自动化设备机械加工件来料检验标准
自动化设备机械加工件来料检验标准
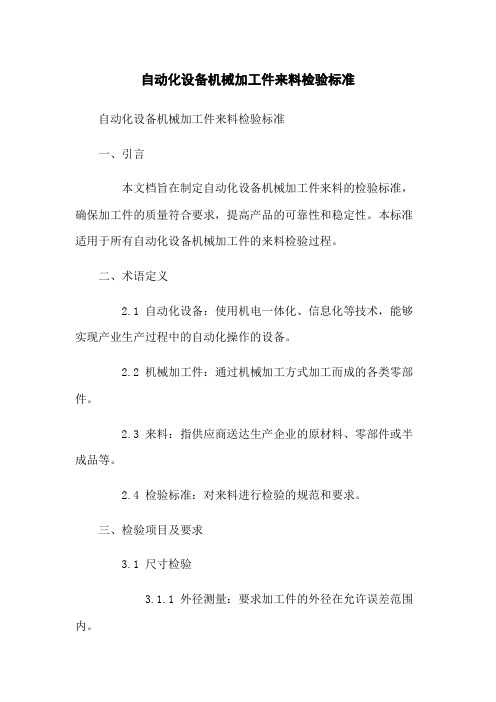
自动化设备机械加工件来料检验标准自动化设备机械加工件来料检验标准一、引言本文档旨在制定自动化设备机械加工件来料的检验标准,确保加工件的质量符合要求,提高产品的可靠性和稳定性。
本标准适用于所有自动化设备机械加工件的来料检验过程。
二、术语定义2.1 自动化设备:使用机电一体化、信息化等技术,能够实现产业生产过程中的自动化操作的设备。
2.2 机械加工件:通过机械加工方式加工而成的各类零部件。
2.3 来料:指供应商送达生产企业的原材料、零部件或半成品等。
2.4 检验标准:对来料进行检验的规范和要求。
三、检验项目及要求3.1 尺寸检验3.1.1 外径测量:要求加工件的外径在允许误差范围内。
3.1.2 内径测量:要求加工件的内径在允许误差范围内。
3.1.3 高度测量:要求加工件的高度在允许误差范围内。
3.2 表面质量检验3.2.1 表面粗糙度检测:要求加工件的表面粗糙度符合要求的等级。
3.2.2 表面缺陷检测:要求加工件的表面没有明显的裂纹、磨损或划痕等缺陷。
3.3 材料成分分析3.3.1 化学成分检测:要求加工件的化学成分符合设计要求。
3.3.2 金相组织检测:要求加工件的金相组织均匀、无明显气孔和夹杂物。
3.4 力学性能检验3.4.1 抗拉强度检测:要求加工件的抗拉强度在允许误差范围内。
3.4.2 延伸率检测:要求加工件的延伸率在允许误差范围内。
四、检验方法4.1 尺寸检验方法4.1.1 使用测量仪器对加工件进行尺寸测量。
4.1.2 根据设计图纸要求,对测量结果进行判断。
4.2 表面质量检验方法4.2.1 使用表面粗糙度仪对加工件表面进行粗糙度检测。
4.2.2 使用目视和触摸等方法对加工件表面进行缺陷检测。
4.3 材料成分分析方法4.3.1 采用化学分析方法对加工件的成分进行检测。
4.3.2 采用金相显微镜等设备对加工件的金相组织进行检测。
4.4 力学性能检验方法4.4.1 使用拉伸试验机对加工件进行抗拉强度检测。
来料检验规范
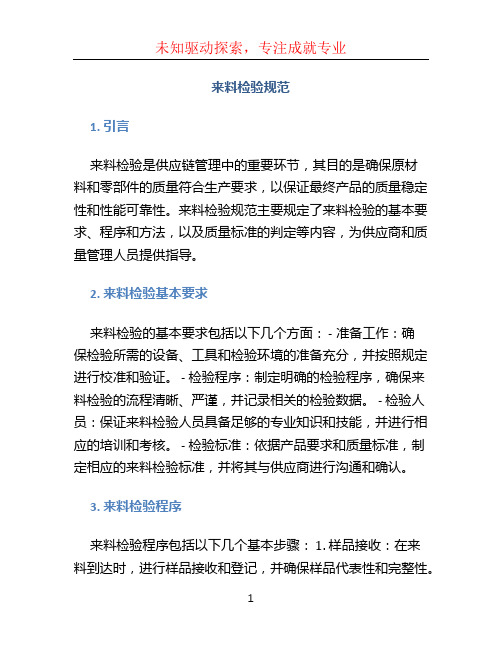
来料检验规范1. 引言来料检验是供应链管理中的重要环节,其目的是确保原材料和零部件的质量符合生产要求,以保证最终产品的质量稳定性和性能可靠性。
来料检验规范主要规定了来料检验的基本要求、程序和方法,以及质量标准的判定等内容,为供应商和质量管理人员提供指导。
2. 来料检验基本要求来料检验的基本要求包括以下几个方面: - 准备工作:确保检验所需的设备、工具和检验环境的准备充分,并按照规定进行校准和验证。
- 检验程序:制定明确的检验程序,确保来料检验的流程清晰、严谨,并记录相关的检验数据。
- 检验人员:保证来料检验人员具备足够的专业知识和技能,并进行相应的培训和考核。
- 检验标准:依据产品要求和质量标准,制定相应的来料检验标准,并将其与供应商进行沟通和确认。
3. 来料检验程序来料检验程序包括以下几个基本步骤: 1. 样品接收:在来料到达时,进行样品接收和登记,并确保样品代表性和完整性。
2. 外观检验:对来料进行外观检查,包括尺寸、颜色、表面质量等方面的检验。
3. 物理性能检验:对来料进行物理性能测试,包括强度、硬度、密度等方面的检验。
4. 化学成分检验:对来料进行化学成分测试,如含量分析、元素分析等。
5. 材料鉴别:使用相应的测试方法和工具进行来料的材料鉴别,确认材料的真实性和原材料的符合性。
6. 尺寸检验:通过测量和检验来料的尺寸准确性,确保其符合图纸和设计要求。
7.功能性能检验:根据产品的功能要求,进行来料的功能性能测试,以确保其满足产品的使用要求。
8. 检验记录:对每个来料样品的检验过程和结果进行详细记录和存档。
4. 质量标准的判定质量标准的判定是来料检验的重要环节,主要包括以下几个方面: - 合格标准:根据产品要求和质量标准,制定合格的定义和界限,对来料进行判定。
- 不合格处理:对不符合质量标准的来料,按照相应的不合格处理程序进行处理,包括退货、返修等。
- 问题解决:对于出现的质量问题,及时与供应商沟通,共同解决问题,并采取预防措施避免类似问题的再次发生。
机械加工件来料通用检验标准

测量范围为 0-500mm,卡尺的测量位置与图纸要求相对应,卡爪左右轻轻摆动,
数显卡尺 最小值为产品的尺寸,工件的全长取前、中、后几点测量,所得最大值与最小值
4
长度尺寸
之差的一半为工件的平行度误差。
工件过长,精度要求不高,可用卷尺测量,测量时需拉直卷尺与规则工件的侧 卷尺
面平行,取两端面间的最小值。
千分尺 小值为外径尺寸,适用于公差范围:<0.02mm。
深度 测量时将深度尺横端面与被测工件的标准面靠紧、摆正、保持垂直,轻轻用力
百分尺 旋转尺尾端旋钮,所得值为实际尺寸。
3
深度尺寸 游标 测量时将深度尺横端面与被测工件的标准面靠紧、摆正、保持垂直,轻轻用力
深度尺 推入,所得值为实际尺寸。
深度量规 通规靠紧工件标准面,无透光现象,止规靠紧加工面有透光现象,为合格产品。
7
内螺纹
完整牙型的通规正好拧进,截短牙型的止规拧不进,工件螺纹精度合格
8
孔距
测量两孔间最小距离,通过运算测量出两孔间中心线距离,对于有角度要求的 分布在工件端面的孔应用角度尺进行测量。
2.3 外观检验条件:在 40W 日光灯下距离 30~40cm(照度约 500Lux~550Lux),旋转角度进行检查,每一面目视时
点比较其测量值,最大值与最小值之差的一半即为孔的圆柱度误差,在孔径圆
周上变换方向,比较其测量值可测孔的圆度。
内径 千分尺
用来测量 50mm 以上的孔径,按孔径选择合适长杆,并用外径千分尺校正零位。 使用时,在孔内摆动,在直径方向找出最大值,轴上找出最小值,这两个重合 值,就是孔的实际尺寸
6
外螺纹
用螺纹环规测量,完整牙型的通规正好拧进,截短牙型的止规拧不进,工件螺 纹精度合格,
机加件通用检验标准[详]
![机加件通用检验标准[详]](https://img.taocdn.com/s3/m/69e85af82cc58bd63186bdba.png)
全跳动用来限制零件上迴转面或端面,整个表面对 基准轴线(或平面)的最大偏离量。
形位公差代号标注示例及其文字说明:
项 目
示例
图解
直 线 度
说明
圆柱表面上任一 素线必须位于轴 向平面内,距离 为公差 0.02 的两 平行直线之间。
word 完美格式
范文范例 精心整理
平 面 度
圆 度
圆 柱 度
线 轮 廓 度
0.5
铝件、钢件表面处理后的尺寸变化:
序号
表面处理
面单边增厚范围
孔单边小范围
1
铝发白
0.002~0.003
0.001~0.002
2
铝发黑
0.004~0.005
0.004~0.005
3
镀镍
一般要根据客户要求,可 以控制 0.004~0.006
大于φ10 的 0.004~ 0.006,小于φ10 的忽略
不计
大于φ10 的 0.003~
4
镀铬
0.003~0.005
0.005,小于φ10 的忽略
不计
5
镀锌
0.005~0.007
0.005~0.007
6
铝硬白
0.008~0.01
0.008~0.01
常用形位公差项目及符号:
word 完美格式
范文范例 精心整理
分类 形 状 公 差
定 向 位 置定 公位 差 跳 动
铆件应牢靠、无松动,螺纹无缺损、无腐蚀等;不允许有加工遗留物;
零件的喷塑、喷漆层应均匀、连续,无缩孔、起泡、开裂、剥落、粉化、流挂、
露底(局部无涂层或涂料覆盖不严)、指印等缺陷;
热处理方法应符合有效版本图纸要求,热处理后不应有过烧、氧化、脱碳、热
机加工零部件质量检验标准
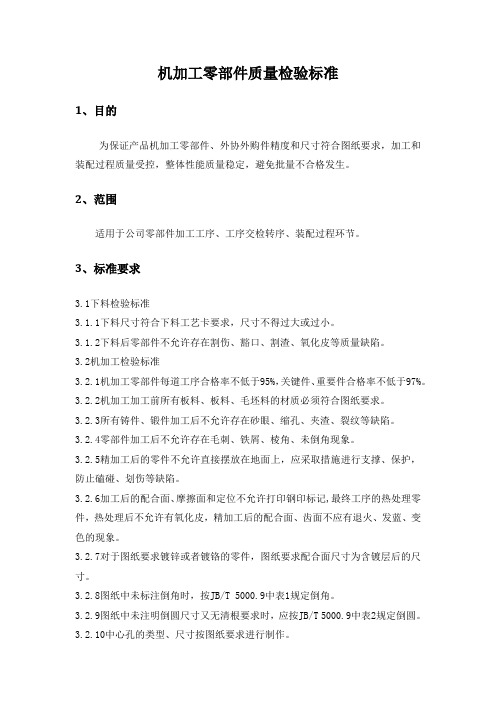
机加工零部件质量检验标准1、目的为保证产品机加工零部件、外协外购件精度和尺寸符合图纸要求,加工和装配过程质量受控,整体性能质量稳定,避免批量不合格发生。
2、范围适用于公司零部件加工工序、工序交检转序、装配过程环节。
3、标准要求3.1下料检验标准3.1.1下料尺寸符合下料工艺卡要求,尺寸不得过大或过小。
3.1.2下料后零部件不允许存在割伤、豁口、割渣、氧化皮等质量缺陷。
3.2机加工检验标准3.2.1机加工零部件每道工序合格率不低于95%,关键件、重要件合格率不低于97%。
3.2.2机加工加工前所有板料、板料、毛坯料的材质必须符合图纸要求。
3.2.3所有铸件、锻件加工后不允许存在砂眼、缩孔、夹渣、裂纹等缺陷。
3.2.4零部件加工后不允许存在毛刺、铁屑、棱角、未倒角现象。
3.2.5精加工后的零件不允许直接摆放在地面上,应采取措施进行支撑、保护,防止磕碰、划伤等缺陷。
3.2.6加工后的配合面、摩擦面和定位不允许打印钢印标记,最终工序的热处理零件,热处理后不允许有氧化皮,精加工后的配合面、齿面不应有退火、发蓝、变色的现象。
3.2.7对于图纸要求镀锌或者镀铬的零件,图纸要求配合面尺寸为含镀层后的尺寸。
3.2.8图纸中未标注倒角时,按JB/T 5000.9中表1规定倒角。
3.2.9图纸中未注明倒圆尺寸又无清根要求时,应按JB/T 5000.9中表2规定倒圆。
3.2.10中心孔的类型、尺寸按图纸要求进行制作。
3.2.11所有内径、外径、轴类加工表面粗糙度必须严格按照图纸制作。
4、职责和要求4.1技术部负责按照产品设计确认产品关键件、重要件并提供清单;负责产品在生产制作过程中图纸尺寸的修改和提供技术支持。
4.2工艺部负责确认关键工序和重要工序并制定工艺文件;负责产品制作过程中加工工艺的指导和工艺文件的制定并监督工作执行情况。
4.3 生产部负责按照最新版设计图纸和工艺文件进行派工,并将图纸和工艺卡一并交给操作者。
操作者在加工前必须熟悉图纸尺寸要求和工艺制作流程要求,熟练掌握本工序所用的工装、夹具和量具的使用,并复检上道工序(如:下料)零部件是否存在尺寸不合格或外观缺陷等质量问题。
自动化设备机械加工件来料检验标准

形位公差的检测方法按照GB/T1958-1980进行,必要时可检测工具进行检测。
7.5性能:
7.5.1镀锌、镀镍、镀铬等镀层附着力检验:新供应商导入时需做检测,用百格刀(或介刀)在供应商提供的60×90×1mm3的样板(同批表面处理)或同批试样工件表面划1mm×1mm格子100个,格子深度以见到基材为准,把3M透明胶纸贴在格子上,用手指抚压10个来回,使胶纸充分贴紧,以45°方向向上快速拉起,在同一个位置上重复做10次,每次用的胶纸要更新,格子不应有脱落。
6.螺纹规、环7.针规8.大理石平台9.万用表/兆欧表10.色板
6.术语及定义
外观面定义:A级表面:在使用过程中经常被客户看见且被关注的部分(如:作业平台,操作面板等)。
C级表面:在使用过程中不会被客户看到的表面部分(如:结合部位)。此表面的外观缺陷应合理而且不至于给客户觉得该产品质量不佳。
7.检验步骤:
7.3.3对机加件的表面缺陷具体标准参考下表:
外观缺
陷类型
缺陷所处
表面类型
允许范围
A级表面
B级表面
C级表面
基材花斑
金属表面
目视可见不允许
不允许
S总≤被测面积的5%
浅划痕
所有表面
目视可见不允许
L≤50×0.4,P≤2,N≥50
P≤5,N≥50
深划痕
所有表面
目视可见不允许
不允许
不允许
凹坑
非拉丝和喷砂面
目视可见不允许
7.6.3必须将产品的各检验特性都检验完毕后,方可进行综合判定。
7.6.4当本标准与实际效果不符且有争议时,以研发及品质部确认结果为准;
7.6.5标准里未体现的缺陷以我司品质部的判定标准为准。
自动化设备机械加工件来料检验标准
自动化设备机械加工件来料检验标准自动化设备机械加工件来料检验标准⒈引言自动化设备机械加工件来料检验是确保进入生产流程的原材料和部件符合质量要求的重要步骤。
本标准旨在规范来料检验的流程和标准,确保产品的质量和可靠性。
⒉术语定义⑴自动化设备:指用于实现自动化生产和操作的设备,包括机械、电气、电子等组成部分。
⑵机械加工件:指通过机械加工工艺加工而成的零件或产品。
⑶来料检验:指对进入生产流程的原材料和部件进行检验,以确定其符合规定的质量要求。
⒊来料检验流程⑴接收来料:将来料送到指定的接收区域,并填写相关的检验记录。
⑵检验一致性:对来料进行一致性检验,包括尺寸检验、外观检验、材质检验等。
⑶检验合格性:根据产品的质量要求进行合格性检验,包括功能性检验、性能测试等。
⑷检验记录:对检验结果进行记录,并填写检验报告。
⑸判定检验结果:根据检验结果,对来料进行判定,判断为合格或不合格。
⑹处理不合格品:对不合格品进行处理,包括退回供应商、返修等。
⑺存储样品:对检验合格的样品进行存储,并进行相应的标识。
⒋检验标准⑴尺寸检验标准:按照产品设计图纸中规定的尺寸要求进行检验。
⑵外观检验标准:按照产品的外观标准和规定的质量要求进行检验。
⑶材质检验标准:按照产品的材质要求进行材质检验。
⑷功能性检验标准:按照产品的功能性要求进行检验。
⑸性能测试标准:按照产品的性能测试要求进行测试。
⒌法律名词及注释⑴ ISO 9001:国际标准化组织制定的质量管理体系标准,用于组织管理和产品质量监控。
⑵ GB/T 2828:中华人民共和国标准,规定了来料检验的一般规则和抽样检验的程序。
⒍附件⒎结束语本文所阐述的来料检验标准为确保自动化设备机械加工件的质量和可靠性提供了指导和规范。
适用本标准进行来料检验,能够有效降低质量风险,提高产品的一致性和合格率。
来料检验标准
隔离并标识来料检验报告特采选用退货 供应商NGOK 跟进签批1. 目的:确保来料质量符合本公司规定要求。
2. 范围:适合公司原辅材料及外加工半成品的检验。
3. 职责:质控部:负责材料的检验。
4.作业流程:5.公司来料按类别分类为:纸张类、辅料类、外协类。
5.1 纸张类 5.1.1 术语及定义:A 、尺寸偏差(横向坚向):对规矩型样品进行平行或垂直方向测量得到数据与标准数据比。
B 、歪斜底:对规矩型样品,进行对角线测量,对比其两者的数据差异。
C 、克重:指在一般条件下,所测量数据(不考虑环境及材料本身的含水量)。
D 、厚薄均匀度:包含同一样张的不同部位或不同样张的同一部位两组数据。
5.1.2 指标要求:来料与《来料通知单》一致,有效的标签(生产厂家、日期、批号及等级等),整批1.仓管员通知IQC 检验。
2.IQC 开始准备检验。
检验合格流程:1、IQC 依据《物料RoHS 对应清单》确认所来物料其有害物质含量是否符合要求后进行后续检验,如不符合作则直接作退货处理;2、检验物料与《收货通知单》一致性及外观有无异常。
3、据物料的抽样标准及检验标准进行验收检查,填写《来料检验报告单》。
3、检验合格后书面通知仓库办理入库手续,并挂“合格品”标识牌,注明检验状态、检验时间及检验人。
检验不合格流程:1、检验不合格的,由IQC 挂“不合格品”标识牌,通知仓库隔离并提交《来料检验报告单上报品质经理处理。
2、根据《来料检验报告单》的签批情况,进行相关处理。
3、特采与选用合格的按合格品流程入仓,选用不合格的与报告签批退货的通知仓库退供应商。
流程 操作规范OKNGIQC 验收物料通知IQC 检验仓库品质部异常处理入库纸张平整,没有卷曲,外观包装一致,包装完好。
5.1.3 抽样标准:5.1.3.1 来料为散装纸(分切纸等)的,按国标GB2828.1-2003的AQL 2.5标准进行抽检。
5.1.3.2来料为板装铜版纸、灰卡纸、单铜纸、哑粉纸的查看外观及生产日期即可。
机械加工检验标准及方法(1)
机械加工检验标准及方法(1)机械加工是现代工业生产中不可或缺的一环,机械加工检验是确保机械加工产品质量的重要环节。
为了确保机械加工产品的合格率,合理地制定适合生产的检验标准及方法是必要的。
本文将详细介绍机械加工检验标准及方法。
机械加工检验标准机械加工产生的产品有尺寸精度、表面质量、几何精度、材料硬度等多个方面的品质要求。
机械加工检验标准是指根据机械加工产品的不同品质要求,制定出一系列检验标准,用于对机械加工产品进行检验。
常见的机械加工检验标准有GB、ISO、JIS等标准。
在实际操作中,应根据机械加工产品的实际需求和使用要求,选择合适的检验标准进行检验。
同时,对于特定的机械加工产品,也可以根据实际需求制定符合实际情况的检验标准。
机械加工材料的检验方法机械加工材料的检验是确保机械加工产品质量的关键环节。
在机械加工成品的检验过程中,不仅要对成品进行检验,还要对原材料进行检验。
下面我们将详细介绍机械加工材料的检验方法。
金属材料的检验方法金属表面缺陷的检验钢材表面缺陷常见有裂纹、划痕、气泡、硅酸盐夹杂物等。
缺陷类型众多,方法不同。
一般来说,通过目视检查、手摸检查、探伤、磁粉探伤等方法可检测出钢材表面缺陷。
但有些缺陷需要通过仔细打磨能够去除,在制作机械零件时才可使用。
金属含量的检验从金属材料中提取样品,经过化学分析,就可以得到其组成。
从而判断其是什么金属及含量是否符合标准。
非金属材料的检验方法干燥状态的检验如混凝土等,在干燥状态下检测其强度。
取样检验如塑料等,可在规定的机器、水平面等条件下,按规定的方法将试样切割成均匀大小的试样,然后采用拉伸、弯曲等方法进行检验。
机械加工验收方法验收是机械加工产品交付使用前的最后一道程序。
通过验收可以确定机械加工产品是否符合质量标准,以及确认产品的使用性能是否符合用户要求。
机械加工产品的验收方法主要包括自检、互检和专家检查。
自检自检主要是由机械加工产品生产者自己进行,通过严格的自我检查,查找产品的问题,使其能够符合相应的质量标准。
