自动挡变速箱钻削过程中断屑与钻头结构的分析
pdc钻头分析
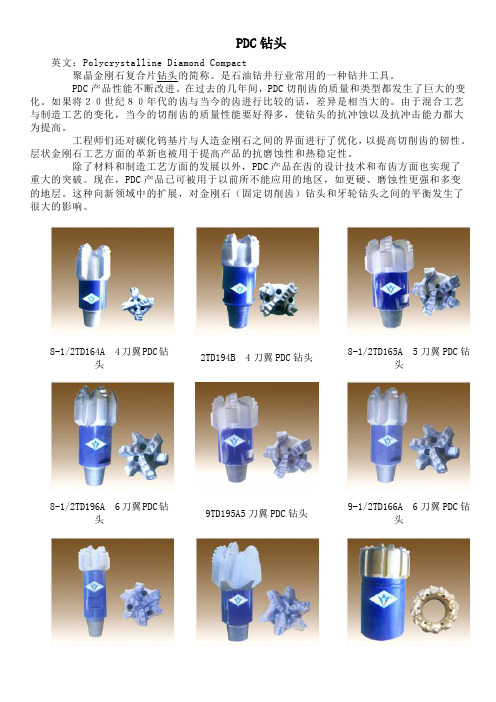
PDC钻头英文:Polycrystalline Diamond Compact聚晶金刚石复合片钻头的简称。
是石油钻井行业常用的一种钻井工具。
PDC产品性能不断改进。
在过去的几年间,PDC切削齿的质量和类型都发生了巨大的变化。
如果将20世纪80年代的齿与当今的齿进行比较的话,差异是相当大的。
由于混合工艺与制造工艺的变化,当今的切削齿的质量性能要好得多,使钻头的抗冲蚀以及抗冲击能力都大为提高。
工程师们还对碳化钨基片与人造金刚石之间的界面进行了优化,以提高切削齿的韧性。
层状金刚石工艺方面的革新也被用于提高产品的抗磨蚀性和热稳定性。
除了材料和制造工艺方面的发展以外,PDC产品在齿的设计技术和布齿方面也实现了重大的突破。
现在,PDC产品已可被用于以前所不能应用的地区,如更硬、磨蚀性更强和多变的地层。
这种向新领域中的扩展,对金刚石(固定切削齿)钻头和牙轮钻头之间的平衡发生了很大的影响。
8-1/2TD164A 4刀翼PDC钻头2TD194B 4刀翼PDC钻头8-1/2TD165A 5刀翼PDC钻头8-1/2TD196A 6刀翼PDC钻头9TD195A5刀翼PDC钻头9-1/2TD166A 6刀翼PDC钻头最初,PDC 钻头只能被用于软页岩地层中,原因是硬的夹层会损坏钻头。
但由于新技术的出现以及结构的变化,目前PDC 钻头已能够用于钻硬夹层和长段的硬岩地层了。
PDC 钻头正越来越多地为人们所选用,特别是随着PDC 齿质量的不断提高,这种情况越发凸显。
由于钻头设计和齿的改进,PDC 钻头的可定向性也随之提高,这进一步削弱了过去在马达钻井中牙轮钻头的优势。
目前,PDC 钻头每天都在许多地层的钻井应用中排挤掉牙轮钻头的市场。
PDC 钻头厚层砾岩钻进技术探索与实践:为了降低海上钻井作业成本、提高作业效率,开发了PDC 钻头厚层砾岩钻进技术.在保持普通PDC 钻头快速切削性能的基础上,通过优选新型高强度PDC 切削 齿、改进钻头切削结构提高钻头的整体强度,通过采用后倾角渐变、力平衡设计、加强切削齿保护等方法提高钻头的稳定性,并且在使用中通过优化钻具组合、采用 合理的钻井参数和"中低排量-中低转速-中高钻压"的平稳钻进模式预防PDC 钻头在砾岩段的先期破坏,有效延长了钻头在砾岩钻进中的寿命.应用该技术实现 了用PDC 钻头在辽东湾一次性钻穿馆陶组和东营组上部疏松地层中垂厚近80 m 的砾岩段,有的井钻穿砾岩段后又直接钻下部中硬地层至完钻井深.采用PDC 钻头厚层砾岩钻进技术,可以大量节省海上钻井作业时间,显著降低钻井费用.PDC 钻头工程技术措施石油钻井装备:1)、首先做好PDC 钻头的选型工作,钻头水眼、流道设计应利于排屑;2)、下入PDC 钻头之前,应充分循环泥浆,清洗井眼,防止起钻后滞留在井眼内的钻屑继续水化分散;3)、下钻时钻头不断刮削井壁,井壁上的泥饼或滞留于井内的钻屑会在钻头下堆积,到一定程度便会压实在钻头上,那么下钻中途进行循环,将钻头 冲洗干净也是有其必要的;4)、下钻过程中还应适当控制速度,防止钻头突然冲入砂桥,钻进一堆烂泥中;另外如果速度恰当,PDC 钻头会顺着上一只钻头所钻的螺旋形井眼轨道行 进,而不是在井壁上划拉下大量泥饼。
