数控铣床基本操作
数控铣床操作说明书
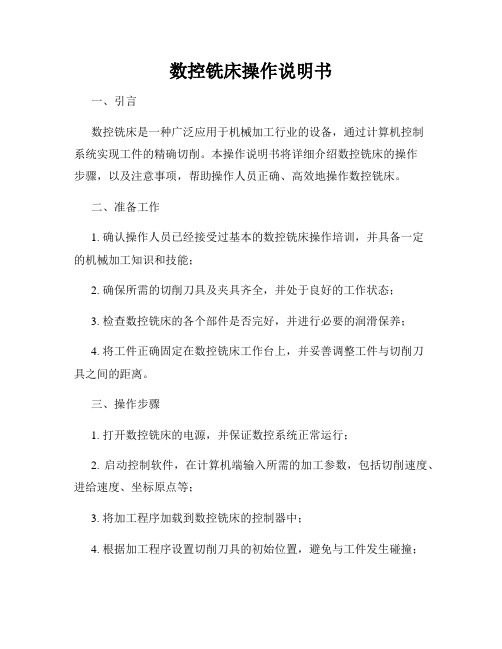
数控铣床操作说明书一、引言数控铣床是一种广泛应用于机械加工行业的设备,通过计算机控制系统实现工件的精确切削。
本操作说明书将详细介绍数控铣床的操作步骤,以及注意事项,帮助操作人员正确、高效地操作数控铣床。
二、准备工作1. 确认操作人员已经接受过基本的数控铣床操作培训,并具备一定的机械加工知识和技能;2. 确保所需的切削刀具及夹具齐全,并处于良好的工作状态;3. 检查数控铣床的各个部件是否完好,并进行必要的润滑保养;4. 将工件正确固定在数控铣床工作台上,并妥善调整工件与切削刀具之间的距离。
三、操作步骤1. 打开数控铣床的电源,并保证数控系统正常运行;2. 启动控制软件,在计算机端输入所需的加工参数,包括切削速度、进给速度、坐标原点等;3. 将加工程序加载到数控铣床的控制器中;4. 根据加工程序设置切削刀具的初始位置,避免与工件发生碰撞;5. 按照加工程序的要求,设置数控铣床的自动运行模式或手动运行模式;6. 在运行之前,请确保操作人员迅速离开数控铣床的操作区域,确保人员的安全;7. 启动数控铣床,开始加工工件;8. 在加工过程中,操作人员需要密切关注加工状态,并根据需要进行相应的调整;9. 加工完成后,关闭数控铣床并断开电源。
四、注意事项1. 操作人员在操作数控铣床前必须穿戴好防护设备,包括工作服、安全帽等;2. 禁止在操作过程中随意触碰数控铣床的运动部件,以免造成伤害;3. 严禁在数控铣床运行时拔插电源或进行其他干扰操作,以免影响设备的工作稳定性;4. 操作人员应定期检查数控铣床的润滑系统,并及时补充润滑油;5. 若发现数控铣床有任何异常情况或故障,应立即停止操作,并及时通知维修人员进行检修;6. 对于加工后的废料和切屑,应及时清理,避免影响下一次操作。
五、操作安全1. 操作人员必须经过正规培训,并持有相关操作证书;2. 操作人员应按照正确的操作流程进行操作,严禁违规操作;3. 在操作过程中,应保持集中注意力,切勿分心;4. 严禁在操作过程中穿戴松散的衣物或配饰;5. 禁止未经授权的人员接触数控铣床。
数控铣床基本操作资料

模块一数控铣床基本操作实训课题1 功能键的使用图1-1MDI面板图1-2机械面板MDI面板各个功能键的作用如表1-1:名称详细说明复位键 REST按下这个键可以使CNC复位或者取消报警帮助键 HELP 当对MDI键的操作不明白时,按下这个键可以获得帮助(帮助功能)软键画面转换软键用来转换画面根据不同的画面,其它软键有不同的功能。
软键功能显示在屏幕的底端。
地址和数字键 N、4←按下这些键可以输入字母,数字或者其它字符。
切换键 SHIFT在该键盘上,有些键具有两个功能。
按下<SHIFT>键可以在这两个功能之间进行切换。
当一个键右下脚的字母可被输入时,就会输入键 INPUT 当按下一个字母键或者数字键时,再按该键数据被输入到缓冲区,并且显示在屏幕上。
要将输入缓冲区的数据拷贝到偏置寄存器中等到,按下INPUT键。
这个键与软键中的[INPUT]键是等效的。
取消键 CAN 按下这个键删除最后一个进入输入缓冲区的字符或符号。
当键输入缓冲区后显示为:>N001X100Z_当按下CAN键时,Z被取消并且显示如下:>N001X100_ 程序编辑键ALT、INSERT、DELETE按下如下键进行程序编辑:ALTER:替换、INSERT:插入、DELETE:删除功能键POS、PROG按下这些键,切换不同功能的显示屏幕。
光标移动键有四种不同的光标移动键。
→:这个键用于将光标向右或者向前移动。
光标以小的单位向前移动。
←:这个键用于将光标向左或者往回移动。
光标以小的单位往回移动。
↓:这个键用于将光标向下或者向前移动。
