两导体表面瞬间熔化一些材料,同时,由于电极和电介液的汽化,形成一个气泡,并且它的压力规则上升直到非常高。然后电流中断,温度突然降低,引起气泡内向爆炸,产生的动力把溶化的物质抛出弹坑,然后被腐蚀的材料在电介液中重新凝结成小的球体,并被电介液排走。然后通过CNC(数控机床)控制的监测和管控,伺服机构执行,使这种放电现象均匀一致,从而达到加工物被加工,使之成为合乎要求之尺寸大小及形状精度的产品。(正负极表面的高温除使工作液气化、热分解气化外,也使金属材料熔化甚至沸腾气化。这些气化后的工作液和金属蒸气瞬间体积猛增,在放电间隙内成为气泡,迅速热膨胀并产生爆炸。观察电火花线切割加工过程可以看到气泡冒出,同时有黑色的工作液流出,并可听到轻微而清脆的爆炸声。电火花线切割加工主要靠热膨胀和局部微爆炸,使熔化、气化了的金属材料抛出蚀除。)
MPa
熔点/
℃
电阻率/Ω·cm
备注
长期
短期
钨
2000
2500
0
1200-1400
3400
0.0612
较脆
钼
2000
2300
30
700
2600
0.0472
较韧
钨钼
2000
2400
15
1000-1100
3000
0.0532
脆韧适中
2.2.2电极丝直径的影响,电极丝直径小,则承受电流小,切缝窄,不利于排屑和稳定加工,切割速度低;电极丝直径过大,切缝大,熔蚀量大,切割阻力相应加大,不利于提高速度,因此,电极丝直径要适中。最常用为Ф0.12~0.18mm。
二、特点
1、电极丝材料不必比工件材料硬;
2、加工过程中不直接接触工件;
3、利用电热加工,其影响加工的因素(脉冲宽度、间隔、电流等)可调整,操作方便,便于自动化;
4、无需成型电极,工件材料预加工少;
5、电极丝很细,可加工复杂形状、微细异形孔、窄缝等,且其切缝小,切除量小,损耗小,节约成本;
6、单位长度电极丝损耗小,对加工精度影响小。
短路电流可用计算法或实测法得到。
用实测法将不同电压、不同脉宽和间隔比的短路电流列成表格,以备随时查用。
变频进给是否处在最佳状态,可用示波器监视工件和电极丝之间的电压波形判断,速度过(高)跟踪时,加工波淡,短路波浓;欠跟踪时,加工波淡,空载波浓;正常跟踪时,加工波浓,短路波和空载波淡。
实频状态
进给状态
加工面状况
切割速度
电极丝
变频调整
过跟踪
2、非电参数
2.1机械传动精度的影响,传动精度高,加工效果好。
2.1.1坐标工作台传动精度的影响,坐标工作台传动精度很大程度上决定线切割的尺寸加工精度,其主要取决于四个因素:传动机构部件的精度(丝杆、螺母、齿轮、蜗杆、导轨等);配合间隙(丝杆副、齿轮副、蜗轮副及键等的配合间隙);装配精度(主要是丝杆与螺母的三线对中,齿轮的均匀配合涡轮蜗杆的吻合相切,纵横向两拖板的丝杆与导轨的平行度两拖板导轨间的垂直度);机床工作环境(温度、湿度、防尘、震动等)。坐标工作台传动精度差,移动的浮动量就大,导致放电间隙经常发生短路或开路现象,使加工不稳定,常在加工表面留下放电痕迹,甚至出现锯齿状条痕,加工精度和表面粗糙度差。同时脉冲利用率低,降低加工速度,严重时造成断丝。
2.2.3电极丝上丝,紧丝的影响,电极丝上丝,紧丝的好坏直接影响电极丝的张力。电极丝过松,抖动大;过紧,张力大,振动小,放电效率相对高,可提高速度,但易断丝。
2.2.4走丝速度的影响,走丝速度高,则电极丝热应力小,减少断丝和短路的几率,可相应提高切割速度,但电极丝抖动大,对导轮的V形槽磨损大,影响切割精度,电极丝寿命减短。
因此减小电极丝抖动,除了保养好设备,保证装配精度,还可加宝石限位器(电极丝保持器)使电极丝在放电间隙中减小振动。
2.2电极丝及其走丝速度的影响
2.2.1电极丝材料的影响,常用电极丝材料有钼丝、钨丝、钨钼丝,常用规格为Ф0.10~0.30mm,常用电极丝种类和性能见下表: