汽车外文翻译 外文文献 英文文献 中英对照 汽车金融研究
汽车专业外文翻译(中英文翻译)

附录1外文翻译Automobile Brake SystemThe braking system is the most important system in cars. If the brakes fail, the result can be disastrous. Brakes are actually energy conversion devices, which convert the kinetic energy (momentum) of the vehicle into thermal energy (heat).When stepping on the brakes, the driver commands a stopping force ten times as powerful as the force that puts the car in motion. The braking system can exert thousands of pounds of pressure on each of the four brakes.Two complete independent braking systems are used on the car. They are the service brake and the parking brake.The service brake acts to slow, stop, or hold the vehicle during normal driving. They are foot-operated by the driver depressing and releasing the brake pedal. The primary purpose of the brake is to hold the vehicle stationary while it is unattended. The parking brake is mechanically operated by when a separate parking brake foot pedal or hand lever is set.The brake system is composed of the following basic components: the “master cylinder” which is located under the hood, and is directly connected to the brake pedal, converts driver foot’s mechanical pressure into hydraulic pressure. Steel “brake lines” and flexible “brake hoses”connect the master cylinder to the “slave cylinders” located at each wheel. Brake fluid, specially designed to work in extreme conditions, fills the system. “Shoes” and “pads” are pushed by the slave cylinders to contact the “drums” and “rotors” thus causing drag, which (hopefully) slows the car.The typical brake system consists of disk brakes in front and either disk or drum brakes in the rear connected by a system of tubes and hoses that link the brake at each wheel to the master cylinder (Figure).Basically, all car brakes are friction brakes. When the driver applies the brake, the control device forces brake shoes, or pads, against the rotating brake drum or disks at wheel. Frictionbetween the shoes or pads and the drums or disks then slows or stops the wheel so that the car is braked.In most modern brake systems (see Figure 15.1), there is a fluid-filled cylinder, called master cylinder, which contains two separate sections, there is a piston in each section and both pistons are connected to a brake pedal in the driver’s compartment. When the brake is pushed down, brake fluid is sent from the master cylinder to the wheels. At the wheels, the fluid pushes shoes, or pads, against revolving drums or disks. The friction between the stationary shoes, or pads, and the revolving drums or disks slows and stops them. This slows or stops the revolving wheels, which, in turn, slow or stop the car.The brake fluid reservoir is on top of the master cylinder. Most cars today have a transparent r reservoir so that you can see the level without opening the cover. The brake fluid level will drop slightly as the brake pads wear. This is a normal condition and no cause for concern. If the level drops noticeably over a short period of time or goes down to about two thirds full, have your brakes checked as soon as possible. Keep the reservoir covered except for the amount of time you need to fill it and never leave a cam of brake fluid uncovered. Brake fluid must maintain a very high boiling point. Exposure to air will cause the fluid to absorb moisture which will lower that boiling point.The brake fluid travels from the master cylinder to the wheels through a series of steel tubes and reinforced rubber hoses. Rubber hoses are only used in places that require flexibility, such as at the front wheels, which move up and down as well as steer. The rest of the system uses non-corrosive seamless steel tubing with special fittings at all attachment points. If a steel line requires a repair, the best procedure is to replace the compete line. If this is not practical, a line can be repaired using special splice fittings that are made for brake system repair. You must never use copper tubing to repair a brake system. They are dangerous and illegal.Drum brakes, it consists of the brake drum, an expander, pull back springs, a stationary back plate, two shoes with friction linings, and anchor pins. The stationary back plate is secured to the flange of the axle housing or to the steering knuckle. The brake drum is mounted on the wheel hub. There is a clearance between the inner surface of the drum and the shoe lining. To apply brakes, the driver pushes pedal, the expander expands the shoes and presses them to the drum. Friction between the brake drum and the friction linings brakes the wheels and the vehicle stops. To release brakes, the driver release the pedal, the pull back spring retracts the shoes thus permitting free rotation of the wheels.Disk brakes, it has a metal disk instead of a drum. A flat shoe, or disk-brake pad, is located on each side of the disk. The shoes squeeze the rotating disk to stop the car. Fluid from the master cylinder forces the pistons to move in, toward the disk. This action pushes the friction pads tightly against the disk. The friction between the shoes and disk slows and stops it. This provides the braking action. Pistons are made of either plastic or metal. There are three general types of disk brakes. They are the floating-caliper type, the fixed-caliper type, and the sliding-caliper type. Floating-caliper and sliding-caliper disk brakes use a single piston. Fixed-caliper disk brakes have either two or four pistons.The brake system assemblies are actuated by mechanical, hydraulic or pneumatic devices. The mechanical leverage is used in the parking brakes fitted in all automobile. When the brake pedal is depressed, the rod pushes the piston of brake master cylinder which presses the fluid. The fluid flows through the pipelines to the power brake unit and then to the wheel cylinder. The fluidpressure expands the cylinder pistons thus pressing the shoes to the drum or disk. If the pedal is released, the piston returns to the initial position, the pull back springs retract the shoes, the fluid is forced back to the master cylinder and braking ceases.The primary purpose of the parking brake is to hold the vehicle stationary while it is unattended. The parking brake is mechanically operated by the driver when a separate parking braking hand lever is set. The hand brake is normally used when the car has already stopped. A lever is pulled and the rear brakes are approached and locked in the “on” position. The car may now be left without fear of its rolling away. When the driver wants to move the car again, he must press a button before the lever can be released. The hand brake must also be able to stop the car in the event of the foot brake failing. For this reason, it is separate from the foot brake uses cable or rods instead of the hydraulic system.Anti-lock Brake SystemAnti-lock brake systems make braking safer and more convenient, Anti-lock brake systems modulate brake system hydraulic pressure to prevent the brakes from locking and the tires from skidding on slippery pavement or during a panic stop.Anti-lock brake systems have been used on aircraft for years, and some domestic car were offered with an early form of anti-lock braking in late 1990’s. Recently, several automakers have introduced more sophisticated anti-lock system. Investigations in Europe, where anti-lock braking systems have been available for a decade, have led one manufacture to state that the number of traffic accidents could be reduced by seven and a half percent if all cars had anti-lock brakes. So some sources predict that all cars will offer anti-lock brakes to improve the safety of the car.Anti-lock systems modulate brake application force several times per second to hold the tires at a controlled amount of slip; all systems accomplish this in basically the same way. One or more speed sensors generate alternating current signal whose frequency increases with the wheel rotational speed. An electronic control unit continuously monitors these signals and if the frequency of a signal drops too rapidly indicating that a wheel is about to lock, the control unit instructs a modulating device to reduce hydraulic pressure to the brake at the affected wheel. When sensor signals indicate the wheel is again rotating normally, the control unit allows increased hydraulic pressure to the brake. This release-apply cycle occurs several time per second to “pump” the b rakes like a driver might but at a much faster rate.In addition to their basic operation, anti-lock systems have two other things in common. First, they do not operate until the brakes are applied with enough force to lock or nearly lock a wheel. At all other times, the system stands ready to function but does not interfere with normal braking. Second, if the anti-lock system fail in any way, the brakes continue to operate without anti-lock capability. A warning light on the instrument panel alerts the driver when a problem exists in the anti-lock system.The current Bosch component Anti-lock Braking System (ABSⅡ), is a second generation design wildly used by European automakers such as BWM, Mercedes-Benz and Porsche. ABSⅡsystem consists of : four wheel speed sensor, electronic control unit and modulator assembly.A speed sensor is fitted at each wheel sends signals about wheel rotation to control unit. Each speed sensor consists of a sensor unit and a gear wheel. The front sensor mounts to the steering knuckle and its gear wheel is pressed onto the stub axle that rotates with the wheel. The rear sensor mounts the rear suspension member and its gear wheel is pressed onto the axle. The sensor itself is a winding with a magnetic core. The core creates a magnetic field around thewinding, and as the teeth of the gear wheel move through this field, an alternating current is induced in the winding. The control unit monitors the rate o change in this frequency to determine impending brake lockup.The cont rol unit’s function can be divided into three parts: signal processing, logic and safety circuitry. The signal processing section is the converter that receives the alternating current signals form the speed sensors and converts them into digital form for the logic section. The logic section then analyzes the digitized signals to calculate any brake pressure changes needed. If impending lockup is sensed, the logic section sends commands to the modulator assembly.Modulator assemblyThe hydraulic modulator assembly regulates pressure to the wheel brakes when it receives commands from the control utuit. The modulator assembly can maintain or reduce pressure over the level it receives from the master cylinder, it also can never apply the brakes by itself. The modulator assembly consists of three high-speed electric solenoid valves, two fluid reservoirs and a turn delivery pump equipped with inlet and outlet check valves. The modulator electrical connector and controlling relays are concealed under a plastic cover of the assembly.Each front wheel is served by electric solenoid valve modulated independently by the control unit. The rear brakes are served by a single solenoid valve and modulated together using the select-low principle. During anti-braking system operation, the control unit cycles the solenoid valves to either hold or release pressure the brake lines. When pressure is released from the brake lines during anti-braking operation, it is routed to a fluid reservoir. There is one reservoir for the front brake circuit. The reservoirs are low-pressure accumulators that store fluid under slight spring pressure until the return delivery pump can return the fluid through the brake lines to the master cylinder.译文汽车制动系统制动系统是汽车中最重要的系统。
汽车 专业 外文 文献 英文 翻译

外文文献原稿和译文原稿A New Type Car -- Hybrid Electric VehicleWith skyrocketing fuel prices and changes in weather patterns, many car manufacturers claimed to develop the kind of vehicles that will increase the mileage and reduce the emissions. Hybrid car is a kind of vehicle which can meet above requirements. A hybrid car features a small fuel-efficient gas engine combined with an electric motor that assists the engine.The reasons of building such a complicated machine are twofold: to reduce tailpipe emissions and to improve mileage. Firstly, hybrid cars are good for the environment. They can reduce smog by 90 percent and they use far less gasoline than conventional cars. Meanwhile, hybrid cars burn less gasoline per mile, so they release fewer greenhouse gases. Secondly, hybrid cars are economical. Hybrid cars, which run on gas and electricity, can get up to 55 to 60 miles per gallon in city driving, while a typical SUV might use three times as much gas for the same distance! There are three reasons can mainly account for that: 1) Hybrid engines are much smaller than those on conventional cars. A hybrid car engine is to accommodate the 99% of driving time when a car is not going up hills or accelerating quickly. When extra acceleration power is needed, it relies on the battery to provide additional force. 2) Hybrid gasoline engine can shut off when the car is stopped and run off their electric motor and battery.3) Hybrid cars often recover braking energy. Electric motors could take the lost kinetic energy in braking and use it to charge the battery. Furthermore, hybrids are better than all-electric cars because hybrid car batteries recharge as you drive so there is no need to plug in. Most electric cars need to be recharged every 50-100miles. Also, most electric cars cannot go faster than 50-60 mph, while hybrids can.Hybrid cars bridge the gap between electric and gasoline-powered cars by traveling further and driving faster and hybrid gas-electric cars are proving to be a feasible alternative at a time of high gas prices. So, in my opinion, hybrid cars will have a bright future.How Does Hybrid Electric Vehicle Work?You probably own a gasoline or diesel-engine car. You may have heard ofelectric vehicles too. A hybrid vehicle or hybrid electric vehicle (HEV) is a combination of both. Hybrid vehicles utilize two or more sources of energy for propulsion. In the case of HEVs, a combustion engine and an electric motor are used.How it works depends on the type of drive train it has. A hybrid vehicle can either have a parallel or series or parallel-series drive train.Parallel HybridThe parallel hybrid car has a gas tank, a combustion engine, transmission, electric motor, and batteries.A parallel hybrid is designed to run directly from either the combustion engine or the electric motor. It can run using both the engine and the motor. As a conventional vehicle, the parallel hybrid draws its power from the combustion engine which will then drive the transmission that turns the wheels. If it is using the electric motor, the car draws its power from the batteries. The energy from the batteries will then power the electric motor that drives the transmission and turns the wheel.Both the combustion engine and the electric motor are used at the same time during quick acceleration, on steep ascend, or when either the engine or the motor needs additional boost.Since the engine is directly connected to the wheels in a parallel drive train, it eliminates the inefficiency of converting mechanical energy into electrical energy and back. This makes a very effective vehicle to drive on the highway.Series HybridThe series hybrid car also has a gas tank, a combustion engine, transmission, electric motor, and batteries with the addition of the generator. The generator can be the electric motor or it can be another separate component.The series configuration is the simplest among the 3. The engine is not connected to the transmission rather it is connected to the electric motor. This means that the transmission can be driven only by the electric motor which draws its energy from the battery pack, the engine or the generator.A hybrid car with a series drive train is more suited for city driving conditions since the engine will not be subjected to the varying speed demands (stop, go, and idle) that contributes to fuel consumption.Series-Parallel HybridThe series-parallel configuration solves the individual problems of the parallel and series hybrid. By combining the 2 designs, the transmission can be directly connected to the engine or can be separated for optimum fuel consumption. The Toyota Prius and the Ford Escape Hybrid use this technology.Honda’s hybridFor those of you who have toyed with the idea of buying a hybrid but were discouraged by the price, you are not alone. In fact, despite the growing concern for the environment, not to mention the skyrocketing price of gas, hybrid cars still only represent a small percentage of global car sales, and a major reason for this is the cost.Hybrids are considered the wave of the future because they not only reduce emissions, addressing the issue of climate change, but they get great gas mileage, animportant consideration with the current price of oil. It should be noted that hybrids can also improve the power of the engine, which compromises any advantages in fuel efficiency and emissions. Whatever the application, however, the technology makes the cars more expensive.Because of this, they are the vehicle of choice for only a small niche of people who can afford them, and they currently enjoy a special status amongst the image conscious celebrity-set. For most average consumers, however, they are not an option.That may soon change.Honda Motor Corporation, one of the largest car manufacturers in the world and a leader in fuel efficient technology, has unveiled it’s plan to introduce a low-cost hybrid by 2009. If they can pull it off, they hope to make the hybrid a more mainstream car that will be more appealing to the general public, with the ultimate goal of achieving greater sales and broader appeal than their current incarnation.This, of course, is making Detroit nervous, and may signal a need for American car makers to start