光标以大的单位向前移动。
↑:这个键用于将光标向上或者往回移动。
光标以大的单位往回移动。
翻页键用于将屏幕显示的页面向下翻页。
用于将屏幕显示的页面往回翻页。
表1-1MDI面板功能键的作用机械面板各个功能键的作用如表1-2::按键、旋钮详细说明急停按钮:紧急情况下按下开关机床停止一切运动。
快速/手轮倍率按键:确定快进时机床运动速度倍率,分别为默认速度的1%、25%、50%、100%。
数控铣床的基本操作方法
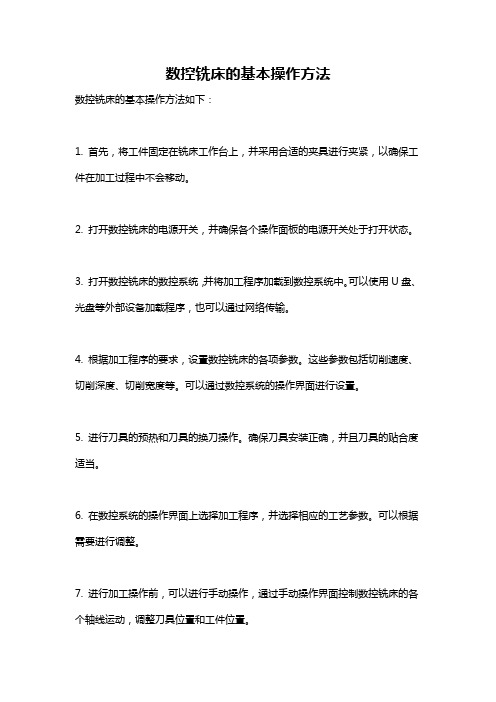
数控铣床的基本操作方法
数控铣床的基本操作方法如下:
1. 首先,将工件固定在铣床工作台上,并采用合适的夹具进行夹紧,以确保工件在加工过程中不会移动。
2. 打开数控铣床的电源开关,并确保各个操作面板的电源开关处于打开状态。
3. 打开数控铣床的数控系统,并将加工程序加载到数控系统中。
可以使用U盘、光盘等外部设备加载程序,也可以通过网络传输。
4. 根据加工程序的要求,设置数控铣床的各项参数。
这些参数包括切削速度、切削深度、切削宽度等。
可以通过数控系统的操作界面进行设置。
5. 进行刀具的预热和刀具的换刀操作。
确保刀具安装正确,并且刀具的贴合度适当。
6. 在数控系统的操作界面上选择加工程序,并选择相应的工艺参数。
可以根据需要进行调整。
7. 进行加工操作前,可以进行手动操作,通过手动操作界面控制数控铣床的各个轴线运动,调整刀具位置和工件位置。
8. 根据加工程序的要求,选择合适的加工模式,可以选择单段加工、连续加工、循环加工等。
9. 开始加工操作,在数控系统的操作界面上点击开始按钮,数控铣床将按照加工程序的要求进行加工操作。
10. 监控加工过程,注意观察加工质量和加工速度,及时调整加工参数和刀具。
11. 加工完成后,关闭数控铣床的电源开关,并进行必要的清理和维护工作。
以上就是数控铣床的基本操作方法,具体的操作流程还需要根据不同的数控铣床型号和加工要求进行调整。
在实际操作中,还需要注意安全事项,并严格按照相关操作规程进行操作。
数控铣床的基本操作(三菱西门子802S系统)

数控铳床的基本操作(三菱西门子802S系统)
项目一
项目一
项目名称 安全规范与机床面板的基本操作 学习时间
20课时 子项目名称 SIEMENS 系统面板的基本操作
学习时间 5课时 任务1开机与回零
操作步骤:第一步,打开墙壁上总开关f 第二步,床身后方的机床开关f 第三步,系统面板旁(上)的系统开关一第四步急停开f 第五步观察各轴是否有足够的运动距离f 第六步(各轴有足够的运动距离条件下)X 、Y 、Z 各轴回零。
回零操作步骤:比如X 回零(其它轴类同),第一步,在回零模式T 第二步,按X+方向不放,直到回零指示灯灯亮。
任务2刀补与对刀参数的填入数控系统
参数
一第二步,按&匚卜软键;一 新刀具 - —
第四步,按.I —3,软键第五步,输
100代表铳刀;一
输刀补操作步骤: 搜索
学习内容 新建刀具
:回
操作步骤:第一步,按W 1键;
第一步, 回
按三
参数 第二步,按等匚)软键;一
第三步,按甘一⅛⅜;f
项目一
4、余料的分析与编程
(只作参考)
分析图纸,能够确定刀具直径选12mm,先确定走刀路线,下列的走刀路线,在CAD 软件中,能够看到余料有三块,解决办法1-2-3与5f6两个走刀路线能够把余料去
除(另一个余料用走直线去除):
44.50
学习内容。
数控铣床使用方法说明书
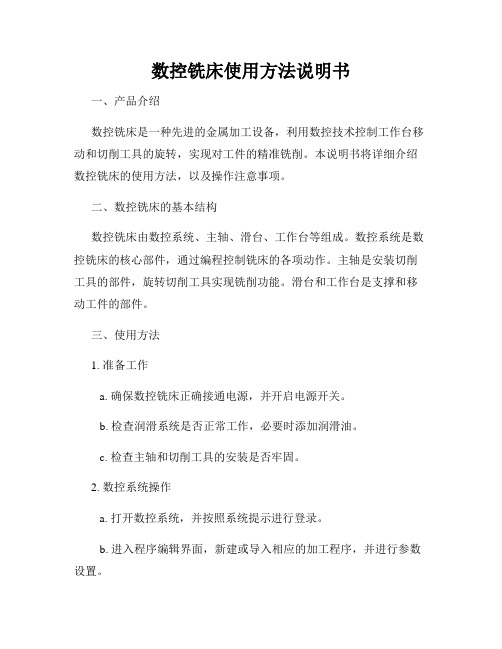
数控铣床使用方法说明书一、产品介绍数控铣床是一种先进的金属加工设备,利用数控技术控制工作台移动和切削工具的旋转,实现对工件的精准铣削。
本说明书将详细介绍数控铣床的使用方法,以及操作注意事项。
二、数控铣床的基本结构数控铣床由数控系统、主轴、滑台、工作台等组成。
数控系统是数控铣床的核心部件,通过编程控制铣床的各项动作。
主轴是安装切削工具的部件,旋转切削工具实现铣削功能。
滑台和工作台是支撑和移动工件的部件。
三、使用方法1. 准备工作a. 确保数控铣床正确接通电源,并开启电源开关。
b. 检查润滑系统是否正常工作,必要时添加润滑油。
c. 检查主轴和切削工具的安装是否牢固。
2. 数控系统操作a. 打开数控系统,并按照系统提示进行登录。
b. 进入程序编辑界面,新建或导入相应的加工程序,并进行参数设置。
c. 根据工件要求,在程序编辑界面编写数控加工程序,包括工件轮廓、加工路径、切削深度等。
d. 编写完成后进行程序的校验和修正,确保程序正确无误。
3. 夹紧工件a. 确保工作台平整、清洁,清除任何杂质和障碍物。
b. 将工件放置在工作台上,并使用夹具将其牢固夹紧,保证工件不会移动或晃动。
4. 工艺参数设置a. 根据工件材料、切削工具类型和加工要求,设置合适的切削速度、进给速度和切削深度。
b. 根据工件形状和加工路径,设置合适的坐标系和坐标原点。
5. 开始加工a. 校对工件坐标系和坐标原点的准确性,确保工件与切削工具的相对位置正确。
b. 启动数控系统,并按照程序加工工序的顺序逐步进行铣削操作。
c. 观察加工过程中的切削情况,如有异常情况及时停机检查。
6. 加工后处理a. 加工完成后,关闭数控系统,并断开电源。
b. 清理加工区域,清除切屑和废料,并对数控铣床进行日常维护和保养。
四、操作注意事项1. 在操作数控铣床之前,应仔细阅读并理解本说明书,并接受相关培训。
2. 在操作过程中,应佩戴适当的个人防护装备,如工作服、安全帽、护目镜等。
数控铣床基本操作 (1)
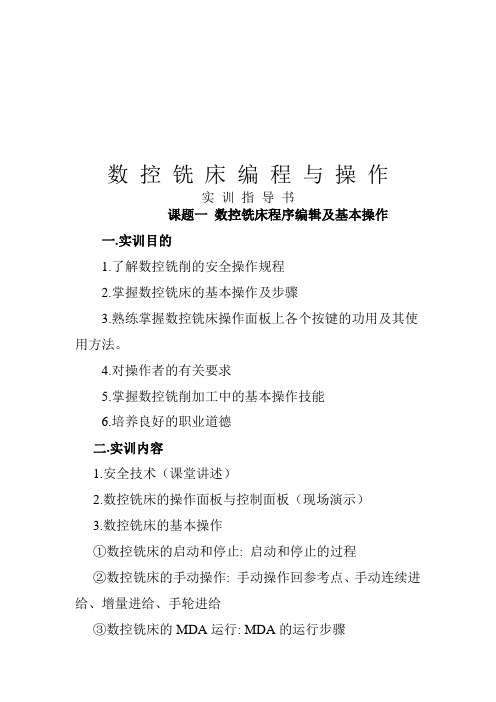
数控铣床编程与操作实训指导书课题一数控铣床程序编辑及基本操作一.实训目的1.了解数控铣削的安全操作规程2.掌握数控铣床的基本操作及步骤3.熟练掌握数控铣床操作面板上各个按键的功用及其使用方法。
4.对操作者的有关要求5.掌握数控铣削加工中的基本操作技能6.培养良好的职业道德二.实训内容1.安全技术(课堂讲述)2.数控铣床的操作面板与控制面板(现场演示)3.数控铣床的基本操作①数控铣床的启动和停止: 启动和停止的过程②数控铣床的手动操作: 手动操作回参考点、手动连续进给、增量进给、手轮进给③数控铣床的MDA运行: MDA的运行步骤④数控铣床的程序和管理⑤加工程序的输入练习三.实训设备1.GSK928数控铣床8台、GSK980数控铣床6台四.实训步骤1.开机、关机、急停、复位、回机床参考点、超程解除操作步.⑴机床的启动(2)关机操作步骤(3)回零(ZERO)(4)急停、复位(5)超程解除步骤2.手动操作步骤(1)点动操作(2)增量进给(3)手摇进给(4)手动数据输入MDA操作(5)对刀操作(现场演示)3.程序编辑(1)编辑新程序(2)选择已编辑程序4.程序运行(1)程序模拟运行(2)程序的单段运行(3)程序自动运行5.数据设置(1)刀偏数据设置(2)刀补数据设置(3)零点偏置数据设定(4)显示设置(5)工作图形显示五.注意事项1.操作数控铣床时应确保安全。
包括人身和设备的安全2.禁止多人同时操作机床3.禁止让机床在同一方向连续“超程”六.实训思考题1.简述数控铣床的安全操作规程.2.机床回零的主要作用是什么?3.机床的开启、运行、停止有那些注意事项?4.写出对刀操作的详细步骤。
七.实训报告要求实训报告实际上就是实训的总结。
对所学的知识、所接触的机床、所操作的内容加以归纳、总结、提高。
1.实训目的2.实训设备3.实训内容4.分析总结在数控铣床上进行启动、停止、手动操作、程序的编辑和管理及MDI运行的步骤。
第二节数控铣床加工中心的基本操作
向,待转动主轴一周时百分表的指针基本上停止在同 一个位置,其指针的跳动量在允许的对刀误差范围内,
这时可以认定主轴的中心就是X、Y轴的原点。
第二章 数控铣床/加工中心的操作
图2-10 采用百分表对刀
第二章 数控铣床/加工中心的操作
5)对刀仪对刀法 在加工中心上加工零件,由于加工内容较多往往 需要更换多把刀具,为了提高机床的使用效率,通常 操作者在机床上通过各种方法获得一把标准刀具参数 后,利用专业对刀设备来获取其他刀具和标准刀具的 直径和长度差值,然后经过计算,把每把刀的数据参 数输入到系统中,这种对刀的方法称为机外对刀法, 也称为对刀仪对刀法。
断刀具与对刀仪是否接触,对刀精度一般可达0.005mm。Z向
对刀仪带有磁性表座,可以牢固地附着在工件或夹具上,其
高度一般为50mm或100mm。图2-11所示为指针式Z向对刀仪。
第二章 数控铣床/加工中心的操作
图2-11 指针式Z向对刀仪
第二章 数控铣床/加工中心的操作
3.建立工件坐标系
(1)用G92指令建立工件坐标系 G92指令在编程时放在程序的第一行,程序在运行 G92指令时并不产生任何动作,只是根据G92后面的坐 标值在相应的位置建立了一个工件坐标系。 格式:G92 X Y Z ; 式中 G92── 表示工件坐标系设定指令; X、Y、Z ──为刀具当前位置相对于设定的工件 坐标系的坐标值。
(2)在系统面板上,按下 按钮,CRT显示器的 左上角显示“程式(MDI)”的字样,
(3)输入要运行的程序段。 (4)按下机床操作面板上的循环启动 按钮, 系统自动执行该程序段。
第二章 数控铣床/加工中心的操作
四、对刀操作
数控铣床基本操作
数控铣床基本操作数控铣床是目前工业生产中普遍使用的金属加工设备,通过预先编写好的程序指挥电脑控制铣刀沿着特定路径进行切削加工。
其加工精度高,效率大大提升。
本文将介绍数控铣床的基本操作步骤。
一、开机将控制台上的开关置于“ON”位置,等待主轴及其他机床部件启动,通常需要等待一段时间才能操作。
二、件零界面打开相应的加工程序,进入件零界面,确认操作台上的工件夹紧装置已夹紧工件。
三、刀具预备按照预定的加工程序选择刀具,安装到刀柄上。
选择合适的工具后,进行零点预置操作。
将工具插入卡格内,对其重新设定零点。
四、各轴回归将控制台上的轴选钮选择所需要进行调整的轴,使用手柄调节轴的位置,对其进行回归。
五、调整坐标通过控制面板上的编辑坐标功能,来进行坐标系轴向的调整。
将坐标值调整到指定数值。
六、手动操作有时需要进行手动操作,以进行协调调整或测试加工效果等。
在此情况下,可以选择手动操作模式,执行加工程序完成拟定的操作步骤。
七、编写加工程序数控铣床加工的特点之一是事先编写好加工程序,使用G、M 代码来控制不同的操作。
在程序中,需要定义加工刀具、加工轨迹等。
确保加工程序的准确性。
八、调整加工预设参数各厂家的数控铣床提供各种加工预设参数,如加速度、速度减缓度等。
在安装和初次使用时,需要根据具体情况进行调整。
九、加工操作通过控制台上的操作按钮完成加工操作。
控制台上通常分为一些卡片,每个卡片制定了不同的加工操作,例如:(1)设置刀具、确定加工序列过程(2)定位物料槽,并且确定工具运行方式(3)协调原点,设置其轴向(4)切割操作,根据指定参数进行切割(5)程序结束,进行刀器装夹和保养等操作。
十、维护保养保持设备的良好工作状态和正确的维护是提高设备运行的关键。
经常进行机床维护保养,如清洁工作、润滑、检查机床部件是否正常等。
总之,数控铣床的基本操作,需要熟练掌握其配置参数、程式的编写、刀具和工件安装、加工操作等方面的操作。
正确机把工程降低因疏忽和偏差带来的损失,提高运转效率。