关于 钻孔时的切屑控制

钻孔时的切屑控制
转速与进给对切屑的影响
当切屑能够从钻头中顺畅排出时,切屑形成是可以接受的。
对其进行识别的最佳方法是在钻削过程中进行监听。
连续的声音表示排屑良好,断续的声音表示切屑堵塞。
检查进给力或功率监视器。
如果存在异常,则原因可能是切屑堵塞。
查看切屑。
如果切屑长而弯曲,但未卷曲,则表示出现切屑堵塞。
查看孔,如果出现切屑堵塞,则将看到不平整表面。
优秀切屑
良好切屑
异常切屑(堵塞危险)
客户处常见的寿命判断标准为了避免切屑堵塞:
·确保使用正确的切削参数和钻头/刀尖槽形
·检查切屑形状- 调整进给量和速度
进入工件时产生的开始时的切屑总是很长,并不会造成任何问题
可转位刀片钻头(U钻)
中心刀片形成容易识别的锥形切屑。
周边刀片形成类似于车削时形成的切屑
外冷
外冷可在切屑形成良好以及孔深较浅时使用。
由于切削刃温度较高,外冷却液的使用可帮助防止积屑瘤的形成。
钻孔时钻头损坏的原因

钻孔时钻头损坏的原因
钻头在钻孔过程中损坏的原因有很多,主要包括以下几个方面:
1. 材料选择不当,钻头的材料选择不当会导致钻头在使用过程
中容易磨损或断裂。
选择适合钻削材料的钻头材料非常重要,比如
对于不同硬度的岩石或金属,需要选择相应耐磨的钻头材料。
2. 钻头设计不合理,钻头的设计不合理也会导致钻头损坏,比
如刃口角度、刃口数量、刃口间距等设计参数不合适会导致钻头容
易磨损或断裂。
3. 钻削参数选择不当,钻削参数包括转速、进给速度、切削深
度等,选择不当会导致钻头过早磨损或断裂。
比如转速过高、进给
速度过快等都会对钻头造成损坏。
4. 使用环境恶劣,钻孔时的使用环境也会对钻头造成损坏,比
如含有硬颗粒的土壤、高温、高湿度等环境都会加速钻头的磨损。
5. 操作不当,操作人员的技术水平和使用方法也会影响钻头的
损坏情况。
比如不正确的安装、不正确的使用方法等都会导致钻头
的损坏。
综上所述,钻头在钻孔过程中损坏的原因是多方面的,包括材料选择、设计、钻削参数、使用环境和操作方法等多个因素。
为了延长钻头的使用寿命,需要综合考虑这些因素,并严格按照操作规程进行操作。
钻孔废品分析和钻头损坏原因

锯齿粗细及用处
二、锯削操作
工件一般应夹在虎钳的左面,以便操作;工 件伸出钳口不应过长,应使锯缝分开钳口侧 面约20mm左右,防止工件在锯割时产生振动;
锯缝线要与钳口侧面保持平行(使锯缝线与 铅垂线方向一致),便于控制锯缝不偏离划 线线条;夹紧要牢靠,同时要防止将工件 夹变形和夹坏已加工面。
二、锉刀的操作
1.锉刀的锉法
较大平锉握法 右手掌心顶住锉刀柄,大拇指按在
锉刀柄上部,其余手指满握刀柄,左手掌压在锉刀尖端
(也可压稍后一点)。手指略收。左手肘与锉刀轴线约
呈450角。
中型锉刀握法 右手与握大锉刀同,左手几个手指
捏住锉刀尖端。
小锉刀握法 右手可与握大、中锉刀一样,左手
用几个手指压住锉刀面。
(2)通过划线来检查毛坯的形状和尺寸是否符 合要求,防止不合格的毛坯投入机械加工而造 成浪费。
(3)通过划线使加工余量合理分配(又称借料), 保证加工时不出或少出废品。
二、划线的种类
划线:平面划线和立体划线 平面划线:在工件的一个平面上划线,
能明确表示加工界限,它与平面作图法 类似。
立体划线:在工件的几个互相成不同角 度的外表(通常是互相垂直的外表)上划线, 即在长、宽、高三个方向上划线。
钻头工作部分折断
损坏原因
1、用磨钝的钻头钻孔 2、进刀量太大 3、切屑堵塞 4、钻孔快穿通时,未减小进给量 5、工件松动 6、钻薄板或铜料时未修磨钻头 7、钻孔已偏斜而强行借正 8、钻削铸铁时,遇到缩孔
切削刃迅速磨损
1、切削速度过高 2、钻头刃磨角度与材料硬度不相适应
三、钳工的特点
钳工是一种比较复杂、细微、工艺要求较高的 工作。
发动机钻孔加工中钻头崩刃及断刀问题解析

过程中增加一次或多次退刀排屑过程 。 发动机加工中的深孔主要有缸体供油孔 、曲轴 斜油孔 等 ,这些油孔 的孔深 与直径 比例都在 1 0以 上, 在加工过程 中 , 需要确保排屑 的性 能 , 防止 断刀 现象的发 生。例如我公 司铸铁 2 5 0 缸体 的顶面的供
钻 头使 用的相 关原 则 。 对发动机 生产领域的钻 头失效的案例进行解析 。钻 头选择及使 用 时背 离了这些基本原 则往往 会 导致 钻头的异 常磨损 、 崩 刃、 断刀, 钻头失效 的解决需从这些基本原 则入 手和分析。
关键 词 : 钻 头崩刃 ; 断刀 ; 深孔加 工 ; 倾 斜表 面钻孔
中图分类号 : T G9 3 7 文献标识码 : B 文章编号 : 1 6 7 2 — 5 4 5 X ( 2 0 1 4) 0 1 — 0 0 8 1 — 0 2
钻孑 L 是 机加 工最 主要 的加 工形 式 , 据 统计 约 7 O%
材质刀具 , 同时需要检查切削液供应量 。 ( 2 ) 切削刃刃尖崩裂。 刃尖崩裂在很多情况下是 由于加工 中异常振动引起的, 例如 : 夹具存在虚夹 ; 主 轴跳动大 ; 主轴 的拉刀力不足 ; 加工 中断续切削等 , 针
头的跳动 、 主轴跳动 、 主轴拉刀力 、 降低切削进给等。 ( 3 ) 切削刃崩裂。 引起切削刃崩裂的原因有 : 不稳 定的工况 、 超过允许的最大磨损量 ; 刀具硬度过高。
( 4 ) 横 刃 磨损 。引起 横 刃 磨损 的原 因有 : 切 削 速
1 发 动机钻 孑 L 加工现 状概述
其直径达到 7 m m, 深度达到 1 5 0 m m, 钻孔所使 ( 1 ) 切削刃磨损过大 。 引起切削刃磨损大的原 因 油孔 , 2 0 。, 有切削速度太 高 , 进 给太低 , 刀具材料硬度不 足 , 切 用 的是螺旋槽 的硬质合金钻头 ,钻头顶角为 1 在钻孔 削液流量不足等 ,对于这些问题 ,我们应该对应需 在钻孔过程中断刀率较高。经剖开工件发现 : 2 0 m m 附近时 , 由于 排 屑 不 畅 通 , 最 终 导 致 要, 选择合适 的切削速度 、 提 高进给 , 更换硬度 高 的 深度 至 1
变速箱拔插断故障分析

案例分析不规范操作引起变速箱严重损坏类型:原创来源:卡车之家作者:齐兵责任编辑:李昂发布时间:2011年11月10日【卡车之家原创】对于法士特变速箱来讲,卡车之家的朋友们可能基本上大部分都有一定的了解和在使用,但是因为车型的不同,很多朋友并没有真正的按照正确的操作来进行合理的使用。
论坛上经常出现如何挂档、怎么使用等问题,其实不同类型的变速箱需要不同的使用方法,这一点非常重要!这不,一个卡友中招了。
一位卡车之家的解放自卸车卡友,他的变速箱是法士特主箱非同步器类型,在前两天非公路道路使用的过程中在没有任何征兆的情况下出现变速箱突然爆裂,车辆无法继续运行的事故,经过和卡友的沟通后得到了一些在拆检中的部分照片。
● 事故现象:变速箱左侧中间轴因左前中间轴轴承破碎引起中间轴失去定位后出现冲击,导致变速箱壳体呈现开放性破损,从变速箱壳体的断裂痕迹上看没有出现疲劳断裂痕迹,基本上可以判定为过载后的瞬时断裂。
打开上盖后发现变速箱内部中间轴齿轮以及二轴上的齿轮均有不同程度的掰齿,但是这种掰齿不属于正常直齿轮掰齿的形态,而且齿尖被打断的极其不规律,非常像类似异物冲击引起。
● 事故分析:在继续仔细查找的时候发现变速箱底部存在一个拨叉的残端,经过了解,为此变速箱的5/6档拨叉的拨叉头部分,图中化红圈的部分;问了一下用户,之前行驶的时候有没有噪音以及换档困难等情况出现,用户说没有;那么我们排除轴承损坏后引起齿轮啮合不当影响换档品质导致拨叉出现疲劳性断裂。
此事故因为牵扯到的是非公路用自卸车型,结合部分道路使用情况;我们简单假设性的设想一下这个变速箱损坏的过程,因为此卡友不是经常上车,车辆经常是交给驾驶员使用,对于目前有关法士特的操作方面,各个企业基本上重视度=0,此用户的这台法士特变速箱可能是采用单杆左操纵没有类似牵引车上的这种带有随动阀的配置,变速箱的高低速转换采用换档手柄左右拍或上下拨片的预选阀类型。
很多驾驶员在对此类变速箱的操作过程中存在较大的误区,尤其是在高档区越级减档到低档区的时候,如果控制不好,通常会在扭矩没有完全中断的情况下主副箱同时进行换档(比方说从8档直接跳至6档或者5档)这时候上盖上的换档拨叉因为滑动啮合套本身需要一定的推力外加上需要换的齿轮转速在不合适的情况下对拨叉来讲形成了一个交变的冲击负荷,及其容易引起拨叉断裂(经过和用户沟通后得知断茬存在鱼鳞状的断裂痕迹区,证明之前已经存在疲劳)一个小小的拨叉,引起上万元的损失,几个简单的动作,引起不小的争议。
硬质合金钻头断裂分析
文章编号:10081690(2018)04005203
AnalysisonCementedCarbideDrillFracturing
LUHongmei,ZHUXinfa
(ShanghaiToolWorksCo.,Ltd.,Shanghai200093,China)
Abstract:CementedcarbideisoneofthemajormaterialsusedforNCcuttingtools.Abatchofcementedcarbide
图 1表明,钻头断裂在刃部。跟踪检查发现,该 批硬质合金钻头的原材料为 A单位供应的含 10% Co、晶粒度为 0.6~0.8μm的亚细晶粒硬质合金,
收稿日期:20180514 作者简介:陆红妹(1983),女,上海人,主要从事金属材料、硬质合金材料检测分析及材料热处理技术工作。
联系电话:02135090427 基金项目:“十三五”国家重点研发计划课题(课题编号:2016YFB0300403)
钻头断裂的原因。分析结果表明:断裂钻头的磁饱和值偏低,并有脱碳,是导致钻头磨削时断裂的
主要原因。硬质合金脱碳将会导致硬度偏高和断裂韧度明显降低。建议加强对用于制作钻头等刀
具的硬质合金原材料的检测,以避免刀具在制造过程中报废。
关键词:硬质合金;钻头;断裂;脱碳
中图分类号:TH142.2 文献标识码:B
櫡櫡櫡櫡櫡櫡櫡櫡 ~测试与分析 ~
櫡櫡櫡櫡櫡櫡櫡櫡
硬质合金钻头断裂分析
陆红妹,祝新发
(上海工具厂有限公司,上海 200093)
摘 要:硬质合金是制造数控刀具的主要材料之一。一批 12mm的硬质合金钻头在磨削过程中发生断
裂。对断裂的硬质合金钻头进行了金相、硬度、密度、磁饱和及矫顽磁力等有关性能的检测,以弄清
钻头结构和破岩机理
1 PDC钻头的结构切削齿、水力系统、排屑槽和保径齿组成。
它有两种基本的类型:钢体钻头和胎体钻头。
钢体钻头完全由机械加工而成,首先将整块合金钢毛坯经机加工成钻头体,再将切削件焊在连接柱上,最后将连接柱压入事先在钻头上钻的孔中(孔不钻透),其加工质量容易保证。
胎体钻头与金刚石钻头制造方法相似,钻头体采用铸造碳化钨粉、碳化钨粉和浸渍料烧结而成,PDC切削件通常带有一伸长衬底焊到钻头上,其具有最好的保径能力,有较强的抗侵蚀能力,没有连接柱,因而不会出现连接柱断裂的现象,但制造工艺复杂些,加工不易控制。
PDC钻头是依靠安装在钻头体上的切削齿切削地层的,这些切削齿按照一定的方式布置在钻头体表面上,切削齿的安装方位角度也不尽相同,切削齿有复合片式和齿柱式两种结构。
复合片式切削齿是将复合片直接焊接在钻头体上预留的凹槽内而成的,它一般用于胎体钻头;齿柱式切削齿是将复合片焊接在碳化钨齿柱上而成的,安装时将其齿柱镶嵌或焊接在钻头体上的齿孔内,它一般用于钢体钻头,也有用于胎体钻头的。
2 PDC钻头的破岩机理PDC钻头的具体破岩方式主要取决于钻头的切削结构及所钻地层的硬度和岩性,主要分为四种:2.1 剪切。
当PDC钻头在软到中等硬度地层钻进时,复合片切削齿在钻压和扭矩的作用下克服地层应力吃入地层并向前滑动,岩石在切削齿作用下沿其剪切方向破碎并产生塑性流动,切削所产生的岩屑呈大块片状。
这一切削过程与刀具切削金属材料非常相似。
2.2 预破碎。