making greener and more fuel efficient vehicles, something they could afford to ignore in the past because hybrid cars weren’t worth their attention (due to such a small market share) while gas-guzzling SUVs have such high profit margins.Honda, meanwhile, has had to confront a growing need to compete with Toyota, which has not only grown to be the world’s largest automaker, but makes the car that has become synonymous with the hybrid movement, the Prius. Honda is therefore faced with the seemingly insurmountable task of challenging Toyota’s dominance in the market.Concurrently, Toyota is racing to lower production costs on the Prius, as well, which would hopefully result in a lower cost to the consumer. All eyes are on a potentially favorable car buyers market in 2009.In the meantime, with even adamant global warming naysayers warming up (no pun intended) to the possibilities of an ecological disaster on the horizon, maybe it’s time that we got over our need to drive huge SUVs and start moderating our fuel consumption.Then again, as gas prices hovering around $4.00 and with no ceiling in sight, we may have little choice in the matter.Engine Operating PrinciplesMost automobile dngines are internal combustion, reciprocating 4-stroke gasoline engines, but other types have been used, including the diesel, the rotary ( Wankel ) , the 2-srtoke, and stratified charge.Reciprocating means up and down or banck and forth, It is the up and down action of a piston in the cylinder blick, or engine block. The blick is an iron or aluminum casting that contains engine cylinders and passges called water jackets for coolant circulation. The top of the block is covered with the cylinder head. Which forms the combustion chanber. The bottom of the block is covered with an oil pan or oil sump.Power is produced by the linear motion of a piston in a cylinder. However, this linear motion must be changed into rotary motion to turn the wheels of cars of trucks. The piston is attached to the top of a connecting rod by a pin, called a piston pin or wrist pin. The bottom of the connecting rod is attached to the crankshaft. The connecting rod transmits the up-and-down motion of the piston to the crankshaft, which changes it into rotary motion.The connecting rod is mounted on the crankshaft with large beaings called rod bearings. Similar bearings, called main bearings, are used to mount the crankshaft in the block. Shown in Fig. 1-1The diameter of the cylinder is called the engine bore. Displacement and compression ratio are two frequently used engine specifications. Displacement indicates engine size, and compression ratio compares the total cylinder volume to compression chamber volume.The term stroke is used to describe the movement of the iston within the cylinder, as well as the distance of piston travel. Depending on the type of engine the operating cycle may require either two or four strokes to complete. The 4-stroke engine is also called Otto cycle engine, in honor of the German engineer, Dr. Nikolaus Otto, who first applied the principle in 1876. In the 4-stroke engine, four strokes of the piston in the cylinder are required to complete one full operating cycle. Each stroke is named after the action it performs intake, compression, power, and exhaust in that order, shown in Fig1-2.1、Intake strokeAs the piston moves down, the vaporized mixture of fuel and air enters the cylinder through open intake valve. To obtain the maximum filling of the cylinder the intake valve opens about 10°before t.b.c., giving 20°overlap. The inlet valve remains open until some 50°after b.d.c. to take advantage of incoming mixture.2、 Compression strokeThe piston turns up, the intake valve closes, the mixture is compressed within the combustion chamber, while the pressure rise to about 1Mpa, depending on various factors including the compression ratio, throttle opening and engine speed. Near the top of the stroke the mixture is ignited by a spark which bridges the gap of the spark plug.3、 Power strokeThe expanding gases of combustion produces a rise in pressure of the gas to some 3.5Mpa, and the piston is forced down in the cylinder. The exhaust valve opens near the bottom of the stroke.4、Exhust strokeThe piston moves back up with the exhaust valve open some 50°before b.d.d., allowing the pressure within the cylinder to fall and to reduce ‘back’pressure on the piston during the exhaust stroke, and the burned gases are pushed out to prepare for the next intake stroke.The intake valve usually opens just before the exhaust stroke. This 4-stroke cycle is continuously repeared in every as long as the engineremains running.A 2-stroke engine also goes through four actions to complete one operatingcycle.However, the intake and the compression actions are combined in one seroke, and the power and exhaust actions are combined in the other stroke. The term2-stroke cycle or 2-stroke is preferred to the term 2-cycle, which is really not accurate.In automobile engines, all pistons are attached to a single crankshaft. The more cylinders an engine has, the more power strokes produced for cach revolution. This means that an 8-cylinder engine runs more smoothly bdcause the power atrokes are closer together in time and in degrees of engine rotation.The cylinders of multi-cylinder automotive engines arranged in one of three ways. 1、Inline engines use a single block of cylinder.Most 4-cylinder and any 6-cylinder engines are of this design. The cylinders do not have to be vertical. They can be inclined either side.2、V-type engines use two equal bands of cylinders, usually inclined 60degrees or 90degrees from the cach other. Most V-type engines have 6 or 8 cylinders, although V-4 and V-12 engines have been built.3、Horizontally opposed or pancake engines have two equal banks of cylinders 180degreeas apart. These space saving engine designs are often air-cooled, and are found in the Chevrolet Carvair, Porsches, Subaus, and V olkswagens. Subaus design is liquid cooled.Late-model V olkswagen vans use a liquid-cooled version of the air cooled VWhorizontally opposed engine.译文新型汽车----混合动力汽车在油价飞涨的今天,汽车制造商被要求发展一种排放低,行驶里程长的汽车。
汽车电子系统中英文对照外文翻译文献

汽车电子系统中英文对照外文翻译文献汽车电子系统中英文对照外文翻译文献(文档含英文原文和中文翻译)The Changing Automotive Environment:High-Temperature ElectronicsR. Wayne Johnson, Fellow, IEEE, John L. Evans, Peter Jacobsen, James R. (Rick) Thompson, and Mark ChristopherAbstract—The underhood automotive environment is harsh and current trends in the automotive electronics industry will be pushing the temperature envelope for electronic components. The desire to place engine control units on the engine and transmission control units either on or in the transmission will push the ambient temperature above 125℃. However, extreme cost pressures,increasing reliability demands (10 year/241 350 km) and the cost of field failures (recalls, liability, customer loyalty) will make the shift to higher temperatures occur incrementally. The coolest spots on engine and in the transmission will be used. These large bodies do provide considerable heat sinking to reduce temperature rise due to power dissipation in the control unit. The majority of near term applications will be at 150 ℃ or less andthese will be worst case temperatures, not nominal. The transition to X-by-wire technology, replacing mechanical and hydraulic systems with electromechanical systems will require more power electronics. Integration of power transistors and smart power devices into the electromechanical actuator will require power devices to operate at 175 ℃ to 200 ℃ . Hybrid electric vehicles and fuel cell vehicles will also drive the demand for higher temperature power electronics. In the case of hybrid electric and fuel cell vehicles, the high temperature will be due to power dissipation. The alternates to high-temperature devices are thermal management systems which add weight and cost. Finally, the number of sensors in vehicles is increasing as more electrically controlled systems are added. Many of these sensors must work in high-temperature environments. The harshest applications are exhaustgas sensors and cylinder pressure or combustion sensors. High-temperature electronics use in automotive systems will continue to grow, but it will be gradual as cost and reliability issues are addressed. This paper examines the motivation for higher temperature operation,the packaging limitations even at 125 C with newer package styles and concludes with a review of challenges at both the semiconductor device and packaging level as temperatures push beyond 125 ℃.Index Terms—Automotive, extreme-environment electronics.I. INTRODUCTIONI N 1977, the average automobile contained $110 worth of electronics [1]. By 2003 the electronics content was $1510 per vehicle and is expected to reach $2285 in 2013 [2].The turning point in automotive electronics was governmentTABLE IMAJOR AUTOMOTIVE ELECTRONIC SYSTEMSTABLE IIAUTOMOTIVETEMPERATUREEXTREMES(DELPHIDELCOELECTRONIC SYSTEMS) [3]regulation in the 1970s mandating emissions control and fuel economy. The complex fuel control required could not be accomplished using traditional mechanical systems. These government regulations coupled with increasing semiconductor computing power at decreasing cost have led to an ever increasing array of automotive electronics. Automotive electronics can be divided into five major categories as shown in Table I.The operating temperature of the electronics is a function of location, power dissipation by the electronics, and the thermal design. The automotive electronics industry defines high-temperature electronics as electronics operating above 125 ℃. However, the actual temperature for various electronics mounting locations varies considerably. Delphi Delco Electronic Systems recently published the typical continuous maximum temperatures as reproduced in Table II [3]. The corresponding underhood temperatures are shown in Fig. 1. The authors note that typical junction temperatures for integrated circuits are 10 ℃to15℃higher than ambient or baseplate temperature, while power devices can reach 25 ℃ higher. At-engine temperatures of 125℃ peak can be maintained by placing the electronics on theintake manifold.Fig. 1. Engine compartment thermal profile (Delphi Delco Electronic Systems) [3].TABLE III THEAUTOMOTIVEENVIRONMENT(GENERALMOTORS ANDDELPHIDELCO ELECTRONICSYSTEMS) [4]TABLE IV REQUIREDOPERATIONTEMPERATURE FORAUTOMOTIVEELECTRONIC SYSTEMS(TOYOTAMOTORCORP. [5]TABLE V MECHATRONICMAXIMUMTEMPERATURERANGES(DAIMLERCHRYSLER,EATONCORPORA TION, ANDAUBURNUNIVERSITY) [6]Fig. 2. Automotive temperatures and related systems (DaimlerChrysler) [8].automotive electronic systems [8]. Fig. 3 shows an actual measured transmission temperature profile during normal and excessive driving conditions [8]. Power braking is a commonly used test condition where the brakes are applied and the engine is revved with the transmission in gear.A similar real-world situation would be applying throttle with the emergency brake applied. Note that when the temperature reached 135℃, the over temperature light came on and at the peak temperature of 145℃, the transmission was beginning to smell of burnt transmission fluid.TABLE VI2002I NTERNATIONAL T ECHNOLOGY R OADMAPFOR S EMICONDUCTORS A MBI ENTOPERATINGTEMPERATURES FORHARSHENVIRONMENTS (AUTOMOTIVE)[9]The 2002 update to the International Technology Roadmap for Semiconductors (ITRS)did not reflect the need for higher operating temperatures for complex integrated circuits,but did recognize increasing temperature requirements for power and linear devices asshown in Table VI [9]. Higher temperature power devices (diodes and transistors) will beused for the power section of power converters and motor drives for electromechanicalactuators. Higher temperature linear devices will be used for analog control of powerconverters and for amplification and some signal processing of sensor outputs prior totransmission to the control units. It should be noted that at the maximum rated temperaturefor a power device, the power handling capability is derated to zero. Thus, a 200℃ ratedpower transistor in a 200℃ environment would have zero current carrying capability. Thus,the actual operating environments must be lower than the maximum rating.In the 2003 edition of the ITRS, the maximum junction temperatures identified forharsh-environment complex integrated circuits was raised to 150℃through 2018 [9]. Theambient operating temperature extreme for harsh-environment complex integrated circuits was defined as 40℃to 125℃through 2009, increasing to 40℃to 150℃for 2010 and beyond. Power/linear devices were not separately listed in 2003.The ITRS is consistent with the current automotive high-temperature limitations. Delphi Delco Electronic Systems offers two production engine controllers (one on ceramic and one on thin laminate) for direct mounting on the engine. These controllers are rated for operation over the temperature range of 40℃to 125℃. The ECU must be mounted on the coolest spot on the engine. The packaging technology is consistent with 140℃ operation, but the ECU is limited by semiconductor and capacitor technologies to 125℃.The future projections in the ITRS are not consistent with the desire to place controllers on-engine or in-transmission. It will not always be possible to use the coolest location for mounting control units. Delphi Delco Electronics Systems has developed an in-transmission controller for use in an ambient temperature of 140℃[10] using ceramic substrate technology. DaimlerChrysler is also designing an in-transmission controller for usewith a maximum ambient temperature of 150℃ (Figs. 4 and 5) [11].II. MECHATRONICSMechatronics, or the integration of electrical and mechanical systems offers a number ofadvantages in automotive assembly. Integration of the engine controller with the engine allows pretest of the engine as a complete system prior to vehicle assembly. Likewise with the integration of the transmission controller and the transmission, pretesting and tuning to account for machining variations can be performed at the transmission factory prior to shipment to the automobile assembly site. In addition, most of the wires connecting to a transmission controller run to the solenoid pack inside the transmission. Integration of the controller into the transmission reduces the wiring harness requirements at the automobile assembly level.Fig. 4. Prototype DaimlerChrysler ceramic transmission controller [11]Fig. 5. DaimlerChrysler in-transmission module [11].The trend in automotive design is to distribute control with network communications. As the industry moves to more X-by-wire systems, this trend will continue. Automotivefinalassembly plants assemble subsystems and components supplied by numerous vendors to build the vehicle. Complete mechatronic subsystems simplify the design, integration, management, inventory control, and assembly of vehicles. As discussed in the previous section, higher temperature electronics will be required to meet future mechatronic designs.III. PACKAGINGCHALLENGES AT125℃Trends in electronics packaging, driven by computer and portable products are resulting in packages which will not meet underhood automotive requirements at 125℃. Most notable are leadless and area array packages such as small ball grid arrays (BGAs) and quadflatpacks no-lead (QFNs). Fig. 6 shows the thermal cycle test 40 ℃to 125℃ results for two sizes of QFN from two suppliers [12]. A typical requirement is for the product to survive 2000–2500 thermal cycles with<1% failure for underhood applications. Smaller I/O QFNs have been found to meet the requirements.Fig. 7 presents the thermal cycle results for BGAs of various body sizes [13]. The die size in the BGA remained constant (8.6 *8.6 mm). As the body size decreases so does the reliability. Only the 23-mm BGA meets the requirements. The 15-mm BGA with the 0.56-mm-thick BT substrate nearly meets the minimum requirements. However, the industry trend is to use thinner BT substrates (0.38 mm) for BGA packages.One solution to increasing the thermal cycle performance of smaller BGAs is to use underfill. Capillary underfill was dispensed and cured after reflow assembly of the BGA. Fig. 8 shows a Weibull plot of the thermal cycle data for the 15-mm BGAs with four different underfills. Underfill UF1 had no failures after 5500 cycles and is, therefore, not plotted. Underfill, therefore, provides a viable approach to meeting underhood automotive requirements with smaller BGAs, but adds process steps, time, and cost to the electronics assembly process.Since portable and computer products dominate the electronics market, the packages developed for these applications are replacing traditional packages such as QFPs for new devices. The automotive electronics industry will have to continuedeveloping assembly approaches such as underfill just to use these new packages in current underhood applications.IV. TECHNOLOGY CHALLENGES ABOVE125 ℃The technical challenges for high-temperature automotive applications are interrelated, but can be divided into semiconductors, passives, substrates,interconnections, and housings/connectors. Industries such as oil well logging have successfully fielded high-temperature electronics operating at 200℃and above. However, automotive electronics are further constrained by high-volume production, low cost, and long-term reliability requirements. The typical operating life for oil well logging electronics may only be 1000 h, production volumes are in the range of 10s or 100s and, while cost is a concern, it is not a dominant issue. In the following paragraphs, the technical challenges for high-temperature automotive electronics are discussed.Semiconductors: The maximum rated ambient temperature for most silicon basedintegrated circuits is 85℃, which is sufficient for consumer, portable, and computing product applications. Devices for military and automotive applications are typically rated to 125℃. A few integrated circuits are rated to 150℃, particularly for power supply controllers and a few automotive applications. Finally, many power semiconductor devices are derated to zero power handling capability at 200℃.Nelmset al.and Johnsonet al.have shown that power insulated-gate bipolar transistors (IGBTs) and metal–oxide–semiconductorfield-effect transistors (MOSFETs) can be used at 200℃[14], [15]. The primary limitations of these power transistors at the higher temperatures are the packaging (the glass transition temperature of common molding compounds is in the 180℃to 200℃range) and the electrical stress on the transistor during hard switching.A number of factors limit the use of silicon at high temperatures. First, with a bandgap of 1.12 eV, the silicon p-n junction becomes intrinsic at high temperature (225℃to 400℃depending on doping levels). The intrinsic carrier concentration is given by (1)As the temperature increases, the intrinsic carrier concentration increases. When the intrinsic carrier concentration nears the doping concentration level, p-n junctions behave as resistors, not diodes, and transistors lose their switching characteristics. One approach used in high-temperature integrated circuit design is to increase the doping levels, which increases the temperature at which the device becomes intrinsic. However, increasing the doping levels decreases the depletion widths, resulting in higher electricfields within the device that can lead to breakdown.A second problem is the increase in leakage current through a reverse-biased p-n junction with increasing temperature. Reverse-biased p-n junctions are commonly used in IC design to provide isolation between devices. The saturation current (I,the ideal reverse-biascurrent of the junction) is proportional to the square of the intrinsic carrier concentrationwhere Ego=bandgap energy atT= 0KThe leakage current approximately doubles for each10℃rise in junction temperature. Increased junction leakage currents increase powerdissipation within the device and can lead to latch-up of the parasitic p-n-p-n structure incomplimentary metal–oxide–semiconductor (CMOS) devices. Epitaxial-CMOS(epi-CMOS) has been developed to improve latch-up resistance as the device dimensionsare decreased due to scaling and provides improved high-temperature performancecompared to bulk CMOS.Silicon-on-insulator (SOI) technology replaces reverse-biased p-n junctions withinsulators, typically SiO2 , reducing the leakage currents and extending the operating rangeof silicon above 200℃. At present, SOI devices are more expensive than conventional p-njunction isolated devices. This is in part due to the limited use of SOI technology. With the continued scaling of device dimensions, SOI is being used in some high-performance applications and the increasing volume may help to eventually lower the cost.Other device performance issues at higher temperatures include gate threshold voltage shifts, decreased noise margin, decreased switching speed, decreased mobility, decreased gain-bandwidth product, and increased amplifier input–offset voltage [16]. Leakage currents also increase for insulators with increasing temperature. This results in increased gate leakage currents, and increased leakage of charge stored in memory cells (data loss). For dynamic memory, the increased leakage currents require faster refresh rates. For nonvolatile memory, the leakage limits the life of the stored data, a particular issue for FLASH memory used in microcontrollers and automotive electronics modules.Beyond the electrical performance of the device, the device reliability must also be considered. Electromigration of the aluminum metallization is a major concern. Electromigration is the movement of the metal atoms due to their bombardment by electrons (current flow). Electromigration results in the formation of hillocks and voids in the conductor traces. The mean time to failure (MTTF) for electromigration is related to the current density (J)and temperature(T) as shown in (3)The exact rate of electromigration and resulting time to failure is a function of the aluminum microstructure. Addition of copper to the aluminum increases electromigration resistance. The trend in the industry to replace aluminum with copper will improve the electromigration resistance by up to three orders of magnitude [17].Time dependent dielectric breakdown (TDDB) is a second reliability concern. Time to failure due to TDDB decreases with increasing temperature. Oxide defects, including pinholes, asperities at the Si–SiO2 interface and localized changes in chemical structure that reduce the barrier height or increase the charge trapping are common sources of early failure [18]. Breakdown can also occur due to hole trapping (Fowler–Nordheim tunneling). The holes can collect at weak spots in the Si–SiO2 interface, increasing the electricfield locally and leading to breakdown [18]. The temperature dependence of time-to-breakdown(tBD) can be expressed as [18]Values reported for Etbd vary in the literature due to its dependence on the oxidefield and the oxide quality. Furthermore, the activation energy increases with breakdown time [18].With proper high-temperature design, junction isolated silicon integrated circuits can be used to junction temperatures of 150℃to 165℃, epi-CMOS can extend the range to 225℃to 250℃ and SOI can be used to 250℃ to 280℃ [16, pp. 224]. High-temperature, nonvolatile memory remains an issue.For temperatures beyond the limits of silicon, silicon carbidebased semiconductors are being developed. The bandgap of SiC ranges from 2.75–3.1 depending on the polytype. SiC has lower leakage currents and higher electric field strength than Si. Due to its wider bandgap, SiC can be used as a semiconductor device at temperatures over 600℃. The primary focus of SiC device research is currently for power devices. SiC power devices may eventuallyfind application as power devices in braking systems and direct fuel injection. High-temperature sensors have also been fabricated with SiC. Berget al.have demonstrated a SiCbased sensor for cylinder pressure in combustion engines [19] at up to 350℃ and Casadyet al.[20] have shown a SiC-based temperature sensor for use to 500℃. At present, the wafer size, cost, and device yield have made SiC devices too expensive for general automotive use. Most SiC devices are discrete, as the level of integration achieved in SiC to date is low.Passives: Thick and thin-film chip resistors are typically rated to 125 ℃. Naefeet al.[21] and Salmonet al.[22] have shown that thick-film resistors can be used at temperatures above 200℃if the allowable absolute tolerance is 5% or greater. The resistors studied were specifically formulated with a higher softening point glass. The minimum resistance as afunction of temperature was shifted from 25℃to 150℃to minimize the temperature coefficient of resistance (TCR) over the temperature range to 300℃. TaN and NiCr thin-film resistors have been shown to have less than 1% drift after 1000 h at 200℃ [23]. Thus, for tighter tolerance applications, thin-film chip resistors are preferred. Wire wound resistors provide a high-temperature option for higher power dissipation levels [21].High-temperature capacitors present more of a challenge. For low-value capacitors, negative-positive-zero (NPO) ceramic and MOS capacitors provide low-temperature coefficient of capacitance (TCC) to 200℃. NPO ceramic capacitorshave been demonstrated to 500℃ [24]. Higher dielectric constant ceramics (X7R, X8R, X9U), used to achieve the high volumetric efficiency necessary for larger capacitor values, exhibit a significant capacitance decrease above the Curie temperature, which is typically between 125℃ to 150℃. As the temperature increases, the leakage current increases, the dissipation factor increases, and the breakdown strength decreases. Increasing the dielectric tape thickness to increase breakdown strength reduces the capacitance and is a tradeoff. X7R ceramic capacitors have been shown to be stable when stored at 200℃[23]. X9U chip capacitors are commercially available for use to 200 C, but there is a significant decrease in capacitance above 150℃.Consideration must also be given to the capacitor electrodes and terminations. Ni is now being substituted for Ag and PdAg to lower capacitor cost. The impact of this change on hightemperature reliability must be evaluated. The surface finish for ceramic capacitor terminations is typically Sn. The melting point of the Sn (232℃) and its interaction with potential solders/brazes must also be considered. Alternate surfacefinishes may be required.For higher value, low-voltage requirements, wet tantalum capacitors show reasonable behavior at 200℃ if the hermetic seal does not lose integrity [23]. Aluminum electrolytics are also available for use to 150℃. Mica paper (260℃) and Teflonfilm (200℃) capacitors can provide higher voltage capability, but are large and bulky [25]. High-temperature capacitors are relatively expensive. V olumetrically efficient, high-voltage, highcapacitance, high-temperature and low-cost capacitors are still needed.Standard transformers and inductor cores with copper wire and teflon insulation are suitable for operation to 200℃. For higher temperature operation, the magnetic core, the conductor metal (Ni instead of Cu) and insulator must be selected to be compatible with the higher temperatures [16, pp. 651–652] Specially designed transformers can be used to 450℃ to 500℃, however, they are limited in operating frequency.Crystals are required for clock frequency generation for microcontrollers. Crystals with acceptable frequency shift over the temperature range from 55℃to 200℃have been demonstrated [22]. However, the selection of packaging materials and assembly process for the crystal are key to high-temperature performance and reliability. For example, epoxies used in assembly must be compatible with 200℃ operation.Substrates: Thick-film substrates with gold metallization have been used in circuits to 500℃[21], [23]. Palladium silver, platinum silver, and silver conductors are morecommonly used in automotive hybrids for reduced cost. Silver migration has been observed with an unpassivated PdAg thick-film conductor under bias at 300℃ [21]. The time-to-failure needs to be examined as a function of temperature and bias voltage with and without passivation. Low-temperature cofired ceramic (LTCC) and high-temperature cofired ceramic (HTCC) are also suitable for high-temperature automotive applications. Embedded resistors are standard to thick-film hybrids, LTCC, and some HTCC technologies. As previously mentioned, thick-film resistors have been demonstrated at temperatures 200℃. Dielectric tapes for embedded capacitors have also been developed for LTCC and HTCC. However, these embedded capacitors have not been characterized for high-temperature use.High-Tg laminates are also available for fabrication of hightemperature printed wiring boards. Cyanate esters [Tg=250℃by differential scanning calorimetry (DSC)], polyimide (260℃by DSC), and liquid crystal polymers(Tm>280℃)provide options for use to 200℃. Cyanate ester boards have been used successfully in test vehicles at 175℃, but failed when exposed to 250℃ [26]. The higher coefficient of thermal expansion (CTE) of the laminate substrates compared to the ceramics must be considered in the selection of component attachment materials. The temperature limits of the laminates with respect to assembly temperatures must also be carefully considered. Work is ongoing to develop and implement embedded resistor and capacitor technology for laminate substrates for conventional temperature ranges. This technology has not been extended to high-temperature applications.One method many manufacturers are using to address the higher temperatures whilemaintaining lower cost is the use of laminate substrates attached to metal. The typical design involves the use of higher Tg( +140℃ and above) laminate substrates attached to an aluminum plate (approximately 2.54-mm thick) using a sheet or liquid adhesive. To assist in thermal performance, the laminate substrate is often thinner (0.76 mm) than traditional automotive substrates for under-the-hood applications. While this design provides improved thermal performance, the attachment of the laminate to aluminum increases the CTE for the overall substrates. The resultant CTE is very dependent on the ability of the attachment material to decouple the CTE between the laminate substrate and the metal backing. However, regardless of the attachment material used, the combination of the laminate and metal will increase the CTE of the overall substrate above that of a stand-alone laminate substrate. This impact can be quite significant in the reliability performance for components with low CTE values (such as ceramic chip resistors). Fig. 9 illustrates the impact of two laminate-to-metal attachment options compared to standard laminate substrates [27], [28]. The reliability data presented is for 2512 ceramic chip resistors attached to a 0.79-mm-thick laminate substrate attached to aluminum using two attachment materials. Notice that while one material significantly outperforms the other, both are less reliable than the same chip resistor attached to laminate without metal backing.This decrease in reliability is also exhibited on small ball grid array (BGA) packages. Fig. 10 shows the reliability of a 15-mm BGA package attached to laminate compared to the same package attached to a laminate substrate with metal backing [27], [28]. The attachment material used for the metal-backed substrate was the best material selected from previous testing. Notice again that the metal-backed substrate deteriorates the reliability. This reliability deterioration is of particular concern since many IC packages used for automotive applications are ball grid array packages and the packaging trend is for reduced packaging size. These packaging trends make the use of metal-backed substrates difficult for next generation products.One potential solution to the above reliability concern is the use of encapsulants and underfills. Fig. 11 illustrates how conformal coating can improve component reliability for surface mount chip resistors [27], [28]. Notice that the reliability varies greatly depending on material composition. However, for components which meet a marginal level of reliability, conformal coatings may assist the design in meeting the target reliability requirements. The same scenario can be found for BGA underfills. Typical underfill materials may extend the component life by a factor of two or more. For marginal IC packages, this enhancement may provide enough reliability improvement toall the designs to meet under-the-hood requirements. Unfortunately, the improvements provided byencapsulants and underfills increase the material cost and adds one or more manufacturing processes for material dispense and cure.Interconnections: Methods of mechanical and electrical interconnection of the active and passive components to the board include chip and wire,flip-chip, and soldering of packaged parts. In chip and wire assembly, epoxy die-attach materials can beused to 165℃ [29]. Polyimide and silicone die-attach materials can be used to 200℃. For higher temperatures, SnPb ( >90Pb), AuGe, AuSi, AuSn, and AuIn have been used. However,with the exception of SnPb, these are hard brazes and with increasing die size, CTE mismatches between the die and the substrate will lead to cracking with thermalcycling. Ag–glass die attach has also been used with Si die, but the die stresses are high [30]. The processing temperatures (330℃ to 425℃) required for the hard brazes and the Ag-glass are not compatible with the laminate-based substrates.Small-diameter Au and Pt wire bonding can be used to 500℃ on thick-film Au with Au pads on the SiC die [22].However, most Si die have aluminum metallization and the use of Au wire is limited to 180 ℃to 200℃due to Au–Al intermetallic formation and Kirkendall voiding. Use of Al wire creates a monometallic bond at the die interface. Pd-doped thick-film Au conductors have been developed for compatibility with small-diameter Al wire to 300℃[31]. While Al wire can be bonded to silver bearing thick-film conductors, the primary concern is corrosion due to the galvanic potential between Al and Ag [32]. Chlorine contamination in the presence of moisture is the primary corrosion mechanism. Increasing the Pd content of the PdAg conductor, extreme care in the cleanliness of the assembly and potting in silicone gel can be used to reduce the risk of corrosion. Au wire can be bonded to pure Ag thick films, but the Ag migrates along the surface of the gold wire at elevated temperatures [33].On laminate substrates, Ni/Aufinishes over the copper are compatible with Au wire (thick Aufinish) and with Al wire (thin Aufinish). In the case of Al wire, the Au layer must be thin so the Al wire bonds to the underlying Ni. Intermetallic formation and voiding will occur if the Au layer is too thick. If a phosphorus containing Ni is used, the phosphorus content should be limited to 6 –8 .Al–Ni bonds are potentially reliable to 300℃, but further study is required [32].For wire bonding to power devices, large-diameter Al wire bonding is used. In some。
毕业设计论文外文文献翻译汽车专业汽修点火系统中英文对照
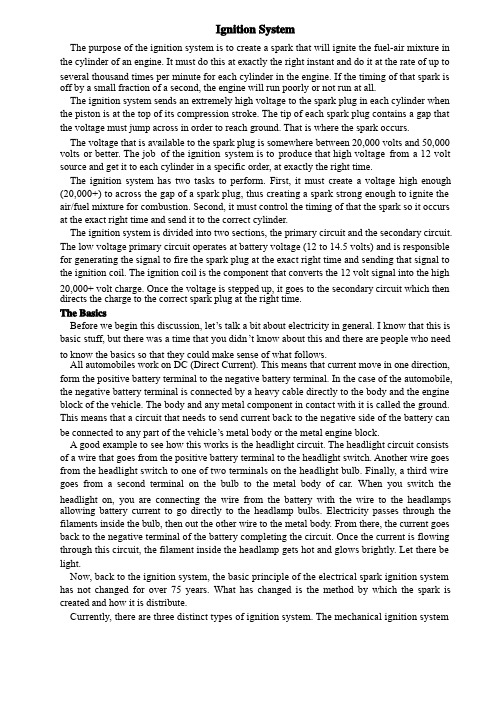