来料检验规范
来料检验规范来料检验是为检验生产用物料质量是否合乎工程技术要求,严格控制不合格品流程,确保产品质量.一、来料检验方法:1)外观检测:一般用目视、手感、样品进行验证;2)尺寸检测:一般用卡尺、千分尺、卷尺、直尺、百分表、塞规和平台等量具验证;3)结构检测:一般用拉力器、扭力器、压力器验证;4)特性检测:如电气的、物理的、化学的、机械的特性,一般采用检测仪器和特定方法来验证.二、来料检验方式的选择:1)全检:适用于来料数量少、价值高、不允许有不合格品物料或工厂指定进行全检的物料.2)抽检:适用于平均数量较多,经常性使用的物料.三、来料检验的程序:1)品质工程师制定检验和试验的规范、作业指导书,由经理批准后发放至检验人员执行.检验和试验的规范包括材料名称、检验项目、标准、方法、记录要求.2)采购部根据到货日期、到货品种、规格、数量等,通知库房和品质部准备来验收和检验工作.3)检验员接到检验通知后,按检验规范进行检验,并填写检验记录和检验日报.4)检验完毕后,对合格的来料贴上合格标识,通知采购与库房人员办理入库手续.5)如果是生产急需的来料,在来不及检验和试验时,须按紧急放行规定的程序执行.6)检测中不合格的来料应及时填写产品检验不合格品单,由品质工程师确认并给出参考意见,提交经理作出处理;重大问题必须提交品质部经理与工程部、生产部审核后再作出处理;不合格的来料不允许入库,并进行相应标识,将移入不合格品库区隔离,采购部按处理意见办理相关事宜;保证不合格的零件、成品不装配,不合格的产品不出厂.7)来料检验和试验的记录由品质部文员每日收取,做好数据统计汇总后,整理成册存档备查,按规定期限妥善保存.8)检验时,如来料检验员无法判定是否合格,应立即请品质工程师或经理会同验收来判定是否合格,会同验收的参与人员必须在检验记录表内签字.9)回馈来料检验情况,并将来料供应商的交货质量情况及检验处理情况记录,每月汇总于供应商的交货质量月报内.10)来料检验员根据来料的实际检验情况,对检验规范提出改善意见.11)来料检验员定期校正检验仪器、量规,保养试验设备,以保证来料检验结构的正确性.四、来料检验的结果:1)检验合格:经来料检验员按照检验规范要求操作,来料检验员应在检验合格证上签名,通知采购与库房收货.2)检验不合格:来料检验员按照检验规范要求操作,检出不合格品应及时填写产品检验不合格品单,会同品质工程师、经理作出处理;不合格品处理有报废、让步接收特采、返工返修三种处理方式;重大问题必须提交品质部经理与工程部、生产部审核后再作出处理;并进行相应标识,将移入不合格品库区隔离,通知采购部根据处理意见办理相关事宜.3)让步接收特采:即来料经检验员的检验发现其质量低于标准要求,但由于生产急需或其他原因,会同品质工程师、经理、工程部、生产部作出降级次品的让步接收处理,会同验收的参与人员必须在检验记录表内签字方可签收.来料检验流程过程检验规范装配过程的质量对一个产品的质量起着决定性的作用,零件的质量是合格的,但由于装配质量不合格,制造出来的产品的质量肯定不合格.为了确保制造出来的产品质量,装配过程中的质量检验工作是非常重要的,是整个制造过程的一个重要环节.一、部装的检验将合格的零件按工艺规程装配成组部件的工艺过程称为部装.部装检验的依据:标准、图纸、工艺文件作业指导书.1、零件外观和场地的检验在部装之前,要对零件的外观质量和场地进行检查,要做到不合格的零件不准装配,场地不符合要求不准装配.1零件加工表面无损伤、锈蚀、划痕.2零件非加工表面的油漆膜无划伤、破损,色泽要符合要求.3零件表面无油垢,装配时要擦洗干净.4零件不得碰撞、划伤.5零件出库时要检查其合格证、质量标志或证明文件,确认其质量合格后,方准进入装配线.6中、小件转入装配场地时不得落地放在托板上.7大件吊进装配场地时需检查放置地基的位置,防止变形.8大件质量配件处理记录.9重要焊接零件的质量检验记录单.10场地要清洁,无其他多余物,装配场地要进行定置管理.2、装配过程的检查检验人员要按检验规范要求,采用巡回方法,监督检查每个装配工位;监督检查工人遵守装配工艺规程;检查有无错装和漏装的零件.装配完毕后,要按规定对产品进行全面检查,做完整的记录备查.二、总装的检验把零件和部件按工艺规程装配成最终产品的工艺过程称为总装.1检验依据产品图纸、装配工艺规程以及产品标准.2检验内容总装过程的检查方法与部装过程的检查方法一样,采用巡回方法监督检查每个装配工位;监督工人遵守装配工艺规程,检查有无错装漏装等.1装配场地必须保持环境清洁,光线要充足,通道要畅通.2总装的零、部件包括外购件、外协件必须符合图样、标准、工艺文件要求.3装配后的螺栓、螺钉头部和螺母的端部面,应与被紧固的零件平面均匀接触,不应倾斜和留有间隙,装配在同一部位的螺钉长度一般应一致;紧固的螺钉、螺栓和螺母不应有松动的现象,影响精度的螺钉,紧固力矩应一致.4在螺母紧固后,各种止动垫圈应达到制动要求.根据结构的需要可采用在螺纹部分涂低强度防松胶代替止动垫圈.5机械转动和移动部件装配后,运动应平稳、轻便、灵活、无阻滞现象,定位机构应保证准确可靠.6有刻度装置的手轮和手柄装配后的反向空程量应符合标准规定.7高速旋转的零、部件在总装时应注意动平衡精度其精度值由设计规定.8重要固定结合面和特别重要固定结合面应紧密贴合.重要固定结合面总重紧固后,用塞尺检查其间隙不得超过标准之规定.特别重要固定结合面,除用涂色法检验外,在紧固前、后均应用塞尺检查间隙量,其量值应符合标准规定.与水平垂直的特别重要固定结合面,可在紧固后检验.用塞尺检查时,应允许局部最多两处插入,其深度应符合标准规定.9滑动导轨表面除用涂色法检查外,还应用塞尺检验,间隙量应符合标准规定;塞尺在导轨、滑块端部的滑动面间插入深度不得超过标准规定.10轴承装配的检验:可调的滑动轴承结构应检验调整余量是否符合标准规定;滚动轴承的结构应检验位置保持正确,受力均匀,无损伤现象;精密度较高的机械应采用冷装的方法进行装配或用加热方法装配;过盈配合的轴承,应检验加热是否均匀;同时检验轴承的清洁度和滑动轴承无尖角锐边;用润滑脂的轴承应检查其润滑脂的标准号、牌号和用量.11齿轮与轴的配合间隙和过盈量应符合标准及图样的规定要求;两啮合齿轮的错位量不允许超过标准的规定;装配后的齿轮转动时,啮合斑点和噪声声压级应符合标准规定.12各种电器元件的规格和性能匹配应符标准规定,必须检查电线的颜色和装配的牢固性并应符合标准规定.3产品的检验产品的检验是一个产品从原材料入厂开始,经过加工、部装、总装,直到成品出厂的全过程中的最后一道综合性检验,通过对产品的性能,几何精度,外观质量等项目的全面检测和试验,根据检测试验结果综合评定被检验产品的质量等级的过程.正常生产的产品出厂检验是为了考核产品制造是否符合图样、标准和技术文件的规定.产品经检验合格后才准出厂,在特殊情况下,经用户同意或应用户要求,可在用户处进行检验.产品的检验分型式检验和产品的出厂检验两种.型式检验是为了全面考核产品的质量;考核产品设计及制造能否满足用户要求;检查产品是否符合有关标准和技术文件的规定;试验检查产品的可靠性;评价产品在制造业中所占的技术含量和水平.凡遇下列情况之一,均应进行型式检验:1新产品定型鉴定时;2产品结构和性能有较大改变时;3定期地考查产品质量;4产品在用户使用中出现了严重的性能不可靠事故.4产品检验的内容1)一般要求1检验前,应将产品安装和调整好,一般应自然调平,使产品处于自然水平位置.2在检验过程,不应调整影响产品性能、精度的机构和零件,否则应复检因调整受厂影响的有关项目.3检验时,应按整机进行,不应拆卸整机,但对运转性能和精度无影响的零件、部件和附件除外.4由于产品结构限制或不具备规定的测试工具时,可用与标准规定同等效果的方法代替.5对于有数字控制的自动化或半自动化的产品,应输入一种典型零件加工程序,做较长时间的空运转,运转时应符合标准规定.2)外观质量的检验1产品外观不应有图样未规定凸起、凹陷,粗糙不平和其他损伤,颜色应符合图样要求.2防护罩应平整均匀,不应翘曲、凹陷.3零、部件外露结合面的边缘应整齐、均匀,不应有明显的错位,其错位量及不均匀量不得超过规定要求.门、盖与产品的结合面应贴合,其贴合缝隙值不得超过规定要求.电气和电气箱等的门、盖周边与其相关件的应均匀,其缝隙不均匀值不得超过规定要求.当配合面边缘及门、盖边长尺寸的长、宽不一致时,可按长边尺寸确定允许值.4外露的焊缝应修整平直、均匀.5装入深孔的螺钉不应突出于零件的表面,其头部与沉孔之间不应有明显的偏心.固定销一般应略突出于零件表面.螺栓尾端应略突出于螺母的端面长度为2-3牙螺纹.外露轴端应突出于包容件的端面,突出时均为倒角.内孔表面与壳体凸缘间的壁厚应均匀对称,其凸缘壁厚之差不应超过规定的要求.6外露零件表面不应有磕碰、锈蚀、螺钉、铆钉和销子端部不得有扭伤、锤伤、划痕等缺陷.7金属手轮轮缘和操纵手柄应有防锈镀层.8镀件、发蓝件、发黑件色调应一致,防护层不得有褪色和脱落现象.9电气、液压、润滑和冷却等管道的外露部分,应布置紧凑、排列整齐、美观,必要部位应用管夹固定:管道不应产生扭曲、折叠等现象.10成品零件未加工的表面,应涂以油漆等涂料,涂料应符合相应的标准要求.3)参数的检验根据产品的设计参数检验其制造过程是否符合相应的产品标准规定.4)空运转试验空运转试验是在无负苘状态下运转产品,检验各机构的运转状态、刚度变化、功率消耗、操纵机构动作的灵活性、平稳性、可靠性和安全性.试验时产品的主运动机构应从最低速度起依次运转,每级速度的运转时间按规定要求进行.用交换齿轮、皮带传动变速和无级变速的产品可作低、中、高速运转.在最高速度时,应运转足够的时间,使主运动机构轴承达到稳定温度.进给机构应作依次变换进给量或进给速度的空运转试验,对于正常生产的产品.检验时,可作低、中、高进给量或进给速度试验.有快速移动机构的产品,应作快速移动的试验.5)温升试验在主轴轴承达到稳定温度时,检验主轴轴承的温度和温升,其值均不得超过相应的标准规定.在达到稳定温度状态下应做下列检验:①主运动机构相关精度冷热态的变化量:②各部轴承法蓝及密封部位不应有漏油或渗油.③检查产品的各油漆面的变形和变化、变质等不良现象.④检查产品中的新材料经升温后的材质变形对质量的影响情况.6)主运动和进给运动的检验检验主运动速度和进给速度进给量的正确性,并检查快速移动速度或时间.在所有速度下,产品的工作机构均应平稳、可靠.7)动作试验产品的动作试验一般包括以下内容:①用一个适当的速度检验主运动和进给运动的起动、停止包括止动、反转和点动等动作是否灵活可靠.②检验自动机构包括自动循环机构的调整和动作是否灵活、可靠.③反复变换主运动或进给运动的速度,检查变速机构是否灵活、可靠以及指示标牌的准确性.④检查转位、定位、分度机构动作是否灵活、准确、可靠.⑤检验调整机构、夹紧机构、读数指示装置和其他附属装置是否灵活、准确、可靠.⑥检验装卸工件、夹具和附件是否灵活、可靠.⑦与产品连接的随机附件应在该产品上试运转,检查其相互关系是否符合没计要求.⑧检验其他操纵机构是否灵活、准确、可靠.⑨检验有刻度装置的手轮反向控程量及手轮、手柄操纵力.空程量和操纵力应符合相应标准的规定.⑩对数控产品应检验重复定位、转动以及返回基准点的正确性,其量值应符合相关标准的规定.8)噪声检验各类产品应按相应的噪声测量标准所规定的方法测量成品噪声的声压级,测量结果不得超过标准的规定.9)空运转功率检验在产品主运动机构各级速度空运转至功率稳定后,检查主传动系统的空运转功率.对主进给运动与主运动分开的产品,必要时还要检查进给系统的空运转功率.10)电气、液压、冷却、润滑系统的检验对电气、液压、冷却、润滑系统也应进行检验.电气全部耐压试验必须按有关标准规定作确保整个产品的安全保护.液压、冷却、润滑系统对高、低压力应全面检查,防止系统的内漏或外漏.11)测量装置检验产品和附件的测量装置应准确、稳定、可靠,便于观察、操作,视场清晰,有密封要求处,应设有可靠的密封防护装置.12)整机连续空运转试验对于自动、半自动数控产品,应进行连续空运转试验,整个空运转过程中不应发生故障.连续运转时间应符合有关标准规定.试验时自动循环应包括所有功能和全工作范围,各次自动循环休止时间不得超过或低于规定要求.专用设备应符合设计规定的工作节拍时间或生产率的要求.13)负荷试验负荷试验是检验产品在负荷状态下运转时的工作性能及可靠性,即加工能力、承载能力或拖引能力等及运转状态指速度的变化、机械的振动、噪声、润滑、密封、止动等等.1产品承载工件最大重量的运转试验.在产品上装上设计规定的最大承载重量的工件,用低速及设计规定的高速运转机械成品,检查该产品运转是否平稳,可靠.2产品主传动系统最大扭矩的试验扭矩试验包括:①主传动系统最大扭矩的试验.②短时间超过规定最大扭矩的试验.试验时,在小于、等于产品计算转速范围内,选一适当转速.逐级改变进给量,使达到规定扭转力矩,检验产品传动系统各传动元件和变速机构是否可靠、平稳和准确.3产品主传动系统达到最大功率的试验抽查选择适当的加工方式、试件材料和尺寸、速度、进给量,逐步改变进给深度,使产品达到最大功率—般为主电机的额定功率.检验产品的结构和稳定性以及电气等系统是否可靠.4传动效率试验产品加载至主电机达到最大功率时,利用标准规定的专门的仪器检验产品主传动系统的传动效率.注意:1不需要做负荷试验的产品,应按专门的规定进行.2工件最大重量、最大扭矩均指设计规定的最大值.14)精度检验产品精度检验足为厂检验产品各种要素对加工工件精度的影响.1几何精度、传动精度检验按各种类型规格产品精度标准、质量分等标准、制造与验收技术条件、企业或地方制定的有关标准的规定进行检验.检验时,产品按设计规定所有零、部件必须装配齐全,应调整部位要调整到最佳位置并锁定.各部分运动应手动,或用低速机动.负荷试验前后均应检验产品的几何精度,不做负荷试验的产品在空运试验后进行,最后—次精度的实测数值记入合格证明书中.2运动的不均匀性检验按有关标准的规定进行检验或试验.3振动试验按有关标准的规定进行试验.4刚度试验在相关的主要件做改动时,必须做刚度试验.按有关标准的规定进行检验.5热变形试验按有关标准的规定进行试验.在精度检验中对热变形有关的项目,按标准的规定进行检验.并考核其热变形量.6工作精度检验按各类型产品精度等有关标准的规定进行检验.工作精度检验时应使产品处于工作状态进行检验按规定使主运动机构运转一定时间,使其温度处于稳定状态.7其他精度检验按有关技术文件的规定进行检验.15)工作试验产品的工作试验是检验产品在各种可能的情况下工作时的工作状况.工作试验时,产品的所有机构、电气、液压、冷却润滑系统以及安全防护装置等均应工作正常.同时,还应检查零件加工精度表面粗糙度、位置精度等、生产率、振动、噪声、粉尘、油雾等.16)寿命试验在生产厂或用户进行考核或抽查其寿命情况,并应符合下列要求:1在两班工作制和遵守使用规则的条件下,产品精度保持在规定的范围内的时间及产品到第一次大修的时间不应少于规定要求. 2重要及易磨损的导轨副应采取耐磨措施,并符合有关标准的要求.对主轴、丝杠、齿轮等主要零件也应采取耐磨措施,以提高其寿命.3导轨面、丝杠等容易被尘屑侵入的部位,应设防护装置.17)其他检试验按订货协议或技术条件中所规定的内容进行检验.例如,有的机械产品要求作耐潮、防腐、防霉、防尘、排放等检验.18)出厂前的检验产品在出厂前要按包装标准和技术条件的要求进行包装,—般还应进行下列检验:1涂漆后包装前进行产品质量检验①检验产品的感观质量,外部零部件整齐无损伤、无锈蚀.②各零部件上的螺钉及其紧固件等应紧固,不应有松动的现象,③各表面不应存在锐角、飞边、毛刺、残漆、污物等:④各种铭牌、指示标牌、标志应符合设计和文件的规定要求.⑤包装质量应检查以下内容:a各导轨面和已加工的零件的外露表面应涂以防锈油.b随机附件和工具的规格数量应符合设计规定.c随机文件应符合有关标准的规定,内容应正确、完整、统一、清晰.d凡油封的部位还应用专用油纸封严.随机工具也应采取油封等防锈措施.e包装箱材料的质量、规格应符合有关标准的规定.f包装箱外的标志字迹清楚、正确、符合设计文件和有关标准的要求.出货检验规范建立出货检查控制程序 ,为确保产品出厂前进行最终检验和测试,判定产品品质符合顾客要求,防止不合格品流出.一、职责1)品质部负责产品出货前检验的执行与结果记录,负责所有技术要求的相关检验记录.2)研发工程部负责检验项目及参数值的确定.3)营销部负责产品出货前的检验通知.4)仓库负责产品出货检验工作的配合.5)生产部负责对不合格产品进行返工返修及按需要执行纠正措施.二、检验控制流程1)产品入库前/出货检验实施:①生产部装配车间完成装配后首先进行内部自检、互检、复检,确认合格后填写内部报检单向品质部报检.报检单内容应清楚反映:机型、名称、报检数量、装配员工自检签名、复检人员签名、具体报检时间②品质部接到生产部装配车间内部报检单后,首先确认报检的机型、数量与销售部出货通知单相符.③品质部确定了生产部报检信息与出货信息一致后对出货产品进行检验.④品质部应重点对机器的结构、功能、系统等按照标准文件设定参数进行测试.⑤在检验过程中发现不良问题较多而且超过 3个低级问题时,检验员无须再检验可以直接向生产部车间主管提出拒检,同时做好不良标识待处理.⑥品质部拒绝检验已作好不良标识后要及时向生产主管反馈不良信息,由生产部装配主管或生产工艺人员找到异常问题机器的装配者要求立即返工并对机器重新检验,直到自检合检后再次向品质报检.⑦品质部接到生产部装配车间二次报检后,应重点对返工的部位进行检验,同时按照系统出厂参数设定值进行调试确保合格,最后将检验结果记录于产品检验报告中.