PDC钻头的“尖/圆”齿交替布置切削结构所特有的岩石破碎方式,主要作用于以纯剪切方式不容易钻进的地层,如中等、中硬和硬地层及带有硬夹层的地层等。
预破碎过程是通过开槽切削来完成的,具有这种切削结构的钻头在钻进过程中,尖形切削齿因与地层接触面积小受力集中而先行吃入地层,岩石在接触应力作用下产生破碎裂纹,随着钻头的不断旋转,尖形齿在岩石中切出一条条小小的螺旋状“卸荷”槽,紧随其后的圆形切削齿则以剪切方式切削强度已大大减弱的大块岩石,达到快速钻进的目的。
变速箱拔插断故障分析
案例分析不规范操作引起变速箱严重损坏类型:原创来源:卡车之家作者:齐兵责任编辑:李昂发布时间:2011年11月10日【卡车之家原创】对于法士特变速箱来讲,卡车之家的朋友们可能基本上大部分都有一定的了解和在使用,但是因为车型的不同,很多朋友并没有真正的按照正确的操作来进行合理的使用。
论坛上经常出现如何挂档、怎么使用等问题,其实不同类型的变速箱需要不同的使用方法,这一点非常重要!这不,一个卡友中招了。
一位卡车之家的解放自卸车卡友,他的变速箱是法士特主箱非同步器类型,在前两天非公路道路使用的过程中在没有任何征兆的情况下出现变速箱突然爆裂,车辆无法继续运行的事故,经过和卡友的沟通后得到了一些在拆检中的部分照片。
● 事故现象:变速箱左侧中间轴因左前中间轴轴承破碎引起中间轴失去定位后出现冲击,导致变速箱壳体呈现开放性破损,从变速箱壳体的断裂痕迹上看没有出现疲劳断裂痕迹,基本上可以判定为过载后的瞬时断裂。
打开上盖后发现变速箱内部中间轴齿轮以及二轴上的齿轮均有不同程度的掰齿,但是这种掰齿不属于正常直齿轮掰齿的形态,而且齿尖被打断的极其不规律,非常像类似异物冲击引起。
● 事故分析:在继续仔细查找的时候发现变速箱底部存在一个拨叉的残端,经过了解,为此变速箱的5/6档拨叉的拨叉头部分,图中化红圈的部分;问了一下用户,之前行驶的时候有没有噪音以及换档困难等情况出现,用户说没有;那么我们排除轴承损坏后引起齿轮啮合不当影响换档品质导致拨叉出现疲劳性断裂。
此事故因为牵扯到的是非公路用自卸车型,结合部分道路使用情况;我们简单假设性的设想一下这个变速箱损坏的过程,因为此卡友不是经常上车,车辆经常是交给驾驶员使用,对于目前有关法士特的操作方面,各个企业基本上重视度=0,此用户的这台法士特变速箱可能是采用单杆左操纵没有类似牵引车上的这种带有随动阀的配置,变速箱的高低速转换采用换档手柄左右拍或上下拨片的预选阀类型。
很多驾驶员在对此类变速箱的操作过程中存在较大的误区,尤其是在高档区越级减档到低档区的时候,如果控制不好,通常会在扭矩没有完全中断的情况下主副箱同时进行换档(比方说从8档直接跳至6档或者5档)这时候上盖上的换档拨叉因为滑动啮合套本身需要一定的推力外加上需要换的齿轮转速在不合适的情况下对拨叉来讲形成了一个交变的冲击负荷,及其容易引起拨叉断裂(经过和用户沟通后得知断茬存在鱼鳞状的断裂痕迹区,证明之前已经存在疲劳)一个小小的拨叉,引起上万元的损失,几个简单的动作,引起不小的争议。
变速箱齿轮轴断裂分析
.