Ignition SystemThe purpose of the ignition system is to create a spark that will ignite the fuel-air mixture in the cylinder of an engine. It must do this at exactly the right instant and do it at the rate of up to several thousand times per minute for each cylinder in the engine. If the timing of that spark is off by a small fraction of a second, the engine will run poorly or not run at all.The ignition system sends an extremely high voltage to the spark plug in each cylinder when the piston is at the top of its compression stroke. The tip of each spark plug contains a gap that the voltage must jump across in order to reach ground. That is where the spark occurs.The voltage that is available to the spark plug is somewhere between 20,000 volts and 50,000 volts or better. The job of the ignition system is to produce that high voltage from a 12 volt source and get it to each cylinder in a specific order, at exactly the right time.The ignition system has two tasks to perform. First, it must create a voltage high enough (20,000+) to across the gap of a spark plug, thus creating a spark strong enough to ignite the air/fuel mixture for combustion. Second, it must control the timing of that the spark so it occurs at the exact right time and send it to the correct cylinder.The ignition system is divided into two sections, the primary circuit and the secondary circuit. The low voltage primary circuit operates at battery voltage (12 to 14.5 volts) and is responsible for generating the signal to fire the spark plug at the exact right time and sending that signal to the ignition coil. The ignition coil is the component that converts the 12 volt signal into the high 20,000+ volt charge. Once the voltage is stepped up, it goes to the secondary circuit which then directs the charge to the correct spark plug at the right time.The BasicsBefore we begin this discussion, let’’s talk a bit about electricity in general. I know that this is Before we begin this discussion, letbasic stuff, but there was a time that you didn’’t know about this and there are people who need basic stuff, but there was a time that you didnto know the basics so that they could make sense of what follows.All automobiles work on DC (Direct Current). This means that current move in one direction, form the positive battery terminal to the negative battery terminal. In the case of the automobile, the negative battery terminal is connected by a heavy cable directly to the body and the engine block of the vehicle. The body and any metal component in contact with it is called the ground. This means that a circuit that needs to send current back to the negative side of the battery can be connected to any part of the vehicle’’s metal body or the metal engine block.be connected to any part of the vehicleA good example to see how this works is the headlight circuit. The headlight circuit consists of a wire that goes from the positive battery terminal to the headlight switch. Another wire goes from the headlight switch to one of two terminals on the headlight bulb. Finally, a third wire goes from a second terminal on the bulb to the metal body of car. When you switch the headlight on, you are connecting the wire from the battery with the wire to the headlamps allowing battery current to go directly to the headlamp bulbs. Electricity passes through the filaments inside the bulb, then out the other wire to the metal body. From there, the current goes back to the negative terminal of the battery completing the circuit. Once the current is flowing through this circuit, the filament inside the headlamp gets hot and glows brightly. Let there be light.Now, back to the ignition system, the basic principle of the electrical spark ignition system has not changed for over 75 years. What has changed is the method by which the spark is created and how it is distribute.Currently, there are three distinct types of ignition system. The mechanical ignition systemwas used prior to 1975. It was mechanical and electrical and used no electronics. By understanding these early system, it will be easier to understand the new electronic andcomputer controlled ignition system, so don’’t skip over it. The electronic ignition system started computer controlled ignition system, so donfinding its way to production vehicles during the early 70s and became popular when better control and improved reliability became important with the advent of emission controls. Finally, the distributor less ignition system became available in the mid 80s. This system was always computer controlled and contained no moving parts, so reliability was greatly improved. Most of these systems required no maintenance except replacing the spark plugs at intervals from 60,000 to over 100,000 miles.Let’’s take a detailed look at each system and see how they work.LetThe Mechanical Ignition SystemThe distributor is the nerve center of the mechanical ignition system and has two tasks to perform. First, it is responsible for triggering coil to generate a spark at the precise instant that it is required (which varies depending how fast the engine is turning and how much load it is under). Second, the distributor is responsible for directing that spark to the proper cylinder (which is why it is called a distributor).The circuit that powers the ignition system is simple and straight forward. When you insert the key in the ignition switch and turn the key to the Run position, you are sending current from the battery through a wire directly to the positive (+) side of the ignition coil. Inside the coil is a series of copper windings that loop around the coil over a hundred times before exiting out the negative (-) side of the coil. From there, a wire takes this current over to the distributor and is connected to a special on/off switch, called the points. When the points are closed, this current goes directly to ground. When current flows from the ignition switch, through the windings in the coil, then to ground, it builds a strong magnetic field inside the coil.The points are made up of a fixed contact point that is fastened to a plate inside the distributor, and a movable contact point mounted on the end of a spring loaded arm. The movable point rides on a 4, 6, or 8 lobe cam (depending on the number of cylinder in the engine) that is mounted on a rotating shaft inside the distributor. This distributor cam rotates in time with the engine, making one complete revolution for every two revolutions of the engine. As it rotates, the cam pushes the points open and closed. Every time the points open, the flow of current is interrupted through the coil, thereby collapsing the magnetic field and releasing a high voltage surge through the secondary coil windings. This voltage surge goes out the top of the coil and through the high-tension coil wire.Now, we have the voltage necessary to fire the spark plug, but we still have to get it to the correct cylinder. The coil wire goes from the coil directly to the distributor cap. Under the cap is a rotor that is mounted on top of the rotating shaft. The rotor has a metal strip on the top that is in constant contact with the center terminal of the distributor cap. It receives the high voltage surge from the coil wire and sends it to the other end of the rotor which rotates past each spark plug terminal inside the cap. As the rotor turns on the shaft, it sends the voltage to the correct spark plug wire, which in turn sends it to the spark plug. The voltage enters the spark plug at the terminal at the top and travels down the core until it reaches the tip. It then jumps across the tip of the spark plug, creating a spark suitable to ignite the fuel-air mixture inside that cylinder. The description I just provided is the simplified version, but should be helpful to visualize the process, but we left out a few things that make up this type of ignition system. For instance, we didn’’t talk about the condenser that is connected to the point, nor did we talk about the system didnto advance the timing. Let’’s take a look at each section and explore it in more detail.to advance the timing. LetThe Ignition SwitchThere are two separate circuits that go from the ignition switch to the coil. One circuit runs through a resistor in order to step down the voltage about 15% in order to protect the points from premature wear. The other circuit sends full battery voltage to the coil. The only time this circuit is used is during cranking. Since the starter draws a considerable amount of current to crank the engine, additional voltage is needed to power the coil. So when the key is turned to the spring-loaded start position, full battery voltage is used. As soon as the engine is running, the driver releases the key to the run position which directs current through the primary resistor to the coil.On some vehicles, the primary resistor is mounted on the firewall and is easy to replace if it fails. On other vehicles, most notably vehicles manufactured by GM, the primary resister is a special resister wire and is bundled in the wiring harness with other wires, making it more difficult to replace, but also more durable.The DistributorWhen you remove the distributor cap from the top of the distributor, you will see the points and condenser. The condenser is a simple capacitor that can store a small amount of current. When the points begin to open the current, flowing through the points looks for an alternative path to ground. If the condenser were not there, it would try to jump across the gap of the point as they begin to open. If this were allowed to happen, the points would quickly burn up and you would hear heavy static on the car radio. To prevent this, the condenser acts like a path to ground. It really is not, but by the time the condenser is saturated, the points are too far apart for the small amount of voltage to jump across the wide point gap. Since the arcing across the opening points is eliminated, the points last longer and there is no static on the radio from point arcing.The points require periodic adjustments in order to keep the engine running at peek efficiency. This is because there is a rubbing block on the points that is in contact with the cam and this rubbing block wears out over time changing he point gap. There are two ways that the points can be measured to see if they need an adjustment. One way is by measuring the gap between the open points when the rubbing block is on the high point of the cam. The other way is by measuring the dwell electrically. The dwell is the amount, in degrees of cam rotation that the points stay closed.On some vehicles, points are adjusted with the engine off and the distributor cap removed. A mechanic will loosen the fixed point and move it slightly, then retighten it in the correct position using a feeler gauge to measure the gap. On other vehicles, most notably GM cars, there is a window in the distributor where a mechanic can insert a tool and adjust the points using a dwell meter while the engine is running. Measuring dwell is much more accurate than setting the points with a feeler gauge.Points have a life expectancy of about 10,000 miles at which time have to be replaced. This is done during a routine major tune up, points, condenser, and the spark plugs are replaced, the timing is set and the carburetor is adjusted. In some cases, to keep the engine running efficiently, a minor tune up would be performed at 5,000 mile increments to adjust the point and reset the timing.Ignition CoilThe ignition coil is nothing more that an electrical transformer. It contains both primary and secondary winding circuit. The coil primary winding contains 100 to 150 turns of heavy copper wire. This wire must be insulated so that the voltage does not jump from loop to loop, shortingit out. If this happened, it could not create the primary magnetic field that is required. The primary circuit wire goes into the coil through the positive terminal, loops around the primary windings, then exits through the negative terminal.The coil secondary winding circuit contains 15,000 to 30,000 turns of fine copper wire, which also must be insulated from each other. The secondary windings sit inside the loops of the primary windings. To further increase the coils magnetic field the windings are wrapped around a soft iron core. To withstand the heat of the current flow, the coil is filled with oil which helps keep it cool.The ignition coil is the heart of the ignition system. As current flows through the coil a strong magnetic field is build up. When the current is shut off, the collapse of this magnetic field to the secondary windings induces a high voltage which is released through the large center terminal. This voltage is then directed to the spark plugs through the distributor.Ignition Timing The timing is set by loosening a hold-down screw and rotating the body of the distributor. Since the spark is triggered at the exact instant that the points begin to open, rotating the distributor body (which the point are mounted on) will change the relationship between the position and the position of the distributor cam, which is on the shaft that is geared to the engine rotation.While setting the initial or base timing is important, for an engine to run properly, the timing needs to change depending on the speed of the engine and the load that it is under. If we can move the plate that the points are mounted on, or we could change the position of the distributor cam in relation to the gear that drives it, we can alter the timing dynamically to suit the needs of the engine.Ignition Wires These cables are designed to handle 20,000 to more than 50,000 volts, enough voltage to toss you across the room if you were to be exposed to it. The job of the spark plug wires is to get that enormous power to the spark plug without leaking out. Spark plug wires have to endure the heat of a running engine as well as the extreme changes in the weather. In order to do their job, spark plug wires are fairly thick, with most of that thickness devoted to insulation with a very thin conductor running down the center. Eventually, the insulation will succumb to the elements and the heat of the engine and begins to harden, crack, dry out, or otherwise break down. When that happens, they will not be able to deliver the necessary voltage to the spark plug and a misfire will occur. That is what is meant by “Not running on all cylinders cylinders””. To correct this problem, the spark plug wires would have to be replaced.Spark plug wires are routed around the engine very carefully. Plastic clips are often used to keep the wires separated so that they do not touch together. This is not always necessary, especially when the wires are new, but as they age, they can begin to leak and crossfire on damp days causing hard starting or a rough running engine.Spark plug wires go from the distributor cap to the spark plugs in a very specific order. This is called the is called the ““firing order firing order”” and is part of the engine design. Each spark plug must only fire at the end of the compression stroke. Each cylinder has a compression stroke at a different time, so it is important for the individual spark plug wire to be routed to the correct cylinder.For instance, a popular V8 engine firing order is 1, 8, 4, 3, 6, 5, 7, 2. The cylinders are numbered from the front to the rear with cylinder #1 on the front-left of the engine. So the cylinders on the left side of the engine are numbered 1, 3, 5, 7while the right side are numbered 2, 4, 6, 8. On some engine, the right bank is 1, 2, 3, 4 while the left bank is 5, 6, 7, 8. A repairmanual will tell you the correct firing order and cylinder layout for a particular engine.The next thing we need to know is what direction the distributor is rotating in, clockwise or counter-clockwise, and which terminal on the distributor caps that #1 cylinder is located. Once we have this information, we can begin routing the spark plug wires.If the wires are installed incorrectly, the engine may backfire, or at the very least, not run on all cylinders. It is very important that the wires are installed correctly.Spark PlugsThe ignition system system’’s sole reason for being is to service the spark plug. It must provide sufficient voltage to jump the gap at the tip of the spark plug and do it at the exact right time, reliably on the order of thousands of times per minute for each spark plug in the engine.The modern spark plug is designed to last many thousands of miles before it requires replacement. These electrical wonders come in many configurations and heat ranges to work properly in a given engine. The heat range of a spark plug dictates whether it will be hot enough to burn off any residue that collects on the tip, but not so hot that it will cause pre-ignition in the engine. Pre-ignition is caused when a spark plug is so hot, that it begins to glow and ignite the fuel-air mixture prematurely, before the spark. Most spark plugs contain a resistor to suppress radio interference. The gap on a spark plug is also important and must be set before the spark plug is installed in the engine. If the gap is too wide, there may not be enough voltage to jump the gap, causing a misfire. If the gap is too small, the spark may be inadequate to ignite a lean fuel-air mixture also causing a misfire.The Electronic Ignition SystemThis section will describe the main differences between the early point & condenser systems and the newer electronic systems. If you are not familiar with the way an ignition system works in general, I strongly recommend that you first read the previous section The Mechanical Ignition System.In the electronic ignition system, the points and condenser were replaced by electronics. On these systems, there were several methods used to replace the points and condenser in order to trigger the coil to fire. One method used a metal wheel with teeth, usually one for each cylinder. This is called an armature. A magnetic pickup coil senses when a tooth passes and sends a signal to the control module to fire the coil.Other systems used an electric eye with a shutter wheel to send a signal to the electronics that it was time to trigger the coil to fire. These systems still need to have the initial timing adjusted by rotating the distributor housing.The advantage of this system, aside from the fact that it is maintenance free, is that the control module can handle much higher primary voltage than the mechanical point. V control module can handle much higher primary voltage than the mechanical point. Voltage can oltage can even be stepped up before sending it to the coil, so the coil can create a much hotter spark, on the order of 50,000 volts that is common with the mechanical systems. These systems only have a single wire from the ignition switch to the coil since a primary resistor is not longer needed. On some vehicles, this control module was mounted inside the distributor where the points used to be mounted. On other designs, the control module was mounted outside the distributor with external wiring to connect it to the pickup coil. On many General Motors engines, the control module was inside the distributor and the coil was mounted on top of the distributor for a one piece unitized ignition system. GM called it high energy ignition or HEI for short.The higher voltages that these systems provided allow the use of a much wider gap on the spark plugs for a longer, fatter spark. This larger sparks also allowed a leaner mixture for betterfuel economy and still insure a smooth running engine.The early electronic systems had limited or no computing power, so timing still a centrifugal and vacuum advance built into the distributor.On some of the later systems, the inside of the distributor is empty and all triggering is performed by a sensor that watches a notched wheel connected to either the crankshaft or the camshaft. These devices are called crankshaft position sensor or camshaft position sensor. In these systems, the job of the distributor is solely to distribute the spark to the correct cylinder through the distributor cap and rotor. The computer handles the timing and any timing advance necessary for the smooth running of the engine.The Distributor Ignition SystemNewer automobiles have evolved from a mechanical system (distributor) to a completely solid state electronic system with no moving parts. These systems are completely controlled by the on-board computer. In place of the distributor, there are multiple coils that each serves one or two spark plugs. A typical 6 cylinder engine has 3 coils that are mounted together in a coil pack””. A spark plug wire comes out of each side of the individual coil and goes to the “packappropriate spark plug. The coil fires both spark plugs at the same time. One spark plug fires on the compression stroke igniting the fuel-air mixture to produce power while the other spark plug fires on the exhaust stroke and does nothing. On some vehicles, there is an individual coil for each cylinder mounted directly on top of the spark plug. This design completely eliminates the high tension spark plug wires for even better reliability. Most of these systems use spark plugs that are designed to last over 100,000 miles, which cuts down on maintenance costs.参考文献:[1] 王欲进,张红伟汽车专业英语[M]. 北京:北京大学出版社,中国林业出版社,2007.8,55—67点火系统点火系统的作用是产生点燃发动机气缸里可燃混合物的火花。
汽车外文翻译 外文文献

外文文献翻译附录A(英文原文)Adaptive Clutch Engaging Process Control Automatic Mechanical Transmission LIU Hai’ou(刘海鸥),CHEN HUI’yan(陈慧岩),DING Hua’rong(丁华荣),HE Zhong’bo(何忠波) Abstract: Based on detail analysis of cluch engaging process control targets and adaptive demands,a control strategy which is based on speed signal,different from that of based on main clutch displacement signal,is put forward.It considers both jerk and slipping work which are the most commonly used quality evaluating indexes of vehicle starting phase.The adaptive control system and its reference model are discussed profoundly.Taking the adaptability to different starting gears and different road conditions as examples,some proving field test records are shown to illusrate the main clutch adaptive control strategy at starting phase.Proving field test gives acceptable results. Key words: automatic mechanical transmission(AMT); transmission technology; adaptive control; main clutch engagement The engaging process control strategy of friction main clutch,whether wet or dry,is the focus in vehicle technology field.Some of the control strategies are based on main clutch displacement signal.An adaptive control strategy has been developed, which is based on main clutch out put shaft speed signal grounded on our research work.It is proved to have extensive adaptability. 1 Control Targets and Adaptive Demands The most commonly used quality evaluating indexes of vehicle starting phase are jerk and slipping work. Jerk—As an index evaluating the smoothness in vehicle starting phase, the jerk is the rate of vehicle longitudinal acceleration.According to this definition,the expression of jerk is given as j=da/dt=d2v/dt2 (1) where j is the jerk;v and a are the vehicle running speed and acceleration respectively. According to vehicle dynamics,the vehicle-run-ning speed is determined by the balance between engine traction force and running resistance and can be expressed as t v D e g gd Gd v A C f G T r i i 2 015 . 21 ) sin ( (2) Where e T is the engine out put torque;G is the vehicle total weight; r is the driving wheel radius; f and are the road resistance coefficient and ram p way angle respectively; D C is the air resistance coefficient. The function of a mechanism is to transform motion from one rigid body to another as part of the action of a machine,There are three types of common mechanical device that can be used as basic elements of a mechanism. 1.—Gear system,in which toothed members in contact transmit motion between rotating shafts. 2.Cam system,where a uniform motion of an input member I converted into a nonunifirm motion of the output member. 3.Plane and spatial linkages are also useful in creating mechanical motions for a point or rigid body. Mechanisms form thee basic geometrical element of many mechanical devices including automatic machinery,typewriters,mechanical toys,textile machinery,and others.A mechanism typically is designed to create a desired motion of a rigid body relative to a reference member.Kinematic design,or kinematic syntheses,of mechanisms often is the first step in the design of a complete machine.When forces are considered,the additional problems of dynamics,bearing loads,stresses,lubrication,and the like are introduced,aad the larger problem become one of machine design. Gear are machine elements that transmit motion by means of successively engaging teeth,Gears transmit motion from one ratating shaft to another, or to a rack that translates. Numerous applications exist in which a constant angular velocity ratio(or constant torque ratio)must be transmitted between shafts, Based on the variety of gear types available, there is no restriction that the input and the output shafts need be either in-line or parallel.Nonlinear angular velocity tratios are also available by using noncircccuar gear,In order to maintain a constant angular velocity,the individual tooth prifle must obey the fundamental law of gearing:for a pair of gears to transmit a constant angular velocity ratio,the shape of theircontacting profiles must be such that the common normal passes through a fixed point on the line of the centers. There are several standard gear types.For applications with parallel shafts,straight spur gear,parallel helical,or herringbone gears are usually used,In the case of intersecting shafts,straight bevel or spiral bevel gears are employed.For nonintersecting and nonparallel shafts,crossed helical,worm,face,skew bevel or hypoid gears would be acceptable choices.For spur gears,the pirch circles of mating gears are tangent to wach other.They roll on one another without sliding.The addendum is the height by which a tooth projects beyond the pitch circle(also the tadial distance between the pitch circle and the addendum circle).The clearance is the amount by which the dedendum (tooth height below the pitch circle)in a given gear exceeds the addendum of its mating gear,The tooth thickness is the distance across the tooth along the are of the pitch circle while the tooth space is the distance between adjacent teeth along the are of the pitch circle.TRhe backlash is the amount by which the width of the tooth space exceeds the thickness of the engaging tooth at the pitchi circle. Helical gears are used to transmit motion between parallel shafts.The helix angle I the same on each gear,but one gear must have a right-hand helix and the other a left-hand helix.The shape of the tooth is the angular edge of the paper becomes a helix.If wo unwind this paper,eachpoint on the angulaaar edge genetares an involute curve,The surface obtained when every point on the edge generates an involute is called an involute helicoids.in helical gears,the line is diagonal across the face of the tooth,It is this gradual engagement of the teeth and the smooth transfer of load from one tooth to another,which give helical gears the ability to transmit heavy loads at high soeeds,Helical gears subject the shaft bearings to both radial and thrust loads.When the thrust loads become high or are objectionable for other reasons,it may be desirable to use double helical gears.A doublehelical gear(herringbone)is equivalent to two helical gears of opposite hand,mounted side by side on he same shaft.They develop opposite thrust reactions and thus cancel at the thrust load.when two or more single helcal gears are mounted on the same shaft,the hand of the gears should be selected so as to produce the minimum thrust load. Straight bevel gears are easy to design and simple to manufacture and give very good results in service if they are mounted accurately and positively.As in the case of spur gears,however,they become noisy at higher values of the pitch-line velocity.In shese cases it is often good design practice to go to the spiral bevel gear,which is the bevel counterpart of the helical gear.As in the case of helicaal gears,spiral bevel bears give a much smoother tooth action than strain bevel gears,and hence are useful where high speed are encountered.It is frequently desirable,as in the case of automotive differential applications,to have gearing similar to bevel gears but with the shaft offset.Such gears are called hyoid gears because their pitch surfaces are hyperboloids of revolution,The tooth action between such gears is a combination of rolling and slidin along a straight line and has much in common with that of worm gears. A shaft is a rotating or stationary ually of circular cross section,having mounted power-transmission lements.Shafmay subjected to bending,tension,compression,or torsional loads,acting singly or in combination with one another,When they are combined,one may expect to find both static and fatigue strength to be important design considerations,since a single shaft may be subjected too static stresses,completely reversed,and repeated stresses,aii acting at the same time. The word “shaft” cover numerous variationgs,such as axles and spindles.An axle is a shaft,either stationary or rotating,not subjected to torsion load.A short rotating shaft is often called a spindle. When either the lateral or the torsional deflection of a shaft must be held to close limits,the shaft must besized on the basis of deflection,before analyzing the stresses,The reason for this is that,if the shaft is made stiff enough so that the deflection is not too large,it is probable that the resulting stresses will be safe,But by no means should the designer assume that they are safe;it is almost always necessary to calculate them so that he knows they are within acceptable limits.Whenever possible,the power-transmission elements,such as gears or pulleys ,should be located close to the supporting bearings.This reduces the bending moment,and hence the deflection and bending stress. According to the discussion of vehicle dynamics, the control of jerk and slipping work is related to the change rate of main clutch transmitting torque. However, the torque transducer cannot be installed in the control system,so the transient torque signal cannot be obtained directly.A method that some investigators use is to control the output torque through controlling main clutch engaging displacement.But the displacement can only reflect torque change indirectly. Their corresponding relationship is affected by many factors. And once the installed position changes or the signal drifts,it will be difficult to control the transmitting torque value accurately. The main clutch adaptive control strategy based on the speed signal adjusts the transmitting torque based on the jerk and the slipping work known from the change of rotating speed signal. 2 Conclusions ①The key technique of adaptive control strategy based on speed signal is the reference model. Different from the strategy based on main clutch displacement signal, it can reflect vehicle dynamics during engaging process and so can satisfy the engaging demands well. ②The reference model based on speed signal can be illustrated by the speed change course curve. Set the parameters for each sector correctly according to smooth and fast engaging demands, and the adaptive control target can be realized through adopting PWM/PFM control method. ③A large amount of tests that were conducted for along time show that thecontrol strategy based on speed signal has good adaptability and can adapt to different gears, road conditions, load, main clutch parameters(temperature, attrition wear and friction material) and driving styles. References: [1] Horn J,Bamberger J,Michan P,et al.Flatness-based clutch control for automated manual transmission[J]. Control Engineering Practice,2003(11):1353-1359.[2] Toshimichi Minowa,Tatsuya Ochi,Hiroshi Kuroiwa, et al. Smooth gear shift control technology for clutch-to-clutch shifting[R].SAE199120121054,1991. [3] Xi Jun qiang.Research on brushless electric motor driven automatic main clutch and its control strategy[D].Beijing:School of Vehicular and Transportation, Beijing Institute of Technology, 2001.(inChinese) [4] Lei Yu long, Ge An lin, Li Yong jun. Main clutch control strategy at vehicle starting phase[J]. Automotive Engineering,2000(4):266-269. (inChinese) [5] Andrew Szadkowski. Shiftability and Shift Quality Issues in Clutch Transmission Systems[R]. SAE 912697,1991. 附录B(译文)适应性离合器在机械自动传动中的加工控制刘海鸥,陈慧岩,丁华荣,何忠波(机械和车辆工程学校,北京技术学院,北京100081,中国)摘要:依靠对离合器运行过程的详细分析控制目标和适应的要求,一个主要依靠速度信号而不是那些依靠离合器的移动信号的控制策略被迅速发展。
车辆工程 汽车 外文翻译 外文文献 英文文献 汽车安全系统技术研究分析
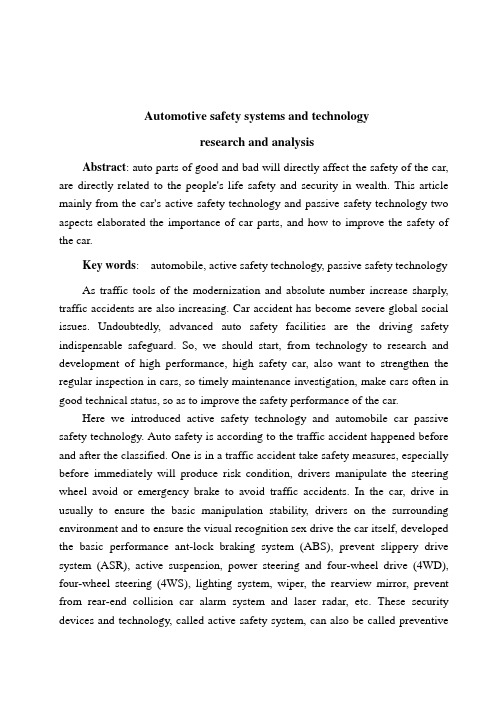
Automotive safety systems and technologyresearch and analysisAbstract: auto parts of good and bad will directly affect the safety of the car, are directly related to the people's life safety and security in wealth. This article mainly from the car's active safety technology and passive safety technology two aspects elaborated the importance of car parts, and how to improve the safety of the car.Key words: automobile, active safety technology, passive safety technologyAs traffic tools of the modernization and absolute number increase sharply, traffic accidents are also increasing. Car accident has become severe global social issues. Undoubtedly, advanced auto safety facilities are the driving safety indispensable safeguard. So, we should start, from technology to research and development of high performance, high safety car, also want to strengthen the regular inspection in cars, so timely maintenance investigation, make cars often in good technical status, so as to improve the safety performance of the car.Here we introduced active safety technology and automobile car passive safety technology. Auto safety is according to the traffic accident happened before and after the classified. One is in a traffic accident take safety measures, especially before immediately will produce risk condition, drivers manipulate the steering wheel avoid or emergency brake to avoid traffic accidents. In the car, drive in usually to ensure the basic manipulation stability, drivers on the surrounding environment and to ensure the visual recognition sex drive the car itself, developed the basic performance ant-lock braking system (ABS), prevent slippery drive system (ASR), active suspension, power steering and four-wheel drive (4WD), four-wheel steering (4WS), lighting system, wiper, the rearview mirror, prevent from rear-end collision car alarm system and laser radar, etc. These security devices and technology, called active safety system, can also be called preventivesecurity system. On the other hand, in order to reduce traffic accidents and company by personnel directly suffer degree, ensure company take staff and pedestrian safety, says the security for passive safety, can also be called conflict safety. When after the accident, in order to prevent disasters, including prevent the expansion of fire and make crew from traffic accident can extricate the security devices and systems, called prevent disaster expand security system.One.Automobile active security technology1. ABS braking systemAnt-lock Braking System (Braking System, lock do by ABS computers as ABS), hydraulic device, the wheel speed sensors, brake hydraulic pipeline and electrical wiring etc. Their structures are shown below.ABS tasseled for the car in various driving conditions braking performance and brake safety particularly important, especially is emergency braking, can make full use of the peak between tire and road surface adhesion properties, improve performance and reduce automobile fight sideslip braking distance, give full play to the braking performance, but also increase the automobile braking process control. So as to reduce the possibility of car accidents.No installation ABS car, if the driving force trample brake pedal, wheel will rapidly lower speed, and finally wheels stop turning, but body because of inertia remains forward sliding. This phenomenon was at the wheel and pavement occur between larger "slip", appear this kind of situation, the car tires of automobile lateral spreads almost disappear, so poor force