数控铣床(加工中心)基本操作
数控铣床(加工中心)基本操作教学目的:1.熟悉数控铣床(加工中心)仿真软件的各功能键的含义2.掌握数控铣床(加工中心)仿真软件的基本操作重点: 数控铣床(加工中心)仿真软件的各功能键的含义;数控铣床(加工中心)仿真软件的基本操作难点: 数控铣床(加工中心)仿真软件的各功能键的含义;数控铣床(加工中心)仿真软件的基本操作一、旧课复习1、什么是机床坐标系、工件坐标系、机床零点、工件原点?2、单一固定循环有几种方式?3、外径、内径粗车循环指令G71有何特点?二、新课的教学内容(一)数控铣床(加工中心)仿真软件系统的进入与退出1、进入数控铣床(加工中心)仿真软件打开电脑,双击VNUC 图标,则进入VNUC仿真系统,屏幕显示下图10-1所示。
单击上方菜单里“选项”选择机床与系统,选择三轴立铣或者加工中心,再选华中世纪星数控铣仿真,即进入华中世纪星数控铣仿真操作。
2、退出数控铣床仿真软件单击屏幕右上方的菜单“文件”,选择“退出”则退出数控铣仿真系统。
(二)数控铣床仿真软件的工作窗口数控铣仿真软件工作窗口分为: 菜单区、工具栏区、机床显示区机床操作面板区、数控系统操作区。
1.菜单区菜单区包含:文件、显示、工艺流程、工具、选项、教学管理、帮助六大菜单。
图10-1 华中世纪星数控铣机床操作面板2.工具栏区图10-2 华中世纪星数控铣机床工具栏区3.常用工具条说明(1)设定刀具(如图10-3所示):输入刀具号→输入刀具名称→可选择端铣刀、球头刀、圆角刀、钻头、镗刀→可定义直径、刀杆长度、转速、进给率→选确定,即可添加到刀具管理库。
(2)添加到主轴(如图10-3所示):在刀具数据库里选择所需刀具,如02刀→按住鼠标左键拉蓝机床刀库上→点安装→再点确定则添加到刀架上图10-3 刀具库添加(3)设定毛坯点击图标,则弹出图10-4,点击新毛坯,出现10-5所示。
图10-4 新毛坯的建立设置毛坯大小、材料、夹具。
图10-5 设置毛坯的尺寸设置压板的形式图10-6 设置压板的形式(4)工件测量:图10-7 工件测量(三)数控铣床仿真软件基本操作在图10-1 所示的右边是数控系统操作键盘,其上面为数控系统显示屏1.编辑键:替代键。
数控铣床基本操作
数控铣床基本操作数控铣床(加工中心)是一种精密的金属加工设备,能够在坐标控制下进行复杂的切削加工操作。
它广泛应用于航空、航天、汽车、船舶、电子、仪器仪表等行业。
下面将详细介绍数控铣床(加工中心)的基本操作。
基本操作包括机床的开机、关机、准备工作、程序的输入、加工工件等。
一、开机准备1.确保数控铣床接上电源并连接好地线,检查电器接线是否良好。
2.打开电源总开关,并按下电源控制柜上的运行按钮。
3.检查机床装置是否处于安全状态,无任何异物。
4.打开电脑主机,并启动数控铣床的控制软件。
5.检查机床的润滑系统是否正常运转,如有异常及时处理。
6.调整机床工作台的位置和速度。
7.检查机床的刀具和夹具是否装好,夹紧工件。
二、程序输入1.启动控制软件,并登录数控铣床控制系统。
3.输入起刀点坐标和刀具调用号。
4.输入切削速度、进给速度和进给量。
5.对工件进行零点的设定与输入。
6.编写加工程序,根据要求输入倒角、孔宽底、加工轮廓等。
7.检查程序的正确性和完整性,如有错误及时修改。
8.保存程序并传输给机床的控制系统。
三、加工操作1.将刀具移到加工起点,按下开始按钮,开始加工。
2.监控加工过程,定期检查刀具磨损情况。
3.如需停止加工,按下停止按钮,将刀具移离工件。
4.加工完毕后,关闭机床的主轴和润滑系统,将刀具安全移入刀具库。
5.关闭控制软件,登出数控铣床的控制系统。
6.除去切屑和清洁工件及机床。
7.关闭机床电源总开关。
四、安全注意事项1.在进行加工操作前,应确保刀具和夹具装好,并严格按照程序设定进行操作。