• 从低倍及金相组织可看出断裂轴的心部保留有一定的铸态 组织和疏松特征。这是由于锻造时锻压比不够,没有使铸 态时的枝晶“碎化”,甚至齿牙基体组织都保留有铸态组 织的形貌特征,这必然要降低使用性能。锻压加工可使钢 中树枝状组织变形为纤维状组织,但当锻压比不足时,不 能完全消除钢中树枝状组织。当钢材及锻件的树枝状偏析 严重时,会使钢的力学性能恶化,特别是塑性与冲击韧性 显著降低。此类零件由于尺寸大,在淬火冷却的后期外层 金属已先于内部冷却至室温,而这时内部的温度仍然很高, 继续降温时内部必然产生体积收缩,从而受到外部的强烈 阻碍,在中心部位产生三向拉应力,而最大拉应力作用在 截面的中心部位。当中心有严重的冶金缺陷时,引起应力 集中效应和对强度的削弱,在三向拉应力的作用下,淬透 零件极易开裂。
图1 齿轮轴断面宏观特征
图2 齿局部放大
图3 齿腰表面局部放大
图4 齿轮轴心部特征
三、化学成分分析
从齿轮轴基体钻取化学分析试样进行成分(质量 分数,% )分析,分析结果表明化学成分符合标准 要求。
C
齿轮轴 0.24
Si
0.30
Mn
1.11
P
0.030
S
0.029
Cr
1.27
Mo
0.24
GB/ZQ4290-89 GB/ZQ4290-
01.7~0.24 01.7~
0.20~0.40 0.20~
0.90~1.20 0.90~
≤0.035
≤0.035
1.1~1.4 1.1~
0.2~0.3 0.2~
四、断口扫描电镜观察
取特征较典型的第5齿和第14齿,经除锈处理后,在扫描 电镜下观察:第5齿的断裂起始部位呈沿晶特征,其余部位 呈解理特征,见图5~图6;第14齿主要呈解理特征。
- 1、下载文档前请自行甄别文档内容的完整性,平台不提供额外的编辑、内容补充、找答案等附加服务。
- 2、"仅部分预览"的文档,不可在线预览部分如存在完整性等问题,可反馈申请退款(可完整预览的文档不适用该条件!)。
- 3、如文档侵犯您的权益,请联系客服反馈,我们会尽快为您处理(人工客服工作时间:9:00-18:30)。
自动挡变速箱钻削过程中断屑与钻头结构的分析
自动挡变速箱壳体材质较一般变速箱材质的韧性大幅增强同时壳体内部结构复杂,最小的孔径只有约5毫米。
因此在钻削过程中产生的的铝屑极易残留在壳体中,难以清洗。
钻削产生的铝屑最后存在于壳体成品中,会造成变速箱严重故障。
文章根据生产中遇到的实际问题,浅析了钻屑过程中断屑与钻头结构之间的关系。
标签:自动挡变速箱;断屑;钻头结构
Abstract:Automatic gearbox shell material than the general transmission material toughness greatly enhanced while the shell internal structure is complex,the smallest aperture is only about 5 mm. Therefore,the aluminum scraps produced in the drilling process are easy to remain in the shell and are difficult to clean. The aluminum scraps produced by drilling finally exist in the finished shell,which will cause serious fault of the gearbox. According to the practical problems encountered in production,the relationship between chip breakage and drill bit structure in the process of drilling cuttings is analyzed in this paper.
Keywords:automatic gearbox;chip-breaking;bit structure
1 概述
在自动挡变速箱的售后问题中,最难以解决的问题之一就是自动挡变速箱壳体机械加工及清洗后的残余铝屑难以去除。