will appear the following phenomena:(1) Steering stability fall: the steering wheel is ineffective, vehicle tail manipulation of curl, serious when vehicle circles or appear folding phenomenon;(2) Handling fall: manipulate the steering wheel and short of steering requirements;(3) Braking distance extended: more than general braking distance.So, we can imagine to have installed ABS system of the car safety is very important.2.the ASR drive torque control systemABS are used to prevent car braking process wheel lock, will wheel sliding rate control in ideal range, so as to shorten the braking distance, improve automobile braking direction stability and steering control, so as to improve the safety of the car. Along with the increase of vehicle performance requirements, not only in braking process required to prevent wheel lock, and asked the driver to prevent drive roller skating turn in the process, making cars in the direction stability, driving process steering control ability and acceleration performance, so are improved by the car drive torque steering system ASR (Accelerations Regulation) Slip. ASR is the perfect complement and ABS ASR, but most alone is set with ABS combined together, commonly used ABS/ASR says, called antiskid control system.ASR is mainly used to prevent car in the beginning, accelerate the wheels, guarantee slip in the car accelerated rate and improve the stability in bad pavement drive attached conditions. It makes no difference speed in the car lock ice roads and muddy road started and to improve its capacity, also can prevent high in speed by turning cars gliding pavement and rear lateral spreads phenomenon.Anyhow, prevent the wheel because ASR slip, can maximize the engine driving moment of cars had enough, ensure the longitudinal force, lateral force and manipulation of power, make cars in starting, steering and accelerate the process, in gliding and muddy road, in a mountain area downhill process can steadily driving, guarantees the safety, reducing tire wear and fuel consumption, and improves the car driving capability.3.VDC systemABS/ASR system successfully solves the brake and the car when driven direction stability problem, but cannot solve the vehicle steering stability problem driving direction. For example when steering road, inevitably by lateral and longitudinal force, only local surface can provide full lateral and longitudinal force, the pilot can control vehicles. If the ground adhesion ability lower lateral, will damage cars driving ability predetermined direction. Rainy days cars driving, oftenhigh-speed steering lateral sliding out, it is the ground because of insufficient lateral adhesion ability. To resolve the issue, and developed countries automobile industry recently in ABS/ASR system on the basis of the development of dynamic Control system (into car Dynamics Control, the abbreviation VDC Vehicle). The system of the car brake, driving, suspension, steering, engine and so on various main assembly control system in function, structure organic ground comprehensive together, can make cars in all kinds of bad working conditions, such as ice road pavement, commuting, river bend pavement and took evasive action moving line, braking and acceleration and the downhill for different conditions, such as bearing, different type pressure and different levels of type wear all have good direction stability, to show the best driving performance. VDC applications, in braking, acceleration and steering aspects of driver's fully released request, is the car of active safety driving a new milestone.VDC of steering control system is mainly by driving for each wheel brake control and engine power output control to realize. For example, if the car turn left front wheel for steering the inadequate capacity tend to slip out of the corner, VDC system can measure imminent, just know lateral spreads left rear brake adopt appropriate measures. If at the same corner, because rear wheel tend to slip out of favor of lateral overmuch, VDC system is proper braking to front-right wheel failure, maintain the stability of the vehicle driving. In extreme cases, VDC system can also take reduce engine to reduce the power output, and to reduce the speed of the demand side adhesion ability to maintain the stability of the vehicle driving. Adopt VDC system, automobile in folio pavement or corner of pavement braking distance still can further reduce.4.CCS cars cruise control systemAuto cruise Control System (Cruiser Control System, abbreviation for CCS) is can make automobile work in engine favorable speed range, reduce driver's driving manipulate labor intensity, improve the driving comfort the automatic driving device.Car cruising system (CCS) role is required by the driver: after a normally-closed switch, no speed on the accelerator pedal can automatically keepthe speed, make the vehicle with the fixed speed. Using this device, when on the highway after a long time, the driver driving not have to control the accelerator pedal, reduce fatigue, while reducing unnecessary speed change, can reduce save fuel.Auto cruise control system is the earliest development of the automotive electronic control system. This system USES another speed sensor, will speed signal input engine control microcomputer, by microcomputer control vacuum system work. This system can make use of the server, speed control switch lever and brake pedal on vacuum lift switches etc, its function and basic system the same.In this system, electronic control device can accord change of driving resistance, automatic regulation engine throttle Angle, make the speed constant. Such not only reduce unnecessary speed change, which saves fuel, also reduced the driver's burden. The electronic cruise control system which is shown in figure 2.Two. Automobile passive safety technology1. Seat beltCar seat belt is a safety device, it can in car collision or sharp turn, make crew to keep its original position as possible without mobile and rotation, avoid collision with in-car hard parts caused damage. Seat belts and airbags, as modern cars are safety devices, but the long history of the former, popularize the scope.The seemingly simple seat belt actually not "simple". Attention has been at the forefront of traffic safety, through the analysis of general motors after a car accident found: seat belt not only makes people protect the lives, can be in more than half of the accident to reduce or even eliminate drivers, motorists are the chance of injury. Car collision or unexpected emergency braking force generated great inertia, will allow the driver and passenger and car windscreen, steering wheel, seat, collision happened objects such as secondary to drive is caused extremely easily crew serious damage, even drive occupant seats or threw the apex, seat belts can will ride in the seat. Bondage personnel When has the accident, which can effectively prevent the collision, and its buffer role can absorbs a greatdeal of kinetic energy, reduce rides personnel extent of the injuries.Fasten your seat belt airbags play our role is also an important condition. Because the airbag to maximize role for the ride in the impact of the physical location, sitting instant action have extremely strict and the requirements. Otherwise, the airbag started strong instantaneous wallops to head are fragile site, may cause serious damage, especially for children, this damage can be fatal. Even the most ordinary three belts, try a can timely in crash that lived rides the bundle, ensure the upper part of a ride in the airbag fully extended range, make the airbag most effectively play efficacy. Accordingly, must not because the car is equipped with airbags and feel carefree seat belt fastened, only to reduce or eliminate the traffic accident happen.2. The airbagWhen the front collision happened strong, because inertia, who rides the body forward fast moving, then seat belts and will try to "pull" rides on person the body, absorb some of the impact energy, while the airbag with "the eyepiece trend" inflatable and completely open; Then the rides the upper body will sink to airbags, gas also began from the vent air uniform escaping, and absorbed most of the impact energy; Subsequently, the ride back seat and return to the body. Above the whole process is almost always happens in a flash, who rides the completely in passive situation, in this case, the passive rely on auxiliary occupant protection system is the only option. Airbags development design is based on the protection on seat belt Co., LTD; they cooperate with each other to ride the play the auxiliary protective effect.Seat belt usage in under the condition of the crew, balloon help reduce chest, head and facial injuries in the seriousness of the collision. When car collision happened before, the first is the car to stop motion, car under the action of inertial force crews to go forward with the original speed still sport. Not wearing a seatbelt crews will and steering dish, front windscreen together, so it can be severely hurt; Wearing a seatbelt as car stop the crew can stop moving forward movement and gradually. If collision violent, crew forward movement of the seat belts, even faster in the complete stop before motion, still and in-car things together. If this fashionin steering the disk or within the popup balloon inflated dash, it can protect the occupant reduce the possibility of car together with things, more uniform dispersion head, chest, absorb the impact energy of movement, thus crew has added effect of seat belts.In addition to seat belts and airbags outside car passive safety technology includes car bumper, automobile safety glass, security body, occupant head and neck protection system (WHIPS), etc. These vehicles to improve the safety performance has very important contributionThree. Automobile active safety new technology1. Eye Car skillsEye Car technology can make each driver eyes in the same relative height, guarantee of pavement and the surrounding a six-lane unimpeded sight and best visibility. This technology can also offer a specific driving environment.Eye Car through the use of first-class motor mobile automatic will different figure driver's eyes tuned to the same height to solve the problem, meanwhile, visibility of steering dish, brake and accelerate pedals and floor and the central adjustment to constitute console to their respective driving conditions. Meanwhile to the former pillar design, will it again from drivers sights removed. Because the bus driver received the most crucial information generally have 90% from outside, acquired through the eyes observe. So, this improvement for vehicle safety is of great significance.2. Cam Car technologyCam Car technology aims to help improve the driver of perception. The technical features are:(1) Installed in the car to camera system on both sides before to make drivers can bypass the large vehicle behind a car or see ahead of pedestrians. In a typical driving situation in the crowded traffic, the pilot of the centre-left cornering could more easily view the opposite of vehicles.(2) Side after buy video camera provides broader visual profile of vision. The camera coverage than traditional rearview mirror wants wide, especially for theadjacent driveway.(3) Installed in a car, the four miniatures sectored form to decorate after a camera can obtain the car panoramic perspective. Image via electronic synthesis, has the zoom and 160 ° wide-angle ability.(4) "night eye" (Night Eye) camera can be in low illumination conditions, when the car is in reverse gear, even in a dark cases can also provide car close range after small images.Four. Automobile passive safety new technology1. Future airbags(1) It cans inflatable screen system. This is a new safety design; its basic principle is to protect in-car occupant's head, when that happens it will carry on the air, air after the tent shape is swelling.(2) Tubular inflatable structure head air sac. This system for supplement current side protection system, still stopover in protecting the chest and abdomen, brachial ministry, to head protection were insufficient. It with rigid body structure, the door body protective just beams, side air sac, can form a complete side safe defend net, this will be the future security protection trend.(3) Head support system. Head support system generally called the headrest, vehicles which the headrest, with seats, not just for comfortable fact is more important to safety. Vehicle if in an emergency brake, the body will have strong to and fro, because the principle of inertia occupant body swinging, especially neck must follow. If no head support buffer headrest, neck injury caused by damage is very surprising.(4) The external airbags.2. Adaptive constraint technology system (ARTS)New adaptive constraint technology system (ARTS) use a series of sensors to monitor the driver seat, seat belt use, in front of the occupant take quality and location and intensity of the collision of the collisions and collision force direction, then according to the specific information such as the collision of each front airbag characteristics of the crew on regulated. The system can further reduce due toimproper airbag for crew on the damage, especially for smaller front row figure crew.3. Automobile energy-absorbing direction columnAuto absorbing in automobile direction tubing through collisions of redistribution to steering wheel wallop, would wallop path to deliver shunt quickly, making the minimum of load on the steering wheel. The steering column by hollow tubes and steering bearings form. Traditional hollow tubes and the steering column steering bearings is integral, steering shaft top and steering connections, the connecting with direction below. And suck can direction string of characteristic is will the steering column in two, divided into unblock steering column and the steering column under two parts; Inside of the steering shaft also divided into two sections, with outgoing quarter agencies between them connected. Once a collision make direction, outgoing quarter mechanism has displacement bottom tailor-made steering shaft will fold, under the steering column move on the steering column, to achieve "indented within" and thus expand space reduce damage.Five. The tire pressure monitoring systemIn a car's tyros high-speed process, all drivers fault is the most worry and the most difficult to prevent, is also sudden traffic accident happened important reasons. According to statistics, China highway in the traffic accident is caused due to 70% of a flat tire, and in the U.S. this ratio is as high as 80%. How to prevent a blowout has become an important task of safe driving. According to the national quality supervise center of rubber tires in the expert analysis, maintain the standard tire pressure driving and the timely discovery tire is to prevent leakage of key blowout. Tire Pressure and Monitoring System (TPMS) - car Tire Pressure Monitoring System will no doubt is the ideal tool. The system is mainly used in automobile driving to tire pressure real-time automatic monitoring; to a flat tire and depression are the police, in order to ensure safety.Drivers from the monitors can know each tire pressure value, when tire pressure below the club set pressure limit, monitor will automatically alarm.Anyhow, car active safety technology and passive safety technology for thesafety of automobile driving is very important, and besides, such as environmental factor, artificial factor of the vehicle safety is also very important. Therefore, we must be prepared to all aspects of requirements and technology, to ensure the safety of vehicle driving.汽车安全系统技术研究分析摘要:汽车各部件的好与坏将直接影响汽车行驶的安全性,直接关系着人们的生命安全和产财安全。
外文文献翻译中英文智能车辆研究
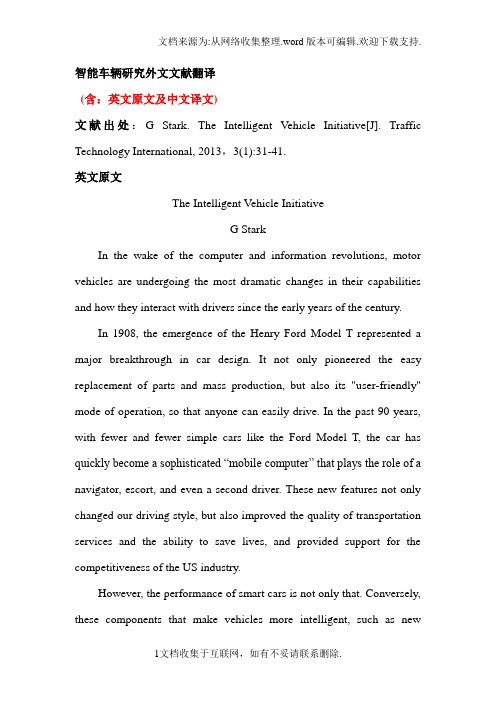