2.避免手指接近切削区域,以免发生意外伤害。
3.加工中应注意工件和夹具的稳定,防止工件移动或夹具松动。
4.检查润滑系统,确保机床运行平稳。
5.注意安全操作规范,按要求佩戴防护设备。
总结数控铣床(加工中心)的基本操作涉及到开机准备、程序输入和加工操作三个方面。
在进行加工操作时,需要严格按照安全操作规范进行,并定期检查机床和刀具的状况。
- 1、下载文档前请自行甄别文档内容的完整性,平台不提供额外的编辑、内容补充、找答案等附加服务。
- 2、"仅部分预览"的文档,不可在线预览部分如存在完整性等问题,可反馈申请退款(可完整预览的文档不适用该条件!)。
- 3、如文档侵犯您的权益,请联系客服反馈,我们会尽快为您处理(人工客服工作时间:9:00-18:30)。
数控铳床基本操作【学习目标】① 了解数控铳床指令。
② 了解数控铳床组成。
③ 了解数控铳床的特点。
④ 了解数控铳床的应用场合。
⑤了解数控铳床的加工围。
【知识学习】」、简单编程指令应用1 . GOO G01例9-1 如图9-1所示,进给速度设为 F=100mm/min, S=800r/min,其程序如下:00721 ;YN10 G90 G54 G00 X20 Y20;GO1N20 S800M03;50-! °N30G01 Y50 F100;-■ |LSN40 X50;...丄1N50 N60 Y 20;X20;G01N70G00 X0 Y0 M05;2050N80 M30;2 . G02、G03 —圆弧插补指令图9-1直线插补G02 ( G03 )指令使刀具按圆弧加工,G02指令刀具相对工件按顺时针方向加工圆弧,是顺圆弧插补指令,反之 G03指令使刀具逆时针方向加工圆弧,是逆圆弧插补指令。
其中:X 、Y 、Z 表示圆弧终点坐标;I 、J 表示圆弧中心相对圆弧起点的坐标值; R 表示圆弧半径,若圆弧w 180。
,则R 为正值; 的进给速度, 它是刀具轨迹切线方向的进给速度。
例9-2对如图9-2 的图形编程方法一: :用 I 、J 编程G90 G00 X42X32 ;G02 X30 Y20J-12F200 ;G03X10I-10方法二: :用 R 编程G90 G00 X42 X32 ;G02 X30 Y20 k-12 F200 ;G03X10k10 ;3. G90 —— 绝对坐标指令,G91 ―― 相对坐标指令。
G90、 G91 表示运动轴的移动方式。
使用若圆〉180。
,贝U R 为负值;F 是圆弧插补绝对坐标指令(G90),程序中的位移量用刀具图 9-3 G90、G91 指的终点坐标表示。
相对坐标指令(G91 )用刀具运动的增量表示。
如图 9-3所示,表示刀具从A 点到B 点的移动,用以上两种方式的编程分别如下:G90 G00 X80 Y150 G91G00X-120Y90这两种编程方式在程序中可以混用,编程员应根据实际情况灵活选用,加快编程速度, 提高程序可靠性。
二、工件坐标系的建立1. G92 --设置加工坐标系格式:G92 X 〜Y 〜Z 〜G92指令是将加工原点设定在相对于刀具起始点的某一空间点上。
例7-3 如图9-4所示,先将刀具移至欲设工件坐标系的上方 100mm 处,执行下列程序,把工件坐标系设在商表面处。
G92 X0 Y0 Z100; G90 G00 X_ Y_;2 . G53 --选择机床坐标系 格式:G53 G90 X 〜 Y 〜Z 〜;G53指令使刀具快速定位到机床坐标系中的 指定位置上,式中X 、丫、Z 后的值为机床坐标系中 的坐标值,其尺寸均为负值。
如 G53 G90 X-100 Y-100 Z-20 则执行后刀具在机床坐标系中的位置如图 示。