⑧二次检验合格下架后,品质部还要根据客户远近评估包装方式并对包装要求进行监控,一定要满足在运输过程中对机器造成损坏因素的预防效果.⑨最后检查包装所使用的包装是否符合规格要求,是否有破损,出货标贴或警示标识是否醒目等,所有工作完成后方可出货.⑩最后品质部还得跟装车过程,监督在装车过程中防止造成损坏.2)库存品出货检验实施:①仓库接到销售部出货通知后通知生产部,要求安排员工将要出货的产品重新提交待检验区,挂上“待检”牌待检,同时并向品质部报检.②品质部接到仓库报检通知后带上相关检验文件和检验记录表单进行全检.③如果在检验过程中发现由于客户要求更改时,技术部研发、工艺人员必须亲自到现场制定解决方案并要跟进,生产部必须安排人员全力配合,并听从调配.④品质部应对更改内容与结果记录于出货检验报告备注栏中,同时相对应的检验指导文件必须做出修改.⑤必须检查包装方式、附件包里面物品是否齐全;是否与装箱清单相符合,同时还得检验出货标识内容包括物料编码、张贴位置等.⑥最后品质部还得跟装车过程,监督在装过程中造成损坏.3)检验准备①营销部根据出货日期提前通知品质部安排检验人员对产品进行检验.②品质部在进行检验前通知仓库进行检验的协作配合准备.③根据出货通知内容和品质部通知时间,仓库把需要检验的待出货产品搬运至验货区,并挂上:“待检”牌.4)出货检验出货检验员依产品工艺标准、顾客相关要求资料及检验规范作业指导书对产品进行全面检验.5)检验项目。
- 1、下载文档前请自行甄别文档内容的完整性,平台不提供额外的编辑、内容补充、找答案等附加服务。
- 2、"仅部分预览"的文档,不可在线预览部分如存在完整性等问题,可反馈申请退款(可完整预览的文档不适用该条件!)。
- 3、如文档侵犯您的权益,请联系客服反馈,我们会尽快为您处理(人工客服工作时间:9:00-18:30)。
文件编号版次A0 页码第1页共6页文件修订记录序号日期版本修改内容承办人12018-12-15 A0 初版发行李蔚华234567891011编制审核批准文件会签分发部门部门会签分发(份数)生产部品质部研发部采购部生效日期: 2018-12-15 制定部门:品质部制定日期: 2018-12-15文件编号版次A0 页码第2页共6页1.目的规范机械加工件的来料检验标准,以使各工序过程的产品质量得以控制。
2.适用范围本标准适用于机械加工件的检验,图纸和技术文件并同使用。
如与国家标准和技术规范冲突时,以技术文件为准。
3.引用标准本标准的尺寸未注单位为 mm。
GB/T 1031 《表面粗糙度参数及其数值》GB/T 1800.4 《极限与配合标准公差等级和孔轴的极限偏差表》GB/T 32535 《普通螺纹收尾、肩距、退刀槽和倒角》GB/T 197 《普通螺纹公差》GB/T 1184 《形状和位置公差未注公差值》GB/T 1804-M 《一般公差未注公差的线性和角度尺寸的公差》GB/T 5277 《紧固件螺栓和螺钉通孔》4.检验方案:GB/T2828 最新版;特殊抽样水准S-1 ,尺寸 / 性能类 AQL=AC/Re(0/1 );外观 AQL=0.4;月综合抽检良率外观< 1%,尺寸结构<0.1%。
5.检验设备 / 工具:1. 游标卡尺(0.01mm) 2. 千分尺( 0.01mm) 3. 内径千分尺 4. 塞尺5. 高度仪6. 螺纹规、环7. 针规8. 大理石平台9. 万用表 / 兆欧表10. 色板6.术语及定义外观面定义: A 级表面:在使用过程中经常被客户看见且被关注的部分(如:作业平台,操作面板等)。
B级表面:在使用过程中很少被客户看见的部分且不会过分关注(如:底部机加件、设备内部件)。
这些表面允许有轻微外观不良。
C 级表面:在使用过程中不会被客户看到的表面部分(如:结合部位)。
此表面的外观缺陷应合理而且不至于给客户觉得该产品质量不佳。
7.检验步骤:7.1 包装要求:7.1.1 所有物料必须使用相应的垫料、间隔物、填充物包装,避免运输过程遭到破坏,每单片产品之间必须隔开,避免相互碰撞导致不良,检验前发现有不符合的包装方式,检验人员有权拒绝接收。
7.1.2 外包装必须具有足够的抗外力强度,以便能保护内部包装物,有色金属制品如铜、铝制品需用报纸或塑料膜包覆;黑色金属需涂覆防锈油。
检验人员发现有外包装破损或有产品裸露的,有权拒绝接收。
7.1.3 所有产品来料必须附带我司提供的技术图纸,或经我司认可的技术图纸,图纸清晰明了,图纸不明确或未附带图纸检验人员有权拒绝接收。
文件名称机械加工件检验标准文件编号版次A0 页码第 3 页共6页7.1.4 产品外包装上必须贴合物料标签,标签内容包含但不限于:物料名称、物料料号、型号规格、数量及检验合格标识等,物料标签必须填写工整、完全,准确,物料标签、实物、送货单、图纸内容一致。
如未按照要求,检验人员有权拒绝接收。
7.2 一致性:同一料号的来料,其外形、规格尺寸、使用材料、加工工艺、表面处理、互换性、颜色、包装等均应有良好的一致性,批与批之间应没有明显差别。
7.3 外观:外观检视条件及方法 :--视力:校正视力 1.0 以上。
--目视距离:检查物距眼睛 A 级面 40cm,B、 C 级面距眼睛一臂之远。
--目视角度: 45 度 ~90 度(检查时产品应转动)。
--目视时间: A 级面 15 秒/ 面,B 、C面 10 秒/ 面。
--灯光:大于 500 LUX 的照明度或正常公司车间照明度。
7.3.1 表面光滑、平整、刀纹、振纹、变形、锈蚀、裂纹、压折等;不允许有加工遗留物存留在物件上;7.3.2 工件不允许有毛刺、批锋。
所有裸露部位(包括精加工的内孔面)必须去除毛刺,以不刮手为限。