智能车辆研究外文文献翻译(含:英文原文及中文译文)文献出处:G Stark. The Intelligent Vehicle Initiative[J]. Traffic Technology International, 2013,3(1):31-41.英文原文The Intelligent Vehicle InitiativeG StarkIn the wake of the computer and information revolutions, motor vehicles are undergoing the most dramatic changes in their capabilities and how they interact with drivers since the early years of the century.In 1908, the emergence of the Henry Ford Model T represented a major breakthrough in car design. It not only pioneered the easy replacement of parts and mass production, but also its "user-friendly" mode of operation, so that anyone can easily drive. In the past 90 years, with fewer and fewer simple cars like the Ford Model T, the car has quickly become a sophisticated “mobile computer” that plays the role of a navigator, escort, and even a second driver. These new features not only changed our driving style, but also improved the quality of transportation services and the ability to save lives, and provided support for the competitiveness of the US industry.However, the performance of smart cars is not only that. Conversely, these components that make vehicles more intelligent, such as newinformation, safety and automation technologies, arrive on the market as spare parts, or as optional equipment, or as special accessories for after-sales services. In order to improve driver safety, these technologies have been continuously developed and put on the market. However, individual technologies have not yet been integrated and they cannot create fully intelligent vehicles that are highly collaborative with drivers.The automotive industry has realized and solved the influx of potential uncoordinated technologies. But their progress is hindered by technical and economic barriers, uncertain consumer preferences, and imperfect standards and guidelines. In addition, neither traditional car manufacturers nor government regulators (unless the security issues are obvious) can control the use of aftermarket products, especially in the use o f trucks and buses. However, there is no “people-oriented” smart vehicle that attempts to integrate and coordinate various technologies to solve problems. We may not only lose the opportunity to implement new in-vehicle technology, but may even unintentionally reduce the safety and performance of driving.Recognizing the importance of intelligent vehicles and the potential dangers of human factors in vehicle design, the Ministry of Transport launched the Intelligent Vehicles Initiative (IVI) in 1997. This initiative aims to accelerate the development and integration of automotive systems to help cars, trucks and bus drivers operate more safely and effectively.The 1980s TV series “Knight Ranger” features smart vehicles that can cross over tall buildings, seem to drive the supersonic itself, spy on bad guys, and have English words and housekeepers. This car is not only smart but smart. Although smart vehicles in the real world will not be able to fly over traffic, they will have strong capabilities. As envisioned by the International Vaccine Research Institute, smart vehicles will be able to provide route instructions, feel objects, warn drivers that collisions will occur, auto signals help drivers stay alert in emergency situations, and may eventually be able to take over driving.The computer-based technology of information and motor vehicles, however, is not a new use. A wide range of automotive computers began the 1980s with the aim of improving vehicle operation and driver comfort. These technologies include the electronic control of the performance of fuel injection engines, especially the reduction of vehicle emissions, improved fuel economy, anti-lock braking systems to help drivers maintain control over slippery roads, and cruise control systems to reduce driver's driving for a long period of time. tedious. And these technologies are mainly to strengthen the vehicle, the latest wave in vehicle technology, of which the most interested is the purpose of the IVI's capabilities, and is intelligent transportation systems designed to strengthen the capabilities of the driver. These systems include early warning and information, driving assistance and automation technology.Research Plan The original research plan for the Mack IVI FOT included requirements to install the LDWS, TSA, and ACN systems on a test fleet of 36 tanker trucks operated by McKenzie Tank Lines in normal revenue service over a 19-month period. The final research plan was a revision of the original plan, because several technical problems with the data-acquisition and transmission systems delayed the start of the FOT. This in turn created logistical problems with the installation of systems and deployment of trucks in the test fleet. Consequently, the FOT was performed over a 12-month period, with a primary focus on the safety benefits of the LDWS, which was installed on 22 trucks. Since the Eaton VORAD (EVT-300) collision warning system (CWS) was standard equipment on the McKenzie Tank Lines tractors used in the FOT, this system was active throughout the FOT. The CWS was not disabled during the FOT, because driving with the CWS was considered to be valid baseline driving for McKenzie Tank Lines drivers, and it would be difficult to separate the effects of removing the CWS and adding the LDWS. All trucks were also equipped with data acquisition and communications equipment. LDWS Evaluation. Use of the LDWS was expected to affect driving performance in two ways. First, there is the immediate effect of warning the driver of a potential lane excursion, which gives the driver an opportunity to change his or her driving behavior before making a large lane excursion. Second, after gainingexperience using the LDWS, the driver’s overall driving performance may improve even without the use of the system. Another possibility is that a driver’s driving performance may decline when the system is disabled, because the driver may become dependent on the system. Three conditions were compared in the experimental design: ♦Phase I –Baseline Period: Data collected during this period would characterize the driving behavior of drivers who were not receiving LDWS feedback.♦ Phase II – Active Period: Data collected during this period would characterize the driving behavior of drivers receiving LDWS feedback.♦ Phase III – Post-Active Period: Data collected during this period would characterize the driving behavior of drivers after the LDWS feedback had been deactivated.Just as people have different professional capabilities, different types and levels of vehicle-mounted smart vehicle technology give “intelligence” to complement this driver. The driver information system expands the knowledge of the driver's route and location. Early warning systems, such as collision avoidance techniques, improve the driver's perception of what is happening in the surrounding environment. Automate and drive technical assistance and simulate the driver's thoughts and actions to actual operations or in case of emergency, long-term vehicles are temporary. However, in smart vehicles will expand the driver's ability, it may also increase the driver's traditional role. Inparticular, within the technology of the new car, the role of the person is expanded from sensory motor skills, writes Thomas Sheridan, professor who is responsible for the Human Machine Systems Laboratory at the Massachusetts Institute of Technology (MIT), "this plan, Programmers, ITS studies in automation, diagnosticians, monitoring learners and managers show the feasibility of the benefits of many technologies that will be applied in smart vehicles.The route guidance system will help drivers to better drive in unfamiliar streets or Finding the fastest route to their destination In 1992 and 1993, field trials conducted by the Department of Transportation at Orlando TravTek showed that a tourist-guided vehicle equipped with a route guidance system reduced the problem of 30% of vehicles turning the wrong corner. Compared with tourists with paper maps, it saves 20% of the time.The collision avoidance system can strengthen traffic safety regulations and completely prevent traffic accidents. According to studies, if drivers can respond for more than half a second, they can avoid 60% of the time. Road traffic accidents and 30% of head-on collisions, and 75% of vehicle accidents are caused by driver's devastation.The National Highway Traffic Safety Administration (NHTSA) estimates that each year The country’s use of these three types of collision avoidance system can avoid 1.1 million traffic accidents and account for 17% of the total number of traffic accidents, which can save 17,500 lives (belt and airbags save about10,500 people) and restore 26 billion US dollars. The other safety facilities are under test, including the automatic collision notification system. When the airbag of a car pops up, the system will automatically send a distress signal, and the drowsy driver warning system can prevent the driver from getting drowsy while the car is driving. To sleep.The in-vehicle automation system can take over driving in case of an emergency or autopilot if it allows long periods of driving. In 1996, the National Highway Traffic Safety Administration began field testing an intelligent cruise control system that can automatically adjust the vehicle's speed to maintain a safe distance from the vehicle in front of it to assess the safety impact of this technology. The more dramatic scene appeared in the drive called "Let's open your hands and let your feet go." Last summer, the National Association of Autonomous Highway Systems (NAHSC), jointly organized by the Ministry of Transport and nine other public and private organizations, demonstrated a prototype of a future fully-automated vehicle on a 12-km section of the I-15 road in Santiago. In the future, the automatic road management system will increase the supervision of traffic managers by 2-3 times at higher speeds and shorter distances. The system may also eliminate the occurrence of human-induced traffic accidents and improve road safety.In addition to providing passengers with safe and efficient transportation, the federal government expects that the inherentdevelopment trend of smart cars may also increase the economic competitiveness of the United States.In order for smart cars to reach their maximum potential, they must be able to communicate with intelligent transportation infrastructure systems and other smart cars. For example, communicating with intelligent infrastructure systems can enable smart cars to understand the occurrence of accidents and then actively choose routes in real time. . The smart car can also act as a probe and send information about the road conditions to the intelligent infrastructure system to create richer road conditions basic information. In addition, fully automated vehicles should also be able to rely, to some extent, on the guidance provided by intelligent infrastructure systems and other smart cars. For example, not long ago, the American Helicopter Association (AHS) in San Diego showed that an automatic car equipped with a magnetic sensor under a bumper was successfully guided by a 1.2 m magnet implanted under the surface of the road.In the next 5 to 10 years, we should be able to see the first generation of products with special drive information and alarm system capabilities. With the development of information these systems will be increasingly perfect. Although the anti-collision system will provide some automatic assistance, drivers still have full control of the car. In addition, because of the initial communication capabilities with the intelligentinfrastructure system, the car will be more intelligent in terms of real-time detection of road conditions.In about 10 to 15 years, the application of some improvement measures will bring us better and smarter second-generation products. Although the driver still has full control of the car, the collision avoidance system will be able to take temporary control in emergency situations. In addition, more sophisticated voice recognition systems will be incorporated into the driver's interaction with the car. Vehicles can communicate with each other to improve their anti-collision ability. Of course, communication with intelligent infrastructure systems will also be more active and effective.In about 20 years, in the third generation of products, we will be able to see fully automated road systems, integrated systems for vehicles and infrastructure, and closer interaction between drivers and cars, such as the use of visual enhancements and visual displays.Looking back at a century of flooding technology, cars stand out as a particularly dynamic invention. In the next century, this vitality will promote the development of information and computer technology. Our next challenge is to integrate new information, security and automation technologies to create people-oriented smart vehicles that improve safety, ground drive efficiency and economic competitiveness.中文译文智能车辆研究G Stark本世纪初期,在计算机和信息革命的影响下,汽车经历了性能和与驾驶者之间的互动方面最富戏剧性的变革。
汽车类论文 英汉互译

英文资料原文及中文翻译稿学院:XXXXXXXXXX专业:XXXXXXXX学生:XXXXXXXXPrevention of the abnormal wear of type measures1 ensure the tire pressureThe standard car tire pressure, determines the correct use of automobile tire performance. Proper pressure can ensure the tread and the road surface to form the largest contact surface. Insufficient air pressure of tire natural enemies. When the tire pressure is insufficient driving caused several phenomenons, often lead to malignant collision rollover accidents. (1) matrix are not optimal for maintaining the stress state of the tread surface and the ground can not form optimal contact state, in faster steering, wheel loses grip can rotate normally, and the locking, rigid sliding vehicle out of control.(2) tire deformation, fetal surface drainage ditch congestion, the water surface easy to form the tire" water " phenomenon.(3) the tire uneven stress, prolong the brake distance. (4) Tire due to structural damage and leakage collapse even burst.(5) forming a tire overloading traffic phenomena. If the wheel pressure is too low, large deformation of rolling resistance is increased, and an increase in engine power and fuel consumption. Excessive tire pressure, tire rigid becomes large, and the ground contact surface is small, tire wear speed; high pressure also easy puncture, especially when the temperature is too high. Therefore shall keep the tire pressure is in the normal range, check the tire pressure to the tire pressure gauge value as the basis, the insufficient air pressure should be added to high pressure gas, should release the excess gas and then measure the air pressure, every day before going out with Tommy bar, a long screwdriver with wooden handle moderately smooth instruments percussion tire check the tires and tire pressure or kicking the tire tread and pneumatic tire deformation of perception, and perception of hub bearing tightness on safe driving is very advantageous.2 ensure the tire temperatureTire pressure and tire temperature is compatible. When the automobile runs, sectional deformation, and the formation of deflection, the tires have internal friction, cause tire tread temperature rise, heat, the air inside the type expands when it is heated, causing the tire pressure is elevated. So that the tire more easily sidewall wear or dry.3 caring capacity and reasonableOverload driving, will increase the load of the tire, the tire ground pressure increases, and the tire's load is certain, should try to avoid overload. General car overload operation situation of truck overload is less, sometimes larger. If necessary, overload, should be controlled within 20%.A truck, in order to shipment, serious overload, such as rated load 5 tons of truck, in order to shipping overload over load to 8 tons or 10 tons of above, various tonnage limits for freight car overloads badly, for automobile tires very adverse, some automobile tire damage is overload pressure type. On straight road runs on a slightly more load on the tire less effect, in very poor road conditions to minimize overload, bumps on the road vibration is too large, and even make thegoods carriage side partial to, make car and tire impact load increased dramatically, to tire the harm is great, should reasonable loading, ensure the tire in can bear the load within a good run.4 speed normalAs the speed increases, deformation of the tire carcass of the vibration frequency, and the circumference of the tire and lateral deformation is also increased. When the vehicle speed to a certain speed, most of the energy converted into heat, so that the working temperature of tire and tire pressure increased, the tire wear intensifies. Therefore, to keep the tire recommended speed.5 peopleKeep in good condition, especially the automobile chassis technical condition is good, is to prevent tire early damage of effective measures. Keep in good condition, should make the vehicle type is subjected to a uniform weight, otherwise, each tire wear is not balanced, carrying heavy tire wear, so as to shorten the service life of the tire. As the tire is overloaded, the tire sidewall bending deformation increased and enlarge the contact area with the ground, the tire temperature rise, accelerate the shoulder wear and damage. Tire overload running, its life will be greatly reduced. Experiments show that the tire if overload 10% to 20%, type mileage will fall by 20% to40%.Therefore, the car must be in accordance with the approved loads, no overload. In addition, the car is loaded, attention should be paid to load uniform load, good are firmly fixed, avoiding the automobile in the running process of the movement of goods, causing the individual tire overload.6 ensure the tire of the regular maintenance and conversionIn order to make tires wear evenly, should periodically check the tires, and attention should be paid to automobile tire replacement, the front of the car tires than the rear tire wear relatively quickly. In a front wheel drive car, the situation is particularly evident, because the front tire must be assumed to be generated by the engine load; after a good front wheel positioning car will still appear before the tire rim wear conditions. Therefore adhere to regularly rotate the tires and achieve full vehicle tires balanced wear will greatly enhance the tire life. According to the automobile manufacturers use manual for the regular implementation of the tire rotation, also visible wear conditions. Wheel transposition method cross transposition method and cross cycle transposition method, periodic inspection car fender, wing and car cargo carriage without and tire rubbing ; always check the type nut is loose ; pay attention to check the tire and tire between any folder stone, if any should be dug in the rock and tire tread patterns debris. The rain through the muddy road tire become dirty, should be promptly cleaned. The car should not park in oil pollution on the ground, prevent the type from corrosion deterioration, and should make the spare tire to maintain normal pressure, to prepare for tire damage when replaced.7 wheel alignment and vehicle wheel dynamic balanceDetection of abnormal wear of tires have symptoms, should be timely check the front wheel positioning correctly, can use four wheel positioning or beam former ruler, protractor and other apparatus to measure the toe-in, caster and the inner angle, when necessary to be adjusted, such as the kingpin wear make angle should bereplaced .Timely check the steering rod is bent and deformed, or should be corrected or replaced, ensure that the steering function is good, camber is measurable, vehicle running stability, reducing the abrasion of types.Although the tire and wheel through the modern manufacturing process, but there are still needed to fix the internal unbalance .At the same time when the automobile is running in the process of the start and stop, turn in the slip caused by tire wear, generating wheel imbalance, the uneven wear. Lead to ride smoothly reduced comfort, when the car runs 8000 kilometers to 9000 kilometers each should be checked when the balance wheel, or as the case to check and adjust wheel dynamic balance performance, equipped with anti-skid chain wheels arranged on both sides, and shall, through the difficult section immediately after the demolition; car got stuck in the mud or deep road, should be try to avoid wheel ; summer long distance running, should be appropriate to increase the number of stops to rest, so that the tire to heat, cooling and discharging prohibited pour of buck, so as not to tire burst or other injury cold contraction.8 the road choiceMotorists should choose the relatively flat good pavement, regardless of the ability to withstand aggressive driving tires to tire life impact.When the vehicle runs normally in poor condition should pay attention to choose the road to prevent pavement stone, glass and other sharp object scrape tire or tires excessive wear, predictable in advance treatment conditions of the road as far as possible to reduce the emergency brake starting acceleration should be stable, when the automobile turns should slow down the right slow, with the bending direction of rotation, avoid sharp turning direction, in order to reduce the wear of the tire.9 good driving habitsAutomobile driving method, relates to the tire and the road surface interactions of all the stress .Incorrect or careless driving the car, will make the service life of tire dramatically shortened. Rapid acceleration, sharp braking, it will cause uneven tread wear .Without heart down and crash barrier, will be on the tire to cause harm.预防轮胎异常磨损的措施1.保证胎压标准的汽车轮胎气压,决定着汽车轮胎的正确使用性能。