3. G54、G55、G56、G57、G58、G59 选择 1 〜 6号工件坐标系格式:G54 G90 G00 (G01) X 〜 Y 〜Z 〜(F 〜)该指令执行后,所有坐标值指定的坐标尺寸都是选定的工件加工坐标系中的位置。
工件坐标系皆以机床原点为参考点,分别以各自与机床原点的偏移量表示,需提前通过 CRT/MDI 方式输入机床部。
这些坐标系存储在机 床存贮器,在机床关机时仍然存在。
例9-4 在图9-6中,用 CRT/MDI 在参数 设置方式下设置了两个加工坐标系:G54 : X-50 Y-50 Z-10N10 G53 G90 X0 Y0 Z0图9-6工件坐标系N20G54G90G01 X50Y0 Z0F100N30 G55G90 G01X100 Y0 Z0 F100则刀尖点的运动轨迹如图7-10 中0AB 所示。
的G55加工坐标系。
若执行下述程序段:G55 : X-100Y-100Z-20这时,建立了原点在 0'的G54加工坐标系和 原点在0〃9-5所图9-5 G53选择机床坐标系的。
G92指令是通过程序来设定、选用加工坐标系的,它所设定的加工坐标系原点与当前 刀具所在的位置有关,这一加工原点在机床坐标系中的位置是随当前刀具位置的不同而改变 的。
G54〜G59指令是通过 MDI 在设置参数方式下设定工件加工坐标系的,一旦设定,加工原点在机床坐标系中的位置是不变的, 它与刀具的当前位置无关,除非再通过MDI 方式修改。
G92指令后虽有坐标值,但不产生轴的移动。
若G54~G59 指令后有坐标值,轴将会移动到目的点。
G92设定的坐标系在系统断电后, 基准点将消失,下一次使用需重新设定。
G54~G59设定的坐标系无论电源关断否,都存在于系统存中,每一次直接调用即可。
四、刀具半径补偿G41、G42 ――刀具半径补偿指令 G40 ――刀具半径补偿取消指令。
如用半径为 R 的刀具加工工件外形轮廓时如图9-8所示,刀具中心必须沿着与轮廓偏离 R 距离的轨道移动。
刀具半径补偿计算就是根据轮廓和刀具半径 R 值计算出刀具中心轨迹,数据机床中的数控装置能 自动根据R 值算出刀心轨迹,并按刀心轨迹运动,这 就是数控系统的刀具半径自动补偿功能。
G41 ――左刀偏指令,即顺着刀具前进方向看,刀具在工件的左边。
G42 ――右刀偏指令,即顺着刀具前进方向看,刀具在工件的右边如图9-9所示。
当G41或G42程序段完成后,用 G40消去偏置值,使刀具中心与编程轨迹重合。
G42例9-5 N10 N20 N30 如图9-7所示,对于 GOO G90 G53; X226.05 Y253.96; X341.85 Y253.96; X341.85 Y186.76;A 、B 、C 的定位程序如下: A 孔定位 B 孔定位 C 孔定位N40从上面的程序可以看出,由于选择了机床零点 作为编程零点,使程序计算工作量很大,且零件中 的尺寸和编程尺寸完全不同,给检查带来了很大的 不便。
这时若采用工件坐标系,选择O i 点作为工件 坐标系G54的零点,则偏置尺寸为 X-278.35 , Y-186.76 ,这样程序就会大大简化,其程序如下:N10 GOO G90 G54; N20 X-52.3 Y67.2; N30 X63.5 Y76.2; N40 X63.5Y0;4 . G92 与 G54 〜G59 G92指令与G54〜G59图9-7工件坐标系A 孔定位B 孔定位C 孔定位 的区别指令都是用于设定工件加工坐标系的,但在使用中是有区别(M7'G401格式:斗 (/[S(Ml皿|[側 XY ZD|GOI | ----- -ZJ 貝F 进万向沿rt 迸万图9-9刀具的补偿方向说明:X 、Y 、Z :建立刀具半径补偿运动的始点。
D ――偏置号,D 后是多位自然数,每个偏置号都是存地址,在这些地址中存放 刀具半径值。
D00地址中的值永远是零。