如图1所示:加工清洗后如果有铝屑滞留,它们会随着变速箱的工作,进入齿轮系中,随之进入运动部件,造成运动部件卡滞,变速箱无法正常工作。
解决这个问题的关键是将铝屑做小,使清洗机能够很轻松地将铝屑冲出变速箱壳体。
本研究就是针对该问题,即来源于将铝屑做小的实际改进,从而分析钻头结构对断屑的一些方法。
2 钻头断屑理论分析
钻头是最易造成铝屑过大且存留在成品壳体中的刀具。
通过对滞留在壳体中铝屑的宽度与钻头的切削有效刃长进行比对,研究表明铝屑由钻头产生。
因此钻头的断屑是变速箱殼体铝屑滞留问题解决的关键。
2.1 切屑形成过程及条件
由金属切削原理可知,在加工韧性材料时,被切削材料是经过第一变形区和第二变形区的变形后从刀具前面脱离而变为切屑的。
如果切屑不能够自然折断,就必须采取一定措施迫使其折断。
那么,在什么样的条件下切屑才能折断呢?我
们分析切屑的折断条件,脆性材料的自然断裂成崩碎切屑,所以在断屑理论中,一般采用最大应变理论作为切屑折断的理论基础,其判据形式是:
由(1)式有:设切屑厚度为ac,切屑卷曲半径为Rc,受阻后切屑半径为为RL,当切屑应变ε达到断裂应变极限εb时,切屑将被折断。
因此切屑折断的条件为:
式中:K为切屑剖面的中性面至粗糙面距离系数,K*ac为切屑剖面的中性面至粗糙面距离。
由(2)式可以看出,切屑厚度ac越大,切屑上向卷曲的曲率半径尺也越小时,应变心就越大,切削就易于折断。
根据上述理论,使连续切屑折断的条件是:加于切屑上的变形力应大于切屑材料的断裂强度极限。
2.2 切屑折断方法
若切屑能在第一变形区内受刀具的挤压而剪断,就必须使作用于滑移面上的最大剪应力大于被加工材料的剪切强度极限,并使切削在第一变形区就脱离材料母体而断裂,形成碎屑。
若切屑经过第一变形区变形后没有折断,继续流向第二变形区,在第二变形区内使切屑的变形量突然增大,就可能使切屑折断。
为此可以采用如下措施:
(1)改变被加工材料的性能。
(2)增加切屑变形,如加大进绐量,使剪切应力加大。
(3)在刀具的前刀面上增加排屑槽。
(4)增大进给量,使切屑来不及塑性变形而折断。
(5)降低切削速度,并加注冷却液,使切屑的塑性降低而易于折断。
3 断屑效果及钻屑力测试试验
前面对钻头的断屑进行分析,从理论上推导、论证了刀具结构的断屑条件,本节根据断屑条件,设计刀具结构,验证其断屑效果。
试验过程设计:
试验机床:德国DMGNHC5000加工中心机床。
生产线正常加工的自动挡变速箱壳体,切削用量:每齿进给量0.30mm/转,线速度:202米/分钟试验刀具:按照试验方案制作前刀面带断屑槽的直径为4.2毫米的整体硬质合金钻头。
试验过程:将机床内部的所有切屑清空,在夹具下放置收集铝屑的托盘,单
步加工易卡铝屑的孔,加工结束后将盘中得到的铝屑和工件中的铝屑聚集在一起,选择最大的铝屑作为样品。
分别用无断屑槽和有断屑槽加工6次,得到12个试验样品,并对样本编号。
测量方法:将样品放置在显微镜中进行拍摄保存为图片,并留有比例尺。
将得到的图片导入AutoCAD软件中。
在AutoCAD软件中测量铝屑的长度和宽度,除以AutoCAD中比例尺测量的长度值,换算得到每一个铝屑的实际长度和实际宽度。
最后,将得到的长度值和宽度值进行比较,将较大值作为铝屑的长度。
结果表明:
(1)带有断屑槽的钻头能解决自动挡
变速箱复杂油孔、盲孔残余铝屑的问题,能适应于变速箱的批量生产。
在通过数据分析对比中发现:断屑槽产生的铝屑长度、宽度较原先铝屑均有明显改善且稳定。
此项研究对分析其他类产品,如发动机缸盖、气缸盖罩等打下了基础,有推广价值。
(2)本文只
论证了断屑槽对自动挡变速箱的影响,对断屑槽的工艺参数,如槽宽、槽深、槽底圆弧半径、棱带宽度未做分析,分析不同材质的变速箱有最适的断屑槽参数,后续将对这一部份内容进行研究分析。
参考文献:
[1]中山一雄.金属切削加工理论[M].李云芳,译.机械工业出版社,1985,3:188-192.
[2]方宁.硬质合金刀片新型断屑槽形及其CAD技术研究[D].华中理工大学,1994.
[3]蒋丽.浅析数控刀具的合理选用[J].智能城市,2017(04):147.
[4]何腾芸.断屑机理和断屑判据研究[J].北京理工大学,哈尔滨科学技术大学学报,1989.
[5]向志杨.钻削典型难加工材料的断屑技术研究[D].东北大学,2009.。