- 1、下载文档前请自行甄别文档内容的完整性,平台不提供额外的编辑、内容补充、找答案等附加服务。
- 2、"仅部分预览"的文档,不可在线预览部分如存在完整性等问题,可反馈申请退款(可完整预览的文档不适用该条件!)。
- 3、如文档侵犯您的权益,请联系客服反馈,我们会尽快为您处理(人工客服工作时间:9:00-18:30)。
Automobile finance researchAbstract:The automobile industry has hundred years history in overseas oneself. The people in carefully examine, savors these 100 year historical time, often saw is the automobile industry magnificent and the wheel nationality's abundance, but has neglected in this century hundred year, billowing automobile dust behind, some unknown hero - automobile finance service station plays vital role. If did not have at that time “the carapace insect” unsolvable with Germany Volkswagenwe rk famous “five Deutsche Mark credits” emerging, does not have today “the unparalleled in the world” automobile empire and world top level German automobile industry; If does not have the Ford automobile credit company to take the lead the automobile finance service to take the impetus auto sale the release lever, standard and gets down fixedly the automobile finance service with the corporate system way, and first uses the securitization in the world the way to allow temporary credit class of the continuously fund, also does not have today automobile industry mammoth and the common people lives the convenience to be quick. In a sense, had the automobile finance service, only then had today automobile industry, today aviation industry and now weather all mechanical manufacturing industries; Also had the automobile finance service, only then had human's radius of action hundred, thousand kilometer level spanning, had the humanity to benefit in the geography space and time expands the humanities spirit sublimation which, the movement speed enhanced brings.Automobile finance researchMust understand truly the automobile industry, must first read the automobile finance; must develop the automobile industry truly, must first develop the automobile finance. Domestic and foreign historical oneself after has made clear this point. China passes for several dozens years to attempt one to leave the automobile finance continuously, the independence develops the automobile industry pathway, the result it can be imagined. Is big until now, realized only then gradually, the automobile finance is the automobile industry ox muzzle, the automobile finance starts one of important keys which the society expends.Although automobile finance expends in the finance in the overseas society,after has become continues the real estate finance the second big finance, but in China whether needs to develop also has the very great dispute. In other words, whether does the automobile finance production and develop in a disorderly way may follow?On the one hand I according to Mr. Liu Fuyuan “the national economy space and time theory”, also “national economy development phase to economical thing and economic phenomena keeping in balance with guiding function” the viewpoint embarks, “deepens and “the consumption pattern has and the change rule” the angle from the finance”, had the development national economy stage space and time characteristic to the automobile finance service to carry on the analysis, proposed “the automobile finance was th e national economy develops the financial phenomenon which under the specific stage appeared inevitably” and “the consumption pattern operating law decided the automobile finance had the development” and so on the viewpoints.On the other hand I attempt through the automobile finance service to macroscopic economical and the microscopic economical function analysis, explained the automobile finance service enhanced the automobile production, the service, the expense domain fund use efficiency, strengthened the financial service superiority, thus further emphasized the automobile finance produces rationality: The automobile finance can adjust in the national economy movement three big contradictory: “Production and expense contradiction”, “turnover of capit al contradiction”, “credit (demand) and deposit (supplies) contradiction”;The automobile finance has “the high value transferability” to the automobile industry, has “the height dependence and the catalytic nature” to the tertiary industry, has “the high placement” to the employment;The automobile finance may play “the maintenance sale system to the automobile manufacturer, the conformity sale strategy, provides the market information the role”; the automobile finance may play to the car dealer “provide s goods in stock financing”, “transport business fund allows temporary credit”, “equipment financing” the role;The automobile finance may play to the automobile user “provides the expense credit”, “rents financing”, “service financing”, “the insurance business”the role;In brief, “the automobile finance can consummate socialized, the marketability financial service system”.Under the above analysis premise, I place the research and the writing key point the automobile finance concrete operation flow in several key questions, argues vigorously establishes a relative consummation the structure system.Because at present in domestic, but also does not have one special to discuss with the literature, even is one has the depth paper, studies the automobile finance question, I only then “look for a needle in a haystack”, seeks some fragmentarily, the dispersible material from the overseas university development facility and in the automobile finance service website.The innovation aspect, belongs in the rese arch area “runs the horse stable place”, the basically entire structure is new, but also is preliminary. According to “automobile finance historical development - - research system foundation; Automobile finance profit pattern - research system core; Automobile finance credit administration - - research system inner layer; Automobile finance financing mechanism - - research system outer layer: Automobile finance product development - research system surface layer” the order launches; In the research techniq ue, has mainly used “the comparison research” the method, in the Western economic, the finance study, the insurance study, the service management science, the financial engineering, consumer economics domain extensive cultivation and so on the marketing study, compatible and gathers, uses these theories to explain diligently the automobile finance the related question, and has formed some new viewpoints, mainly has “the automobile finance increment profit pattern” in the concrete content, “the credit reimburses ability management”, “the automobile finance multi-dimensional financing structure”, “the automobile finance financial product development”, “the automobile finance product achievements marketing” and so on.First, understands the automobile finance “the development history”.Has analyzed the automobile finance service company's general evolution history process and the current several kind of main existence form, including “bigautomobile manufacture enterprise attached”, “big bank financial group attached”, “independent type”; Has analyzed the automobile finance service company newly “the compound superiority”; Also analyzed “the economical globalization” in the process the automobile finance service to start to appear “the multi-dimensional strate gy”, “the deepened strategy” and “the hypothesized service” the trend of development.Specially has also analyzed the Chinese automobile finance special development experience and the advantages in this foundation. According to “the modern effective marke t hypothesis”, has analyzed “the interest rate control” in the situation, the Chinese automobile money market non-validity, has drawn some basic conclusions: Induces and the start huge individual deposit with the automobile finance service, supports the national economy high speed to grow continually: The automobile finance service is helpful “the automobile expends the leading” in the establishment the market pattern; The automobile finance service is helpful to the elimination “the automobile demand growt h regional characteristic incline” the question; The automobile finance service is helpful in the display uses the Chinese automobile storage quantity property. Also to develop the automobile finance service existence “the human vehicle to be contradictory”, “the road vehicle is contradictory” and so on the main restriction factor to carry on the appraisal, proposed specially: The automobile finance can “the creation supplies”, be the science solution above question “the key”.After the understanding automobile finance service historical present situation, has then analyzed the automobile finance service existence “the origin of life” - - the profit pattern. This also is further is proving the automobile finance existence “the rationality” the question.After the introduction automobile finance profit pattern basic meaning, I divide into it “the basic profit pattern” and “the increment profit pattern” two kinds, and from “service management theory”, “financial service theory” the angle, proved the automobil e finance service profit pattern “not to be possible to know touches the nature”, “the indivisibility”, “the different principle” and so on the characteristics, proposed “the automobile finance service profit pattern core factor was the customer loyal degr ee of satisfaction”, “the automobile finance serviceprofit pattern secondary factor is the automobile finance service transmission quality”. Also to “the market concentration degree”, “the market entered the barrier”, “the market mechanism” and so on the market parameters has carried on the description.I the Western economic “the market analysis” the theory introduction, will also analyze and obtain “the perfect competitive market to the automobile finance service profit pattern non-serviceability”, “hav e monopolized the market completely to the automobile finance service profit pattern non-serviceability”, “the monopoly struggled the market mechanism unexpectedly to the automobile finance service profit pattern serviceability”, “the oligopoly market to t he automobile finance service profit pattern serviceability” the conclusion, and has specifically analyzed under each kind of market condition, automobile finance service profit pattern running status.In this part, my another new viewpoint is, proved the automobile finance service to rise in value fully the profit pattern necessity, the concrete method, the fund composition, the investment principle, the investment portfolio. Also introduced I apply the investment bank fundamental research development one kind of typical automobile finance service to raise in value the profit pattern - “to buy the vehicle to manage finances the profit pattern”.If the automobile finance service profit pattern is a core, then the credit administration is controls this patt ern the key. After inspects “the credit theory”, “the consumer credit theory” these theory origin, has emphatically analyzed the automobile finance service credit system function and the automobile finance service credit system specific connotation and the category, emphasized the key point is eliminates the automobile finance the information dissymmetry, according to credit rank decision financing quantity and deadline. Also “paid (deposit) toself-to restrain the mechanism”, “the joint and several liability mechanism”, “the credit system mechanism” and so on the automobile finance service credit operations machine has manufactured the description, has established the measure automobile finance service individual loan risk and the automobile finance reimburses ability management the essential method, and established the automobile finance service credit system on our country to propose thecountermeasure.The automobile finance service financing structure plays is gathering accepts the fund the role, is the support, the guarantee automobile finance profit pattern display function “the power” .It both automobile finance profit pattern control, and reaction in automobile finance profit pattern, therefore, met down has conducted the research to it. The automobile finance service company finances the structure rationale to have “the financial capital to say”, “the banking capital circulation said”, and “the transaction expense said”. The automobile finance service financing history process has experienced “endogen financing”, “extraneous source financing” and “highly effective in extraneous source financing”. Has analyzed the automobile finance service company's financing structural model and the automobile finance service company best financing structure function, as well as the influence automobile finance Service Company finances the structure primary factor. Also with emphasis introduced the automobile finance service company's several kind of main financing form, specially introduced in the automobile finance credit property securitization financing form, in the automobile finance service intangible asset capitalization financing strategy, in the automobile finance service special permission management financing strategy, in the automobile finance service project financing strategy, the automobile finance service level border financing strategy.The automobile finance service product development sells the camp is the entire system final link, it realizes the automobile finance profit pattern tool, is the automobile finance credit administration carrier, is the automobile finance financing mechanism operation goal.The automobile finance service product makes a general reference thought the automobile transaction and the use allows temporary credit the financial structure which the fund carries on (quantity, deadline, cost and so on), the financial strategy design and the corresponding legal contract arrangement, is each kind of question solution which in the reality the automobile finance service station faces, including encompassment price optimization aspect automobile finance product; Encompassment circumvention sale policy, system development automobile finance product: Revolves the automobile expends in the process to have servicelink convenience, efficient and indemnificatory development automobile finance product. The automobile finance service product characteristic by took the general use commodity the automobile and decided as the financial service contractual relationship two big factors: Has “compound”, “the accuracy”, “the risk”, “the continuous nature”, “the selectivity” and so on;The automobile finance product design is in the finance study is most difficult one of richest challenging topics. It is the automobile finance analysis inverse problem. Automobile finance product design general flow, including “goal design”, “structural design”, “product fixed price”, “risk income characteristic analysis”, “product standardization”. The automobile finance product benefit appraised the method includes: “Profit margin discount law”, “information feedback law”.The automobile finance product development innovation is the China monetary system reform intrinsic request, the interest rate marketability, is develops the Chinese automobile finance product core and the key.Had the automobile finance service product, but also must open “the direct marketing channel”, “the straight multiple marketing channel”, “on the net the marketing”, carries on “the potency to the automobile finance product sale personnel to dr ive”, and to “the potency drove” has carried on the model description.The analysis opens the Chinese automobile finance service market existence “the merger and acquisition conformity”, “the market reorganization” and so on the tendencies, proposed carries out Chinese Silver Jail to meet the spirit, the perfect automobile finance service company governs the structure, the use “the independent pattern”, “the union pattern”, “the Chinese-foreign joint venture pattern”, establishes the Chinese specialized au tomobile finance service organization, impels the automobile finance service industry moderately to grow in advance, promotes our country automobile industry, the financial service industry overall competitive power.文献来源:/Article/Automotive/index.html汽车金融研究摘要:汽车工业在国外己有百年历史。