刀具半径补偿的建立,只能在 G00或G01方式下完成,一旦建立了刀具半径补偿,在没被取消之前一直有效。
例9-6 如图9-10所示,在XY 平面使用半径补偿(没有Z 轴移动)进行轮廓铳削,程 序如下:00723 ; N10 G90 G54 G17 G00 X0 Y0 N20S1000 M03;N30 G41 X20 Y10 D01; N40 G01 Y50 F100; N50 X50; N60 Y20; N70 X10;N80 G40 G00 X0 Y0 M05; N90M30;说明:1 )刀具半径补偿的建立或取消, 刀具半径偿补,在没被取消之前一直有效。
2) 当刀具补偿号为 D00时,等同于取消刀具半径补偿。
3) 一般情况下刀具半径补偿号要在刀补取消后才能比变幻,如果在补偿方式下变换补 偿号,当前句目的地补偿量将按新的给定值,而当前局开始点补偿则不便。
4)刀具半径补偿可以利用在同一程序改变刀补大小实现粗、精加工。
粗加工刀补 -刀具半径+精加工余量精加工刀补=刀具半径+(修正量)5) 在进行刀补的时候,向扩大刀具中心轨迹方向的补偿,对刀具直径的要求较小。
对于缩小刀具中心轨迹方向的补偿,对刀具的直径有一定的要求,刀具的半径应当小于轮廓的最小半径,否则将形成刀路的自交叉或缩小成点的情况。
6) 在偏置方式中如果有相邻两句或两句以上程序段无刀具补偿平面轴的移动,刀具就 有可能将产生过切。
五、刀具长度补偿G43、G44 ――刀具长度偏置指令 G49 ――刀具长度偏置取消指令当一个加工程序要使用几把不同刀具时,由于所选用的刀具长度各异,或者刀具磨损后G17 — -刀具半径补偿平面为 XY 平面 G17 — -刀具半径补偿平面为 XY 平面 G18 — -刀具半径补偿平面为 ZX 平面 G19 — -刀具半径补偿平面为 YZ .t . t .平面G41- 左刀补(在丿J 具刖进方向左侧补偿G42 — -右刀补(在刀具刖进方向右侧补偿 G40 — —取消刀具半径补偿)如图9-9 )如图9-9只能在 G00或G01方式下完成,一旦建立了长度发生变化,因而在同一坐标系,在 Z 值不变的情况下可能是刀具的端面在Z 轴方向的实际位置有所不同, 这就给编程带来了困难。
为编程方便,调试刀具容易,就需要统一刀具长度方向定位基准,这样就产生了刀具长度偏置功能如图 9-11所示。
刀具长度偏置指令用于刀具轴向的补偿,它使刀具在 Z 方向上的实际位移量等于补偿轴终点坐标值加上(或减去)补偿值。
G17G43格式;IG44 X Y Z HC ;011 0G4Q 1 JG17 ――刀具长度补偿轴为 Z 轴 G18 ――刀具长度补偿轴为 Y 轴 G19 ――刀具长度补偿轴为 X 轴 G49 ――取消刀具长度补偿G43 ――正向偏置(补偿轴终点加上偏置值) G44 ――负向偏置(补偿轴终点减去偏置值) X, Y, Z ―― G00/G01 的参数即刀补建立或取消的终点H ――刀具长度补偿偏置号(H00~H99) 。
H 字是存地址,在该地址 中装有刀具的偏置量(刀柄锥部的基准面 到刀尖的距离),该偏置量代表了刀补表 中对应的长度补偿值。
G43、G44、G49指令都是模态 代码可相互注销,并且 G43、G44只能 在G00或G01方式完成,在没有被G49取 消前一直有效。
米用G43 ( G44 )指令后,编程人员就不一定要知道实际使用的刀具长度, 可按假定的刀具长度进行编程。
或者在加工过程中, 若刀具长度发生变化或更新刀具时,不需要变更程序,只要改变刀具长度偏置值即可。
例9-7 如图9-12,用装在主轴上的立铳刀加工 川、W 面,必须把刀具从基准面I 移近工件上表面,再作 Z 向切入进给,这两个动作程序如下:对移动,移动距离为-348+H01 即-348+100=-248mm。