7.3.3 对机加件的表面缺陷具体标准参考下表:外观缺缺陷所处允许范围陷类型表面类型 A 级表面 B 级表面 C 级表面基材花金属表面目视可见不允许不允许S 总≤被测面积的5%斑浅划痕所有表面目视可见不允许L≤ 50×0.4 , P≤2,N ≥ 50P≤5,N ≥ 50深划痕所有表面目视可见不允许不允许不允许凹坑非拉丝和喷砂面目视可见不允许直径≤ 0.5 , P≤ 2, N≥ 50不限制凹凸痕所有表面目视可见不允许不允许直径≤ 2.0 , P≤ 5,N ≥50抛光区金属表面目视可见不允许不允许S 总≤被测面积的 5% 烧伤拉丝面目视可见不允许不允许不限制水印电镀、绝缘氧化目视可见不允许S≤3.0 , N≤50不限制露白镀锌、镀镍、镀铬目视可见不允许不允许S≤4.0 , P≤3修补镀铬/镀锌目视可见不允许S≤3.0 , P≤ 1S 总≤被测面积的 5%颗粒所有表面目视可见不允许直径≤ 1.0 , P≤ 2,N≥50直径≤ 3.0 , P≤ 5,N ≥50备注S 为单个缺陷面积(2mm), P 为缺陷数量(个), L 为缺陷长度( mm) ,N 为缺陷的间距( mm)文件名称机械加工件检验标准文件编号版次A0 页码第 4 页共 6 页7.4 尺寸结构:7.4.1 针对零件尺寸精度要求选择合适的检验仪器,按《机械加工件检验标准》、有效版本图纸, 对已经确认的关键尺寸进行检验 ; 并记录指定尺寸的检验数据。
7.4.2 其余尺寸仅作符合性验证, 合格尺寸不作检验记录; 只记录不合格尺寸,图纸上有明确公差要求的,按照要求进行判定。
实测尺寸超出公差即为不合格。
图纸未标注的按照GB/T 1804-M 判定。
如下图:尺寸段> 6mm >6-30mm >30-120mm > 120-400mm> 400-1000mm>1000-2000mm>2000-4000mm中等级公差 m±0.1mm ±0.2mm ± 0.3mm ±0.5mm ± 0.8mm ±1.2mm ±2mm7.4.3 螺纹检验:螺纹规或环规需通规通止规止;但当出现通规不通时可用经螺纹规或环规(6G)检验合格的螺母或螺钉以本公司规定的扭力扭矩试装, 螺钉或螺母能顺畅通过则可接受。
来料20 件以下抽取样品数量不少于3 件进行全螺纹检验,20 件以上(含)抽取至少5 件样品进行全螺纹检验。
7.4.4 平面部分翘曲度测量依据图纸要求,图纸未标注默认按照0.3mm测量,测量时需四边、四角测量八个部位,任一部位超标判定不合格。
7.4.6 对图纸上没有明确倒角、倒圆尺寸的,按照C0.2 ~C0.5 或 R0.2 ~ R0.5 加工作业,特殊情况下可按照 C0.1 ~C0.2 进行加工。
除图纸明确注明不用倒角的部位外,所有部位必须倒角或倒圆。
7.4.7 形状和位置公差的检验7.4.7.1 基本要求1)图纸上对形位公差有明确要求的,按照图纸要求进行检验。
2)图纸上对形位公差没有明确要求的,其形位公差由加工工艺保证,一般不做检验;对形位公差有怀疑时,需进行检验。
3)客户另行要求的,以客户要求为准。
7.4.7.2 形状和位置公差要求为了保证工件形位公差符合设计要求,在加工过程中,要求检测重要的形位公差要求,如回转性工件的同轴度等。
未明确要求的形位公差按照GB1184-1996 的 K 级精度检验。
7.4.7.3 检测方法形位公差的检测方法按照GB/T1958-1980 进行,必要时可检测工具进行检测。
文件名称机械加工件检验标准文件编号版次A0页码第5页共6页7.5 性 能:7.5.1 镀锌、镀镍、镀铬等镀层附着力检验:新供应商导入时需做检测,用百格刀(或介刀)在供应商提3 1mm × 1mm 格子 100 个,格子深度供的 60× 90× 1mm 的样板(同批表面处理) 或同批试样工件表面划 以见到基材为准,把 3M 透明胶纸贴在格子上,用手指抚压 10 个来回,使胶纸充分贴紧,以 45°方 向向上快速拉起,在同一个位置上重复做 10 次,每次用的胶纸要更新,格子不应有脱落。
7.5.2 表面硬度检验:新供应商导入时需做检测,用硬度计测试 (HV 、 HRC 等 ) 或 H 级硬度之铅笔以 45o 角用 5mm/s 速度 500g 力向前推进,擦拭干净后不出现划痕为合格。
镀层硬度标准按照工程图纸,图纸未标注的参考下图:镀层工艺 硬度 镀层工艺 硬度 镀层工艺 硬度镀层工艺硬度氰化镀铜 100-160HV 化学镍 500-800HV 铬 750-1000HV 锌酸盐镀锌 100-140HV 焦磷酸盐铜 160-200HV 半光亮镍 400-500HV纯金浴50-80HV酸性镀锌 60-90HV 硫酸盐镀铜150-180HV全光亮镍500-600HV 合金浴金 160-240HV氰化镀锌60-90HV7.5.3 丝印耐化学试剂性检验:新供应商导入时需做检测,用纯净水浸过的擦布在有丝印的表面擦拭 15秒,再用酒精浸过的擦布擦拭 15 秒,最后用异丙醇浸过的擦布擦拭15 秒, ( 注:擦拭时施加约 500 克的压力,每秒一个来回 ) ,镀层不变色、不脱层和露底面为合格。
7.5.4 镀层膜厚检测:新供应商导入时需做检测, 用膜厚仪检测镀层厚度, 图纸有要求厚度的按照图纸要求,图纸未标注按≥ 20μ m 。
7.5.5 绝缘处理检验:绝缘电阻表校准后将被测物的两端分别接在“接地”及“线路”上个接线柱上,轻轻转动摇柄使转速由慢至快并< 120 转 / 分钟,指针在“∞”表示开路,指针在“ 0”表示短路。
7.6 检验基本原则文件名称机械加工件检验标准文件编号版次A0 页码第6页共6页7.6.1 供应商提交产品为试样样品或样机产品时全检验。
7.6.2 返工返修的工件必须再次提交检验合格后才能放行。
7.6.3 必须将产品的各检验特性都检验完毕后,方可进行综合判定。
7.6.4 当本标准与实际效果不符且有争议时,以研发及品质部确认结果为准;7.6.5 标准里未体现的缺陷以我司品质部的判定标准为准。
8.0 相关记录《来料检验履历表》《来料检验异常单》。